Homemade Prototype
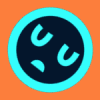
hotdawg23
Solar Expert Posts: 32 ✭
I know homemade panels most likely have a short life but i am building a panel as an experiment and have decided to use glass as a cover for this 21x45 inch panel. Thyis will be used to charge a backup battery on my automatic gate.
I have encountered a problem on the glass as most glass you buy these days have a slight tint to it.
question is... how would this tint effect the solar cell output?
I have encountered a problem on the glass as most glass you buy these days have a slight tint to it.
question is... how would this tint effect the solar cell output?
Comments
-
Re: Homemade Prototype
it will decrease it.
I'm guess 10 to 20%. And that is wild guess.
Just put a few extra cells on it to compensate.
Small panels like this are actually economical to do yourself since commercial ones cost around $2.90 a watt and you can make your own for $1/watt or so.
Of course you might mess up a panel or two before you get it right in which case you should of never bothered. -
Re: Homemade Prototype
Depends on the wavelengths that it blocks. The only sure way to know is to take your mostly-completed project out in full sunlight and take some measurements, then place the glass over it and take the same measurements.4.5 kw APC UPS powered by a Prius, 12 kw Generac, Honda EU3000is -
Re: Homemade Prototype
Hmm, The entire glass is tinted? or just a certain area?
I also want to know, how are you going to make the solar panel, what are you using as backing? Are you going to encapsulate the cells?
How many cells are you going to use per panel? is this for a 12 volt system or 24 volt system?
Do you plan to use diodes?
What size cells are you using? -
Re: Homemade Prototype
Simplest way is to use a solar cell (or small panel) connected to a Amp Meter.
Connect to the cell in full sun. Measure short circuit current. Say it is 0.95 amps.
Then place the cell under the glass and measure current again. Say 0.73 amps.- 0.73a/0.95 amps = 0.768 = 76.8% efficient or 23% loss
-BillNear San Francisco California: 3.5kWatt Grid Tied Solar power system+small backup genset -
Re: Homemade PrototypeUrbandialect wrote: »Hmm, The entire glass is tinted? or just a certain area?
I also want to know, how are you going to make the solar panel, what are you using as backing? Are you going to encapsulate the cells?
How many cells are you going to use per panel? is this for a 12 volt system or 24 volt system?
Do you plan to use diodes?
What size cells are you using?
I ran across new factory built double paned window that appears to have just the slightest of tint to them. When i took one end off it i discovered that the space between the glass panes themselves was about 3/8 of an inch. i plan to mount the solar cells on say 1/4 inch pegboard and slide the completed unit in between the panes and after testing it i will seal the end back up after i lay it in direct sun for abour 2 hours. this will pull a vacuum and get rid of all the moisture that resides there.
Yes to diodes.
Since this is an experiment it will be 12V. The window is 21x45 inches.
My cells are 3x6. SOOOO it will be 3 wide and 15 high.
therefore it will have 45 cells at.5V per and 1.8Watts per -
Re: Homemade Prototype
I do know window glass is tyically coated to block some wave lengths of light, as a thermal barrier (to increase the R value) not sure how it will effect a solar panel built from it. I know they are considered a poor choice for a solar oven.
I also know that panel manufaturers use to always say how they were using low iron glass, not sure if they still are or if it's just become industry wide, or the panels are so cheap they can't afford to...Home system 4000 watt (Evergreen) array standing, with 2 Midnite Classic Lites, Midnite E-panel, Magnum MS4024, Prosine 1800(now backup) and Exeltech 1100(former backup...lol), 660 ah 24v Forklift battery(now 10 years old). Off grid for 20 years (if I include 8 months on a bicycle).
- Assorted other systems, pieces and to many panels in the closet to not do more projects. -
Re: Homemade Prototype
thinking about baking pegboard makes me wince .. i got glass from doitbest.com, they have several sizes available, glass front and back, check this out ---
http://www.youtube.com/watch?v=TkkSr7BqAsM
diodes can actually be put anywhere in the circuit, not a big deal to me anyway .. -
Re: Homemade PrototypeI ran across new factory built double paned window that appears to have just the slightest of tint to them. When i took one end off it i discovered that the space between the glass panes themselves was about 3/8 of an inch. i plan to mount the solar cells on say 1/4 inch pegboard and slide the completed unit in between the panes and after testing it i will seal the end back up after i lay it in direct sun for abour 2 hours. this will pull a vacuum and get rid of all the moisture that resides there.
Yes to diodes.
