Attaching and securing a large solar array to a van roof two ways for safety
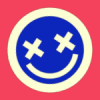
I have a 170" wheelbase Sprinter and 5 100W panels. I plan on bolting the long edges of the panels together to make one large panel, 5 panels wide. I will also bolt the short edges to two 8 foot aluminum angle brackets. Here's an illustration of what I mean. (The light gray lines between the panels indicate where bolts would be, underneath the panels, holding them together. Though, I might use aluminum or steel plates and bolt the plates to the panels using their existing holes.
Once that's all done, I'm going to be mounting it onto two Superstruts that I will bolt through my roof. The Superstruts are 10 feet long and mount with the U shape upright. They have special nuts that sit under the lip of the U opening that you can bolt down into. The nuts have little teeth on them to bite into the strut.
I'm thinking of using four of these heavy duty angle brackets to hold the panels to the Superstruts in such a way that one edge could hinge up for tilting the panels. These might look small in the image, but those holes are over 1/2" in diameter. These are seriously heavy duty brackets made for Superstruts.
Even if using Loctite thread locker and plenty of torque, there's always the chance that a bolt or two will work its way loose on the highway leading to a catastrophic failure. The panels could fly off the roof and hit another motorist. I'd only lose $550 in panels, but they could injure or kill someone. I'm thinking I need a secondary safety mechanism to prevent this, making the worst case scenario be some damage to the panels themselves or to my van.
My first thought was to drill a hole (or pair of holes) at each of the four corners of the combined panels, and thread 1/8" coated steel cable through them, then permanently or temporarily crimping the cable together. (The image shows temporary crimping hardware. I could also do permanent crimps.) The other end of the cable would go through holes I drill into the sides of the Superstruts, where I'd crimp them again. Then, if the bolts worked themselves loose, the cable would stop the panels from flying off, but they'd probably make a hell of a racket bouncing around, alerting me to the problem.
One problem with this idea is I'd like to tilt the panels. I would tilt them all at once as a unit towards the side of the van. I'd either have to only add this safety cable to the hinged side of the panels, or come up with a quick release mechanism for the cable on the tilted edge.
One idea I had was to see if I could use PC locking cables. I could thread the cable through holes in the panel, and add the lock to the end. Then I'd probably need some place to stick the lock to prevent it from rattling around. A little mounting bracket of some sort. Then, I could undo the lock, unbolt the panels, and tilt them with whatever tilting mechanism I end up with. In addition, this would add a little security, Especially if I add some kind of knobbed bolt as a quick release.
I could use the angle brackets, ratcheting knobs, and rivnuts. The ratcheting knobs can be torqued down pretty well, even with limited space to get your hand around it. The rivnuts would also be used for the vertical support that keeps the panels tilted up. I could have upright supports with several holes for various latitudes, and use some more of the same knobs. I'd need some wingnuts for the bottom, or female knobs.
Instead of cables, I could probably find a way to incorporate locking pins or something similar. They are inherently quick-release, which is nice. I'm having trouble visualizing where they would go, though, especially on the hinged side. On the side that tilts up, maybe I could use a couple of small hasps. And then why use pins when I could lock them! (Panel theft is definitely a risk.) The hasps could be screwed to the panels and Superstruts if I pre-drilled some holes.
Maybe I'm too set on trying to use the angle brackets I linked above. Maybe I should use traditional hinges all the way along one edge. With so many hinges and bolts along one edge, it seems like there'd be little to no chance of them all coming loose. I'll just have to figure out a way to attach the hinges to the Superstruts. I don't think I could use those fancy nuts. The bolts would just get in the way. Might have to drill holes on the side and bolt them on that way. Unless I could find some special hinges that had a good amount of clearance between the two plates. Or some sort of offset hinges. Googling "offset hinges" produced all sorts of interesting results.
At this point I'm just thinking out loud. Any other ideas? Has anyone else done something similar?
Comments
-
Don't use loctite. Use SS hardware, and backup the factory nuts with NyLoc nuts. Use anti-size on all the hardware, SS has a nasty habit of galling itself if not lubed.
Don't us PC laptop lock gear, it's not rated for any weather and will rust up on you.
Something like hot rod hood latch pins, with weatherproof locks or hitch pins from tractors, whatever you use, has to take the weather.
