Little help with PV array capacity.
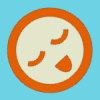
fastline
Registered Users Posts: 31 ✭✭
OK, I am trying to estimate the total KWH potential in my state. I can gather whatever data from NREL that I need BUT I need to relate this data to the PV panels. When I search for this, there are just pages of "how many do I need". I have my needs covered, I just need to determine total harvest per day.
For instance, in peak season, we receive an average of about 6kwh/d/M2. I can only assume this is maximum available flux from all light wavelengths? I know a very rough ballpark I use is a known "1000W/M2" of total sun energy. Obviously we cannot harvest all of that as electricity today. A panel might have roughly 17% efficiency so that might be about 170W/M2 converted to electric. I see a lot of panels measuring about 77x44 which is about 2sqM and a rough Wattage of about 320W. So far all this math is making sense.
However, what flux are they measured at? How do we drive this back to total harvest for a day? So far I am just using a ballpark on that 6kwh/d*17% which gets you about 1kwh/d/M2. If I install 30 panels, that is 60m2*1kwh/d or a total harvest of 60kwh/d.
When I look at the panels, that are about 170W/m2, that is 10,200W, but the flux from the sun will vary and I know there are graphs showing the flux throughout the day but how will the panels perform with less than optimal conditions? I realize much of this is guess work as you can't count on the sun, but I just need to get the math right. Maybe I am just over thinking this.
For instance, in peak season, we receive an average of about 6kwh/d/M2. I can only assume this is maximum available flux from all light wavelengths? I know a very rough ballpark I use is a known "1000W/M2" of total sun energy. Obviously we cannot harvest all of that as electricity today. A panel might have roughly 17% efficiency so that might be about 170W/M2 converted to electric. I see a lot of panels measuring about 77x44 which is about 2sqM and a rough Wattage of about 320W. So far all this math is making sense.
However, what flux are they measured at? How do we drive this back to total harvest for a day? So far I am just using a ballpark on that 6kwh/d*17% which gets you about 1kwh/d/M2. If I install 30 panels, that is 60m2*1kwh/d or a total harvest of 60kwh/d.
When I look at the panels, that are about 170W/m2, that is 10,200W, but the flux from the sun will vary and I know there are graphs showing the flux throughout the day but how will the panels perform with less than optimal conditions? I realize much of this is guess work as you can't count on the sun, but I just need to get the math right. Maybe I am just over thinking this.
Comments
-
I will suspect you are an engineer and unwilling to let others do the work for you...lol
I don't know if you have tried PVWatts, try to allow them to do the calculations for you of solar insolation at PVWatts, plug in your array's angle and orientation ;
https://pvwatts.nrel.gov/
They use l4% for losses, I would prefer closer to 25% or the Normal Operating Cell Temperature value, or NOCT value as compared to Standard Test Conditions (STC the 'label' rating) as a %.
Home system 4000 watt (Evergreen) array standing, with 2 Midnite Classic Lites, Midnite E-panel, Magnum MS4024, Prosine 1800(now backup) and Exeltech 1100(former backup...lol), 660 ah 24v Forklift battery(now 10 years old). Off grid for 20 years (if I include 8 months on a bicycle).
- Assorted other systems, pieces and to many panels in the closet to not do more projects. -
The panels are rated at 1,000 Watts per sq meter of sun... Basically full noontime energy. That is your solar panel's power rating.
And the details, the solar panels are rated at ~75F/25C (room temperature). Output voltage falls with increasing Cell temperature--And cell temperature is much higher under full sun, at higher cell temperatures, Vmp (voltage maximum power) falls. (Imp, does very slightly rise as cell temperature rises, but is generally ignored). The panel's ratings are based on a "flash" test... Simulated sunlight for a few seconds--So cells stay "cool".- Power = Voltage * Current
- Energy = Voltage * Current * Time (for our needs, we use "hours")
The reality is that solar is highly variable, and even measuring energy harvest is (without lab grade equipment/setup) is, at best, within ~10% accuracy. Going for higher accuracies is just not worth it (and getting down towards 1-2% accuracy, even lab grade equipment will diverge in their readings).
