PWM or MPPT
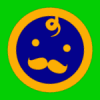
Mastermind
Registered Users Posts: 2 ✭
I have a 175 watt solar panel with 36.5V and 4.80A, from which I have to charge a 12V battery through a PWM charge controller, means 14V x 4.80A = 67W , so the panel works on 67watts? If I use a MPPT charge controller will it makes any difference?
Tagged:
Comments
-
A MPPT controller would deliver 95% of the panel harvest, which is over 2x what the PWM controller delivers.Generally, the tipping point cost wise, is 300w of panel, but you can see,67w via PWMcompare to165w MPPT(actually, the panel will seldom produce more than 80% of Pmax =140w, regardless of controller)Powerfab top of pole PV mount | Listeroid 6/1 w/st5 gen head | XW6048 inverter/chgr | Iota 48V/15A charger | Morningstar 60A MPPT | 48V, 800A NiFe Battery (in series)| 15, Evergreen 205w "12V" PV array on pole | Midnight ePanel | Grundfos 10 SO5-9 with 3 wire Franklin Electric motor (1/2hp 240V 1ph ) on a timer for 3 hr noontime run - Runs off PV ||
|| Midnight Classic 200 | 10, Evergreen 200w in a 160VOC array ||
|| VEC1093 12V Charger | Maha C401 aa/aaa Charger | SureSine | Sunsaver MPPT 15A
solar: http://tinyurl.com/LMR-Solar
gen: http://tinyurl.com/LMR-Lister , -
But when I connect the panel direct with the battery with out pwm controller, panel draws the same amps I.e 4.8, why is that ?
-
Mastermind said:But when I connect the panel direct with the battery with out pwm controller, panel draws the same amps I.e 4.8, why is that ?
If the panel were connected directly to the battery for an extended period time, the voltage would continue to rise above the safe limits which would generate heat and ultimately damage the battery, hense the need to control.
1500W, 6× Schutten 250W Poly panels , Schneider MPPT 60 150 CC, Schneider SW 2524 inverter, 400Ah LFP 24V nominal battery with Battery Bodyguard BMS
Second system 1890W 3 × 300W No name brand poly, 3×330 Sunsolar Poly panels, Morningstar TS 60 PWM controller, no name 2000W inverter 400Ah LFP 24V nominal battery with Daly BMS, used for water pumping and day time air conditioning.
5Kw Yanmar clone single cylinder air cooled diesel generator for rare emergency charging and welding. -
Mastermind said:But when I connect the panel direct with the battery with out pwm controller, panel draws the same amps I.e 4.8, why is that ?
Powerfab top of pole PV mount | Listeroid 6/1 w/st5 gen head | XW6048 inverter/chgr | Iota 48V/15A charger | Morningstar 60A MPPT | 48V, 800A NiFe Battery (in series)| 15, Evergreen 205w "12V" PV array on pole | Midnight ePanel | Grundfos 10 SO5-9 with 3 wire Franklin Electric motor (1/2hp 240V 1ph ) on a timer for 3 hr noontime run - Runs off PV ||
|| Midnight Classic 200 | 10, Evergreen 200w in a 160VOC array ||
|| VEC1093 12V Charger | Maha C401 aa/aaa Charger | SureSine | Sunsaver MPPT 15A
solar: http://tinyurl.com/LMR-Solar
gen: http://tinyurl.com/LMR-Lister , -
A PWM controller is simply an On/Off switch... The higher percent of time the switch is on, the more "average" charging current (PWM is pulse width modulation... Say you have a 1 second cycle--if the switch is on 10%, it is on for 0.1 second out of 1.0 second. If it is on 100% of the time, the switch is on for ~1.0 second out of every 1.0 second).
Solar panels output current in proportion to the amount of sun. Full noon time sun, panel pointed at sun, you will get ~Imp (current maximum power) from zero volts to Vmp, then current will fall to zero amps at Voc (Voltage open circuit). Note--This is an approximation, but works good enough for this explanation. If you have 50% sun, then you get 0.50 * Imp worth of current).
