Fast Voltage drop at 100% charge
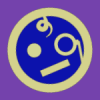
jonnyd
Registered Users Posts: 2 ✭
Hello!
I need help troubleshooting a voltage drop I am experiencing.
I just built a van electric setup running solar (525W), Alternator (30v) and shore power to two LiFePo4 100ah batteries. All tied in via positive and negative busbars. I monitor system with Victron battery monitor.
The system has been working very well for about a month.
Today I entered the van to the sound of the Renogy 2000W inverter low Voltage trip alarm.
Turn it off, check the battery via monitor. Full or close to full charge. Put a load on it, and it does not reduce charge at all (stays at steady 100%).
Rather, the voltage drops, and fast. With a draw of 160 watts voltage will go from 12.8 to 10.8v in less than 10 min. Yesterday this wasnt happening, and literally nothing has changed that I know of.
Im thinking it might be a ground connection: The only ground I have for the whole system is the starter/car battery chassis ground on the Promaster, and it runs in 6awg wire about 25ft to the back of the van.
I checked all connections, cleaned any corrosion, redid a lugs. Nothing. I added an auxiliary ground to chassis near busbars, nothing.
If I turn my main control switch off and then back on, things turn on for a split second, then everything shuts off, including battery monitor, everything. The only way i found to turn it all back on was to hit the start button on my sterling Battery to Battery charger connecting to the starter battery and ground.
Im at a loss what could be causing such fast voltage drop at full charge on new batteries. Any ideas are welcome!
Thank you!
I need help troubleshooting a voltage drop I am experiencing.
I just built a van electric setup running solar (525W), Alternator (30v) and shore power to two LiFePo4 100ah batteries. All tied in via positive and negative busbars. I monitor system with Victron battery monitor.
The system has been working very well for about a month.
Today I entered the van to the sound of the Renogy 2000W inverter low Voltage trip alarm.
Turn it off, check the battery via monitor. Full or close to full charge. Put a load on it, and it does not reduce charge at all (stays at steady 100%).
Rather, the voltage drops, and fast. With a draw of 160 watts voltage will go from 12.8 to 10.8v in less than 10 min. Yesterday this wasnt happening, and literally nothing has changed that I know of.
Im thinking it might be a ground connection: The only ground I have for the whole system is the starter/car battery chassis ground on the Promaster, and it runs in 6awg wire about 25ft to the back of the van.
I checked all connections, cleaned any corrosion, redid a lugs. Nothing. I added an auxiliary ground to chassis near busbars, nothing.
If I turn my main control switch off and then back on, things turn on for a split second, then everything shuts off, including battery monitor, everything. The only way i found to turn it all back on was to hit the start button on my sterling Battery to Battery charger connecting to the starter battery and ground.
Im at a loss what could be causing such fast voltage drop at full charge on new batteries. Any ideas are welcome!
Thank you!
Comments
-
A fully charged 12V nominal LiFePo4 battery would be ~ 14.4V or 3.6 volts per cell, 12.8 or 3.20 VPC is about 17% so it's no surprise the voltage drops rapidly when a load is connected. Typically it's best to operate in the 90% to 20% state of charge (SOC) range to prevent damaging the cells which become unbalanced, at the lower extreme in a top ballanced bank, the reverse in a bottom ballanced bank.
The chart above represents an approximate SOC but in reality it is dependent on individual cells as monitored by the battery monitoring system (BMS), the first cell to drop below a value will disconnect the load on discharge assuming a BMS is being used. The BMS also terminates charging when the highest cell reaches a value typically ~3.600V.
Because each BMS is different in the way it functions the above is a generalization but its close, there are other factors not mentioned regarding loads, charging regime, which are important, this is further complicated by combining an alternator and presumably a lead acid battery, my opinion for what it's worth, is keep them divorced from on another, they have different needs.
Not being familiar with Renolgy equipment or its capabilities, I would assume it is tailored to lead acid batteries where 12.8V may represent 100% SOC but that is merely speculation. You need to be very careful in understanding your battery requiments, LiFePo4 are very sensitive to overcharging and over dischargeing, hopefully there is a BMS involved which protected the individual cells but often these parameters are extremes, meaning it's better to avoid them, kind of like the oil idiot light on a car, when it comes on it means there is no oil and the majority of the damage is already done.
Most inverters are tailored to lead acid with low battery cut out (LBCO) values too low for LiFePo4, the very minimum should be 12V as opposed to 10.5V, but ~12.9V would be preferable, for this reason a cellular phone will warn of low battery at ~20%, it's to preserve the life expectancy.
