Is a 24V inverter safer than a 12V inverter at 2200W
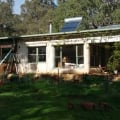
karrak
Solar Expert Posts: 326 ✭✭✭✭
There are a number of 12V inverters made by reputable manufacturers that will output more than 2200W on a continuous basis so it puzzles me that some people seem to be of the view that it is unsafe running 12V inverters at this power level and insist you should use a 24V inverter.
The main safety concern seems to be that a 12V inverter running a 2200W load will be drawing around 200A from the battery compared to 100A for a 24V inverter.
Assuming that the correct size cables and connectors are used and that the connections are done properly I can't see any difference. On both the 12V and 24V inverter you still have the same amount of power passing through the cable and connections.
With any inverter if there is a fault, be it a bad connection or the cable is too small there will be too large a voltage drop at the site of the fault that may generate enough heat to start a fire. This voltage drop is limited by the inverter's low voltage shutdown voltage. For a 12V inverter this is usually 10.5V and for a 24V inverter it is 21V. The amount of power available to cause a fire by the fault will be the voltage drop * current. For a 12V battery this will be around (12.0-10.5)*200=300W and for a 24V battery it will be (24-21)*100=300W
Am I missing something?
The main safety concern seems to be that a 12V inverter running a 2200W load will be drawing around 200A from the battery compared to 100A for a 24V inverter.
Assuming that the correct size cables and connectors are used and that the connections are done properly I can't see any difference. On both the 12V and 24V inverter you still have the same amount of power passing through the cable and connections.
With any inverter if there is a fault, be it a bad connection or the cable is too small there will be too large a voltage drop at the site of the fault that may generate enough heat to start a fire. This voltage drop is limited by the inverter's low voltage shutdown voltage. For a 12V inverter this is usually 10.5V and for a 24V inverter it is 21V. The amount of power available to cause a fire by the fault will be the voltage drop * current. For a 12V battery this will be around (12.0-10.5)*200=300W and for a 24V battery it will be (24-21)*100=300W
Am I missing something?
Off-Grid with LFP (LiFePO4) battery, battery Installed April 2013
32x90Ah Winston cells 2p16s (48V), MPP Solar PIP5048MS 5kW Inverter/80A MPPT controller/60A charger, 1900W of Solar Panels
modified BMS based on TI bq769x0 cell monitors.
Homemade overall system monitoring and power management https://github.com/simat/BatteryMonitor
32x90Ah Winston cells 2p16s (48V), MPP Solar PIP5048MS 5kW Inverter/80A MPPT controller/60A charger, 1900W of Solar Panels
modified BMS based on TI bq769x0 cell monitors.
Homemade overall system monitoring and power management https://github.com/simat/BatteryMonitor
Comments
-
In theory you are correct, but in reality the higher the amps in the circuit = lower overall efficiency.
Balancing two or more 12 Volt batteries in parallel is not easy, as balancing batteries in series.
48 Volt systems are common.
Designed correctly, a 12 volt system can be as safe as a 24 volt system.
It is more difficult to extinguish high amperage DC arcing vs low amperage -
Safe or unsafe is not really the issue.
The key phrase is "Assuming that the correct size cables and connectors are used". Cables are sized for the Amps. With 24 volts, the amps are half what they are for 12 volts, so you can use smaller cables with 24 volts than with 12 volts.
A 12 volt system will require more batteries in parallel than a 24 volt system. It is difficult to completely balance charge and discharge for parallel batteries.
Take a look at some battery specifications and configurations and calculate whether or not you can actually get 200 amps out of a 12 volt battery bank.
Keith
-
Theoretically from a safety point of view, there is no difference assuming all conductors, connectors and most importantly overcurrent protection are utilized, the difference is generally not safety related but more an economic difference, lower voltages mean more current, so larger conductors, larger fuses/circuit breakers and larger battery capacity to cover the current demand, lower voltages may mean more parallel strings. Going to a higher voltage reduces the current so smaller "ballance of system" devices can be used, higher array wattage can be utilized and batteries connected in series are inherently easier to maintain. So generally there is a limit to the economic viability of a 12V system, perhaps in the 1000W range but as the demand gets higher it only makes sence to increase the voltage.1500W, 6× Schutten 250W Poly panels , Schneider MPPT 60 150 CC, Schneider SW 2524 inverter, 400Ah LFP 24V nominal battery with Battery Bodyguard BMS
Second system 1890W 3 × 300W No name brand poly, 3×330 Sunsolar Poly panels, Morningstar TS 60 PWM controller, no name 2000W inverter 400Ah LFP 24V nominal battery with Daly BMS, used for water pumping and day time air conditioning.
