Battery charging
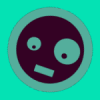
GANNY
Registered Users Posts: 7 ✭✭
I have a 48v wind turbine system At what stage does the wind turbine start to charge my 48v battery bank? My windmill does not deliver 48v all the time. Does the battery get any charge when the turbine is producing less than 48v.
I thank you in advance for your answer
I thank you in advance for your answer
Tagged:
Comments
-
You need to check the specifications, but generally a wind turbine needs something like 10-12 MPH wind to start producing any appreciable amount of power. And most produce their maximum output around 25-30 MPH. And to get good non-turbulent airflow, the turbine is usually at least 30 feet high, and above any surrounding trees/buildings/etc. A turbine will not produce much energy if there is turbulent airflow. For a turbine to produce energy, it is usually mounted high (30-90 feet) in a "miserably windy" area (trees flagging from prevailing winds).
And the output voltage of the turbine/rectifier/charge controller needs to be above the battery voltage to begin charging. A typical fully charged battery is around 12.8 volts / 51.2 volts (12/48 volt battery bank) resting, 13.6 / 54.4 Volts for "float voltage", and 14.75 / 59.0 volts for full charging current (flooded cell lead acid type batteries).
-BillNear San Francisco California: 3.5kWatt Grid Tied Solar power system+small backup genset -
The turbine needs to exceed the voltage of the battery to allow current to flow, so in short the answer is no. Wind generation is on the surface seems very simple, unfortunately it also requires specific criteria in order to function, wind speed, unobstructed flow and so forth, which very few areas actually have, unless the local trees and shrubs grow horizontally due to prevailing winds it's unlikely that wind would provide any meaningful production.
1500W, 6× Schutten 250W Poly panels , Schneider MPPT 60 150 CC, Schneider SW 2524 inverter, 400Ah LFP 24V nominal battery with Battery Bodyguard BMS
Second system 1890W 3 × 300W No name brand poly, 3×330 Sunsolar Poly panels, Morningstar TS 60 PWM controller, no name 2000W inverter 400Ah LFP 24V nominal battery with Daly BMS, used for water pumping and day time air conditioning.
5Kw Yanmar clone single cylinder air cooled diesel generator for rare emergency charging and welding. -
You could connect a DC-DC converter to it so that it would apply some charge even when output is below the battery voltage.
I am available for custom hardware/firmware development
-
Thanks for your experience What is the PROS and CONS of introduction of step up gear to increase the rpm of the rotor?
-
GANNY said:Thanks for your experience What is the PROS and CONS of introduction of step up gear to increase the rpm of the rotor?
Increasing the rotor RPM via gearing will result in lower torque, this along with the gear train losses would result in less potential energy.1500W, 6× Schutten 250W Poly panels , Schneider MPPT 60 150 CC, Schneider SW 2524 inverter, 400Ah LFP 24V nominal battery with Battery Bodyguard BMS
Second system 1890W 3 × 300W No name brand poly, 3×330 Sunsolar Poly panels, Morningstar TS 60 PWM controller, no name 2000W inverter 400Ah LFP 24V nominal battery with Daly BMS, used for water pumping and day time air conditioning.
5Kw Yanmar clone single cylinder air cooled diesel generator for rare emergency charging and welding. -
Thanks once more. I appreciate the resultant lower torque but can this be upset if I increase the diameter of the blades to 18' . I have been using 10' diameter blades
-
jonr said:You could connect a DC-DC converter to it so that it would apply some charge even when output is below the battery voltage.
-
Thank you JONR . You made my day. That is GREAT.
-
Changing blades and diameter--You need to make sure they match the turbine requirements. Too large of diameter, tip speed limits (optimum) RPM. Too large of blades, can exceed braking torque capabilities of alternator (instead of shutting down in high winds, will over drive alternator and overheat, possibly self destruct from high RPM.
A boost converter.... Yes it can bring low voltage output up from the turbine, but pulling current from the turbine, will add torque and slow down the RPMs even more... How much power you can harvest from this--Don't know. But don't expect very much additional harvest.
-BillNear San Francisco California: 3.5kWatt Grid Tied Solar power system+small backup genset -
I had used N35 magnet now I intend to use N42 magnet My thinking is that increasing the magnet strength will increase the turbine output
Any thought about this will be of tremendous help to me -
Stronger magnets should increase the voltage given the same rpm so the turbine should in theory start charging in lower wind speeds. I have no way of knowing how much of a change there would be.
Hope this helps. -
> N35 magnet now I intend to use N42
Should be about a 10% increase in voltage and the same power.I am available for custom hardware/firmware development
Categories
- All Categories
- 228 Forum & Website
- 136 Solar Forum News and Announcements
- 1.4K Solar News, Reviews, & Product Announcements
- 199 Solar Information links & sources, event announcements
- 898 Solar Product Reviews & Opinions
- 256 Solar Skeptics, Hype, & Scams Corner
- 22.5K Solar Electric Power, Wind Power & Balance of System
- 3.5K General Solar Power Topics
- 6.7K Solar Beginners Corner
- 1K PV Installers Forum - NEC, Wiring, Installation
- 2.1K Advanced Solar Electric Technical Forum
- 5.6K Off Grid Solar & Battery Systems
- 428 Caravan, Recreational Vehicle, and Marine Power Systems
- 1.1K Grid Tie and Grid Interactive Systems
- 654 Solar Water Pumping
- 816 Wind Power Generation
- 624 Energy Use & Conservation
- 619 Discussion Forums/Café
- 312 In the Weeds--Member's Choice
- 75 Construction
- 124 New Battery Technologies
- 108 Old Battery Tech Discussions
- 3.8K Solar News - Automatic Feed
- 3.8K Solar Energy News RSS Feed