Help With Planning New Off Grid System?
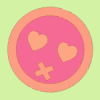
Up_Nord_Dere
Registered Users Posts: 14 ✭✭
I am trying to DIY an off grid system for a seasonal cabin. I really want to know as much as I can about how every component works because it will be installed in the middle of nowhere. I attached the latest version of my diagram. I put breakers on both the pos. and neg. from the batteries so that I can completely isolate them when we close up the cabin in the fall. This cabin is in northern Minnesota, so the batteries will be subjected to sub-freezing temps. When we show up in January, we'll heat the cabin up (batteries will be inside) and once they reach temperature I will reconnect them. The manufacturer assured me that this will not damage them and they come with a 10 year warranty.
I'm looking for suggestions and feedback. The grounding issue is confusing, but I spoke with an installer a couple of days ago and I feel like I'm starting to get my head around it.
I'm looking for suggestions and feedback. The grounding issue is confusing, but I spoke with an installer a couple of days ago and I feel like I'm starting to get my head around it.
Comments
-
My system is isolated for 6 months of the year. Freezing temperatures. There has been no problem with the batteries so far. I leave my charge controller and batteries connected to the panels when I close up for the season, so there is some charging done until the panels get snow covered.
But as long as your batteries are fully charged when you leave you should have not problem.Island cottage solar system with appriximately 2500 watts of panels, 1kw facing southeast 1.3kw facing southwest 170watt ancient Arco's facing due south. All panels in parallel for a 24 volt system. Trace DR1524 MSW inverter which has performed flawlessly since 1994. Outback Flexmax 80 MPPT charge controller four 467A-h AGM batteries. Insignia 11.5 cubic foot electric fridge 1/4hp GSW piston pump. My 31st year. -
Thanks, that's helpful. I know a lot of RV'ers do something similar. Battle Born wanted me to completely disconnect them so there wouldn't be any draw at all, including from a monitor.
-
LiFePO4 (and Li Ion rechargeables in general) do not like to be charged/discharged AT ALL in sub freezing conditions. They will be permanently damaged if power is drawn/charged when the battery is "frozen".
So, Battle Born's suggestions sound correct.
Lead Acid batteries, the higher the state of charge, the lower temperatures they can function without damage (dead battery freezes at approximatly 32F, fully charged battery freezes below -75F or so).
-BillNear San Francisco California: 3.5kWatt Grid Tied Solar power system+small backup genset -
It routinely gets to -20F in the winter, so any battery is going to be challenged. I'm really hoping that the completely disconnected LiFePO4 is the way to go. Any comments on my wiring diagram? I'm a total noob. Been working hard to get educated.
-
Should this be in the beginners area?
-
You need to check with Battle Born directly about storage (and operational) temperature range. Their product, their warranty.
I think you have a 100 Amp fuse in the Midnite box on the negative battery lead? If you tie battery negative (return) to your system ground, then you really do not need a breaker/fuse in the negative battery lead--Just tie (all) return/negative leads to the negative battery bus.
Your "Bluesmart" charger should have a fuse/breaker on its connection to the positive battery bus (depending on its wire/cable current rating). Same for the 4 AWG that leaves the +Battery Bus... It should have a fuse/breaker (battery is the source of "high current" for everything--Which need protecting)).
Personally, I would like to see the charge controller's Vbatt output "home run" back to the + Battery bus. And also the AC inverter to its own +Batt Bus. I do worry that the "noise" from the AC inverter sharing the same wiring can cause the MPPT charge controller to get confused--Home running both back to the Battey Bus should reduce the electrical noise.
You want to to keep the charge controller +/- Battery Bus leads short and heavy--I would plan on a maximum wiring drop of 0.05 to 0.10 volts (accurate battery voltage means faster & more accurate charging from the charge controller).
That is my first pass set of comments...
-BillNear San Francisco California: 3.5kWatt Grid Tied Solar power system+small backup genset -
Thanks Bill! Very helpful. I really appreciate you taking the time.