Powerfab top of pole PV mount | Listeroid 6/1 w/st5 gen head | XW6048 inverter/chgr | Iota 48V/15A charger | Morningstar 60A MPPT | 48V, 800A NiFe Battery (in series)| 15, Evergreen 205w "12V" PV array on pole | Midnight ePanel | Grundfos 10 SO5-9 with 3 wire Franklin Electric motor (1/2hp 240V 1ph ) on a timer for 3 hr noontime run - Runs off PV ||
|| Midnight Classic 200 | 10, Evergreen 200w in a 160VOC array ||
|| VEC1093 12V Charger | Maha C401 aa/aaa Charger | SureSine | Sunsaver MPPT 15A
solar: http://tinyurl.com/LMR-Solar
gen: http://tinyurl.com/LMR-Lister , -
Superstrut is available in both aluminum and stainless, aluminum will be lighter, galvanized steel will tend to rust, especially where cut and where bolts break the zinc coating, just a thought.
1500W, 6× Schutten 250W Poly panels , Schneider MPPT 60 150 CC, Schneider SW 2524 inverter, 400Ah LFP 24V nominal battery with Battery Bodyguard BMS
Second system 1890W 3 × 300W No name brand poly, 3×330 Sunsolar Poly panels, Morningstar TS 60 PWM controller, no name 2000W inverter 400Ah LFP 24V nominal battery with Daly BMS, used for water pumping and day time air conditioning.
5Kw Yanmar clone single cylinder air cooled diesel generator for rare emergency charging and welding. -
I was thinking of using yellow zinc plated grade 8 steel bolts. They are stronger than stainless, but I'm not even sure I even need that much strength. I'm not sure how they compare in terms of overall corrosion resistance. I know that if you scratch through the coating, they'll rust. Thanks for the tips on galling. I'd never heard of that before.
Regarding the nylon lock nuts: I use them a lot, but I'm not sure how I'd get them onto the bolts behind the Superstrut nuts. There's not a lot of space in there. The overall dimensions of the struts are 1-5/8" square, and it's heavy gauge metal. Again, not a lot of room in there. Any suggestions?
The Superstruts themselves are yellow zinc plated: "...trivalent chromium finish applied over zinc". Their nuts have the same coating. I didn't realize they made aluminum ones. I've never seen them in stores. Looking online, I don't see them either. I see similar products... Unistrut brand? I was just thinking about priming and painting the steel ones with Krylon automotive acrylic. I don't plan on cutting them, but I will need to drill some holes for mounting hasps using metal screws. They could corrode there. I could always paint the hasps, too, screws and holes and all. Or maybe use some lap sealant.
-
I have used Zinc Paint on stuff near the ocean:
And there are conversion (acids) that take light surface rust and converts to a stable form of "rust". Also, this treatment does a really nice job of preping the steel surface for a nice ust resistant paint:
I have used the phosphoric conversion "acid" based chemicals and found that work very well. Don't know anything about the Tannic Acid versions.
I never have had any luck with Navel Jelly.
You probably don't need grade 8 bolts... And depending on their hardness and surface treatment (and any post plating heat teratment), you could possibly end up with hydrogen embrittlment. A very nasty problem (high strength steels, water/salt water, plating, high hardness).
Nominally, your sturcture should withstand 50 to 100 lbs per square foot of panel (check the ratings of the panels you want to use for snow loading and wind loading numbers). One a larger array--Those loadings can create lots of worrysome stresses in the framework.
High strength bolts with hydrogen embrittlement are much more prone to failure at any stress, than low strength steels.
https://duckduckgo.com/?q=grade+8+bolts+and+hydrogen+embritalment&atb=v122-1__&ia=web
Not a trivial issue...
-Bill
Near San Francisco California: 3.5kWatt Grid Tied Solar power system+small backup genset -
Create an air foil at the leading edge of the array to keep freeway speed wind out from under the panels.
2.1 Kw Suntech 175 mono, Classic 200, Trace SW 4024 ( 15 years old but brand new out of sealed factory box Jan. 2015), Bogart Tri-metric, 460 Ah. 24 volt LiFePo4 battery bank. Plenty of Baja Sea of Cortez sunshine.
