Charger hot spot
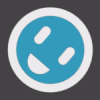
onebad
Registered Users Posts: 12 ✭✭
I have a Renogy 60 amp DC to DC charger wired as instructed into my 200 a/h battery bank. I used #4 welding cable as instructed by Renogy tech support and another solar installer. Everyone seems to agree #4 cable is more than sufficient for this purpose. I know that fuses are best located as close to the power source as possible but their isn’t any space under the hood to put the 90 amp anl fuse that won’t block the starter battery from being removed so it’s located just before the charger behind the driver’s seat. The issue is the cable on the output side of the fuse get hot to the touch (just so you know the fuse is on the positive cable). Fortunately I put a switch in the control line so I’m able to turn off the charger so it’s not only controlled by the ignition. Is the heat an indication that the the cable is just not big enough or is the location of the fuse so far (8 to 10 feet) from the starter battery the possible problem. The fuse has never blown and the connection is secure. As of right now I intend to replace the #4 wire with #2 or maybe #0 welding wire. Another flaw in my system is that when I run the charger and I’m not at highway speed the voltage indicator drops to 9ish volts, I’ve learned to run the engine for a few minutes after turning off the charger to send power into my starter battery or it might not have the power to start my engine the next time I turn the key. Do I need a higher output alternator? Could this be connected to my heat issue? Whew!
Thank you for your attention.
Thank you for your attention.
Comments
-
Heat is an indication of High Resistance. Which with a battery cable, needs to be only half an ohm.
I would suspect the crimp of the lug to the cable being the high resistance. Big cables need big crimpers with 3 foot handles, or a hydraulic 10 ton crimper.
2nd guess would be the terminal itself, not making good connection to the battery post
Powerfab top of pole PV mount | Listeroid 6/1 w/st5 gen head | XW6048 inverter/chgr | Iota 48V/15A charger | Morningstar 60A MPPT | 48V, 800A NiFe Battery (in series)| 15, Evergreen 205w "12V" PV array on pole | Midnight ePanel | Grundfos 10 SO5-9 with 3 wire Franklin Electric motor (1/2hp 240V 1ph ) on a timer for 3 hr noontime run - Runs off PV ||
|| Midnight Classic 200 | 10, Evergreen 200w in a 160VOC array ||
|| VEC1093 12V Charger | Maha C401 aa/aaa Charger | SureSine | Sunsaver MPPT 15A
solar: http://tinyurl.com/LMR-Solar
gen: http://tinyurl.com/LMR-Lister , -
Thank you for your input right after breakfast I’m going to look closer at that connection. I have a 12 ton crimper but the way the connection is set up is to insert the wire and tighten a set screw. Not the best way to make what I think is a fairly high current connection. I don’t know how to work around this issue but my first thought is to consult a local auto stereo installer, they work with anl fuses and high current amp(lifiers). I’ll let you know how it works.
-
One and two fuse compact holders, up to 300 Amp fuse holders for battery terminals and other tight spaces:
https://www.bluesea.com/products/5191/MRBF_Terminal_Fuse_Block_-_30_to_300A (one fuse)
And a two fuse version:
https://www.bluesea.com/products/2151/Dual_MRBF_Terminal_Fuse_Block_-_30_to_300A
Remember that fuses are not included with the basic holder.
Regarding your alternator... The typical (up until you get these new cars with integrated electrical systems, Li Ion or other exotic batteries, etc.)... The charging voltage at the battery should be around 13.8 to 14.4 (around 75F). And ideally around 14.2 to 14.4 volts (typically).
If the alternator is below 13.8 volts, the alternator, brushes, or regulator may need to be replaced (if serviceable), or get a replacement at the auto-parts store (some stores, you can bring the alternator and test it on their machine).
Note: Bad brushes can be intermittent (take to store, and the alternator works). If the alternator has over ~100,000 miles on it and it is having problems, usually time to replace (don't want a bearing failure 10,000 miles later).
You have a switch on the solar charge controller? Is this on the Vbatt side, or on the Vpanel side? In general, you need to connect battery power to Solar chargers first, and disconnect battery power last. If you have solar panels on the charge controller without battery power first, the controller can "boot" in a strange mode--Or even be damaged (they need stable battery power to work correctly).
What size alternator did your vehicle come with... Something like a 60-100 Amp or so? Note that car alternators usually only supply near maximum current when they are cold--As they get hot, their max output current will drop.
Hard starting--If your battery has not seen a minimum ~14.2 volts most of the time when driving, then the alternator is probably bad, and if your battery has been sitting (resting, no load/no charge) at ~12.5 volts or less, the battery (lead acid types) will sulfate and eventually lose capacity (can take weeks or months to happen). You may need to get your battery tested too (auto-parts stores usually have a portable battery tester to check starting current capability).
