I am looking to double my solar array
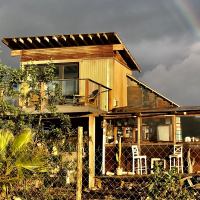
______________________________________________________________________________________________________________
This probably shows I'm a beginner
I currently have six panels that are 230 W, 37VOC, 7.67Amp
I can pick up 6 panels, at a great price, that are not the same specs but close
They are 230W, 37.4 Voc 8.43A
I am thinking that they match close enough to wire one from each group in series then parallel to create a six panel string then do that again for the next string. I should not just add the six new mismatched panels together to create a new string. Would this confuse the Charge controller or is the difference so little that the controller will cope?
Comments
-
The controller will never notice. Those voltage differences are tiny. The total amperages will add at the combiner.
System 1) 15 Renogy 300w + 4 250W Astronergy panels, Midnight 200 CC, 8 Trojan L16 bat., Schneider XW6848 NA inverter, AC-Delco 6000w gen.System 2) 8 YingLi 250W panels, Midnight 200CC, three 8V Rolls batteries, Schneider Conext 4024 inverter (workshop) -
I do not understand your wiring diagram... Are all panels in parallel (Vmp~37 volts, Imp-array=6xImp-panel)? Or are some in series?
Both are very close in Vmp and Imp ratings... Less than the 2-5% variations you may see from panel to panel.
I don't think you can measure the "real differences" with a DMM in the field, and the MPPT controller would not care.
-BillNear San Francisco California: 3.5kWatt Grid Tied Solar power system+small backup genset -
BB. said:I do not understand your wiring diagram... Are all panels in parallel (Vmp~37 volts, Imp-array=6xImp-panel)? Or are some in series?
I Instead of simply asking , "What is the best way to wire my 12 panels for my 48 volt battery Bank ?", I’m trying to figure it on my own so that I may have a better understanding. What I am hoping to clarify, with this diagram, is that I will be wiring four groups/strings of 3 panels in Series then connecting two groups/strings of 6 panels in Parallel taking those two strings to the combiner box. The Diagram hopefully would help.
I feel my calculations are correct but of course being a beginner I’d love to hear a confirmation I’m on the right track.
SIX , 30V 7.67 Amp, panels in series / parallel will create 60 volts with 23.01Amp
If I had two strings, the same as above, going to combiner. Wouldn’t that create 60 volts at 46.02 amps. Being a good charge rate for the bank?
-
Yes, you got it right.
What is the voltage of your battery bank (12/24/48?). And its Amp*Hour rating (at 20 hour rate)? And what kinds of batteries do you have?
And what is the Vpanel-max input voltage for your MPPT charge controller? For a Vmp-array ~ 60 volts, that would work very well for a MPPT controller with a minimum of 90-100 DC input rating (Vmp and Voc rise when the temperature falls--Typically below freezing, you have to be very careful to not "over voltage" your MPPT input and ruin it.
Details matter here.
An example of the details... You have a combiner box with fuses/breakers. You have paralleled 3 parallel strings of panels into one wire into the combiner box (and another pair for the second array). The "correct" way to do this is to bring in one set of wires for each 2 panels in series. You want the fuse/breaker to protect each string. So in this case, you would need 6x fuses/breaker combiner box.
Also, I am not familiar with the combiner box/fuses/breakers you have there... I am not sure the wiring is correct... Guessing, but it looks like the wires are going into the hole where the screw driver tightens the screws. The wire should go into from the side of the fuse holders.
And in this case, each RED wire should go into the bottom only (one wire per fuse hold). And each of the black wires should go into the "Bus" terminal block to the right (see the red wires on the left block of 4--Those are coming from the fuses. The black wires should probably go into the terminal block to the right (no wires at this point) from the top.
And at the bottom of those blocks, your heavy AWG copper wire goes into the bottom of the blocks (right one is positive, left one is negative).
Limit here is that this is a 4 position fuse/bus combiner, and you would need 6x combiner. Example:
https://www.solar-electric.com/mnpv6.html
Positive cables (6x) each goes into the bottom of a circuit breaker. The top is a metal busbar with 2x lugs for connecting back to the solar charge controller.
The bottom left is an insulated bus bar for the black/negative wires. And there are larger holes for heavy cable back to charge controller.
