correct inverter size
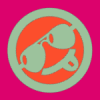
Comments
-
Yes, your inverter must be 24v with a 24v battery bank. Your inverter must be 12v for a 12v battery bank.
I always have more questions than answers. That's the nature of life. -
And, if you have a much higher panel/array voltage than battery bank (i.e., >20 Volts Vmp for a 12 volt battery bank), then you should have an MPPT (maximum power point tracking) solar charge controller to efficiently take the "high voltage/low current" of the array and efficiently down convert to the low voltage/higher current to charge the battery bank.
A PWM (pulse width modulated) solar charge controller works well with smaller solar power systems and "correctly matched" panel voltage to battery bank voltage (such as Vmp-array ~ 17.5 volts to 12 volt battery bank).
Otherwise, as Marc, says... The Inverter only "cares" about the battery bank voltage itself.
You can run into other "design issues" such as having too large of AC inverter (and too large of AC loads) with too small of solar array and/or too small battery bank. If you have poor sun (too far north/south, poor weather, shading from trees/buildings/etc.) can also greatly reduce solar power harvest and delivery.
If you wish, tell us more about your needs. Average Watts (average power), amount of Watt*Hours per day (total energy used per day), location (hours of sun per day), battery bank sizing (or expectations such as 2 days of stored energy to support bad weather, etc.)... And the type of battery bank (i.e., "cheap" flooded cell lead acid, Li Ion/LiFePO4 for RV use, etc.)....
Most folks underestimate their loads and overestimate how much energy a solar system can supply in a day. And AC inverters are "cheap" while battery banks, solar panels, solar charge controllers all quickly add up in price.
-BillNear San Francisco California: 3.5kWatt Grid Tied Solar power system+small backup genset -
Thx for the prompt responses. My panels are used Siemens SM110-24P's and I am starting out with just 2 but could expand to 3 or 4 over time. 110 watts per panel, 3.15 amps, rated at 35V. I went with a Renogy Rover 40 amp MTTP 12V/24V DC input thinking I need at least 35amp MTTR if I go to 3 panels, plus it handles the 24v to 12V difference. Inverter is a 12V Renogy 3000W Ren, hence based on answers to my original question it sounds like I will be fine with that. Will start with a two 100ah LifePro4 Lithium battery bank series connected. Remote camp in Maine, running 2 circuits with 2 lights per circuit, and and 3-4 outlets per circuits that won't be running much other than a TV and recharging phones and laptop. Because the camp is remote I can't get in there to see fridge specs until snow is gone but hope to run fridge electric at least some of the time (it runs propane or electric). Will hang panels at a 44 degree angle.
If you see any red flags with my set up please share. Lots of information to learn with this. Thx again -
A fridge that will run on 12 volts or propane usually has a heating element to run it from electricity. These are notoriously inefficient and would require probably 2kw of panels to run this type of fridge for any length of time.
Keep the fridge running on propane or expect to spend a LOT more money to run it from solar.Island cottage solar system with appriximately 2500 watts of panels, 1kw facing southeast 1.3kw facing southwest 170watt ancient Arco's facing due south. All panels in parallel for a 24 volt system. Trace DR1524 MSW inverter which has performed flawlessly since 1994. Outback Flexmax 80 MPPT charge controller four 467A-h AGM batteries. Insignia 11.5 cubic foot electric fridge 1/4hp GSW piston pump. My 31st year. -
awesome info on the fridge. I will keep propane. Also appreciate you showing your set up in the footer of your note. I will consider facing panels in two different directions. Camp location is heavily wooded so appropriate setup to max sunlight will take some time. Thx
-
The best thing to do... Get a Kill-a-Watt (or similar brand) type meter for measuring AC power/energy usage and a DC AH/WH meter for the DC side (if you have much in the way of DC):
https://www.amazon.com/kill-a-watt/s?k=kill-a-watt
https://www.amazon.com/s?k=dc+current+voltage+amperage+power+energy+panel+meter&sprefix=dc+current+voltage
And measure your daily loads and appliance draws.
Just to give an idea of what a 400 Watt (solar panel) system can supply. Pick Quebec City as near to up state Maine, fixed array facing south:
http://www.solarelectricityhandbook.com/solar-irradiance.htmlQuebec City
Measured in kWh/m2/day onto a solar panel set at a 43° angle from vertical:
Average Solar Insolation figures
(For best year-round performance)
Note that lithium Ion battery bank generally cannot be charged or (heavily discharged) much below 40F (check mfg. specifications for your battery). Toss the bottom 3 months (dead of winter, need genset to make up for poor sun conditions):Jan Feb Mar Apr May Jun 2.55
3.61
4.46
4.70
4.59
4.76
Jul Aug Sep Oct Nov Dec 4.64
4.66
4.02
2.95
2.21
2.04
- 400 Watts * 0.61 Li Ion off grid AC power system eff * 2.95 hours of sun per day (October) = 719 Watt*Hours per day October "break even" harvest
- 6 x 10 Watt LED lamps x 5 hours per day = 300 WH per day lighting
- 3 x 10 WH per day cell phones = 30 Watt*hours per day for phone charging
- 20 Watt LED TV * 5 hours per day = 100 WH per day TV
- 719 WH harvest - 300 - 30 - 100 = 289 WH per day for laptop
- 289 WH per day laptop / 30 Watt laptop draw = 9.6 hours per day laptop usage
More or less, for "base loads" (loads you must use say lighting and cell phone) plan on using 50% to 65% of daily predicted harvest. And "optional loads" such as TV and laptop for entertainment--Cut back on in poor weather (or run small backup genet).
Conservation is also important here too... For example, you can get 12/24 VDC LED bulbs and fixtures from Amazon/web and save the losses of an AC inverter. 60 Watts of LED lightning may be more than you need--A few 5 Watt spot lights for table/work areas is enough. For a laptop just cruising the web--A cheap ChromeBook at 10 Watts or less vs a 30+ Watt for a "gaming/higher end" laptop.
Anyway... Some suggestions... Always measure your loads. Nameplate numbers are usually not very helpful and the hours per day is important too. If you are going with 100-200 watts of solar--That is going to be some really reduced energy usage.
-BillNear San Francisco California: 3.5kWatt Grid Tied Solar power system+small backup genset -
Wow, great info. Very much appreciated. Couple more questions/ comments:
-- help me understand panel voltage better. My panels are 24 volt panels per the online specs. But it reads as follows on the back of the panel: Max Syst. : Open Ckt Voltage 600V, Open Ckt 43.5V. Rated 35V. Not sure what all this means as compared to it being a 24V panel....I have been assuming the panel generates 35V's - is that correct? or is it a 24V?
-- Wire sizes - Before understanding this better I went out and bought several 10 AWG cables. Since then I have tried a few wire size calculators and I'm thinking 10 AWG may be too large. Calcs ask for amps, volts, and cable length. I have been using 3.15 amps because I understand that is constant despite how many panels you have (110 watts, 3.45 short crkt, 3.15A Rated). Using 70V assuming it is 35 x 2 due to two panels, and I am using 20 feet for now. They come back with 16 AWG which seems light...
