hard wiring solar panels
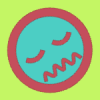
jdfnnl
Registered Users Posts: 15 ✭✭
Has anyone gotten into hard wiring panels directly to the charge controller, essentially undoing the crimps and soldering new wire onto these terminals. Just thought of trying to do away with all the clutter caused by the mc4 connectors, etc. Would be easier daisy-chaining new wires in a series arrangement, but in my case I would like to connect two panels in parallel and so would necessitate more than two sets going in/out of one of these if I use it as a junction box. Something just seems kind of lazy sloppy, and extravagant about using the various mc4 parallel connectors ..
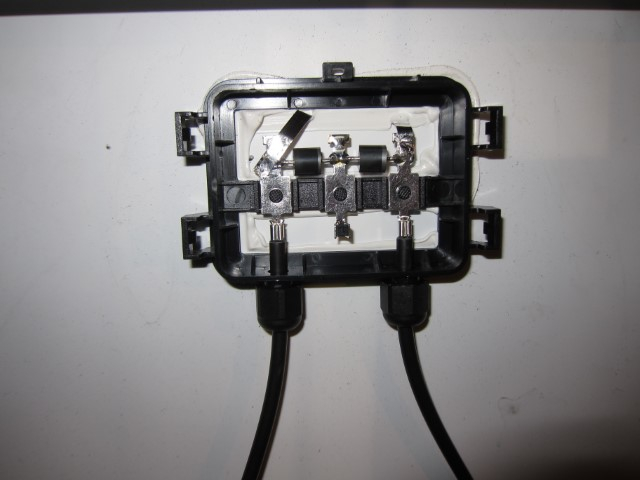
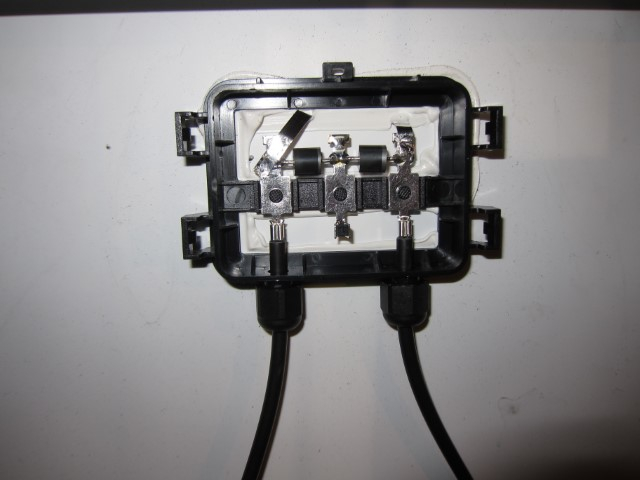
Comments
-
So you'll no longer be using a MPPT type charge controller?
https://forum.solar-electric.com/discussion/355946/hard-wiring-panels-in-parallel#latest
Home system 4000 watt (Evergreen) array standing, with 2 Midnite Classic Lites, Midnite E-panel, Magnum MS4024, Prosine 1800(now backup) and Exeltech 1100(former backup...lol), 660 ah 24v Forklift battery(now 10 years old). Off grid for 20 years (if I include 8 months on a bicycle).
- Assorted other systems, pieces and to many panels in the closet to not do more projects. -
Cutting the MC4 connectors will generally invalidate the panel warranty. Not a big issue with the low $$$/Watt prices of most panels this days).
If you go through the panel j-box, make sure you have a good seal. Water in j-boxes will generally take a panel down in something like months-year. Also, when wiring the panels, try to have a drip loop before any j-box. The loop being lower than the j-box entry will drain water off the wire before it can migrate into the j-box seals.
-BillNear San Francisco California: 3.5kWatt Grid Tied Solar power system+small backup genset -
probably will just go the easy route and buy some mc4 parallel connectors and patch cables. This is only because I am not going with a series arrangement which would still need only two cables to each panel daisy-chained, but with parallel I would have to figure out new seals and so forth. Not sure a good source of those water-proof ports -- I would only need two more, then the soldering would be easy.
Photowhit said:So you'll no longer be using a MPPT type charge controller?
https://forum.solar-electric.com/discussion/355946/hard-wiring-panels-in-parallel#latest -
jdfnnl said:So you'll no longer be using a MPPT type charge controller?
https://forum.solar-electric.com/discussion/355946/hard-wiring-panels-in-parallel#latestHome system 4000 watt (Evergreen) array standing, with 2 Midnite Classic Lites, Midnite E-panel, Magnum MS4024, Prosine 1800(now backup) and Exeltech 1100(former backup...lol), 660 ah 24v Forklift battery(now 10 years old). Off grid for 20 years (if I include 8 months on a bicycle).
