Charge Controller!? (and general help)
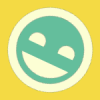
Nikola
Registered Users Posts: 6 ✭✭
Hi, new here!
I'm building a cargo trailer work shop and I need help choosing a CHARGE CONTROLLER.
I have 3 (310 Watt 24V panels) = 930W wired in parallel
930 watts / 24V = 38.75 Amps
I heard that you should add and extra 25% to be safe, so that would be 48.44 Amps.... So I need a 50 Amp PWM charge controller? Is this correct, or can I go with a 40 Amp controller?
Anyone have any suggestions of a decent charge controller?
Is this one good?------>AMAZON CHARGE CONTROLLER
Thanks!!
I'm building a cargo trailer work shop and I need help choosing a CHARGE CONTROLLER.
I have 3 (310 Watt 24V panels) = 930W wired in parallel
930 watts / 24V = 38.75 Amps
I heard that you should add and extra 25% to be safe, so that would be 48.44 Amps.... So I need a 50 Amp PWM charge controller? Is this correct, or can I go with a 40 Amp controller?
Anyone have any suggestions of a decent charge controller?
Is this one good?------>AMAZON CHARGE CONTROLLER
Thanks!!
Tagged:
Comments
-
Don't expect that kind of amperage with a PWM controller, won't happen. At best you will get 8.38 amps x 3 = 25.14 amps.
If you use a MPPT controller you can expect higher power somewhere in the 38 amp range.
The controller you have listed here is a low grade PWM controller. I have used them. they are OK, at best. Spend a little more money on a decent MPPT controller and enjoy a full harvest from your panels.
2.1 Kw Suntech 175 mono, Classic 200, Trace SW 4024 ( 15 years old but brand new out of sealed factory box Jan. 2015), Bogart Tri-metric, 460 Ah. 24 volt LiFePo4 battery bank. Plenty of Baja Sea of Cortez sunshine.
-
I have no problem with PWM controllers, they are cost effective and produce well with panels that are the proper voltage for your system. If you intend to have a 24 volt system, inverter, battery bank and your panels are in the 34-37 volt VMP area then a PWM would likely be cost effective for you. I don't know anything about the charge controller you have linked to. Y-Solar makes some that are at least 'okay'.
Please note When you suggest This;Nikola said:930 watts / 24V = 38.75 Amps
With a PWM charge controller, you will get close to the IMP amperage passed through the charge controller. You can find this information on the back of your solar panel, but it should be around 930/35 (VMP)= @26 amps, in reality it will be somewhat less than this as the current (amperage) will drop a bit in the heat.
I would suggest a Midnite Brat controller for a 'high end controller if you don't expect to increase your array.
https://www.solar-electric.com/midnite-solar-brat-pwm-solar-charge-controller.html
Some people can't handle a simple controller and want to see the current system voltage, I think this is made by Y-solar who might make the one you have linked to;
https://www.amazon.com/HQST-Regulator-Charge-Controller-Display/dp/B00FB3OPKM/ref=sr_1_3?ie=UTF8&qid=1514412254&sr=8-3&keywords=y-solar+charge+controller
If you want to use a MPPT type charge controller, you should be careful. You have 3 panels and MPPT type controller need about 2x the system voltage to work effectively. Since you have 3 you would want to put all three in series and some controllers won't be able to handle the high VOC.
The typical potential can be calculated for MPPT type using the formula total wattage 930 x .75 (de-rating for voltage drop in normal operating temperatures.) divided by the charging current for your system voltage. a 24 volt battery bank would charge at about 29 volts. 930x.75=697.5 697.5/29= 24 amps. While you might generate a bit more on cold days this would be considered the norm. If you can find NOCT (Normal Operating Cell Temperature) values in you spec sheet they would be more accurate, but 75% will be very close.
Again if you don't plan to expand your system, Midnite make a nice 30 amp MPPT charge controller;
https://www.solar-electric.com/midnite-solar-kid-mppt-solar-charge-controller-black.html
Home system 4000 watt (Evergreen) array standing, with 2 Midnite Classic Lites, Midnite E-panel, Magnum MS4024, Prosine 1800(now backup) and Exeltech 1100(former backup...lol), 660 ah 24v Forklift battery(now 10 years old). Off grid for 20 years (if I include 8 months on a bicycle).
- Assorted other systems, pieces and to many panels in the closet to not do more projects. -
Can you give us the specifications for your 310 Watt panels? Note that many of these "grid tied" type panels have Vmp~30 volts (some are Vmp~35 volts, others may be higher or lower).
For a 24 volt lead acid battery bank, you need a solar panel (or solar array) with the Vmp (voltage maximum power) in the range of ~35 to 40 VDC (commonly known as 72 cell panels).
