Series Wiring In Sets of Three & What Charge Controller to Buy

gregbyst
Registered Users Posts: 38 ✭✭
Hello,
How do I wire 9 panels in 3 sets of 3, wired in series, and then the 3 sets wired together in parallel? What voltage and current do I use to add up to determine the correct charge controller? The Vmpp or the Voc? What current, the Impp or the Isc?
So for my fifth wheel I am going to have 9 260 watt panels and 3 130 watt panels. The specs are in the pictures. I was told that in order to charge my 24 volt battery bank I need to wire my panels In series to make the voltage high enough to get the most bang for my buck out of the panels and the available sunlight. The person who told me this was a tech support person from Midnite Solar. I Was calling to see which solar combiner would work for me and asking about the MNPV-12. Since I have an un-even number of panels I need to wire in sets of three, according to him, and then wire those sets in parallel.
The plan is now to get the MNPV-6 because I will have 3 of the strings used by the 9 panel (260 watt) group and the other 3 strings used by each of the panels in my 3 panel (130 watt group). I will have two separate charge controllers for my two different groups.
I learned how to wire pairs of panels in series and parallel, but how do I wire in series? Because of this oversight, I bought a charge controller with only up to 92 VDC and rated for 100amps. So now I am wondering which numbers to go by when looking at the charge controller I'm going to get. On here I found a Victron (screenshot of specs below) but im not sure if it's what I need. Can someone tell me which numbers I need to use off the panels to calculate what the charge controller can handle?
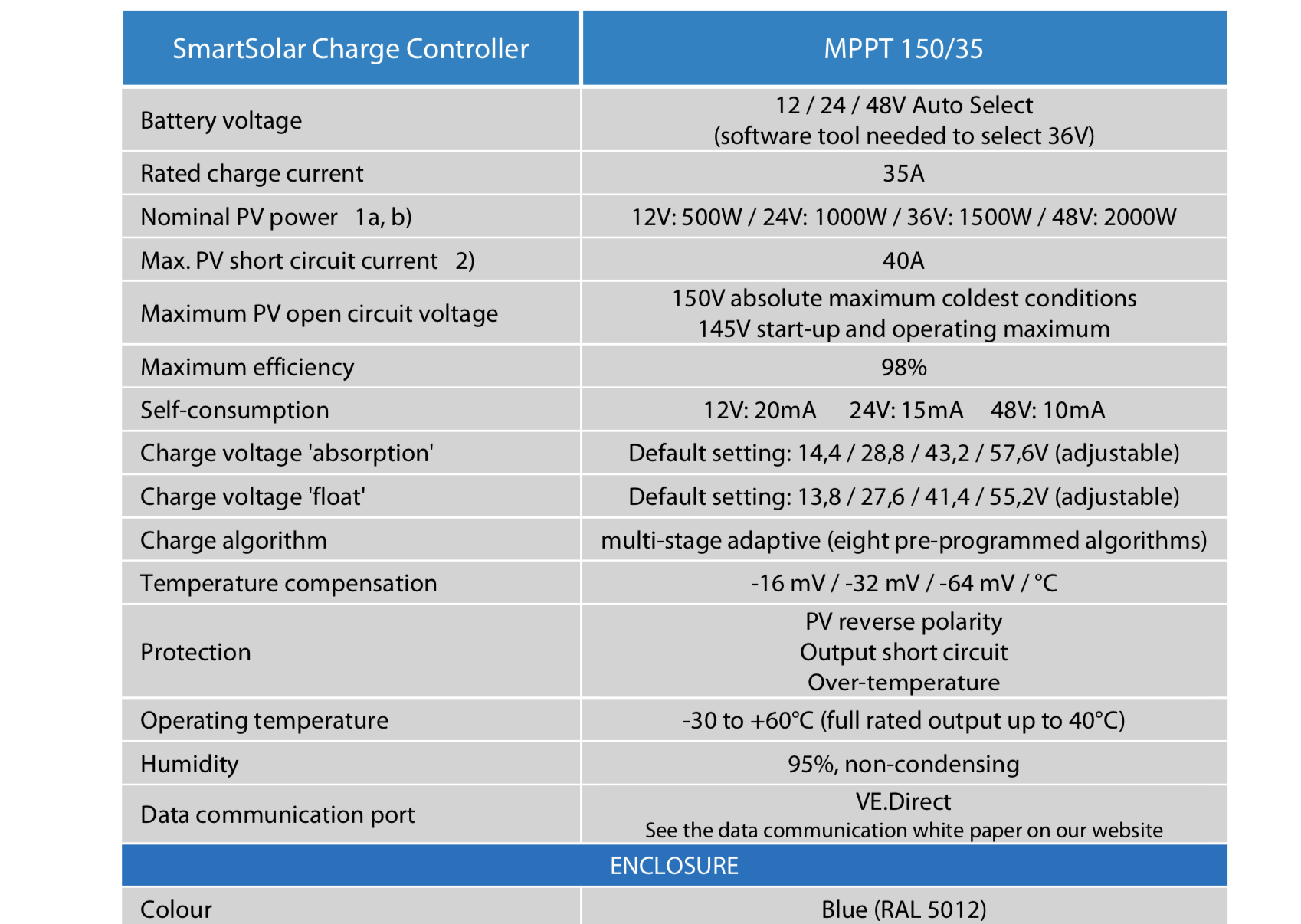
