Stand Alone, PV/Genny Hybrid Questions
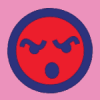
IowaSolarGuy
Registered Users Posts: 10 ✭
Hey Guys,
I have a customer who purchased a bunch of equiptment online from various sources. Here is the run down of the system. I would like some advise on combiners and components for this system.
He has;
24 Sharp NE170-U1
2 Outback MX 60 Charge controllers
16 Interstate UL-16 Batteries
1 Xantrex XW 6048 Inverter
I was planning on using the Outback Flexware PV12 as the combiner for the PV array. I now need one on the other side of the MX 60's. Xantrex wants 1500 for their XW combiner box but my customer is a cheap-o and wants to go as far as building his own combiner out of an old box and components from the local hardware store. Any recommendations?
I will run mostly DC finely stranded AWG 6 for allmost all of the wiring. We have very short runs on the system.
Let me know what you guys think.
I have a customer who purchased a bunch of equiptment online from various sources. Here is the run down of the system. I would like some advise on combiners and components for this system.
He has;
24 Sharp NE170-U1
2 Outback MX 60 Charge controllers
16 Interstate UL-16 Batteries
1 Xantrex XW 6048 Inverter
I was planning on using the Outback Flexware PV12 as the combiner for the PV array. I now need one on the other side of the MX 60's. Xantrex wants 1500 for their XW combiner box but my customer is a cheap-o and wants to go as far as building his own combiner out of an old box and components from the local hardware store. Any recommendations?
I will run mostly DC finely stranded AWG 6 for allmost all of the wiring. We have very short runs on the system.
Let me know what you guys think.
Comments
-
Re: Stand Alone, PV/Genny Hybrid QuestionsIowaSolarGuy wrote: »I will run mostly DC finely stranded AWG 6 for allmost all of the wiring.
Beware - many crimp connectors are designed for fat strands, and the fine strands compress and escape over time. Unless you use terminations spec'd for fine strand wire (welding cable ?) your fire insurance may be voided, after a fire.
I'm sure many folks have done this just fine, but just letting you know.
I've also been advised that soldering wires into crimp connectors, has 2 problems:
1) when the solder wicks into the bundle of strands, it stops, and this becomes a high stress flex point where wires break.
2) if you have a short circuit, the wires heat up, the solder melts, and the wire goes free.Powerfab top of pole PV mount | Listeroid 6/1 w/st5 gen head | XW6048 inverter/chgr | Iota 48V/15A charger | Morningstar 60A MPPT | 48V, 800A NiFe Battery (in series)| 15, Evergreen 205w "12V" PV array on pole | Midnight ePanel | Grundfos 10 SO5-9 with 3 wire Franklin Electric motor (1/2hp 240V 1ph ) on a timer for 3 hr noontime run - Runs off PV ||
|| Midnight Classic 200 | 10, Evergreen 200w in a 160VOC array ||
|| VEC1093 12V Charger | Maha C401 aa/aaa Charger | SureSine | Sunsaver MPPT 15A
solar: http://tinyurl.com/LMR-Solar
gen: http://tinyurl.com/LMR-Lister , -
Re: Stand Alone, PV/Genny Hybrid Questions
Besides the "fine strand" point in last post, I also wonder why you would need #6 wire if you have short runs.
You can put up to 4 of those panels in series with the FM60 for about 21 amps max per string, #8 would be enough (#10 would usually be enough, but may not meet code, depending on installation). From the charge controller to the battery bank you may need larger than #6 since you are running at 60 amps. -
Re: Stand Alone, PV/Genny Hybrid Questions
I always crimp and solder , finishing off with heat shrink, In my opinion the wicking effect improves the fatigue resistance of the connection by spreading the stress point along the cable, My experience coming from 20 yr`s + working in the motor sport industry, and never seeing any fail, Where you are going to get that sort of vibration in a PV setup ?
It will also improve voltage drop.
The reason cable come`s a little loose and gets a small volt drop in both crimped and clamped connections over time is through Temperature work hardening (heating and cooling) and corrosion, Soldering cures all of these. If you did get a dead short, I would say, the solder joint would not be the first thing to fail.