Vmp~30 volts is not high enough to quickly/fully charge a 24 volt battery bank. The Vmp-hot voltage can fall as low as ~25.5 volts on a hot day, an you need (for flooded cell lead acid batteries) around Vbat~29-32 volts.
PWM controllers (Pulse Width Modulation) essentially pass the Vmp array voltage straight through (basically an electronic switch that turns on and off many times a second).
MPPT controllers (Maximum Power Point Tracking) are typically "buck mode" switching power supplies, they can take higher voltages and efficiently "down convert" to lower voltages.
As an example, you would take 2x 310 Watt panels (Vmp~30 volts typical) and put them in series for Vmp-array~60 volts. The MPPT controller will down convert to the ~29 volts needed by the battery bank for charging. Or, you can take 3x 30 volt panels in series for Vmp-array 90 volts and work just fine with a higher end MPPT charge controller (many will take a bit over 100 VDC Vmp just fine).
-Bill
Near San Francisco California: 3.5kWatt Grid Tied Solar power system+small backup genset -
Thanks all for the help!
Volt max power is 36.38V. So 930W / 36.38V = 25.56 max amps to the controller, so the Midnight Brat that @Photowhit mentioned would be perfect??
System specs are attached:
I have 6 of these batteries from Craigslist out of a "cell phone" tower:
Used ebay (great condition:)
I'm hoping my 1800W inverter will allow me to run lights and a 1500W heat lamp, and other tools like a skill saw or 30 gal air compressor not at the same time of course. I would have to shut everything down including lights if I ran a 15A skill saw, Correct?
Thanks a bunch!
-
You probably wouldn't need the lights if you were running your Skill saw during daylight hours. And while the saw can draw up to 15 amps, it might not always take that much current when cutting thinner material. Your solar system should do fine with the heavy but intermittent nature of the loads you have mentioned (although how long did you intend to run that heat lamp?)
LED lights take very little power in comparison to the incandescents used only a few years ago.Island cottage solar system with appriximately 2500 watts of panels, 1kw facing southeast 1.3kw facing southwest 170watt ancient Arco's facing due south. All panels in parallel for a 24 volt system. Trace DR1524 MSW inverter which has performed flawlessly since 1994. Outback Flexmax 80 MPPT charge controller four 467A-h AGM batteries. Insignia 11.5 cubic foot electric fridge 1/4hp GSW piston pump. My 31st year. -
Heat lamp would be ran maybe 20 - 30 minutes or less a few times per day (most likely only in winter.)
The inverter has 2900W surge rating for 5 seconds. Hopefully it's perfect and I won't have to upgrade.
I need to make sure I get the right charge controller though. I like the Midnight brat, but want to make sure it's right.
Also, can anyone tell me if the batteries pictured are AGM or Flooded? I'm pretty sure they're flooded.
Sorry, but I am new to all this. I'm grateful that there's a beginner's section here.
Thanks!
-
Nikola said:Sorry, but I am new to all this. I'm grateful that there's a beginner's section here.
THE GOOD;Nikola said:The inverter has 2900W surge rating for 5 seconds. Hopefully it's perfect and I won't have to upgrade.
THE BAD;Nikola said:Also, can anyone tell me if the batteries pictured are AGM or Flooded? I'm pretty sure they're flooded.
Link to specs; http://www.makopower.com/site/assets/files/1101/ups12-490mrlp.pdf
They are 112 amp hr (at 20 hour rate). A single string would have 112 amp hours at 24 volts, or (24x112=) 2688 watt hours.
To give you an idea, in general you wouldn't want to run down past 50%, since these are desiged for float mode with rare deep cycling, I'd suggest staying in the upper 25% That's only @650 watt hour of use, likely <20 minutes of run time on the skill saw!
Home system 4000 watt (Evergreen) array standing, with 2 Midnite Classic Lites, Midnite E-panel, Magnum MS4024, Prosine 1800(now backup) and Exeltech 1100(former backup...lol), 660 ah 24v Forklift battery(now 10 years old). Off grid for 20 years (if I include 8 months on a bicycle).
- Assorted other systems, pieces and to many panels in the closet to not do more projects. -
depending on the motor on the air compressor, it may not start it, too much surge. Only one way to find out
Powerfab top of pole PV mount | Listeroid 6/1 w/st5 gen head | XW6048 inverter/chgr | Iota 48V/15A charger | Morningstar 60A MPPT | 48V, 800A NiFe Battery (in series)| 15, Evergreen 205w "12V" PV array on pole | Midnight ePanel | Grundfos 10 SO5-9 with 3 wire Franklin Electric motor (1/2hp 240V 1ph ) on a timer for 3 hr noontime run - Runs off PV ||
|| Midnight Classic 200 | 10, Evergreen 200w in a 160VOC array ||
|| VEC1093 12V Charger | Maha C401 aa/aaa Charger | SureSine | Sunsaver MPPT 15A
solar: http://tinyurl.com/LMR-Solar
gen: http://tinyurl.com/LMR-Lister , -
And you have Vmp~36 volt panels--Those are perfect for use with PWM solar charge controllers (connect your panels in parallel--You should fuse/breaker each panel through a combiner box if you have 3 or more panels for fire safety).
