Convert dc to ac without transforming the voltage
Options
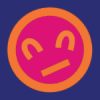
thierry
Registered Users Posts: 20 ✭✭
1. I have 8 solar panels. 23 - 29 v output. 7,5 max amp, 175 W max output ...
2. I have an electric waterpump with an expansion barrel pumping up ground water ... The pump is installed below the expansion barrel below the ground surface so i cannot see it. But from experience i know it must be between 1000 and 1500 watt.
3. I have a large capacity of reservoirs to collect rainwater for gardening.
4. I only use the waterpump during the summer when we have exceptional drougth to fill up the reservoirs once in a while. Happens maybe 5 times a year. Maximum 10 times and i only need to pump a few hours max to fill all my reservoirs.
5. I do not like noisy generators.
6. So here is my reasoning ...
If i connect the solarpanels in series i have a voltage between 184 (8 × 23) and 232 (8 × 29) volt.
I think on 184 volts the pump will run slower but i do not care because time is not my enemy but much rather my friend.
The max output will not damage my pump.
The problem however is DC output from the solarpanels and the pump ofcourse needs AC. So i guess i only need to convert from dc to ac. No need to transform to another voltage.
I can find all kinds of converters and transformers combined on the internet but non of them who don t change the voltage.
I have two questions ...
1. Your opinion about my reasoning ... does it make sense or do i see it the wrong way ? I barely know something about electricity indeed.
2. If it makes sense i reckon it would not be that hard to make my own converter fit for what i want to do. How could i accomplish this ?
Comments
-
What you ask for is not "that hard" to do (solar panels => AC inverter => AC loads)...But, in general, most AC loads do not like brownouts and/or stopping&starting during the day.A frequent answer is to use a VFD (Variable Frequency Drive)... These can be programmed/made to take energy from a solar array and provide 3 phase variable frequency (and voltage) to a pump motor.. I.e., when first starting low frequency to drive motor to get it spinning, then increase frequency to 100% RPM... And as clouds go overhead, or the sun starts to go down in the West, the VFD will reduce pump speed (keep pumping at a lower rate, so more total water is pumped in a day). However, generally these are designed for 3 phase motors.There are also DC pumps which can be connected directly to solar, or through a Linear Current Booster... A DC motor needs lots of current, but not that much voltage to begin turning--Which an LCB provides--Then as sun rises, the LCB limits voltage the DC pump at 12 or 24 volts. LCBs tend to be expensive, brushed DC motor/pumps tend to be cheap--But brushed motors have a limited life (brushes/commutator). There are electrically commutated DC motors--But may not be cheap either (basically a VFD/Inverter internal to the motor, or through an external motor controller).You can also directly connect a DC pump to a solar array--But this may have issues (solar panels are not anywhere near an "ideal battery").You are now in a hole... There is lots of neat stuff out there, but most would require you to either do a full battery+AC inverter support for your present AC pump--Or instead buy new hardware, or design your own solar input AC inverter--Can be done, but not an "easy" project).A 12 volt or 24 volt RV water pump would probably be a good solution plus a pair of 6 volt @ 200 AH golf cart batteries...Or if you have 120 VAC within a few hundred feet, run a direct burial cable from the AC source to the pump...And perhaps one of our members has found a batteryless solar panel=>AC pump solution (there are GT Inverters that output q120 VAC during sunny weather if the utility power failures--But they are not a cheap solution for your pumping requirements.-BillNear San Francisco California: 3.5kWatt Grid Tied Solar power system+small backup genset
-
