Outback inverter with lifepo4 battery
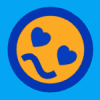
I have many storage batteries,48v 400ah,700ah to 1000ah lifepo4,now my clients want to work with Outback inverter,but the BMS I used is my own protocol for charge/discharge ,temperature protection.Is there special protocol needed to communicate with Outback?Or I could plug directly with Outback,which could be programmed with Outback itself.
Much appreciate for any help.
Comments
-
What you are asking, requires electronic engineering, to adapt a BMS to a different protocol system, good luck. i cannot help you.Powerfab top of pole PV mount | Listeroid 6/1 w/st5 gen head | XW6048 inverter/chgr | Iota 48V/15A charger | Morningstar 60A MPPT | 48V, 800A NiFe Battery (in series)| 15, Evergreen 205w "12V" PV array on pole | Midnight ePanel | Grundfos 10 SO5-9 with 3 wire Franklin Electric motor (1/2hp 240V 1ph ) on a timer for 3 hr noontime run - Runs off PV ||
|| Midnight Classic 200 | 10, Evergreen 200w in a 160VOC array ||
|| VEC1093 12V Charger | Maha C401 aa/aaa Charger | SureSine | Sunsaver MPPT 15A
solar: http://tinyurl.com/LMR-Solar
gen: http://tinyurl.com/LMR-Lister , -
Many BMS systems when connected to a charging source/discharging sink are setup for failsafe operation.
For example, you may have a two step process. Some inverters (and charge controllers have a "ground fault detect" circuit you may be able to "hack") have an input line which is an "inhibit" (remote on/off) or programmable input that may be used for on/off.
And you have a second output from your BMS that controls (for example) a big old relay.
One relay option is to use a "latching relay"... Uses a bit of power for an (example) internal electric motor that changes on/off state:
https://www.bluesea.com/search/results/latching relay
Another option is the old "crowbar" function. You have a high amperage fuse or circuit breaker to your battery bank, and you attach a standard (big relay) on the output of the fuse/breaker. When your BMS detects a reason for a hard fail (over/under voltage, over/under temperature), your BMS turns on the relay and shorts out the fuse/breaker and causes it to trip. This is what Schneider uses on (one of?) their Li Ion systems.
Or, you could use the latching relay between the battery bank and and the battery bus (like the BlueSea above), and use your BMS to cycle the relay when needed.
Getting into a digital data link between your BMS and the rest of the system... You will have to work with the manufacturer(s) for that.
Some vendors such as MorningStar publish their comm standards. Others like Midnite Solar may have an open interface over Internet or other methods (and may be willing to work with you).
-BillNear San Francisco California: 3.5kWatt Grid Tied Solar power system+small backup genset -
I use a simple Kilovac contactor with an economiser circuit built it. My Orion BMS provides a signal that drops when any fault is detected. It is fail safe because if I lose power it cuts off power to the contactor. It draws 130 milliamp to hold the contactor closed at 12v. I am grid tied so when the batteries drop out I still have the grid but I do have to restart the batteries after i determine what fault tripped them.
I communicated with Outback about using Canbus because my Skybox uses Canbus. Outback said they would have to develope the protocol with Orion for me to use Canbus. That was a longshot but the advantage is it would have given me better control over the charging process and possibly some control over using the grid when my batteries hit a SOC point. My BMS tracks SOC and while my Skybox is used mostly for load shifting I would want to maintain a reserve in the event of a power outage. Some day I may pursue that with Orion and see if they would be interested.8 kW Enphase micros AC coupled to a SolArk 12K -
This link may provide information that can be used to see how Outback recommend use with a particular battery manufacturer, Simpliphi in this case. Although I have not read this link in detail, I have read the Schneider/Simpliphi one and found much of the information helpful. The method I've adopted to turn the inverter off is unconventional but effective, using a second passive BMS which has external signals to drive contactors, perhaps not something to use for a client.
https://simpliphipower.com/product/access-outback/1500W, 6× Schutten 250W Poly panels , Schneider MPPT 60 150 CC, Schneider SW 2524 inverter, 400Ah LFP 24V nominal battery with Battery Bodyguard BMS
Second system 1890W 3 × 300W No name brand poly, 3×330 Sunsolar Poly panels, Morningstar TS 60 PWM controller, no name 2000W inverter 400Ah LFP 24V nominal battery with Daly BMS, used for water pumping and day time air conditioning.