Power is = Voltage * Current... If you have 4.8 Amps from the solar panel, the power "into the battery" depends on the battery voltage:- PWM charging a 12 volt battery with a "24 volt" solar panel:
- Pbatt ~ Vbatt*Ibatt = 10.5 volts battery * 4.8 amps (near dead battery) = 50.4 Watts
- Pbatt = 12.8 volts * 4.8 amps (charging battery) = 61.44 Watts
- Pbatt = 14.75 volts * 4.8 amps (~80-90% state of charge) = 70.8 watts
- PWM charging a 24 volt battery with "24 volt" panel:
- Pbatt = 29.5 Volts * 4.8 amps (80-90% SoC battery) = 141.6 Watts
Think of the PWM controller like a 1 speed transmission.
Think of the MPPT controller like an automatic transmission that matches the "optimum" panel voltage+current input (i.e., RPM and Torque from engine) to that of the battery bank (i.e., RPM and Torque at wheels).
-Bill
Near San Francisco California: 3.5kWatt Grid Tied Solar power system+small backup genset - PWM charging a 12 volt battery with a "24 volt" solar panel:
-
BB. said:A PWM controller is simply an On/Off switch... The higher percent of time the switch is on, the more "average" charging current (PWM is pulse width modulation... Say you have a 1 second cycle--if the switch is on 10%, it is on for 0.1 second out of 1.0 second. If it is on 100% of the time, the switch is on for ~1.0 second out of every 1.0 second).
Solar panels output current in proportion to the amount of sun. Full noon time sun, panel pointed at sun, you will get ~Imp (current maximum power) from zero volts to Vmp, then current will fall to zero amps at Voc (Voltage open circuit). Note--This is an approximation, but works good enough for this explanation. If you have 50% sun, then you get 0.50 * Imp worth of current).
Power is = Voltage * Current... If you have 4.8 Amps from the solar panel, the power "into the battery" depends on the battery voltage:- PWM charging a 12 volt battery with a "24 volt" solar panel:
- Pbatt ~ Vbatt*Ibatt = 10.5 volts battery * 4.8 amps (near dead battery) = 50.4 Watts
- Pbatt = 12.8 volts * 4.8 amps (charging battery) = 61.44 Watts
- Pbatt = 14.75 volts * 4.8 amps (~80-90% state of charge) = 70.8 watts
- PWM charging a 24 volt battery with "24 volt" panel:
- Pbatt = 29.5 Volts * 4.8 amps (80-90% SoC battery) = 141.6 Watts
Think of the PWM controller like a 1 speed transmission.
Think of the MPPT controller like an automatic transmission that matches the "optimum" panel voltage+current input (i.e., RPM and Torque from engine) to that of the battery bank (i.e., RPM and Torque at wheels).
-BillThanks for that great explanation.A quick followup question - if you were doing a design around a PWM charge controller, is there an average loss factor that you would use when trying to calculate the size of your modules/array. I have seen .95-.98 used for MPPT charge controllers, but haven't come across a consensus number for PWM.Alex - PWM charging a 12 volt battery with a "24 volt" solar panel:
-
Alex, you are very welcome.
Regarding loss factor. I use the same loss factor for both pwm and mppt controllers of 0.77 ...
More or less, solar panels are rated under standard sun and room temperature (75F or so).
In real life, panel Vmp is roughly 81% of factory spec in warm to hot weather in full sun. Add a few percent of loses for controller and dust on panels, you get a nominal 75% 77% end to end efficiency (solar array to charge controller to battery bank).
Add battery charging loses (80 to 90% efficiency for flooded cell lead acid batteries), ac inverter loses (120/240 vac), and you are looking at panel to ac load efficiency of 52%.
For 400 Watt or less array, a pwm system usually is more cost effective.
For systems over 800 Watt array, mppt systems usually make more sense.
My suggestion is to paper design 2 or more different systems and cost them out. And see what works better for you.
BillNear San Francisco California: 3.5kWatt Grid Tied Solar power system+small backup genset -
I'm not entirely sure what you mean by "loss factor". A pwm controller should be a bit more efficient than a mppt (no voltage transformation loss), but overall losses really depend on factors Bill noted.Off-grid.
