Understanding motor help... lock up amps, motor position...
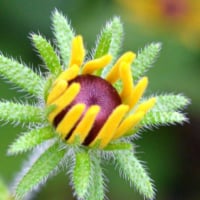
Photowhit
Solar Expert Posts: 6,017 ✭✭✭✭✭
So I bought a project a week ago... I was looking for a lathe chuck and picked up a rather nice lathe (without a motor), chuck and tools for $120 (yes I stole it, not I didn't hold a gun or wear a mask, but had one ready if requested, we just social distanced...)
So I now I want to install a motor. It will take 3/4 - 1.5hp 56C face plate mount motor.
So a inexpensive, 1 hp motor from Automation Direct runs $143, and the listed Lock rotor amps is 80 amps!!! I assume since it has a start up capacitor, my inverter will never see this?

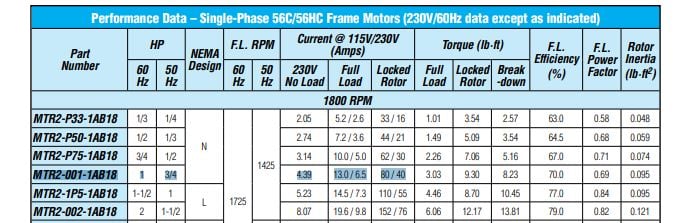
I can also get a 'run capacitor' it says it's to decrease power factor while running, allowing the motor to run more efficiently. Not sure what the savings are, I'll likely be doing mostly the same small stuff/low demand stuff, I'm currently dong on a tiny 350 watt table top lathe. So will a run capacitor help more on the low end or high end of demand?