.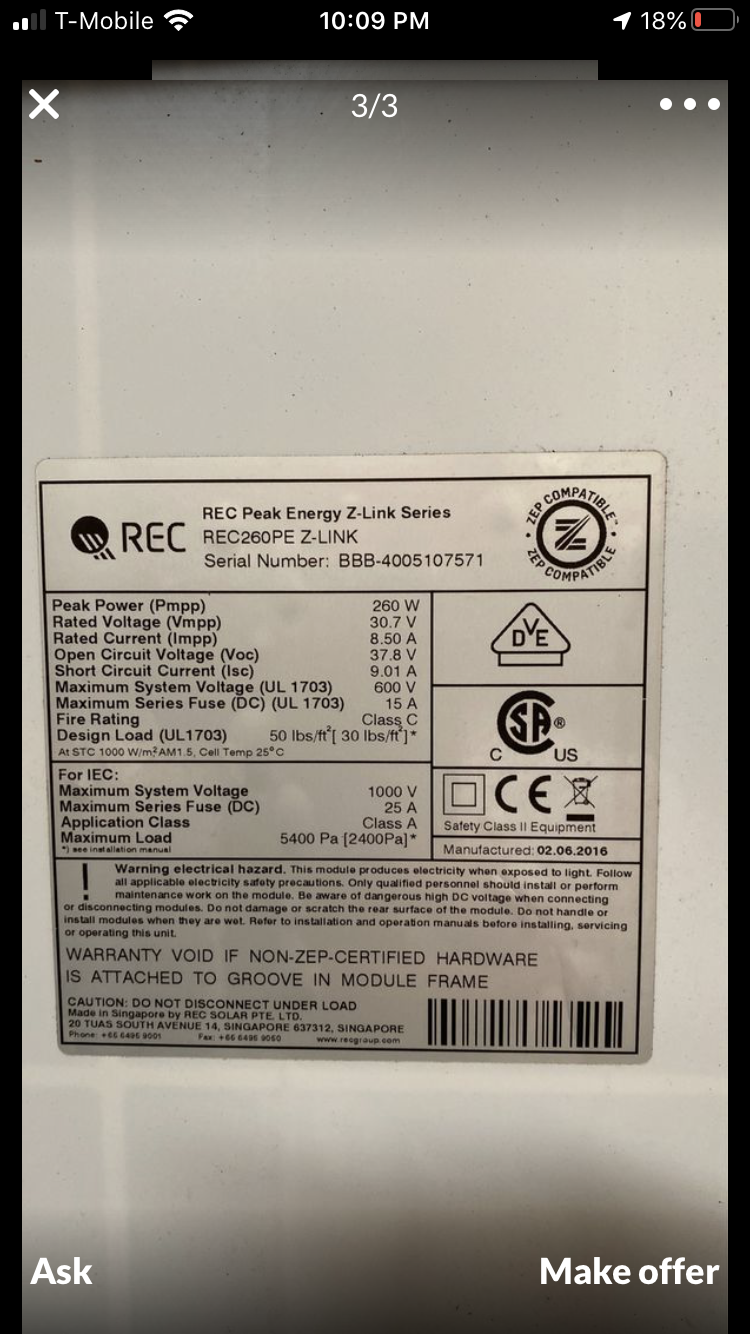
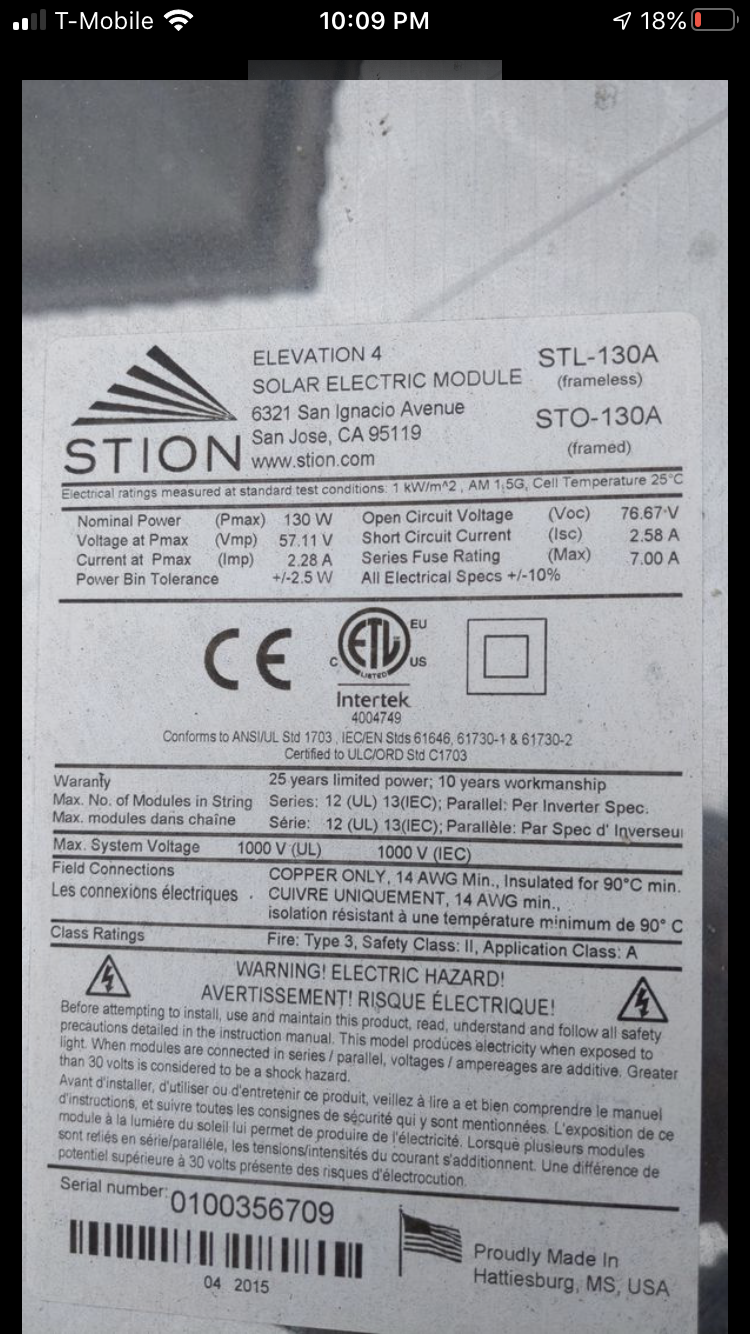
How do I wire 9 panels in 3 sets of 3, wired in series, and then the 3 sets wired together in parallel? What voltage and current do I use to add up to determine the correct charge controller? The Vmpp or the Voc? What current, the Impp or the Isc?
So for my fifth wheel I am going to have 9 260 watt panels and 3 130 watt panels. The specs are in the pictures. I was told that in order to charge my 24 volt battery bank I need to wire my panels In series to make the voltage high enough to get the most bang for my buck out of the panels and the available sunlight. The person who told me this was a tech support person from Midnite Solar. I Was calling to see which solar combiner would work for me and asking about the MNPV-12. Since I have an un-even number of panels I need to wire in sets of three, according to him, and then wire those sets in parallel.
The plan is now to get the MNPV-6 because I will have 3 of the strings used by the 9 panel (260 watt) group and the other 3 strings used by each of the panels in my 3 panel (130 watt group). I will have two separate charge controllers for my two different groups.
I learned how to wire pairs of panels in series and parallel, but how do I wire in series? Because of this oversight, I bought a charge controller with only up to 92 VDC and rated for 100amps. So now I am wondering which numbers to go by when looking at the charge controller I'm going to get. On here I found a Victron (screenshot of specs below) but im not sure if it's what I need. Can someone tell me which numbers I need to use off the panels to calculate what the charge controller can handle?
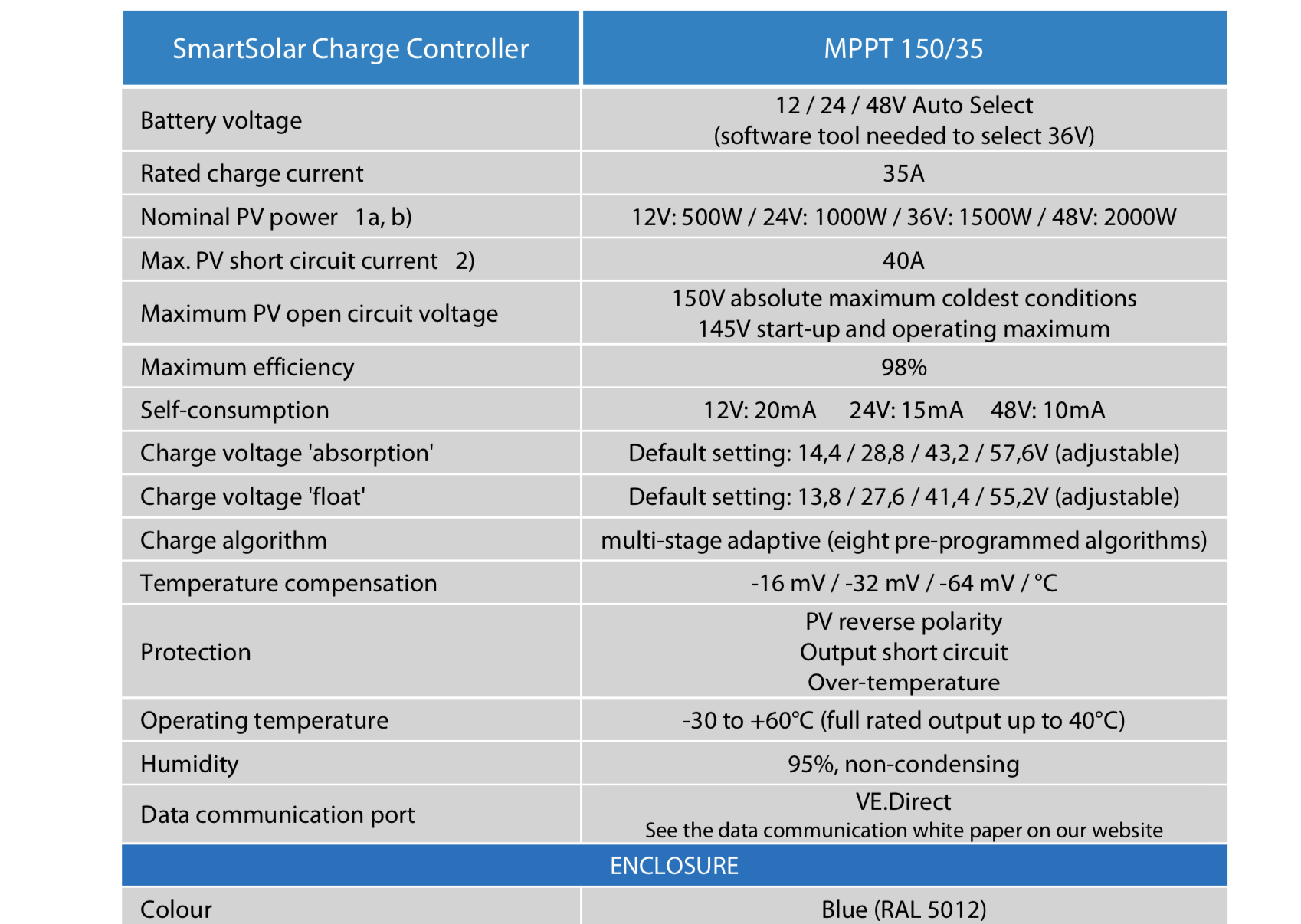
.
