Solar Piston Pump unable to start
We're helping an institution which purchased a Dankoff Solarforce piston pump form AZ wind & sun. The project is based in Rwanda to supply a hospital with much needed water. The idea is to pump water from the lake, up to the storage tank on top of the hill They dynamic head calculations indicate that the pump should be able to run. Though, the pump was able to push water to the tank, it has failed to start on subsequent days with very similar irradiation. The pump can be assisted to start by pushing the fly wheel, it will then work for a few seconds and stall again.
Below is a diagram.
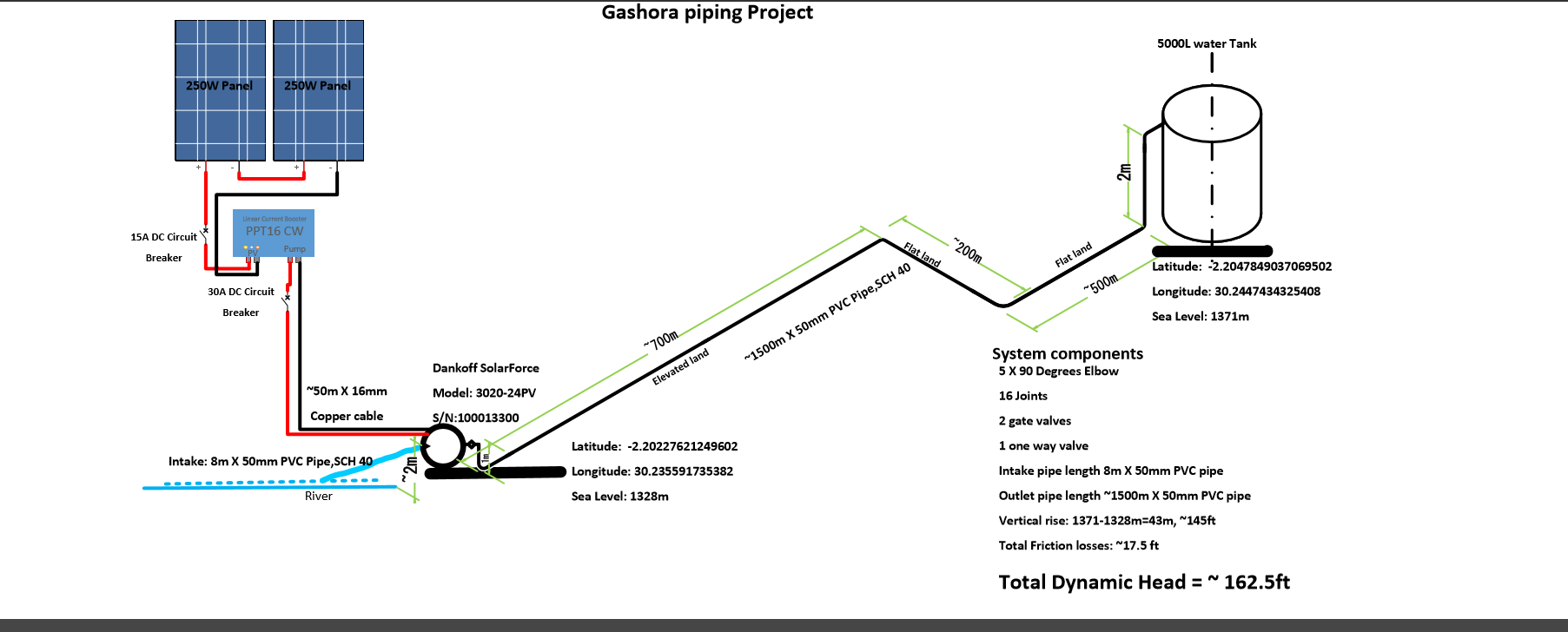
We initially assumed it was the long suction section. This was in the range of a 100ft. Which we reduced by having a trench put in, bringing the water much closer to the pump. We also, tried running the pump from a bucket in order to remove that variable.
We know think it's the extra 90' joins we have in the pip up the hill. Though in our dynamic head calculation we took these into account.
Our next idea is to test with some 24v Batteries in order to take the sun out of the equation. Any idea's are most welcome.