Have a good one
Tim
ps if you look at most of this type connector`s, They have a small hole in the end of the "wire hole" It is to see the cable is in correctly and run solder into, -
Re: Stand Alone, PV/Genny Hybrid Questions24 Sharp NE170-U1
2 Outback MX 60 Charge controllers
16 Interstate UL-16 Batteries
1 Xantrex XW 6048 InverterYou can put up to 4 of those panels in series with the FM60 for about 21 amps max per string,
I respectfully disagree with the suggestion that the OP could "...put up to 4 of those panels in series with the FM60...". At 43.2 Voc STC per module, this configuration (172.8 Voc STC) would surely damage -- if not kill -- the MX60 charge controller, or any charge controller rated at 150 VDC max. In fact, depending on ambient weather conditions, even three modules in series could present an issue with cold weather Voc....but my customer is a cheap-o and wants to go as far as building his own combiner out of an old box and components from the local hardware store. Any recommendations?
The circuit breakers available for the PV-12 combiner box are rated for up to 150 VDC. More on that later.
ISG: Can you tell us more about where (city and state) this system will be installed?
More later...
Jim / crewzer -
Re: Stand Alone, PV/Genny Hybrid Questions
The system will be installed in Indianola Iowa.
I will have 12 strings of two panels. 24 panels total. We are going to use #10 wire from the PV array to the Outback Flex12 combiner. Then from the Combiner to the MX controllers I will use the AWG #6 wire, Its overkill but I like it like that. Plus our temps in Iowa drop to below zero during the winter.
Now comes the tricky part, at least for me. I need to parallel the MX 60's before I connect to the battery bank; which is 16 Interstate UL-16's that are 6 volt and 375 Ah @ 20 h. I need to use a fused disconnect, where I plan on hooking both legs into one disconnect. It needs to be 150v rated and a 100 amp fuse or breaker.
This is where I run into problems. Here is how I calculated my amperage.
Isc of panel 5.47, each leg 6 x 5.47 = 32.82. Two legs combined 65.64 x 1.25 = 82.05 x 1.25 = 102.56.
This is going to need a large wire from this "disconnect or breaker" to the batteries. Now the batteries we are going to use 1/0 welding wire to connect the batteries together. I am also a bit unclear about how to properly size the wire for the battery bank. The max amount of amps this battery can output depends on the load, which depends on the inverters ability to pull, correct? The inverter is rated for 44-64 amps DC up to 100 A continous charge rate. So if I have a run of say 10 feet I could use 1/0 and be fine correct?
My questions are what is the best and economical solution for the Disconnects and breaker panels for everything after the charge controllers? Is it worth spending the 1500 for the XW distrubution panel or can we find DC breakers/ disconnects that will do the same job?
ISG -
Re: Stand Alone, PV/Genny Hybrid Questions
A few errors in your thinking;
The Charge controllers require current protection on both input and output, you cannot just combine the output of the MX60's, then to a over current device.
You can't parallel the inputs to the MX60's, they require separate solar input
Also, the battery bank needs its own over current protection as does the XW6048
#6 is far from overkill for the combined solar and charge controller output, just adequate. For a XW6048, you should be using 2 or 4 AUT for the battery/inverter connections
I would highly recommend you get the current NEC
http://www.amazon.com/National-Electrical-Code-Protection-Association/dp/0877657904/ref=pd_bbs_sr_1?ie=UTF8&s=books&qid=1232474051&sr=8-1
Read all of the 690 code, since you are getting paid to do this, you not only need to do this correctly, but you have a financial liability as well.
This should also be installed under the proper permits and inspected by the local building department. Large battery banks, solar, charge controllers , high power inverters all can be lethal devices if improperly installed, this is no joke and please take this seriously -
Re: Stand Alone, PV/Genny Hybrid Questions
Regarding crimp vs solder--A properly done crimp is more reliable than solder when the joint is exposed to vibration and flexing (solder focuses the bending force right at where the solder ends--properly done crimps, i.e., crimp in the middle of the sleeve, not at where the wire enters, do not focus the bending at one point).
If the joint is protected against flexing, the solder won't hurt (from my years designing and working on computers, network devices, and aircraft). Soldering an energy carrying circuit without crimping would violate NEC (at least I am pretty sure it does--as I recall from years ago).
Regarding the connection of the MX60 charge controllers--my recommendation would be to use two circuit breakers (or fuses/disconnects)--one for each unit. Normally this would be required for safety (a 60-80 amp breaker protecting the MX60, vs paralleled 100+ amp breaker protecting two MX60's... End up with 100 amps from the breaker + 60 amps from the other MX60 feeding the second failed MX60). Make the common parallel connection at the battery bus bar / common connection area (with short, well supported+insulated+protected wire to prevent possibility of shorts between the bus bar and the breaker).