-- Also on cable sizes - if you went with a larger cable (10 awg vs 16 awg for example), does that significantly reduce my charging power and duration to charge?
-- MC4 connectors are a one size fits all cable sizes, correct?
-- Using 10 AWG wire to connect my batteries together in series. Sound OK?
-- Totally missed the temp on the batteries. Mine rate at 32-122F charging and -4-140K Discharge. But the pro is I don't get out there much past November and plan was to take them home at end of system. I went back and forth on battery types and missed this.....
-- Sounds like I will need more power in my array based on my usage, though laptop use will be minimal and TYV use very minimal. But I want to get the two panel setup working and expand from there (I have 4 more panels).
Thanks again. You all have been great -
You are very welcome. All we ask is you, perhaps, post your final system design (pictures, drawings, sizing, etc.) and let us know how it is working for your needs and any lessons learned. That way we can all learn a bit more.
Your questions:
-- help me understand panel voltage better. My panels are 24 volt panels per the online specs. But it reads as follows on the back of the panel: Max Syst. : Open Ckt Voltage 600V, Open Ckt 43.5V. Rated 35V. Not sure what all this means as compared to it being a 24V panel....I have been assuming the panel generates 35V's - is that correct? or is it a 24V?
More or less, a "24 volt" panel does not mean much in our world. The "original" specifications for solar arrays were:- "12 volt" array => Vmp~17.5 volts
- "24 volt" array => Vmp~35.0 volts
- "48 volt" array => Vmp~70.0 volts
Silicon cells, their voltage (Voc--Voltage open circuit, and Vmp--Voltage maximum power) are rated at 25C/77F under an "artifical sun" for a few seconds "flash" mfg. quality test. As cells/panels get hot, their output voltage falls (a "hot panel" will see Vmp fall to around 80% of "standard test conditions" "name plate/marketing voltage". Or--As panels get hot, the Vmp=17.5 * 0.80 temp derating=14 volts (desert, full sun, hot day, no wind--worst case conditions) and you need ~14-15 volts to charge a "hot" 12 volt battery bank (lead acid battery charging temperature falls as they get "hot" too).
That is how "12 volt" panels and their kin (24/48 volt panels) got their "original" naming.
Now, probably, the vast majority of solar panels are made for the "Grid Tied" inverter market (homes, solar farms, etc.). And since they connect to MPPT based GT inverters, there is no "standard" voltage requirement... It can run from 100 volts to near a 1,000 volts for a solar panel string today...
For that Vmp=>Battery voltage match--In the olden days were PWM (pulse width modulated) charge controllers... Basically an On/Off transistor (or even relay in the very old designs). So to get the most efficient use of solar panel power with PWM controllers--That is the "12 volt panel" with the "12 volt battery bank" match.
Today, almost all off grid systems use MPPT type (maximum power point tracking) solar charge controllers. These are digital switching power supplies (inductors to store switching energy) that can take high voltage/low current from the array and efficiently down convert to low voltage/high current to charge the battery bank. These controllers can take a wide range of input voltage (brand and model dependent)... From 18 volts to 110+ Vmp-array to even 400+ Volts Vmp-array for some controllers. The computer controlled switching power supply (MPPT solar charger) is sort of like the "variable AC Variac" transformers of the AC power world.
The 600 or 1,000 VDC max voltage rating is the maximum working voltage that panel can be put in series with other panels (Voc-array maximum).
Solar panels are "current sources", not "batteries" in the electrical engineering sense... You can read about solar panels and their electrical properties here (practical discussion, not a materials study of doped silicon):
https://forum.solar-electric.com/discussion/5458/two-strings-in-parallel-with-unequal-string-voltages
-- Wire sizes - Before understanding this better I went out and bought several 10 AWG cables. Since then I have tried a few wire size calculators and I'm thinking 10 AWG may be too large. Calcs ask for amps, volts, and cable length. I have been using 3.15 amps because I understand that is constant despite how many panels you have (110 watts, 3.45 short crkt, 3.15A Rated). Using 70V assuming it is 35 x 2 due to two panels, and I am using 20 feet for now. They come back with 16 AWG which seems light...
The Imp (current maximum power) is at rated sunlight (noon sun, panel pointing at sun, clear day, 1,000 Watts per sq meter)--Imp does rise (a little bit) as panel temperature rises (but is usually ignored because it is so small of rise). Isc (short circuit current) is used to ensure that wiring is heavy enough/fused correctly to ensure that the cables (and panels) do not catch fire with a "dead short".
Your are correct, the 100% sun Imp is constant as you add panels in series (1/2/3/4--10/etc.). However when you add panels (or strings of panels) in parallel, the Imp of each string adds together. 2 parallel strings, then 2*3.15Amps Imp=6.30 amps Imp-array, etc.).
And when you put 3 or more strings in parallel, you usually use a "combiner box" which has one circuit breaker/fuse per string. This because the "series fuse rating" is such that when you have two or more panel strings feeding a "shorted panel/string", those can "over current" the shorted panel--Hence the series fuse/breaker in each string.
When sizing wire for the array (or anything)--Two questions. The first is the total max continuous current--Sizing the wire/breaker if needed, to support that current. You should use Isc for wiring/fusing the wiring. I like to start with the NEC (National Electrical Code) simplified AWG vs Current vs Insulation rating:
https://lugsdirect.com/WireCurrentAmpacitiesNEC-Table-301-16.htm
For current rating, 16 AWG is "OK" for 3.xx amps with high temperature insulation. For most jobs, suggest a minimum of 14 AWG--Common house wiring. Easy to get, relatively strong, easy to terminate.
And there is sizing for voltage drop... Here is where it gets confusing. PWM controllers--Nominally Vmp~17.5 volts and you want around 1% to 3% max voltage drop:- Vmp 18v * 0.01 = 0.18 volt drop
- Vmp 17.5v * 0.03 = 0.525 volt drop
With MPPT type controllers, you can pick a higher Vmp-array voltage with 2-4-whatever panels in series. A) this reduces current flow so you can use smaller AWG cable andthe reduced current flow means less voltage drop and "more allowed" voltage drop--Which saves a lot on copper cable costs...
PWM controllers generally a few 10's of feet from controller to array--Or the cables get expensive (lots of copper). With MPPT controllers, roughly, you can go upwards of 100's of feet from array to controller with "reasonable sized cables"--Something like 1/8th the cable costs vs a "low voltage" array.
