Rigid mounted generator engine
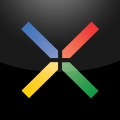
liamg
Registered Users Posts: 43 ✭✭
Hello,
I'm in a process of transforming a portable generator into a stationary one. I'm going to place it into a soundproofing large box, which is mounted on a pretty large outdoor concrete base.
I have already built a metal framework on that concrete base to acomodate the engine body but I wonder if I should keep the original engine elastic mounts or should I rigidly bolt it directly to the frame.
To be honest, I have actually mounted the engine without those elastic mounts and ran it for awhile. There was no sound/vibrations propagation at all (as I've just mentioned, that concrete base it's quite large) but I don't know if the engine will be affected by this lack of stretching.
Does anybody have any clue on this matter?
Comments
-
Purely guesswork, but I suspect the flex mounts are there for more than simply preventing sound and vibration from propagating. They may also prevent metal fatigue etc in the generator itself. For example, if a piston and surrounding block can move together to a degree, it would lessen the inertial stress resulting from any play between the two.Off-grid.
Main system ~4kw panels into 2xMNClassic150 370ah 48v bank 2xOutback 3548 inverter 120v + 240v autotransformer
Night system ~1kw panels into 1xMNClassic150 700ah 12v bank morningstar 300w inverter -
I guess you're right - that's what I was afraid of.
I already have a plan B though: I'll put some springs on the mounting bolts to allow the engine to "float". But.. it will only allow for unidirectional movement (up-down).
Should I keep the original rubber mounts then?? -
I run model airplane engines as a hobby. Some years ago, modelers started mounting the engines on flexible mounts to reduce transmitted vibration to the airframes. Most of these engines are single cylinder and vibrate quite a bit. Not ONE engine manufacturer recommends these flexible mountings preferring the engines to be mounted as rigidly as possible.
I'd be inclined to bolt that puppy down to a concrete base if I had the option.Island cottage solar system with appriximately 2500 watts of panels, 1kw facing southeast 1.3kw facing southwest 170watt ancient Arco's facing due south. All panels in parallel for a 24 volt system. Trace DR1524 MSW inverter which has performed flawlessly since 1994. Outback Flexmax 80 MPPT charge controller four 467A-h AGM batteries. Insignia 11.5 cubic foot electric fridge 1/4hp GSW piston pump. My 31st year. -
My generator shed has a 12" slab that the engine is firmly bolted to. If you can actually engineer a floating, vibration isolation mount, that would be great, but randomly trying motor and transmission mounts to see what works, will disappoint you. My backup generator has a isolation mount, maintenance cycle calls for mount replacements every 500 hours. At 3600 rpm it's stable, but shutdown and startup, it has oscillation nodes and flails wildly for a couple seconds as it spins through them.
Powerfab top of pole PV mount | Listeroid 6/1 w/st5 gen head | XW6048 inverter/chgr | Iota 48V/15A charger | Morningstar 60A MPPT | 48V, 800A NiFe Battery (in series)| 15, Evergreen 205w "12V" PV array on pole | Midnight ePanel | Grundfos 10 SO5-9 with 3 wire Franklin Electric motor (1/2hp 240V 1ph ) on a timer for 3 hr noontime run - Runs off PV ||
|| Midnight Classic 200 | 10, Evergreen 200w in a 160VOC array ||
|| VEC1093 12V Charger | Maha C401 aa/aaa Charger | SureSine | Sunsaver MPPT 15A
solar: http://tinyurl.com/LMR-Solar
gen: http://tinyurl.com/LMR-Lister , -
I forgot to mention that I'm taking about a Honda GX200 engine (200cc/6.5HP).
Many thanks for your kind support (though I really don't know what to do next).
Maybe an airplane (as I've read about the early Harley's choppers) have already some degree of free movement that allows the engine to stretch itself.
Bolting it firmly on a big concrete slab could be a completely different story. Does anyone have (seen) a genuine stationary generator (small engine) to confirm the actual mounting solution?
Any supporting literature/links would be nice. -
During my HVAC days, we mounted compressors on neoprene pads to absorb vibration from damaging components, metal fatigue and transmitting noise into the concrete. Also used similar ones, much larger to mount generators for the same reasons, they are just a pad with a hole, I personally would recommend using something, rather than nothing, it's the higher frequency vibrations which fatigue metal, linked are the ones we used, there are many others.
http://www.ecompressedair.com/accessories/vibration-pads.aspx
1500W, 6× Schutten 250W Poly panels , Schneider MPPT 60 150 CC, Schneider SW 2524 inverter, 400Ah LFP 24V nominal battery with Battery Bodyguard BMS
Second system 1890W 3 × 300W No name brand poly, 3×330 Sunsolar Poly panels, Morningstar TS 60 PWM controller, no name 2000W inverter 400Ah LFP 24V nominal battery with Daly BMS, used for water pumping and day time air conditioning.