Since this is an experiment it will be 12V. The window is 21x45 inches.
My cells are 3x6. SOOOO it will be 3 wide and 15 high.
therefore it will have 45 cells at.5V per and 1.8Watts per
I see, that should work, I guess you'll have to run the bus bars out the side where the 3/8 opening is and finish the final wiring for your + and - leads outside of the panel,
Plus it should be easy to break back in and remove the pegboard w/the cells on it if anything was to go wrong after putting it together.. I like it!!
22 volts should be good, have alot of voltage to play with in the event you have any voltage drop(loss) due to wiring and distance, I'm going to start wiring mine for 20 plus voltage too, i plan to use alot of safety devices and diodes that steal alittle power here and there, so i'll build it alittle over to compensate
If you can take a picture of the finished product and post it so i can check out your design, that way if i ever come across some glass like that i'll know how to go about making the panel, only going threw one tint of the glass instead of both tinted pieces is a great ideal -
Re: Homemade Prototype
pegboard = flammable
just saying, be careful folksPowerfab top of pole PV mount | Listeroid 6/1 w/st5 gen head | XW6048 inverter/chgr | Iota 48V/15A charger | Morningstar 60A MPPT | 48V, 800A NiFe Battery (in series)| 15, Evergreen 205w "12V" PV array on pole | Midnight ePanel | Grundfos 10 SO5-9 with 3 wire Franklin Electric motor (1/2hp 240V 1ph ) on a timer for 3 hr noontime run - Runs off PV ||
|| Midnight Classic 200 | 10, Evergreen 200w in a 160VOC array ||
|| VEC1093 12V Charger | Maha C401 aa/aaa Charger | SureSine | Sunsaver MPPT 15A
solar: http://tinyurl.com/LMR-Solar
gen: http://tinyurl.com/LMR-Lister , -
Re: Homemade Prototype
most automatic gate openers I've seen use either a 5 or 10 watt panel to maintain its battery. Depends on how often you cycle the gate, and the weight of the lever it's moving. -
Re: Homemade Prototypethinking about baking pegboard makes me wince .. i got glass from doitbest.com, they have several sizes available, glass front and back, check this out ---
http://www.youtube.com/watch?v=TkkSr7BqAsM
diodes can actually be put anywhere in the circuit, not a big deal to me anyway ..
You are correct about that pegboard idea. i got that from one of the webs where DIY guys were making panels.
I am open for suggestion on this as well.
I thought about using glass as a mounting agent instead of pegboard and sliding the whole thing in. Still a feasible idea xcept glass is expensive.
I did view the utube guy and his idea is same as mine xcept he is gluing the glass to the solar cells and then fitting the frame to it.
My window cost $20 and is somewhat less than the utube way. -
Re: Homemade Prototype
If you watch the entire series there are so many red flags raised along the way. The man is patient and methodical, but perhaps too focused. He mounts his panels almost flat on a tin roof, no air space, upon an old wooden garage. Plus, he has 8 batteries connected in two strings of 4 in a straight parallel fashion, Additionally he shuns the idea of a charge controller at all, rather switch his panels off and on manually to maintain 13.8 volts.
This is fine if you want to sit in the garage and watch a meter all day. Is he going to run back and forth to the garage every time the sun goes behind the clouds? And then he talks about adding some sort of remote timer to regulate the charge, well, then why not just add a controller and save the hassle?
I asked him about the space beneath his panels, and did it effect his output. He replied that there is an inch of clearance, and that he can watch the voltage fluctuate on a breezy day.thinking about baking pegboard makes me wince .. i got glass from doitbest.com, they have several sizes available, glass front and back, check this out ---
http://www.youtube.com/watch?v=TkkSr7BqAsM
diodes can actually be put anywhere in the circuit, not a big deal to me anyway .. -
Re: Homemade PrototypeUrbandialect wrote: »I see, that should work, I guess you'll have to run the bus bars out the side where the 3/8 opening is and finish the final wiring for your + and - leads outside of the panel,
Plus it should be easy to break back in and remove the pegboard w/the cells on it if anything was to go wrong after putting it together.. I like it!!