- Assorted other systems, pieces and to many panels in the closet to not do more projects. -
MPPT can really only "squeeze out more power" in very cold weather (sub freezing or below)...And that is probably in the range of 10% to maybe a bit more. Not worth a lot of "extra" costs.
Where you get savings is that series connected panels need fewer "patch cables" and fewer Combiner Box fuses/breakers..
For example 3 panels in parallel means 3 fuses in a combiner box (and connectors for 3x set of panel connections).
If you put 3 panels in series, then you don't even need a combiner box or more than 1 set of MC4 patch cables... And you can use much thinner copper cables from array to charge controller/battery shed (or mount array much farther from battery shed/home if needed for better sun).
Of course, your panels have to match the MPPT controller specifications (i.e., three panels in series, etc.).
-BillNear San Francisco California: 3.5kWatt Grid Tied Solar power system+small backup genset -
Wasn't even thinking of fusing the panels between the controller because the 12ga cables have way more capacity than any short circuit current a panel could produce. Also I became convinced an MPPT would offer a bit more of a harvest from this video in this thread: https://www.cheaprvliving.com/forums/showthread.php?tid=41010
-
I did a few second look at the video... And I am not sure how accurate that is. Details matter.
And you can get 5% error between different charge controller readings if you are not using separate current meter (like a DC current clamp DMM) to measure both controllers' output).
And, there is an issue at what voltage the battery bank is. PWM is a fixed current output based on solar panel and sun. MPPT has a variable output current that also depends on battery bank voltage. Lower bank voltage, higher current output. For example:- 100 Watt panel / 17.5 Vmp = 5.71 Amps -- This would be the maximum charging current from PWM at noon on a clear day
- 100 Watt panel * 0.77 panel+controller derating * 1/14.5 volt charging voltage = 5.3 amps MPPT typical "best" harvest warm climate
- 100 Watt panel * 0.77 panel+controller derating * 1/12.0 volt charging voltage = 6.4 amps MPPT charging a near dead/low voltage battery bank
Power wise:- 5.71 amps * 12.0 volt battery charging = 68.5 Watts into battery (PWM)
- 5.71 amps * 14.5 volts battery charging = 82.8 Watts into battery (PWM)
- 100 Watts * 0.77 panel+controller deraign = 77 Watts typical best case MPPT harvest
- Power = Voltage * Current -- MPPT controllers can trade off Current and Voltage for "constant" Power (like an automatic transmission on a car--Matches V and I to battery bank needs)
Near San Francisco California: 3.5kWatt Grid Tied Solar power system+small backup genset -
It should have an advantage in the method he is using it. He has angled the panels directly at the sun and has set the system to an artificially low level. 12 or 12.1 volts would represent a battery who's resting voltage would be around 11-11.4 volts. basically a dead battery. If you regularly take your battery this low, save your money on solar and just throw it in the toilet.
The artificially low voltage allows the MPPT to work properly! Because it is 30% less than the panel is capable of producing. Once the battery/system reaches 13-13.5 volts and the panels heat up. I doubt he'll see much difference and it may well go negative if measured as current passing to the battery. Remember that the MPPT will make sweeps to check on the best voltage level to present to the battery and will use more energy it's self in small systems.
I don't think he's trying to mis-lead you, I just think he is ignorant... Heck he appears to sell or install flexible panels which are very short lived and really only should be used for very specific uses. I'd rather trust boB and Robin Gudgel. Who created some of the first effective MPPT type charge controllers.
These guys;
http://www.thesolar.biz/Midnite-Solar.htm
Both pop in here from time to time, boB has said he wouldn't expect more than a 10% advantage from MPPT type controllers to PWM when using panels that are designed to charge batteries of a specific voltage. Also he has suggested that you need 30% higher voltage than the system voltage to allow MPPT charge controller to work properly. It says so right on their string sizing tool...
While other manufacturers don't come right out and say it, it can be inferred in the fact that Morning star's string sizing tool will NOT suggest a string size with panels designed to work with a specific voltage in parallel, or y-solar suggesting strings of 2 or 3 panels in their manual.