5Kw Yanmar clone single cylinder air cooled diesel generator for rare emergency charging and welding. -
I couldn't find anything credible to indicate that rigid mounting causes wear or fatigue to the engine itself. Might even be that letting the engine vibrate freely on mounts causes more noise (like the flexible foam edges of a loudspeaker allow the cone to move, creating more movement and noise).
I am available for custom hardware/firmware development
-
Short article:
https://power.cummins.com/sites/default/files/literature/technicalpapers/PT-9008-AntiVibrationMount.pdfEngine driven generator sets produce vibrations, just as most machinery with moving and rotating parts. The transmission of these vibrations should me minimized to avoid nuisance from noise and vibration, as well as physical damage to the generator set itself and the structure supporting the generator set.-Bill
Near San Francisco California: 3.5kWatt Grid Tied Solar power system+small backup genset -
@BB.:
Thanks for posting that paper.
Anyway, I've read the entire article and your post twice but still don't get it: should I go with a rigid mounting or not?
> @BB. said:
>
>The transmission of these vibrations should me minimized to avoid nuisance from noise and vibration, as well as physical damage to the generator set itself and the structure supporting the generator set.
>
So the engine vibrations could actually damage the engine itself? As long as the engine will be safe, I do prefer to bolt it down to that concrete slab. My only intention is to reduce the engine vibration as it might affect the muffler, the fuel hose and so on.
@jonr:
Many thanks for your time. Neither I could find that piece of information (if a rigid mounting may cause wear or fatigue of the engine itself). -
@liamg
Since the Honda engine should be pretty smooth, I would think you could use floor mount rubber isolators. They are only about 5 to 10 dollars a set.
Rick4480W PV, MNE175DR-TR, MN Classic 150, Outback Radian GS4048A, Mate3, 51.2V 360AH nominal LiFePO4, Kohler Pro 5.2E genset. -
Okay, that's a nice piece of isolator, indeed. Anyway, I still have the original rubber mounts or I could make use of some steel springs BUT, then again:
May a rigid mounting cause wear or fatigue of the engine itself? -
To be honest, I am of mixed feelings too.
Soft mounts, the engine moves more. Fuel and electrical lines need flex joints.
Fixed mounts, then you worry that attach points get over stressed (engine castings, frames, motor to generator attachments, etc.).
My dad had an old 4 wheel drive with a 4 cylinder engine that was 1/2 of their 8 cylinder design. It vibrated terribly and shook everything off the engine at one time or another. Remember the generator bolts fracturing and having to tickle them out with a screw driver from the hole.
-BillNear San Francisco California: 3.5kWatt Grid Tied Solar power system+small backup genset -
[quote]@Estragon said:
For example, if a piston and surrounding block can move together to a degree, it would lessen the inertial stress resulting from any play between the two.[/quote]
That is the question: those engine vibrations help with the inertial stress or they're just a waste of energy?
@BB.:
Thanks for sharing your (dad) experiences.
Beside the fuel hose and the electrical lines, I'm more concerned about the new (oversized) muffler: it has a rigid connection with the engine and all those vibrations are amplified by its inertial mass thus putting an extra stress on the engine (chain reaction). -
A big issue with designing "mounts"... Generally you want mounts that are energy absorbing to a degree (such as neoprene). If not, you can get harmonics that can make (certain frequencies) of vibrations worse (i.e., when using steel springs, no energy dissipated, any resonant amplitudes increase).
Another short article:
https://www.cpower.com/PDF/InfoSheets/22.pdf1.0 IntroductionI guess--After thinking about the issue--I would not hard mount a genset to a concrete pad. Other than transmitting noise/pressure waves in the soil (if an issue where you are), I would worry about the genset "pounding" out the J-Bolt anchors in the concrete (if the forces/vibrations are great enough).
An engine driven generator system is subjected to vibration generated by the reciprocating forces within the
engine. A system designer will use vibration isolators to prevent excessive vibration being transmitted to other
components and the surroundings where the unit is installed.
This information sheet details the various types of vibration isolators used to protect a generator set’s
surroundings and the two types of vibration found in a system.
Here is a detailed article about installing a CAT sized genset (concrete pad, etc.):
https://s7d2.scene7.com/is/content/Caterpillar/CM20160713-53120-50907
One quick piece of information from the article--Thermal expansion of the geset vs the hard mounting to the pad could cause stress fractures in the concrete (smaller gensets, less of a problem, probably). Flexible mountings are helpful for this issue.
-Bill
Near San Francisco California: 3.5kWatt Grid Tied Solar power system+small backup genset -
FWIW, I have a 4kw Onan diesel generator mounted on a wooden pallet with rubber feet which is screwed into a concrete pad. It has rubber hoses between the copper supply lines, and a flexible stainless steel exhaust connection to muffler. It bucks enough when starting and stopping, and vibrates enough while running, that I'm not sure how long a fixed mount would last.