22 volts should be good, have alot of voltage to play with in the event you have any voltage drop(loss) due to wiring and distance, I'm going to start wiring mine for 20 plus voltage too, i plan to use alot of safety devices and diodes that steal alittle power here and there, so i'll build it alittle over to compensate
If you can take a picture of the finished product and post it so i can check out your design, that way if i ever come across some glass like that i'll know how to go about making the panel, only going threw one tint of the glass instead of both tinted pieces is a great ideal
Uh ohh. Brings up another question on voltage. I should be producing 22+ volts for a 12 V battery. What can i use to bring that down to 12V in order to charge the12V battery. Can a charge controller autimatically do that? -
Re: Homemade PrototypeUh ohh. Brings up another question on voltage. I should be producing 22+ volts for a 12 V battery. What can i use to bring that down to 12V in order to charge the12V battery. Can a charge controller autimatically do that?
Two types of controllers exist (3 if you count your DVM and a switch, as in the video)
PWM, simple, but they waste power as heat,
MPPT, complex. $$, but they wring every watt out of your panels.Powerfab top of pole PV mount | Listeroid 6/1 w/st5 gen head | XW6048 inverter/chgr | Iota 48V/15A charger | Morningstar 60A MPPT | 48V, 800A NiFe Battery (in series)| 15, Evergreen 205w "12V" PV array on pole | Midnight ePanel | Grundfos 10 SO5-9 with 3 wire Franklin Electric motor (1/2hp 240V 1ph ) on a timer for 3 hr noontime run - Runs off PV ||
|| Midnight Classic 200 | 10, Evergreen 200w in a 160VOC array ||
|| VEC1093 12V Charger | Maha C401 aa/aaa Charger | SureSine | Sunsaver MPPT 15A
solar: http://tinyurl.com/LMR-Solar
gen: http://tinyurl.com/LMR-Lister , -
Re: Homemade Prototype
You have to look at the Vmp of the panel vs Voc... Vmp~17.5 volts for proper charging of a 12 volt battery bank; Voc~21 volts or so...
Which is your 22 volts? Voc (open circuit) or Vmp (maximum power)?
The farther away Vmp gets from ~17.5-18.0 volts, the poorer the efficiency is with a PWM controller.
35 volt Vmp on a 12 volt battery bank, about 50% efficient.
-BillNear San Francisco California: 3.5kWatt Grid Tied Solar power system+small backup genset -
Re: Homemade Prototype35 volt Vmp on a 12 volt battery bank, about 50% efficient.
I have first hand experience in this department, if you go over 30 Vmp and try to charge a 12 volt battery bank using a PWM charge controller? IT WILL NOT WORK, have to say under 30 Vmp per panel -
Re: Homemade PrototypeYou have to look at the Vmp of the panel vs Voc... Vmp~17.5 volts for proper charging of a 12 volt battery bank; Voc~21 volts or so...
Which is your 22 volts? Voc (open circuit) or Vmp (maximum power)?
The farther away Vmp gets from ~17.5-18.0 volts, the poorer the efficiency is with a PWM controller.
35 volt Vmp on a 12 volt battery bank, about 50% efficient.
-Bill
Bill,
Have not tested it yet but the cells are rated at .5V each so i am guessing that would be the Voc. I understand that the Vmp will be somewhat less than that so from what i am hearing the 22 volts would drop to about the 17 or 18V area. Won;t know until i get it all assembled.
Also, i am under the impression that the PWM controller would be a bad choice.
As a side note, i ran accross 20 more of those factory windows today at $20 each. These are 32x56 inches and very heavy but same construction as my prototype. I am buying them for future use. So, all i am learning here , can be applied when i start the real thing. -
Re: Homemade Prototype
Roughly Vmp=0.5 volts... Unloaded (Voc) would be higher.
PWM are fine and have been used for many decades... More or less, I suggest that 200 watts or less, PWM is probably more cost efficient.
400 watts or more, look at MPPT...
However, if you have specialized needs (such as long distance from Array to Charge Controller), then MPPT might be a better choice for 200 watt or slightly smaller array.