All the best,
Alp
Comments
-
The calculations, at least in theroy seem to be accurate, including total head, elevation, wire size etcetera, which would leave one possibility, that I can think of, the voltage is collapsing under load. Have you measured the actual voltage at the motor? Using batteries to test this theory would be a good method, perhaps the PV is just a little too small, since it will run for a short time with start assist. Have you tried removing the pipe from the outlet to eliminate the back pressure 40 meters is 4 bar, or ~60 psi.1500W, 6× Schutten 250W Poly panels , Schneider MPPT 60 150 CC, Schneider SW 2524 inverter, 400Ah LFP 24V nominal battery with Battery Bodyguard BMS
Second system 1890W 3 × 300W No name brand poly, 3×330 Sunsolar Poly panels, Morningstar TS 60 PWM controller, no name 2000W inverter 400Ah LFP 24V nominal battery with Daly BMS, used for water pumping and day time air conditioning.
5Kw Yanmar clone single cylinder air cooled diesel generator for rare emergency charging and welding. -
If the pump worked on the initial fill and failed on restart, you could very well have a head pressure problem. I see in your parts list a one way valve( check valve) but don’t see its location. I would install a check valve at the top of your initial 700M climb. As @mcgivor stated, drain your pipe to the well head (pump outlet) and try starting the pump again to see if it will run. If it does the check valve I mentioned might work. I didn’t look at your mechanical specs on your pump or panel config., too early in the am and my coffee hasn’t kicked in yet.
Update:Ok coffee kicking in. How did you attach the 16mm cable to you LCB (linear current booster) the specs says the max wire size is 6 Awg on the output. Plus the only linear I see listed is the PPT-16D-3R not the PPT16 CW you have listed in your diagram? You have plenty of PV watts according to the pump specs but you don’t list the panel specs. The linear has a max PV input of 75V, I assume you’re under that? Could you post some pictures of the actual install? It would be helpful.. And as mcgivor said "Have you measured the actual voltage at the motor?" i would add, check voltage at pump under load.
-
@atilev Your diagram shows 2×250 watt panels in series, 250W panels are most likely 60 cell, the manual states when using these, the custom PV voltage selection is used, see belowNote: The 24V setting will by default be for a 72 cell panel by default. Because of the increase in popularity of 60 cell 24 volt panels we have included a custom PV voltage selection that is set for a 24V nominal 60 cell panel. For 60 cell 24V panels move the PV voltage selection jumper to the CUS position
Are they in series? If so the voltage would double, perhaps they should be in parallel.1500W, 6× Schutten 250W Poly panels , Schneider MPPT 60 150 CC, Schneider SW 2524 inverter, 400Ah LFP 24V nominal battery with Battery Bodyguard BMS
Second system 1890W 3 × 300W No name brand poly, 3×330 Sunsolar Poly panels, Morningstar TS 60 PWM controller, no name 2000W inverter 400Ah LFP 24V nominal battery with Daly BMS, used for water pumping and day time air conditioning.
5Kw Yanmar clone single cylinder air cooled diesel generator for rare emergency charging and welding. -
I am curious, 16mm (squared) wire is equivalent to #5 AWG. . Running 50 meters you have about 320+ feet of wire, round trip. That's a lot of wire to carry the current over. The starting surge of the pump is rated at 30 amps. I don't know how much benefit your LCB is going to give but it sure seems like you are asking a lot from those two, approx. 8 1/4 amp panels.
2.1 Kw Suntech 175 mono, Classic 200, Trace SW 4024 ( 15 years old but brand new out of sealed factory box Jan. 2015), Bogart Tri-metric, 460 Ah. 24 volt LiFePo4 battery bank. Plenty of Baja Sea of Cortez sunshine.
-
littleharbor2, are you sure "16mm wire is equivalent to #5 AWG" last I checked 16mm was about .62" dia. and 5 Awg is approx,0.1819 but I come from the land of inches..lol
-
The question is , is this 16mm diameter or 16 mm squared area. I see what you are saying but the voltage chart I referred to shows 16 mm diameter at something considerably over 4/0 or about 5 AWG for 16 mm squared. I may be wrong assuming they are referring to 16 mm squared wire but I had to figure they aren't using such huge wire in such a long run. If I am wrong then I guess that's what I get for assuming.
https://www.calculator.net/voltage-drop-calculator.html
2.1 Kw Suntech 175 mono, Classic 200, Trace SW 4024 ( 15 years old but brand new out of sealed factory box Jan. 2015), Bogart Tri-metric, 460 Ah. 24 volt LiFePo4 battery bank. Plenty of Baja Sea of Cortez sunshine.
-
16 square mm is more or less 5 AWG, using a volt drop calculator, there would be about 21V at 30A, running at ~12A would be ~22.7 or 5%, give or take, not ideal but workable, bringing the two closer together would be benificial without doubt.1500W, 6× Schutten 250W Poly panels , Schneider MPPT 60 150 CC, Schneider SW 2524 inverter, 400Ah LFP 24V nominal battery with Battery Bodyguard BMS
Second system 1890W 3 × 300W No name brand poly, 3×330 Sunsolar Poly panels, Morningstar TS 60 PWM controller, no name 2000W inverter 400Ah LFP 24V nominal battery with Daly BMS, used for water pumping and day time air conditioning.