It specifies that no specific motor orientation is required, since I will mount this with the face plate, I assume if I spin this 45 or 90 degrees and use the mounting bracket to mount an on/off, emergency shut down and reverse speed box that won't be a problem? Here's a picture of a 3000 setup with a DC motor, the speed controller and 3 postion switch for Fwd/Off/Rev is a very Bad position, right at the knee and blocking any pivot and use as an open ended lathe.
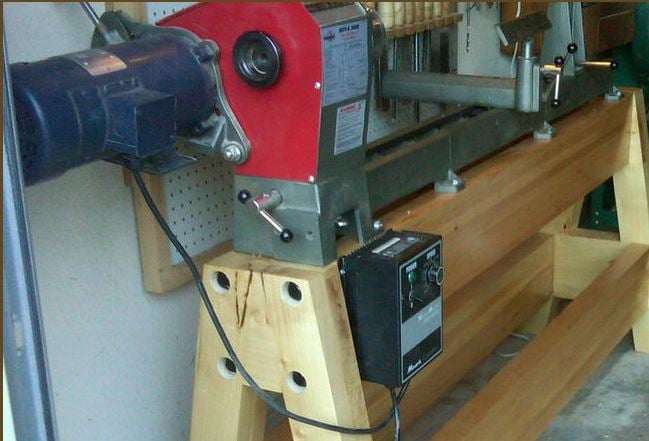
Here's the lathe in original configuration with a switch on the motor, I suspect taking advantage of pretty much what I want to do, using the original motor mount to mount a switch;
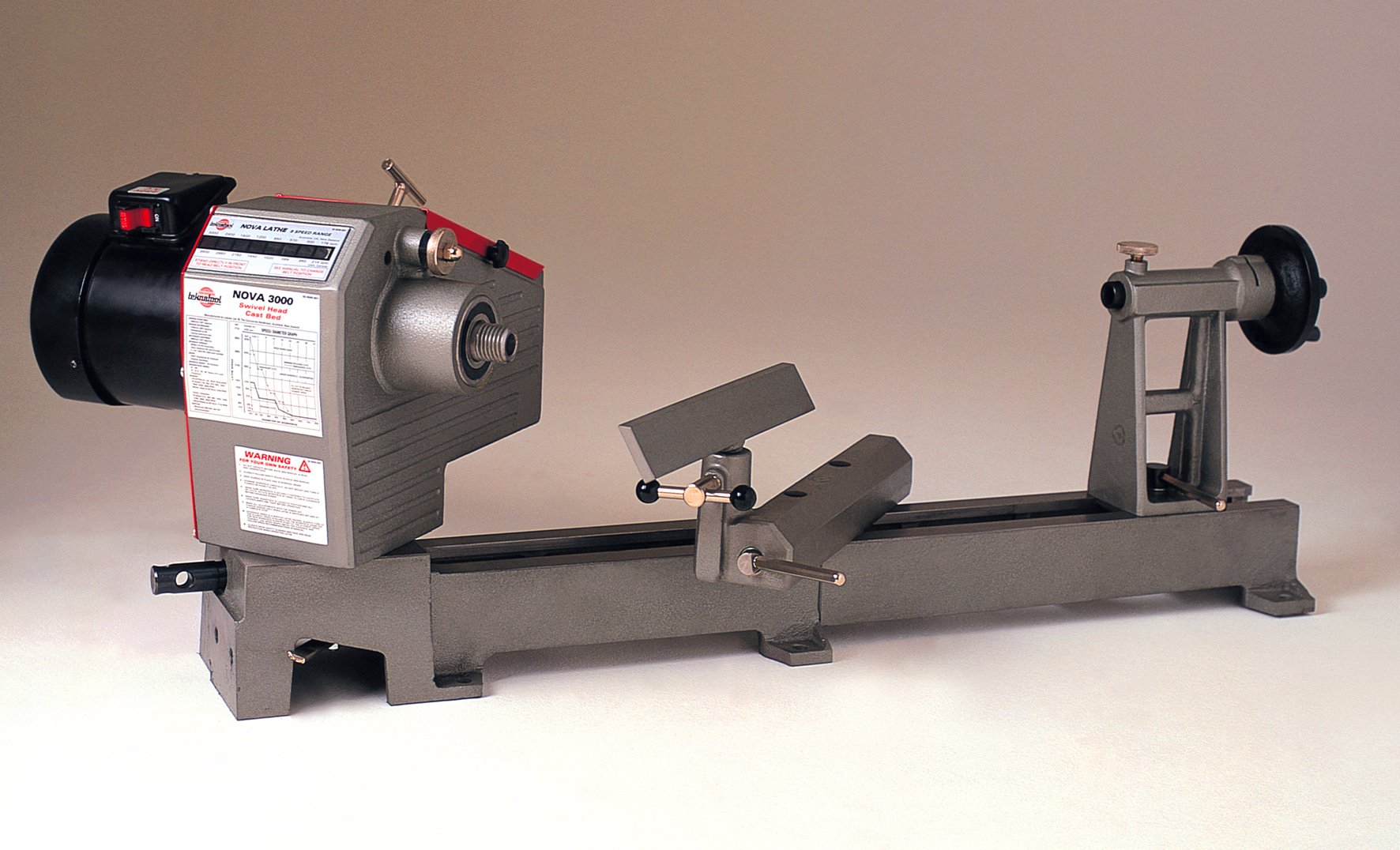
I've Never done any large object turning, so suspect I'll just play with it a bit, but it will be fun to have the capabilities. That's the reason I'm only doing a 1h motor. I might go ahead and do the 1.5hp for potential resale or next user.
Just for fun, the lathe is a Nova 3000, likely had a DC variable speed upgrade and the previous owner took the motor before paying some bills with the lathe/chuck and tools. The chuck is a Vicmarc VM100 with 3 sets of jaws, and it came with 3 Henry Taylor Gouges, 3 Sorby tools and a PM metals skew. The picture they posted didn't show the chuck, just 2 sets of chuck jaws.

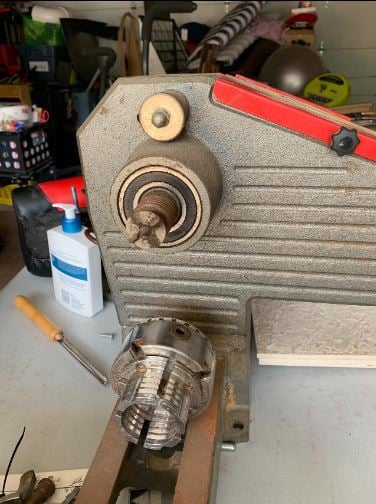
Thanks for any insight!
