Inverter eating up my power!

mike760
Registered Users Posts: 57 ✭✭
4 @ Conext XW Pro 6848 120/240 Off-Grid Multi-Unit; new install
Something strange is happening with the AC Load. I have 4 inverters so I have the standard setup of four 60A breakers using the breaker bus bars to parallel them. I turned on all 4 DC breakers to power up all of the inverters. I connected a 220VAC/9A load and turned on the first AC breaker which is connected to the master inverter and it supplies power as it should. I then turned on the second AC breaker for the second inverter and the load switches from inverter 1 to inverter 2 instead of sharing. Inverter 1 displays 0.00 load and inverter 2 displays about 1.6. As I turn on breakers 3 and 4 the load is equalized between inverters 2-4 but the first one stays at 0 load on the display. I then turned off the 220 load and noticed that inverters 2-4 were still displaying about 2KW total load. I checked the amperage on each leg of the AC Load terminals and found that the total amperage of inverters 2-4 matched that of inverter 1 (approx 9A).
Ground and neutral test 0A. When I shut off the AC breaker for inverter 1 the load across all inverters drops to 0.
Where could the power be going when there is no load connected? Well, I took a reading on the DC cables coming off inverter 1 and found that it jumped about 25A every time I turn on the AC breaker for inverter 1 and one additional inverter.
So.... basically inverter one (master) is drawing power on its AC Load terminals from the AC Load terminals of the other 3 inverters and dumping the power onto the DC terminals. Is this even possible?!?!
Check out the pic from the gateway:
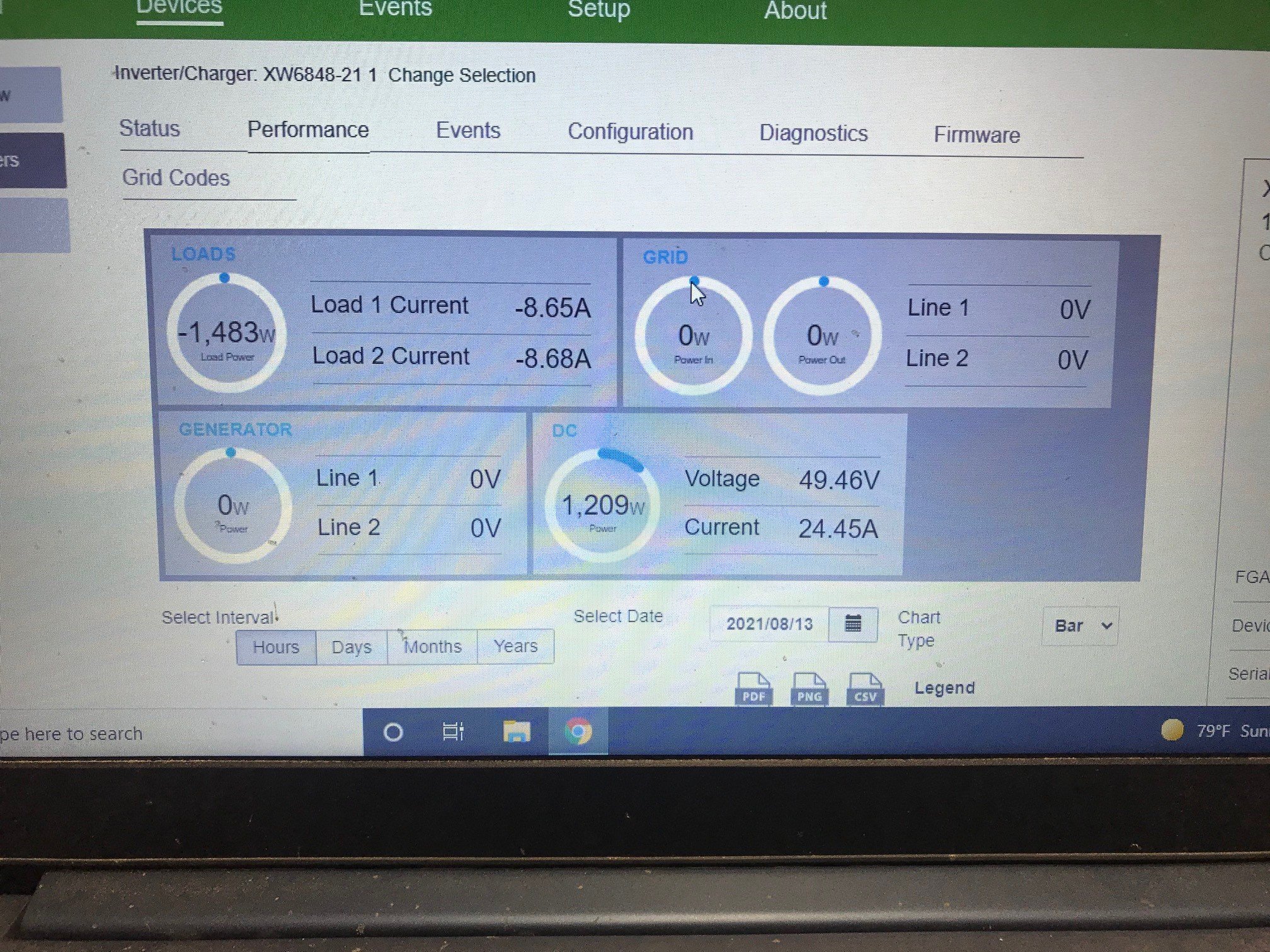

Something strange is happening with the AC Load. I have 4 inverters so I have the standard setup of four 60A breakers using the breaker bus bars to parallel them. I turned on all 4 DC breakers to power up all of the inverters. I connected a 220VAC/9A load and turned on the first AC breaker which is connected to the master inverter