Hope this helps explain some of the basics, please elaborate with details which may be helpful, such as controller settings, actual batter specifications if drop in replacement type or not, BMS specifications if applicable and so on.1500W, 6× Schutten 250W Poly panels , Schneider MPPT 60 150 CC, Schneider SW 2524 inverter, 400Ah LFP 24V nominal battery with Battery Bodyguard BMS
Second system 1890W 3 × 300W No name brand poly, 3×330 Sunsolar Poly panels, Morningstar TS 60 PWM controller, no name 2000W inverter 400Ah LFP 24V nominal battery with Daly BMS, used for water pumping and day time air conditioning.
5Kw Yanmar clone single cylinder air cooled diesel generator for rare emergency charging and welding. -
I suspect the batteries are in the lowest stage of charge, which is why the voltage collapses so quickly. You need to use a good volt meter and compare the cells in the battery pack.
Powerfab top of pole PV mount | Listeroid 6/1 w/st5 gen head | XW6048 inverter/chgr | Iota 48V/15A charger | Morningstar 60A MPPT | 48V, 800A NiFe Battery (in series)| 15, Evergreen 205w "12V" PV array on pole | Midnight ePanel | Grundfos 10 SO5-9 with 3 wire Franklin Electric motor (1/2hp 240V 1ph ) on a timer for 3 hr noontime run - Runs off PV ||
|| Midnight Classic 200 | 10, Evergreen 200w in a 160VOC array ||
|| VEC1093 12V Charger | Maha C401 aa/aaa Charger | SureSine | Sunsaver MPPT 15A
solar: http://tinyurl.com/LMR-Solar
gen: http://tinyurl.com/LMR-Lister , -
Rather than thinking the voltage drop might be wiring, why don't you simply measure the voltage directly at the battery terminals using a meter? The Victron reports battery SOC by coulomb counting (keeping track of current in/out of the battery). It has to be kept in sync with the actual battery state to work right. I'll bet your battery is very discharged and the monitor is out of sync. How is the shunt wired? Nothing should connect directly to the battery negative except the shunt, or the monitor will quickly get out of sync. Frequent partial charge/discharge cycles without a full charge will also cause it to lose sync. Finally, there are settings in the monitor which cause an automatic sync. If set wrong, it won't sync correctly and will think the battery is 100% charged when it isn't.
-
Thanks for the suggestions! Hadnt even considered it was an incorrect monitor sync reading. I just dont know how it would have gotten so discharged as to to be at such low voltage--probably the frequent discharge without full charge over time. When I shut the whole system down and restart it, the victron monitor goes back to saying it is 100%, though I know for a fact it wasnt. Definitely wrong. Ill get back to you once i give it a full charge and then put it under load and see what happens. Current multimeter voltage reading at batteries is 13.1. Shunt is wired one 2/0 from - bus bar, one 2/0 from battery terminal which has a temp sensor also on it, and one 16awg to positive on battery for power.
-
According to that diagram, that shunt is doing nothing. You have the battery negative wired to a bus bar, and everything else connected to that bus bar. The shunt needs to go between the batteries and the bus bar, so all current in/out of the battery goes through it.
Categories
- All Categories
- 228 Forum & Website
- 136 Solar Forum News and Announcements
- 1.4K Solar News, Reviews, & Product Announcements
- 199 Solar Information links & sources, event announcements
- 898 Solar Product Reviews & Opinions
- 256 Solar Skeptics, Hype, & Scams Corner
- 22.5K Solar Electric Power, Wind Power & Balance of System
- 3.5K General Solar Power Topics
- 6.7K Solar Beginners Corner
- 1K PV Installers Forum - NEC, Wiring, Installation
- 2.1K Advanced Solar Electric Technical Forum
- 5.6K Off Grid Solar & Battery Systems
- 428 Caravan, Recreational Vehicle, and Marine Power Systems
- 1.1K Grid Tie and Grid Interactive Systems
- 654 Solar Water Pumping
- 816 Wind Power Generation
- 624 Energy Use & Conservation
- 619 Discussion Forums/Café
- 312 In the Weeds--Member's Choice
- 75 Construction
- 124 New Battery Technologies
- 108 Old Battery Tech Discussions
- 3.8K Solar News - Automatic Feed
- 3.8K Solar Energy News RSS Feed