Main system ~4kw panels into 2xMNClassic150 370ah 48v bank 2xOutback 3548 inverter 120v + 240v autotransformer
Night system ~1kw panels into 1xMNClassic150 700ah 12v bank morningstar 300w inverter -
Estragon said:I'm not entirely sure what you mean by "loss factor". A pwm controller should be a bit more efficient than a mppt (no voltage transformation loss), but overall losses really depend on factors Bill noted.Let me explain my thinking and you can clarify my thinking.With a 12 volt nominal system, the production of a panel is constrained by the voltage of the battery at all times.With a 12 volt nominal system a MPPT charge controller is able to convert voltage that exceeds the maximum charging voltage of a 12 volt battery into current and gets around this inherent limitation.There is a difference in the amount of energy that the respective types of charge controllers are able to convert into usable energy from the same given solar panel/array. A PWM charge controller would have a loss relative to a MPPT charge controller during times when the temperature of the solar module permits an operational voltage that exceeds the maximum charging voltage of the battery. When designing a system a MPPT charge controller would provide more usable energy with the same solar resource and module when working in an environment like where I work - 3200-4200m above sea level, correct? Do you ever try to quantify this benefit or loss of usable energy in a design when you are sizing your array/module?I work primarily with extremely small-scale systems.
-
The cost of MPPT controllers is higher than PWM so there is a point where the benefits exceeds the need for additional PV to achieve the same energy. There is a misconception that MPPT will always increase output over PWM, in many cases it's true but where temperatures are always high 35°C+ as well as being at low altitude, the benefits are minimal. Here's some good reading material
https://www.solar-electric.com/learning-center/batteries-and-charging/mppt-solar-charge-controllers.html
1500W, 6× Schutten 250W Poly panels , Schneider MPPT 60 150 CC, Schneider SW 2524 inverter, 400Ah LFP 24V nominal battery with Battery Bodyguard BMS
Second system 1890W 3 × 300W No name brand poly, 3×330 Sunsolar Poly panels, Morningstar TS 60 PWM controller, no name 2000W inverter 400Ah LFP 24V nominal battery with Daly BMS, used for water pumping and day time air conditioning.
5Kw Yanmar clone single cylinder air cooled diesel generator for rare emergency charging and welding. -
alexj said:Do you ever try to quantify this benefit or loss of usable energy in a design when you are sizing your array/module?I work primarily with extremely small-scale systems.
Things t note in designing small-scale systems, MPPT type controllers also need some 'head space' so solar panels should present about 30% higher voltage than the system will be charging at. Hence a 12 volt system that is charging at 15 volts should present about (15x1.35=) 20.25 volts. This is higher than the VMP of 12 volt nominal panels so multiple panels or panels with more than 36 cells should be used.
MPPT shines when solar panels aren't matched to battery voltage, like cell configurations of 54 and 60 cells. There are some very large panels made with 72 cells now, making large 24 and 48 volt arrays on PWM more cost effective and some what reason to consider. Having run a small cabin on a 24 volt 16-1700 watt array and a 60 amp PWM controller for 5-6 years I am comfortable in saying it works out nicely.
Home system 4000 watt (Evergreen) array standing, with 2 Midnite Classic Lites, Midnite E-panel, Magnum MS4024, Prosine 1800(now backup) and Exeltech 1100(former backup...lol), 660 ah 24v Forklift battery(now 10 years old). Off grid for 20 years (if I include 8 months on a bicycle).
- Assorted other systems, pieces and to many panels in the closet to not do more projects. -
Assuming the high altitude locations are cool/cold, an mppt controller will quite likely produce more with available solar. To quantify the difference, you would want to do a couple of paper designs to define variables like panel/string voltage and temp coefficients in the design ambient conditions.
I've seen production curve charts at Midnite Solar website, but they're for larger controllers. I don't know if they would apply to smaller controllers. At altitude, you'll want to derate the controller output, but classics may still be big for "extremely small scale systems".
If high altitude is also high latitude, self consumption could be an issue. Many (most, all?) mppt controllers take more power just being on and waiting for input vs pwm. This self consumption would be a factor in any case, but could be a deal breaker in an unattended high latitude winter application.Off-grid.
Main system ~4kw panels into 2xMNClassic150 370ah 48v bank 2xOutback 3548 inverter 120v + 240v autotransformer
Night system ~1kw panels into 1xMNClassic150 700ah 12v bank morningstar 300w inverter -
By their nature, PWM controllers have high ripple current and voltage. It's not clear to me, but this has been reported to increase heating/gassing and reduce battery life. 5% of C20 is a common spec, meaning a 100AH battery shouldn't see more than a 5A rapid variation in charge current. I can't see how a PWM controller can avoid this.
http://www2.exide.com/Media/files/Location Data/Battery Charging & Storage Specs 11_13_15.pdf
I am available for custom hardware/firmware development
-
jonr said:By their nature, PWM controllers have high ripple current and voltage. It's not clear to me, but this has been reported to increase heating/gassing and reduce battery life. 5% of C20 is a common spec, meaning a 100AH battery shouldn't see more than a 5A rapid variation in charge current.jonr said:I can't see how a PWM controller can avoid this.