-Bill
Near San Francisco California: 3.5kWatt Grid Tied Solar power system+small backup genset -
mike95490 said:depending on the motor on the air compressor, it may not start it, too much surge. Only one way to find outPhotowhit said:They are 112 amp hr (at 20 hour rate). A single string would have 112 amp hours at 24 volts, or (24x112=) 2688 watt hours.
To give you an idea, in general you wouldn't want to run down past 50%, since these are desiged for float mode with rare deep cycling, I'd suggest staying in the upper 25% That's only @650 watt hour of use, likely <20 minutes of run time on the skill saw!
I would have 2 sets of 3 batteries wired in parallel. So.. 24v and 336Ah = 8064Wh. 25% of which is 2016Wh. (25% though? Really?)
So if I wanted to use 25% of the battery for 20 hours straight, I could only run 100.8 watts continuously for 20 hours?
336Ah x 24V x 0.25 (percent of discharge) x 0.90 (inverter efficiency) / 1500 watts (heat/curing lamp) = 1.21 hours
So I can run the 1500 watt curing lamp continuously for about 1.2 hours before I deplete the battery to 75% (not accounting for other losses.)BB. said:And you have Vmp~36 volt panels--Those are perfect for use with PWM solar charge controllers (connect your panels in parallel--You should fuse/breaker each panel through a combiner box if you have 3 or more panels for fire safety).
-Bill
I was just planning on putting one fuse on the positive wire to the CC.
And then a breaker going to the inverter.
-
Typically, for that size panel, it is 15 amp fuse/breaker (don't need false trips).
By the way, your inverter appears to be 12 VDC input... Does not work with a 24 volt battery bank (if that was your plan). You cannot daw "split power" (12 volts from 1/2 a 24 volt battery bank) without lots of problems.
-Bill
Near San Francisco California: 3.5kWatt Grid Tied Solar power system+small backup genset -
BB. said:By the way, your inverter appears to be 12 VDC input... Does not work with a 24 volt battery bank (if that was your plan). You cannot daw "split power" (12 volts from 1/2 a 24 volt battery bank) without lots of problems.
Home system 4000 watt (Evergreen) array standing, with 2 Midnite Classic Lites, Midnite E-panel, Magnum MS4024, Prosine 1800(now backup) and Exeltech 1100(former backup...lol), 660 ah 24v Forklift battery(now 10 years old). Off grid for 20 years (if I include 8 months on a bicycle).
- Assorted other systems, pieces and to many panels in the closet to not do more projects. -
Home system 4000 watt (Evergreen) array standing, with 2 Midnite Classic Lites, Midnite E-panel, Magnum MS4024, Prosine 1800(now backup) and Exeltech 1100(former backup...lol), 660 ah 24v Forklift battery(now 10 years old). Off grid for 20 years (if I include 8 months on a bicycle).
- Assorted other systems, pieces and to many panels in the closet to not do more projects. -
Yes they are all 24 Volt.
-
Never mind, that was the 12 volt battery label, not the inverter.
-BillNear San Francisco California: 3.5kWatt Grid Tied Solar power system+small backup genset -
A couple of points on the run time numbers; the 20 hour rate doesn't apply to fast discharges, and capacity is temperature dependent. The apparent capacity of the battery will be considerably lower at a ~1hr rate vs 20hr rate, and also at low temps. Mine lose about 1/3 of capacity in winter in an enclosed but unheated crawlspace.
336Ah x 24V x 0.25 (percent of discharge) x 0.90 (inverter efficiency) / 1500 watts (heat/curing lamp) = 1.21 hours
So I can run the 1500 watt curing lamp continuously for about 1.2 hours before I deplete the battery to 75% (not accounting for other losses.)BB. said:And you have Vmp~36 volt panels--Those are perfect for use with PWM solar charge controllers (connect your panels in parallel--You should fuse/breaker each panel through a combiner box if you have 3 or more panels for fire safety).
-Bill
I was just planning on putting one fuse on the positive wire to the CC.
And then a breaker going to the inverter.
You should fuse individual panels when you have more than two because a short in one panel could be fed by the combined current of the remaining ones. You would normally also put a larger fuse/breaker on the larger wire going from the combiner to the controller. Note that with batteries in parallel groups of three, the same fusing applies. Each battery should be fused IMO.