5Kw Yanmar clone single cylinder air cooled diesel generator for rare emergency charging and welding. -
Think we all wrote at the same time, so no connection to one another, but essentially the same reply.1500W, 6× Schutten 250W Poly panels , Schneider MPPT 60 150 CC, Schneider SW 2524 inverter, 400Ah LFP 24V nominal battery with Battery Bodyguard BMS
Second system 1890W 3 × 300W No name brand poly, 3×330 Sunsolar Poly panels, Morningstar TS 60 PWM controller, no name 2000W inverter 400Ah LFP 24V nominal battery with Daly BMS, used for water pumping and day time air conditioning.
5Kw Yanmar clone single cylinder air cooled diesel generator for rare emergency charging and welding. -
Key words are "properly sized and maintained". If connections become corroded, usually due to limited maintenance, the higher amperage at 12 volts is going to make more heat.
Another consideration is the amount of time the inverter is running at full steam. If only occasional high loads are experienced (Skill saw for eg) it would be less of a concern.
Island cottage solar system with appriximately 2500 watts of panels, 1kw facing southeast 1.3kw facing southwest 170watt ancient Arco's facing due south. All panels in parallel for a 24 volt system. Trace DR1524 MSW inverter which has performed flawlessly since 1994. Outback Flexmax 80 MPPT charge controller four 467A-h AGM batteries. Insignia 11.5 cubic foot electric fridge 1/4hp GSW piston pump. My 31st year. -
Defects. A small defect has a much larger impact with a 12V system. A crimp internal to the inverter, or a bad spot on a PCB trace. It may pass a 5 min test, but the criticality at 12V 200A, is much more, than at 100A.
Powerfab top of pole PV mount | Listeroid 6/1 w/st5 gen head | XW6048 inverter/chgr | Iota 48V/15A charger | Morningstar 60A MPPT | 48V, 800A NiFe Battery (in series)| 15, Evergreen 205w "12V" PV array on pole | Midnight ePanel | Grundfos 10 SO5-9 with 3 wire Franklin Electric motor (1/2hp 240V 1ph ) on a timer for 3 hr noontime run - Runs off PV ||
|| Midnight Classic 200 | 10, Evergreen 200w in a 160VOC array ||
|| VEC1093 12V Charger | Maha C401 aa/aaa Charger | SureSine | Sunsaver MPPT 15A
solar: http://tinyurl.com/LMR-Solar
gen: http://tinyurl.com/LMR-Lister , -
Safety, I might give a small edge to 24 volt systems mostly for the reasons others have give.
...but Smart Design 24 volt has so many advantages;
Inverter and charge controllers will operate at lower temps for the same output (hence likely last longer).
Double the size array for each charge controller.
Fewer strings of batteries and panels
less wiring, breakers, fuses.
Home system 4000 watt (Evergreen) array standing, with 2 Midnite Classic Lites, Midnite E-panel, Magnum MS4024, Prosine 1800(now backup) and Exeltech 1100(former backup...lol), 660 ah 24v Forklift battery(now 10 years old). Off grid for 20 years (if I include 8 months on a bicycle).
- Assorted other systems, pieces and to many panels in the closet to not do more projects. -
Thanks for the replies.
Regarding issues of corrosion causing high resistance I would have thought that the extra surface area of the higher current connections would balance this problem up.
Regarding faults within the inverter, PCB trace widths, solder pads and plated through holes will be larger in higher current inverters which again I would have thought would balance the problem up.
Paralleling batteries up is another interesting topic. With lithium batteries if the wiring is done correctly as far as I can see it is actually beneficial to parallel batteries up. I have little experience with lead acid batteries in off-grid systems but wonder how many of the problems that we hear about are caused by poor battery interconnection design.
As a general rule I agree that the larger the power output the higher the voltage but don't think this should be the only criteria to base system voltage on. For use in RVs or marine based systems using the same voltage as the RV or boat would be a consideration. Another consideration might be that if your average power usage is low but you need high peak power output for running high power equipment like welders, pumps etc.
Simon
Off-Grid with LFP (LiFePO4) battery, battery Installed April 2013
32x90Ah Winston cells 2p16s (48V), MPP Solar PIP5048MS 5kW Inverter/80A MPPT controller/60A charger, 1900W of Solar Panels
modified BMS based on TI bq769x0 cell monitors.
Homemade overall system monitoring and power management https://github.com/simat/BatteryMonitor
-
In terms of shock risk, higher voltage = higher risk so in that sense, I suppose 12v is marginally safer than 24v.Off-grid.