Home system 4000 watt (Evergreen) array standing, with 2 Midnite Classic Lites, Midnite E-panel, Magnum MS4024, Prosine 1800(now backup) and Exeltech 1100(former backup...lol), 660 ah 24v Forklift battery(now 10 years old). Off grid for 20 years (if I include 8 months on a bicycle).
- Assorted other systems, pieces and to many panels in the closet to not do more projects. -
> A battery seeing greater than 5% of it's amps during float stage... shouldn't be in float stage
A PWM controller can't control peak current or voltage - when it turns on, how can it avoid > 5A flowing?I am available for custom hardware/firmware development
-
jonr said:> A battery seeing greater than 5% of it's amps during float stage... shouldn't be in float stage
A PWM controller can't control peak current or voltage - when it turns on, how can it avoid > 5A flowing?
Home system 4000 watt (Evergreen) array standing, with 2 Midnite Classic Lites, Midnite E-panel, Magnum MS4024, Prosine 1800(now backup) and Exeltech 1100(former backup...lol), 660 ah 24v Forklift battery(now 10 years old). Off grid for 20 years (if I include 8 months on a bicycle).
- Assorted other systems, pieces and to many panels in the closet to not do more projects. -
If there are DC loads on the battery, (e.g. inverter, DC lights), then the Float and Absorb current can be quite a bit and at times require the controller to go back to MPPT mode. i.e. Absorb MPPT or Float MPPT etc...
-
Apply enough voltage and even fully charged batteries will allow 5A of current to flow. 18+V is common on 12V nominal systems.
I am available for custom hardware/firmware development
-
jonr said:18+V is common on 12V nominal systems.
Except that most 12V inverters will complain or turn themselves off if battery voltage gets to 16 volts. or so. Sometimes less.
boB
-
My understanding is 18+v may be common on the pv side of an mppt controller, which an inverter (hopefully) never sees. The inverter sees battery voltage.
A pwm controller will be at or near battery voltage. Unless the battery is very small (like a capacitor) the pulsed voltage at the battery won't get to anything like Vmp.
I'm still learning this stuff though, so I stand to be corrected. I don't see how ripple is a problem for batteries.Off-grid.
Main system ~4kw panels into 2xMNClassic150 370ah 48v bank 2xOutback 3548 inverter 120v + 240v autotransformer
Night system ~1kw panels into 1xMNClassic150 700ah 12v bank morningstar 300w inverter -
jonr said:Apply enough voltage and even fully charged batteries will allow 5A of current to flow. 18+V is common on 12V nominal systems.
Do you understand that 'Float' is a stage of charging when the charge controller limits the voltage, using pulses and the electrochemical nature of batteries to limit the system voltage. At these lower voltages very minimal amounts of current flow to the battery.
By definition, Float is a state of full or nearly full charge. If the charge controller is allowing higher voltage then it is not in 'float' stage and we have no reference to problems from your source. If you just don't want to understand... Don't.
Home system 4000 watt (Evergreen) array standing, with 2 Midnite Classic Lites, Midnite E-panel, Magnum MS4024, Prosine 1800(now backup) and Exeltech 1100(former backup...lol), 660 ah 24v Forklift battery(now 10 years old). Off grid for 20 years (if I include 8 months on a bicycle).
- Assorted other systems, pieces and to many panels in the closet to not do more projects. -
jonr said:> A battery seeing greater than 5% of it's amps during float stage... shouldn't be in float stage
A PWM controller can't control peak current or voltage - when it turns on, how can it avoid > 5A flowing?
It's not in 'Float' the parameters of your argument.
Home system 4000 watt (Evergreen) array standing, with 2 Midnite Classic Lites, Midnite E-panel, Magnum MS4024, Prosine 1800(now backup) and Exeltech 1100(former backup...lol), 660 ah 24v Forklift battery(now 10 years old). Off grid for 20 years (if I include 8 months on a bicycle).
- Assorted other systems, pieces and to many panels in the closet to not do more projects. -
Photowhit said:As far as I know MPPT charge controller revert to PWM at some point after reaching absorb, once in float it is likely receiving a pulsed current flow once in float.MPPT has a native method to reduce power: run the panels at a power point that produces less. You can check for this behavior by watching panel voltage move toward Voc as power demands decrease.
