Why is there 12v, 24v and 48v? What's the difference?
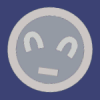
hmongsolar
Registered Users Posts: 6 ✭✭
Do they each do their own uniqe job?
As far as I see, all systems work the same.
100W Solar Panel will charge 12v Battery, using a smaller controller, using cheaper wires, Cheaper inverters.
So why double the battery to make 24v? Why make 4 12v battery into 48v system when you can utilize those 4 batteries and get 400Ah if using a 12v system?
So in all, why do people choose bigger systems vs. 12v when 12v can do the same job?
Can someone explain?
As far as I see, all systems work the same.
100W Solar Panel will charge 12v Battery, using a smaller controller, using cheaper wires, Cheaper inverters.
So why double the battery to make 24v? Why make 4 12v battery into 48v system when you can utilize those 4 batteries and get 400Ah if using a 12v system?
So in all, why do people choose bigger systems vs. 12v when 12v can do the same job?
Can someone explain?
Comments
-
Current, the flow of electrons within a conductor is inversely proportional to the voltage or potential difference, therefore as the voltage increases the current is reduced. To calculate the current for a given load the formula P= V × I would be used, P being power, V being voltage, I being current.
As an example say we had a known load of 1000W, we know the voltage to be used is 12V, we would transpose the formula to I = P / V
or I = 1000 / 12 which would be 83.33 amps.
When the voltage is increased to 24V is I = 1000 / 24 which would be 41.66 amps,
When the voltage is increased to 48V is I = 1000 / 48 which would be 20.83 amps.
Because a conductors current carrying capacity is limited by its cross sectional area, or gauge using a higher voltage allows more energy to be transferred. Let's use a nominal gauge of 10 AWG which is rated at 30A, using the same formula P = V × I
At 12V the power allowable would be 12V × 30A = 360 watts
At 24V the power allowable would be 24V × 30A = 720 watts
At 48V the power allowable would be 48V × 30A = 1440 watts
Therefore it's more economical to use a higher voltage when dealing with higher loads because the conductors and other devices, such as overcurrent protection can be smaller, thus saving in ballance of system costs.
This rationale applies to the charge controller as well, they are rated by current but allowing different nominal voltages, using a low voltage limits the array capacity in the same way as the conductor example above.
When building a system it's the load capacity which determines the most practical nominal voltage, 12V is generally considered suitable for low power systems of 1000W or less.
Batteries follow the same rules, to achieve the current needed for a high power low voltage system, there often needs to be many batteries in parallel which is impractical as it becomes difficult to keep them in ballance leading to premature failure, not to mention the cost of conductors needed to do so.
The same formula P ÷V × I applies to batteries, 12V at 400Ah is 4800W, 24V at 200Ah is 4800W, 48V at 100Ah is 4800W,
This is a simplified explanation which I hope helps you understand, if not ask more questions.1500W, 6× Schutten 250W Poly panels , Schneider MPPT 60 150 CC, Schneider SW 2524 inverter, 400Ah LFP 24V nominal battery with Battery Bodyguard BMS
Second system 1890W 3 × 300W No name brand poly, 3×330 Sunsolar Poly panels, Morningstar TS 60 PWM controller, no name 2000W inverter 400Ah LFP 24V nominal battery with Daly BMS, used for water pumping and day time air conditioning.
5Kw Yanmar clone single cylinder air cooled diesel generator for rare emergency charging and welding. -
Precisely.
Alot of persons would also say it would be nice to have equipment above 48vdc but then there is the safety issue. So yes in short they have their application. -
Couple simple points:
12V is for small, simple systems with typically less than 800 watts of panels.
48V is for full time off gridders - typically using more than 1600 watts of panels.
Wiring runs cooler with less resistance at higher voltage levels. So 48V wiring can be ~ 1/4 the size of 12V wiring. Assuming, for example, that both systems have the same wattage flowing through them.
Also - running eight 6V batteries in parallel (for 48V) is potentially problematic. 48V allows one to run these eight batteries in serial.
I'd like to see a 120V system but do not expect it. It would carry a potentially lethal shock hazard. Anything below 30V is considered "safe". The advantage would be found in efficient wiring and a much cheaper inverter. All the inverter would have to do is convert DC to AC.First Bank:16 180 watt Grape Solar with FM80 controller and 3648 Inverter....Fullriver 8D AGM solar batteries. Second Bank/MacGyver Special: 10 165(?) watt BP Solar with Renogy MPPT 40A controller/ and Xantrex C-35 PWM controller/ and Morningstar PWM controller...Cotek 24V PSW inverter....forklift and diesel locomotive batteries -
softdown said:Also - running eight 6V batteries in parallel (for 48V) is potentially problematic. for 6v in parallel is still 6v, it doubles the ah.