Main system ~4kw panels into 2xMNClassic150 370ah 48v bank 2xOutback 3548 inverter 120v + 240v autotransformer
Night system ~1kw panels into 1xMNClassic150 700ah 12v bank morningstar 300w inverter -
Estragon said:In terms of shock risk, higher voltage = higher risk so in that sense, I suppose 12v is marginally safer than 24v.
I considered that, but for passage through skin, I thought the threshold was around 30 volts. I'll check later, but certainly a consideration for 48 volt systems. I do believe the NEC has added restricted access for DC above 30 volts.Home system 4000 watt (Evergreen) array standing, with 2 Midnite Classic Lites, Midnite E-panel, Magnum MS4024, Prosine 1800(now backup) and Exeltech 1100(former backup...lol), 660 ah 24v Forklift battery(now 10 years old). Off grid for 20 years (if I include 8 months on a bicycle).
- Assorted other systems, pieces and to many panels in the closet to not do more projects. -
I still like a rule of thumb that I read about years ago:
12 volt is OK for up to 1000 watts of panels.
24 volt is OK for up to 2000 watts of panels.
Overly simplified? Sure....but it usually works based on what posters have to say about their systems. I know that Photowit rues the day day that he settled on 24 volt because it makes expansion more expensive and difficult. It can be easier to do a 24 volt battery system though.
We have a lot of solar pros that can argue with anything. They know a lot more than me as a rule.
First Bank:16 180 watt Grape Solar with FM80 controller and 3648 Inverter....Fullriver 8D AGM solar batteries. Second Bank/MacGyver Special: 10 165(?) watt BP Solar with Renogy MPPT 40A controller/ and Xantrex C-35 PWM controller/ and Morningstar PWM controller...Cotek 24V PSW inverter....forklift and diesel locomotive batteries -
softdown said:... know that Photowit rues the day day that he settled on 24 volt because it makes expansion more expensive and difficult. ...
Even then it was a close thing, as to whether it was better to replace the battery and inverter, $2500 + $1500, or live with what I had for 9-14 years until I would need to replace the battery and purchase a 24 v inverter large enough for the place and at least 1 extra charge controller $1500 + $500. I ended up living with the small cabin inverter and have now for 4 years.
Certainly not ideal, it will be a major expense shortly after I retire. I'm learning to live with-in the constraints of a 1800 watt inverter and an 1100 watt inverter that I turn on when doing outside work. I might yet put up my spare 1800 watt inverter and have a dedicated line for an air conditioner or water heater for sunny days. ...but that would require a separate line and a transfer switch and box.
It can be a pain running the hot water heater and forgetting and turning on the microwave. I likely pop off the inverter (over load and the inverter automatically shuts down) once a month during the hot months accidentally.
Softdown is right in my estimation for the rough break down of when it's advisable to move up to a larger voltage system. I had planned on a 3500-4000 watt inverter for this place. I will look toward this and a 48 volt system when I retire this battery. I have a 5000 watt array in place now, and will add a small south facing array and a dedicated hater heating array in the next little bit. I know I've been talking about this for a while, but have even cleaned off the porch to set up the drill press and band (or chop) saw to make the mounts, and have the lumber, wire, combiner box...
Home system 4000 watt (Evergreen) array standing, with 2 Midnite Classic Lites, Midnite E-panel, Magnum MS4024, Prosine 1800(now backup) and Exeltech 1100(former backup...lol), 660 ah 24v Forklift battery(now 10 years old). Off grid for 20 years (if I include 8 months on a bicycle).
- Assorted other systems, pieces and to many panels in the closet to not do more projects.
Categories
- All Categories
- 229 Forum & Website
- 137 Solar Forum News and Announcements
- 1.4K Solar News, Reviews, & Product Announcements
- 199 Solar Information links & sources, event announcements
- 898 Solar Product Reviews & Opinions
- 256 Solar Skeptics, Hype, & Scams Corner
- 22.5K Solar Electric Power, Wind Power & Balance of System
- 3.5K General Solar Power Topics
- 6.7K Solar Beginners Corner
- 1K PV Installers Forum - NEC, Wiring, Installation
- 2.1K Advanced Solar Electric Technical Forum
- 5.6K Off Grid Solar & Battery Systems
- 428 Caravan, Recreational Vehicle, and Marine Power Systems
- 1.1K Grid Tie and Grid Interactive Systems
- 654 Solar Water Pumping
- 816 Wind Power Generation
- 624 Energy Use & Conservation
- 619 Discussion Forums/Café
- 312 In the Weeds--Member's Choice
- 75 Construction
- 124 New Battery Technologies
- 108 Old Battery Tech Discussions
- 3.8K Solar News - Automatic Feed
- 3.8K Solar Energy News RSS Feed