Off-grid.
Main system ~4kw panels into 2xMNClassic150 370ah 48v bank 2xOutback 3548 inverter 120v + 240v autotransformer
Night system ~1kw panels into 1xMNClassic150 700ah 12v bank morningstar 300w inverter -
Estragon said:
Note that with batteries in parallel groups of three, the same fusing applies. Each battery should be fused IMO.
I believe the diagram below is what you are suggesting.
How do I determine the wire sizes and thus, the fuse/breaker sizes, for A, B, and C labeled in the picture below?
Thank you all for the help!!
-
a) inverter manual will suggest a wire size for the length of cable run (I'll guess around 90A, & 1/O cable)
b) charge controller manual will suggest a wire size ( Brat is PWM, 30A, 10ga wire, but i'd use 8ga)
c) I have no idea what you are trying to do to those batteries
I prefer breakers over fuses. Midnight sells some nice DC rated, switching rated, breakers
Powerfab top of pole PV mount | Listeroid 6/1 w/st5 gen head | XW6048 inverter/chgr | Iota 48V/15A charger | Morningstar 60A MPPT | 48V, 800A NiFe Battery (in series)| 15, Evergreen 205w "12V" PV array on pole | Midnight ePanel | Grundfos 10 SO5-9 with 3 wire Franklin Electric motor (1/2hp 240V 1ph ) on a timer for 3 hr noontime run - Runs off PV ||
|| Midnight Classic 200 | 10, Evergreen 200w in a 160VOC array ||
|| VEC1093 12V Charger | Maha C401 aa/aaa Charger | SureSine | Sunsaver MPPT 15A
solar: http://tinyurl.com/LMR-Solar
gen: http://tinyurl.com/LMR-Lister , -
As @mike95490 says, breaker sizes should be spec'd in manuals. I also prefer breakers for inputs and outputs to controller and inverter as they're better for using as disconnects. For wire size, I like to use the largest cable that will physically fit on the controller and inverter terminals, and keep run length as short as possible.
Individual battery fuses should be sized to protect the smallest wire in the circuits (likely the cables marked "C". Heavy wire there too (I'd use 1ga or larger) with quality crimps to minimize differences in resistance. I would also move the negative series connection on each group of batteries to the far left negative terminal on the left group (and far right on the right hand group) so the circuit runs diagonally through the group.
When these batteries die, I would consider replacing with larger deep cycle 6v batteries, such as 350ah L16s in a single string.Off-grid.
Main system ~4kw panels into 2xMNClassic150 370ah 48v bank 2xOutback 3548 inverter 120v + 240v autotransformer
Night system ~1kw panels into 1xMNClassic150 700ah 12v bank morningstar 300w inverter -
For "C", generally, you just jumper the left low battery to the left high batter, etc. (each battery in series with its mate). Saves you 3 battery fuses. No mid-point battery bus.
Using "cross connects" or that "C" bus bar is not needed if the batteries are working correctly. And if you have a problem battery, it hides the failure (it makes all parallel connected batteries have the "same voltage" when you use a meter to check voltages. With all batteries in their own series strings, you can measure the voltage of each battery and see high/low battery voltage readings that need to be investigated.
Cross connecting batteries is common with Li Ion batteries. I still don't like it, but it probably is done to make BMS (battery management systems) easier/cheaper (fewer cell voltage monitoring points).
-Bill
Near San Francisco California: 3.5kWatt Grid Tied Solar power system+small backup genset
Categories
- All Categories
- 228 Forum & Website
- 136 Solar Forum News and Announcements
- 1.4K Solar News, Reviews, & Product Announcements
- 199 Solar Information links & sources, event announcements
- 898 Solar Product Reviews & Opinions
- 256 Solar Skeptics, Hype, & Scams Corner
- 22.5K Solar Electric Power, Wind Power & Balance of System
- 3.5K General Solar Power Topics
- 6.7K Solar Beginners Corner
- 1K PV Installers Forum - NEC, Wiring, Installation
- 2.1K Advanced Solar Electric Technical Forum
- 5.6K Off Grid Solar & Battery Systems
- 428 Caravan, Recreational Vehicle, and Marine Power Systems
- 1.1K Grid Tie and Grid Interactive Systems
- 654 Solar Water Pumping
- 816 Wind Power Generation
- 624 Energy Use & Conservation
- 619 Discussion Forums/Café
- 312 In the Weeds--Member's Choice
- 75 Construction
- 124 New Battery Technologies
- 108 Old Battery Tech Discussions
- 3.8K Solar News - Automatic Feed
- 3.8K Solar Energy News RSS Feed