I am not quite sure I understand the DC connection for your XW6048 inverter. If you are going to use the full output of the inverter (I don't have the specs, just going with generalities):
6,000 watts / 42 volts (min. batt volt) = 142 amps
But assuming the inverter is ~90% efficient:
142 amps / 0.9 = 158 amps
And assuming NEC 80% maximum current on circuit+breaker:
158 amps / 0.8 = 197.5 amps ~ 200 amp breakers and wiring
Once you have the branch current requirements, then you can go through the NEC and find the appropriate wire/insulation for your needs (conduit fill, etc.). Then double check using the voltage drop calculator to ensure that you will not have too much drop from the battery to the inverter.
Of course, if you plan on not using the full 6kW of the inverters output--then you can back it down to 100 amps or so (which would support ~3kWatts max continuous).
I assume there is some information in the XW installation manual that will give you the exact requirements per UL/NEC...
From my experience--the first time you do the install, having the factory distribution panel is probably worth the money. Once you have seen how they do things, what components they use, and what issues they address--then you can make the make/buy decission with more confidence for the next installs.
-Bill
SG typed faster than I... But we agree in the overall requirements.
Don't parallel the inputs or outputs of your MX60 controllers. It is not safe, and may not work (if inputs are paralleled).
When working with normal AC circuits, there is one source, and multiple loads. Easy to figure out what to do...
With Solar PV--there are multiple sources and loads. You have to be very careful that when you mix the two together, that you don't end up adding three sources together (like the two MX60s + 100 amp breaker which end up two sources supplying too much current, for safety, to a failed MX60).Near San Francisco California: 3.5kWatt Grid Tied Solar power system+small backup genset -
Re: Stand Alone, PV/Genny Hybrid Questions
ISG,
Thanks for the extra info. I'll follow up with you tomorrow AM.
Regards,
Jim / crewzer -
Re: Stand Alone, PV/Genny Hybrid Questions
bb,
paralleling the outputs of controllers is commonplace with proper fusing or if extra controls are needed as with some controllers. the inputs to controllers is where the problem lies i believe as this shouldn't be shared. in other words, having a pv or string connected to more than one controller and back to a common load should not occur. i do have to admit that all of the ins and outs of their connectivity and reasons for them are just beyond my knowledge as to how and why. i know this is a side offshoot in this thread, but i wouldn't mind further explanations from some of our re electrical engineers here on the forum if they could shed some light on some of these scenarios and what may occur. i could guess at the reasons, but i would rather hear the reasons rather than guess. -
Re: Stand Alone, PV/Genny Hybrid Questions
Interestingly, when I first joined here I would not have recommended attaching two solar chargers (each with its own battery bank) to one set of solar panels--in general.
But, if they are negative ground, PWM controllers--then it should be OK (done in RV's, for example).
For MPPT controllers connected in parallel--I would believe that the MPPT algorithms would be confused. And that would apply whether connected to one battery bank or separate battery banks.
The issue I was really concerned about was paralleling two (or more) solar charge controllers (really any power source) behind one breaker.
One way I try to figure out if something is "safe" is to look at one of the branch connections and see what would happen if I shorted one item. Example:
60 amp MX60 A
60 amp MX60 B
60+60 * 1/0.8 = 150 amp breaker (NEC Branch Rating)
Circuit with A+B+Breaker
iF "A" shorted, current available = B+Breaker=60+150=210 amps
Which is way more than the 80 amp breaker or wiring maximum rated that is required for the MX 60 (or whatever is the maximum rated breaker).
Notice, that if paralleling the two controllers, the wiring would need to be rated for 210 amps to each controller--instead of the 80 amp that would normally be required.
The above may or may not comply with how the solar stuff is done in the "code"--just how I look at the problem, before running running it through the "code" an making sure the rest is to requirements.
-BillNear San Francisco California: 3.5kWatt Grid Tied Solar power system+small backup genset -
Re: Stand Alone, PV/Genny Hybrid Questions
"Interestingly, when I first joined here I would not have recommended attaching two solar chargers (each with its own battery bank) to one set of solar panels--in general."
i am not recommending that either, but i would like to hear what happens under the various circumstances that we can imagine like shared pvs going into seperate controllers be it with the same loads or not. i don't believe it was ever said what happens under these conditions. -
Re: Stand Alone, PV/Genny Hybrid Questions
Much Appreciated Gentlemen,
This is my first project, the classroom applications are a bit different than real life.