-BillNear San Francisco California: 3.5kWatt Grid Tied Solar power system+small backup genset -
Re: Homemade PrototypeUrbandialect wrote: »I have first hand experience in this department, if you go over 30 Vmp and try to charge a 12 volt battery bank using a PWM charge controller? IT WILL NOT WORK, have to say under 30 Vmp per panel
What do you mean, it will not work ? If you stay below the kill voltage of the controller, it has to work. But as your VMP gets further from battery voltage, you have to rely on the Isc spec, that's what you will be charging at, not the panel wattage. All the watts between the battery voltage, and the PV VMP - get lost.Powerfab top of pole PV mount | Listeroid 6/1 w/st5 gen head | XW6048 inverter/chgr | Iota 48V/15A charger | Morningstar 60A MPPT | 48V, 800A NiFe Battery (in series)| 15, Evergreen 205w "12V" PV array on pole | Midnight ePanel | Grundfos 10 SO5-9 with 3 wire Franklin Electric motor (1/2hp 240V 1ph ) on a timer for 3 hr noontime run - Runs off PV ||
|| Midnight Classic 200 | 10, Evergreen 200w in a 160VOC array ||
|| VEC1093 12V Charger | Maha C401 aa/aaa Charger | SureSine | Sunsaver MPPT 15A
solar: http://tinyurl.com/LMR-Solar
gen: http://tinyurl.com/LMR-Lister , -
Re: Homemade PrototypeWhat do you mean, it will not work ? If you stay below the kill voltage of the controller, it has to work. But as your VMP gets further from battery voltage, you have to rely on the Isc spec, that's what you will be charging at, not the panel wattage. All the watts between the battery voltage, and the PV VMP - get lost.
think of it like this, each cell = 0.5 VMP. No matter what your voltage meter reads, so if each cell is 0.5 then the maximum number of cells you can have in a panel is 60 with out going over 30 VMP, once you go over that # your PWM charge controller is looking for a 24 volt battery to charge, not the 12 volt battery you have hooked up to it.
I had 2 panels that failed and where only putting out 11 volts (on my volt meter), i figured if i wired them together in series, this should boost the voltage to 22 volts, and guess what the voltage was on my volt meter when i did that? 22 volts! I already had 2 panels i made at 20 volts hooked up to my PWM charge controller that where working fine, I unhooked them and i hooked the 2 panel wired in series to the charge controller, and nothing happen, wouldn't charge the battery, hooked the other 2 panels up and the green light came on and i was back in business, tried to wire the 2 panels in series in parallel with the other 2 panels and the green light went off.
I came here on this site and these guys finally help me get to the bottom of it, Look at the VMP rating on the charge controller and know that no matter what your voltage meter reads, each one of those cells is roughly 0.5 VMP, that's number is the safest estimation to go with -
Re: Homemade Prototype
Actually most of the better PWM controllers will take 12, 24, 48, or sometimes even 96 Volts input. But they expect that nominal to be the same on the output. When it isn't, the difference goes to heat and the power is lost. Urbandialect got caught on a cheap one that had fits from over-voltage on the input.
Confucius say: Beware the cheap Chinese charge controller! -
Re: Homemade PrototypeRoughly Vmp=0.5 volts... Unloaded (Voc) would be higher.
PWM are fine and have been used for many decades... More or less, I suggest that 200 watts or less, PWM is probably more cost efficient.
400 watts or more, look at MPPT...
However, if you have specialized needs (such as long distance from Array to Charge Controller), then MPPT might be a better choice for 200 watt or slightly smaller array.
-Bill
Bill
thanks for this info.
I went to Ebay looking at the controllers and found that the PWM models are really cheap and do come in several AMP loads and input from 12V to 48V mostly. They do talk about maximum watts as well. Some would handle larger vollts.
However when i got to the MPPT charge controllers, which ran 3 to 4 times the cost of the PWM, i never found one that mentioned watts. Did i miss something here?
I did conclude, based on what you are telling me and what i absorbed from Ebay, that neither one of these would be appropriate for an array?
I have a controller in hand that i will use on the prototype. It can handle 12V or 24Volts. -
Re: Homemade Prototype
More or less, controllers are rated on output current and output voltage... So, a 25 amp controller charging a 12 volt battery at 14.5 volts would be:- 25 amps * 14.5 volts charging = 356 Watts
- 25 amps * 17.5 volts = 437.5 Watt Solar array
- 356 watt out / 437.5 watts in = 0.81 = 81% efficiency.
You can do similar calculations for MPPT controllers--but here you would need to derate Vmp for your typical weather+ambient temperature+wind+mounting variables (how hot does the panel rise above ambient, how much do you loose to dust/age, etc.). (Vmp falls with increasing temperature--Imp does rise very slightly with increasing temperatures, but can be ignored for everything we do here).
Or, you can use the 0.77 to 0.82 or so derating (I am conservative, so I aways use the 0.77 derating... At worst, you will be 5% points "happier"with your system performance).
Clear as mud?
-BillNear San Francisco California: 3.5kWatt Grid Tied Solar power system+small backup genset -
Re: Homemade PrototypeMore or less, controllers are rated on output current and output voltage... So, a 25 amp controller charging a 12 volt battery at 14.5 volts would be:
- 25 amps * 14.5 volts charging = 356 Watts
- 25 amps * 17.5 volts = 437.5 Watt Solar array
- 356 watt out / 437.5 watts in = 0.81 = 81% efficiency.