I use a simple voltage drop calculator to estimate the voltage drop. Say 40 feet, 3.15 amps, and 2 panels in series for Vmp~70 volts. Using 14 AWG copper wire:
https://www.calculator.net/voltage-drop-calculator.html?necmaterial=copper&necwiresize=0&necconduit=pvc&necpf=1&material=copper&wiresize=0.4066&resistance=1.2&resistanceunit=okm&voltage=70&phase=dc&noofconductor=1&distance=40&distanceunit=feet&eres=3.15&x=58&y=23&ctype=necResult
Voltage drop: 0.78
14 AWG cable for decent wire run length.
Voltage drop percentage: 1.12%
Voltage at the end: 69.22
If same with 2 panels in parallel for Vmp-array 35 volts and 6.30 amps:
https://www.calculator.net/voltage-drop-calculator.html?necmaterial=copper&necwiresize=0&necconduit=pvc&necpf=1&material=copper&wiresize=0.4066&resistance=1.2&resistanceunit=okm&voltage=35&phase=dc&noofconductor=1&distance=40&distanceunit=feet&eres=6.3&x=50&y=31&ctype=necResult
Voltage drop: 1.57
Voltage drop percentage: 4.48%
Voltage at the end: 33.43And if done with "12 volt panels" in parallel--This drop would have been even "worse".
-- Also on cable sizes - if you went with a larger cable (10 awg vs 16 awg for example), does that significantly reduce my charging power and duration to charge?
Depends on your array--But with your panels and MPPT controller--You will not see much change... You have to do an exact design, then run the check--But it would look like this:
- P=V*I = 0.78 volt drop * 3.15 amp string current = 2.5 Watts "lost to voltage drop" vs 200 Watt array
For battery bank to AC inverter, you want a maximum of 0.5 volt drop in that wiring (inverters can draw lots of current)--And short+heavy cable is required here too (most inverter and controller manuals talk about DC wiring requirements).
-- MC4 connectors are a one size fits all cable sizes, correct?
MC4 to MC4 connection--All "same size".
HOWEVER, the specific connector housing and "pin+socket" are dependent on wire AWG and insulation thickness--For example:
https://www.solar-electric.com/lib/wind-sun/Multi-Contact-Specs.pdf
And "easy " method to address the MC4 connections... Buy a male/female cable and cut it in 1/2 -- To connect from your array to your combiner box/home run cables to your battery shed...
https://www.solar-electric.com/search/?q=mc4
-- Using 10 AWG wire to connect my batteries together in series. Sound OK?
Need to know more about your battery bank--I thought 2x 12 volt batteries in parallel--But you said 2x XX volt batteries in series???
Anyway... You have a 3,000 Watt AC inverter planned. The maximum current for such an inverter would be:- 3,000 Watt * 1/0.85 AC inverter eff * 1/10.5 volt battery cutoff = 336 Amps max continuous 12 volt battery bus current
A Typical 100 AH Li Ion battery will supply something like 60-100 Amps continuous (just a wild guess).
10 AWG to wire batteries together--Not near heavy enough as I understand your system... Even the battery bank is probably "too small" to run a 3 kWatt AC inverter at "full tilt".
-- Totally missed the temp on the batteries. Mine rate at 32-122F charging and -4-140K Discharge. But the pro is I don't get out there much past November and plan was to take them home at end of system. I went back and forth on battery types and missed this.....
Lead acid batteries are pretty nice for "cold" (sub freezing) applications. Li Ion rechargeables are great for moderate to hot climates. "Heated batteries", insulated battery boxes, etc. are typical solution... Root cellars, ground contact battery boxes, etc. can help moderate temperatures too.
-- Sounds like I will need more power in my array based on my usage, though laptop use will be minimal and TYV use very minimal. But I want to get the two panel setup working and expand from there (I have 4 more panels).
A 200 AH @ 12 volt battery bank will supply (Lithium)--Note I like to plan for 70% planned discharge, but as others here will point out, they can cycle close to 90% capacity--I like to be "conservative":- 200 AH * 12 volts * 0.85 inverter eff * 0.70 battery planned capacity = 1,428 WH of stored 120 VAC energy
For what you talked about--I would be looking at a 300 Watt AC inverter for your system. And use a genset to run a Skill Saw or other tools when needed.
Say you run your system 5 hours in the evening---For two nights, the average AC power usage would be:- 1,428 WH (70% battery capacity) 1/ 10 hours for two nights = 142.8 Watts "average" AC load
We started "in the middle" talking about what you had/wanted in terms of hardware... I suggest starting with your loads and design a system to support those loads with "balanced" power needs, battery bank, solar array, charge controller, AC inverter, etc.
It is difficult for me to "do the math/modeling" your system... Two many moving targets (I can write the equations with 200/300/400 Watt panels, design a system to support a 3 kWatt inverter for use with Skill Saw and Induction Cooktop, etc.) and I think it would be more confusing than helpful.
I think there is enough to start with above... Does this help you "nail down" your power needs and system requirements a bit better?
A 300 Watt Inverter, 400 Watt array, and 200 AH @ 12 volt battery bank is probably a more "balanced" system design.
-BillNear San Francisco California: 3.5kWatt Grid Tied Solar power system+small backup genset -
Do you ,in fact, have MC-4 connectors on these panels? I know the age of these panels would have come with MC-3 connectors. The connectors may have been changed out sometime in their lifetime though.
These are MC-3 connectors.
These are MC-4 connectors.
2.1 Kw Suntech 175 mono, Classic 200, Trace SW 4024 ( 15 years old but brand new out of sealed factory box Jan. 2015), Bogart Tri-metric, 460 Ah. 24 volt LiFePo4 battery bank. Plenty of Baja Sea of Cortez sunshine.
-
Short answer to is #10 wire too large?