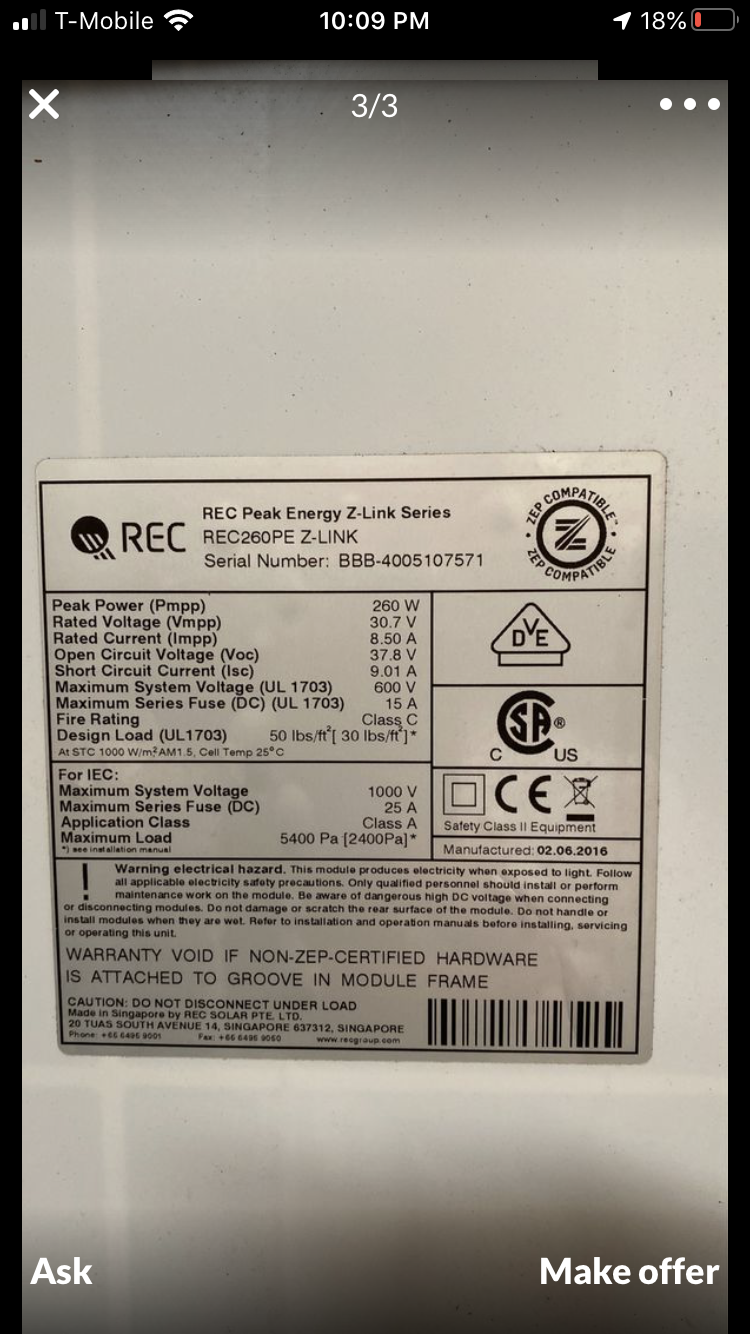
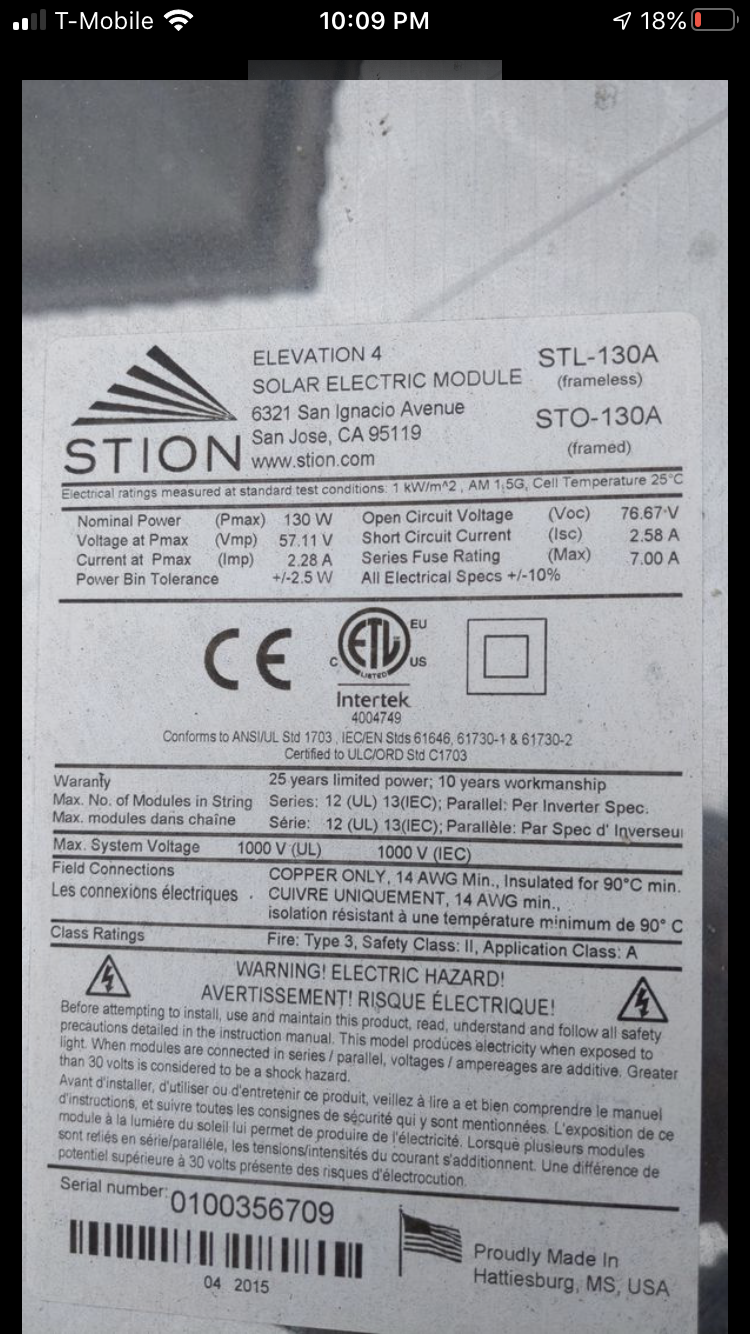
- 4 of the 12 volt, 200ah AGM renogy batteries (I sent a screenshot of the specs above).
- 150/60 MPPT Epever Charge Controller
- 3000 watt (9000 peak) inverter/charger/auto-transfer switch
- PV array of 6 260 watt, 30.7 Vmpp, 8.5 Impp.
- Battery Shunt Monitor (https://www.amazon.com/gp/product/B07FGFFHC6/ref=ppx_yo_dt_b_asin_title_o07_s00?ie=UTF8&psc=1)
Also, I live in a fifth wheel!
- 150/60 MPPT Epever Charge Controller
- 3000 watt (9000 peak) inverter/charger/auto-transfer switch
- PV array of 6 260 watt, 30.7 Vmpp, 8.5 Impp.
- Battery Shunt Monitor (https://www.amazon.com/gp/product/B07FGFFHC6/ref=ppx_yo_dt_b_asin_title_o07_s00?ie=UTF8&psc=1)
Also, I live in a fifth wheel!
Comments
-
The Voc would be used to determine the maximum voltage for the controller ( no current flow )
The Isc is the maximum current flow (no voltage )
The Imp is the current at maximum power ( voltage and current at optimal value )
Serial connection is daisy chain connecting positive to negative with the MC4 connectors, voltage adds, current remains the same as a single panel. Parrallel is the opposite all positives are connected together, all negatives together, voltage is the same as a single panel, current is multiplied by the number of panels in parallel.
Important thing to consider is when series connected the maximum voltage will be affected by temperature, the colder it is the higher the voltage.
To offer advice on the best arrangement or what equipment is required, the nominal voltage is needed along with the battery capacity.
Most importantly, it's better to design a system to support the loads rather than the other way around, which most often leads to dissapointment, start with the loads because everything else needed depends on that.
Which of the panels do you intend to use, the top picture would be the most flexible type.1500W, 6× Schutten 250W Poly panels , Schneider MPPT 60 150 CC, Schneider SW 2524 inverter, 400Ah LFP 24V nominal battery with Battery Bodyguard BMS
Second system 1890W 3 × 300W No name brand poly, 3×330 Sunsolar Poly panels, Morningstar TS 60 PWM controller, no name 2000W inverter 400Ah LFP 24V nominal battery with Daly BMS, used for water pumping and day time air conditioning.
5Kw Yanmar clone single cylinder air cooled diesel generator for rare emergency charging and welding. -
mcgivor said:The Voc would be used to determine the maximum voltage for the controller ( no current flow )
The Isc is the maximum current flow (no voltage )
The Imp is the current at maximum power ( voltage and current at optimal value )
Serial connection is daisy chain connecting positive to negative with the MC4 connectors, voltage adds, current remains the same as a single panel. Parrallel is the opposite all positives are connected together, all negatives together, voltage is the same as a single panel, current is multiplied by the number of panels in parallel.
Important thing to consider is when series connected the maximum voltage will be affected by temperature, the colder it is the higher the voltage.
To offer advice on the best arrangement or what equipment is required, the nominal voltage is needed along with the battery capacity.
Most importantly, it's better to design a system to support the loads rather than the other way around, which most often leads to dissapointment, start with the loads because everything else needed depends on that.