and it supplies power as it should. I then turned on the second AC breaker for the second inverter and the load switches from inverter 1 to inverter 2 instead of sharing. Inverter 1 displays 0.00 load and inverter 2 displays about 1.6. As I turn on breakers 3 and 4 the load is equalized between inverters 2-4 but the first one stays at 0 load on the display. I then turned off the 220 load and noticed that inverters 2-4 were still displaying about 2KW total load. I checked the amperage on each leg of the AC Load terminals and found that the total amperage of inverters 2-4 matched that of inverter 1 (approx 9A).
Ground and neutral test 0A. When I shut off the AC breaker for inverter 1 the load across all inverters drops to 0.
Where could the power be going when there is no load connected? Well, I took a reading on the DC cables coming off inverter 1 and found that it jumped about 25A every time I turn on the AC breaker for inverter 1 and one additional inverter.
So.... basically inverter one (master) is drawing power on its AC Load terminals from the AC Load terminals of the other 3 inverters and dumping the power onto the DC terminals. Is this even possible?!?!
Check out the pic from the gateway:
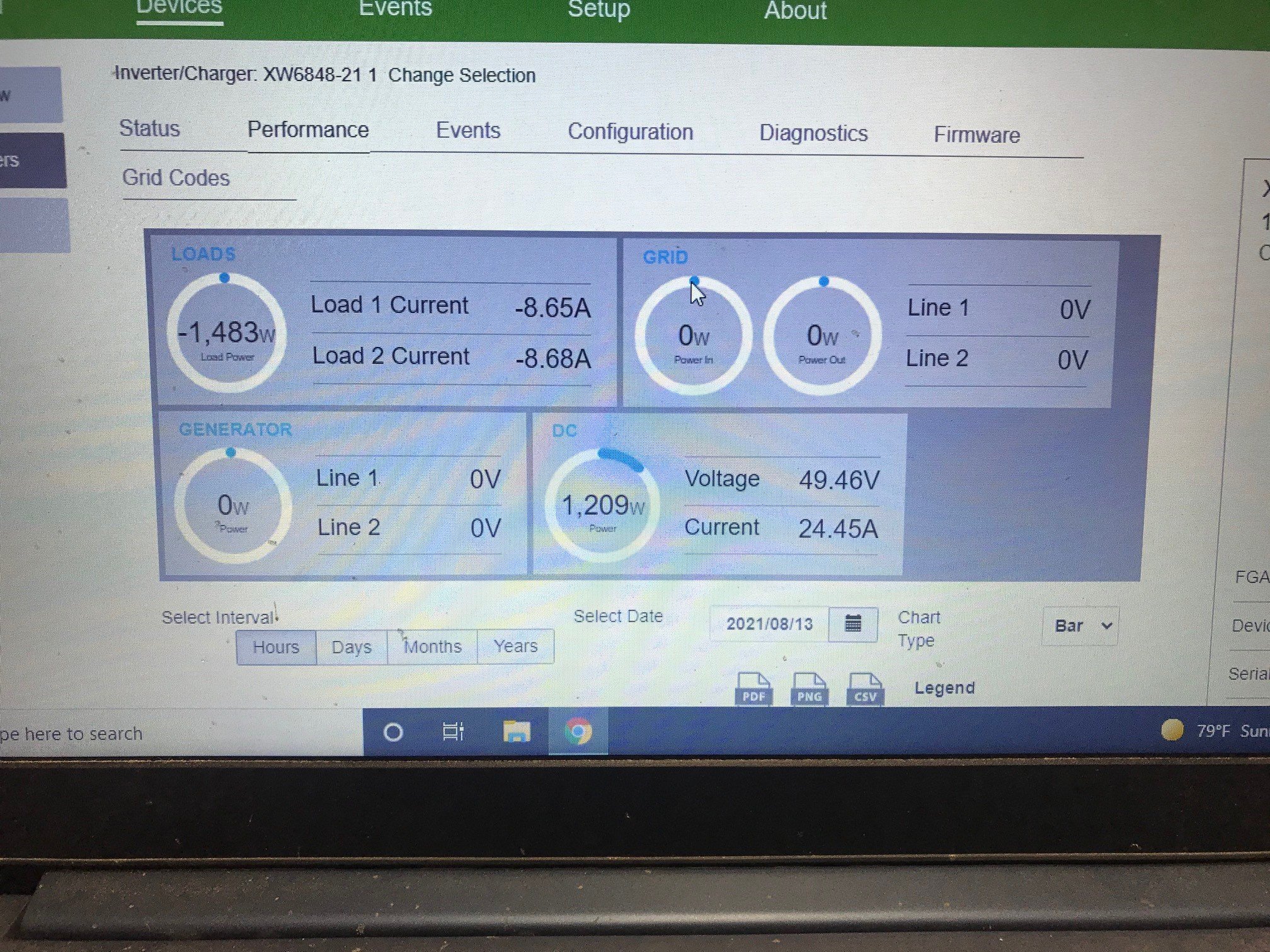
Comments
-
There may be several things involved. I am not directly famiiar with parallel ganged 6648 operation so these comments are general technical aspects that can happen.
With their comm interconnect and syncronization process they likely have a scheme to conserve inverter overhead idle power if the load requirement can be met with one inverter. Each inverter requires 30-40 watts just to idle so why waste the power if output AC load is met easily by one inverter. The situation might be a different strategy if the inverters must be ready to take a high starting surge device where all inverters need to immediately available when the surge requirement might happen. It does take a few millisecs to bring an idling inverter out of idle to active mode. I am not sure how the 6648 handles this.