You can do similar calculations for MPPT controllers--but here you would need to derate Vmp for your typical weather+ambient temperature+wind+mounting variables (how hot does the panel rise above ambient, how much do you loose to dust/age, etc.). (Vmp falls with increasing temperature--Imp does rise very slightly with increasing temperatures, but can be ignored for everything we do here).
Or, you can use the 0.77 to 0.82 or so derating (I am conservative, so I aways use the 0.77 derating... At worst, you will be 5% points "happier"with your system performance).
Clear as mud?
-Bill
Good explanation. I believe I get it. Is the 14.5 volts in the formula theoritical? Cause i somehow got the impression it might be Voc? At any rate i am using a 10 amp charger and 10 amps will be maximum output no matter what the volts. Therefor, plugging in the 10 amps into the formula i will be under the 200 watts safe zone you mentioned before for the PWM. So i will go ahead with the prototype using this charger. -
Re: Homemade Prototype
Note, the 14.5 volts is the battery charging voltage (typically between 14.2 and 14.85 depending on battery type), not Voc or Vmp...
Vmp>Vbatt-charging -- So, to allow for Vmp drop with high temperature, wiring and controller voltage drops, you need Vmp~17.5 volts minimum.
Voc (open circuit) has no meaning for charging--it is usually calculated as the maximum open circuit voltage on a cold day (can damage controller input circuit when not charging battery bank).
Very roughly, in an area with extreme hot and cold weather conditions, the controller input range is roughly 2:1 between Voc-cold and Vmp-hot (i.e., around 30 volts to 15 volts with "12 volt" panels).
The 200 watt or lower for PWM is just a reflection that small arrays are not usually worth spending the big $$$$ for a MPPT controller... It is not a safety or limitation on PWM controllers... There are 48 volt 60 amp charge controllers which can handle:- 60 volts charging * 60 amps = 3,600 watts (there may be some deratings--check manuals)
One other issue for configuring systems... Maximum current through a PWM controller is controlled by the size of the solar array.
For a MPPT type controller, the maximum output current is actually controlled by the MPPT internal switching power supply--So the array can (safely) be larger than the MPPT controller's output current rating without any problems (as long as the Varray is withing the MPPT controller's input limits).
-BillNear San Francisco California: 3.5kWatt Grid Tied Solar power system+small backup genset -
Re: Homemade Prototype
And in case anyone is wondering, the smallest (good) MPPT controller is the Morningstar SunSaver 15 Amp: http://www.solar-electric.com/mosumpsochco.html It's spec'd for 200 Watts on a 12 Volt system and 400 Watts on a 24 Volt system.
Rogue http://www.roguepowertech.com/products/mpt3024.htm offers a 30 Amp MPPT controller and Blue Sky http://www.solar-electric.com/blskyenmpsoc.html offers models from 15 Amps to 60 Amps. How beneficial is MPPT on a small system? Depends on the circumstances. Usually it's not cost effective, but if you have to squeeze out every possible Watt the options are there.
Just thought I'd mention them. -
Re: Homemade PrototypeNote, the 14.5 volts is the battery charging voltage (typically between 14.2 and 14.85 depending on battery type), not Voc or Vmp...
Vmp>Vbatt-charging -- So, to allow for Vmp drop with high temperature, wiring and controller voltage drops, you need Vmp~17.5 volts minimum.
Voc (open circuit) has no meaning for charging--it is usually calculated as the maximum open circuit voltage on a cold day (can damage controller input circuit when not charging battery bank).
Very roughly, in an area with extreme hot and cold weather conditions, the controller input range is roughly 2:1 between Voc-cold and Vmp-hot (i.e., around 30 volts to 15 volts with "12 volt" panels).
The 200 watt or lower for PWM is just a reflection that small arrays are not usually worth spending the big $$$$ for a MPPT controller... It is not a safety or limitation on PWM controllers... There are 48 volt 60 amp charge controllers which can handle:- 60 volts charging * 60 amps = 3,600 watts (there may be some deratings--check manuals)
One other issue for configuring systems... Maximum current through a PWM controller is controlled by the size of the solar array.
For a MPPT type controller, the maximum output current is actually controlled by the MPPT internal switching power supply--So the array can (safely) be larger than the MPPT controller's output current rating without any problems (as long as the Varray is withing the MPPT controller's input limits).
