Under performing LiPo
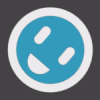
onebad
Registered Users Posts: 12 ✭✭
I have two 100AH lithium batteries and two 100W solar panels and a 60amp DC to DC charger, all Renogy. The system works but seems to be under performing. On sunny days the batteries will charge up to 13.2 V but if I moved into shade within minutes the voltage drop to 12.8 even if I was in the sun for hours. Further, if I drive and run the charger (I put a switch in front of the charger so I can control if and when it runs) the batteries will get up to 14.2 but when I turn off the charger within 10 minutes the voltage will drop to 12.8. I have a fridge/freezer that is the biggest draw on my system but that shouldn’t cause such a drastic drop in voltage, besides I often turn my fridge off at night and I still have to start my engine/charger to keep the batteries from draining. I sent one of my batteries to Renogy and they said it tested and held a 14.4 charge. I haven’t sent them the other one because I’m laid off and if it tests good it will cost me $60 to have it sent back. I see people on YouTube who’s battery bank sits at 13.7 or higher, why won’t my battery bank hold that level of charge? Thank you.
Tagged:
Comments
-
The title says LiPo but are they in fact LiFePo4 ? How many hours were they on charge what state of discharge were they at when charging commenced.
A 100Ah battery discharged to 20% SOC would take approximately 7 hours with 2 × 100W panels in perfect sun, using 75% average output of rated wattage. Since solar charging is only at peak for a short period of time, it's possible they are not receiving enough input to complete the cycle. Seeing the voltage drop from 13.2v when on charge then dropping to12.8V is normal as the charging source has to be at a higher potential in order for current to flow.
As an experiment try charging over multiple days until the voltage reaches the target setpoint or increase the array capacity to 400W to ensure the capacity can be replaced in a single day if deeply discharged.
1500W, 6× Schutten 250W Poly panels , Schneider MPPT 60 150 CC, Schneider SW 2524 inverter, 400Ah LFP 24V nominal battery with Battery Bodyguard BMS
Second system 1890W 3 × 300W No name brand poly, 3×330 Sunsolar Poly panels, Morningstar TS 60 PWM controller, no name 2000W inverter 400Ah LFP 24V nominal battery with Daly BMS, used for water pumping and day time air conditioning.
5Kw Yanmar clone single cylinder air cooled diesel generator for rare emergency charging and welding. -
Thanks for responding. The batteries are Renogy lithium iron phosphate LiFePo4. The main question I have is, why on the occasions when The bank does get above 12.8v it seems to lose voltage very quickly. Example, last night Before I parked for the night at around 9:30 I went for a ride and charge the batteries up to 13.1V, (12.9 when I turned the charger off) I turned off my fridge and had only my Maxxair fan and one LED light on. I had to run the engine/charger at 1:30ish because the voltage had dropped to 11.8 and experience has been that won’t make it through the rest of the night without shutting down. So from 9:30 to 1:30 my vent fan and one 15 watt LED took my bank from 12.9v to 11.8v. I may be wrong but that seems excessive.
As for adding panels to my array I sized the charge controller so that I can add two more 100 watt panels but as I said in my post I’m laid off now so that’s not an option. Thanks again for responding. -
12.9 volts is 3.225 volts per cell which could be anywhere on a very flat charge/discharge curve. My guess is your batteries are not getting charged to their capacity. Can you increase your charging to 3.5 per cell or 14 volts for the pack? If you have a good meter see how many Amphours you can add at that voltage. It is normal for Lithium batteries to settle at around 3.3 volts per cell when charged to 3.50 to 3.65 volts per cell.8 kW Enphase micros AC coupled to a SolArk 12K
-
If Renogy said the battery is fine I would tend to believe them. I, like the others, do not believe you have enough charging capacity to satiate your batteries efficiently . 200 watts of panels is somewhat negligible for two 100 Ah batteries. It would take a long time to charge them. I'd get they do much better with 400 watts of panels. Probably want very similar panels.First Bank:16 180 watt Grape Solar with FM80 controller and 3648 Inverter....Fullriver 8D AGM solar batteries. Second Bank/MacGyver Special: 10 165(?) watt BP Solar with Renogy MPPT 40A controller/ and Xantrex C-35 PWM controller/ and Morningstar PWM controller...Cotek 24V PSW inverter....forklift and diesel locomotive batteries
-
I suspect that there may be some confusion. When you charge a battery at a given voltage, that is the charging voltage, and not necessarily the battery voltage. When you disconnect the charger, the voltage that you read is the battery voltage. That is what you charged the battery "up to."Reread the first sentence in Ampster's post above. It is important to understand what he is saying. If you don't get that, ask!MarcI always have more questions than answers. That's the nature of life.