At this point, I highly suggest you get some sort of DC+AC current clamp dmm (digital mulitmeter). You need to measure the charging and load currents in your system and see what is happening. Note there are AC only current clamp meters and they are very nice--Just not what we need for solar/car electrical system diagnosing. Check the specifications closely--There are AC only clamp meters that also measure AC+DC voltages--Not the same:
https://www.amazon.com/UT210E-Handheld-Digital-Resistance-Capacitance/dp/B06XSMDMYV (cheap, good enough, up to 100 Amp current)
https://www.amazon.com/gp/product/B019CY4FB4 (nicer, up to 400 Amps current)
The whole question of "is your alternator" large enough... Are you using one battery bank (house and engine starting)?
What is the AH rating of the bank (assuming 12 volts)?
What is the vehicle/any information about alternator (some have "heavy duty" alternator options).
Unless you drive a lot, you probably have to rely on your solar charging system for most of your bank charging (enough panels vs your loads vs your battery bank capacity).
Should you isolate your chassis/engine battery from your house battery bank? Can always look for stuff to charge both batteries when on the road.
And as Mike says, a hot spot is generally a connection issue (not crimped correctly, dirty/corroded terminal, etc.). If the cable was too small, the whole cable length would be warm and/or you would have too much voltage d(lrop:
4 AWG @ 60 amps @ 10 feet:
https://www.calculator.net/voltage-drop-calculator.html?material=copper&wiresize=0.8152&voltage=12&phase=dc&noofconductor=1&distance=10&distanceunit=feet&eres=60&x=62&y=22
Voltage drop: 0.30
Voltage drop percentage: 2.48%
Voltage at the end: 11.7
That is not great--I would be suggesting around 0.05 to 0.10 volts max drop (12 volt system) from charge controller to battery bank.... If you are anywhere near 60 amps, that is a loss of 0.3 volts (14.4 at controller, and 14.1 at battery bus). That will slow down battery charging quite a bit, and extend absorb time a lot too (as current falls, drop falls, battery continues to charge). You don't have many hours of sun per day to "waste" time with slow charging.
Is there anyway you can move the charger much closer to the battery? Ideally, you want 1/3rd the distance or 3x heavier wire (like 2/0 for 10 feet will be 0.094 volt drop--And that is towards getting "crazy" heavy cable for this application).
Are you running both + and - cable from controller to battery bank, or are using just + cable and chassis ground (+/- pair of cables is much better).
-BillNear San Francisco California: 3.5kWatt Grid Tied Solar power system+small backup genset -
Thanks Bill. The switch I referred to is the control (on/off) switch for the DC to DC battery charger. It only carries 12 volts to tell the charger to turn on when the ignition is on. I put it in place so that I could control when/if the DC to DC charger is on. I do have a kill switch between the solar panels and the charge controller but that’s fine.My 1994 van has 96k miles on it and aside from when the DC to DC charger is on while I’m low speed city driving it operates normally. I was just wondering if/why the charger which is asking for enough power to send 60 amps/hour to my battery bank was starving my starter battery. I will ask my mechanic if it’s operating properly before I make further plans for it.
As I said I would I found a car audio installer to consult, Brian at Cartronics. He thinks the heat problem is the welding cable itself. He said he’s seen many guys trick out their car with hydraulics only to see the welding cable they used cause a heat problem and cause damage to their pumps. He says welding cable isn’t designed to carry a constant load. I think I trust his judgment. As we walked to my van past the Ferrari in his parking lot I pointed at it and said “sweet“, he said “You should see my other one“. He Installs audio and alarm systems in high end cars and in boats. Since the hi seas are even more demanding than highways I’m going to trust his 38 years of experience and switch out the #4 welding cable between the battery and the fuse, and the fuse to the charger. He sold me the same kind of power cable he’s going to use on that Ferrari he’s giving to his daughter, it’s called OFC power cable. He also sold me a fuse holder that uses a ring terminal connection rather than the set screw type I have on there now. I’ll let you know how it works. Again, thank you for your response. -
Regarding using a DC to DC converter from Van alternator/battery to house battery charging. It is certainly possible that if you are pulling 60 Amps (by the way Amperes is Joules per Second--So Amp/Hour is not the correct term--Amps is already a "rate") from the chassis electrical system, it is certainly possible that you are drawing more current (if a constant 60 Amp draw) than the alternator is able to supply (again as alternators get hot, their output current usually falls). Monitoring your chassis battery voltage would be a quick way to verify if your DC to DC converter is exceeding the alternator's output (you need to see >~13.8 Volts on the chassis battery when the motor is running at anything above idle). If you are seeing less than that, the chassis battery is not being properly charged. If you see less than ~12.8 volts, the chassis battery is actually being discharged. SLI batteries (starting, lights, ignition) do not like to be cycled much more than 15% discharge (below ~85% state of charge)--SLI batteries will have a much shorter life if deeply discharged.