Second is charger setup for battery charging. If one inverter has a float or absorb setting that is different from others each will try to regulate the battery to its respective setting. The highest float or absorb inverter will try to push the battery to that level. The lower setting inverter seeing higher then its setting will try to drag down the battery level. This can just push AC power back out to be sucked in by other inverter trying to keep higher battery voltage regulation setting. Power just circulates around the two inverters in opposite directions.
I would expect with inter-inverter communications they should resolve this on its own but maybe for battery charge level it does not do this since it cannot be sure which of the two different settings is the true desired setting. The best way to handle this would be the assigned master inverter is where user sets up parameters that are then communicated out to other inverter via comm bus.
A hybrid inverter is like a auto transmission with a particular 'gearing ratio' setting when it is running. If battery is pulled higher in voltage by external source the AC hybrid inverter at a given 'gearing ratio' will force the higher voltage battery down by pulling DC current and pushing AC power output. It may not change its 'gearing ratio' unless pushing to grid is disallowed or AC out loads are not sufficient to consume the AC current push from the inverter trying to drag down its battery voltage to meet the setting values.
So make sure all the inverters have the same battery charging parameters, and they match as there can be calibration accuracy variation on each inverter. On my older series conected inverters I have to 'tweek' one of the battery float levels down 0.1v from other to minimize the circulating power issue because the calibration is not perfect between the two inverters.
Biggest user confusions on the XW inverters is there are so many setting parameters that can have inter-dependent ramifications to other settings that are not obvious to the user.