When you use Vmp/Imp/Pmp, you have already taken the panel efficiency (17% is a "high efficiency" standard solar panel--Crystalline Cell, vs 8% or less for a non-crystalline type panel). That makes things easier.
If you want to see the "variability" of day to day harvests, using Photowhit's link to PVWATTS, and download the hourly data into a spreadsheet. That data is based on a "statistically selected" average day over the last ~20 years. The next day, is another "average" day's worth of data (real data for a specific date).
The number I use is ~81% of "marketing" (standard test conditions) for Vmp voltage drop.. And 95% for MPPT charge controller efficiency. 0.81*0.95=0.77 ... Photowhit's 75% derating is fine too.
Solar panels can meet or exceed their STC ratings, but that really only happens on very clear/cold (generally subfreezing) days when the cells are below 25C.
Note that MPPT type (Maximum Power Point Tracking) charge controllers are power conversion devices... Power-in*controller-efficiency=Power-out... So falling (or rising) Vmp panel voltages will affect harvest. Basically (t, ypically) a buck mode switching power supply.
PWM (Pulse Width Modulated) controllers are simpler and cheaper controllers... Basically just an "on/off" switch. So as long as Vpanel>Vbatt, the equation for power is Vbatt*Imp=Pbattery ...
Even though the two controllers are very different in their physical operation, in the end I use the same power/energy equations (and efficiency). This does assume that both controllers are running in summer... In winter (and subfreezing weather), MPPT controllers can harvest more energy than PWM... But I don't bother accounting for that. In very cold climates, there is very little hours of sun per day--And 20% more harvest of a small number is still a small number.
For many reasons, MPPT controllers are generally chosen for larger systems (typically >800 Watt solar array), The MPPT controllers are more expensive, but have other advantages that allow longer distances from solar array to battery shed, using cheaper GT type solar panels, use less copper from array to battery shed, etc.
PWM controllers can work fine for smaller systems, and save money--But I highly suggest that you do paper designs of both first to see what works out best for you.
In the end, using "hours of sun" per day, the harvest equation I use is:- Array size (Rated Power in Watts) * 0.77 panel+controller deratings * hours of sun per day = Watt*Hours per day harvest
- Array size (Rated Power in Watts) * 0.52 end to end system efficiency * hours of sun per day = predicted day's average energy harvest
- System efficiency = 0.81 panel derate (Vmp-hot) * 0.95 MPPT controller eff * 0.80 Flooded Cell Battery Eff * 0.85 AC inverter eff = 0.52 overall system efficiency
We try not to make too many hidden fudge factors--The above is relatively conservative--But I have others.. For example, dividing loads between "base loads" that are required every day (refrigerator, LED lighting, cell phone charging) vs "optional" loads that can be postponed or are worth running a genset for a few hours (well pumping, washing machine, electric cooking, etc.).... For that, I suggest something like another 50-65% derating... Assume that you will harvest, relatively reliably, 50-65% of "predicted harvest", and on "nice days", run the rest of the loads.
But all of this is really dependent on your personal energy needs.... Some people, run off their off grid systems assuming they will be running a genset every day or two during winter/bad weather. And if you are in the "great white north"--That is pretty much a requirement.
For folks that live towards the southern/western US, they can make it through winter with a larger solar array and no genset usage required... Choices.
-BillNear San Francisco California: 3.5kWatt Grid Tied Solar power system+small backup genset -
Thanks guys. So in a "ballpark" way of thinking, I am pretty close. I ran through the calc provided above and obtained data that is very close, though they are adding in additional losses such as the inverter, that I had not yet calculated for. I am sure further derates such as BB mentioned with thermal effects causing a voltage decrease.