The bus bar to the right is the ground bus bar--All your frame ground wires would go here.
Here is a very detailed document for wiring a combiner box--Different hardware but same wiring results:
https://www.solar-electric.com/lib/wind-sun/PVcombiners-explained.pdf
-BillNear San Francisco California: 3.5kWatt Grid Tied Solar power system+small backup genset -
It would appear the wiring, according to the diagram provided, is incorrect being that it would result in a dead short across the fuse, the negative wires should be connected to the negative terminal block on the right.1500W, 6× Schutten 250W Poly panels , Schneider MPPT 60 150 CC, Schneider SW 2524 inverter, 400Ah LFP 24V nominal battery with Battery Bodyguard BMS
Second system 1890W 3 × 300W No name brand poly, 3×330 Sunsolar Poly panels, Morningstar TS 60 PWM controller, no name 2000W inverter 400Ah LFP 24V nominal battery with Daly BMS, used for water pumping and day time air conditioning.
5Kw Yanmar clone single cylinder air cooled diesel generator for rare emergency charging and welding. -
ARGHH !!! If I'm reading that drawing - you have
2 panels in series. then 3 groups in parallel onto 1 set of power leads
+
2 panels in series. then 3 groups in parallel onto 1 set of power leads
so you have 6 strings in parallel and only 2 protection devices.
2S6P in conventional shorthand
Your wiring better be better than your sketches, they are very hard to follow.
Powerfab top of pole PV mount | Listeroid 6/1 w/st5 gen head | XW6048 inverter/chgr | Iota 48V/15A charger | Morningstar 60A MPPT | 48V, 800A NiFe Battery (in series)| 15, Evergreen 205w "12V" PV array on pole | Midnight ePanel | Grundfos 10 SO5-9 with 3 wire Franklin Electric motor (1/2hp 240V 1ph ) on a timer for 3 hr noontime run - Runs off PV ||
|| Midnight Classic 200 | 10, Evergreen 200w in a 160VOC array ||
|| VEC1093 12V Charger | Maha C401 aa/aaa Charger | SureSine | Sunsaver MPPT 15A
solar: http://tinyurl.com/LMR-Solar
gen: http://tinyurl.com/LMR-Lister , -
BB. said:Yes, you got it right.
Positive cables (6x) each goes into the bottom of a circuit breaker. The top is a metal busbar with 2x lugs for connecting back to the solar charge controller.
The bottom left is an insulated bus bar for the black/negative wires. And there are larger holes for heavy cable back to charge controller.
The bus bar to the right is the ground bus bar--All your frame ground wires would go here.
________________________________________________________________________________________________Well wiring of panels down. WooHoo! Thanks Bill.so much more to go.The combiner is going to be a weeks worth of studying for me. what else can I install into a combiner to clear the chaos of a set up ? But from what I gathered quickly each 3panel string should go to it's own breaker? I understand locations for wires .Dah, black wire to negative bar, not torquing screw of breaker.
Here's a diagram of what I have so far as a system. (old panel setup)I think it's pretty close. Want to get it worked out with batteries I've had for 4 years before I shell out for a 7.5Kwh or 10Kwh lifepr4 battery.
-
Bj,Slow down on the panel wiring... You have 2 series x 3 parallel strings... For a 48 volt battery bank, you want 3 series panels.
- 2x 37 volt Vmp panels = 74 Volts Vmp-array
That is barely high enough Vmp-array for a 48 volt battery bank. With a good quality MPPT controller, in warm to hot weather, the MPPT controller will be running (more or less) like a PWM controller.For an Outback controller with Vpanel max input voltage of 140 (or 150?) VDC, you want Vmp array to be:- 59 volt charging battery bank * 1.3x MPPT fudge factor (you want Vmp-array>>Vbatt for MPPT operation) = 76.7 Vmp-array-std voltage minimum suggested
- 3 series panels * 37 volts = 111 Volts Vmp-array-std (standard name plate rating)
The issue here is that in very cold, sub freezing climates, your Voc of the array could exceed 140 (150?) VDC max for the controller. Guessing that your panels would "over voltage" the Outback at something like -10C. You need to verify your minimum temperatures and solar panels you want to use... I am just doing a quick guess that your place does not fall below ~0C (32F). This is an important part of the design process.If you are using Outback controllers, here is there string sizing tool down load:If you end up with 3x series panels and 4x parallel strings (3s x 4p) for 12 panels total... Your estimated maximum array output to the battery bank would be:- 12 x 230 Watt panels = 2,760 Watt array
- 2,750 Watt array * 0.77 panel+controller deratings * 1/58 volts nominal charging = 36.5 Amps (cool/clear day/battery in "bulk charging")--Basically your best expected for a hand full of solar noons a year.