-Whit
So I now I want to install a motor. It will take 3/4 - 1.5hp 56C face plate mount motor.
So a inexpensive, 1 hp motor from Automation Direct runs $143, and the listed Lock rotor amps is 80 amps!!! I assume since it has a start up capacitor, my inverter will never see this?
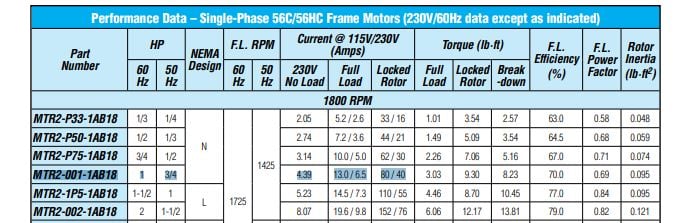
I can also get a 'run capacitor' it says it's to decrease power factor while running, allowing the motor to run more efficiently. Not sure what the savings are, I'll likely be doing mostly the same small stuff/low demand stuff, I'm currently dong on a tiny 350 watt table top lathe. So will a run capacitor help more on the low end or high end of demand?
It specifies that no specific motor orientation is required, since I will mount this with the face plate, I assume if I spin this 45 or 90 degrees and use the mounting bracket to mount an on/off, emergency shut down and reverse speed box that won't be a problem? Here's a picture of a 3000 setup with a DC motor, the speed controller and 3 postion switch for Fwd/Off/Rev is a very Bad position, right at the knee and blocking any pivot and use as an open ended lathe.
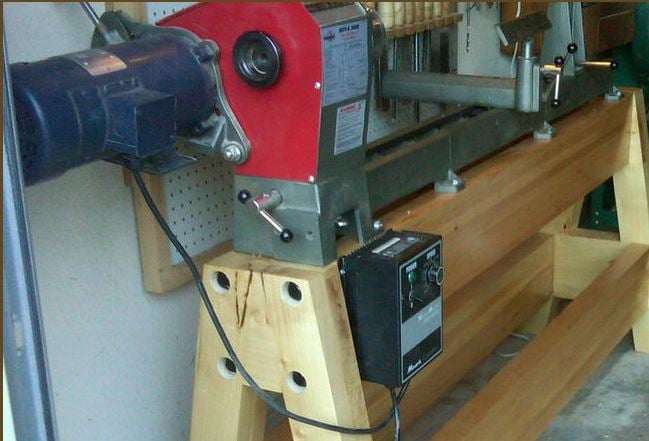
Here's the lathe in original configuration with a switch on the motor, I suspect taking advantage of pretty much what I want to do, using the original motor mount to mount a switch;