BB. said:What you ask for is not "that hard" to do (solar panels => AC inverter => AC loads)...But, in general, most AC loads do not like brownouts and/or stopping&starting during the day.A frequent answer is to use a VFD (Variable Frequency Drive)... These can be programmed/made to take energy from a solar array and provide 3 phase variable frequency (and voltage) to a pump motor.. I.e., when first starting low frequency to drive motor to get it spinning, then increase frequency to 100% RPM... And as clouds go overhead, or the sun starts to go down in the West, the VFD will reduce pump speed (keep pumping at a lower rate, so more total water is pumped in a day). However, generally these are designed for 3 phase motors.There are also DC pumps which can be connected directly to solar, or through a Linear Current Booster... A DC motor needs lots of current, but not that much voltage to begin turning--Which an LCB provides--Then as sun rises, the LCB limits voltage the DC pump at 12 or 24 volts. LCBs tend to be expensive, brushed DC motor/pumps tend to be cheap--But brushed motors have a limited life (brushes/commutator). There are electrically commutated DC motors--But may not be cheap either (basically a VFD/Inverter internal to the motor, or through an external motor controller).You can also directly connect a DC pump to a solar array--But this may have issues (solar panels are not anywhere near an "ideal battery").You are now in a hole... There is lots of neat stuff out there, but most would require you to either do a full battery+AC inverter support for your present AC pump--Or instead buy new hardware, or design your own solar input AC inverter--Can be done, but not an "easy" project).A 12 volt or 24 volt RV water pump would probably be a good solution plus a pair of 6 volt @ 200 AH golf cart batteries...Or if you have 120 VAC within a few hundred feet, run a direct burial cable from the AC source to the pump...And perhaps one of our members has found a batteryless solar panel=>AC pump solution (there are GT Inverters that output q120 VAC during sunny weather if the utility power failures--But they are not a cheap solution for your pumping requirements.-Bill
-
Sounds like Grundfos or similar DC pump with integrated VFD/Pump controller.
Yes, you could just simple series parallel solar panels to achieve (say 2,000 Watt array) with Vmp~220 VDC...
Some guesses:- 220 Volts / 30 Volt Vmp (typical) less expensive GT panels = 7.33 panels, round up to 8 in series
- 2,000 Watts * 1/0.81 typical "hot panel" power derating = 2,469 Watt array
- 2,469 Watt array / 8 panels in series = 309 Watt panels (8x309 Watt panels in series)
- 309 Watt panel / 30 Volts Vmp = 10.3 Amps
https://www.solar-electric.com/silfab-sla-m-310-solar-panel.html (example panel with "close enough" specs).
It would be great to get the name plate rating/brand/model of motor to figure out its exact power requirements (again solar panels are very "poor" batteries and have very wide operating specifications.
Also, if you use an On/Off Switch, make sure it is rated for >220 VDC and >10 ADC ... AC switches on high voltage DC circuits can arc/fail.
-Bill
Near San Francisco California: 3.5kWatt Grid Tied Solar power system+small backup genset -
BB. said:Sounds like Grundfos or similar DC pump with integrated VFD/Pump controller.
Yes, you could just simple series parallel solar panels to achieve (say 2,000 Watt array) with Vmp~220 VDC...
Some guesses:- 220 Volts / 30 Volt Vmp (typical) less expensive GT panels = 7.33 panels, round up to 8 in series
- 2,000 Watts * 1/0.81 typical "hot panel" power derating = 2,469 Watt array
- 2,469 Watt array / 8 panels in series = 309 Watt panels (8x309 Watt panels in series)
- 309 Watt panel / 30 Volts Vmp = 10.3 Amps
https://www.solar-electric.com/silfab-sla-m-310-solar-panel.html (example panel with "close enough" specs).
It would be great to get the name plate rating/brand/model of motor to figure out its exact power requirements (again solar panels are very "poor" batteries and have very wide operating specifications.
Also, if you use an On/Off Switch, make sure it is rated for >220 VDC and >10 ADC ... AC switches on high voltage DC circuits can arc/fail.
-Bill
-
thierry said:1. Your opinion about my reasoning ... does it make sense or do i see it the wrong way ? I barely know something about electricity indeed.2. If it makes sense i reckon it would not be that hard to make my own converter fit for what i want to do. How could i accomplish this ?