5Kw Yanmar clone single cylinder air cooled diesel generator for rare emergency charging and welding. -
mcgivor said:This link may provide information tnihat can be used to see how Outback recommend use with a particular battery manufacturer, Simpliphi in this case.. .......The method I've adopted to turn the inverter off is unconventional but effective, using a second passive BMS which has external signals to drive contactors, perhaps not something to use for a client.
https://simpliphipower.com/product/access-outback/
The SimpliPhi link didn't provide much insight to how it interacts with the Radian. It may use Canbus since I recall seeing some video from a conference. I suspect it is proprietary since they are marketing it as an integrated product. Essentially they are positioning that as an solution to compete with the Tesla Powerall. In their case that product looks like it can perform off grid, grid tied or in self consumption mode.8 kW Enphase micros AC coupled to a SolArk 12K -
Ampster said:mcgivor said:This link may provide information tnihat can be used to see how Outback recommend use with a particular battery manufacturer, Simpliphi in this case. Although I have not read this link in detail, I have read the Schneider/Simpliphi one and found much of the information helpful. The method I've adopted to turn the inverter off is unconventional but effective, using a second passive BMS which has external signals to drive contactors, perhaps not something to use for a client.
https://simpliphipower.com/product/access-outback/
The SimpliPhi link didn't provide much insight to how it interacts with the Radian. It may use Canbus since I recall seeing some video from a conference..1500W, 6× Schutten 250W Poly panels , Schneider MPPT 60 150 CC, Schneider SW 2524 inverter, 400Ah LFP 24V nominal battery with Battery Bodyguard BMS
Second system 1890W 3 × 300W No name brand poly, 3×330 Sunsolar Poly panels, Morningstar TS 60 PWM controller, no name 2000W inverter 400Ah LFP 24V nominal battery with Daly BMS, used for water pumping and day time air conditioning.
5Kw Yanmar clone single cylinder air cooled diesel generator for rare emergency charging and welding. -
Thanks for all the suggestion and good ideas.I did add CANbus ,and RJ45 connector to the battery pack,normally every inverter brand has their own protocol for battery protection,like charge/discharge,current,which is similar with BMS function,and I checked with some inverter engineers,they told me most of the protocols are the same ,except the address,like for over charge protection,for A inverter the address is 0010,but for another brand maybe 0001.Then makes us very hard to competitive with all the inverters.
But I do notice that let lithium ion batter works as lead acid battery type, then the communication is not needed.We set the protection in our own BMS,I really hope that some organizations or institutes could set a standard protocol between lithium ion battery with Inverter,then all could benefit.
-
Ampster said:mcgivor said:This link may provide information tnihat can be used to see how Outback recommend use with a particular battery manufacturer, Simpliphi in this case.. .......The method I've adopted to turn the inverter off is unconventional but effective, using a second passive BMS which has external signals to drive contactors, perhaps not something to use for a client.
https://simpliphipower.com/product/access-outback/
The SimpliPhi link didn't provide much insight to how it interacts with the Radian. It may use Canbus since I recall seeing some video from a conference. I suspect it is proprietary since they are marketing it as an integrated product. Essentially they are positioning that as an solution to compete with the Tesla Powerall. In their case that product looks like it can perform off grid, grid tied or in self consumption mode.
The similar settings is what I used for Schneider gear, increasing current setpoints to reflect my larger capacity, the Outback inverter would appear to be capable of higher LBCO which is nice, the SW 2524-230 has a maximum of 24V, hopefully they will, or have increased this, as being able to disconnect using LBCO would save the battery from over discharge.1500W, 6× Schutten 250W Poly panels , Schneider MPPT 60 150 CC, Schneider SW 2524 inverter, 400Ah LFP 24V nominal battery with Battery Bodyguard BMS
Second system 1890W 3 × 300W No name brand poly, 3×330 Sunsolar Poly panels, Morningstar TS 60 PWM controller, no name 2000W inverter 400Ah LFP 24V nominal battery with Daly BMS, used for water pumping and day time air conditioning.