Here is one issue I have. I need to design for the highest string voltage so I do not exceed ratings of the MPPT controller. Is the "open circuit voltage" the maximum with certainty? One MPPT I am looking at has a 450V rating, but 500V "open circuit" rating. Uh, like if the controller is seeing 500V, it certainly is not open circuit! I am confused by this.
All in all, I am not opposed to adding panels to offset efficiency issues, but I am running into voltage thresholds. Obviously voltage will drop with load, and with heat, but maximum system voltage must still be considered. I can only imagine the bang that will occur from a dielectric failure.
As well, I will ask a rather stupid question. Yes I am in engineering and worked for an electric company but some of this is new.. I am trying to determine safe practices for service and installation of a string system. If you are installing during the day, those panels want to make some power so it would seem at some point you will either be handling a full voltage conductor to make connection, or a series of disconnects need employed near the panels? I have no intention of doing anything until this matter is well understood. I work around 480V commonly and know the dangers well. Would like to avoid some high voltage welding.
-
fastline said:Here is one issue I have. I need to design for the highest string voltage so I do not exceed ratings of the MPPT controller. Is the "open circuit voltage" the maximum with certainty? One MPPT I am looking at has a 450V rating, but 500V "open circuit" rating. Uh, like if the controller is seeing 500V, it certainly is not open circuit! I am confused by this.fastline said:I am trying to determine safe practices for service and installation of a string system. If you are installing during the day, those panels want to make some power so it would seem at some point you will either be handling a full voltage conductor to make connection, or a series of disconnects need employed near the panels?
In off grid applictions you would have DC rated breaker (or fuse) between the array and the charge controller.
Home system 4000 watt (Evergreen) array standing, with 2 Midnite Classic Lites, Midnite E-panel, Magnum MS4024, Prosine 1800(now backup) and Exeltech 1100(former backup...lol), 660 ah 24v Forklift battery(now 10 years old). Off grid for 20 years (if I include 8 months on a bicycle).
- Assorted other systems, pieces and to many panels in the closet to not do more projects. -
Yes, this if off-grid. I would like to get some data for highest possible Voc. Where?
And yes, this will be a field or stand alone install. So far some of the panels I am considering have 12ga wire on them, with a max Imp current of 6A. For this reason, I feel wiring the panels as 2 in parallel would work best? If I have 450Voc max input to the controller, and the panels have a 65Voc, and do a 2p5s config for a total of 325V/12A, that should all live comfortable. It should also leave some room for expansion in the future on the wiring. I will obviously run bigger home run wiring. -
Open Circuit is defined as the Controller is connected and monitoring, but there is not enough solar radiation to sustain power production. Think of a few minutes before dawn, there is light, but if you stood outside, you would not feel any warmth. Panels can produce their voltage with light from a flashlight beam (less than a watt of power) but when the controller trys to sweep to find the MPPT point, there is no power, so it sleeps for another 2 minutes. Meanwhile the PV is "open circuit" and the controller is hooked up to it, senses voltage, and trys to start again...... finally there is enough power and it starts to harvest 5 watts ! But for the last 10 minutes, it's been getting warmed by the panels Voc. That's the Controller Killer.
Powerfab top of pole PV mount | Listeroid 6/1 w/st5 gen head | XW6048 inverter/chgr | Iota 48V/15A charger | Morningstar 60A MPPT | 48V, 800A NiFe Battery (in series)| 15, Evergreen 205w "12V" PV array on pole | Midnight ePanel | Grundfos 10 SO5-9 with 3 wire Franklin Electric motor (1/2hp 240V 1ph ) on a timer for 3 hr noontime run - Runs off PV ||
|| Midnight Classic 200 | 10, Evergreen 200w in a 160VOC array ||
|| VEC1093 12V Charger | Maha C401 aa/aaa Charger | SureSine | Sunsaver MPPT 15A
solar: http://tinyurl.com/LMR-Solar
gen: http://tinyurl.com/LMR-Lister , -
Here is a bit of an explination on the "IV" curves of generic solar panels (and current/voltage/power curves vs temperature):
https://forum.solar-electric.com/discussion/5458/two-strings-in-parallel-with-unequal-string-voltages
The Voc-cold maximum voltage is based on the coldest mornings you will see, and the Vpanel-max input voltage rating of your controller... Assuming no current flow through panel (this is the maximum voltage across the input FET/Transistors--So this is a valid concern. It is the voltage that breaks down the transistor junctions--And it is highest when no current is being drawn by the Controller/battery bank/loads).