Wires are never too large!Island cottage solar system with appriximately 2500 watts of panels, 1kw facing southeast 1.3kw facing southwest 170watt ancient Arco's facing due south. All panels in parallel for a 24 volt system. Trace DR1524 MSW inverter which has performed flawlessly since 1994. Outback Flexmax 80 MPPT charge controller four 467A-h AGM batteries. Insignia 11.5 cubic foot electric fridge 1/4hp GSW piston pump. My 31st year. -
My education continues based on your responses. This is a lot of info to absorb and after spending quite a few hours today reviewing all this I am getting most of it. I have started to play around modeling 500 and 1000 watt inverts because I worry about future wattage growth. I am leaning towards your recommendation for 300 watts while adding another 100 ah battery to my bank. Based on my calcs that gives me a nice increase in usage time before battery depletion. Let me know if this looks correct:Your model - 300 watt inverter with 200ah battery pack:300 Watt * 1/0.85 AC inverter eff * 1/10.5 volt battery cutoff = 33.61 Amps max continuous 12v battery current(used a web calculator to come up with 4.7605 hours, i.e. 30 mins based on the 33.61 amps, 20% depletion and 200 ah)Or200 AH * 12 volts * 0.85 inverter eff * 0.70 battery planned capacity = 1,428 WH of stored 120 VAC energy1,428WH / 300 watt inverter = 4.76 hoursNow to model for a 300 watt inverter with 300ah battery pack:300 Watt * 1/0.85 AC inverter eff * 1/10.5 volt battery cutoff = 33.61 Amps max continuous 12v battery current(used a web calculator to come up with 7.141 hours, i.e. 30 mins based on the 33.61 amps, 20% depletion and 300 ah)Or300 AH * 12 volts * 0.85 inverter eff * 0.70 battery planned capacity = 2,142 WH of stored 120 VAC energy2,142 / 300 watt inverter = 7.14 hoursIf my calcs are correct, it was interesting to see how just increasing the inverter size to 500W with another 100ah battery added to the bank still significantly reduces run time. Drops it to 4.28 hoursMy remaining questions:Q1: Future growth. I worry about such a small inverter if I may want to increase the load down the road. I'm thinkingif I need to increase my inverter size in the future it may not be as simple as just getting a bigger inverter. So backto an earlier question - using a 10 awg from panels to mttp controller does not hurt me much and is still safe, correct?Q1A: I could not translate what this link was showing me. I get the concept, just did not understand the data presented:Q2: Based on your VDC information, am I translating this correctly: Panels are 600VDC, so 600 / 35V rated = 17 maxnumber of serial wired panels in my array? If answer is yes, since I only have 6 of these panels (installing 2 tostart) I am fine VDC panels wise - correct?Q3: For my original wire size question you stated that from MTTP controller to Battery Bank and from Battery Bank to Inverterthat you need to be more careful - meaning 14awg will not suffice. You state "short + heavy" but I would like better clarity onthat - so will the 10 awg cable work for the design I have shared MTTP controller to Battery Bank and from Battery Bank toInverter? Just want to make sure.Q4: MC4 connections. Is it me or are there not a lot on MC4 options out there for 14 awg? Just about everything out thereis 10 awg, and very few of the specs even mention what size awg the MC4 supports. And for those that do show the specsmost are only good for 10 awg to 13 awg. Any recommendations on places to get MC4's that support 14 awg? All this makes me thinkmost DYI people are going with 10 awg MC4's. The link you shared showed 14 awg MC4's but could not find that company on the webQ5: wiring - you mention "14 awg - common house wiring". Your not talking like 12/2 romax wire are you? Thinking not but had to askQ6: inverter draw - do the inverters only draw from the battery bank what they need, or if they are on, even with no load draw, are they still drawing full tilt? I ask because I think all the calcs above are based on full load draw, so assuming I will have longer run times than what is calced.FYI 1: My battery bank will be wired in a series, not parallel.Again thanks for your help and patience. I have learned a ton. Retired 4 years from the IT world. Dusting off a lot ofcobwebs here.
-
saw a bunch of responses after I posted my last response. sorry.
littleharbor2 - my panels just have the screw connections on the back inside a square box. So I will just strip the wire and insert then tighten the screw. On the other ends I will have MC4 connectors - they seem the way to go. See my last (long) post with MC4 remaining questions. Big thing is most on market seem to be AWG 10 and want to know if they rate for down to AWG 14.
706jim - no wire too big. Perfect. Just what I was hoping for.
BB - my last post was primarily to you based on your last response to me.
Thanks again guys.
-
The 300 Watt inverter (600 Watt peak/surge)--Assume you are probably using 100-150 Watts average power (for a cabin or RV environment).
This is a real "work horse" of an inverter for 300 Watts on a 12 volt bank:
https://www.solar-electric.com/morningstar-si-300-115v-ul-inverter.html
No fans, remote on/off, and "search mode" (looking for >~8 Watts of AC load, then turns on to power load).
In the olden days, a "full featured" 300 Watt inverter was rare. These days, Victron and others now have small 12 VDC inverters with lots of features too.
You really need to look at and measure (if possible) your loads (i.e., Kill-a-Watt or similar meter). Because I have zero information on "your power needs"--I was using examples of how much energy you would expect from the hardware you are looking at (i.e., 5 hours a night for 2 nights with XXX AH battery bank @ 12 volts).
It is sort of difficult to use 100% rated output of any energy source (AC inverter, Genset, etc.)... The only sources that come close to doing this is Lighting, Electric Heating, etc. The rest (motors, electronics, computers, etc.) have variable power requirements and possible surge power needs (starting motors, etc.)--So aiming at using an average power (like 100-150 Watts from a 300 Watt inverter) is a more practical model (i.e., a laptop computer may use 8-30 Watts running, but upwards of 65 Watts when charging the internal battery pack).
To "set expectations" for energy usage. That was the model of 5 hours a night, for 2x nights, and using 70% (or 90% if you want) of your lithium battery bank:- 2 nights * 5 hours per evening = 10 hours of power needs (two day "without sun")
- 200 AH Li battery bank * 12 volts * 0.70 of bank capacity = 1,680 WH of bank capacity
- 1,680 WH bank capacity * 0.85 AC inverter eff * 1/10 hours of stored energy usage = 142.8 Watt average AC load support with buffer
But it does show that a 300 Watt inverter is a closer match vs the 3,000 Watt inverter.
Your power needs could be higher (say you want to run a blender)--And a 500 or 1,000 Watt inverter is needed to support the surge load. But you only run the blender for 1 minute--Need larger inverter for peak Watts--But 1 minute of higher load is not much in Watt*Hours (energy) usage:- 500 Watt load * 1 minute runtime * 1/60 minutes per hour = 8.3 Watt*Hours
- 8.3 WH load / 1,680 WH battery bank capacity = 0.005 = 0.5% of bank capacity
It is the smaller loads that run for many hours that use a lot of energy:- 30 Watts lights + 30 Watt computer = 60 Watt load
- 60 Watt load * 5 hours per evening = 300 Watt*Hour loads
Q1: Future growth. I worry about such a small inverter if I may want to increase the load down the road. I'm thinking if I need to increase my inverter size in the future it may not be as simple as just getting a bigger inverter. So back to an earlier question - using a 10 awg from panels to mttp controller does not hurt me much and is still safe, correct?
It is relativity difficult and expensive to "expand" a solar power system or to "allow" for future expansion. You can perhaps "double" a system from 500 Watts to 1,000 Watt inverter. But then you need 2x larger battery bank AH capacity, 2x more solar panels, a second solar charge controller (or a larger controller), etc.
But at some point you need to look at battery bank voltage... A 12 Volt battery bank works OK with 1,200-1,800 Watt inverter. But if you want to go to 3,000+ Watts--Then you really need a 24 volt (or even 48 volt) Battery Bank. Toss the 12 volt inverter, rewire the array to higher Vmp-array voltage, more panels, larger/new solar charge controller (that handles 48 volt bus, etc.)...
If you really think you need a larger system--Design it now and implement it--Perhaps with a smaller array and smaller AC inverter for now if $$$ or other issues limit building "full system now".
It is almost impossible to say that 10 AWG is OK for an expanded system... Too many variables/decisions to be made.Q1A: I could not translate what this link was showing me. I get the concept, just did not understand the data presented:https://lugsdirect.com/WireCurrentAmpacitiesNEC-Table-301-16.htm
I am not sure were your confusion is.... The top row is different insulation types--From "low temperature" to "higher" temperature insulation. High temperature insulation can support more current in the same thickness of copper wire (there are different "classes" of insulation besides temperature--W for wet locations, oil resistance, sunlight resistance, etc.).