5Kw Yanmar clone single cylinder air cooled diesel generator for rare emergency charging and welding. -
Thanks, the detail helped. I come from years of working with Lithium and some of the terms used for Lead Acid are confusing. I didn't have solar charging with my former Radian and I used an external charger and turned off the internal charger on the Radian so I never had to deal with those issues. Now I have an Outback Skybox and recently added some solar panels but have not set up the charging parameters. I see that these settings also disable Float which I have done. When I get back in 10 days I will use this information to setup my Skybox for solar charging. Somewhere along the way someone said that Bulk is analogous to the Constant Current phase and Absorb is like the Constant Voltage phase where the current begins to taper.
8 kW Enphase micros AC coupled to a SolArk 12K -
What model Outback are you looking at connecting to?Some, maybe all have a manual on/off external switch input which might be useful. Hopefully the max charge/discharge current could be programmed into the Outback via other means which doesn't require the BMS.I agree that it is a real pain there are no open source CANBUS industry wide standards for solar equipment! One reason I avoid name branded equipment if it uses proprietary or closed standards or can't be easily reverse engineered.SimonOff-Grid with LFP (LiFePO4) battery, battery Installed April 2013
32x90Ah Winston cells 2p16s (48V), MPP Solar PIP5048MS 5kW Inverter/80A MPPT controller/60A charger, 1900W of Solar Panels
modified BMS based on TI bq769x0 cell monitors.
Homemade overall system monitoring and power management https://github.com/simat/BatteryMonitor
-
Ampster said:I see that these settings also disable Float which I have done. When I get back in 10 days I will use this information to setup my Skybox for solar charging. Somewhere along the way someone said that Bulk is analogous to the Constant Current phase and Absorb is like the Constant Voltage phase where the current begins to taper.I am not sure that disabling float is necessary or a good idea with LFP batteries. My experience is that charging to 3.45V/cell and floating at 3.35V/cell will keep the battery fully charged when there is enough sun regardless of external loads and has little if any impact on the life of the battery.You are right, Bulk is analogous to "Constant Current" or in reality as much current as the solar panels will provide and Absorb is Constant Voltage.SimonOff-Grid with LFP (LiFePO4) battery, battery Installed April 2013
32x90Ah Winston cells 2p16s (48V), MPP Solar PIP5048MS 5kW Inverter/80A MPPT controller/60A charger, 1900W of Solar Panels
modified BMS based on TI bq769x0 cell monitors.
Homemade overall system monitoring and power management https://github.com/simat/BatteryMonitor
-
karrak said:What model Outback are you looking at connecting to? NiSome, maybe all have a manual on/off external switch input which might be useful. Hopefully the max charge/discharge current could be programmed into the Outback via other means which doesn't require the BMS.
I use the BMS primarily as a check on my battery health. I am seeing bigger deltas at each end and therefore have high and low cell alarms and low voltage cutouts set to drop the battery out of the system with a contactor to protect the pack. I haven't found an external input on the Skybox that could give me that control.
Thanks for the feedback.8 kW Enphase micros AC coupled to a SolArk 12K -
Since we're battery manufacturer,we could connect all the models of Outback,mainly Skybox.I just found one clients used the battery we produced with Outback without communicating,and we didn't design any communication like RS485,CAN. i think there's no problem for Outback now.But I keep searching more protocols,now I have two inverter brands protocol.For the charge issue,LFP battery,the charge voltage is 3.65v,but the rated voltage is 3.2v,normally the cut-off voltage will set 2V.NCM battery,charge voltage is 4.2V,rated 3.65v,2.5 cut-off. Many users will increase the cut-off voltage to avoid the over-discharge.We suggest to control the DOD (80%-90%) to increase the service life,floating charge is not necessary for lithium ion battery.