Here is an example of the math for the Voc-cold calculation:
https://forum.solar-electric.com/discussion/18475/rule-of-thumb-for-derating-pv-output-based-on-ambient-temp-is-there-such-a-thing
Midnite has a pretty nice website tool for Voc/Vmp calculations:
http://www.midnitesolar.com/sizingTool_kid/index.php (smaller "kid" controller)
http://www.midnitesolar.com/sizingTool/index.php (larger "classic" controller)
These days, it is getting more difficult to find all of the detailed parameters for calculating thermal offsets... But, more or less, Mono and Crystalline solar panels have very similar thermal factors. You may also see different factors... degree K, degree C, %K, %C, etc... So you have to be sure to understand the units of the factor, and exactly how to write the proper equation.
-BillNear San Francisco California: 3.5kWatt Grid Tied Solar power system+small backup genset -
I should also add... You can see (especially on higher voltage GT type inverters), different input voltages.. A Vpanel-max (never to exceed), possibly a Vmppt-min/max range (i.e., when MPPT will actually function... To low of voltage, acts like a PWM controller, to high of voltage, the MPPT function is not "efficient"). Also, you may see a minimum Vpanel input voltage (starting GT inverter).
And, Midnite is known from their "Hyper-Volt" protection... For example, they may have a 150 VDC max input operational voltage... But are safely shutdown to Vpanel-input has high as 150 Volts (Vpanel-max) + Vbatt actual voltage--I.e,. 150 Volts + 48 Volt battery bank voltage at that moment... Hypervolt "safe" shut would be from 150 VDC to 198 VDC in this example.
As always, read the supporting documents and ask questions if you are not sure... This stuff is not always obvious or simple. And mistakes can invalidate your warranty (higher end controllers "Log" Vpanel max input voltage) to expensive repairs (actually blow out your input FETs).
-BillNear San Francisco California: 3.5kWatt Grid Tied Solar power system+small backup genset -
Bam, thanks guys. I found a little conversion table that gets me close from Midnight. Looks like I am more than covered for now. Pretty annoying on the limited voltage input because i can guarantee FETs are available cheap for 1000V. However, I guess some could reason that if some DIYers play with 1kv, it might start to put a damper on the PV fun. Then you get regulations that say "only a licensed tech can buy these because they are dangerous"......
This brings me to another ignorant question I have yet to deal with. I have many acres for my install, no biggy. I am in manufacturing so setting up a tracking system should not be too major, However, I simply cannot understand why in our midwest state many panels are angled towards the South? Is this just to even out the highs and lows and optimize for winter? I also want to know more about tracking, even just single axis before I build something. Is there cost effective solutions? I know most don't do it and a panel can accept light at a angle but the angle reduces the effective area so that can't help.