Please note that your RV guy does hook up the panel in series to the MPPT controller, so if you don't believe me, believe him!Home system 4000 watt (Evergreen) array standing, with 2 Midnite Classic Lites, Midnite E-panel, Magnum MS4024, Prosine 1800(now backup) and Exeltech 1100(former backup...lol), 660 ah 24v Forklift battery(now 10 years old). Off grid for 20 years (if I include 8 months on a bicycle).
- Assorted other systems, pieces and to many panels in the closet to not do more projects. -
Guess this makes me not much less ignorant, except that I am in touch with you guys who know how to throw down the technical knowledge. Can't say it's rational, but just have the feeling an MPPT can squeeze out more power in low light conditions, but sense I would need to delve into the intricacies of the way each operates. I was considering a series arrangement except that the array will be on my vehicle and subject to different conditions that may impart shade on one panel and not the other now and then. All considered, this system would pull just as much power using this Renogy Wanderer PWM as a Rover Elite MPPT?
VS
I actually ordered the wanderer and figured upon returning the MPPT based on the confidence you instilled in the first thread, especially because there is no room to add more panels ..
By the way, I found that those ports on the panel boxes are called cable glands.
-
Shading on solar panels can drop output from 50% to 100% (yes, 1/2 to zero harvest energy).
A "shaded" solar cell "goes high resistance" (or technically, its current flow goes to whatever the amount of sunlight/skyshine/etc. falls on the cell). Since the cells are in series in solar panels (i.e., 36 cells * 0.5 volt per cell = ~18 volts Vmp)--That means that one cell limits the current from Imp (based on sunlight) to that one shaded cell (1/10th to 1/100th of the current available from the rest of the cells in the series string).
There are different solar panel configuration (36 cells in serie is 18 Volts Vmp; 60 cells in series for 30 volts Vmp, 72 cells for 36 volt Vmp, etc.). And some panels have several strings in parallel (i.e., a 72 cell panel can be 2x strings of 36 cells for Vmp 18 volts at 2x the current per cell/string).
Modern panels all pretty much have "bypass" diodes.. They are in parallel with ~18 to 24 cells or so. If you have two solar panels in series, and one panel has some shade, the bypass diode will let current flow "around" the dark segment.
Solar cells are really just "giant" diodes. And if you put much more than ~12 volts across a shaded (high resistance) "dark" cell, it will ruin the cell (over voltage the reverse biased dark cell/diode). The bypass diodes allow that current to "go around" that dark cell.
The whole question of (for example) for panels in parallel, and one is shaded... That one panel will effectively stop producing Vmp, and its current output will drop to zero. And the other three will perform normally.
If you have the 4 panels in series, and one cell is shaded... Then you will lose (for example if 18 cells per bypass diode), the Vmp of that panel will drop from 18 volts to ~9 volts--And the rest of the string will still produce full current at 9 volts... So that is a 50% reduction of that shaded panel.
But we cannot usually control shade to one cell in a panel (or just allow one column of cells)... Generally the shade falls across both/all strings and that means the whole panel loses output voltage... And you are down to 3 panels producing full voltage and one panel not producing any voltage--So you still have only 3 panels producing energy (assuming the Vmp-array >> the minimum input needed for that MPPT controller + Battery Bank voltage.
In rare conditions, you can make it all work for you.. For example, if you install panels in portrate (sideways) in a snowy environment... The snow collecting on the bottom edge of the panels covers 1/2 the cells in one string---The upper 1/2 of the panel can still be in sun and produce some useful power (again, depending on the rest of the panels series/parallel connections, and the MPPT+Battery bank configurations).
Otherwise, modern mono/poly crystalline panels--There output current is pretty much proportional to the amount of solar energy hitting the cells/panels. In fact, a solar cell/panel driving into a current meter (more or less a dead short) is a pretty accurate solar energy measuring tool.
When solar panels were $10-$30 per Watt--Almost anything you could do to improve harvest was cheaper than adding more panels. With solar panels down in the $1 to $0.50 per Watt range, it is usually cheaper to add 10% more panels than to change from PWM to MPPT charge controller to increase harvest by 10% (mostly in winter--Summer harvest is not "improved" with MPPT over PWM because Vmp-array falls as panel temperature rises in hot weather).