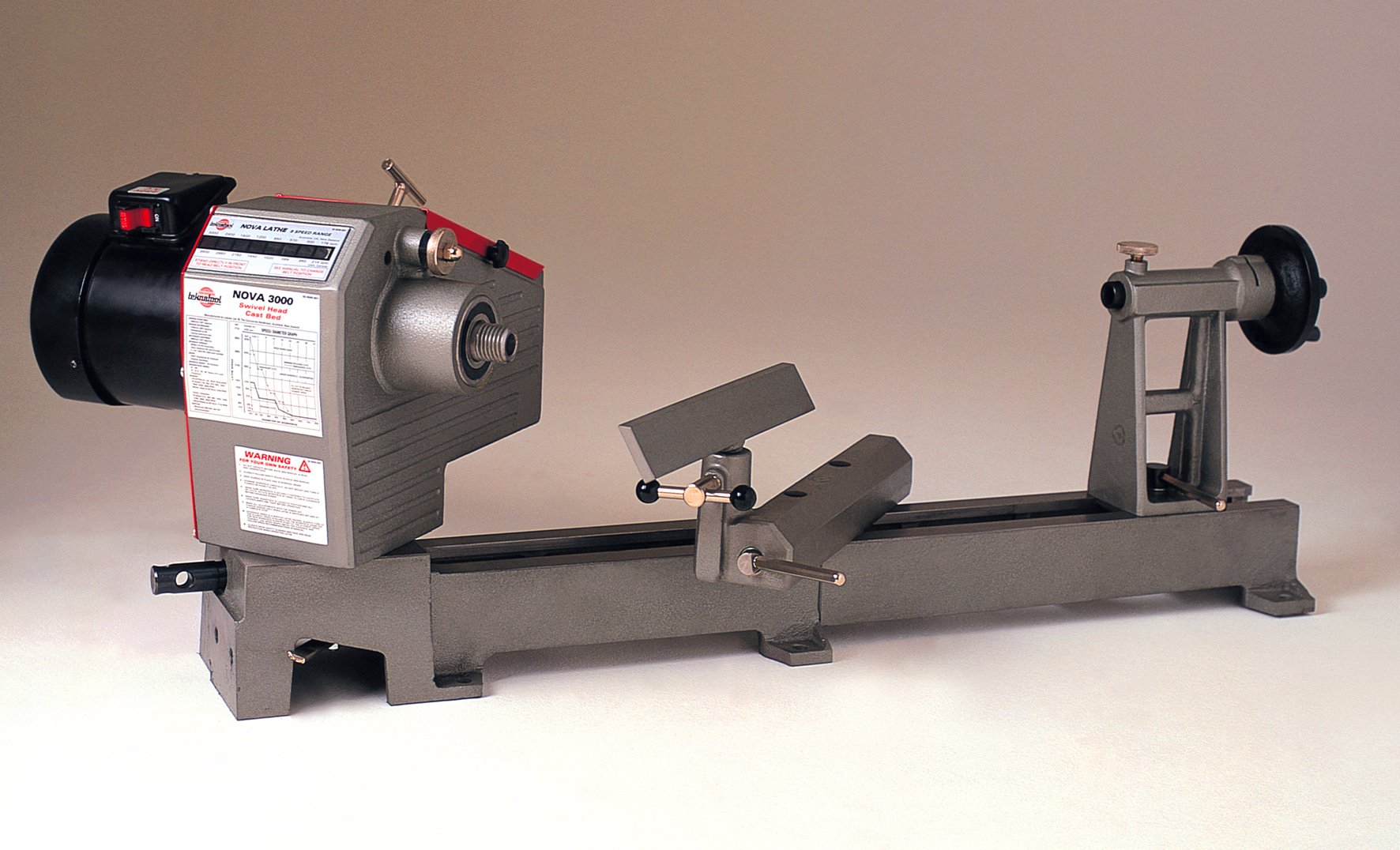
I've Never done any large object turning, so suspect I'll just play with it a bit, but it will be fun to have the capabilities. That's the reason I'm only doing a 1h motor. I might go ahead and do the 1.5hp for potential resale or next user.
Just for fun, the lathe is a Nova 3000, likely had a DC variable speed upgrade and the previous owner took the motor before paying some bills with the lathe/chuck and tools. The chuck is a Vicmarc VM100 with 3 sets of jaws, and it came with 3 Henry Taylor Gouges, 3 Sorby tools and a PM metals skew. The picture they posted didn't show the chuck, just 2 sets of chuck jaws.
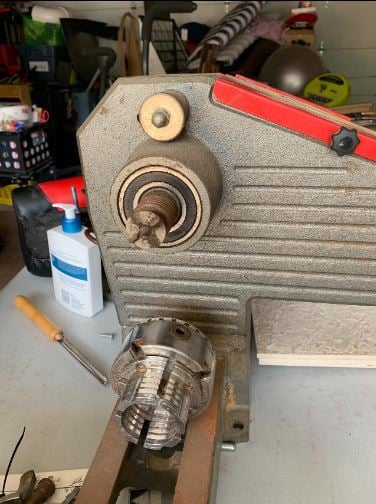
Thanks for any insight!
-Whit
Home system 4000 watt (Evergreen) array standing, with 2 Midnite Classic Lites, Midnite E-panel, Magnum MS4024, Prosine 1800(now backup) and Exeltech 1100(former backup...lol), 660 ah 24v Forklift battery(now 10 years old). Off grid for 20 years (if I include 8 months on a bicycle).
- Assorted other systems, pieces and to many panels in the closet to not do more projects.
- Assorted other systems, pieces and to many panels in the closet to not do more projects.
Comments
-
I didn't know you could reverse an ordinary motor.