Example of discussion about several types of insulation (random example):
https://forums.mikeholt.com/threads/use-2-rhw-vs-thhn.148716/
Yes, this is very confusing.Q2: Based on your VDC information, am I translating this correctly: Panels are 600VDC, so 600 / 35V rated = 17 max number of serial wired panels in my array? If answer is yes, since I only have 6 of these panels (installing 2 to start) I am fine VDC panels wise - correct?Again, this stuff is confusing. And I suggest that we go through the process after the back of the envelope sizing. Once you see how it is done the first time--It makes more sense (I don't want to keep throwing "random/made up" numbers around--That gets confusing too).
No--Your panels are rated at Voc~40 volts @ 77F/25C. And as panels get colder, the voltage goes up:
600 VDC rated voltage / 40 volts Voc = 15 panels "maximum" in series (based on panel max voltage rating)
HOWEVER, you also need to look at the Solar Charge Controller max input rating... For many Vpanel-max is 100-150 VDC. You need to figure out the maximum series panels for the controller rating... Very roughly for a 150 VDC MPPT controller in very cold climate you can put only 2-3 panels in series to ensure you do not exceed Vpanel-max-cold rating of controller.
Some MPPT controller manufactures supply a program to help plan the array--For example here is one of Midnite's:
https://www.midnitesolar.com/sizingTool/index.phpQ3: For my original wire size question you stated that from MTTP controller to Battery Bank and from Battery Bank to Inverter that you need to be more careful - meaning 14awg will not suffice. You state "short + heavy" but I would like better clarity on that - so will the 10 awg cable work for the design I have shared MTTP controller to Battery Bank and from Battery Bank to Inverter? Just want to make sure.
Need exact numbers/product here. How many Amps for inverter, solar array, charge controller, AC inverter, etc...
In general, the solar array and Charger to battery bank wiring is "smaller AWG". Battery bank to AC inverter is typically "much heavier" AWG cable. There is no "generic" right answer. Details matter.Q4: MC4 connections. Is it me or are there not a lot on MC4 options out there for 14 awg? Just about everything out there is 10 awg, and very few of the specs even mention what size awg the MC4 supports. And for those that do show the specs most are only good for 10 awg to 13 awg. Any recommendations on places to get MC4's that support 14 awg? All this makes me think most DYI people are going with 10 awg MC4's. The link you shared showed 14 awg MC4's but could not find that company on the web
Yes, there are lots of limitations out there. You might make 10 AWG connections between solar panels--But only need 14 AWG cable run back to the charge controller (using a J-Box and wire nuts or crimp connectors to transition from 10 AWG to 14 AWG).
If you are OK with 10 AWG the whole way--Great. If you are cost sensitive and want to use wire that is 1/2 or 1/3 the cost--Then transition to 14 AWG is better for you... Just part of the design process. I was using 10 vs 14 AWG to show that "higher voltage" arrays allow you to use smaller wiring. Again, it is better that we do a design for your system--And not a "generic" answer--Which sometimes just confuses the issue.
Q5: wiring - you mention "14 awg - common house wiring". Your not talking like 12/2 romax wire are you? Thinking not but had to ask
There is 14/2 wiring too... But Romex is not allowed to be used outside (in sunlight). You need to put cable in conduit or use UV rated wiring.
You can run into other issues too... Exposed UV rated insulation is not rodent proof. If you have problems with little animals and sharp teeth--Then you may want to run your wiring in metal conduit.
Q6: inverter draw - do the inverters only draw from the battery bank what they need, or if they are on, even with no load draw, are they still drawing full tilt? I ask because I think all the calcs above are based on full load draw, so assuming I will have longer run times than what is calced.
You are correct--AC inverters draw DC current/power only based on the actual AC loads (with some conversion losses).
However, an AC inverter does draw some power to run the electronics/switches even if there are no AC loads. Also known as Tare Losses.
A small 12 volt 300 Watt AC inverter may draw 6 Watts just being turned on and no loads.
A large 4 kWatt inverter may draw 20-40 Watts just turned on.
For the most part, we sort of "bury" the Tare Losses in the 85% AC inverter efficiency.
But if you have a 4 kWatt inverter with 40 Watts of Tare Losses, and running a 30 Watt computer... The inverter will draw >70 Watts from the battery bus... This is where on a smaller system the 300 Watt inverter is more efficient... 30Watt load + 6Watt Tare = 36 Watts from DC battery bus.
Yea--I kind of get a bit lost in the details too... Your batteries in series vs parallel--12 volt or 24 volt battery bus, etc.... Answering not just your questions but other posters too. I am sorry about that. Some times get lost in "your system details" vs more open Q&A about "what if".
-BillNear San Francisco California: 3.5kWatt Grid Tied Solar power system+small backup genset -
prtrc said:saw a bunch of responses after I posted my last response. sorry.
littleharbor2 - my panels just have the screw connections on the back inside a square box. So I will just strip the wire and insert then tighten the screw. On the other ends I will have MC4 connectors - they seem the way to go. See my last (long) post with MC4 remaining questions. Big thing is most on market seem to be AWG 10 and want to know if they rate for down to AWG 14.
706jim - no wire too big. Perfect. Just what I was hoping for.
BB - my last post was primarily to you based on your last response to me.
Thanks again guys.
2.1 Kw Suntech 175 mono, Classic 200, Trace SW 4024 ( 15 years old but brand new out of sealed factory box Jan. 2015), Bogart Tri-metric, 460 Ah. 24 volt LiFePo4 battery bank. Plenty of Baja Sea of Cortez sunshine.
-
What tools are folks using to draw up their designs? Free is better (at least to me). Thx
-
BB - digging deeper on this:
"HOWEVER, you also need to look at the Solar Charge Controller max input rating... For many Vpanel-max is 100-150 VDC. You need to figure out the maximum series panels for the controller rating... Very roughly for a 150 VDC MPPT controller in very cold climate you can put only 2-3 panels in series to ensure you do not exceed Vpanel-max-cold rating of controller."
Due to the voltage of my current panels being what they are, if I want to add more panels to either current design or in the future, I think the better solution is to wire in parallel rather than series. This will allow me to leverage a lower cost MPPT controller (Renogy RVR-40 at 100 VDC is what I already purchased) that will run well below the 100 VDC of that controller. 3 panels would be <10 apps, so theoretically with my controller I could expand my panels to 12 (though unlikely). Also parallel has the benefit of if one panel has reduced performance (malfunction or one in the shade while others in sun for example) the others are not impacted. Make sense? Any other items to consider - like cold impact to parallel wired solution, or any impacts to a 300 watt inverter solution via parallel wiring and adding adding a 3rd panel?Additional MC4 question - while looking a many random solution design diagrams today throughout various URL's I noticed that the positive wires coming out of panels of a parallel wired solution have a additional MC4 type "connector" between the male positive wire from the panel and the branch connectors. What are those and why are they needed? Random example:
https://www.explorist.life/how-series-vs-parallel-wired-solar-panels-affects-amps-and-volts/I know I started in the middle (did not size my power needs first) but I am trying to understand how all the really pieces work. If I sized my load first got help with a design based on that I would have had a working solution and called it good. But I would not have learned half of what I have so far. Though answers to my questions have lead to multiple additional questions, I am learning a lot.