-
bill von novak said:I think you will be _way_ better off with a DC pump and a pump controller like an LCB. Then you are using the pump the way it's designed to be used.You speak as if i can just simply replace the pump. The pump is builth into the ground and the weekendhouse is on top of that. Installing it cost the former owner several thousands of euros. And i am using the pump the way it is designed to be. It is a 220V AC pump and i power it with a 5kw generator. Would be nice however if i could replace that generator by the solar panels as a power source. Why ? No noise ... no fuel ... good for the environment ... good for my pocket ... good for nature surrounding my land.
-
thierry said:bill von novak said:I think you will be _way_ better off with a DC pump and a pump controller like an LCB. Then you are using the pump the way it's designed to be used.You speak as if i can just simply replace the pump. The pump is builth into the ground and the weekendhouse is on top of that. Installing it cost the former owner several thousands of euros. And i am using the pump the way it is designed to be. It is a 220V AC pump and i power it with a 5kw generator. Would be nice however if i could replace that generator by the solar panels as a power source. Why ? No noise ... no fuel ... good for the environment ... good for my pocket ... good for nature surrounding my land.
This particular one is 3 phase, single phase are probably available, this would allow series panels up to 390 VDC, no batteries required.1500W, 6× Schutten 250W Poly panels , Schneider MPPT 60 150 CC, Schneider SW 2524 inverter, 400Ah LFP 24V nominal battery with Battery Bodyguard BMS
Second system 1890W 3 × 300W No name brand poly, 3×330 Sunsolar Poly panels, Morningstar TS 60 PWM controller, no name 2000W inverter 400Ah LFP 24V nominal battery with Daly BMS, used for water pumping and day time air conditioning.
5Kw Yanmar clone single cylinder air cooled diesel generator for rare emergency charging and welding. -
Driving a motor with variable speed is a piece of cake with 3 phase. Not so with single phase. I doubt one exists. Just watched a video of some Colorado company with one, they wanted $4,000. Buy two or three at a minimum if getting one from China. You will never get it fixed.
-
Here is a single phase one http://www.kewoinverter.com/1phaseinverter.html that accepts solar input, I must agree 3 phase is more common and simpler, Hitachi also has some single phase inverter controllers with MPPT input controller. Single phase may be single speed.1500W, 6× Schutten 250W Poly panels , Schneider MPPT 60 150 CC, Schneider SW 2524 inverter, 400Ah LFP 24V nominal battery with Battery Bodyguard BMS
Second system 1890W 3 × 300W No name brand poly, 3×330 Sunsolar Poly panels, Morningstar TS 60 PWM controller, no name 2000W inverter 400Ah LFP 24V nominal battery with Daly BMS, used for water pumping and day time air conditioning.
5Kw Yanmar clone single cylinder air cooled diesel generator for rare emergency charging and welding. -
thierry said:If i connect the solarpanels in series i have a voltage between 184 (8 × 23) and 232 (8 × 29) volt.I think on 184 volts the pump will run slower but i do not care because time is not my enemy but much rather my friend.The max output will not damage my pump.