I will tell my customer that we should use the factory distribution panel, this will likely make my life much easier.
As for the MX 60's, I was a bit confused on the purpose of two charge controllers but this is what he purchased.
The way I understand this I should use two separate disconnects and breakers, then hook them both to a bus bar and then to the battery bank. I believe it will be best to have just one bank of batteries; not two separate banks for each controller. I believe this would cause problems with the inverters ability to recharge the bank with a genny.
One more quick question, is there a spray coating that you guys use to prevent the batteries from corrosion? We were also planning on crimping the wire and I will likely not solder unless we have to.
Again I appreciate your input and expertise.
ISG -
Re: Stand Alone, PV/Genny Hybrid Questions
While there are sprays (mostly hokey) available, nothing beats plain old silicone grease, particularly silicone high-vacuum grease. It stays put and dies not evaporate, nor does it mix with water and wash away. Dow-Corning - a little dab will do ya.
If you have a proper crimper (usually hydraulic with specific dies, or one with really long handles and specific dies) a crimp should be "gas tight". One way to check is to sacrafice a test connection - cut it open and look for any voids. Another is to pull it apart, and measure how much force that takes.
My personal experience is that a perfect crimp is like most other perfect things - hard to come by. A good solder job after crimping as well as possible can help. A bad solder job can hurt. The objection to solder on the basis that it will overheat and allow the joint to disconnect only applies if the joint is crimped so badly that it would fall apart on its own, if crimping is done first and solder follows it. A good greasing certainly beats a bad solder job. Using solder to hold wires in place is never a good idea - there should always be a mechanical connection before solder gets involved.
Solder making a stress concentration in stranded wire can be a legitimate complaint, particularly if the wire moves much. Proper application of heat, and if needed a heat sink, can control this, but it takes some skill. -
Re: Stand Alone, PV/Genny Hybrid QuestionsAs for the MX 60's, I was a bit confused on the purpose of two charge controllers but this is what he purchased.
It's generally OK to have two MPPT controllers, each with its own separate PV array, connected to a common battery bank.
More tomorrow...
Jim / crewzer -
Re: Stand Alone, PV/Genny Hybrid Questions
sorry that my sidetracking confused you isg. you will need to have pvs feeding each controller dedicated only to one of the controllers. in other words 12 pvs will go to controller a and 12 pvs will go to controller b. the 2 controllers are a must due to the power limitations on a single controller. your buddy has more power than 1 controller is rated for. after all of the proper fusing and a disconnect, it is perfectly fine for the single large battery bank common to both controllers and it is preferred by most of us too except in some cases where a second battery bank may get switched in place of the first one due to other circumstances and is not the norm. -
Re: Stand Alone, PV/Genny Hybrid Questions
What they all said. Getting back to basics like Niel started, 12 panels to a fuse/breaker/combiner box, then to controller A, then to another fuse/breaker and finally to the main battery bus. Then repeat this with controller B. So basically you have an A and B solar setup feeding the battery bank, either can fail (or be serviced) on its own and the other will continue functioning with no interconnecting parts until they hit the bus.
I also recommend at least a 2 AUT; I have 4 AUT between the bus and our XW6048.3kw solar PV, 4 LiFePO4 100a, xw 6048, Honda eu2000i, iota DLS-54-13, Tesla 3, Leaf, Volt, 4 ton horizontal geothermal, grid tied - Green Bay, WI -
Re: Stand Alone, PV/Genny Hybrid Questions24 Sharp NE170-U1
2 Outback MX 60 Charge controllers
16 Interstate UL-16 Batteries
1 Xantrex XW 6048 InverterThe system will be installed in Indianola Iowa.
I indicated in my Jan. 20 post that there could be a problem with the Sharp 170 modules wired in series groups of three. It turns out that this is indeed an issue for the proposed combination of equipment. In fact, it’s my view that it’s a non-starter.
Here are the details.
Reference information:- Sharp NE-170U1: http://www.sharpusa.com/files/SESG-170U1.pdf
- Weather data: www.weather.com
- MX60 specifications: http://www.outbackpower.com/pdf/manuals/mx60_pv_mppt.pdf
- NEC 2008, Article 690 (in general), 690-7 (in particular)
The Sharp module’s STC Voc spec is 43.2 V (ref 25 C), and the Voc temperature coefficient is -0.36%/C. The record low temperature for Indianola, IA is -37 C (-35 F), and the average low temperature (in January) is -13 C (9 F).