-
Again I'll say, you need to charge the battery to capacity,, 200W is insufficient to get the job done, if adding more PV is not an option right now then multiple days without any loads, which includes the inverter if applicable, is the only logical solution. Running the vehicle to charge is extremely inefficient given the time required, if the voltage is dropping to 11.8V which is 2.95 volts per cell then it's at ~4% state of charge, this is extremely hard on the battery and will result in lower cycle count.
Actually I'm surprised the BMS hasn't cut the loads at 11.8V, most would do so at 12V or 3.000 volts per cellor higher, then again if using anything other than an accurate meter to read the voltage, it's probably inaccurate.
See attached pdf which shows the standing voltage per cell versus state of charge, this is after charging without any loads preferably with an hour or more elapsed.
1500W, 6× Schutten 250W Poly panels , Schneider MPPT 60 150 CC, Schneider SW 2524 inverter, 400Ah LFP 24V nominal battery with Battery Bodyguard BMS
Second system 1890W 3 × 300W No name brand poly, 3×330 Sunsolar Poly panels, Morningstar TS 60 PWM controller, no name 2000W inverter 400Ah LFP 24V nominal battery with Daly BMS, used for water pumping and day time air conditioning.
5Kw Yanmar clone single cylinder air cooled diesel generator for rare emergency charging and welding. -
What is model of panels and are you using an MPPT controller. Some '12v' mono panels (like Renogy's) have reduced their cell count to 32 or 33 series cells. These low Vmp, low cell count, panels may not have enough overhead voltage to run an MPPT controller. They work okay with PWM controller.
This would only aggrevate your problem of not have sufficient panels to charge two 100 AH batteries in one day. If you are lucky you will get maybe 750 WH's from two 100 watt panels per day. That is roughly replacing about a quarter of 200 AH battery capacity per day. -
If you have a decent voltmeter, when the battery is charging, check the voltage at both the charge controller Vbatt terminals, and the battery terminals. For a 12 volt system, you want a maximum of 0.05 to 0.10 volt drop from charge controller to battery bank.
Too large of voltage drop will slow charging and could leave the batteries under charged. You generally need short(er) and heavy(ier) cables from the charge controller to the battery bank to keep voltage drop low.
-BillNear San Francisco California: 3.5kWatt Grid Tied Solar power system+small backup genset -
Thank you all for responding. The panels are Renogy and the charge controller is mppt. It’s clear that I need to get more panels/ higher input to the battery bank which I will do as soon as I can. It’s also clear I need a battery monitor. The 40 amp Rover charge controller came with I think #6 cables I will investigate what is the largest gage that can fit in the opening of the terminal.
-
A lot of inverters and controllers have undersized input and output lugs. It is quite odd.First Bank:16 180 watt Grape Solar with FM80 controller and 3648 Inverter....Fullriver 8D AGM solar batteries. Second Bank/MacGyver Special: 10 165(?) watt BP Solar with Renogy MPPT 40A controller/ and Xantrex C-35 PWM controller/ and Morningstar PWM controller...Cotek 24V PSW inverter....forklift and diesel locomotive batteries
Categories
- All Categories
- 229 Forum & Website
- 137 Solar Forum News and Announcements
- 1.4K Solar News, Reviews, & Product Announcements
- 199 Solar Information links & sources, event announcements
- 898 Solar Product Reviews & Opinions
- 256 Solar Skeptics, Hype, & Scams Corner
- 22.5K Solar Electric Power, Wind Power & Balance of System
- 3.5K General Solar Power Topics
- 6.7K Solar Beginners Corner
- 1K PV Installers Forum - NEC, Wiring, Installation
- 2.1K Advanced Solar Electric Technical Forum
- 5.6K Off Grid Solar & Battery Systems
- 428 Caravan, Recreational Vehicle, and Marine Power Systems
- 1.1K Grid Tie and Grid Interactive Systems
- 654 Solar Water Pumping
- 816 Wind Power Generation
- 624 Energy Use & Conservation
- 619 Discussion Forums/Café
- 312 In the Weeds--Member's Choice
- 75 Construction
- 124 New Battery Technologies
- 108 Old Battery Tech Discussions
- 3.8K Solar News - Automatic Feed
- 3.8K Solar Energy News RSS Feed