-
I don't think anyone would be happy with that single phase unless the array was way oversized. Single phase motors are terrible at very low speeds. I think there is a lot of fine print. Three phase you can slow to a creep. I've run 2 HP 480V three phase motors on a 220V 0.1KW
-
Mike_s,
The conversion ratio of RMS voltage to peak to peak is: RMS times 1.414 is peak to peak, therefore 200 volts RMS is 282.2 volts peak to peak.......and conversely conversion of peak to peak to RMS is peak to peak times .707 so 200 volts peak to peak is 141.4 volts RMS2 Classic 150, 2 Kid, 5 arrays 7.5 kw total 2ea. 2S6P Sharp NE-170/NE-165, 1ea. 12P Sanyo HIT 200, 2ea. 4/6P Sanyo HIT 200, MagnaSine MS4024AE, Exeltech XP-1100, 2 Banks L-16 battery, Rolls-Surette S-530 and Interstate Traction, Shunts with whizbangJr and Bogart Tri-Metric, iCharger i208B dc-dc buck/boost converter with BMS for small form lithium 8S 16650 or LiFePO4, -
Well, that sounds extraordinarily foolish! All motors eventually fail. Maybe not next year, maybe not in 2025, but 10-15 years down the road, and you eventually WILL have to face pump replacement. Having a pump at 125 meters down fail myself was an expensive learning experience! In my own case, having constructed a room over the well-head, I constructed a "hatch" where the steel roofing could just be unbolted to allow a crane to pull out the pump. You can create a 230VAC system that will power your pump. I did. It will not however be good for your pocket. It does however allow me to completely silently pump water from 8am till 4pm.You speak as if i can just simply replace the pump. The pump is builth into the ground and the weekendhouse is on top of that. Installing it cost the former owner several thousands of euros. And i am using the pump the way it is designed to be. It is a 220V AC pump and i power it with a 5kw generator. Would be nice however if i could replace that generator by the solar panels as a power source. Why ? No noise ... no fuel ... good for the environment ... good for my pocket ... good for nature surrounding my land.
System 1) 15 Renogy 300w + 4 250W Astronergy panels, Midnight 200 CC, 8 Trojan L16 bat., Schneider XW6848 NA inverter, AC-Delco 6000w gen.System 2) 8 YingLi 250W panels, Midnight 200CC, three 8V Rolls batteries, Schneider Conext 4024 inverter (workshop) -
I just remembered talking to a guy that convinced a company to replace all of its motor controls wit VFD to save energy. Six months later they started having about two motors a month fail. These drives start creating standing waves at the transitions over 100 feet. These old motors did not have the insulation to deal with 2KV spikes continuously. You will find some motors mention inverter ready. Three phase line filters are especially recommended for long runs with submerged pumpa.
-
Tecnodave said:Mike_s,
The conversion ratio of RMS voltage to peak to peak is: RMS times 1.414 is peak to peak, therefore 200 volts RMS is 282.2 volts peak to peak.......and conversely conversion of peak to peak to RMS is peak to peak times .707 so 200 volts peak to peak is 141.4 volts RMS
-
I'm no kind of expert on AC, but is (+) peak to (-) peak (or trough) voltage relevant to much of anything?
I get that curve shape, timing, and capacitance/inductance matters. Just not sure how RMS peak x 2 matters.Off-grid.
Main system ~4kw panels into 2xMNClassic150 370ah 48v bank 2xOutback 3548 inverter 120v + 240v autotransformer
Night system ~1kw panels into 1xMNClassic150 700ah 12v bank morningstar 300w inverter -
Estragon said:I'm no kind of expert on AC, but is (+) peak to (-) peak (or trough) voltage relevant to much of anything?
I get that curve shape, timing, and capacitance/inductance matters. Just not sure how RMS peak x 2 matters.1500W, 6× Schutten 250W Poly panels , Schneider MPPT 60 150 CC, Schneider SW 2524 inverter, 400Ah LFP 24V nominal battery with Battery Bodyguard BMS
Second system 1890W 3 × 300W No name brand poly, 3×330 Sunsolar Poly panels, Morningstar TS 60 PWM controller, no name 2000W inverter 400Ah LFP 24V nominal battery with Daly BMS, used for water pumping and day time air conditioning.