-
So there are 4 ports for power to go in/out on this system:
1. AC1 (Grid)
2. AC2 (Generator)
3. AC Load (Distribution Panel)
4. DC (Battery Bank)
AC1 & DC should be able to have bi-directional power flow for purposes of grid supply/sell and charge/discharge respectively. I would not think that power should flow into the AC Load terminal and exit the DC terminals. This would essentially create a loop in a multi-inverter system. One inverter is pulling power from the batteries to feed it into another so it can charge the batteries? Something doesn't sound right there. Especially when the charger is disabled on this inverter.
I will review the charger settings as recommended. I just can't get away from certain things like the fact that it shows a 2000W load when there is no load and power is going around in circles. -
Just back down your max charging current settings on all the inverters to a very low level and see if your 2000 watt drops accordingly.
If you have a clip on DC amp meter you would also see the current flow direction and level into the various inverters. -
I disabled the chargers on all 4 inverters and I have the same problem. I also checked DC flow and inverters 2-4 are drawing power from the batteries and inverter 1 is sending/charging the batteries. AC power is flowing from the AC Load terminals of inverter 2-4 and going into the AC Load terminals for inverter 1. My meter readings also match the readings from the gateway as you can see from the original screen shot.
-
You asked about the devices in the system another post. What have you got besides 4 xwp's? Network is critical on large systems.
Have you read the multiunit design guide from Schneider? What do they say?
A picture of the install may help to break this down. Everything good with firmware? There were fixes that applied recently for offgrid XWP's. I had 2 large ones that got fixed last winter.
This sounds to me like either config or firmware.
So humor me to play along, what are you doing with this much power offgrid? A machine shop? Micro grid?"we go where power lines don't" Sierra Nevada mountain area
htps://offgridsolar1.com/
E-mail offgridsolar@sti.net -
I can post a few pics but no laughing. This is my first install and I do have some stuff temp'd in so I'm not done yet. Unless someone sees something major incorrect/dangerous, then go easy on me.
-
So Inv 1 is backfeeding via AC_out port to battery while 2-4 (assume that means 2,3, & 4) are forward feeding battery to their AC_out. This is the circular power flow.You did not mention about AC_in's on the various inverters so as per sheet shot I assume there is no AC_in to any of the inverters.Does this issue remain the same if you have AC_in to inverters? AC_in would be master for phase in this case. If inverter 1 had a calibration problem between phase measurement and inverter phase setting it would immediately shut down when connect relay was closed to AC_in due to inverter overload caused by phasing not aligned well. Need to try this on grid and not a generator.
The actual inverter circuit is hardwired to AC_out and all four inverters AC_Out are hardwired in parallel and should be synchronized (unless you open an AC_out breaker on an inverter).
The fact you say inverter 1 is allowing backflow into AC_out port sounds like AC coupling in enabled. I don't recall if AC_coupling function has to be user enabled or not. Normally I would expect it to throw an error like AC_in connected to AC_out unless AC_coupling allowed. Perhaps the 6648 allows some backflow if there are multiple inverters tied in parallel but I would think it would only be for small period of time while inverters adjust there levels and would complain if 2kW is continously backfeeding unless AC coupling was allowed.
Assuming you have no actual defect in an inverter, you likely have a setup issue. I would review manual for all the setups for running parallel inverters. Also any AC_coupling settings. If there is no AC_in, one of the four inverters have to be the master for phase synchronization. If inverter 1 is running slightly off phase to other three it could show the issue you describe.
Does issue go away if you leave inverter 1 out of the mix?
Also, check to make sure L1 & L2 wiring on AC_out's are not reversed on any inverter. -
RC, yes I think you understand what I've got going over here. This is off-grid and the situation is happening without any generator input. So no AC input at all. AC coupling is enabled because when I disabled it, the inverters all display dashes and do not do anything. The generator is connected to AC1 as specified in the multi-inverter configuration guide but was disconnected to eliminate possibilities. And yes, if I turn off the AC breaker for inverter 1 the load on 2-4 goes away.
When I load the system with about 2000W it still has the same problem. When I load it with more, say 24000W it seems like it goes away but inverter 1 never shares the same load. Today I observed inverter 1 at 8K and the other three at about 5K. And then sometimes 2-3 are at 6K and inverter 1 is at 2K. Really weird... I thought they should all be fairly close at all times but inverter 1 is always doing its own thing.