Single phase motors have a Start winding with a Cap, so that the voltage and amps are out of phase enough to get the rotor to spin instead of jittering at 60hz. The Cap and the winding determine which way the motor will start spinning. I don't know if that can be done in a control box external to the motor.
LRA That's going to be a problem for the inverter, which DOES have to dump that power into the starting winding to get things moving. I don't know if a soft start cap can improve that. Once the motor gets a couple of RPM, the power demand goes down quickly. 2 seconds should be the time window I would expect for 0 to full speed. And the LRA amps would only be for the first second.
Now I want to compare your motor chart to my motor chart. I would expect them to be pretty close for the same HP rating
Well, 1HP is different. sorry.
Powerfab top of pole PV mount | Listeroid 6/1 w/st5 gen head | XW6048 inverter/chgr | Iota 48V/15A charger | Morningstar 60A MPPT | 48V, 800A NiFe Battery (in series)| 15, Evergreen 205w "12V" PV array on pole | Midnight ePanel | Grundfos 10 SO5-9 with 3 wire Franklin Electric motor (1/2hp 240V 1ph ) on a timer for 3 hr noontime run - Runs off PV ||
|| Midnight Classic 200 | 10, Evergreen 200w in a 160VOC array ||
|| VEC1093 12V Charger | Maha C401 aa/aaa Charger | SureSine | Sunsaver MPPT 15A
solar: http://tinyurl.com/LMR-Solar
gen: http://tinyurl.com/LMR-Lister , -
Just for the heck of it, I looked up "soft start" systems.
https://www.amazon.com/Air-Conditioner-Soft-Start/s?k=Air+Conditioner+Soft+Start
And they are not cheap for nicer units.
Since this is a lathe, you do not need high starting torque (unlike a refrigeration compressor which can need a lot of starting torque).
If you can reduce the starting surge, that sure would be easier on your inverter.
Motor Run Capacitor... There are several major methods to start a single phase induction motor.
One is the use of starting capacitor (and a centrifugal switch). The capacitor is only "on" when starting (in series with the starting coil). The capacitor provides the phase difference so the motor can start rotating with the starting winding. Provides high starting current.
Another is to use a motor run capacitor. This capacitor is always in the circuit. Has less starting torque.
And there are motors that have both a start and run capacitors:
https://www.quora.com/How-do-start-and-run-capacitors-differ?share=1Motor Start capacitor is commonly used in single phase FHP motors to give a high starting torque. Capacitor is usually an aluminium electrolytic capacitor in series with auxiliary winding. It remains in circuit till the motor attains about 70% of rated speed. A centrifugal switch on its shaft cuts off the capacitor and auxiliary winding at this point and motor runs on single winding thereafter.There is a separate use of a "motor run" type capacitor. Used to "correct" poor power factor. This capacitor is placed across the L1/L2 AC lines.
Values of motor start capacitor are much higher than run types to achieve high torque. These can be used for motors from 1/8th HP to 2.5 HP, and have large tolerances. Typically values from 40-60 mfd to 200–250 mfd and voltage rating of 230 V are common. Because of high values, starting torque is quite high, required in large single phase motors. Basically these have benn constructed as two electrolytic capacitors connected back to back internally. The loss factor is therefore high, and capacitor remains in circuit just for under 3 seconds.
Motor run capacitors are electrostatic capacitors in series with auxiliary windings of motor, which remain in circuit permanently connected. They provide running torque all the time, maintaining phase difference between windings. The loss factor is low, being mostly MPP film capacitor, and values are also low, from 1.25 mfd to 36 mfd for different applications.
A third type, capacitor start capacitor run motor uses both motor start and motor run capacitor in parallel. Larger capacitor is cut off as motor gais speed, and then motor runs with run capacitor of smaller value. This construction gives high starting torque and also good running torque, and is most efficient, though expensive.
An induction motor is "inductive" (current lags voltage). And with a capacitor, voltage leads current.
If you put the phase correcting capacitor across the motor leads (after the power switch). By doing this you can take a "poor power factor" motor (like 0.6 or 0.7) and bring it to 0.95 PF (you don't go to 1.00 because of other issues).
This is normally done in large installations (like oil refineries and such) that have lots of induction motors.