So, you do not need much over a 40 amp MPPT controller for this proposed array--Especially in a warm/hot climate.And to be clear... The rule is if you have 3 or more parallel strings (i.e., 3s x 2p or 3s x 4p or more Xp's), each 3 panel string should have its its own breaker/fuse. This is to prevent a shorted string from being fed too much current from the other 2+ parallel strings and setting the wiring on fire.If you do choose a 3s x 4p array, your 4 port combiner box would be fine (one place for each series string to connect to).Your last drawing shows 6 panels (aka 3s x 2p connected)... If still 12 panels (3s x 4p) that is still OK.You should have 4 positive wires from the array (one for each "series string") and 4 negative wires from the array (again, one per series string of 3 panels).And you need to figure out how thick the wiring needs to be. 7.78 Amp panels would typically have a series fuse (breaker) rating of 15 amps (could be 20 amps)... The minimum AWG for 15 amp wiring is 14 AWG, and for 20 amp wiring is 12 AWG... You can use heavier, and you may want to if you have long wire runs from array to charge controller...For example, say you have 7.78 Amps @ 50 foot (one way) array to combiner box run, and you want 1% to 3% voltage drop maximum. You can use a simple voltage drop calculator to figure out the voltage drops for such a setup (assume Vmp-array 3 series * 37 volts = 111 VDC Vmp-array).Voltage drop: 1.96
Voltage drop percentage: 1.77%
Voltage at the end: 109.04In this case, even 14 AWG wiring gives results between 1% and 3% drop... Heavier AWG cable will have less drop... For example 10 AWG:Voltage drop: 0.78
Voltage drop percentage: 0.70%
Voltage at the end: 110.22Very little wasted voltage and energy (and why going to higher voltage arrays and MPPT charge controllers are very nice--You don't need very heavy copper wiring out to the array...You need to plug in your numbers (distance, array configuration, etc.) to get "your answers".Personally, for solar arrays, and battery chargers (AC battery chargers, solar chargers, etc.), I like to use a 1.25 (1/0.80) derating factor. Charging a battery can output XX.X amps (rated output) for a few hours until a discharged battery gets near full... So for your solar array of 7.78 amps per string, the branch circuit/fusing minimum suggested would be:- 7.78 amps from array * 1.25 NEC derating = 9.725 Amps ~ 10 amp minimum rated branch wiring and fuse (example)
You have to figure out these numbers for the Outback to battery bank, and any AC charger (or inverter/charger).Also each "wire/cable" that leaves the + battery bank bus, should have its own properly rated fuse. For example a 3.6 kWatt @ 48 volt AC inverter, the worst case current draw would be:- 3,600 Watts * 1/0.85 inverter eff * 1/42 VDC battery cutoff voltage = 100.8 amps maximum draw from inverter
So your branch wiring and fuse/breaker needs to be rated for this current. You should check voltage drop from battery bank to inverter (for 48 volt battery bank, suggested max drop would be ~2 volts).And wiring from your charge controller.. Wiring and fuse/breaker at battery bus needs to manage the charging current (typically the maximum rating of the MPPT controller)... Say 60 Amp controller, with 1.25 NEC derating:- 60 amp controller rating * 1.25 NEC derating = 75 Amp minimum branch wiring/breaker/fuse suggested (or round up to 80 amps, next standard value).