It's circa 1983, and runs fine. Only problem I've had with it is a fuse holder that got old and brittle.
The article Bill linked to doesn't explicitly say what the issue is (that I saw), but does mention damage to the generator itself if not damped in some way.
I also have a little honda. It has rubber feet too, but doesn't vibrate as much. If I mounted it permanently, I'd put rubber feet on the mount, because I'm not smart enough to out-think the engineers that put rubber feet on it in the first place.Off-grid.
Main system ~4kw panels into 2xMNClassic150 370ah 48v bank 2xOutback 3548 inverter 120v + 240v autotransformer
Night system ~1kw panels into 1xMNClassic150 700ah 12v bank morningstar 300w inverter -
The problem with those engineers is that they have designed a PORTABLE product.
By example, I have a spare B&S generator (1.4kW) which has a small problem: it's walking alone!It's like a baby toddler: you never find it where you left it.
There is an explanation though: its engine is rigidly bolted to the frame and the frame itself has only three little rubber feet.
That's it, for a portable device, one needs to isolate those engine vibrations from the frame to avoid the walking issue.
And, for now, I still believe this is the only reason of using those rubber mounts (on a portable generator).
@BB.:
The J-Bolt concrete anchors that I'm using are very strong - there's no chance of damage. I'm only worried about the engine itself. -
Harmonic balancers, dual inertia flywheels, counter rotating ballance shafts, isolation dampers, rubber mounts, flex couplings, hydraulic mounts, the list goes on, all designed to reduce vibration or smooth out the inherent issues found on reciprocating engines, or compressors for that matter. Every time the piston is at top (or bottom) dead center it comes to a complete stop, causing a pulse, this, depending on rotational speed is happening many times per second, smooth running engines, such as a V16, tend to cancel these pulses to a large degree by a pulse in the opposite direction, but never 100%. Take the generators rubber mounts off, place on a concrete floor, unbolted, start it up, if it remains perfectly still and dose not creep around, it is close to perfect in terms of ballance, or vibration. Obviously it will not be perfect, so bolting to a concrete slab without isolation pads, of some description, would mean these vibrations would be transmitted somewhere, where depends on frequency and harmonics, but my guess is the concrete won't be absorbing much.
These are only my opinions based on experience and study, FWIW, YMMV etc.1500W, 6× Schutten 250W Poly panels , Schneider MPPT 60 150 CC, Schneider SW 2524 inverter, 400Ah LFP 24V nominal battery with Battery Bodyguard BMS
Second system 1890W 3 × 300W No name brand poly, 3×330 Sunsolar Poly panels, Morningstar TS 60 PWM controller, no name 2000W inverter 400Ah LFP 24V nominal battery with Daly BMS, used for water pumping and day time air conditioning.
5Kw Yanmar clone single cylinder air cooled diesel generator for rare emergency charging and welding. -
Once again, I'm really not worried about the concrete anchors. There are plenty of them and they are oversized, too.
Like I did mention in the first post, I already ran the generator for few minutes (using a rigid mount) and there was no signs of stress for those concrete anchors.
Btw, the engine were running pretty smooth in this rigid mount position. I just don't know if it hurts inside.. -
Have you tried looking for similarly sized units that are meant to be stationary? might get some clues there...
KID #51B 4s 140W to 24V 900Ah C&D AGM
CL#29032 FW 2126/ 2073/ 2133 175A E-Panel WBjr, 3 x 4s 140W to 24V 900Ah C&D AGM
Cotek ST1500W 24V Inverter,OmniCharge 3024,
2 x Cisco WRT54GL i/c DD-WRT Rtr & Bridge,
Eu3/2/1000i Gens, 1680W & E-Panel/WBjr to come, CL #647 asleep
West Chilcotin, BC, Canada
Categories
- All Categories
- 229 Forum & Website
- 137 Solar Forum News and Announcements
- 1.4K Solar News, Reviews, & Product Announcements
- 199 Solar Information links & sources, event announcements
- 898 Solar Product Reviews & Opinions
- 256 Solar Skeptics, Hype, & Scams Corner
- 22.5K Solar Electric Power, Wind Power & Balance of System
- 3.5K General Solar Power Topics
- 6.7K Solar Beginners Corner
- 1K PV Installers Forum - NEC, Wiring, Installation
- 2.1K Advanced Solar Electric Technical Forum
- 5.6K Off Grid Solar & Battery Systems
- 428 Caravan, Recreational Vehicle, and Marine Power Systems
- 1.1K Grid Tie and Grid Interactive Systems
- 654 Solar Water Pumping
- 816 Wind Power Generation
- 624 Energy Use & Conservation
- 619 Discussion Forums/Café
- 312 In the Weeds--Member's Choice
- 75 Construction
- 124 New Battery Technologies
- 108 Old Battery Tech Discussions
- 3.8K Solar News - Automatic Feed
- 3.8K Solar Energy News RSS Feed