When looking for "OFC Power Cable"--Make sure that it is not Copper Clad Aluminium cable, but pure copper (prefered). Aluminium has more internal resistance, and some other issues (used in house wiring) with long term reliable connections.
Using a binding screw on fine strand welding cable (that does not have a thimble crimped on the cable first, or other "help")--The fine strands tend to "squirm" out from other a "simple" binding screw and make for poor longer term connections (vs course stranded or solid cables).
-Bill
Near San Francisco California: 3.5kWatt Grid Tied Solar power system+small backup genset -
I agree with the connection terminal issue if only heating on output side of fuse.
If your vehicle battery is droping to 9'ish volts that is bad. You will destroy the vehicle battery. I am not familar with the DC-DC converter but it sounds like a buck-boost converter. That means it will charge the battery regardless of condition of source battery to the point it trips charger's low input voltage from source battery. It should not be sucking your vehicle battery down to 9-10 volts. If there is a setting on the charger for low input voltage cutout set it to something like 12vdc to prevent from killing your vehicle battery.
Single #4 welding wire 30' long at 50 amps will have 0.4 volt drop. You have to add negative return to that however you are accomplishing that. I would not rely solely on chassis for negative return. Often there is a large negative cable from battery to engine block for starter but small gauge wire from negative on battery to chassis.
An alternator will only put out what it is capable of but it will get hot if run at maximum amperage for long time, especially without sufficent air flow from driving on the highway. They also do not put out anything near rated output at 700-800 rpm of engine idle. There are alternators (used in police cars) that produce more output at low rpm. You can buy a cheap voltmeter to plug into a cigarette lighter to monitor vehicle voltage to keep tabs on vehicle. An alternator should keep vehicle voltage to 13.2v to 13.5v normally when vehicle battery is charged. If you are dropping below 12.5v while charging RV battery then you are pulling too much power.
I would consider getting a higher amperage alternator but check to make sure your belts and pulley can handle the extra mechanical load. You should also get a 120vac charger to use when AC power is available so not to rely solely on vehicle charging. Running your vehicle just to charge your RV battery is very inefficient use of gas. A little 2kW quiet inverter generator would be much better then using your vehicle. Don't forget about carbon monoxide from your vehicle or generator. At least the generator can be moved away on a long extension cord.
-
Thanks again Bill. I’ve been touch with a performance auto supplier about a higher output alternator but he wasn’t sure if/when he could get it (not that can afford it right now). I know there are “smart“ chargers that will only charge your leisure batteries after your starter battery has been sufficiently charged and they will use power from your leisure batteries to start your engine if your starter battery is low on power. That could be in my future.RC, I’ve never heard the term buck-boost but I think you’re right, this charger doesn’t care what the state of your starter battery is it charges your leisure battery regardless. If I were choosing a battery charger now I would get a smart one. Unfortunately this charger does not have any adjustments aside from adjusting for the type of battery (AGM, lithium etc.) I do have a cable that goes back to the negative post of my starter battery. My inverter is not also a charger so I have no way to plug-in to AC. These are all things to consider when I get back to work. As for carbon monoxide I have two detectors. Thank you all for your time and helping educate me on a subject I am out of my depth on.
Categories
- All Categories
- 229 Forum & Website
- 137 Solar Forum News and Announcements
- 1.4K Solar News, Reviews, & Product Announcements
- 199 Solar Information links & sources, event announcements
- 898 Solar Product Reviews & Opinions
- 256 Solar Skeptics, Hype, & Scams Corner
- 22.5K Solar Electric Power, Wind Power & Balance of System
- 3.5K General Solar Power Topics
- 6.7K Solar Beginners Corner
- 1K PV Installers Forum - NEC, Wiring, Installation
- 2.1K Advanced Solar Electric Technical Forum
- 5.6K Off Grid Solar & Battery Systems
- 428 Caravan, Recreational Vehicle, and Marine Power Systems
- 1.1K Grid Tie and Grid Interactive Systems
- 654 Solar Water Pumping
- 816 Wind Power Generation
- 624 Energy Use & Conservation
- 619 Discussion Forums/Café
- 312 In the Weeds--Member's Choice
- 75 Construction
- 124 New Battery Technologies
- 108 Old Battery Tech Discussions
- 3.8K Solar News - Automatic Feed
- 3.8K Solar Energy News RSS Feed