What tool do you use for design diagrams? Looked around for free ones but did not have a lot of luck. I was a huge Visio guy throughout my IT career, but it is a pricy solution that needs additional add ins for solar objects. Would like to find something free :-)
Thx
-
Working backwards...
I have been too long out of engineering schematic entry... The tools I used to use we made the "objects" (connectors, electronic blocks, chips, etc.) and them wired them together with "live" wire/bus connections. It was very neat because you could move the objects around the page and the wires/busses would stretch/contract/redraw to keep the "connection end points". Could turn out a lot of pages of schematics very quickly once the the objects were created.
Most drawing packages, if you move "something" (a solar panel, charge controller, etc.), you end up having to redraw the interconnects because they did not "anchor" to the objects.
Where I would start:
https://duckduckgo.com/?q=free+schematic+capture+software&ia=web
Others here may have some suggestions. Or just any drawing package and it probably works OK.
Regarding "starting in the middle"... As long as you are happy. It is difficult to figure out the "level of confusion" I/we may be causing with some of these replies.
I think the MC4 odd piece out you are looking at is a water/sun proof fuse holder:
https://www.amazon.com/PowMr-M-C-4-Waterproof-Line-Holder/dp/B08C26GJGQ
This gets back to the requirement that (typically) with three or more strings in parallel, you need a series fuse per string to protect against a random short circuit from overheating a solar panel wire/panel itself and starting a fire.
Using MC4 fuses vs Combiner Boxes with fuses or breakers:
https://www.solar-electric.com/lib/wind-sun/PVcombiners-explained.pdf
https://www.solar-electric.com/lib/wind-sun/MNPV3-6-Instructions.pdf
MC4 fuse holders are cheap and easy... Metal combiner boxes with circuit breakers--A bit more "rugged" and you can switch on/off strings with a breaker to test wiring/work on system/etc. MC4 connectors need a too to open, have limited mate/breaker life, and you need a "Y" connector to connect parallel back to on wire to charge controller. And if you have a lot of parallel panel strings, may have issues trying to use all MC4 "Y" back to single wire (i.e., >10 AWG cable needed?)..
Regarding connecting/configuring a solar array. Again details matter. Need panel Voc/Vmp/Isc/Imp numbers, the minimum ambient temperature for your area, and the max Vpanel input for the charge controller.
And the details matter department. Matching array configuration to controller configuration. Say you have a 43 Voc / 35 Vmp / 8.22 Isc / 7.87 Imp panel (275 Watt panel) / 24 volt battery bank and you have a 0F minimum ambient temperature. Using the Midnite string tool, a quick check yields:
https://www.midnitesolar.com/sizingTool/index.phpPV Array Rated PV Array Power: 1100 Watts Anticipated Array Power @ 104F: 1026 Watts Rated PV Array Current: 15.74 Amps Battery Charging Current @ 28.8 V: 38.2 Amps VMP (Maximum Power Point Voltage) : 70 Volts VOC (Open Circuit Voltage): 86 Volts VMP @ 0 F°: 83.4 Volts VOC @ 0 F°: 98.2 Volts
For a 2x series by 2x parallel, you get very close to the 100 VDC Vpanel max at 0F...
I used a 24 volt battery bank and 104F max ambient we get 70 Volts Vmp-hot... That will work for 12/24/48 VDC battery bank.
Each panel variation (brand/model/voltages/etc.) needs to be "double checked" that all specifications/controller requirements are met.
-Bill
Near San Francisco California: 3.5kWatt Grid Tied Solar power system+small backup genset -
BB - Thanks again for the continued education and patience. Your responses concerning the MC4 fuses is leading me towards using a combiner box instead of a MC4 fuse set up. I am getting close. Next set of questions: Q1: Combiner boxes. Much like you need to check to make sure your PV's voltage is not too high for a specific MPPT based on it's VDC, I assume you need to make sure the combiner box can handle the DC voltage into it as well. For example here are specs from a random combiner box: # Max Connection PV Array: 4 Max input current of single PV array: 10A Total Input current of PV Array: 40A Max input voltage of single PV Array: 250V Max output voltage: 250V Operational Temp: -30c to 70c/-22f to 158f Understanding details matter, my panels are 100W/600V/43.5V Voc/35V Imp/3.45a Isc/3.15 Imp) panels. Q1a - Is the combiner box basically equivalent to a parallel-only wired design? I am thinking yes based on the current figures above (total input current is 10a x 4 = 40a) Q1b - Based on my panels (above) is the combiner "max input voltage of single PV array" based on 1) the Voc (43.5) which is below 250V, or (I am thinking this assuming Q1a answer is yes) 2) the total of all panels Voc - which if two panels would be 43.5Vx2=87V which is still below 250v, or 3) Panels Max Sys open circuit Voltage, 600V? - in which case would be too high Q2: Series Modules vs Parallel Strings. It gets confusing because my understanding is when you connect/wire PV's together it is called "stringing" PV's together. So if you connect/wire just 2 PV's together in Parallel I would think you would have no Modules in Series so "# of Modules in Series" calc value would be set to 0. And 1 string of two PV's wired together in parallel so "# of Parallel Strings" calc value would be set to 1. But the calc can't have a 0 value set for either PV Array parms. The easiest way for me to better understand the correct values to enter is to ask what values I need to plug into the Midnight calculator for "Number of modules in a Series" and "Number of Parallel Strings" based on a couple example configurations. FYI - I have a good understanding of the mechanics of actually wiring PV's together (series or parallel or series/parallel), but obviously not the science behind it hense my question. Config #panels Wiring between panels # modules in a Series # parallel Strings 1 2 Parallel 1 2 <== my guess please confirm 2 2 Series 2 1 <== my guess please confirm 3 4 Series/Parallel 2 2 <== from you previous response example Q3: Based on the above two questions answers (Q1a = yes, Q1b = 1, Q2 = correct as depicted) I am good with the random combiner box based on specs listed above and the 40a MTTP at 100VDC. Thanks
-
Sorry formatting on previous post all failed.
Let me try this again: BB - Thanks again for the continued education and patience. Your responses concerning the MC4 fuses is leading me towards use a combiner box instead of a MC4 fuse set up. I am getting close.
