Proper connections after solar charger
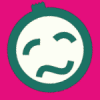
HandymanJoe
Registered Users Posts: 3 ✭
I have 4-100 watt panels wired in parallel to the charge controller, then to the battery bank with connections made. Now where do i connect the heavy wires to the inverter.
Comments
-
Welcome to the forum HandymanJoe,
Here is a quick explination of how to configure a battery bank with two or more parallel strings of batteries:
http://www.smartgauge.co.uk/batt_con.html
From the charge controller to the battery bank, you want the cables (and fuse/circuit breaker) to be (ideally) 1.25x larger than the expected maximum current:- 400 Watts of panels * 1/17.5 volts Vmp array = ~23 Amps expected maximum continous current
- FYI: 400 Watts * 0.77 typical best case current * 1/14.5 volts charging = 21 amps typical best case harvest current
- 23 Amps * 1.25 NEC derating for continuous current = 29 Amps ~ 30 Amp minimum controller to battery bank branch circuit wiring/breaker/fuse ratings.
Typically the heavy current cables are from the battery bank to common +/- connections. The AC inverter typically draws the most current.
Say you have a 400 Watt AC inverter, the maximum current would be:- 400 Watts * 1/0.85 inverter AC efficiency * 1/10.5 volt battery cutoff = 44.8 Amps
Recommend a maximum of 0.5 volts from (12 volt) battery bank to DC input of AC inverter at maximum inverter power.
The simplified NEC (national electric code) cable ratings are:
https://lugsdirect.com/WireCurrentAmpacitiesNEC-Table-301-16.htm
When dealing with solar/electrical--Details matter here... Charging/discharging current. Battery bank AH and Voltage rating (type of batteries too). Length of wiring/cabling, etc.
Fuses and Circuit Breakers are there to prevent your wiring from overheating/catching/setting fires. For "unattended" solar system operation (nobody present), you want to ensure that you are protected against fires/etc.
Many times, fuses are nice because they do not only protect against over current... They give you handy on/off switches too (and many times, breakers are the same price or cheaper than fuses--Especially at higher current ratings).
-BillNear San Francisco California: 3.5kWatt Grid Tied Solar power system+small backup genset -
HandymanJoe said:I have 4-100 watt panels wired in parallel to the charge controller, then to the battery bank with connections made. Now where do i connect the heavy wires to the inverter.Home system 4000 watt (Evergreen) array standing, with 2 Midnite Classic Lites, Midnite E-panel, Magnum MS4024, Prosine 1800(now backup) and Exeltech 1100(former backup...lol), 660 ah 24v Forklift battery(now 10 years old). Off grid for 20 years (if I include 8 months on a bicycle).
- Assorted other systems, pieces and to many panels in the closet to not do more projects. -
Yes that's just what i did. From the 4-100 watt panels are . So i have 2 banks, wired to the cc with #10 wire and #6 going to the input of the bank. The output of the bank to the inverter is #4 welder cable. the circuits from the inverter are #14 house wire. The batteries are wired in 2 parallel banks. they are 600 cca which =s 320 AH if i did the math right. HandymanJoe
-
10 AWG from Charge Controller to Battery bank is OK for current capacity... However, it is a bit on the small side for voltage drop.
For a 12 volt battery bank, for accurate/fastest charging, you want aroun 0.10 to 0.20 volt drop so that charge controller "sees" accurate charging voltage... Just some quick math:- 400 Watt array * 0.77 panel+controller derating * 11/4.5 volts charging = 21.2 volts (more or less) best case charging current
https://www.calculator.net/voltage-drop-calculator.html?necmaterial=copper&necwiresize=2&necconduit=pvc&necpf=1&material=copper&wiresize=0.4066&resistance=1.2&resistanceunit=okm&voltage=14.5&phase=dc&noofconductor=1&distance=2&distanceunit=feet&eres=21.2&x=59&y=21&ctype=necResult
Voltage drop: 0.10
Ideally, 2 feet or less wire run for 0.10 volt drop--Or heavier cable to have less voltage drop.
Voltage drop percentage: 0.70%
Voltage at the end: 14.4
Having 0.2 volt drop is not the end of the world... But you can see that running relatively small 10 AWG cable does severely limit cable run from charger to battery bank.
Following the Inverter installation instructions is always a good start... If you can tell us a bit more about your system (type of battery bank, AC inverter Watt rating, length of cable from battery bank to inverter, etc... We can help a bit more.
Having an AC inverter with a "real" on/off switch of some sort is a big help (turn off when not running AC loads can save "tare losses" from an idle inverter with zero loads)... And if no true on/off function, then a circuit breaker from battery to AC inverter DC terminal is nice.