The PV module’s temperature-corrected Voc for -37 C is: (43.2 + ((-37 – 25) x -0.36% x 43.2))) = 52.84 V. The Voc of a series string of three modules is 52.84 V x 3 = 158.53 V. This value exceeds the maximum input voltage specification for the MX60 controller (150 VDC), and it also exceeds the maximum voltage spec for commonly available DC circuit breakers (also 150 V) used in PV combiner boxes.
This input voltage may/will damage the MX60, and, because the controller records the highest Voc, this operation may also void the controller’s warranty. Should your installation require a permit and inspection, the inspector may fail the system because of this design defect.
The module’s temperature-corrected Voc for -13 C is: (43.2 + ((-13 – 25) x -0.36% x 43.2))) = 49.11 V. The Voc of a series string of three modules is 49.11 V x 3 = 147.33 V. This value exceeds the maximum operational voltage specification for the MX60 controller (141 VDC).
Operating the controller at between 141 VDC and 150 VDC will cause the controller to suspend operation until the array warms up and its Voc drops to below 141 VDC. Since the array Voc will hit ~141 V when the ambient temp drops to ~0 C (~32 F), I would expect the controller to suspend operation on many mornings from November through March.
In summary, the combination of the selected PV modules, the charge controller, and, probably, the PV combiner box’ DC circuit breakers, would not, in my view, be suitable for your system’s environment. This particular compatibility issue is sometimes referred to as the “72 V array problem”, and three of your “24 V” nominal PV modules in series add up to “72 V”.
The 150 VDC limit is common for solar charge controllers. This is the limit for all OutBack charge controllers, and the same limit is used by many of our competitors. I know of one charge controller with a higher input voltage specs, but NAWS, this site’s sponsor, apparently no longer stocks this particular model.
Note that rewiring the array for series strings of two modules instead of three really isn’t an option. Due to high ambient summer temperatures {29 C (85 F) average in July, 45 C (113 F) record}, this array configuration’s operating voltage in the summer would be too low to fully charge the flooded-cell batteries.
You may not have many options at this point. One would be to consider adding ‘Low Temperature Overvoltage Bypass” devices. These devices bypass one module when the temperature drops below a specific threshold, and then they reconnect the module when the temperature increases. You’d need eight for your present array (one for each series string).
See: http://www.apollo-solar.net/specsheets/ApolloSolarLTOBSpecs.pdf
Another option would be to work with your customer’s dealer/installer to take back the Sanyo 170 modules and credit them for a different product. I’d be happy to provide you with a list of module configurations that would both meet the NEC code requirements and function correctly in your location. The list will be short, however, due to the combination of the product specs, high- and low ambient temperatures, and a 48 V (nominal) flooded-cell battery system.
I’m sorry to be the bearer of such bad news. But, I hope this helps, and that you’ll ultimately end up with the system performance you’re expecting.
Regards,
Jim Goodnight / "crewzer"
Eastern Regional Sales Manager
OutBack Power Systems
-
Re: Stand Alone, PV/Genny Hybrid Questions
Crewzer,
So your saying that if we continue as planned which was two seperate arrays each with 6 strings in parallel of 2 panels in series, for a combined Voc of 86.4 without calculating temp coefficient. This would not work in the summer due to low voltage, but if we change that to 3 panels groups in series it will melt/shutdown the controllers in the winter.
We have a back up diesel generator that will be hooked to the XW inverter to keep these batteries topped off. I am not sure if he knew about the summer temp derating but I am hoping that this will solve the summer low power problem.
That is something I will keep in mind as I design my own systems in the future. We knew that we were not going to be able to put more than two panels in series due to the voltage restrictions of the MX 60's and our lovely cold winters.
I was just informed that the customer purchased four 12v Caterpillar batteries that he wants to add to his bank of Ul-16's. I am not to sure about combining two different types of batteries due to the Ah capacity of each, won't this cause problems during recharge?
Also I have a copy of the NEC 2005, is this to outdated? -
Re: Stand Alone, PV/Genny Hybrid Questions
ISG,So your saying that if we continue as planned which was two seperate arrays each with 6 strings in parallel of 2 panels in series, for a combined Voc of 86.4 without calculating temp coefficient. This would not work in the summer due to low voltage, but if we change that to 3 panels groups in series it will melt/shutdown the controllers in the winter.