Which of the panels do you intend to use, the top picture would be the most flexible type.
When Series connecting then, I just use the MC4 connector that combined two panels in series and then combine an additional panel with those connecter for a triple series connection?
In regards to the loads, I have taken advantage of all the possible space I have on my fifth wheel and I am going to construct a ground array. In total my nominal power should be 2, 370 watts. That's all I can fit. I have a generator as well for super hot days where I want to continually run the AC.
My battery bank will consist of 4 200 ah AGM batteries wired in series and then parallel to be a 24 volt, 400 ah bank (I know that effectively it's only 200 ah since I can't drain below the halfway point without hurting the batteries).
I would like more batteries but this is what I can afford.
Thank you so much for the info about the temperature and voltage! What kind of voltage buffer should I use when purchasing my charge controller? I plan on traveling around to colder places, but currently am in Long Beach CA.
I plan to use both panels. 9 of the first one with 6 mounted on the roof and the remainder as a ground array and 3 of the second one also mounted on the roof. I was going get a separate charge controller for the other 3 and wire them all in parallel. Then put both panels to the MNPV-6 solar combiner box before going to their designated charge controller.- 4 of the 12 volt, 200ah AGM renogy batteries (I sent a screenshot of the specs above).
- 150/60 MPPT Epever Charge Controller
- 3000 watt (9000 peak) inverter/charger/auto-transfer switch
- PV array of 6 260 watt, 30.7 Vmpp, 8.5 Impp.
- Battery Shunt Monitor (https://www.amazon.com/gp/product/B07FGFFHC6/ref=ppx_yo_dt_b_asin_title_o07_s00?ie=UTF8&psc=1)
Also, I live in a fifth wheel! -
gregbyst said:Thank you. Is the Isc what I use to determine maximum amperage for the charge controller?gregbyst said:Also, does the nominal voltage for the charge controller (as listed in the specs for the Victron above) need to match the nominal voltage of my combined panels? Since watts= volts x amps, why isn't the nominal power for the charge controller 40 (amps) x 150 (volts) = 5,800?
Perhaps easiest to think of your array by it's output and figure out your charge controllers needs;
You have 9 - 260 watt panels for a (9x260=) 2340 watt array.
They are configured in strings of 3 so for each string the VMP will be (3x30.7v=) 92.1V and the IMP will remain the same as 8.5 amps
For the three strings combined in parallel the voltage will remain the same and the IMP will be (3x8.5amps=)25.5 amps.
In addition you will want to know the max voc, so 3x37.8v= 113.4 volts
So you have an array producing 2340 watts total as 92.1 volts with an IMP of 25.5 amps (92.1x25.5=2348..watts rounding errors)
You have a 24 volt battery bank, of 400 amphours. Do you know the max charging capacity of your batteries? Renogy have a pretty high charge rate, not sure others do... but looks like you could charge up to 40% of capacity, I'd certainly shoot for something less, even if you use a temperature probe.
You'll be moving around so we don't know your location for max safe VOC as the VOC will reach higher in extreme low temps.
So something that can got to at least 130v VOC, and handle charging for the 24 volt battery bank, since you are using MPPT you can just divide the array wattage by the charging voltage or 2340/24=98.5amps, A lot of reasons you won't approach this number unless there is an unusually situation, panels only produce about 75% of their name plate unless very cold, batteries start charging at less than ideal angles to the sun, as the battery reaches near full it will accept less current. All the major MPPT solar chargers can be 'overpaneled' it's even suggested because the panels typically produce 75-80% of their name plate, that to be most cost effective that you do over panel somewhat.
Home system 4000 watt (Evergreen) array standing, with 2 Midnite Classic Lites, Midnite E-panel, Magnum MS4024, Prosine 1800(now backup) and Exeltech 1100(former backup...lol), 660 ah 24v Forklift battery(now 10 years old). Off grid for 20 years (if I include 8 months on a bicycle).
- Assorted other systems, pieces and to many panels in the closet to not do more projects. -
Photowhit said:gregbyst said:Thank you. Is the Isc what I use to determine maximum amperage for the charge controller?gregbyst said:Also, does the nominal voltage for the charge controller (as listed in the specs for the Victron above) need to match the nominal voltage of my combined panels? Since watts= volts x amps, why isn't the nominal power for the charge controller 40 (amps) x 150 (volts) = 5,800?
Perhaps easiest to think of your array by it's output and figure out your charge controllers needs;
You have 9 - 260 watt panels for a (9x260=) 2340 watt array.
They are configured in strings of 3 so for each string the VMP will be (3x30.7v=) 92.1V and the IMP will remain the same as 8.5 amps
For the three strings combined in parallel the voltage will remain the same and the IMP will be (3x8.5amps=)25.5 amps.
In addition you will want to know the max voc, so 3x37.8v= 113.4 volts
So you have an array producing 2340 watts total as 92.1 volts with an IMP of 25.5 amps (92.1x25.5=2348..watts rounding errors)
You have a 24 volt battery bank, of 400 amphours. Do you know the max charging capacity of your batteries? Renogy have a pretty high charge rate, not sure others do... but looks like you could charge up to 40% of capacity, I'd certainly shoot for something less, even if you use a temperature probe.
You'll be moving around so we don't know your location for max safe VOC as the VOC will reach higher in extreme low temps.
So something that can got to at least 130v VOC, and handle charging for the 24 volt battery bank, since you are using MPPT you can just divide the array wattage by the charging voltage or 2340/24=98.5amps, A lot of reasons you won't approach this number unless there is an unusually situation, panels only produce about 75% of their name plate unless very cold, batteries start charging at less than ideal angles to the sun, as the battery reaches near full it will accept less current. All the major MPPT solar chargers can be 'overpaneled' it's even suggested because the panels typically produce 75-80% of their name plate, that to be most cost effective that you do over panel somewhat.
My batteries are renogy ones. I don't know their charging information- nothing came with the batteries like a manual. These are the ones I got. I can still return them if there's a better deal out there, but I can't really afford anything more.
https://www.homedepot.com/p/Renogy-Deep-Cycle-AGM-Battery-12-Volt-200Ah-for-Solar-Panels-Solar-System-BATT-AGM12-200/303413126?source=shoppingads&locale=en-US&mtc=Shopping-B-F_Brand-G-Multi-NA-Multi-NA-Feed-PLA-NA-NA-Catchall_PLA&cm_mmc=Shopping-B-F_Brand-G-Multi-NA-Multi-NA-Feed-PLA-NA-NA-Catchall_PLA-71700000014585962-58700001236285396-92700052972852848&gclid=Cj0KCQjwt4X8BRCPARIsABmcnOqNMS2el-hIPwnoz_-SUqNO_Qnq6AfV-ut1wBI-Adhwn1_l19-_B_caAv9PEALw_wcB&gclsrc=aw.ds
So with the over paneling thing, I can get a charge controller that is rated less than the total array wattage?- 4 of the 12 volt, 200ah AGM renogy batteries (I sent a screenshot of the specs above).
- 150/60 MPPT Epever Charge Controller
- 3000 watt (9000 peak) inverter/charger/auto-transfer switch
- PV array of 6 260 watt, 30.7 Vmpp, 8.5 Impp.
- Battery Shunt Monitor (https://www.amazon.com/gp/product/B07FGFFHC6/ref=ppx_yo_dt_b_asin_title_o07_s00?ie=UTF8&psc=1)
Also, I live in a fifth wheel! -
found this online. Am I looking for the "max charge current" (60 amps)?
- 4 of the 12 volt, 200ah AGM renogy batteries (I sent a screenshot of the specs above).
- 150/60 MPPT Epever Charge Controller
- 3000 watt (9000 peak) inverter/charger/auto-transfer switch
- PV array of 6 260 watt, 30.7 Vmpp, 8.5 Impp.
- Battery Shunt Monitor (https://www.amazon.com/gp/product/B07FGFFHC6/ref=ppx_yo_dt_b_asin_title_o07_s00?ie=UTF8&psc=1)
Also, I live in a fifth wheel! -
Yes, charging current of about 30% of capacity. at 60 amps, so figure 120 amps at 400 amps 24 volt battery. I'd be sure to use a temperature probe! As I said, you will rarely have and need the max output at one time, but it will be nice to know you may get some charging or at least staying even while running your AC on lower settings.
You might as well use Midnight classic's array sizing tool and see how your numbers work out using their Classic 150. I LOVE their charge controllers, but I WOULD NOT BUY ONE for an RV! They have a lot of fan noise that might drive you crazy. Mine live outside in a power center for my home.
www.midnitesolar.com/sizingTool/
I believe the Schneider 60/150 or MorningStar's MPPT 60 TriStar are the economical choices at around $500-600. You will be pushing near maximum capacity on these often in the heat running air conditioning all day. Figure 75% of 2340 watt array, charging at 27-29 volts or 2340 x .75 /28 volts = 62 amps .