To your points: I bought the batteries direct from Battle Born and that was their stipulation: total isolation during storage, both neg. and pos. I think I'm good there. That's the purpose of the 100 amp breaker (not fuse) on the neg in the Midnite box. I could just pull the lugs off the batteries, but I'm trying to make it turn-key for my family and (let's face it, I'm not getting any younger or smarter) myself. Last fall trip, flip the breakers in the prescribed order, lock the door and leave. Less chance for reversed polarity, dropped wrench shorting the batteries, etc. Could just as easily be a surface mount switch, but I didn't find one that seemed robust and cost-effective compared to a breaker.
Bluesmart charger: Backup to use with Honda 1000 inverter/generator. Fuse that because a battery short would toast the tiny wires? That makes sense. Thanks. Option: leave it out entirely, connect with jumper cable type clamps if batteries get low? Probably a dumb idea.
Isn't the 4AWG protected by the 80A breaker downstream on the way to the inverter?
MPPT Vbatt output: If I get what you're saying, you want individual wires from SCC+ to batt and from inverter+ to batt. A SCC home run would have to run through the 100A breaker in order to satisfy the battery isolation requirement. As would a home run from the inverter. If they share that breaker, isn't that the same as using a bus? Or do I have to abandon the turnkey idea? Get out the wrench in the fall, pull the 1/0 cables off the battery posts.
Thanks again, I'm finally feeling like I might pull this off. We're hoping to get to the cabin in June when I'm done teaching and do a self-enforced 14 day quarantine. Sure would be nice to have a working fridge. Looking forward to continuing to learn this stuff. -
You might want to check with Battle Born on this. When storing Lifepo4 batteries it's generally recommended they should not be in a fully charged state, but rather at a 40% SOC, on a 12V nominal 4S battery that would be ~ 13.32V.1500W, 6× Schutten 250W Poly panels , Schneider MPPT 60 150 CC, Schneider SW 2524 inverter, 400Ah LFP 24V nominal battery with Battery Bodyguard BMS
Second system 1890W 3 × 300W No name brand poly, 3×330 Sunsolar Poly panels, Morningstar TS 60 PWM controller, no name 2000W inverter 400Ah LFP 24V nominal battery with Daly BMS, used for water pumping and day time air conditioning.
5Kw Yanmar clone single cylinder air cooled diesel generator for rare emergency charging and welding. -
Up,
Ideally, you would want to "gang" the + and - battery breakers together (such as the 2 pole 240 VAC breakers in standard home wiring--If one breaker trips, the second is tripped too--Don't know if you can gang these breakers. But, if you ground the negative bus to Safety Ground, it should not be a big issue.
Remember that fuses/breakers are there to protect the wiring from overcurrent/catching fire. Whether it is a device/load that shorts/draws too much current (for the wire), or if the wire itself gets shorted directly (goes through sheet metal hole, sharp metal edge cuts through insulation, etc.).
Same issue with the breaker near the AC inverter DC input... Breaker/fuses should be next to the source of high current (typically Battery Bus in DC systems). It is to protect against any "possible" short circuit--Not just the AC inverter shorting. Something metal falls on the DC terminals, a crimp fails and the cable pulls out/shorts, etc.
Wire up with proper fuse/breaker protection on the battery charger output... Jumper clamps are not very reliable.
For an 800 Watt 24 volt AC inverter, the branch circuit wiring rating:- 800 Watts * 1/0.85 inverter eff * 1/21.0 volts battery cut off = 45 Amps max current
- 800 Watts * 1/0.85 inverter eff * 1/21.0 volts battery cut off * 1.25 NEC continuous current derating = 56 Amps
https://lugsdirect.com/WireCurrentAmpacitiesNEC-Table-301-16.htm
Regarding the solar array and MPPT charge controller... For a 100/50 amp MPPT controller, the suggested maximum array size would be:- 50 amps charging * 29.0 volts charging * 1/0.77 panel+controller deraring = 1,883 Watt array "typical cost effective" maximum
Your solar array of 6 x 100 Watt panels @ Vmp~18 volts(?)... For a 24 volt battery bank, you want the Vmp to be >> 35 volts (for an MPPT type charge controller)... Instead of 2 panels in series * 3 parallel strings... You should use 3 panels in series * 2 parallel strings. That gives you Vmp-array ~ 54 Volts. That gives your MPPT controller a better input voltage (for efficient operation), and the higher Vmp-array and lower Imp, reduces voltage drop and array current.
Depending on your final array size... You might be able to use smaller than 6 AWG wiring.