For homes, we pay for kWatt*Hours--Or actual energy used. Presently, we (residential) customers do not "pay" for kVA (i.e., a 0.70 PF motor uses 1/0.70=1.4x more current). So there is no reason for "us" to do this.
In a large facility, the utility can charge for poor power factor--And would take the kWH cost and multiply by 1.4x the power bill to account for the poor power factor.
For a person with an AC inverter--A poor power factor means that your wiring (and transformer) and AC inverter has to output the extra current to support the poor power factor (need larger wire, possibly larger Watt or VA rated inverter).
However, (more or less), your DC Watts is the same with good or poor power factor. So a PFC capacitor does not save battery/solar power/generator fuel usage.
-Bill
Near San Francisco California: 3.5kWatt Grid Tied Solar power system+small backup genset -
mike95490 said:I didn't know you could reverse an ordinary motor.
This is from their manual;
Reverse is handy on a lathe, so it's a concern.mike95490 said:I don't know if that can be done in a control box external to the motor.
Am I reading this wrong?mike95490 said:LRA That's going to be a problem for the inverter, which DOES have to dump that power into the starting winding to get things moving. I don't know if a soft start cap can improve that. Once the motor gets a couple of RPM, the power demand goes down quickly. 2 seconds should be the time window I would expect for 0 to full speed. And the LRA amps would only be for the first second.
I don't know where your chart of motor horse power ratings comes from, looks mostly for 230v 4" motor...
The 13 amps is in line with what other 56C size motors use for 1hp motors, so I'm not to worried about that. I was surprised that their 1.5 hp only used 14.5 amps... For comparisons I looked at major manufacturers of 56C motors, Baldor's 1hp uses 11.8 amps and Leeson 12.8 amps. So I think I'm in the right ball park. This was sold without a motor and so long as I'm attaching a motor rated similar to the others available.
Home system 4000 watt (Evergreen) array standing, with 2 Midnite Classic Lites, Midnite E-panel, Magnum MS4024, Prosine 1800(now backup) and Exeltech 1100(former backup...lol), 660 ah 24v Forklift battery(now 10 years old). Off grid for 20 years (if I include 8 months on a bicycle).
- Assorted other systems, pieces and to many panels in the closet to not do more projects. -
BB. said:Since this is a lathe, you do not need high starting torque (unlike a refrigeration compressor which can need a lot of starting torque).
If you can reduce the starting surge, that sure would be easier on your inverter.
Motor Run Capacitor... There are several major methods to start a single phase induction motor.
One is the use of starting capacitor (and a centrifugal switch). The capacitor is only "on" when starting (in series with the starting coil). The capacitor provides the phase difference so the motor can start rotating with the starting winding. Provides high starting current.
Lathes do have a bit of load when starting, The chuck weighs 4-5 pounds and then a big chunk of wood may weigh 2-3x that, but there is a pulley system between them and there will be no additional resistance from cutting. I actually suspect that the heaviest draw would be on startup, since the spinning mass should reduce the cutting resistance, unless you get a catch which will often spin the belt... but I'm not sure, never have used as large a lathe as this.
I think the option of adding a run time capacitor is only $23, so I guess it would reduce the load on my inverter. Not a huge worry, but something to think about.
https://www.automationdirect.com/adc/shopping/catalog/motors/ac_motors_-_general_purpose/general_purpose/mtr2-001-1ab18
Home system 4000 watt (Evergreen) array standing, with 2 Midnite Classic Lites, Midnite E-panel, Magnum MS4024, Prosine 1800(now backup) and Exeltech 1100(former backup...lol), 660 ah 24v Forklift battery(now 10 years old). Off grid for 20 years (if I include 8 months on a bicycle).
- Assorted other systems, pieces and to many panels in the closet to not do more projects. -
In theory, Locked Rotor Amps is the maximum current with the motor stalled. Actual starting current will be less--How much, I am not sure.
The starting capacitor is not to lessen starting/locked rotor amps. It is to help create a rotating field inside the induction motor--With a second set of windings offset from the main windings. And, as I recall (I think--Been many years), the starting cap increases starting current (provides more current to provide more starting torque)--Not less.
Other starting types (motor run, shaded pole, etc.) have lower starting torque, so they would have lower starting current (again--been many years for me).