Outback FM80 has a fan as well, as the Midnite 150, both would better handle the load, but might drive you crazy!
The higher end Schneider Context MPPT 80 I don't think has a fan, but is $1000 and designed for higher voltage input.
Victron makes a 150/70 (70 amp) I heard good things about the company, but mostly in smaller installs, I have no feedback about this unit. I do think they ae fanless.
So you are reading me thinking...lol.
I might search RV groups and ask about noise from the Outback Flexmax 80 (FM80). I've read enough about Midnite's turbo fan driving people nuts, I'd hate to recommend it. Don't get me wrong, I own 3 and am a happy customer!Home system 4000 watt (Evergreen) array standing, with 2 Midnite Classic Lites, Midnite E-panel, Magnum MS4024, Prosine 1800(now backup) and Exeltech 1100(former backup...lol), 660 ah 24v Forklift battery(now 10 years old). Off grid for 20 years (if I include 8 months on a bicycle).
- Assorted other systems, pieces and to many panels in the closet to not do more projects. -
Photowhit said:Yes, charging current of about 30% of capacity. at 60 amps, so figure 120 amps at 400 amps 24 volt battery. I'd be sure to use a temperature probe! As I said, you will rarely have and need the max output at one time, but it will be nice to know you may get some charging or at least staying even while running your AC on lower settings.
You might as well use Midnight classic's array sizing tool and see how your numbers work out using their Classic 150. I LOVE their charge controllers, but I WOULD NOT BUY ONE for an RV! They have a lot of fan noise that might drive you crazy. Mine live outside in a power center for my home.
www.midnitesolar.com/sizingTool/
I believe the Schneider 60/150 or MorningStar's MPPT 60 TriStar are the economical choices at around $500-600. You will be pushing near maximum capacity on these often in the heat running air conditioning all day. Figure 75% of 2340 watt array, charging at 27-29 volts or 2340 x .75 /28 volts = 62 amps .
Outback FM80 has a fan as well, as the Midnite 150, both would better handle the load, but might drive you crazy!
The higher end Schneider Context MPPT 80 I don't think has a fan, but is $1000 and designed for higher voltage input.
Victron makes a 150/70 (70 amp) I heard good things about the company, but mostly in smaller installs, I have no feedback about this unit. I do think they ae fanless.
So you are reading me thinking...lol.
I might search RV groups and ask about noise from the Outback Flexmax 80 (FM80). I've read enough about Midnite's turbo fan driving people nuts, I'd hate to recommend it. Don't get me wrong, I own 3 and am a happy customer!
Why is it that I need a temperature probe/monitor on my battery bank again? Why is there risk of them heating up? Because the charge controller may fail or something?
And again, with the overpaneling thing you mentioned, I will be okay purchasing a charge controller that is rated for less than my combined nominal power since it will only generate roughly 80% of the power? So that would be 1,872 watts.
So for example, my charge controller could *generously* be rated for 2000 watts, 130 VOC (for the temp changes that will drive up the voltage), and rated at 100 amps? Or am I getting this wrong and I need my total wattage to be within range of the charge controller? Will it damage if it goes over it sometimes, or will it just not accept the extra energy?- 4 of the 12 volt, 200ah AGM renogy batteries (I sent a screenshot of the specs above).
- 150/60 MPPT Epever Charge Controller
- 3000 watt (9000 peak) inverter/charger/auto-transfer switch
- PV array of 6 260 watt, 30.7 Vmpp, 8.5 Impp.
- Battery Shunt Monitor (https://www.amazon.com/gp/product/B07FGFFHC6/ref=ppx_yo_dt_b_asin_title_o07_s00?ie=UTF8&psc=1)
Also, I live in a fifth wheel! -
gregbyst said:How did you learn all this stuff btw?gregbyst said:Why is it that I need a temperature probe/monitor on my battery bank again? Why is there risk of them heating up? Because the charge controller may fail or something?gregbyst said:And again, with the overpaneling thing you mentioned, I will be okay purchasing a charge controller that is rated for less than my combined nominal power since it will only generate roughly 80% of the power? So that would be 1,872 watts.
So for example, my charge controller could *generously* be rated for 2000 watts, 130 VOC (for the temp changes that will drive up the voltage), and rated at 100 amps? Or am I getting this wrong and I need my total wattage to be within range of the charge controller? Will it damage if it goes over it sometimes, or will it just not accept the extra energy?
I encourage you to plug your numbers into the Midnite array sizing tool, it will give you some idea. The people at Midnite Started Outback (which created one of the first higher current MPPT controllers)
I'm not sure what your plans are for an inverter, both Schneider and Outback make integrated systems which might be a good fit for you. Sounds like you intend to run some pretty high loads and want an integrated generator.
@Dave Angelini has installed many integrated systems on homes, and might offer some ideas. He knows Schneider equipment quite well! The 9 panel setup is just a bit limiting, won't fit all 9 on the high voltage Schneider and may waste some on the 60 amp.
@Marc Kurth knows and understands AGM batteries, and might address their use in confined places and using a temperature probe...
Home system 4000 watt (Evergreen) array standing, with 2 Midnite Classic Lites, Midnite E-panel, Magnum MS4024, Prosine 1800(now backup) and Exeltech 1100(former backup...lol), 660 ah 24v Forklift battery(now 10 years old). Off grid for 20 years (if I include 8 months on a bicycle).
- Assorted other systems, pieces and to many panels in the closet to not do more projects. -
@gregbyst said.
Why is it that I need a temperature probe/monitor on my battery bank again? Why is there risk of them heating up? Because the charge controller may fail or something?
The remote temperature sensor ( RTS ) provides information to the controller to modulate the charging voltage depending on the temperature of the battery itself. The sensor is typically positioned half way down a battery preferably in the middle of the bank insulated from ambient air with styrofoam or equivalent material.
Lead acid batteries have a nominal operating temperature of 25°C, however the actual temperature may be higher or lower depending on influences such as charging, dischargeing or ambient temperature swings. As battery temperature rises above 25°C the required charging voltage needs to be reduced to prevent overcharging which promotes gassing, similarly as temperature drops below nominal the charging voltage needs to be increased to prevent undercharging.
For a 24V nominal bank the controller will compensate by adjusting the charging voltage 0.060 V for every °C so for example if the controller were set at 28.8V bulk/absorb, the temperature compensated value at 35°C would be 28.2V, conversely at 15°C the compensated value would be 29.2V, using Morningstar correction values, some other controllers may vary slightly but all will be close.
The use of a RTS is particularly important with AGM batteries in non climate controlled environments, they, unlike the flooded type LA batteries, cannot tolerate overcharging.1500W, 6× Schutten 250W Poly panels , Schneider MPPT 60 150 CC, Schneider SW 2524 inverter, 400Ah LFP 24V nominal battery with Battery Bodyguard BMS
Second system 1890W 3 × 300W No name brand poly, 3×330 Sunsolar Poly panels, Morningstar TS 60 PWM controller, no name 2000W inverter 400Ah LFP 24V nominal battery with Daly BMS, used for water pumping and day time air conditioning.
5Kw Yanmar clone single cylinder air cooled diesel generator for rare emergency charging and welding. -
mcgivor said:@gregbyst said.
Why is it that I need a temperature probe/monitor on my battery bank again? Why is there risk of them heating up? Because the charge controller may fail or something?
The remote temperature sensor ( RTS ) provides information to the controller to modulate the charging voltage depending on the temperature of the battery itself. The sensor is typically positioned half way down a battery preferably in the middle of the bank insulated from ambient air with styrofoam or equivalent material.
Lead acid batteries have a nominal operating temperature of 25°C, however the actual temperature may be higher or lower depending on influences such as charging, dischargeing or ambient temperature swings. As battery temperature rises above 25°C the required charging voltage needs to be reduced to prevent overcharging which promotes gassing, similarly as temperature drops below nominal the charging voltage needs to be increased to prevent undercharging.
For a 24V nominal bank the controller will compensate by adjusting the charging voltage 0.060 V for every °C so for example if the controller were set at 28.8V bulk/absorb, the temperature compensated value at 35°C would be 28.2V, conversely at 15°C the compensated value would be 29.2V, using Morningstar correction values, some other controllers may vary slightly but all will be close.
The use of a RTS is particularly important with AGM batteries in non climate controlled environments, they, unlike the flooded type LA batteries, cannot tolerate overcharging.- 4 of the 12 volt, 200ah AGM renogy batteries (I sent a screenshot of the specs above).
- 150/60 MPPT Epever Charge Controller
- 3000 watt (9000 peak) inverter/charger/auto-transfer switch
- PV array of 6 260 watt, 30.7 Vmpp, 8.5 Impp.