-Bill
Now i know why i majored in Acounting in college rather than Electrical Engineering!!
Anyway, here is where i get confused. I was under impression that AMPS was a product of the array, or panel, but from what i see it is from the charge controller output?
So my next thought was, if you are on a 12V system the only difference in the level of AMPS was the time it takes to re charge the battery or batteries? -
Re: Homemade Prototype
I usually fall back on water analogies, or in this case, mechanical analogies... (so sue me :roll:):- PWM: Nothing more than an ON/OFF switch. Current in = current out. Voltage at the array is either Voc (open circuit, switch off), or Vbatt-charging (switch on, battery bank sets system voltage). Turn switch on/off (fast or slow) to control average current flow into the battery bank. Nothing more than a single speed bicycle. You have to match the input voltage/current (peddle RPM/torque) to the output battery bank (wheel speed). Torque (current) in from the peddles equals torque (current out) to the wheel.
- MPPT: Think of a Transmission on a car or bike... The governing equation is Power=Volts*Current... When Vmp~Vbatt-charging, the transmission is in high gear or (roughly) 1:1. When the Vmp-array>Vbatt-charging, the transmission is in "low gear"... Takes the high voltage/low current from the array and (efficiently) down converts to low voltage/high current (engine turns fast, low torque; wheels turn slow with high torque).
- Note that P=V*I... If you double V (voltage), then you will have 1/2 the current (amps) for the same power:
- 145 watts = 10 amps * 14.5 volts (energy into battery bank)
- 145 watts = 5 amps * 29 volts (energy out from a "24 volt" solar array)
- The conversion from input to output (picking the "right gear") is continuously being performed by the on board computer based on the array/sun conditions and the needs of the battery bank. As the battery bank approaches full--the MPPT controller falls back to (more or less) PWM type operation.
-BillNear San Francisco California: 3.5kWatt Grid Tied Solar power system+small backup genset -
Re: Homemade PrototypeBill/Cariboo
Now i know why i majored in Acounting in college rather than Electrical Engineering!!
Anyway, here is where i get confused. I was under impression that AMPS was a product of the array, or panel, but from what i see it is from the charge controller output?
It's both.
Panels have a current rating as well as Voltage rating (actually three Voltage ratings) which together become the power in Watts: Vmp * Imp, more or less. You don't have a real power figure without both current and Voltage.
But when you "switch circuits" between one part of a system and another, things change. So the Voltage and the current flowing to the charge controller is not the same as the Voltage and current flowing from the charge controller. This is why panel Voltage needs to be higher than charging Voltage: as in 17.5 Volts to get 14.4 Volts for charging a "12 Volt" battery.
When more wire and components (resistance) are things change. Inevitably there is a power loss, even with MPPT. The MPPT advantage is to be able to convert higher Voltage into more charging current, whereas with a PWM controller that potential "extra" power is just lost as heat (the 81% efficiency Bill mentioned).So my next thought was, if you are on a 12V system the only difference in the level of AMPS was the time it takes to re charge the battery or batteries?
True, to a certain extent. More current = faster charge rate, which is desirable when you have basically a 4 hour window of opportunity to recharge the batteries in. But at the same time there is both a minimum rate and a maximum rate for any given battery: too low and nothing happens, too high and the battery cooks.
Categories
- All Categories
- 229 Forum & Website
- 137 Solar Forum News and Announcements
- 1.4K Solar News, Reviews, & Product Announcements
- 199 Solar Information links & sources, event announcements
- 898 Solar Product Reviews & Opinions
- 256 Solar Skeptics, Hype, & Scams Corner
- 22.5K Solar Electric Power, Wind Power & Balance of System
- 3.5K General Solar Power Topics
- 6.7K Solar Beginners Corner
- 1K PV Installers Forum - NEC, Wiring, Installation
- 2.1K Advanced Solar Electric Technical Forum
- 5.6K Off Grid Solar & Battery Systems
- 428 Caravan, Recreational Vehicle, and Marine Power Systems
- 1.1K Grid Tie and Grid Interactive Systems
- 654 Solar Water Pumping
- 816 Wind Power Generation
- 624 Energy Use & Conservation
- 619 Discussion Forums/Café
- 312 In the Weeds--Member's Choice
- 75 Construction
- 124 New Battery Technologies
- 108 Old Battery Tech Discussions
- 3.8K Solar News - Automatic Feed
- 3.8K Solar Energy News RSS Feed