-BillNear San Francisco California: 3.5kWatt Grid Tied Solar power system+small backup genset -
The BB battery may have internal housekeeping circuits that could be draining the battery all winter. It could stay ON even if you disconnect all cables for 5 months, again check directly with BB to see the best way to store the Li battery in cold temps
Powerfab top of pole PV mount | Listeroid 6/1 w/st5 gen head | XW6048 inverter/chgr | Iota 48V/15A charger | Morningstar 60A MPPT | 48V, 800A NiFe Battery (in series)| 15, Evergreen 205w "12V" PV array on pole | Midnight ePanel | Grundfos 10 SO5-9 with 3 wire Franklin Electric motor (1/2hp 240V 1ph ) on a timer for 3 hr noontime run - Runs off PV ||
|| Midnight Classic 200 | 10, Evergreen 200w in a 160VOC array ||
|| VEC1093 12V Charger | Maha C401 aa/aaa Charger | SureSine | Sunsaver MPPT 15A
solar: http://tinyurl.com/LMR-Solar
gen: http://tinyurl.com/LMR-Lister , -
Thanks again Bill! A lot to digest. I'm sure I'll have more questions after I parse this. This is super helpful information.
-
mcgivor said:You might want to check with Battle Born on this. When storing Lifepo4 batteries it's generally recommended they should not be in a fully charged state, but rather at a 40% SOC, on a 12V nominal 4S battery that would be ~ 13.32V.
-
BB. said:Up,
Ideally, you would want to "gang" the + and - battery breakers together (such as the 2 pole 240 VAC breakers in standard home wiring--If one breaker trips, the second is tripped too--Don't know if you can gang these breakers. But, if you ground the negative bus to Safety Ground, it should not be a big issue.
2.) Bond the negative and ground bus in the left hand midnite quad on my drawing? All of what you said makes sense, and the last thing I think I'm still a little shaky on (not surprisingly) is grounding. The inverter has a movable jumper to choose between either bonding or floating the neutral. It has a single NEMA plug outlet but eventually I want to have a proper load center and conduit (float neutral in inverter, bond in load center). Does that make sense? What about grounding the frames of the ground mounted PV panels? Can they go on the same ground rod?BB. said:Up,
For an 800 Watt 24 volt AC inverter, the branch circuit wiring rating:- 800 Watts * 1/0.85 inverter eff * 1/21.0 volts battery cut off = 45 Amps max current
- 800 Watts * 1/0.85 inverter eff * 1/21.0 volts battery cut off * 1.25 NEC continuous current derating = 56 Amps
I agree with your assessment. In fact I originally spec'd a 50A breaker in that location based on the same math you did, and I actually have it in my pile of equipment right now. Bought the batteries, inverter, SCC as a package and they spec'd 6AWG with a 75A fuse (breakers of that value don't seem to exist) so for some reason I went up instead of down. They were concerned about surge current and nuisance trips. I think I'll install the 50A and see if we get a lot of nuisance trips. If so, reevaluate. Not planning any big AC motors, so we're probably fine.Regarding the solar array and MPPT charge controller... For a 100/50 amp MPPT controller, the suggested maximum array size would be:- 50 amps charging * 29.0 volts charging * 1/0.77 panel+controller deraring = 1,883 Watt array "typical cost effective" maximum
Your solar array of 6 x 100 Watt panels @ Vmp~18 volts(?)... For a 24 volt battery bank, you want the Vmp to be >> 35 volts (for an MPPT type charge controller)... Instead of 2 panels in series * 3 parallel strings... You should use 3 panels in series * 2 parallel strings. That gives you Vmp-array ~ 54 Volts. That gives your MPPT controller a better input voltage (for efficient operation), and the higher Vmp-array and lower Imp, reduces voltage drop and array current.
Depending on your final array size... You might be able to use smaller than 6 AWG wiring.
-Bill
Yes, leaving room for growth. And yes, Vmp is 18V per panel, 36 per string. I'll have to think about 2 strings of 3. My only hesitation is that's getting into the danger zone for Volts. I won't be able to bury the conduit from the ground mount. Very rocky ground. Little kids and lots of wildlife around. Am I correct that you're saying the MPPT will be more efficient because it's designed to go as high as 100V?