5Kw Yanmar clone single cylinder air cooled diesel generator for rare emergency charging and welding. -
yeah I saw that as well and is why I asked him how he attached it to the LCB. 50m is one heck of a long dc run and what his voltage at the pump under load was.
-
Metric cable sizes are usually stated in square mm not cross section diameter.FWIW1500W, 6× Schutten 250W Poly panels , Schneider MPPT 60 150 CC, Schneider SW 2524 inverter, 400Ah LFP 24V nominal battery with Battery Bodyguard BMS
Second system 1890W 3 × 300W No name brand poly, 3×330 Sunsolar Poly panels, Morningstar TS 60 PWM controller, no name 2000W inverter 400Ah LFP 24V nominal battery with Daly BMS, used for water pumping and day time air conditioning.
5Kw Yanmar clone single cylinder air cooled diesel generator for rare emergency charging and welding. -
Thanks mcgivor..I guess if all else fails the pump has a hand crank..lol
-
I assume the check valve is what I would call a foot valve that's at the river end of the suction line, and prevents the pump from losing prime?Off-grid.
Main system ~4kw panels into 2xMNClassic150 370ah 48v bank 2xOutback 3548 inverter 120v + 240v autotransformer
Night system ~1kw panels into 1xMNClassic150 700ah 12v bank morningstar 300w inverter -
Estragon said:I assume the check valve is what I would call a foot valve that's at the river end of the suction line, and prevents the pump from losing prime?
-
Piston pumps draw power unevenly (on the piston upstroke and even that isn't linear). You did install the surge tank at the pump, put the right amount of air in it and locate the check valve right after it? This smooths the small dynamic head component. Batteries should help with the rest of it - it's not clear what the peak amps draw is and if the LCB and/or the panels can handle it. Hmm, looks to me like a 4F, 24V car audio capacitor would be about right - might work and be less maintenance than batteries.
I'd locate the LCB near the pump (less amps over the long wire).
Running the pump at zero static head for a day might help - "Run-in: Your new pump may be stiff at first, causing higher current draw than anticipated. This will correct itself as parts wear in."
Note: your drawing should be labeled: Total static + dynamic head = 162.5 ft.I am available for custom hardware/firmware development
-
If there's a check valve after the surge tank on the line up the hill to the holding tank, it might be worth having a second look at how much it adds to head numbers.
I have one in a septic line between a holding tank and septic field. The rise is only a few feet and run is maybe 75'. I modified the installation with a bypass around the check valve so in winter it would drain back and not freeze in the line. With the bypass closed (going through the check valve) it took just about all day to dose the field. With the bypass open, an hour or so. I just leave the bypass open now as the check valve causes way more power consumption than just repumping the pipe of stuff.Off-grid.
Main system ~4kw panels into 2xMNClassic150 370ah 48v bank 2xOutback 3548 inverter 120v + 240v autotransformer
Night system ~1kw panels into 1xMNClassic150 700ah 12v bank morningstar 300w inverter -
Hi Guys,
Thanks for all the comments and suggestions. I was away during the weekend, hence only getting to go through all of them.
To answer the first questions.
- Voltage drop during run. This was an initial idea. We checked the voltage while the pump was started up.
The voltage was as steady as the pump started up.
- Check valve: Check valve is located at the outlet of the pump, prior to pipe. (How do we include this in dynamic head calculation?) How will moving it to the top of the climb help? @Aguarancher
- Pressure tank (surge tank) on pump is there. According to dankoff, it comes pre-pressurized. We haven'd added any air into it.
- @mcgivor @Aguarancher The panels are 60 cell ubink panels in series. I've attached the specs.
- 50m is a long way so yes, moving the LCB closer to the pump might help. At least it's worth testing and using a battery might validate this as well.
- @Estragon There is a foot valve on the intake, there is also a check valve on the outlet to deal with the back pressure.
Things to try:
- Check valve on top of climbe
-- LCB near pump
- Calculate dynamic head with check valve component?
Thanks everyone for the responses. -
Based on "Will accept 12, 24 or 36 volt PV array", I think the LCB is designed for input from your panels in parallel. And check the LCB settings.
Try using 24V of batteries and if that doesn't work, batteries with no LCB.