In North America, most fuses and breakers are (more or less) rated to blow at 100% current and not blow at 80% or less current. Charging your battery bank at 60 amps for a few hours, and a standard 60 amp breaker/fuse may false trip (Outback makes some breakers that are rated for 100% current and not trip--They are a special case).Your battery bank is properly wired for series/parallel operation... And typically we suggest 5% to 13%+ rate of charge. 5% works for weekend/sunny weather systems, 10%+ suggested for full time off grid usage (in Baja, you may get 5% to work for you because of all the sun, and if you don't use much energy). Anyway, the math looks like this:- 360 AH battery bank * 59 volts charging * 1/0.77 panel+controller derating * 0.05 rate of charge = 1,379 Watt array minimum
- 360 AH battery bank * 59 volts charging * 1/0.77 panel+controller derating * 0.10 rate of charge = 2,758 Watt array nominal
- 360 AH battery bank * 59 volts charging * 1/0.77 panel+controller derating * 0.13 rate of charge = 3,586 Watt array "typical" cost effective maximum array
And, if you know how much energy you want to use, we can check the battery bank AH sizing and array sizing tooWill stop here for now... Lots of stuff discussed. Questions/corrections to my guesses?-BillNear San Francisco California: 3.5kWatt Grid Tied Solar power system+small backup genset -
Looks like you want to use an Outback MPPT type charge controller. They have a downloadable string sizing tool that works with Excel;
Here;
http://www.outbackpower.com/resources/technical-support/string-sizing-tool
I believe Outback has a hard 150 volt limit, so as Bill is saying you will want to see an ultimate cold VOC of less than 150 volts.bajamox said:
...Wouldn’t that create 60 volts at 46.02 amps. Being a good charge rate for the bank?
I think 60 cell panels (Those with a VOC in your range) usually work well with this charge controller in strings of 3. Run them through the String sizing tool to see where you stand.Home system 4000 watt (Evergreen) array standing, with 2 Midnite Classic Lites, Midnite E-panel, Magnum MS4024, Prosine 1800(now backup) and Exeltech 1100(former backup...lol), 660 ah 24v Forklift battery(now 10 years old). Off grid for 20 years (if I include 8 months on a bicycle).
- Assorted other systems, pieces and to many panels in the closet to not do more projects. -
BB. said:I am just doing a quick guess that your place does not fall below ~0C (32F). This is an important part of the design process.
- HARDLY DROPS BELOW 40 F. AND HARDLY GOES ABOVE 90F
If you are using Outback controllers, here is there string sizing tool down load:- Was not able to input my panels configuration into string sizing tool
If you end up with 3x series panels and 4x parallel strings (3s x 4p) for 12 panels total... Your estimated maximum array output to the battery bank would be:12 x 230 Watt panels = 2,760 Watt array
2,750 Watt array * 0.77 panel+controller deratings * 1/58 volts nominal charging = 36.5 Amps (cool/clear day/battery in "bulk charging")--Basically your best expected for a hand full of solar noons a year.If you can tell us your rough location, we can figure out the hours of sun per day and how much "useful" energy you can harvest by month...- I have yet to purchase the combiner I like that the Midnite solar MNPV4 actually comes with breaker and bus bars but the Outback does not, they would be additional. Can the midnite be equipped with fuse between array positive bus bar and feed to controllerSide note: I see next to your name is Administrator so, thinking, you are part of the Northern Arizona Wind & Sun team. I do intend to purchase the rest of my system components from you as I have bought most of them for this new system so far from you.
- Clarification: this again shows my ignorance, (each "wire/cable" that leaves the + battery bank bus) this essentially means a fuse between controller and inverter on Positive cable? Can the Midnite MNPV4 be equipped with fuse between array positive bus bar and feed to controller, to keep indoor component setup more clutter free? I'm now going to be trying to figure the fuse size .
150 miles south of Ensenada panels face +- 155 SEUnobstructed Sun path video shot Oct 4 last year https://mox90291.smugmug.com/Baja/Solar/i-GpxpK2q- Chart shows “full power charging” closest city to my location. I’m sure other sun hours would provide additional residual power charging each panel. But let’s not add that to calculations. I believe I am correct in thinking the rated wattage per panel produce that amount per hour.
-
- So my 6 235W =1.4Kwh and my 6 255 =1.5Kwh for total of 2.9Kwh per hour
-
- Therefore 2.9Kwh @ an August day would produce 2.9 x 5.88 = 17 Kwh
And, if you know how much energy you want to use, we can check the battery bank AH sizing and array sizing too- Daily power consumption is calculated at 4.5Kwh
- Bill, just can't thank you enough a lot of this is still over my head , but it is gettin in there
Will stop here for now... Lots of stuff discussed. Questions/corrections to my guesses?-Bill
-
You could run your panels through Midnite's String sizing tool, use the Midnite Classic 150 as your controller. I think they give the High VOC as a number, as well as charging/array numbers. I know others use their tool, and the guys at Midnite started and sold Outback, and may still own a chunk of it.
http://www.midnitesolar.com/sizingTool/
Home system 4000 watt (Evergreen) array standing, with 2 Midnite Classic Lites, Midnite E-panel, Magnum MS4024, Prosine 1800(now backup) and Exeltech 1100(former backup...lol), 660 ah 24v Forklift battery(now 10 years old). Off grid for 20 years (if I include 8 months on a bicycle).