Next set of questions: Q1: Combiner boxes. Much like you need to check to make sure your PV's voltage is not too high for a specific MPPT based on it's VDC, I assume you need to make sure the combiner box can handle the DC voltage into it as well. For example here are specs from a random combiner box:
# Max Connection PV Array: 4 Max Input current of single PV array: 10A Total Input current of PV array: 40A
Max Input Voltage of single PV Array: 250V Max Output Voltage: 250V Operational Temp -30c-70c -22f-158f
Understanding details matter, my panels are 100W/600V/43.5V Voc/35V Imp/3.45a Isc/3.15 Imp) panels.
Q1a - Is the combiner box basically equivalent to a parallel-only wired design? I am thinking yes based on the current figures above (total input current is 10a x 4 = 40a)
Q1b - Based on my panels (above) is the combiner "max input voltage of single PV array" based on 1) the Voc (43.5) which is below 250V, or (I am thinking this assuming Q1a answer is yes) 2) the total of all panels Voc - which if two panels would be 43.5Vx2=87V which is still below 250v, or 3) Panels Max Sys open circuit Voltage, 600V? - in which case would be too high
Q2: Series Modules vs Parallel Strings. It gets confusing because my understanding is when you connect/wire PV's together it is called "stringing" PV's together. So if you connect/wire just 2 PV's together in Parallel I would think you would have no Modules in Series so "# of Modules in Series" calc value would be set to 0. And 1 string of two PV's wired together in parallel so "# of Parallel Strings" calc value would be set to 1. But the calc can't have a 0 value set for either PV Array parms. The easiest way for me to better understand the correct values to enter is to ask what values I need to plug into the Midnight calculator for "Number of modules in a Series" and "Number of Parallel Strings" based on a couple example configurations. FYI - I have a good understanding of the mechanics of actually wiring PV's together (series or parallel or series/parallel), but obviously not the science behind it hence my question.
Config #panels Wiring between panels # modules in a Series # parallel Strings
1 2 Parallel 1 2 <== my guess please validate
2 2 Series 2 1 <== my guess please validate
3 4 Series and Parallel 2 2 <== you provided in previous response
Q3: Based on the above two questions answers (Q1a = yes, Q1b = 1, Q2 = correct as depicted) I think I am good with the random combiner box based on specs listed above and 40a MTTP at 100VDC.
Thx -
Thoughts?
-
Next set of questions: Q1: Combiner boxes. Much like you need to check to make sure your PV's voltage is not too high for a specific MPPT based on it's VDC, I assume you need to make sure the combiner box can handle the DC voltage into it as well. For example here are specs from a random combiner box:
# Max Connection PV Array: 4 Max Input current of single PV array: 10A Total Input current of PV array: 40A
Max Input Voltage of single PV Array: 250V Max Output Voltage: 250V Operational Temp -30c-70c -22f-158f
Understanding details matter, my panels are 100W/600V/43.5V Voc/35V Imp/3.45a Isc/3.15 Imp) panels.
Q1a - Is the combiner box basically equivalent to a parallel-only wired design? I am thinking yes based on the current figures above (total input current is 10a x 4 = 40a)
Yes, checking voltage/current ratings for Combiner box is important... And specifically for fuse/circuit breaker ratings. DC current is "much more difficult" to interrupt vs AC current. So you need to confirm the fuses and/or circuit breakers are rated for the VDC Voltage and AAC rated Amperes.
You may wish to confirm that any additional panels you may purchase in the "near term" are rated for 10 amps or lower series rated fuses/Isc current. Larger panels can have 15 amp rated series over current protection--This may limit you in the future.
With your present 100 Watt @ Vmp=17 volts @ Imp=3.17 amps... You are limited to 4x3.15amps = 12.6 amps total for a 2 series * 4 parallel array. Total wattage ~800 or 880 Watts (8 * 100 watt panels or 8 * 110 Watt panels) for this "4 port" combiner box.
Q1b - Based on my panels (above) is the combiner "max input voltage of single PV array" based on 1) the Voc (43.5) which is below 250V, or (I am thinking this assuming Q1a answer is yes) 2) the total of all panels Voc - which if two panels would be 43.5Vx2=87V which is still below 250v, or 3) Panels Max Sys open circuit Voltage, 600V? - in which case would be too high
I am a bit lost on what controller (40 Amp MPPT type with 100 VDC max panel input?), what battery bank voltage (12 or 24 VDC?).
Since a typical lower end MPPT controller has 100 Vpanel-max voltage--That is well below the 250 VDC rating of the Combiner box... And you need to check the ratings of the circuit breakers... I.e., 10 amps @ 150 VDC or whatever.
Actually I am going to stop making guesses here with "numbers" here ... You are asking specific information but I am not sure/lost about the a) solar panel Vmp/Imp and series fuse ratings, number of panels maximum you wish to use, the MPPT controller Vpanel-max and output current rating, the voltage of your battery bank (12/24 or what)...
Pretty much, for smaller solar power systems, the solar charge controller (MPPT or PWM type) is usually the only "ratings" you have to worry about--And then configure the X series * Y parallel array with "correct" series protection fuse/breaker Amp value per string (if you have 3 or more parallel strings).
Q2: Series Modules vs Parallel Strings. It gets confusing because my understanding is when you connect/wire PV's together it is called "stringing" PV's together. So if you connect/wire just 2 PV's together in Parallel I would think you would have no Modules in Series so "# of Modules in Series" calc value would be set to 0. And 1 string of two PV's wired together in parallel so "# of Parallel Strings" calc value would be set to 1. But the calc can't have a 0 value set for either PV Array parms. The easiest way for me to better understand the correct values to enter is to ask what values I need to plug into the Midnight calculator for "Number of modules in a Series" and "Number of Parallel Strings" based on a couple example configurations. FYI - I have a good understanding of the mechanics of actually wiring PV's together (series or parallel or series/parallel), but obviously not the science behind it hence my question.
Config #panels Wiring between panels # modules in a Series # parallel Strings
1 2 Parallel 1 2 <== my guess please validate
2 2 Series 2 1 <== my guess please validate
3 4 Series and Parallel 2 2 <== you provided in previous response
Stringing the panels together--More or less we talk about panel "strings" (panels connected in series) to add "panel voltages" together. And adding multiple series strings in "Parallel" to add current(s) together.
The X series * Y parallel I would call the array "configuration"... To be honest, I am not in the solar business, so my terms are just basic english/engineering explanations. The "industry/installer" terms may be different (and technical terms are a weakness of mine anyway--I have to be careful not to confuse folks).
If you have two panels in parallel--We still talk about 1 series * 2 parallel... I.e., 1 panel is not "zero" in series--It is 1 in series (itself). Just remember that each panel has something like 36-60-72 individual solar cells in series to make a single panel (each solar cell is has a Vmp of ~0.5 volts--36 cells in series = ~18 vols Vmp-panel).
Yes--Your 1-3 configuration chart is "correct".... 1s*2p, 2s*1p, 2s*2p, etc...
Q3: Based on the above two questions answers (Q1a = yes, Q1b = 1, Q2 = correct as depicted) I think I am good with the random combiner box based on specs listed above and 40a MTTP at 100VDC.