-
Jacob_U said:Since we're battery manufacturer,we could connect all the models........8 kW Enphase micros AC coupled to a SolArk 12K
-
Ampster said:Jacob_U said:Since we're battery manufacturer,we could connect all the models........
-
mcnutt13579 said:Ampster said:Jacob_U said:Since we're battery manufacturer,we could connect all the models........1500W, 6× Schutten 250W Poly panels , Schneider MPPT 60 150 CC, Schneider SW 2524 inverter, 400Ah LFP 24V nominal battery with Battery Bodyguard BMS
Second system 1890W 3 × 300W No name brand poly, 3×330 Sunsolar Poly panels, Morningstar TS 60 PWM controller, no name 2000W inverter 400Ah LFP 24V nominal battery with Daly BMS, used for water pumping and day time air conditioning.
5Kw Yanmar clone single cylinder air cooled diesel generator for rare emergency charging and welding. -
I don't see any problems.
Letting people and companies ask (and answer) questions related to solar--I find it interesting.
There will always be some "leakage" between the design and marketing. But we have had good discussions with the folks from Midnite Solar (as an example) over the years.
-Bill "moderator" B.Near San Francisco California: 3.5kWatt Grid Tied Solar power system+small backup genset -
My apologies to @Jacob_U who I now realize started this thread.
8 kW Enphase micros AC coupled to a SolArk 12K -
No problem.
-Bill
Near San Francisco California: 3.5kWatt Grid Tied Solar power system+small backup genset -
@Ampster ,I started this conversion,because I really met the cases,before we just produced the battery,and the clients sent us the protocol,but these several cases for Outback,clients always told us that there's no communicating for Outback,I had searched over 1 weeks to figure our the answers,then found the forum,really like everyone share his views here,solution is the first thing I want to get,it's much better if promotion works.😁
-
You are correct. If you had time and money to spend developing a Canbus protocol with Ouback you may never recover your investment. It is much simpler for a DIYer like myself to set the high and low limits on the Outback and use my BMS for information and as a last resort fail safe.
I appreciate that you were at least interested enough to ask the questions. Maybe, like @mcnutt13579 said, someone will develop a standard. I see Canbus chargers for Lithium but in that case there are only about 3 or 4 commands that are important. Lead Acid is much more complex in term of the number of settings.
8 kW Enphase micros AC coupled to a SolArk 12K -
Probably the most universal way for a BMS to communicate simple on/off to inverters and chargers are two 5V 1A outputs. Not a complete solution, but easier to work with than most protocols.
Morningstar suggests that their charge controller can be told to stop charging safely by using a relay to add resistance to the battery temperature sensor. This probably works on many other charge controllers. Don't put a relay or mosfet in series with the charger->battery line.
I wired a relay to the on/off switch on my inverter. This works fine to stop load/over-discharge.
I am available for custom hardware/firmware development
Categories
- All Categories
- 228 Forum & Website
- 136 Solar Forum News and Announcements
- 1.4K Solar News, Reviews, & Product Announcements
- 199 Solar Information links & sources, event announcements
- 898 Solar Product Reviews & Opinions
- 256 Solar Skeptics, Hype, & Scams Corner
- 22.5K Solar Electric Power, Wind Power & Balance of System
- 3.5K General Solar Power Topics
- 6.7K Solar Beginners Corner
- 1K PV Installers Forum - NEC, Wiring, Installation
- 2.1K Advanced Solar Electric Technical Forum
- 5.6K Off Grid Solar & Battery Systems
- 428 Caravan, Recreational Vehicle, and Marine Power Systems
- 1.1K Grid Tie and Grid Interactive Systems
- 654 Solar Water Pumping
- 816 Wind Power Generation
- 624 Energy Use & Conservation
- 619 Discussion Forums/Café
- 312 In the Weeds--Member's Choice
- 75 Construction
- 124 New Battery Technologies
- 108 Old Battery Tech Discussions
- 3.8K Solar News - Automatic Feed
- 3.8K Solar Energy News RSS Feed