And the capacitor does not "store" energy like a battery (i.e., supply steady current to get the motor turning). It is there to provide "out of phase current" because of the series capacitance to the start windings (offset from main windings). Once the motor is close to running RPM (around 70%?) the starting cap/winding power is cut off by a switch (inside the motor, or voltage controlled relay, etc.).
With standard single phase and split phase (120/240 VAC) mains power--There is no "natural" rotation between L1 and L2 voltages/connections. With 3 phase power, between L1/L2/L3 power, there is a natural rotation (120 degrees between each phase, vs 180 degrees between single phase power).
So, with a capacitor/motor run capacitor/other types of self starting induction motors (split phase, shaded pole)--The whole idea is to have a rotating field inside the motor. Then the rotor, which is a stack of steel plates, experiences the rotating field, which generates currents inside the rotor. Those currents then create a magnetic field which is "dragged" by the rotating field.
If you noticed, the 60 Hz rotating field (2 pairs of main windings) would give 1,800 RPM--However, the standard induction motor (the "induced currents" in the rotor) "slip" to generate the N/S magnetic field in the rotor--Giving the motor something like 1,760 RPM... The difference between 1,800 RPM field rotation and the 1,760 RPM actual shaft RPM is the "slip" that is needed to "generate" the magnetic field in the rotor.
Once the single phase phase motor is up to speed... There is a bunch of complicated math on why the the "non-rotating field" is now rotating.
One thing you may want to look into... Get a 3 phase motor and a VFD (variable frequency drive). The VFD will give you soft start, variable RPM, reverse rotation.
You should get a VFD rated 3 phase motor. VFDs generally are more like MSW inverters, causing induction motors to run hotter than they would on Utility Power/Pure Sine Wave power (VFD rated motor has higher temperature rated windings, derated for heat, etc.). Under industrial use (high loads, constantly running), VFD driven 3 phase motors will not last as long motors on conventional power.
-BillNear San Francisco California: 3.5kWatt Grid Tied Solar power system+small backup genset -
Thank you Bill,
I do have a 1hp cheap Duramax lathe, that runs, actually runs on my old 1800 watt inverter with a low peak maybe 3000 watts. I don't think the motor is face mountable, it's not sealed and has no reverse. I was just looking for a chuck when I ran across this deal. So perhaps it's just a minor load to start, I've never loaded it with anything heavy, heck just 2x2 between spindles.
So it sounds like you don't think this motor is reversible? Am I misreading the chart I posted above?Home system 4000 watt (Evergreen) array standing, with 2 Midnite Classic Lites, Midnite E-panel, Magnum MS4024, Prosine 1800(now backup) and Exeltech 1100(former backup...lol), 660 ah 24v Forklift battery(now 10 years old). Off grid for 20 years (if I include 8 months on a bicycle).
- Assorted other systems, pieces and to many panels in the closet to not do more projects. -
From your chart, the motor is reversible.
Just use a 4 way switch for Red and Black wires in above diagram:
Straight Through
Red============Red
Black===========Black
Cross connects Red to Black, and Black to Red
Red======== ========Red
\ /
X
/ \
Black======= ========Black
Using an industrial drum switch (single phase, reversing) should work... Something like one of these (I am not sure--You need to confirm for your application--These are not trivial to research):
https://www.amazon.com/1-5-Electric-Reversing-Returned-RS-1A-MS/dp/B008BFT7GY
https://www.amazon.com/Relay-Controls-CECOMINOD078669-B004VBTPDW/dp/B004VBTPDW
-BillNear San Francisco California: 3.5kWatt Grid Tied Solar power system+small backup genset -
I'm sure there must be some panel mounted versions around. I've got the mechanical box drum switch from the 1hp craftsman motor, sorry no specific photo of it.
I had hoped to just add a 4x6x6 electrical box to base mount plate of the motor, so it would be a nice clean display. Maybe even adding a hall tach to give quick visual information that I have the belt in the correct position. There are little windows to do a visual inspection, but not always easy to see. The little windows are on the right of the picture below.