Also - running eight 6V batteries in parallel (for 48V) is potentially problematic. 48V allows one to run these eight batteries in serial.
Hi softdown. i have a question on the above quote; what is problematic with 6v batts / in series for 48volts?
and
i'm not understanding your comment of
can you clarify what i'm not understanding plz.
Reason i ask is> i'm using 6v batts ( eight in total wired in series / parallel) for 5 + years / zero issues. for 24v system.
i'm wanting to rewire to 48 volts one day . when i upgrade to 48 split phase invester /
Thankyou . Neil.
-
I think Softdown made a typo... 8x 6 volt batteries in series is 48 volts.
We have had folks that have used something like 10 or 12 x 12 volt batteries in parallel (and other combinations)--And I try to get people to avoid doing that. Usually they have a source of cheap (or free) smaller AH batteries and try to parallel a bunch of then (or series x parallel) into a large battery bank.
For many reasons, lots of parallel lead acid batteries are not great... Lots of electrical connections, there should be a fuse/breaker per parallel connected string (to keep a short circuit in/around one battery string from being overheated/possible threat of fire from the bunches of other batteries connected in parallel.
Not a lot of people put fuses/breakers on their paralleled battery strings (typically 3 or more parallel strings) because it gets expensive and a pain with all the extra hardware.
Generally, it is better to get larger AH batteries--And there are even 6/4/2 volt batteries (2 volts is a single lead acid cell) and build a single (or 2 or 3 parallel strings if you have to) to get your larger AH battery bank.
Also, for flooded cell lead acid batteries, you need to check the cells for electrolyte levels/add distilled water when needed. Having 60x cells for 10x 12 volt batteries (small AH size--10-80 AH I have seen), vs just getting 100 to 800+ AH cells (or single batteries) and wiring them up in series (only 6 cells to check water levels on).
Anyway--It is easier to deal in specifics (your xx Volts @ yyy AH) battery bank and talk about needs. If you want, start another discussion and we can talk about your system.
-BillNear San Francisco California: 3.5kWatt Grid Tied Solar power system+small backup genset -
Example to think about - let's say you need 600 watts as your goal to run some small items. Using a 12v system the current would be 50 amps(600/12). Using a 24v system the current would be only 25 amps(600/24). Wire can only hold so much current before it heats up and catches fire. Think of a garden hose where massive water needs to push through. The most confusing part is the rating of wire - basically a 4 gauge wire is really thick and is used to connect batteries. 12 gauge wire is a lot smaller.
50 amps of current would need 6 gauge wire(there are charts to help you figure this out). 6 gauge wire is very thick(to allow that much current to flow). It is more expensive and harder to cut, crimp, etc. If you have a long run it will be $$$.
25 amps of current on the 24v would need only 10 gauge which is smaller. You don't have to buy a bunch of expensive tools to work with this wire. It also is much cheaper.
You also need to consider what size inverter you will need. You can't plug anything that heats or cools into a small inverter. Lots of things to consider but hope this helps! -
Kimmerj, welcome to the forum. And I did leave you a note to check the main forum for your moved set of questions.
And, here is a simplified chart of NEC AWG size to nominal max Amps by gauge and insulation types:
https://lugsdirect.com/WireCurrentAmpacitiesNEC-Table-301-16.htm
-BillNear San Francisco California: 3.5kWatt Grid Tied Solar power system+small backup genset
Categories
- All Categories
- 228 Forum & Website
- 136 Solar Forum News and Announcements
- 1.4K Solar News, Reviews, & Product Announcements
- 199 Solar Information links & sources, event announcements
- 898 Solar Product Reviews & Opinions
- 256 Solar Skeptics, Hype, & Scams Corner
- 22.5K Solar Electric Power, Wind Power & Balance of System
- 3.5K General Solar Power Topics
- 6.7K Solar Beginners Corner
- 1K PV Installers Forum - NEC, Wiring, Installation
- 2.1K Advanced Solar Electric Technical Forum
- 5.6K Off Grid Solar & Battery Systems
- 428 Caravan, Recreational Vehicle, and Marine Power Systems
- 1.1K Grid Tie and Grid Interactive Systems
- 654 Solar Water Pumping
- 816 Wind Power Generation
- 624 Energy Use & Conservation
- 619 Discussion Forums/Café
- 312 In the Weeds--Member's Choice
- 75 Construction
- 124 New Battery Technologies
- 108 Old Battery Tech Discussions
- 3.8K Solar News - Automatic Feed
- 3.8K Solar Energy News RSS Feed