Lithium Iron Phosphate Balancer
Options
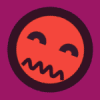
dexter12353
Registered Users Posts: 19 ✭✭
Just got my new LiFePO4 battery bank and got the balancer installed.
Purchased this one from the Electric Car Parts company, it's capable of moving up to 6 amps per cell. This is the highest capacity that I have seen to this point. I'm charging at around 30 amps with the generator and around 50 amps absolute max with solar, the battery bank is 100ah of CALB LiFePO4. Planning on upping this to CA180's later on with a long term goal of a system of approx. 800ah.
The batteries are very slightly used but are keeping together pretty well. It was a very tough call on deciding whether or not to fuse the balance lines - If they are fused and the wires short out things are protected, but if the fuses blow for whatever reason and now there is no balancing, theoretically a cell can be overcharged and that could be equally as bad.
Here's a link to the video I made covering the install.
https://www.youtube.com/watch?v=eHJP2pXRznk
Purchased this one from the Electric Car Parts company, it's capable of moving up to 6 amps per cell. This is the highest capacity that I have seen to this point. I'm charging at around 30 amps with the generator and around 50 amps absolute max with solar, the battery bank is 100ah of CALB LiFePO4. Planning on upping this to CA180's later on with a long term goal of a system of approx. 800ah.
The batteries are very slightly used but are keeping together pretty well. It was a very tough call on deciding whether or not to fuse the balance lines - If they are fused and the wires short out things are protected, but if the fuses blow for whatever reason and now there is no balancing, theoretically a cell can be overcharged and that could be equally as bad.
Here's a link to the video I made covering the install.
https://www.youtube.com/watch?v=eHJP2pXRznk
Comments
-
The ballancing boards typically need to operate at at maximum cell voltage 3.600V to perform their ballancing, in off-grid applications it's generally not recommended to operate in the upper 5%. Usually the cells would be ballanced initially, after which the charging voltage would be limited to a value below that threshold, typically ~28V or 3.500 VPC, in reality it will be slightly less due to voltage drop.
Do you have a link to the balancers so others may view the specifications? Usually a BMS would protect the batteries should a sence wire become detached for some reason by cutting charging due to eronious cell count, perhaps the ballance has something similar.
1500W, 6× Schutten 250W Poly panels , Schneider MPPT 60 150 CC, Schneider SW 2524 inverter, 400Ah LFP 24V nominal battery with Battery Bodyguard BMS
Second system 1890W 3 × 300W No name brand poly, 3×330 Sunsolar Poly panels, Morningstar TS 60 PWM controller, no name 2000W inverter 400Ah LFP 24V nominal battery with Daly BMS, used for water pumping and day time air conditioning.
5Kw Yanmar clone single cylinder air cooled diesel generator for rare emergency charging and welding. -
I should say. You have a over-concerned about over charge. First we know, you are using a battery pack. When your battery charger( solar controller or other generator). You should have set a limit charging voltage. Like 16S LiFePo4 charging voltage should be 58.4 volt. When you connect to charging, the charging controller always know how much voltage the battery pack it is. and keep a constant voltage charging action.Your battery pack should have a basic BMS. when the BMS detect a single series reached 3.65. It will stop charging. that's why a BMS is so important.But if your balance function is dead. Means you will always has some series cells not fully charged everytime. Because once a series is fully charged, then all stoped chargeing. As time goes by, the difference of voltage will be much bigger. and some battery is under big stress. Very easy damage some of the cells.Thats why we suggest to use realiable production:1. Use brand new cells, make sure all cell are from a same production pilot. even they are same model NO. same brand.2. Make sure all the cell with same voltage, capacity, and internal resistance. So, the battery can use long time.3. USE a realiable BMS system. And health to use to the battery, charging it often. Not over discharge it.
CoreMax Technology company limited
P: 086-755-28080015 M: 0086-17688915553
Wechat: Sellbattery Skype: ODMbattery QQ:3572623261W: cmxbattery.com coremax-tech.com E: sales@coremax-tech.com
A: B2 MaoYuan Industry HuanGuan South Road Guanlan Long Hua BaoAn Shenzhen China. -
> whether or not to fuse...a cell can be overcharged
Ideally a system will a) balance with significant amps, b) stop charge/discharge if outside safe range, c) detect a lack of connection, d) sound an alarm if anything is wrong and e) provide some diagnostics (like a test button to simulate over voltage).
I am available for custom hardware/firmware development
-
Dynametix said:Balancing Boards usually need maximum voltage to operate.