Even if your dynamic head number is off by 2x, it should still work. But head related problems are easy to diagnose - just open the pipe up at places, reducing head.I am available for custom hardware/firmware development
-
HI @jonr we checked with the LCB manufacturer and the settings should be Ok. They also suggested wiring in series.
-
Where are your gate valves located and are they open? Some pictures of the system would be helpful.
-
According to engineeringtoolbox.com, the minor head loss coefficient for a check valve is roughly the same as for a 1/2 closed gate valve.Off-grid.
Main system ~4kw panels into 2xMNClassic150 370ah 48v bank 2xOutback 3548 inverter 120v + 240v autotransformer
Night system ~1kw panels into 1xMNClassic150 700ah 12v bank morningstar 300w inverter -
Hi gate valves are located at the outflow of the pump and are open. Unfortunately, don't have many pictures. I will be heading to site later this week and plan to take more.
-
A while back I had a piston pump which always leaked back to the well and filled with air, in order to prime it ,I inserted a tee near the output with a vertical pipe with a gate valve to prime and know when it was pumping, once water flowed it would be closed. Although this is not your issue, if such a setup were used in your situation, it could eliminate back pressure and see if it is back pressure preventing startup.1500W, 6× Schutten 250W Poly panels , Schneider MPPT 60 150 CC, Schneider SW 2524 inverter, 400Ah LFP 24V nominal battery with Battery Bodyguard BMS
Second system 1890W 3 × 300W No name brand poly, 3×330 Sunsolar Poly panels, Morningstar TS 60 PWM controller, no name 2000W inverter 400Ah LFP 24V nominal battery with Daly BMS, used for water pumping and day time air conditioning.
5Kw Yanmar clone single cylinder air cooled diesel generator for rare emergency charging and welding. -
Hi Guy, I was back on site last weekend. First I noticed that the surge tank had no air in it. We had this filled up to 100psi. I then attached a pressure guage and another ball valve on the outlet of the pump. I ran the pump with 24v batteries, the pump could only get up to 45-50 psi. It would stall after. I also noticed that the pump fails to start with 25v straight from the batteries and only starts when you give push on the crank. Also it runs very slowly even when under no load. (I might think this is due to the lower voltage, but I'm not sure).
Scratching my head at this point on what else to try.
One thought, the water is not very clear and I'm wondering if excess mud going into the piston could be causing too much friction.
Some pictures. -
The surge tank should be 1/2 of the working pressure (per the manual). 1/2 of 163.5 ft = 35 psi. 100 psi is just as bad as no air and this could be the entire problem (on upstroke, pump has to work against the inertia of lots of non-compressible water).
I assume it's a DC motor with brushes. If so, bad brushes or a dirty commutator can cause starting problems and low torque. Would be interesting to know amp draw and volts at the pump just before stalling. Amps would be low with dirty brushes and high with something causing a restriction.
I agree that the battery's < 29V will cause some decrease in max pressure. Thin wires (like I see in the picture) would drop it even further.
There is no possibility to install a larger pulley on the pump (more torque, less GPM)?I am available for custom hardware/firmware development
-
@jonr regarding PSI ok that makes sense. I read in the manual as 1.5 of pressure. 0.5 makes sense. I'll try that.
Amp draw is something a bit harder to test as most multi meters are only rated 10A at the max draw of the pump is 12A.
The pump motor is indeed brushed. This is something we haven't checked though the pump is brand new so not sure what could have happened there.
I thought about a larger pump pully but, then we are playing around with non-standard specs and it feels the pump is just not operating according to it's spechs.
-
I would think you would want the foot valve 12” off the bottom. The cleaner the water the better. All the valves and fittings on the output side of the pump before the check valve are really of no use but to add restriction to flow and can be removed. If you feel you really need the pressure gauge then it can be placed before the check valve as you have it. I see a Square D pressure switch laying on the ground, what purpose does it serve? Also check to see that the “V” belt isn’t over tightened. The electrical fitting sitting on top of the pump should be reinstalled to keep from cutting the wires where they exit the motor. As you know the pump should start without hand cranking. Stalling out would indicate pressure lock or low voltage. Lowering the surge tank pressure may fix that. The system pressure is determined by pumping with all the valves open with water going into the holding tank. If you were pumping against a valve closed after the pressure gauge, that would stall the pump and your pressure reading would give you false information as to the systems pressure.
-
At most, the pressure tank empty pressure should be at (or a bit below) the "on pressure" of the pump. You want to diaphragm to provide pressure/water volume while the pump switch is off (from high to low set point of the pump switch).