- Assorted other systems, pieces and to many panels in the closet to not do more projects. -
I prefer Websites vs string sizing download tools... Anyway, you can use the Midnite tool to get most of the information:Just a quick guess at your panels' specifications gives:Classic, Classic SL & Classic Lite Charge Controller Selection
150 200 250 Max Operating Voltage 150 200 250 Max Non operating VOC (HyperVOC) @ 48V Nominal Battery Voltage 198 248 298 Maximum Number Of Modules In Series 3 4 6 Max Number Of Modules In Series (Using HyperVOC) 4 6 7 Max Allowable Output Current Per Classic
Based On This Current Configuration83 70 55 Max Allowable Wattage Per Classic
Based On This Current Configuration4847 4080 3212 Present PV Array Wattage Of This Configuration 2760 2760 2760 Design Check Max VOC OK OK OK Temperature The Classic Will
Enter HyperVOC-103 F° -344.2 F° -587.2 F° Array Power (Wattage) OK OK OK Classics Required 0.6 0.7 0.9 PV Array Rated PV Array Power: 2760 Watts Anticipated Array Power @ 90F: 2671 Watts Rated PV Array Current: 31.48 Amps Battery Charging Current @ 57.6 V: 47.9 Amps VMP (Maximum Power Point Voltage) : 91.8 Volts VOC (Open Circuit Voltage): 112.8 Volts VMP @ 40 F°: 100.2 Volts VOC @ 40 F°: 120.6 Volts So, three panels in series gives 120.6 volts @ 40F ... Well below the ~140-150 max voltage for an Outback controllerI am not affiliated with NAWS in any way... I am just an unpaid volunteer here (as is pretty much everyone else volunteering their time). NAWS does not monitor the forum for questions and answers (if something comes up that NAWS needs to answer, I will forward the questions to them via email and get an answer). I am an "administrator" on the website--But that is basically still just a moderator function (cleaning up spills--Which does not happen often here. Everyone is very polite and works hard to help answer questions).NAWS does pay for the software support and engineering issues with the forum software--So if you find that you are happy with NAWS (pricing and service, and the open forum we have here)--I (and NAWS) would be very happy with your business.Your series/parallel panel connections are good now. I have no idea how long your distances are and where the combiner box will be installed (near the array, or near your charge controller/battery shed). Overall, you can pull 4 sets of smaller cables 50 feet, or 1 pair of heavier cable that 50' distance--The amount of copper would be the same and about the same cost overall for the cabling. And should use the voltage drop calculator to make sure your voltage drop is not excessive.For example, 32.42 Amps Imp (4p strings), 30', 8 AWG copper cable at ~90 volts:Voltage drop: 1.22
Voltage drop percentage: 1.36%
Voltage at the end: 88.78Looks good for the 8AWG section. As long as the 10 AWG sections are relatively short, should not be an issue with voltage drop (as always, verify drop for 8.x amps at xx feet at 10 AWG at 90 volts to confirm).Yes, every positive wire that leaves the positive battery bank bus bar should be protected by a fuse/circuit breaker (again, circuit breakers are nice because you can also use as an On/Off switch).One pair of wires from battery bank to +&- Battery bus bars. And each pair of wires should be sized for the loads (or charging source). XXX amps for a large inverter, XX amps to charge controller, X amps to LED lighting, etc.The E-Panels are somewhat variable and can be customized by NAWS, if needed (I think). They are also differences between Outback, Midnite, Schneider, etc...