I still am a big fan of MPPT... But this is because they work with "cheap" GT type solar panels (panels that do not "match" PWM to Battery Bank voltage such as Vmp-30 volt and higher panels) and efficiently take the higher voltage/lower current array and down convert to lower voltage and higher current for the battery bank. "Cheap panels" and "expensive MPPT" make for less expensive systems vs "12 volt panels" (more expensive) and "cheap" PWM controllers.
I also like MPPT controllers because they can supply full voltage and current to a battery bank in very hot weather. An 18 volt panel will drop to near 14.4 volts--And you need >15 volts for "full" voltage and current to charge using a PWM controller on a lead acid battery bank to 14.8 or 15.0 volts. If you are in a very hot climate, a PWM controller can be handicapped a bit.
And even if an MPPT controller could produce 2-5% more power vs PWM in low light conditions (i.e., a 100 Watt panel in 10% light would output 10 Watts--5% increase of 10 Watts PWM harvest with an "improved" MPPT harvest would be 10.5 Watts... You would be hard pressed to prove it with standard DMMs and Current Clamp meters (very close to the accuracy limits of the meters and variability of test conditions/temperature/sunlight/battery bank voltage, etc.). I could add a 10 watt panel (10% more array) much easier and probably get more "useful" harvest.
I try to avoid the PWM vs MPPT vs Low Light etc. efficiency arguments. While there are real physical effects and differences--They are typically so small, an otherwise properly designed system--The differences pretty much disappear when compared to overall operation.
These days, I don't even bother with different efficiency numbers between PWM and MPPT controller designs. They are different, but for most folks, it just clouds the other issues (siuch as matching array configuration to controller type to battery bank voltage, proper wire AWG, etc.).
Other issues usually take president... Panel angles (vs trackers vs virtual tracking), getting rid of any shading, choice of batteries and panels, etc. need to resolved to get a reliable/cost effective system.
-BillNear San Francisco California: 3.5kWatt Grid Tied Solar power system+small backup genset -
Feel like I just read something copied and pasted from a prior post because there was nothing concerning a modest 200W system such as what I am going for. Are you arguing I ought keep this MPPT and put the panels in series since the bypass diodes would circumvent any benefit from putting them in parallel?
-
If you have any shade issues, run the panels in parallel, and you may be better off with PWM controller, if your panels are low voltage
No shade, run in series and use a MPPT controller. Check the Min & Max voltages for the controller vs your panels, make sure they are compatible with each other
Mucking about in the J-boxes with new consumer wiring is on your dime, it's a lot harder to keep that water (even condensation can build up) out than you would expect.
Powerfab top of pole PV mount | Listeroid 6/1 w/st5 gen head | XW6048 inverter/chgr | Iota 48V/15A charger | Morningstar 60A MPPT | 48V, 800A NiFe Battery (in series)| 15, Evergreen 205w "12V" PV array on pole | Midnight ePanel | Grundfos 10 SO5-9 with 3 wire Franklin Electric motor (1/2hp 240V 1ph ) on a timer for 3 hr noontime run - Runs off PV ||
|| Midnight Classic 200 | 10, Evergreen 200w in a 160VOC array ||
|| VEC1093 12V Charger | Maha C401 aa/aaa Charger | SureSine | Sunsaver MPPT 15A
solar: http://tinyurl.com/LMR-Solar
gen: http://tinyurl.com/LMR-Lister ,
Categories
- All Categories
- 228 Forum & Website
- 136 Solar Forum News and Announcements
- 1.4K Solar News, Reviews, & Product Announcements
- 199 Solar Information links & sources, event announcements
- 898 Solar Product Reviews & Opinions
- 256 Solar Skeptics, Hype, & Scams Corner
- 22.5K Solar Electric Power, Wind Power & Balance of System
- 3.5K General Solar Power Topics
- 6.7K Solar Beginners Corner
- 1K PV Installers Forum - NEC, Wiring, Installation
- 2.1K Advanced Solar Electric Technical Forum
- 5.6K Off Grid Solar & Battery Systems
- 428 Caravan, Recreational Vehicle, and Marine Power Systems
- 1.1K Grid Tie and Grid Interactive Systems
- 654 Solar Water Pumping
- 816 Wind Power Generation
- 624 Energy Use & Conservation
- 619 Discussion Forums/Café
- 312 In the Weeds--Member's Choice
- 75 Construction
- 124 New Battery Technologies
- 108 Old Battery Tech Discussions
- 3.8K Solar News - Automatic Feed
- 3.8K Solar Energy News RSS Feed