Yes, generically correct... Specific correctness need actual panel+controller+battery bank "numbers".
For a 40 Amp MPPT controller, the maximum/optimum array Wattage would look something like this (always refer to the controller manual for exact requirements):- 40 amps * 14.5 volts charging * 1/0.77 solar panel and controller deratings = 753 Watt array
- 40 amps * 29.0 volts charging * 1/0.77 solar panel and controller deratings = 1,506 Watt array
For anything larger than a "small" system--24 (or even 48) VDC systems tend to be cheaper overall to build out (less current at higher DC voltage, smaller diameter wires. A 40 Amp controller can handle a 2x larger array on a 24 volt bank vs a 12 volt bank, etc...
If your panels are 17.4 volts Vmp--Then 4 panels in series is about the maximum for a 0F ambient temperature array. If it gets colder when you run the solar power system (winter camp)--Then perhaps 3 in series is about maximum.
Note--Depending on the number of panels/size of panels/etc... If you plan on 4 or 8 panels total (>0F)--Then you could have 4s * 1p or 4s * 2p array--And not even need a combiner box (only need combiner box if 3 or more parallel strings for more solar panels).
-Bill
Near San Francisco California: 3.5kWatt Grid Tied Solar power system+small backup genset -
Thanks BB - I think I am there. Only thing remaining for me to do if research combiner boxes more. Tho 10A breakers within the combiner box (per my design) appears to be fine, I will do more research. Can't say thanks enough for you sticking with me on this. Any fatal flaws let me know
-
The breakers in the combiner box, should not be larger in amps, than the Series Fuse spec on the back of the solar panel.
for small panels, 10A breakers seems to be a lot larger than it should be.
3.5A panels should not have much more than a 7A breaker on each.
The combiner box breaker/fuse prevents a damaged panel from sucking power from good panels, and lighting something on fire
Powerfab top of pole PV mount | Listeroid 6/1 w/st5 gen head | XW6048 inverter/chgr | Iota 48V/15A charger | Morningstar 60A MPPT | 48V, 800A NiFe Battery (in series)| 15, Evergreen 205w "12V" PV array on pole | Midnight ePanel | Grundfos 10 SO5-9 with 3 wire Franklin Electric motor (1/2hp 240V 1ph ) on a timer for 3 hr noontime run - Runs off PV ||
|| Midnight Classic 200 | 10, Evergreen 200w in a 160VOC array ||
|| VEC1093 12V Charger | Maha C401 aa/aaa Charger | SureSine | Sunsaver MPPT 15A
solar: http://tinyurl.com/LMR-Solar
gen: http://tinyurl.com/LMR-Lister , -
Thanks Mike. Any leads on a combiner box with the breakers below 10A? Been searching around on the web and smallest amp breaker I can find is 10A which appears to be the standard. Also, any leads on where to purchase the breakers found in combiner boxes? I am assuming you can't swap them out with regular home breakers.
-
Look here, for example:
Midnite Solar MNEPV 150 Volts 7 Amps DC Circuit Breaker | Northern Arizona Wind & Sun (solar-electric.com)
The MNEPV Breakers will fit in the following type of Combiners:
Search results for: 'MNPV' | Northern Arizona Wind & Sun (solar-electric.com)
FWIW, VicOff Grid - Two systems -- 4 SW+ 5548 Inverters, Surrette 4KS25 1280 AH X2@48V, 11.1 KW STC PV, 4X MidNite Classic 150 w/ WBjrs, Beta KID on S-530s, MX-60s, MN Bkrs/Boxes. 25 KVA Polyphase Kubota diesel, Honda Eu6500isa, Eu3000is-es, Eu2000, Eu1000 gensets. Thanks Wind-Sun for this great Forum. -
prtrc said:Thanks Mike. Any leads on a combiner box with the breakers below 10A? Been searching around on the web and smallest amp breaker I can find is 10A which appears to be the standard. Also, any leads on where to purchase the breakers found in combiner boxes? I am assuming you can't swap them out with regular home breakers.
Our host sells them, 7% off sale going on now, you may also want to sign in, sometimes a lower price;
Midnite Solar MNEPV 150 Volts 5 Amps DC Circuit Breaker | Northern Arizona Wind & Sun (solar-electric.com)
Home system 4000 watt (Evergreen) array standing, with 2 Midnite Classic Lites, Midnite E-panel, Magnum MS4024, Prosine 1800(now backup) and Exeltech 1100(former backup...lol), 660 ah 24v Forklift battery(now 10 years old). Off grid for 20 years (if I include 8 months on a bicycle).
- Assorted other systems, pieces and to many panels in the closet to not do more projects. -
Finally have my system functional today after some delays. I have it hooked up here at home as a dry run (did not use a combiner box for now since only 2 panels) , and when the roads dry out I will set up at my remote camp. Thanks for all the input so far from various contributors.
Something did surprise me today when I first connected everything - the amperage seemed much higher from the panels to the controller than I expected. As a reminder my panels are 3.15 A IMP, 3.45 A ISC. I have my panels wired in parallel, so I was expecting 6+ amps at the solar controller. While my panels were in direct 100% sunlight, the controller was showing 12.5+ amps from the panels. I had to run an errand so I disconnected the panels at the connectors, and reconnected on my return. The sun was intermittent at that time (60/40 clouds to sun) so now I'm running around 1.75 amps to the controller from the panels. Voltage is running around 38 (panels are VMP 35 VOC 43.5). I have a second (Charge) and third (Discharge) meter wired after the battery bank and before inverter and it reads basically the same amperage.
Why in direct sunlight was the amperage so high?
BTW - Panels are 10A rated so I have a10A fuse on each + wire coming from the panels. As stated overkill for my current 2-panel set up but I will be expanding the number of panels once at my remote camp.
Thx
Categories
- All Categories
- 228 Forum & Website
- 136 Solar Forum News and Announcements
- 1.4K Solar News, Reviews, & Product Announcements
- 199 Solar Information links & sources, event announcements
- 898 Solar Product Reviews & Opinions
- 256 Solar Skeptics, Hype, & Scams Corner
- 22.5K Solar Electric Power, Wind Power & Balance of System
- 3.5K General Solar Power Topics
- 6.7K Solar Beginners Corner
- 1K PV Installers Forum - NEC, Wiring, Installation
- 2.1K Advanced Solar Electric Technical Forum
- 5.6K Off Grid Solar & Battery Systems
- 428 Caravan, Recreational Vehicle, and Marine Power Systems
- 1.1K Grid Tie and Grid Interactive Systems
- 654 Solar Water Pumping
- 816 Wind Power Generation
- 624 Energy Use & Conservation
- 619 Discussion Forums/Café
- 312 In the Weeds--Member's Choice
- 75 Construction
- 124 New Battery Technologies
- 108 Old Battery Tech Discussions
- 3.8K Solar News - Automatic Feed
- 3.8K Solar Energy News RSS Feed