-
> If the charge controller is allowing higher voltage...
Photowit, if you think that a PWM controller can limit peak voltage (ie, during msecs of on time) or that a PWM controller never switches on in float, I'm fine with you "going away".
fratermus is correct - ie, if only 5A flows out of 20A of panels, the voltage produced (and seen by the battery when a PWM controller is switched on) will be close to Voc.
I am available for custom hardware/firmware development
-
Not sure where this discussion is headed with the "go away" statements, but from my observations and discussions with Morningstar tech support this is my understanding. With a Morningstar TS60 PWM remote meter I observe the array voltage in float, it is near VOC 43.2 V, battery voltage is 27V, 24V nominal system zero measurable amps. Morningstar tech support sent this explanation to describe how the controller works........The duty cycle is used to determine when to transition into float. The duty cycle is derived from a square waveform and the percentage of time - out of each complete cycle - when current is allowed to flow. Current is regulated by opening and closing the PV-battery circuit -- the essence of a series charge controller. A 50% duty cycle means that current is flowing, and interrupted for, half of the cycle. Our controllers pulse with a frequency of 300 Hz, so each cycle lasts 1/300th of a second. By varying the duty cycle, we can control the average current going into the battery so that the regulation voltage is maintained but not exceeded. As the battery reaches full charge at a particular voltage, it will require less and less current to maintain that voltage and the duty cycle will decrease. The duty cycle will approach zero %, but will never actually get there because losses and battery self-discharge require at least some current to maintain regulation voltage. A Morningstar PWM controller's float transition algorithm waits for the duty cycle to reach 30% or less before starting a one hour timer. When the timer expires, the controller moves from absorption to float voltage. A 30% duty cycle simply means that 30% of AVAILABLE charging current is allowed to pass. Duty cycle is the best measure we have to determine how deep a battery may be in regulation. Factors affecting the accuracy of this method include: 1. Reduced radiation and current. With less available charge current, the duty cycle will inevitably be higher making the transition to float more difficult; 2. Load on the battery. Loads on the battery drain current from the battery which causes a higher duty cycle. If the load is large enough (greater than the amount of solar current ) it can pull the controller into 100% duty cycle and out of absorption - into bulk charging; 3. Aging batteries. Old batteries tend to absorb more current at regulation, keeping duty cycle high. Sulfation leads to higher internal resistance, and more energy loss in the form of heat, which leads to excessive water loss.
Hope some will find this information useful, interestingly this use of high frequancy pulses is used in desulfators, for what that's worth.1500W, 6× Schutten 250W Poly panels , Schneider MPPT 60 150 CC, Schneider SW 2524 inverter, 400Ah LFP 24V nominal battery with Battery Bodyguard BMS
Second system 1890W 3 × 300W No name brand poly, 3×330 Sunsolar Poly panels, Morningstar TS 60 PWM controller, no name 2000W inverter 400Ah LFP 24V nominal battery with Daly BMS, used for water pumping and day time air conditioning.
5Kw Yanmar clone single cylinder air cooled diesel generator for rare emergency charging and welding.
Categories
- All Categories
- 229 Forum & Website
- 137 Solar Forum News and Announcements
- 1.4K Solar News, Reviews, & Product Announcements
- 199 Solar Information links & sources, event announcements
- 898 Solar Product Reviews & Opinions
- 256 Solar Skeptics, Hype, & Scams Corner
- 22.5K Solar Electric Power, Wind Power & Balance of System
- 3.5K General Solar Power Topics
- 6.7K Solar Beginners Corner
- 1K PV Installers Forum - NEC, Wiring, Installation
- 2.1K Advanced Solar Electric Technical Forum
- 5.6K Off Grid Solar & Battery Systems
- 428 Caravan, Recreational Vehicle, and Marine Power Systems
- 1.1K Grid Tie and Grid Interactive Systems
- 654 Solar Water Pumping
- 816 Wind Power Generation
- 624 Energy Use & Conservation
- 619 Discussion Forums/Café
- 312 In the Weeds--Member's Choice
- 75 Construction
- 124 New Battery Technologies
- 108 Old Battery Tech Discussions
- 3.8K Solar News - Automatic Feed
- 3.8K Solar Energy News RSS Feed