-
Any charge controller has input and output limits... With MPPT controllers, the limits get a bit more complex (Vmp-hot vs Voc-cold, etc.).
MPPT are sort of like the DC equivalent of a variable transformer. They match the "output of the array" with the input requirements of the battery bank.
PWM controller are simple on/off switches...
Both are pretty closely matched for efficiency--When the Vmp-array is ~18 volts (for a 12 volt battery bank)... The Vmp-array falls as the panels get hot (~20C over ambient) while panels are rated at 25C (marketing numbers). As Vmp-array falls towards ~15 volts (hot day, no wind) and battery bank approach 14.75 volts--There is very little losses. And MPPT cannot make up for the drop in Vmp-array-hot (lost of solar panel capability when hot, is a loss--MPPT cannot make up for that).
When panels are well below sub freezing, then the higher Vmp-array-cold voltage can be "harvested" by the MPPT controller (power=voltage*current). MPPT can collect 10-20% more energy in very cold conditions/climate.
Where MPPT really shine--The ability run high voltage (& low current) for the solar array--You can run ~6 AWG smaller wiring for the same loss of energy in the wiring (typically aim for 1-3% losses in solar wiring) (I.e., 12 AWG vs 6 AWG heavier solar array wiring wiring for Vmp~18 volts and 14.xx volt battery).
Other things that MPPT can do... It gives you more head room--PWM systems in hot climates have less "voltage headroom" and it gets a bit harder to Equalize charge the battery bank (low array voltage, high battery voltage of ~15-16 volts EQ charge).
Also, many MPPT controllers have more features (Internet, Bluetooth, integration with battery monitors & AC Inverters & Remote diagnostics/configurations. That does come with higher $$$ and somewhat more power usage for functions and features (when not charging).
And other things... Instead of 6x panels in series (combiner box with 6x breakers/fuses) vs 3 panels in series * 2 parallel connections (no combiner box needed).
The "cheaper" GT solar panels are typically Vmp-30 volts or higher, and many times do not "match" Vmp-array with Vbatt requirements (18v array /12v bank; 36v/24v bank; 72v/48v bank). GT panels are frequently 1/2 the $$$/Watt cost vs "battery friendly" panels. Also GT panels tend to be 200-300+ Watts, vs the typical 140 Watt max panels for battery friendly PWM matches. Fewer panels, fewer electrical connections, lower costs... All nice. However, panels that are >140 Watts or so, typically need two people safely move panels around/install.
-Bill
Near San Francisco California: 3.5kWatt Grid Tied Solar power system+small backup genset -
Thanks again Bill!
I think I'm figuring this stuff out. Any thoughts on how I have grounded things in my diagram? -
Generally, I like to keep AC and DC grounding separate--And they should only "tie" at one point (typically the Frame/Chassis ground if vehicle, or at the ground rod/cold water pipe if in a building).
You don't want the green wire ground to become part of the current path for normal operation (like tieing the return path at the main panel, and again at a sub panel).
Also, keeping the DC separate from the AC grounding (except for "The One" grounding point where all grounds meet). The reason is that a standard AC grounding may be a 6 AWG cable for main panel, and as little as 14 AWG out to remote metal J-Boxes, etc.
And the DC side, if you have a very large battery (AH) and Main Battery Breaker--For example, if the DC main breaker is >~200 Amps, a 6 AWG cable is not heavy enough "safety ground"... So on the DC side for large systems, you don't want "DC Fault Current" to flow through AC safety grounds (6 AWG or even 14 AWG green wires). And you don't want to run 4 or 2 AWG cable out with your AC power (that has small AWG safety ground).
Of course, if you do tie DC and AC grounds together at the Main Chassis or Main Ground rod, then using DC Grounds for AC systems (like an epanel that contains both DC and AC wiring), it not going to be a safety problem.
I earlier suggested (I think I did anyway), that your Battery Negative Bus be grounded to the chassis/frame/ground rod point... This allows a short circuit anywhere to find a current path back to the return (wither DC battery bus, or AC Neutral). The idea is to always have the "Return Line" always (Neutral/Return) "ground bonded" in the one location--This ensures that the short circuit current will flow and trip the protective fuse/breaker on the "Hot" side of the circuit (+DC or L1/L2/Hot on AC side).
