2 AWG from combiner box?
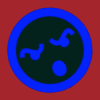
streetsofarklow
Registered Users Posts: 3 ✭
I've encountered a logistical issue with my build and I'm hoping for some help. I'm choosing to run 6x100 watt panels in parallel on my camper (12v system). Yes, I know it's less efficient, but it's what I'm going with for shading reasons. Here's my problem: the math tells me I should be going with 2 AWG from my combiner box into my charge controller (MPPT). Each panel's ISC is 6.24A, which will yield a combined 37.4A. Taking irradiance and continuous use into account (x1.25 for each per NEC guidelines), we now have 58.4A. Next is temperature correction. I figure the hottest ambient temp I'll encounter is 115-120F. When adding another 40F due to roof proximity (per NEC), we're left needing a wire gauge that can handle 100.7A (58.4/.58). But wait, there's more! With 6 conductors in the circuit (after branch-connecting two sets of three panels), NEC tells us to divide by an additional 0.8, which puts us at 125.8A. Using 90C copper wire, this means according to the NEC I'll need 2 AWG running out of my combiner box. Now, this is what the code says, but do I really need to do it this way? The run from my combiner box to my charge controller is under 10 feet, so it's doable, but then I'm left with another problem: the largest gauge the charge controller accepts is AWG 6. Can't I just throw a 50A breaker on 6 AWG and call it good? Or does worst-case temperature scenario mean the wire could really melt, independent of my amperage?
Bonus question: Is it okay to use the branch connectors to parallel three panels with 10 AWG (heaviest gauge that fits the Renogy branch connectors)? The math says I'd need AWG 8 to correct for up to 50A, but Renogy says "IP 65 Protection" rates their wire up to 185F, so I think I'm probably fine.
Thanks for any help you guys can provide. I'm new to this, and am probably being too cautious. I've searched for hours online, but haven't found similar examples.
Bonus question: Is it okay to use the branch connectors to parallel three panels with 10 AWG (heaviest gauge that fits the Renogy branch connectors)? The math says I'd need AWG 8 to correct for up to 50A, but Renogy says "IP 65 Protection" rates their wire up to 185F, so I think I'm probably fine.
Thanks for any help you guys can provide. I'm new to this, and am probably being too cautious. I've searched for hours online, but haven't found similar examples.
Tagged:
Comments
-
streetsofarklow said:I've encountered a logistical issue with my build and I'm hoping for some help. I'm choosing to run 6x100 watt panels in parallel on my camper (12v system). Yes, I know it's less efficient, but it's what I'm going with for shading reasons. Here's my problem: the math tells me I should be going with 2 AWG from my combiner box into my charge controller (MPPT). Each panel's ISC is 6.24A, which will yield a combined 37.4A. Taking irradiance and continuous use into account (x1.25 for each per NEC guidelines), we now have 58.4A. Next is temperature correction. I figure the hottest ambient temp I'll encounter is 115-120F. When adding another 40F due to roof proximity (per NEC), we're left needing a wire gauge that can handle 100.7A (58.4/.58). But wait, there's more! With 6 conductors in the circuit (after branch-connecting two sets of three panels), NEC tells us to divide by an additional 0.8, which puts us at 125.8A. Using 90C copper wire, this means according to the NEC I'll need 2 AWG running out of my combiner box. Now, this is what the code says, but do I really need to do it this way? The run from my combiner box to my charge controller is under 10 feet, so it's doable, but then I'm left with another problem: the largest gauge the charge controller accepts is AWG 6. Can't I just throw a 50A breaker on 6 AWG and call it good? Or does worst-case temperature scenario mean the wire could really melt, independent of my amperage?
Bonus question: Is it okay to use the branch connectors to parallel three panels with 10 AWG (heaviest gauge that fits the Renogy branch connectors)? The math says I'd need AWG 8 to correct for up to 50A, but Renogy says "IP 65 Protection" rates their wire up to 185F, so I think I'm probably fine.
Thanks for any help you guys can provide. I'm new to this, and am probably being too cautious. I've searched for hours online, but haven't found similar examples.
Your panels are going to produce less than rated - not more. Real world.First Bank:16 180 watt Grape Solar with FM80 controller and 3648 Inverter....Fullriver 8D AGM solar batteries. Second Bank/MacGyver Special: 10 165(?) watt BP Solar with Renogy MPPT 40A controller/ and Xantrex C-35 PWM controller/ and Morningstar PWM controller...Cotek 24V PSW inverter....forklift and diesel locomotive batteries -
Assuming 80% PV efficiency (in general) and a very low battery of ~11 volts, the most you are likely to see is ~45 amps...on a very good day. #6 should be fine, even # 8 should work. Breaker or fuse it for 50 amps and you should be fine. I run 600 watts of parallel 12 volt panels into a 30 amp controller and very seldom...if ever does it clip. I home runner (from two different array locations, one on the roof, one on the wall, #6 and breakered it at 40 amps. Never had a problem. You do want to fuse your parallel PV however. MC 4 inline fuses are the ticket, probably with a ISC of under 7 I would fuse it with 10 amp fuses.