-Bill
Near San Francisco California: 3.5kWatt Grid Tied Solar power system+small backup genset -
Thanks Bill, I used #10 wire on the panels to the cc cause that what the wired the panels with. The length from panels is 14 ft. The battery bank is 4 12 marine batteries from Costco. The inverter is a 2k inverter name tag gone but has on/off switch. The battery to inverter is 5ft . The +lead from the bb to inverter is fused with a 150 amp fuse. T -lead is not fused. The solar panels are each fused with 30 amp fuses cause that's all #10 wire will carry. Thanks for your help and ideas, i hope i have answered your questions. Handymanjoe
-
HandymanJoe,
It is best if you make your Q&A's here in the forum... We really are not setup to have "wall" discussions as most people do not look/follow them:While 108 VAC is a bit on the low side--It is within the range of 108 to 134 VAC (120 +/- 10%) which (seems to be) the US/North America range.I have my solar array wired and operating. The readout on my CC says 14.7 volts going to the batteries. Now when I turn on the inverter i only get 108 volts from the 110 socket. Have i made a mistake along the line from the panels to the inverter? After spending all this money i don't have a voltage that will run my Dremel. What next? need all the help i can get at this point.
There can be other issues too..- Check the DC input voltage... Low DC input can cause low AC inverter output
- Is your Dremel tool not working? (running slow, not starting/buzzing?)
If this was an MSW (Modified Sine/Square Wave) inverter--There are other issues. MSW inverters will typically read "low" output voltage when using a typical DC voltmeter.
If you have an RMS (Root Mean Square) AC volt meter, they will read lower voltage for an MSW (modified square wave) inverter. RMS or Root Mean Square reading meter--It takes multiple samples of an "arbitrary" wave form (sine wave, square wave, modified square wave) and "integrates" the area under the wave form and gives a voltage that is the equivalent "power" of a DC voltage.
True RMS meters used to be much more expensive, and rarely seen (see Fluke)... Newer meters even down to the $50 level are available these days.
https://www.fluke.com/en-us/learn/blog/electrical/what-is-true-rms
A typical non-RMS reading digital meter simply reads the peak voltage of the sine wave and divides by the square root of 2 to get the RMS equivalent:- 120 VAC * srt(s) = 170 Volts peak
If you connect other loads (lights, drill, etc.) to the inverter, do the other types of loads work at all?
At this point--I am not ready to blame the 108 VAC reading on the inverter as causing your Dremel tool problems.
There are some AC loads that have problems with MSW inverters. The MSW wave form has a "lower peak voltage" than the PSW type. And some power supplies have problems with that lower voltage--Looks like an "AC brownout" condition.
Another issue is that MSW wave forms have lots of "harmonics" (PSW ~ 5% or less total harmonic distortion and MSW have something like 25-30% THD). For transformers, induction motors, and some other AC power devices have problems with the high THD and they can overheat and fail (quickly or over time). Instead of less than 5% THD being converted to heat, and MSW inverter can have 25-30% THD converted to heat (in transformers, induction motors, and such).
There are also (mainly older these days?) tool battery chargers that failed on MSW inverters...
Not to say that all will fail on MSW--Probably 80% of AC loads work fine, and 10-20% can overheat/fail. If you plug in battery chargers and other small electronics & wall transformers, watch their temperature and unplug if they are overheating. And don't use an MSW inverter to power induction motors--Especially those used for refrigerators and freezers (these are "heavily loaded compressor induction motors and are known to "run hot" on MSW).
-BillNear San Francisco California: 3.5kWatt Grid Tied Solar power system+small backup genset
Categories
- All Categories
- 228 Forum & Website
- 136 Solar Forum News and Announcements
- 1.4K Solar News, Reviews, & Product Announcements
- 199 Solar Information links & sources, event announcements
- 898 Solar Product Reviews & Opinions
- 256 Solar Skeptics, Hype, & Scams Corner
- 22.5K Solar Electric Power, Wind Power & Balance of System
- 3.5K General Solar Power Topics
- 6.7K Solar Beginners Corner
- 1K PV Installers Forum - NEC, Wiring, Installation
- 2.1K Advanced Solar Electric Technical Forum
- 5.6K Off Grid Solar & Battery Systems
- 428 Caravan, Recreational Vehicle, and Marine Power Systems
- 1.1K Grid Tie and Grid Interactive Systems
- 654 Solar Water Pumping
- 816 Wind Power Generation
- 624 Energy Use & Conservation
- 619 Discussion Forums/Café
- 312 In the Weeds--Member's Choice
- 75 Construction
- 124 New Battery Technologies
- 108 Old Battery Tech Discussions
- 3.8K Solar News - Automatic Feed
- 3.8K Solar Energy News RSS Feed