A "truly floating power supply" (whether 12/24/48 VDC or 120/240 VAC) can be done, but that is when you want gang tripped breakers on both "Hot" and "Return" lines--It gets a bit confusing, but it is possible for a floating system to be shorted (say + near battery bus) shorted to earth--And the negative bus now becomes "negative" with respect to ground--And if you do not have breaker/fuses on the "return bus", you can get 200 Amps of DC current on an 18 AWG wire "return/Negative" to an LED light fixture and "fry/start a fire" on an "unprotected DC negative circuit".
I know, it is confusing--But ideally, you always want to ground reference your return line on the battery bank--So you never have a floating DC output, and you only need breakers/fuses on the + leads (each wire leaving the positive battery bus needs its own fuse/breaker rated for the size of the wire).
Where not to ground reference the Neutral--Most MSW (Modified sine/square wave) AC inverters do not have a floating AC output. And if you try to ground bond a "neutral" on the MSW inverter, it shorts it out internally. (PSW/TSW inverters generally have isolated AC outputs and can safely ground bond the Neutral). As always, refer to the manual.
Using an AC GFI outlet (or breaker) can negate the "need" to ground reference the AC neutral (GFI will trip if short from Hot or Neutral to ground and shut off the circuit).
And you will find that most small power systems (less than 3 kWatt AC???) seem to float the AC outputs. Some use GFI outlet protection (generators/AC inverters) and some don't. Portable systems are kinds of "loosey goosey" on ground bonding.
-BillNear San Francisco California: 3.5kWatt Grid Tied Solar power system+small backup genset -
New Version of diagram attached. A few days of noodling and sleeping on it, and it's really starting to gel in my brain. Thanks all for the input.
Added fuses for inverter and SCC
Charger has an inline fuse in the cord. Hadn't caught that before.
Home run for SCC and Inverter to Bus.
Downsized breakers for 6AWG
-
A couple of quick notes...
Fuses/breakers should be near the +Bus bar (OK, I see fuses next to bus bar, and local disconnect/breakers near the devices--OK).
If you are using a 24 VDC battery bank, you need (optimal for use with MPPT controller), to have 3x series panels * 2 parallel strings... You need >>~36 volts Vmp for MPPT controller+24 volt bus (if this was PWM, then 2x series = Vmp-array~36 volts is perfect). If you only (presently) have 2x parallel strings, you don't need the combiner box+breakers/fuses... Only need if 3 or more parallel strings. Perfectly OK if only 2x parallel strings to have combiner box--And really nice if you plan on adding some more panels later.
If you have any chances of lightning in your area, put a second ground rod at the base of the solar array. Ideally, I would tie the second "remote ground rod" to both the solar array (this is for lightning ground to reduce the chances of lightning getting to the house), and the 6 AWG wiring from the "house" (this is to prevent short circuits making the local metal "hot").
Having fuses and breakers in the same line (fuses near bank, breaker near loads)... OK, and if you want local disconnects, that is OK. You might "oversize" the fuse to 80 amps or a bit more for the solar charge controller... I would like to pop the 70 amp breaker first (if something does go wrong), rather than having to debug/replace the (sometimes not cheap) fuses. It would be OK to use breakers near the +Bus too... Many of the larger fuses and holders end up being close in pricing of similar rated breakers.
For your loads--You should double check the manual... For example, the fridge takes around 2-3 Amps... Sometimes the designers limit the maximum line current to less than the 15 amp breaker you are using...
That is quick look... When things are a bit quieter, I will take a second look.
-BillNear San Francisco California: 3.5kWatt Grid Tied Solar power system+small backup genset -
With reference to the breakers in the Midnight quad enclosure, it's bad practice to use two wires in a single terminal, instead of jumpers run them to the positive bus
1500W, 6× Schutten 250W Poly panels , Schneider MPPT 60 150 CC, Schneider SW 2524 inverter, 400Ah LFP 24V nominal battery with Battery Bodyguard BMS
Second system 1890W 3 × 300W No name brand poly, 3×330 Sunsolar Poly panels, Morningstar TS 60 PWM controller, no name 2000W inverter 400Ah LFP 24V nominal battery with Daly BMS, used for water pumping and day time air conditioning.