I'd pretty much like to recreate the control box that they have on the lathe. They use a panel mounted rotary switch on a motor mounted box. with an I/O and emergency shut down (which is really pretty far away from anything. Looks like it can mount the motor in 90 degree increments, so could have a cleaner looking box than the original (for the newer lathe) which looks awkward. I have the I/O switch with an big 'off cover' from a table saw.
I actually found the replacement part at Nova; No wiring diagram though;
More to think about...
Home system 4000 watt (Evergreen) array standing, with 2 Midnite Classic Lites, Midnite E-panel, Magnum MS4024, Prosine 1800(now backup) and Exeltech 1100(former backup...lol), 660 ah 24v Forklift battery(now 10 years old). Off grid for 20 years (if I include 8 months on a bicycle).
- Assorted other systems, pieces and to many panels in the closet to not do more projects. -
The Lathe has a box to reverse the motor. The motor has to be compatible with that, not just the frame size, AFIK.
Powerfab top of pole PV mount | Listeroid 6/1 w/st5 gen head | XW6048 inverter/chgr | Iota 48V/15A charger | Morningstar 60A MPPT | 48V, 800A NiFe Battery (in series)| 15, Evergreen 205w "12V" PV array on pole | Midnight ePanel | Grundfos 10 SO5-9 with 3 wire Franklin Electric motor (1/2hp 240V 1ph ) on a timer for 3 hr noontime run - Runs off PV ||
|| Midnight Classic 200 | 10, Evergreen 200w in a 160VOC array ||
|| VEC1093 12V Charger | Maha C401 aa/aaa Charger | SureSine | Sunsaver MPPT 15A
solar: http://tinyurl.com/LMR-Solar
gen: http://tinyurl.com/LMR-Lister , -
mike95490 said:The Lathe has a box to reverse the motor. The motor has to be compatible with that, not just the frame size, AFIK.Home system 4000 watt (Evergreen) array standing, with 2 Midnite Classic Lites, Midnite E-panel, Magnum MS4024, Prosine 1800(now backup) and Exeltech 1100(former backup...lol), 660 ah 24v Forklift battery(now 10 years old). Off grid for 20 years (if I include 8 months on a bicycle).
- Assorted other systems, pieces and to many panels in the closet to not do more projects. -
My bad, at first glance, I thought that was the wire diagram for the switch. That motor has several extra leads, so i guess it works
Powerfab top of pole PV mount | Listeroid 6/1 w/st5 gen head | XW6048 inverter/chgr | Iota 48V/15A charger | Morningstar 60A MPPT | 48V, 800A NiFe Battery (in series)| 15, Evergreen 205w "12V" PV array on pole | Midnight ePanel | Grundfos 10 SO5-9 with 3 wire Franklin Electric motor (1/2hp 240V 1ph ) on a timer for 3 hr noontime run - Runs off PV ||
|| Midnight Classic 200 | 10, Evergreen 200w in a 160VOC array ||
|| VEC1093 12V Charger | Maha C401 aa/aaa Charger | SureSine | Sunsaver MPPT 15A
solar: http://tinyurl.com/LMR-Solar
gen: http://tinyurl.com/LMR-Lister ,
Categories
- All Categories
- 228 Forum & Website
- 136 Solar Forum News and Announcements
- 1.4K Solar News, Reviews, & Product Announcements
- 199 Solar Information links & sources, event announcements
- 898 Solar Product Reviews & Opinions
- 256 Solar Skeptics, Hype, & Scams Corner
- 22.5K Solar Electric Power, Wind Power & Balance of System
- 3.5K General Solar Power Topics
- 6.7K Solar Beginners Corner
- 1K PV Installers Forum - NEC, Wiring, Installation
- 2.1K Advanced Solar Electric Technical Forum
- 5.6K Off Grid Solar & Battery Systems
- 428 Caravan, Recreational Vehicle, and Marine Power Systems
- 1.1K Grid Tie and Grid Interactive Systems
- 654 Solar Water Pumping
- 816 Wind Power Generation
- 624 Energy Use & Conservation
- 619 Discussion Forums/Café
- 312 In the Weeds--Member's Choice
- 75 Construction
- 124 New Battery Technologies
- 108 Old Battery Tech Discussions
- 3.8K Solar News - Automatic Feed
- 3.8K Solar Energy News RSS Feed