54.5 V is way below the (somewhat murky) charging and EQ requirements for the 48 V Interstate L-16 battery bank. See: http://www.batteries-faq.com/activekb/questions.php?questionid=1I was just informed that the customer purchased four 12v Caterpillar batteries that he wants to add to his bank of Ul-16's. I am not to sure about combining two different types of batteries due to the Ah capacity of each, won't this cause problems during recharge?Also I have a copy of the NEC 2005, is this to outdated?
HTH,
Jim / crewzer -
Re: Stand Alone, PV/Genny Hybrid Questions
Another approach would be to find a "12V" panel that also puts out about the same amps, and stack 2 of the Sharp panels with one of this panel for instance:
http://store.solar-electric.com/so85wa12voso.html
or
http://store.solar-electric.com/kysokc85wa12.html
To make a "60 volt" (nominal, very nominal) array. Not perfect, but the MPPT will make it as perfect as it can be.
Waiting for the "when will it be approved and available?" Classic from Midnight would be a third option, figuring that the MX60's can be sold off when it arrives, and if it arrives before summer, you'd be set. But I hate planning for things that are not quite here yet, even though I own a Spectro-Acoustics 217R (Midnight & Outback & Xantrex & Trace pre-history reference - and I bought it new). -
Re: Stand Alone, PV/Genny Hybrid QuestionsAnother approach would be to find a "12V" panel that also puts out about the same amps, and stack 2 of the Sharp panels with one of this panel for instance:
The only issue here is size different for mounting and my customers propensity to not want to spend more money.
Is there an easy solution for this summer issue? Will the "murky" charging voltage damage the longevity of the batteries? Will he have to run the genny daily to top off the batteries? Can we wire the batteries in 24v or 36v bank and have the MPPT step down the voltage? -
Re: Stand Alone, PV/Genny Hybrid Questions
The main problem with a lower voltage bank is that you have a 48V inverter already bought. -
Re: Stand Alone, PV/Genny Hybrid Questions
Yes, you can reduce the battery bank voltage--but you may need more charge controllers... They are current limited in their output--so if you drop the battery voltage by 1/2, you will get 2x the current (more charge controllers to manage the extra current).
Of course, then you will have to find the appropriate GT Inverter at 24 volts (vs the 48 volt Xantrex XW you are looking at now).
I think Ecnerwal's suggestion is a good one--find some reduced voltage panels (near same rated current), and then sell/return 8 of the Sharp panels... Of course, this will reduce output--so you may need to mix and match a couple extra "2.5 panel" strings--depending on customer's requirements and mounting area.
Other than the panels may look different--it should be a reliable solution (after checking against controller specifications).
-BillNear San Francisco California: 3.5kWatt Grid Tied Solar power system+small backup genset -
Re: Stand Alone, PV/Genny Hybrid Questions
I am not suggesting going against the advice Jim has given, but I am running four KC130's in series and haven't had an issue. The lowest solar input voltage I have seen on our MX-60 on a hot summer day was 62, but it typically runs in the upper 60's in summer. Granted I am grid tied so my battery bank only needs to get pushed to 54 volts to get the XW to start selling, so I have some head room. If it were me I would wire it with 2 in series understanding on some hot summer days you might not get as much as you could otherwise. I would upsize the longer panel to controller wiring to avoid any additional loss at that point.3kw solar PV, 4 LiFePO4 100a, xw 6048, Honda eu2000i, iota DLS-54-13, Tesla 3, Leaf, Volt, 4 ton horizontal geothermal, grid tied - Green Bay, WI -
Re: Stand Alone, PV/Genny Hybrid Questions
ISG,Is there an easy solution for this summer issue?
Building on some of the suggestions above, you could consider going with a 24 V battery system. One approach would involve returning/selling the XW6048 and replacing it with an XW4024. You’d also need to go from two charge controllers to three. Three 1,360 W STC eight-module PV sub arrays would each be wired up as 2 (modules per series string) x 4 (series strings in parallel). There’d be no high- or low-voltage array problems in the summer or winter.Will the "murky" charging voltage damage the longevity of the batteries? Will he have to run the genny daily to top off the batteries?Can we wire the batteries in 24v or 36v bank and have the MPPT step down the voltage?... I am running four KC130's in series and haven't had an issue. The lowest solar input voltage I have seen on our MX-60 on a hot summer day was 62, but it typically runs in the upper 60's in summer.