-
BMS are part of what I'd really like to get some feedback on.I need to replace my lead-acid battery bank prematurely and I am going LiFePO4. I need between 600 and 800 kwh depending on how extravagant I want to be and here's what I am leaning toward. I should add that based on 6 years with 470 Ah lead acid bank, my pulls are typically less than 40A and I have only very rarely seen 50A for a short time. Before my wife and I destroyed the batteries recently, we rarely went under 80% unless there were several days of clouds or snow. We live at altitude in the sunny SW.96 Fortune 100Ah batteries https://www.electriccarpartscompany.com/Fortune-100Ah-Aluminum-Encased-Battery hooked in groups of 6 parallel, then series to get nominal 48V 600AhBMS leaning toward Orion Jr 2 https://www.electriccarpartscompany.com/Orion-Jr-2-BMSwhich also requires 16 LED https://www.electriccarpartscompany.com/3V-1S-Lithium-Lighted-Battery-BalancersI am curious about what you think about this overall system, is there a better way? I opted away from the cheaper BMS because I am worried about failure and Orion seems to have a good rep.I am also curious about anybody's experience with Electric Car Parts Co. There are Powerwall options from Greensun and Meritech that would be cheaper for more power but I am leery about an overseas transaction and the lack of support I'd be likely to receive. Thoughts?Among the things I am worried about is will shallow cycling (we do have occasional deep cycle needs but less than 20 times/year) will shorten the life of lithium batteries if they are fully charged between cycles?Should we charge them to the max rated voltage of 3.65 cells each cycle or would it be better to only go up to 90%?Will the BMS work if it is hooked only to each parallel group, i.e. each group of 6 batteries in parallel will have one balancer?What else should I be losing sleep over?Any thoughts are welcome and I would greatly appreciate your being gentle as I already know that I am very ignorant and on a nearly vertical learning curve about lithium set up.
12 * 300 W (10 fixed rooftop, 2 movable pole mount), Morningstar Tristar MPPT 60, Magnum 4448 PAE, 64 200Ah CALB in 4p16s arrangement with 16 LED Balancers and a Choice BMS300 (It is lousy and I don't recommend but it provides high and low voltage cutoff) -
generally speaking about overseas buying..... buyer beware... ask all the questions you can think of , ask to speak to XYZ again, etcget shipping insurance that you buy through your Customs Broker and if possible have the unit WELL palletized at the factory. Fork lift guys here don't give a HOOT.... It WASN'T me!
KID #51B 4s 140W to 24V 900Ah C&D AGM
CL#29032 FW 2126/ 2073/ 2133 175A E-Panel WBjr, 3 x 4s 140W to 24V 900Ah C&D AGM
Cotek ST1500W 24V Inverter,OmniCharge 3024,
2 x Cisco WRT54GL i/c DD-WRT Rtr & Bridge,
Eu3/2/1000i Gens, 1680W & E-Panel/WBjr to come, CL #647 asleep
West Chilcotin, BC, Canada -
Don't be intimidated it's not that complicated to build a DIY bank once the fundementals are understood.
For a BMS I contacted a manufacturer, they requested specifications, maximum load current, maximum charge current, battery capacity and charging source etcetera, their engineering department then recommend one based on my reply.
Both the batteries and BMS I ordered were from China, the support has been excellent from the supplier's I used. No experience with Electriccarparts.
Shallow cycles will extend the life expectancy, they can be used at partial states of charge without negative impact as well.
The only time they really need to be charged to 3.65 VPC is when initial ballancing is performed and perhaps every couple of years, under normal cycling it's best to only charge to ~3.40 VPC, somewhere in the 90% region, likewise discharge to 20% maximum which results in 70% of nominal capacity used.
The cells would be arranged parallel first then series, for 600Ah, 6 100Ah in parallel to form a cell block, the BMS sense wire for each cell will be connected to the cell block, 8 for 24V, 16 for 48V nominal. The ballancer would be redundant because the maximum voltage would be below it's operating range using 3.4 VPC , to understand this you need to consider how the cells are ballanced in the first place.
In EV applications the cells would typically be bottom ballanced to allow maximum capacity availability, in solar applications the cells are typically top ballanced, in both cases all cells or cell blocks are connected in parallel, then either charged to maximum voltage or discharged to a minimum voltage value. The cells can be top or bottom ballanced, but not both, with top ballancing a 3.65VP LiFePo4 single cell charger can be used to safeguard aginst voltage runaway which happens extremely fast without a proper charger, likewise with discharge things happen extremely fast, both over or under voltage can result in permanent damage to the cells.