- Battery Shunt Monitor (https://www.amazon.com/gp/product/B07FGFFHC6/ref=ppx_yo_dt_b_asin_title_o07_s00?ie=UTF8&psc=1)
Also, I live in a fifth wheel! -
Photowhit said:gregbyst said:How did you learn all this stuff btw?gregbyst said:Why is it that I need a temperature probe/monitor on my battery bank again? Why is there risk of them heating up? Because the charge controller may fail or something?gregbyst said:And again, with the overpaneling thing you mentioned, I will be okay purchasing a charge controller that is rated for less than my combined nominal power since it will only generate roughly 80% of the power? So that would be 1,872 watts.
So for example, my charge controller could *generously* be rated for 2000 watts, 130 VOC (for the temp changes that will drive up the voltage), and rated at 100 amps? Or am I getting this wrong and I need my total wattage to be within range of the charge controller? Will it damage if it goes over it sometimes, or will it just not accept the extra energy?
I encourage you to plug your numbers into the Midnite array sizing tool, it will give you some idea. The people at Midnite Started Outback (which created one of the first higher current MPPT controllers)
I'm not sure what your plans are for an inverter, both Schneider and Outback make integrated systems which might be a good fit for you. Sounds like you intend to run some pretty high loads and want an integrated generator.
@Dave Angelini has installed many integrated systems on homes, and might offer some ideas. He knows Schneider equipment quite well! The 9 panel setup is just a bit limiting, won't fit all 9 on the high voltage Schneider and may waste some on the 60 amp.
@Marc Kurth knows and understands AGM batteries, and might address their use in confined places and using a temperature probe...
- What is the "output current" you mentioned that most MPPT charge controllers can limit? Is this the Imp?
- Do all MPPT charge controller's have an input section for the battery temp. probe and the capability of adjusting the charging current based on the detected temp?- 4 of the 12 volt, 200ah AGM renogy batteries (I sent a screenshot of the specs above).
- 150/60 MPPT Epever Charge Controller
- 3000 watt (9000 peak) inverter/charger/auto-transfer switch
- PV array of 6 260 watt, 30.7 Vmpp, 8.5 Impp.
- Battery Shunt Monitor (https://www.amazon.com/gp/product/B07FGFFHC6/ref=ppx_yo_dt_b_asin_title_o07_s00?ie=UTF8&psc=1)
Also, I live in a fifth wheel! -
Just different abbreviations in nomenclature, RTS or remote temperature sensor or BTS battery temperature sensor, same thing, the importance of both is equal.1500W, 6× Schutten 250W Poly panels , Schneider MPPT 60 150 CC, Schneider SW 2524 inverter, 400Ah LFP 24V nominal battery with Battery Bodyguard BMS
Second system 1890W 3 × 300W No name brand poly, 3×330 Sunsolar Poly panels, Morningstar TS 60 PWM controller, no name 2000W inverter 400Ah LFP 24V nominal battery with Daly BMS, used for water pumping and day time air conditioning.
5Kw Yanmar clone single cylinder air cooled diesel generator for rare emergency charging and welding. -
So my inverter will turn off if the battery temp is too high or something? Or will the inverter's BTS plug to the charge controller?- 4 of the 12 volt, 200ah AGM renogy batteries (I sent a screenshot of the specs above).
- 150/60 MPPT Epever Charge Controller
- 3000 watt (9000 peak) inverter/charger/auto-transfer switch
- PV array of 6 260 watt, 30.7 Vmpp, 8.5 Impp.
- Battery Shunt Monitor (https://www.amazon.com/gp/product/B07FGFFHC6/ref=ppx_yo_dt_b_asin_title_o07_s00?ie=UTF8&psc=1)
Also, I live in a fifth wheel! -
The purpose of the sensor, RTS or BTS, is to modulate the charging voltage depending on the temperature of the battery, either increasing it when below 25°C or decreasing when it's above said value. This generally has no influence on the inverter itself, all it was to,see is sufficient voltage, unless the loads exceed the rated output thereby dropping the battery voltage below it's minimum threshold, or if in equalization the voltage exceeds the inverter's limitations.
1500W, 6× Schutten 250W Poly panels , Schneider MPPT 60 150 CC, Schneider SW 2524 inverter, 400Ah LFP 24V nominal battery with Battery Bodyguard BMS
Second system 1890W 3 × 300W No name brand poly, 3×330 Sunsolar Poly panels, Morningstar TS 60 PWM controller, no name 2000W inverter 400Ah LFP 24V nominal battery with Daly BMS, used for water pumping and day time air conditioning.
5Kw Yanmar clone single cylinder air cooled diesel generator for rare emergency charging and welding. -
> - What is the "output current" you mentioned that most MPPT charge controllers can limit? Is this the Imp?
Most solar MPPT controllers have an output stage to the batteries, rated in Amps. Exceeding that limit damages the controller, so nearly all controllers have an internal circuit that limits the output to the rated limit. Because of this internal limiter, many controllers can be "over-panelled" to some extent, some 2x, some 3x depending on the brand quality of how much they can limit.
Nearly all controllers also include thermal limiting, to prevent overheating, and they reduce output as their internal temperature increases. Likewise, many have BTS to fine tune charging voltage at the battery.
Imp is a PV panel rating, mostly used when matching panels for series connections. [ Current Max Power ]
(Strange how there are several electrical terms that use different letters for much the same item.
Amps can be A or I or Current. Volts can be V or E. )
Powerfab top of pole PV mount | Listeroid 6/1 w/st5 gen head | XW6048 inverter/chgr | Iota 48V/15A charger | Morningstar 60A MPPT | 48V, 800A NiFe Battery (in series)| 15, Evergreen 205w "12V" PV array on pole | Midnight ePanel | Grundfos 10 SO5-9 with 3 wire Franklin Electric motor (1/2hp 240V 1ph ) on a timer for 3 hr noontime run - Runs off PV ||
|| Midnight Classic 200 | 10, Evergreen 200w in a 160VOC array ||
|| VEC1093 12V Charger | Maha C401 aa/aaa Charger | SureSine | Sunsaver MPPT 15A
solar: http://tinyurl.com/LMR-Solar
gen: http://tinyurl.com/LMR-Lister , -
mike95490 said:> - What is the "output current" you mentioned that most MPPT charge controllers can limit? Is this the Imp?
Most solar MPPT controllers have an output stage to the batteries, rated in Amps. Exceeding that limit damages the controller, so nearly all controllers have an internal circuit that limits the output to the rated limit. Because of this internal limiter, many controllers can be "over-panelled" to some extent, some 2x, some 3x depending on the brand quality of how much they can limit.
Nearly all controllers also include thermal limiting, to prevent overheating, and they reduce output as their internal temperature increases. Likewise, many have BTS to fine tune charging voltage at the battery.
Imp is a PV panel rating, mostly used when matching panels for series connections. [ Current Max Power ]
(Strange how there are several electrical terms that use different letters for much the same item.
Amps can be A or I or Current. Volts can be V or E. )- 4 of the 12 volt, 200ah AGM renogy batteries (I sent a screenshot of the specs above).
- 150/60 MPPT Epever Charge Controller
- 3000 watt (9000 peak) inverter/charger/auto-transfer switch
- PV array of 6 260 watt, 30.7 Vmpp, 8.5 Impp.
- Battery Shunt Monitor (https://www.amazon.com/gp/product/B07FGFFHC6/ref=ppx_yo_dt_b_asin_title_o07_s00?ie=UTF8&psc=1)
Also, I live in a fifth wheel! -
mcgivor said:The purpose of the sensor, RTS or BTS, is to modulate the charging voltage depending on the temperature of the battery, either increasing it when below 25°C or decreasing when it's above said value. This generally has no influence on the inverter itself, all it was to,see is sufficient voltage, unless the loads exceed the rated output thereby dropping the battery voltage below it's minimum threshold, or if in equalization the voltage exceeds the inverter's limitations.- 4 of the 12 volt, 200ah AGM renogy batteries (I sent a screenshot of the specs above).
- 150/60 MPPT Epever Charge Controller
- 3000 watt (9000 peak) inverter/charger/auto-transfer switch
- PV array of 6 260 watt, 30.7 Vmpp, 8.5 Impp.
- Battery Shunt Monitor (https://www.amazon.com/gp/product/B07FGFFHC6/ref=ppx_yo_dt_b_asin_title_o07_s00?ie=UTF8&psc=1)
Also, I live in a fifth wheel! -
You "rate" your charge controller by figuring out how much charge current you must have to keep your batteries healthy. If your battery bank needs 85A to recharge, you look for a 100A controller or two 60A controllers.
Charge controllers (good ones) have a solar PV string calculator to help you size the PV array for the controller
http://www.midnitesolar.com/sizingTool/index.php
If your inverter came with a BTS, you attach the BTS to the case of the battery below the waterline, and cover it (insulate it) with some foam or Styrofoam so it gets a good read of the battery. Most come with a way to bolt it to a battery terminal, but that just measures how hot the terminal gets with a lot of amps going thru it. (resistance heating). The BTS tells the Inverter, when it's in "Charge From The Grid/Generator" mode, how hot the battery is and what the charging voltage should be.