Tony -
Awesome, thanks guys. I was considering trimming, crimping a Ferrule or just using split bolts. But yeah 6 gauge should be fine, I was mostly worried about worst-case desert scenarios. I just don't have enough experience to know what's an abundance of safety and what's a true fire hazard.
-
streetsofarklow said:I've encountered a logistical issue with my build and I'm hoping for some help. I'm choosing to run 6x100 watt panels in parallel on my camper (12v system). Yes, I know it's less efficient, but it's what I'm going with for shading reasons. Here's my problem: the math tells me I should be going with 2 AWG from my combiner box into my charge controller (MPPT). Each panel's ISC is 6.24A, which will yield a combined 37.4A. Taking irradiance and continuous use into account (x1.25 for each per NEC guidelines), we now have 58.4A. Next is temperature correction. I figure the hottest ambient temp I'll encounter is 115-120F. When adding another 40F due to roof proximity (per NEC), we're left needing a wire gauge that can handle 100.7A (58.4/.58). But wait, there's more! With 6 conductors in the circuit (after branch-connecting two sets of three panels), NEC tells us to divide by an additional 0.8, which puts us at 125.8A. Using 90C copper wire, this means according to the NEC I'll need 2 AWG running out of my combiner box. Now, this is what the code says, but do I really need to do it this way? The run from my combiner box to my charge controller is under 10 feet, so it's doable, but then I'm left with another problem: the largest gauge the charge controller accepts is AWG 6. Can't I just throw a 50A breaker on 6 AWG and call it good? Or does worst-case temperature scenario mean the wire could really melt, independent of my amperage?
Bonus question: Is it okay to use the branch connectors to parallel three panels with 10 AWG (heaviest gauge that fits the Renogy branch connectors)? The math says I'd need AWG 8 to correct for up to 50A, but Renogy says "IP 65 Protection" rates their wire up to 185F, so I think I'm probably fine.
Thanks for any help you guys can provide. I'm new to this, and am probably being too cautious. I've searched for hours online, but haven't found similar examples.
Being you will be using an MPPT controller, with the 100W panels it would be better to series wire at least two so as to have the voltage high enough for the MPPT to actually work, otherwise it will act much like a PWM controller. As voltage is inversely proportional to current the current will be reduced meaning smaller conductors could be utilized. Understandably shading issues may prevent this.
Use NEC rules as a guide, code rules are subject to many clauses, exceptions and not withstanding clauses, leading to confusion. They are also intended for building applications not vehicular, as such trying to follow them to the letter often seems impossible. Just my opinion.1500W, 6× Schutten 250W Poly panels , Schneider MPPT 60 150 CC, Schneider SW 2524 inverter, 400Ah LFP 24V nominal battery with Battery Bodyguard BMS
Second system 1890W 3 × 300W No name brand poly, 3×330 Sunsolar Poly panels, Morningstar TS 60 PWM controller, no name 2000W inverter 400Ah LFP 24V nominal battery with Daly BMS, used for water pumping and day time air conditioning.
5Kw Yanmar clone single cylinder air cooled diesel generator for rare emergency charging and welding. -
Run your scenario through this simple calculator: https://pvwatts.nrel.gov
I have so many projects going on that I missed that your panels will likely be flat. They almost have to be on a mobile camper.First Bank:16 180 watt Grape Solar with FM80 controller and 3648 Inverter....Fullriver 8D AGM solar batteries. Second Bank/MacGyver Special: 10 165(?) watt BP Solar with Renogy MPPT 40A controller/ and Xantrex C-35 PWM controller/ and Morningstar PWM controller...Cotek 24V PSW inverter....forklift and diesel locomotive batteries -
Okay, so it looks like I'll be alright with a lower gauge. I knew the amp draw would be significantly lower, but was just trying to do the proper math and be cautious, as I'm not an electrician. Thanks for the advice
Categories
- All Categories
- 228 Forum & Website
- 136 Solar Forum News and Announcements
- 1.4K Solar News, Reviews, & Product Announcements
- 199 Solar Information links & sources, event announcements
- 898 Solar Product Reviews & Opinions
- 256 Solar Skeptics, Hype, & Scams Corner
- 22.5K Solar Electric Power, Wind Power & Balance of System
- 3.5K General Solar Power Topics
- 6.7K Solar Beginners Corner
- 1K PV Installers Forum - NEC, Wiring, Installation
- 2.1K Advanced Solar Electric Technical Forum
- 5.6K Off Grid Solar & Battery Systems
- 428 Caravan, Recreational Vehicle, and Marine Power Systems
- 1.1K Grid Tie and Grid Interactive Systems
- 654 Solar Water Pumping
- 816 Wind Power Generation
- 624 Energy Use & Conservation
- 619 Discussion Forums/Café
- 312 In the Weeds--Member's Choice
- 75 Construction
- 124 New Battery Technologies
- 108 Old Battery Tech Discussions
- 3.8K Solar News - Automatic Feed
- 3.8K Solar Energy News RSS Feed