I don't think I could honestly design my rack system and not design for at least manual adjustment, if not single axis tracking with manual 2nd. I might have to go in with a temporary for now but I don't see many people tracking? Just too complex? Expensive? I guess for guys on a roof, that won't work well but that I am not. -
FET's are extremely unforgiving. Any excursion beyond spec limits, and they die. But even common ringing in a 100V, nearly DC circuit, can cause brief voltage excursions, and poof - no FET. And often, the failure sends HV surge into the gate driver circuit and frys all that stuff too. So it's a big thing, using FETs rated for +5x over expected voltage, and they still burn out at the blink of an eye. Tuning a bank of parallel FETs to match their drivers is no small task either.Powerfab top of pole PV mount | Listeroid 6/1 w/st5 gen head | XW6048 inverter/chgr | Iota 48V/15A charger | Morningstar 60A MPPT | 48V, 800A NiFe Battery (in series)| 15, Evergreen 205w "12V" PV array on pole | Midnight ePanel | Grundfos 10 SO5-9 with 3 wire Franklin Electric motor (1/2hp 240V 1ph ) on a timer for 3 hr noontime run - Runs off PV ||
|| Midnight Classic 200 | 10, Evergreen 200w in a 160VOC array ||
|| VEC1093 12V Charger | Maha C401 aa/aaa Charger | SureSine | Sunsaver MPPT 15A
solar: http://tinyurl.com/LMR-Solar
gen: http://tinyurl.com/LMR-Lister , -
I will agree but IGBTs in high voltage VFDs seem to live without much issue, even with ringing in the line sets from various things. To some degree, I just think the more expensive and better electrics are not used due to cost savings. I guess it can add up with you need 1500 components and they all cost 10 cents more.
I am sure i will get the chance to get into one of these inverters and do some board level repairs. Just hoping they are built to be serviced.
I can deal with overload/overheat failures but lightning!!!!! shit!!! Nearly everything that has beat me on the electronics bench has been a lightning victim. It LOVES microcontrollers. Never a fuse, never an MOV, never a gate drive, ALWAYS a chipset.
One thing I am looking to do is use a BIG disconnect for the PV array and if I happen to be home (likely) during a storm, I will disconnect them from the system. You need a BIG airgap to avoid lighning damage. Then of course it will just hit my inverter shed and take everything else out. lol -
Not much survives direct lightning strike. Often damage is from near by strikes. Midnite makes some of the best surge protectors. Street price is around $90;
http://www.midnitesolar.com/products.php?productCat_ID=23
Orientation of an array to south is helpful for winter production when the sun rises and falls in narrower southern angle.
Manny also angle there array steeper to catch more winter production. Tracking may actually be a psychological aspect. I've lived on solar electric 'off grid' for l7+ years now. I really don't want to worry about anything, rarely check things, everything is properly setup once month I check the electrolyte levels and usually SG on the battery and do an equalizing cycle. The rest of the time it provides my electric. Some people here check things every day several times day.
If I was setting up today I would setup the array for 'virtual tracking' with half the array southeast and half the array southwest. Solar panels are cheap and it would allow for more running off the array and less/shorter battery use and still nothing extra to worry about.
I don't know the issues with higher voltage FETs, but I suspect there is more to it. Midnite made their charge controllers in 3 different input voltage handling models l50, 200 and 250, the higher the voltage the less current hey can handle. There are now some high voltage charge controllers at 600v (Morningstar and Schneider) they retail about double the price.
Home system 4000 watt (Evergreen) array standing, with 2 Midnite Classic Lites, Midnite E-panel, Magnum MS4024, Prosine 1800(now backup) and Exeltech 1100(former backup...lol), 660 ah 24v Forklift battery(now 10 years old). Off grid for 20 years (if I include 8 months on a bicycle).
- Assorted other systems, pieces and to many panels in the closet to not do more projects. -
Is it possible to put a small load like a resistor or a led light in front of the input of the charge controller so it won't have high VOC reach the controller in the early cold morning? or the expensive controller should have protective circuit to disconnect the high VOC from the controller until it reach the safe level.XW6848+ Magnum 4448PAE (Backup) 7800 watts total mixed Panels, 370 AH @48volts battery bank. Grid assist and soon be Tied.