Your solar charge controller needs it's own BTS.
Once you have more than 2 strings ( you have 3 strings, and I think you plan to wire 3S3P ? ) you need to have circuit protection to prevent 2 good strings from starting a fire on a 3rd, bad string. Best way is to use 3 breakers, and then you also have an easy way to compare / check PV string outputs against each other
And you need a 4th breaker to use as as switch for the battery - Charge Controller cable, so you can easily reboot the controller if needed, and as a safety in case the CC develops a Fault and starts smoking.
Powerfab top of pole PV mount | Listeroid 6/1 w/st5 gen head | XW6048 inverter/chgr | Iota 48V/15A charger | Morningstar 60A MPPT | 48V, 800A NiFe Battery (in series)| 15, Evergreen 205w "12V" PV array on pole | Midnight ePanel | Grundfos 10 SO5-9 with 3 wire Franklin Electric motor (1/2hp 240V 1ph ) on a timer for 3 hr noontime run - Runs off PV ||
|| Midnight Classic 200 | 10, Evergreen 200w in a 160VOC array ||
|| VEC1093 12V Charger | Maha C401 aa/aaa Charger | SureSine | Sunsaver MPPT 15A
solar: http://tinyurl.com/LMR-Solar
gen: http://tinyurl.com/LMR-Lister , -
For a solar charge controller... There is a maximum input voltage from the array (Voc-cold -- Voltage open circuit) and Ipanel max current... Sometimes Ipanel is the same as the controller's output current rating--Sometimes the input max current is less than the controller' output rating--Depends on brand and model... You can have a controller with 60 amp output rating and either 60 amp input rating max, or 48 amps max input (or other numbers)....
The RTS/BTS (remote/battery temperature sensor)--There can be one RTS input for each charger (one for the solar charger, another for the inverter-charger, and another for an AC battery charger.... If the various chargers are not networked together, then each one needs its own RTS to monitor battery temperature (and do temperature connection of the charging voltage). Many solar chargers have RTS connections, some inverter-chargers have RTS, and a few AC battery chargers have RTS...
There are a few companies that make entire systems--Such as Schneider XW inverter-charters, MPPT solar charge controllers, etc... And for this company specifically, generally there is one RTS installed, and the reading is shared across the networked equipment.
Generally, you look at the battery bank and decide if you want 5%, 10%, or 13%+ rate of charge for the battery bank. 5% rate of charge can work with sunny weather/summer weekend systems. For full time off grid, 10%+ is highly recommended.
And you also need to figure out how big of solar array you need to supply your daily loads based on hours per day by season (your array needs to be large enough to recharge your daily average use plus a safety factor.
For example, you have a 400 AH @ 24 volt battery bank... So the base charging capacity looks like:- 400 AH * 29.0 volts charging * 1/0.77 panel+controller deratings * 0.05 rate of charge = 753 Watt array minimum (~40 Amps charging)
- 400 AH * 29.0 volts charging * 1/0.77 panel+controller deratings * 0.13 rate of charge = 1,958 Watt array "typical" cost effective maximum (~52 Amps charging)
Now, ideally, we would be designing for your daily loads... But since you already have the array defined at 2,370 Watts... And you are somewhere around where??? (I may have missed your location). Say near Phoenix AZ with a fixed array:Phoenix
Measured in kWh/m2/day onto a solar panel set at a 57° angle from vertical:
Average Solar Insolation figures
(For best year-round performance)
To figure out how much your array can harvest in December:Jan Feb Mar Apr May Jun 4.92
5.55
6.45
6.83
6.74
6.57
Jul Aug Sep Oct Nov Dec 6.08
5.78
6.03
5.82
5.24
4.74
- 2,370 Watt array * 0.52 off grid AC system eff * 4.74 hours of sun per day (long term December average) = 5,842 WH per day (Dec Ave)
- 400 AH * 24 volts * 0.85 AC inverter eff * 1/2 days storage * 0.50 max discharge = 2,040 WH per day (overnight, or cloudy weather for 2 days)...
- 400 AH * 500 Watts per 100 AH (at 24 volts) = 2,000 Watts maximum suggested AC inverter for FLA battery bank (AGM can supply more surge current if needed)
For your solar array, the minimum suggested MPPT type charge controller output rating (Amps) would be:- 2,370 Watt array * 0.77 panel+controller deratings * 1/29 volts charging = ~63 Amps minimum (60 would be OK too)
Of course, you can get a larger controller (like 80+ amps)--And run at less than maximum rated current--The controller will run cooler, and should last longer (heat kills electronics)--But that is your choice. (controllers need good ventilation--Don't install inside a closet or under a shelf--need good air flow).
Will stop here... I like to start with the paper design--Then find hardware (and the costs) needed to build out the system (or change some requirements if needed)... Sort of difficult to jump into the middle--And start buying hardware without a good system overview (paper design) first.
-Bill
Near San Francisco California: 3.5kWatt Grid Tied Solar power system+small backup genset -
mike95490 said:You "rate" your charge controller by figuring out how much charge current you must have to keep your batteries healthy. If your battery bank needs 85A to recharge, you look for a 100A controller or two 60A controllers.
Charge controllers (good ones) have a solar PV string calculator to help you size the PV array for the controller
http://www.midnitesolar.com/sizingTool/index.php
If your inverter came with a BTS, you attach the BTS to the case of the battery below the waterline, and cover it (insulate it) with some foam or Styrofoam so it gets a good read of the battery. Most come with a way to bolt it to a battery terminal, but that just measures how hot the terminal gets with a lot of amps going thru it. (resistance heating). The BTS tells the Inverter, when it's in "Charge From The Grid/Generator" mode, how hot the battery is and what the charging voltage should be.
Your solar charge controller needs it's own BTS.
Once you have more than 2 strings ( you have 3 strings, and I think you plan to wire 3S3P ? ) you need to have circuit protection to prevent 2 good strings from starting a fire on a 3rd, bad string. Best way is to use 3 breakers, and then you also have an easy way to compare / check PV string outputs against each other
And you need a 4th breaker to use as as switch for the battery - Charge Controller cable, so you can easily reboot the controller if needed, and as a safety in case the CC develops a Fault and starts smoking.
Does that mean I need a solar combiner box? Could I go with the MNPV 6?
Also, regarding the shut off switch logistics... that shut off goes between the positive busbar and the batteries right? And the charge controller, inverter, and (in my case since I'm at 24 volts) DC-DC step down converter also connect to that bus bar?- 4 of the 12 volt, 200ah AGM renogy batteries (I sent a screenshot of the specs above).
- 150/60 MPPT Epever Charge Controller
- 3000 watt (9000 peak) inverter/charger/auto-transfer switch
- PV array of 6 260 watt, 30.7 Vmpp, 8.5 Impp.
- Battery Shunt Monitor (https://www.amazon.com/gp/product/B07FGFFHC6/ref=ppx_yo_dt_b_asin_title_o07_s00?ie=UTF8&psc=1)
Also, I live in a fifth wheel! -
BB. said:For a solar charge controller... There is a maximum input voltage from the array (Voc-cold -- Voltage open circuit) and Ipanel max current... Sometimes Ipanel is the same as the controller's output current rating--Sometimes the input max current is less than the controller' output rating--Depends on brand and model... You can have a controller with 60 amp output rating and either 60 amp input rating max, or 48 amps max input (or other numbers)....
The RTS/BTS (remote/battery temperature sensor)--There can be one RTS input for each charger (one for the solar charger, another for the inverter-charger, and another for an AC battery charger.... If the various chargers are not networked together, then each one needs its own RTS to monitor battery temperature (and do temperature connection of the charging voltage). Many solar chargers have RTS connections, some inverter-chargers have RTS, and a few AC battery chargers have RTS...
There are a few companies that make entire systems--Such as Schneider XW inverter-charters, MPPT solar charge controllers, etc... And for this company specifically, generally there is one RTS installed, and the reading is shared across the networked equipment.
Generally, you look at the battery bank and decide if you want 5%, 10%, or 13%+ rate of charge for the battery bank. 5% rate of charge can work with sunny weather/summer weekend systems. For full time off grid, 10%+ is highly recommended.
And you also need to figure out how big of solar array you need to supply your daily loads based on hours per day by season (your array needs to be large enough to recharge your daily average use plus a safety factor.