-
Ok Dave, here are a couple pics. It's basically a 35' container that I converted into a solar shack. I might have some other pics too if I can find them.
It's hard to take pics in such a small building but anyway.... it's work in progress...
I poured a pad for my generator. It puts out about 125KVA. Got a Volvo Penta turbo charged diesel in it with a Mecc Alte 125KVA alternator that puts out enough to run my coffee maker and some other things. I also set a 1000GAL diesel tank to cut down on trips to the gas station. I know the output line is temp'd on the ground right now, not the best, but there are two 2" conduits that run underneath the pad and pop up in the generator power compartment. Maybe I'll pull the wires for it this week. I currently have two arrays with 132 panels each at 250W, so total 264 panels 66,000W. As you can see at the end on the left I am clearing a spot for the third array. -
"AC coupling is enabled because when I disabled it, the inverters all display dashes and do not do anything."
That does not sound normal unless it is a requirement for paralleling inverters. Ask Conext support about that. I don't have experience running those inverters in parallel but can understand why there may be some short time backfeeding when one unit is brought on line and standby'd based on different load demands.
I assume you have the same firmware version on all inverters. -
Yea RC, AC coupling is a default and should be left on for XW pro series.
Still no answer on the firmware revision. I can't pry that out of you. Nice install and it looks to me like all of the basics were done. Can't see the external XFER, is it there?"we go where power lines don't" Sierra Nevada mountain area
htps://offgridsolar1.com/
E-mail offgridsolar@sti.net -
Ok, I might have come across the answer while searching for something else. It's an old doc but I think it clears things up to a certain extent. Looks like this behavior of feeding power back through the output is by design.
Here's a link to the "Application Note":
https://download.schneider-electric.com/files?p_enDocType=Data+Bulletin&p_File_Name=AC+Coupling+Application+Note.pdf&p_Doc_Ref=976-0240-01-01
-
Here ya go Dave!
1.11.00bn28
Here's a pic from the business side of the two arrays. They are each about 25'D by a little over 100'W.
-
And the ASCO 300 Series ATS:
-
BTW, SE apparently does not support this configuration as of a few months ago. They now want to eliminate the ATS and install an external contactor instead. So they don't really want to help out much with the settings. I am currently using the AUX port to signal low SOC to engage the ATS/Genset.
-
I think you are wrong on SE. The ASCO external contactor has been a part of more than 2+ XW systems for at least as long as I can remember.
At least 10 years. The multi-unit design manual was updated this year. I was in training last spring for it with Xwp and Schneider ASCO
Are you cooling that container?"we go where power lines don't" Sierra Nevada mountain area
htps://offgridsolar1.com/
E-mail offgridsolar@sti.net -
I dunno about being wrong on that there Dave... While I agree that ASCO was part of it in the past, that no longer seems to be the situation. I have an email from SE requesting that I remove the ASCO from my config and replace it with a contactor so that I have a supported configuration. There are no longer any references to an ATS or ASCO for any new installs. I'll leave a link to the complete doc below but here is a clip from the documentation:
https://solar.schneider-electric.com/wp-content/uploads/2020/07/XW-Pro-Multi-unit-Design-Guide-990-91373.pdf
-
Oh and ya I'm cooling it with about 3 tons of air. Generates lots and lots of heat! A cooling system is a must for anyone considering any sizable system.
-
This is what I used last winter but it sounds like you have had both ways of saving the internal 60A relays?
The screen below is for grid but the offgrid version is just swapping the connection over to AC2 and a genset.
If you are still with the problem, maybe you have damaged an internal relay? There are alot of contacts in the relays that have to be perfect.
Pull the covers over the relay pcb and look for smoky plastic covers. If they are good, and it sounds like everything else is correct to me, then as RC said triple check your wiring. This issue is not normal with XWpro. The earlier issues with multiunit systems was fixed and both of my clients are good. Below is a screen of some of them. Has Schneider looked at your system from the cloud? You may want to insist on it or hire me😉
I always try and follow the less is more for offgrid. Supporting huge loads is too much work and it can be cheaper in the long run to just spend the money on conservation of the loads. I know you do not want to hear that and it is impressive how much work you have put into this. Have a good day !