-Bill
Near San Francisco California: 3.5kWatt Grid Tied Solar power system+small backup genset -
Bill, I don't think he has a pressure tank, just a 5000L storage tank. I assume he just pumps till the storage tank is full and then turns off the breaker to the pump.
-
Maybe I am missing something:Pressure tank (surge tank) on pump is there. According to dankoff, it comes pre-pressurized. We haven'd added any air into it.If the pump is stalling, it is simply not getting enough voltage/current (wattage) from the array. Or the back pressure is too high for the pump+array configuration.
...
I was back on site last weekend. First I noticed that the surge tank had no air in it. We had this filled up to 100psi. I then attached a pressure gauge and another ball valve on the outlet of the pump. I ran the pump with 24v batteries, the pump could only get up to 45-50 psi. It would stall after.
The pump has a small "surge tank" that is used for "smoothing" the water flow from the physical piston pump (I think).
If just a surge tank, then 50% of average line pressure should be fine.
https://www.solar-electric.com/dasofopipufo1.htmlImportant: Adjust the precharge air properly. You must do this with water exhausted from the tank, so that your water pressure is zero. Then, set the air pressure to 2 or 3 PSI below your cut-in pressure. If you readjust your pressure switch settings, remember to adjust the precharge again. If you plan to use a pressurized system, the pressure tank must be a minimum of 60 gallon size.https://www.solar-electric.com/lib/wind-sun/Solarforce-specs.pdf
https://www.solar-electric.com/lib/wind-sun/Solarforce-battery-AC-install.pdf
It looks like the pump is rated to 80-100 psi maximum (pressure relief valve range).
I see batteries there--Was that just to test the pump, or are batteries permanently installed?
Regarding the LCB:
https://www.solar-electric.com/solar-converters-ppt-16-linear-current-booster.html
https://www.solar-electric.com/lib/wind-sun/PPT_16_D.pdf
Is the LCB set to the correct output voltage selection?
What is the DC voltage at the pump motor under load?
Is the wiring heavy enough to carry upwards of 30 amps (maximum from LCB output) with minimal voltage drop?
If this is 16 mm^2 (not 16 mm diameter) cable at 50 meters (~5 awg @ 165 feet one way run):
http://www.calculator.net/voltage-drop-calculator.html?material=copper&wiresize=1.028&voltage=24&phase=dc&noofconductor=1&distance=165&distanceunit=feet&eres=30&x=91&y=9
Voltage drop: 3.10
Voltage drop percentage: 12.92%
Voltage at the end: 20.9
That long of wire run is costing you ~3 volts drop to the pump... That could certainly raise questions about votlage at the pump and possible cause of stalling at 50 PSI.
Dirty/muddy water will increase wear on the pump--but should not cause it to stall. If your water source allows, can you set up a settling pond pond prior to the pump intake--That will help keep dirt out of the pump (prevent sediment from settling at pipe right/45 degree angles and in the pipe itself.
Sorry if I am getting some of the discussion wrong--I am spending time on moderation too and have skimmed the longer/more complex threads.
-Bill
Near San Francisco California: 3.5kWatt Grid Tied Solar power system+small backup genset -
The surge tank is for the operation of the pump to reduce "hammering" of the piston. I don't think some of the older piston pumps even had them. Wish we could get waynefromnscanada to chime in, but he hasn't posted in a long time. Someday we may be able to take a VR tour of work sites like this... it would sure help clear up the question we all have.
-
Moving the LCB to the pump will allow it to correct for voltage drop over the long wires.
I am available for custom hardware/firmware development
Categories
- All Categories
- 227 Forum & Website
- 135 Solar Forum News and Announcements
- 1.3K Solar News, Reviews, & Product Announcements
- 198 Solar Information links & sources, event announcements
- 895 Solar Product Reviews & Opinions
- 255 Solar Skeptics, Hype, & Scams Corner
- 22.4K Solar Electric Power, Wind Power & Balance of System
- 3.5K General Solar Power Topics
- 6.7K Solar Beginners Corner
- 1K PV Installers Forum - NEC, Wiring, Installation
- 2.1K Advanced Solar Electric Technical Forum
- 5.5K Off Grid Solar & Battery Systems
- 428 Caravan, Recreational Vehicle, and Marine Power Systems
- 1.1K Grid Tie and Grid Interactive Systems
- 652 Solar Water Pumping
- 815 Wind Power Generation
- 624 Energy Use & Conservation
- 617 Discussion Forums/Café
- 310 In the Weeds--Member's Choice
- 75 Construction
- 124 New Battery Technologies
- 108 Old Battery Tech Discussions
- 3.8K Solar News - Automatic Feed
- 3.8K Solar Energy News RSS Feed