5Kw Yanmar clone single cylinder air cooled diesel generator for rare emergency charging and welding. -
mcgivor said:Peak to peak is meaningless as it's never at both positive and negative potentials at the same time.You have lived in DC land too long.RMS voltage and P-P voltage are critical. I just read a long article about VFD drives, and how fixed speed motors, connected to VFD controllers, are being fried from P-P voltages induced in them. P-P voltage is why most household wire is rated 600V, otherwise, why not rate it to only 300 ?Powerfab top of pole PV mount | Listeroid 6/1 w/st5 gen head | XW6048 inverter/chgr | Iota 48V/15A charger | Morningstar 60A MPPT | 48V, 800A NiFe Battery (in series)| 15, Evergreen 205w "12V" PV array on pole | Midnight ePanel | Grundfos 10 SO5-9 with 3 wire Franklin Electric motor (1/2hp 240V 1ph ) on a timer for 3 hr noontime run - Runs off PV ||
|| Midnight Classic 200 | 10, Evergreen 200w in a 160VOC array ||
|| VEC1093 12V Charger | Maha C401 aa/aaa Charger | SureSine | Sunsaver MPPT 15A
solar: http://tinyurl.com/LMR-Solar
gen: http://tinyurl.com/LMR-Lister , -
mike95490 said:mcgivor said:Peak to peak is meaningless as it's never at both positive and negative potentials at the same time.You have lived in DC land too long.RMS voltage and P-P voltage are critical. I just read a long article about VFD drives, and how fixed speed motors, connected to VFD controllers, are being fried from P-P voltages induced in them. P-P voltage is why most household wire is rated 600V, otherwise, why not rate it to only 300 ?
The rating for insulation is based on RMS of the peak voltage to ground, not peak to peak, typically the insulation value of low voltage conductors such as 600V is actually way in excess of its rated value. This discussion https://forums.mikeholt.com/showthread.php?t=127506 briefly discusses the topic. The problem with using frequency drives with motors not specifically designed for them, is the drives tend to produce spikes in the waveform, these have a tendency to break down the insulation of the windings creating shorts between them, leading to premature failure, something I'm very familiar with.
1500W, 6× Schutten 250W Poly panels , Schneider MPPT 60 150 CC, Schneider SW 2524 inverter, 400Ah LFP 24V nominal battery with Battery Bodyguard BMS
Second system 1890W 3 × 300W No name brand poly, 3×330 Sunsolar Poly panels, Morningstar TS 60 PWM controller, no name 2000W inverter 400Ah LFP 24V nominal battery with Daly BMS, used for water pumping and day time air conditioning.
5Kw Yanmar clone single cylinder air cooled diesel generator for rare emergency charging and welding. -
mcgivor said:Peak to peak is meaningless as it's never at both positive and negative potentials at the same time.
-
Estragon said:I'm no kind of expert on AC, but is (+) peak to (-) peak (or trough) voltage relevant to much of anything?
I get that curve shape, timing, and capacitance/inductance matters. Just not sure how RMS peak x 2 matters. -
Back to the thread topic, here is a Danfoss 230VDC to 230VAC inverter, it would seem it can accept up to 380VDC, https://www.alibaba.com/product-detail/inverter-12kw-danfoss-vlt-2811-inverter_60679221182.html
Just a reference link, contacting Danfoss directly would probably be a good idea, Alibaba specs are for multiple units and often misleading, getting lost in translation.1500W, 6× Schutten 250W Poly panels , Schneider MPPT 60 150 CC, Schneider SW 2524 inverter, 400Ah LFP 24V nominal battery with Battery Bodyguard BMS
Second system 1890W 3 × 300W No name brand poly, 3×330 Sunsolar Poly panels, Morningstar TS 60 PWM controller, no name 2000W inverter 400Ah LFP 24V nominal battery with Daly BMS, used for water pumping and day time air conditioning.
5Kw Yanmar clone single cylinder air cooled diesel generator for rare emergency charging and welding. -
mike_s said:Estragon said:I'm no kind of expert on AC, but is (+) peak to (-) peak (or trough) voltage relevant to much of anything?
I get that curve shape, timing, and capacitance/inductance matters. Just not sure how RMS peak x 2 matters.
Seems to me there's nothing simple in changing DC into (grid quality) AC. If it was, we'd all be fine with cheap hardware store MSW inverters. Especially with motor loads, it gets complicated pretty fast.Off-grid.