The links below are a great source of general information, not nesesarally specifically for solar but useful for general information.
http://liionbms.com/php/bms_options.php#7
http://nordkyndesign.com/assembling-a-lithium-iron-phosphate-marine-house-bank/
The attached pdf is the BMS I ordered, it costs ~$100
One suggestion, start a new discussion to concentrate response to your particular project.
1500W, 6× Schutten 250W Poly panels , Schneider MPPT 60 150 CC, Schneider SW 2524 inverter, 400Ah LFP 24V nominal battery with Battery Bodyguard BMS
Second system 1890W 3 × 300W No name brand poly, 3×330 Sunsolar Poly panels, Morningstar TS 60 PWM controller, no name 2000W inverter 400Ah LFP 24V nominal battery with Daly BMS, used for water pumping and day time air conditioning.
5Kw Yanmar clone single cylinder air cooled diesel generator for rare emergency charging and welding. -
Thank you very much for that thorough reply. You're right, I shouldn't hijack this thread so I started a new one. I will copy your comment there so I can ask follow-up questions.mcgivor said:Don't be intimidated it's not that complicated to build a DIY bank once the fundementals are understood.
For a BMS I contacted a manufacturer, they requested specifications, maximum load current, maximum charge current, battery capacity and charging source etcetera, their engineering department then recommend one based on my reply.
Both the batteries and BMS I ordered were from China, the support has been excellent from the supplier's I used. No experience with Electriccarparts.
Shallow cycles will extend the life expectancy, they can be used at partial states of charge without negative impact as well.
The only time they really need to be charged to 3.65 VPC is when initial ballancing is performed and perhaps every couple of years, under normal cycling it's best to only charge to ~3.40 VPC, somewhere in the 90% region, likewise discharge to 20% maximum which results in 70% of nominal capacity used.
The cells would be arranged parallel first then series, for 600Ah, 6 100Ah in parallel to form a cell block, the BMS sense wire for each cell will be connected to the cell block, 8 for 24V, 16 for 48V nominal. The ballancer would be redundant because the maximum voltage would be below it's operating range using 3.4 VPC , to understand this you need to consider how the cells are ballanced in the first place.
In EV applications the cells would typically be bottom ballanced to allow maximum capacity availability, in solar applications the cells are typically top ballanced, in both cases all cells or cell blocks are connected in parallel, then either charged to maximum voltage or discharged to a minimum voltage value. The cells can be top or bottom ballanced, but not both, with top ballancing a 3.65VP LiFePo4 single cell charger can be used to safeguard aginst voltage runaway which happens extremely fast without a proper charger, likewise with discharge things happen extremely fast, both over or under voltage can result in permanent damage to the cells.
The links below are a great source of general information, not nesesarally specifically for solar but useful for general information.
http://liionbms.com/php/bms_options.php#7
http://nordkyndesign.com/assembling-a-lithium-iron-phosphate-marine-house-bank/
The attached pdf is the BMS I ordered, it costs ~$100
One suggestion, start a new discussion to concentrate response to your particular project.
12 * 300 W (10 fixed rooftop, 2 movable pole mount), Morningstar Tristar MPPT 60, Magnum 4448 PAE, 64 200Ah CALB in 4p16s arrangement with 16 LED Balancers and a Choice BMS300 (It is lousy and I don't recommend but it provides high and low voltage cutoff)
Categories
- All Categories
- 228 Forum & Website
- 136 Solar Forum News and Announcements
- 1.3K Solar News, Reviews, & Product Announcements
- 198 Solar Information links & sources, event announcements
- 895 Solar Product Reviews & Opinions
- 255 Solar Skeptics, Hype, & Scams Corner
- 22.4K Solar Electric Power, Wind Power & Balance of System
- 3.5K General Solar Power Topics
- 6.7K Solar Beginners Corner
- 1K PV Installers Forum - NEC, Wiring, Installation
- 2.1K Advanced Solar Electric Technical Forum
- 5.5K Off Grid Solar & Battery Systems
- 428 Caravan, Recreational Vehicle, and Marine Power Systems
- 1.1K Grid Tie and Grid Interactive Systems
- 652 Solar Water Pumping
- 815 Wind Power Generation
- 624 Energy Use & Conservation
- 618 Discussion Forums/Café
- 311 In the Weeds--Member's Choice
- 75 Construction
- 124 New Battery Technologies
- 108 Old Battery Tech Discussions
- 3.8K Solar News - Automatic Feed
- 3.8K Solar Energy News RSS Feed