HTH,
Jim / crewzer -
Re: Stand Alone, PV/Genny Hybrid Questions
Maybe the lucky zoneI am located in Green Bay, WI if that helps at all and the panels are mounted starting about 4 inches off the roof and go up from there with good convection cooling, they are tilted with a bias towards winter at about 55* so they may not get as hot as they would with a flat southern exposure as well.
And as Jim pointed out (and I forgot) my AGM's require lower voltages then regular lead acid's.3kw solar PV, 4 LiFePO4 100a, xw 6048, Honda eu2000i, iota DLS-54-13, Tesla 3, Leaf, Volt, 4 ton horizontal geothermal, grid tied - Green Bay, WI -
Re: Stand Alone, PV/Genny Hybrid QuestionsIs there an easy solution for this summer issue?
hmmmm....
Jim / crewzer -
Re: Stand Alone, PV/Genny Hybrid Questions
The problem with a switching method - if manual, the owner needs to remember to do it - the code folk are generally not happy with that, since the home might be sold, or the person who remembers to do that might be incapacitated or expire, and there the system sits, ready to produce more than rated voltage....
If automated, the automated system could fail. I guess if apollo (?) is making a listed system to switch out a panel, someone feels that it's not too likely to fail.
A good old fashioned bimetallic thermostat that switched in a hefty resistor across the leads (rather than switching out a panel) would be among the more reliable methods - but I still don't know that it would meet code. That could have the resistor sized so that you still got useful power out to the charge controller, just removing the "open circuit" condition when the VOC would be too high. The resistor robs a little power, but by doing so keeps the output voltage below 140, and all is peachy.
For that matter you could ignore the temperature and build a charge controller that switched in a series of "dump" resistors if it found the voltage to be creeping too high as it was sweeping - or working the other direction, it switches in all its dump resistors (as default configuration for night, say), measures voltage, and if that's low enough, switches out one and rechecks - if still low switches out another, until it gets to the point of switching out the last one, if that fits its model.
A PTC thermistor could also work, in theory, but I can't find any parts with a low enough operating point, in practice, on a quick look.
<edit - add>
The thing being, code tends to be concerned with what happens when things go wrong, and things can go wrong with any of these schemes to pull the voltage down. The cold-climate 150 VDC VOC solution is "60V" arrays, because even when things go wrong, they won't go above the rated voltage of the 150vdc breakers... -
Re: Stand Alone, PV/Genny Hybrid Questions
I agree... it's a pretty "sketchy" concept...
Jim / crewzer -
Re: Stand Alone, PV/Genny Hybrid Questions
Sounds like I have some more work to do. I will talk to my customer and see what he thinks.
My last question is regarding wire. I have been trying to source some wire in town and most of the suppliers have very little knowledge of anything DC related. I have been doing some research and found that the use of the finely stranded cable often causes more problems than its worth. So I am going to order the standard class B stranded wire.
What is the best type of coating/insulation to order? I have not received the new NEC code book yet or I would not need to ask this. I read that the typical THHN-2 or USE-2 are not acceptable any more. It then says that specific PV wire is required, do I ask my supplier for that specifically?
Please advise
James
Categories
- All Categories
- 229 Forum & Website
- 137 Solar Forum News and Announcements
- 1.4K Solar News, Reviews, & Product Announcements
- 199 Solar Information links & sources, event announcements
- 898 Solar Product Reviews & Opinions
- 256 Solar Skeptics, Hype, & Scams Corner
- 22.5K Solar Electric Power, Wind Power & Balance of System
- 3.5K General Solar Power Topics
- 6.7K Solar Beginners Corner
- 1K PV Installers Forum - NEC, Wiring, Installation
- 2.1K Advanced Solar Electric Technical Forum
- 5.6K Off Grid Solar & Battery Systems
- 428 Caravan, Recreational Vehicle, and Marine Power Systems
- 1.1K Grid Tie and Grid Interactive Systems
- 654 Solar Water Pumping
- 816 Wind Power Generation
- 624 Energy Use & Conservation
- 619 Discussion Forums/Café
- 312 In the Weeds--Member's Choice
- 75 Construction
- 124 New Battery Technologies
- 108 Old Battery Tech Discussions
- 3.8K Solar News - Automatic Feed
- 3.8K Solar Energy News RSS Feed