An example of a larger E-Panel:And there are instructions, wiring diagram, etc. on the above web page.https://www.solar-electric.com/lib/wind-sun/E-Panels-explained.pdf (overall explanation of E-Panels from Midnite)Looking at your load sheet--The average loads add up to ~1,212 Watts... A ~2,000 to 2,400 Watt (or even 3,600 Watts if you want to allow for growth) AC inverter would be more than enough. Remember there are always details that can cause issues... For example, a typical frost free fridge has a 600 Watt defrost heater--So you have to add the heater (which is over the 74 Watt compressor draw--By the way, is the 74 Watts measured? Seems a little low--Typically 100-120 Watts is what I have seen).Any way, your "real load" is probably closer to 1,800 Watts with everything on (you probably will not have all "on at the same time").Assuming 4.5 kWatt*Hours per day of 120 VDC power (will you need any 240 VAC power?). First the battery bank using standard rules of thumb for FLA battery bank:- 4,500 WH per day * 1/0.85 AC inverter eff * 2 days storage * 1/0.50 max discharge * 1/48 volt battery bank = 441 AH @ 48 volt battery bank (not a "small system")
A 440 AH @ 48 volt battery bank can manage a maximum AC inverter (and solar array) of ~ 4,400 Watts... So a 2,400 to 3,600 Watt AC inverter is fine (you have to check the battery bank is large enough to meet the maximum AC inverter draw, and 2x that for surge current support). [for a 48 volt battery bank, use 1,000 Watts AC inverter/Array maximum sizing for every 100 AH battery bank capacity. 441 AH @ 48 volts -> 4,410 Watt "max" loading/array]Sizing the solar array... First based on Battery WH capacity and 5% to 13%+ rate of charge (assume 6 volt @ ~220 AH batteries, 8 in series for 48 volts, and 2 parallel for 440 AH capacity):- 441 AH * 58 volts charging * 1/0.77 panel+controller deratings * 0.05 rate of charge = 1,661 Watt array minimum
- 441 AH * 58 volts charging * 1/0.77 panel+controller deratings * 0.10 rate of charge = 3,322 Watt array nominal (recommended for full time off grid minimum)
- 441 AH * 58 volts charging * 1/0.77 panel+controller deratings * 0.13 rate of charge = 4,318 Watt array "typical" cost effective maximum
- 4.500 WH per day loads * 1/0.52 off grid AC system end to end eff with FLA batteries * 1/5.0 hours of sun = 1,731 Watt array "break even" in winter (5.0 hours of sun per day average)
The idea being you want to supply your base loads 24 hours per day * 365 days per year (refrigerator, lighting, laptop). And other loads (A/C, floor heating, etc.) are "optional" you only use A/C in hot weather, and floor heating in cold weather--And you can avoid either if cloudy/stormy weather... You should plan on using ~50% to 65% of yoru predicted harvest for "base loads":- 4,500 WH per day total * 0.50 base load fudge factor = 2,200 WH per day for base loads (50%)
- 4,500 WH per day total * 0.65 base load fudge factor = 2,925 WH per day for base loads (65%)
Sizing your solar array... It is always trade offs. In your case, lots of sun even during winter. Good solar harvest year round. You may still want more power/backup power--A genset? Or go with a larger array (like 3,322+ Watts) and do without a generator.
The above are just rules of thumbs... You will need to adjust to your needs (and what is available locally, $$$ you want to pay, etc.). That is the reason I show all the math--So you can adjust for your assumptions and see how that affects other parts of the system design.All the above numbers are approximate... With solar power, any number you use within 10% of the above numbers are pretty much "identical" (i.e., 3,000 Watt array about the same as a 3,300 Watt array). Don't sweat the small stuff (I use 3+ digits to avoid rounding errors and so you can follow where one value is created, and where it is used next (rather than variables A, B, C, etc.).-BillNear San Francisco California: 3.5kWatt Grid Tied Solar power system+small backup genset -
Bill is quite modest, but does such an incredible job of giving complete answers, some times other contributors can be truly amazed! I can't recall, but I think the double spacing comes with his interaction with our current software while on a phone (or maybe tablet). That would put a long reply like this in perspective! WOW! just WOW!
If you will be where you are comfortable leaving batteries outside, I'd suggest that's not a bad course of action. Then just run a monitor of some sort into the structure. My systems have always lived outside. Even in the heat of summer my battery protected from direct sunlight, stayed at a high temperature of less than 80 degrees, while outside temps ran as high as mid 90's and lows around 73-74.
Here's an example of a small E-Panel in my current setup. The wiring for the array comes in from the back. The heavy cables running off to go to the battery bank, the blue wires are temperature sensors (I had 2 because I didn't have the charge controllers wired together originally). The original inverter is from my cabin system and is a 1800 watt ProSine (now a Schneider company) I've replaced it with a 4024 Magnum.