"we go where power lines don't" Sierra Nevada mountain area
htps://offgridsolar1.com/
E-mail offgridsolar@sti.net -
This is a new install and it started with these issues on powerup and with only a 2000W load so I doubt I cooked a relay. I did inspect them anyway and they are all nice and clear. I'm not grid connected so I don't see the need for a second ATS. I might have to implement the contactors though in order to get support and then figure out what do do with the ATS.
All of the wires are connected correctly. SE has not connected to it yet but maybe they should just to check out all my settings. I know smaller is easier but this system is going to continue to grow. I have 24 of the Rolls 2YS31P batts right now and another 24 on the way. The amount of amperage is getting crazy along with the equipment and wiring to support it. I'll see if I can snap a couple pics of the disconnects for the generator power to support everything.
-
mike760 said:Ok, I might have come across the answer while searching for something else. It's an old doc but I think it clears things up to a certain extent. Looks like this behavior of feeding power back through the output is by design.
Here's a link to the "Application Note":
https://download.schneider-electric.com/files?p_enDocType=Data+Bulletin&p_File_Name=AC+Coupling+Application+Note.pdf&p_Doc_Ref=976-0240-01-01
The paragraph after the yellowed paragraph is the crafty worded issue it can create. Power has to go somewhere. When backfeeding ACout, choices are push it to grid or push it to battery. If grid is not present or setup blocks backfeeding grid then only thing left is dumping to batteries.
What the text below yellowed paragraph says if battery is full 'the charge is terminated'. What it doesn't say is with no alternative place to push the power the only choice is to shut the inverter down when battery cannot accept any more backflow power.
The inverter could raise the ACout voltage until backflow drops to zero but that is not a viable option beyond a minor increase. This is what the parallel inverters do to regulate the load leveling but again it should only be a slight change in ACout voltage.
What the op's problem is the other three parallel inverters are sucking down the battery so inverter 1 can backfeed to battery. Round and round the power flow goes. One of the inverters, likely #1, is incorrectly interpreting its ACout voltage or battery voltage. Having different battery charge voltage settings between inverters, like inverter 1 thinks the battery voltage is lower then its float voltage setting, is usually the cause of this if just a setup issue. Internal unit calibration for voltage reading being off can also cause it.
Actually that brings up a point. If battery cabling has more loss to one inverter it could cause something like this. Could be something as small as a poorly tighten or crimped lug connection. That connection would likely get warm. -
I did some troubleshooting by adjusting the charge settings. In one config, I turned off the charge on #1 and left it on for #2-4. Same result. I then disabled charging on all four. Same result. So I can accept this if the documentation says that it is possible to have a current backflow but 2000W??? I think that is way too much and it throws the displays off and the reporting in the gateway.
I can check the connections again but I installed everything very carefully. As you can see from the previous pic, all of my connections have either crimp ferrules or crimp lugs. All lugs were equally crimped with a hydraulic crimper and I even put all of the heat shrink on there. I purchased lot of rolls of wire from Polar to make all of the custom length connections. (BTW Polar wire is awesome) I followed the torque guides for all connections. I also checked temps all over the place with my laser as well as inspecting with my thermal imager and everything looks great. Most temps around 70F with some around 90F depending on what's happening.
I'm going to turn some things off and check them over again. Today the system has been averaging a 15KW load. Inverter 1 display usually shows 0 while inverter 2-4 show about 5.0. Gateway shows inverter 1 with a load varying from -300W to 200W. DC power also bouncing around from positive to negative. -
From what the text imples the backfeed limit is based solely on battery absorb voltage setting. This may also mean, other then absorb voltage setting, all other charging parameters are ignored, including charging disabled setting. This makes sense since there is no other option then having the battery take all the backfeed power.
Wording is a little wrong "bulk voltage" should read "absorb voltage" -
The battery should not be being backfed in a DC coupled system as here. You can test this by disabling the XW's chargers. This is not the problem as this happens during times when the genset is not on, I think....
Another way to eliminate this is to look at frequency during bulk or absorb or float. If it is rock steady 60 then you can check off AC coupling being an issue.
AC coupling is designed in on Pro to be extremely fast and to not interfer with DC coupled charging or genset operation."we go where power lines don't" Sierra Nevada mountain area
htps://offgridsolar1.com/
E-mail offgridsolar@sti.net -
Dave, see my last post from yesterday re troubleshooting by disabling the chargers. This did not stop the problem and remember I am totally off-grid, There are no utilities available here... I don't even have an address.