For example, you have a 400 AH @ 24 volt battery bank... So the base charging capacity looks like:- 400 AH * 29.0 volts charging * 1/0.77 panel+controller deratings * 0.05 rate of charge = 753 Watt array minimum (~40 Amps charging)
- 400 AH * 29.0 volts charging * 1/0.77 panel+controller deratings * 0.13 rate of charge = 1,958 Watt array "typical" cost effective maximum (~52 Amps charging)
Now, ideally, we would be designing for your daily loads... But since you already have the array defined at 2,370 Watts... And you are somewhere around where??? (I may have missed your location). Say near Phoenix AZ with a fixed array:Phoenix
Measured in kWh/m2/day onto a solar panel set at a 57° angle from vertical:
Average Solar Insolation figures
(For best year-round performance)
To figure out how much your array can harvest in December:Jan Feb Mar Apr May Jun 4.92
5.55
6.45
6.83
6.74
6.57
Jul Aug Sep Oct Nov Dec 6.08
5.78
6.03
5.82
5.24
4.74
- 2,370 Watt array * 0.52 off grid AC system eff * 4.74 hours of sun per day (long term December average) = 5,842 WH per day (Dec Ave)
- 400 AH * 24 volts * 0.85 AC inverter eff * 1/2 days storage * 0.50 max discharge = 2,040 WH per day (overnight, or cloudy weather for 2 days)...
- 400 AH * 500 Watts per 100 AH (at 24 volts) = 2,000 Watts maximum suggested AC inverter for FLA battery bank (AGM can supply more surge current if needed)
For your solar array, the minimum suggested MPPT type charge controller output rating (Amps) would be:- 2,370 Watt array * 0.77 panel+controller deratings * 1/29 volts charging = ~63 Amps minimum (60 would be OK too)
Of course, you can get a larger controller (like 80+ amps)--And run at less than maximum rated current--The controller will run cooler, and should last longer (heat kills electronics)--But that is your choice. (controllers need good ventilation--Don't install inside a closet or under a shelf--need good air flow).
Will stop here... I like to start with the paper design--Then find hardware (and the costs) needed to build out the system (or change some requirements if needed)... Sort of difficult to jump into the middle--And start buying hardware without a good system overview (paper design) first.
-Bill
The reason my array is not sized according to my loads is because I can only fit so many panels with me on my RV roof and ground array.
The roof of my RV will have only 6 of the big 260 watt panels but it will also have 3 of the smaller 130 watt ones. That will be my continuous solar that I plan on using constantly. I think there will be times when I can't use the ground array (3 additional of the 260 watt panels), and I will just be running off that. Will I have to adjust my charge controller each time I plug in the ground array, or will it automatically adjust?
Also I am living full time out of the RV with my fiancé so the batteries will be used continuously. I'm not sure if what you meant by the "two day battery storage" thing is that I won't be using the batteries or not... I was going to go with a 3,000 watt inverter actually so that I can run my air conditioner off the inverter. Without a soft starter it won't work on a 2000 watt one. My thinking was that my 400ah bank at 24 volt gives me 9,600 watts for an hour. Since I won't discharge past 50 % for battery health it's effectively only 4,800 watts for an hour. I don't plan on running my Air conditioner for very long on batteries alone, but if I need to, because the sun won't charge my batteries sufficiently, I can always turn on my generator to charge them. Am I missing something here?
Can all charge controller's be used to overpanel and if not, how do I tell? For example, can this one?
https://www.amazon.com/Controller-12V24V48V-Battery-Regulator-Batteries/dp/B07GW57RN5/ref=sr_1_8?dchild=1&keywords=150+volt+charge+controller&qid=1603342779&s=lawn-garden&sr=1-8&th=1
Also, I am in California but do plan on traveling around eventually (still living full time out of it) and I have no current way to tilt the panels. I can invest in that down the line I suppose.
I appreciate the help figuring out the charge controller. So, in order to over panel for cost effectiveness I am looking for a charge controller that can charge at 60 amps (output current) for my 24 volt battery bank. It needs to be able to handle a VOC of like 150V for when it gets cold, and it needs to be able to handle the overall array wattage of 1,800 watts (2,340 x .77)?
So it seems the charge controller I linked above falls short a little bit too much then?- 4 of the 12 volt, 200ah AGM renogy batteries (I sent a screenshot of the specs above).
- 150/60 MPPT Epever Charge Controller
- 3000 watt (9000 peak) inverter/charger/auto-transfer switch
- PV array of 6 260 watt, 30.7 Vmpp, 8.5 Impp.
- Battery Shunt Monitor (https://www.amazon.com/gp/product/B07FGFFHC6/ref=ppx_yo_dt_b_asin_title_o07_s00?ie=UTF8&psc=1)
Also, I live in a fifth wheel! -
Wow. Whoa....
3 of these panels and 3 of those panels ?? And 3 more on the ground ??
Running a 24V system ?
You will need to have panels wired to produce at least 40Vmp with a MPPT charge controller.
Mixing different kinds of panels becomes an issue, voltages have to match OR amps have to match. you cannot mismatch these things, you have to design the system
So to start, lets get the
Vmp
Voc
Imp
for each of your 3 kinds of panels. and the Max input voltage you controller will work at. Small controllers top out at 50V. moderate ones at 75V and major ones at 150V, before they fry. Large controllers for large arrays work up to 600V dc input
And we need to cold temp you can expect to see every 5 years, a cold frosty morning causes PV array voltage to rise and can over voltage your controller and fry it.
Powerfab top of pole PV mount | Listeroid 6/1 w/st5 gen head | XW6048 inverter/chgr | Iota 48V/15A charger | Morningstar 60A MPPT | 48V, 800A NiFe Battery (in series)| 15, Evergreen 205w "12V" PV array on pole | Midnight ePanel | Grundfos 10 SO5-9 with 3 wire Franklin Electric motor (1/2hp 240V 1ph ) on a timer for 3 hr noontime run - Runs off PV ||
|| Midnight Classic 200 | 10, Evergreen 200w in a 160VOC array ||
|| VEC1093 12V Charger | Maha C401 aa/aaa Charger | SureSine | Sunsaver MPPT 15A
solar: http://tinyurl.com/LMR-Solar
gen: http://tinyurl.com/LMR-Lister , -
No, it's only two different types of panels. There will be a roof and ground array. The roof will have 6 of the big 260 watt panels and the three smaller panels will fill in the gaps on the roof (the smaller ones are the 130 watt panels). The ground array (3 panels) will be of the same kind as the roof type. I will have all 9 (both the roof and ground array) of the 260 watt panels wired to the same charge controller and the other ones will be on a separate charge controller. I am not too wired about those ones right now and the separate charge controller. I was going to get to that later on. I won't be mixing panels.
Right now I just care about having the right charge controller for the 9 260 watt panels.
I plan on traveling around in my trailer eventually, but for now I am in California where it does not get very frosty.- 4 of the 12 volt, 200ah AGM renogy batteries (I sent a screenshot of the specs above).
- 150/60 MPPT Epever Charge Controller
- 3000 watt (9000 peak) inverter/charger/auto-transfer switch
- PV array of 6 260 watt, 30.7 Vmpp, 8.5 Impp.
- Battery Shunt Monitor (https://www.amazon.com/gp/product/B07FGFFHC6/ref=ppx_yo_dt_b_asin_title_o07_s00?ie=UTF8&psc=1)
Also, I live in a fifth wheel! -
Here are the panel specs:- 4 of the 12 volt, 200ah AGM renogy batteries (I sent a screenshot of the specs above).
- 150/60 MPPT Epever Charge Controller
- 3000 watt (9000 peak) inverter/charger/auto-transfer switch
- PV array of 6 260 watt, 30.7 Vmpp, 8.5 Impp.
- Battery Shunt Monitor (https://www.amazon.com/gp/product/B07FGFFHC6/ref=ppx_yo_dt_b_asin_title_o07_s00?ie=UTF8&psc=1)
Also, I live in a fifth wheel!
Categories
- All Categories
- 229 Forum & Website
- 137 Solar Forum News and Announcements
- 1.4K Solar News, Reviews, & Product Announcements
- 199 Solar Information links & sources, event announcements
- 898 Solar Product Reviews & Opinions
- 256 Solar Skeptics, Hype, & Scams Corner
- 22.5K Solar Electric Power, Wind Power & Balance of System
- 3.5K General Solar Power Topics
- 6.7K Solar Beginners Corner
- 1K PV Installers Forum - NEC, Wiring, Installation
- 2.1K Advanced Solar Electric Technical Forum
- 5.6K Off Grid Solar & Battery Systems
- 428 Caravan, Recreational Vehicle, and Marine Power Systems
- 1.1K Grid Tie and Grid Interactive Systems
- 654 Solar Water Pumping
- 816 Wind Power Generation
- 624 Energy Use & Conservation
- 619 Discussion Forums/Café
- 312 In the Weeds--Member's Choice
- 75 Construction
- 124 New Battery Technologies
- 108 Old Battery Tech Discussions
- 3.8K Solar News - Automatic Feed
- 3.8K Solar Energy News RSS Feed