A breakdown of the wiring and breakers goes like this;
Blue arrows are the negative and red are the '+'.
The E-Panels also come with a transfer switch along the Din rail between the Large Inverter Breaker and the Din rail above. So you can hardwire a generator into your system and wire a breaker between the Inverter and the Home breaker box. Making this your main panel.
Home system 4000 watt (Evergreen) array standing, with 2 Midnite Classic Lites, Midnite E-panel, Magnum MS4024, Prosine 1800(now backup) and Exeltech 1100(former backup...lol), 660 ah 24v Forklift battery(now 10 years old). Off grid for 20 years (if I include 8 months on a bicycle).
- Assorted other systems, pieces and to many panels in the closet to not do more projects. -
How much "useful" energy you can harvest... For example, the "best" you would probably be able to see power and current wise (cool/clear spring or fall near solar noon):
- 2,900 Watts array * 0.77 panel+controller derating = 2,233 Watts
Assuming you batteries are less than 80% state of charge (and/or you have other Loads on your system), the peak current is dependent on battery bank voltage (for MPPT controllers):- 2,900 Watt array * 0.77 derate * 1/59 volts charging (absorb) = 37.85 amps
- 2,900 Watt array * 0.77 derate * 1/48 volts charging = 46.5 Amps
With a battery system, the batteries (and state of charge, battery bus voltage, other loads DC and AC) all will "affect" your peak current from your charge controller/peak power from your array...Most of the time, you probably will not be even close to the above current--And yet everything will be OK (batteries not that discharged, no heavy loads on your inverter, etc.).We use the 5.0 hours of sun per day as a short hand... If the sun was "stuck at noon" at your location for 5 hours, then suddenly set.The reality is the sun moves across the sky, and you (probably) have a fixed array faxing south at 58 degrees from vertical (or whatever). The software "maps" the sun's energy onto a fixed "flat panel" and gives us the simple 5.0 hours of sun per day.In fact, the sun rises and starts at a few watts and slowly ramps up to "maximum" harvest around noon (+/- an hour or so). And then the sun slowly sets again.So the 5 hours of harvest is spread out over 8+ hours.By the way, Lead Acid batteries need a lot of time on charge (if they are heavily discharged). One way to make this work better is called "virtual tracking". Let up 1/2 your array facing south east (towards rising sun) and the other 1/2 south west (towards setting sun). Given that you are so close to the equator (vs northern USA and Canada), I am not sure how much this will help extend charging times.You can play with PV Watts--There is an output option for hour by hour for 365 days.-BillNear San Francisco California: 3.5kWatt Grid Tied Solar power system+small backup genset -
Photowhit said:You could run your panels through Midnite's String sizing tool, use the Midnite Classic 150 as your controller. I think they give the High VOC as a number, as well as charging/array numbers. I know others use their tool, and the guys at Midnite started and sold Outback, and may still own a chunk of it.
http://www.midnitesolar.com/sizingTool/
Thanks for the heads up on this sizing tool. Simple
Categories
- All Categories
- 229 Forum & Website
- 137 Solar Forum News and Announcements
- 1.4K Solar News, Reviews, & Product Announcements
- 199 Solar Information links & sources, event announcements
- 898 Solar Product Reviews & Opinions
- 256 Solar Skeptics, Hype, & Scams Corner
- 22.5K Solar Electric Power, Wind Power & Balance of System
- 3.5K General Solar Power Topics
- 6.7K Solar Beginners Corner
- 1K PV Installers Forum - NEC, Wiring, Installation
- 2.1K Advanced Solar Electric Technical Forum
- 5.6K Off Grid Solar & Battery Systems
- 428 Caravan, Recreational Vehicle, and Marine Power Systems
- 1.1K Grid Tie and Grid Interactive Systems
- 654 Solar Water Pumping
- 816 Wind Power Generation
- 624 Energy Use & Conservation
- 619 Discussion Forums/Café
- 312 In the Weeds--Member's Choice
- 75 Construction
- 124 New Battery Technologies
- 108 Old Battery Tech Discussions
- 3.8K Solar News - Automatic Feed
- 3.8K Solar Energy News RSS Feed