-
My point was to RC and not you Mike. Been offgrid here for 30 years next spring!"we go where power lines don't" Sierra Nevada mountain area
htps://offgridsolar1.com/
E-mail offgridsolar@sti.net -
Oh got ya. Got some questions on my batteries. Should I start a new thread or go for it here?
-
I suggest you continue with this thread... Lots of details about your system already--Keeping all system information together is usually helpful.
You can do a second thread if you think the battery discussion will distract from your present topic.
-BillNear San Francisco California: 3.5kWatt Grid Tied Solar power system+small backup genset -
Ok so I am concerned about my batteries being fully charged. The battmon and SCP both indicate that the batteries are at 100%. They reached this level about 10am and maintained it until 5pm today. This afternoon at about 3pm I decided to check the charge state. It is my understanding that the only way to accurately determine the true SOC is to use a refractometer, not even a hydrometer. So I broke out my scope and tested the specific gravity on all 24 batteries. The results are posted below. I am concerned that they all were in the fair category with some being borderline discharged. None were in the good category on the scope. I also listed the manufacturer's table for charge percentage at the end. These batteries are less than a year old. I have a feeling that it is not so much bad batteries as it is incorrect charging/reporting by the conext system. Battery type is Rolls Surrette 2YS31P.
Batt # 8/18/2021 1 1.235 2 1.21 3 1.22 4 1.23 5 1.23 6 1.24 7 1.235 8 1.24 9 1.24 10 1.235 11 1.245 12 1.24 13 1.23 14 1.24 15 1.24 16 1.23 17 1.24 18 1.23 19 1.24 20 1.225 21 1.22 22 1.23 23 1.23 24 1.24 Average 1.233125 Charge Specific Gravity 100 1.255 - 1.275 75 1.215 - 1.235 50 1.180 - 1.200 25 1.155 - 1.165 0 1.110 - 1.130
Any feedback is appreciated.
-
Hi Mike,
Nice system that you have there.
Here is a Link to the Surrette Battery User Manual, there are charging parameters, on page 13:
https://www.rollsbattery.com/wp-content/uploads/2018/01/Rolls_Battery_Manual.pdf
It is not clear, just how this battery bank has been/is being used. If cycled-daily, how much Distilled Water has been needed, and how often, to make up for water loss?
If you have not yet done so, why not EQ that battery bank, in the lower range of suggested EQ voltages?
Did you follow the suggested method of Commissioning a Flooded battery bank, within days of the arrival of this bank?
As you probably know, many more battery banks are killed from undercharging, than are killed from overcharging.
And, IMO, a good glass tube/glass float Hydrometer is perfectly fine for measuring SGs, as long as it has numbers on its scale, and, not just colors and words ...
More later, Thanks, VicOff Grid - Two systems -- 4 SW+ 5548 Inverters, Surrette 4KS25 1280 AH X2@48V, 11.1 KW STC PV, 4X MidNite Classic 150 w/ WBjrs, Beta KID on S-530s, MX-60s, MN Bkrs/Boxes. 25 KVA Polyphase Kubota diesel, Honda Eu6500isa, Eu3000is-es, Eu2000, Eu1000 gensets. Thanks Wind-Sun for this great Forum.
Categories
- All Categories
- 228 Forum & Website
- 136 Solar Forum News and Announcements
- 1.4K Solar News, Reviews, & Product Announcements
- 199 Solar Information links & sources, event announcements
- 898 Solar Product Reviews & Opinions
- 256 Solar Skeptics, Hype, & Scams Corner
- 22.5K Solar Electric Power, Wind Power & Balance of System
- 3.5K General Solar Power Topics
- 6.7K Solar Beginners Corner
- 1K PV Installers Forum - NEC, Wiring, Installation
- 2.1K Advanced Solar Electric Technical Forum
- 5.6K Off Grid Solar & Battery Systems
- 428 Caravan, Recreational Vehicle, and Marine Power Systems
- 1.1K Grid Tie and Grid Interactive Systems
- 654 Solar Water Pumping
- 816 Wind Power Generation
- 624 Energy Use & Conservation
- 619 Discussion Forums/Café
- 312 In the Weeds--Member's Choice
- 75 Construction
- 124 New Battery Technologies
- 108 Old Battery Tech Discussions
- 3.8K Solar News - Automatic Feed
- 3.8K Solar Energy News RSS Feed