-
Let me be the heretic & cheap charlie here. Fixing mechanisms are ridiculously expensive IMHO when all you really need for most RV-type installations is marine ply, a solar-rated sealant, and suitable screws rated for the material you are drilling through or fixing to. The sealant and the screws are factors you need to determine as per your particular circumstances.
I will use a 150 watt panel as an example. Cut out of a marine ply sheet 6x slightly rectangular pieces of sufficient structural integrity to accommodate two screws to each piece, one screwed to the frame of the panel, and the other to the RV roof. You will need one rectangular piece of marine ply for each corner and one for the middle of each long side of the panel.
To assemble, all you need do is screw the ply pieces first to the frame of the panel, making sure there is plenty of sealant between the frame and the ply. This will stop any potential for screws to vibrate out. Plus also the screw length and ply depth need be of sufficient dimension so that if a screw does vibrate out it will connect with the roof surface and go no further sufficient to cause a dislocation.
Next step, place the panel with the ply pieces on the RV roof and screw into place. Make sure there is a good amount of sealant between the RV roof and the plywood piece.
As a further protection, after affixing to the RV roof I would apply two or three heavy coats of UV rated paint to all sun exposed ply.
760W panel array, 4 x 6v 220 ah Crown batteries, Tristar TS-45 PWM controller, no name 600 PSW inverter. -
So much for the tilting feature.
2.1 Kw Suntech 175 mono, Classic 200, Trace SW 4024 ( 15 years old but brand new out of sealed factory box Jan. 2015), Bogart Tri-metric, 460 Ah. 24 volt LiFePo4 battery bank. Plenty of Baja Sea of Cortez sunshine.
-
If the implication is to mount the panels on a sheet of plywood, there would be no, or very little ventilation, resulting in heat buildup, low output and probably shorter lifespan.
The idea I've always had, as just a thought for mobile applications, would be to use stainless steel casement hinges to achieve tilt, mounted to a ridged frame with lock down clasps for travel. It would be better if each module was independent to limit stress on the hinges themselves, mounted sideways they could achieve optimum angle without shadowing the neighboring modules.
Just some thoughts to ponder http://www.welcharm.com/en/product/products-0-62.html
1500W, 6× Schutten 250W Poly panels , Schneider MPPT 60 150 CC, Schneider SW 2524 inverter, 400Ah LFP 24V nominal battery with Battery Bodyguard BMS
Second system 1890W 3 × 300W No name brand poly, 3×330 Sunsolar Poly panels, Morningstar TS 60 PWM controller, no name 2000W inverter 400Ah LFP 24V nominal battery with Daly BMS, used for water pumping and day time air conditioning.
5Kw Yanmar clone single cylinder air cooled diesel generator for rare emergency charging and welding. -
The ply is only situated at the corners of the panel and a similar size piece situated in the middle of each of the long sides. Ventilation is not a problem.
Granted though it may not look as flash as other fixing systems. But my RV is a 40 year old bus conversion, certainly not of huge value. Wouldn't recommend for a big $$$ late model type RV.
760W panel array, 4 x 6v 220 ah Crown batteries, Tristar TS-45 PWM controller, no name 600 PSW inverter.
Categories
- All Categories
- 228 Forum & Website
- 136 Solar Forum News and Announcements
- 1.4K Solar News, Reviews, & Product Announcements
- 199 Solar Information links & sources, event announcements
- 898 Solar Product Reviews & Opinions
- 256 Solar Skeptics, Hype, & Scams Corner
- 22.5K Solar Electric Power, Wind Power & Balance of System
- 3.5K General Solar Power Topics
- 6.7K Solar Beginners Corner
- 1K PV Installers Forum - NEC, Wiring, Installation
- 2.1K Advanced Solar Electric Technical Forum
- 5.6K Off Grid Solar & Battery Systems
- 428 Caravan, Recreational Vehicle, and Marine Power Systems
- 1.1K Grid Tie and Grid Interactive Systems
- 654 Solar Water Pumping
- 816 Wind Power Generation
- 624 Energy Use & Conservation
- 619 Discussion Forums/Café
- 312 In the Weeds--Member's Choice
- 75 Construction
- 124 New Battery Technologies
- 108 Old Battery Tech Discussions
- 3.8K Solar News - Automatic Feed
- 3.8K Solar Energy News RSS Feed