Main system ~4kw panels into 2xMNClassic150 370ah 48v bank 2xOutback 3548 inverter 120v + 240v autotransformer
Night system ~1kw panels into 1xMNClassic150 700ah 12v bank morningstar 300w inverter -
Estragon said:mike_s said:It matters if you're trying to simply/directly change DC into AC. That's what this thread is about.
Seems to me there's nothing simple in changing DC into (grid quality) AC. If it was, we'd all be fine with cheap hardware store MSW inverters. Especially with motor loads, it gets complicated pretty fast. -
In the typical full H bridge, the peak voltage is not doubled. One side or the other is switched to the common negative at the desired frequency and the other side is pulsed to positive with a variable duty cycle at a much higher frequency. An inductor averages out those pulses to make a sine wave. The motor can be thought of as an inductor. In three phase there are three half bridges.
-
How about ...1. Connecting the 10 solarpanels in parallel. This would give me 28 V dc 75 amp output.2. Converting this into 230 V ac by use of a converter that is sold for truckdrivers who want to watch television in their cabin etc when sleeping on the road.So instead of feeding the converter with power from batteries directly feeding him solarenergy ...Good idea ? Foolish idea ?I have found such converter for a reasonable price. It outputs 230V ac max 1500 Watt and it needs an input of in between 20 and 31 V dc.
-
Here is "thierry's" pump link through google translate (to English):
https://translate.google.com/translate?sl=auto&tl=en&u=https%3A%2F%2Fclasalpumps.com%2Fnl%2Fzuigerpompen%2Fhydrofoorgroepen
I don't see any motor specifications at all.. It looks like a standard induction motor--And I would guess there are configuraiton options (voltage, frequency, 1/3 phase, etc.).
Yes, it is possible to put a bunch of solar panels in parallel and run an "off the shelf" AC inverter. One vendor did that, but I cannot find their product... It appeared to be a voltage controlled switch. When the DC input fell below the AC inverter's input voltage, it would power off/on the inverter when the voltage was restored (many AC inverters will "lock off" when the DC input falls below LVD--low voltage cutoff--The voltage controlled switch cut power to reset the inverter and allow it to start again).
I still think that a VFD (variable frequency drive) would be a better fit--But there is a lot of research needed to figure out what motor you have on the pump and match it with a "solar capable input" VFD to get everything working.
10 years ago, a solar VFD setup was not common--These days, there are a bunch of vendors (including China based) that are seliing these VFDs (from what I can see).
-BillNear San Francisco California: 3.5kWatt Grid Tied Solar power system+small backup genset -
What i know about the pump through experience is that it doesn t work on a 750 w generator. But it does work with a 1500 w generator ...
-
and al the generators i have used output 230V ac 50 hz. No 3 phase connections on it.
-
and here is the convertor i have in mind. Its dutch again but on the right you can see the technical specifications.
Categories
- All Categories
- 227 Forum & Website
- 135 Solar Forum News and Announcements
- 1.3K Solar News, Reviews, & Product Announcements
- 198 Solar Information links & sources, event announcements
- 895 Solar Product Reviews & Opinions
- 255 Solar Skeptics, Hype, & Scams Corner
- 22.4K Solar Electric Power, Wind Power & Balance of System
- 3.5K General Solar Power Topics
- 6.7K Solar Beginners Corner
- 1K PV Installers Forum - NEC, Wiring, Installation
- 2.1K Advanced Solar Electric Technical Forum
- 5.5K Off Grid Solar & Battery Systems
- 428 Caravan, Recreational Vehicle, and Marine Power Systems
- 1.1K Grid Tie and Grid Interactive Systems
- 652 Solar Water Pumping
- 815 Wind Power Generation
- 624 Energy Use & Conservation
- 618 Discussion Forums/Café
- 311 In the Weeds--Member's Choice
- 75 Construction
- 124 New Battery Technologies
- 108 Old Battery Tech Discussions
- 3.8K Solar News - Automatic Feed
- 3.8K Solar Energy News RSS Feed