5Kw Yanmar clone single cylinder air cooled diesel generator for rare emergency charging and welding. -
Thanks guys! Bill, I know you said this earlier, forgot about that part about two strings of 3 panels. The only reason not to do it would be encroaching shade would take out half the array instead of one third. So are you saying I could ditch the combiner box, use MC4 branch connectors to parallel them and run the wires straight inside? Just stick with the 10 gauge PV wire in conduit?
Fridge has a built in fuse. The breaker is a simple way to shut it down, protect that wire run.
Mcgivor, the bus bar only has four posts. I need to double up lugs somewhere. Better on the bus bar? Or still no good? Really don't want a second bus bar. Really don't want to mess with making one. -
Shade is a killer for Solar Electric panels.... To double check wiring:
- 100 Watt Pmp panel / 18 volts Vmp = 5.56 Amps Imp
- 3x 18 Volts Vmp = 54 Volts Vmp-array
- 2x 5.56 Amps Imp = 11.12 Amps Imp-array
- 10 AWG wiring @ 40 Feet one way run @ 54 volts @ 11.12 Amps
Voltage drop: 0.89
Voltage drop percentage: 1.65%
Voltage at the end: 53.11
That would work... Typically aim for 1% to 3% drop on wiring.
Rather than using the MC4 adapters... There is always buying a couple of lengths of male/female cables and cutting them in 1/2. Just use a water resistant J-Box with wire nuts:
https://www.solar-electric.com/residential/wiring-cables/pv-wire-cables-connectors.html
But either adapters or jumper cables would work...
-BillNear San Francisco California: 3.5kWatt Grid Tied Solar power system+small backup genset -
Total redesign. The breakers I was going to use for the battery disconnects wouldn't work with 1/0 lugs in a Midnite Quad. The breakers are so close together that the lugs were actually touching. Going with Blue Sea disconnect switches. Fuses and switch out of a copper bar busbar. Photo of the design from Explorist.life attached (fuse sizes in the photo not for my system). Just when I thought I could see the finish line! I'll get there eventually.
-
Well that's new and likely should be discussed.
My guess is this is a 'thermoelectric cooler'?
They seem nice, but the math is bad for these in general, as yes it uses just 56 watts, but it does that continuously, so uses 56x24hours or 1344 watt hours per day. For that they generally cool only to 40 degrees less than the air it's surrounded by.
Home system 4000 watt (Evergreen) array standing, with 2 Midnite Classic Lites, Midnite E-panel, Magnum MS4024, Prosine 1800(now backup) and Exeltech 1100(former backup...lol), 660 ah 24v Forklift battery(now 10 years old). Off grid for 20 years (if I include 8 months on a bicycle).
- Assorted other systems, pieces and to many panels in the closet to not do more projects. -
No, it's a Danfoss/Secop compressor. Unique 10.3 cubic foot. The company claims 570 Watthours/day. More the first day we show up and the cabinet is warm, but once it gets to temp. that's their guess. I just realized I have a typo on the diagram. The ground line running from the negative post on the battery is listed as 6AWG, but probably should be 1/0, right? To match the other battery cables?
Categories
- All Categories
- 228 Forum & Website
- 136 Solar Forum News and Announcements
- 1.4K Solar News, Reviews, & Product Announcements
- 199 Solar Information links & sources, event announcements
- 898 Solar Product Reviews & Opinions
- 256 Solar Skeptics, Hype, & Scams Corner
- 22.5K Solar Electric Power, Wind Power & Balance of System
- 3.5K General Solar Power Topics
- 6.7K Solar Beginners Corner
- 1K PV Installers Forum - NEC, Wiring, Installation
- 2.1K Advanced Solar Electric Technical Forum
- 5.6K Off Grid Solar & Battery Systems
- 428 Caravan, Recreational Vehicle, and Marine Power Systems
- 1.1K Grid Tie and Grid Interactive Systems
- 654 Solar Water Pumping
- 816 Wind Power Generation
- 624 Energy Use & Conservation
- 619 Discussion Forums/Café
- 312 In the Weeds--Member's Choice
- 75 Construction
- 124 New Battery Technologies
- 108 Old Battery Tech Discussions
- 3.8K Solar News - Automatic Feed
- 3.8K Solar Energy News RSS Feed