-
You might be able to use a 145V zener diode, but it would need to be a 50w version and mounted on a heat sink. And you hope it works all the time !! The "knee" curve of the zener would be critical and would have to be examined carefully before counting on it to save your CC investment.Edit - I'll also add, that your zener may be activated late afternoon, if your batteries are full, and the CC has throttled back, pushing the system voltage up as it "ruins" the MPPT function. So you may need closer to a 500w zener !! This would have to be a pretty well engineered piece of gear, as being a "little off" will smoke your CC.Powerfab top of pole PV mount | Listeroid 6/1 w/st5 gen head | XW6048 inverter/chgr | Iota 48V/15A charger | Morningstar 60A MPPT | 48V, 800A NiFe Battery (in series)| 15, Evergreen 205w "12V" PV array on pole | Midnight ePanel | Grundfos 10 SO5-9 with 3 wire Franklin Electric motor (1/2hp 240V 1ph ) on a timer for 3 hr noontime run - Runs off PV ||
|| Midnight Classic 200 | 10, Evergreen 200w in a 160VOC array ||
|| VEC1093 12V Charger | Maha C401 aa/aaa Charger | SureSine | Sunsaver MPPT 15A
solar: http://tinyurl.com/LMR-Solar
gen: http://tinyurl.com/LMR-Lister , -
Is it possible... Yes. Is it something that could "solve" the problem... It would be a waste of energy,
Lots of unknowns... How cold, how quick will sun hit panel, tracking or fixed, what is the maximum low for the next 10-20 years, etc... Do you manually turn off loads when it gets above 0C/32F? (and forget one day to turn the panel load on before next cold morning, etc.).
One person (at least) here looked at a (for example) using 3 panels in series in the winter and 4 panels in series during the summer... (use a switch to put panel 4th panel in series with the other 3 panels, or to bypass). Did he do it? I don't remember.
I am a big believer in putting the effort (and, unfortunately the $$$) in the project during design/installation... And have a system you can "forget about" for the next XX years (other than normal maintenance).
Murphy's Law... Anything that can go wrong will go wrong. And you can add, at the worst possible time in the worst possible way.
-BillNear San Francisco California: 3.5kWatt Grid Tied Solar power system+small backup genset -
Agree with BB. I feel we are in a time when semiconductors can most certainly work in the voltages we are targeting here. Add some buffer for FET protection and run with it. Personally, I feel the sensitivity of FETs being directly connected to a field of PVs, it is nearly inevitable that a little charge build up or something will take them out and the design strategy has to be geared towards replacement of the components (who even thinks like that anymore) and failure isolation. In many instances, optos are a preferred choice for gate isolation. I lost count of how many circuits I have been in that the FETs were purposely integrated to be a PITA to replace so you are forced to buy another. That is the equipment I prefer to avoid because when something fails, I will have it on the operating table in minutes and can usually have parts next day. I don't wish to be bound by silly "proprietary games".
Categories
- All Categories
- 229 Forum & Website
- 137 Solar Forum News and Announcements
- 1.4K Solar News, Reviews, & Product Announcements
- 199 Solar Information links & sources, event announcements
- 898 Solar Product Reviews & Opinions
- 256 Solar Skeptics, Hype, & Scams Corner
- 22.5K Solar Electric Power, Wind Power & Balance of System
- 3.5K General Solar Power Topics
- 6.7K Solar Beginners Corner
- 1K PV Installers Forum - NEC, Wiring, Installation
- 2.1K Advanced Solar Electric Technical Forum
- 5.6K Off Grid Solar & Battery Systems
- 428 Caravan, Recreational Vehicle, and Marine Power Systems
- 1.1K Grid Tie and Grid Interactive Systems
- 654 Solar Water Pumping
- 816 Wind Power Generation
- 624 Energy Use & Conservation
- 619 Discussion Forums/Café
- 312 In the Weeds--Member's Choice
- 75 Construction
- 124 New Battery Technologies
- 108 Old Battery Tech Discussions
- 3.8K Solar News - Automatic Feed
- 3.8K Solar Energy News RSS Feed