Lithium or apparently highest power deep cycle?
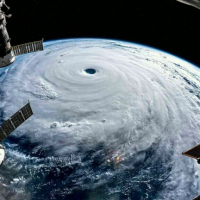
spacebass
Registered Users Posts: 87 ✭✭
Hi , David from Thailand here (English) thank you for having me.
My first dabble in Solar, I will have 4 x 340 watt 24 volt mono panels in series parallel , a tracer 40 amp AN series mppt controller and a high quality 24 volt 3000'watt sine wave 9000 watt peak inverter , charger, UPS, (Applegreen).
The question is batteries I can' t get my head round aH , so I am asking the board whether I should use 2 x 120aH Lithium 12 volt or 3 x 165 aH deep cycle 8 volt in series. The price is about the same.
I will be using it to run (as far as possible) 2 x 75 watt fans most of the time, 2 x 14 cub ft inverter fridge freezers about 130 watts each, microwave 1200 watts not much, coffee cup water heater 600'watts quite a lot, water cooler 79 watts 3 hours, washing machine top loader no heater a couple of times a week when it's sunny, 40 watts of led lights all night and a bit more,led TV 100 watts 4 hours a day 3 phone chargers , and 1 inverter air con 1000 Watts 3 hours at night ,
This is my starter and I could add another similar bank if this is too hopeless.
I live in a sunny place in Thailand (Rayong) the sun is most of the time too hot to hang out on the roof where the panels will be with no shade.
Thank You for your kind consideration.
My first dabble in Solar, I will have 4 x 340 watt 24 volt mono panels in series parallel , a tracer 40 amp AN series mppt controller and a high quality 24 volt 3000'watt sine wave 9000 watt peak inverter , charger, UPS, (Applegreen).
The question is batteries I can' t get my head round aH , so I am asking the board whether I should use 2 x 120aH Lithium 12 volt or 3 x 165 aH deep cycle 8 volt in series. The price is about the same.
I will be using it to run (as far as possible) 2 x 75 watt fans most of the time, 2 x 14 cub ft inverter fridge freezers about 130 watts each, microwave 1200 watts not much, coffee cup water heater 600'watts quite a lot, water cooler 79 watts 3 hours, washing machine top loader no heater a couple of times a week when it's sunny, 40 watts of led lights all night and a bit more,led TV 100 watts 4 hours a day 3 phone chargers , and 1 inverter air con 1000 Watts 3 hours at night ,
This is my starter and I could add another similar bank if this is too hopeless.
I live in a sunny place in Thailand (Rayong) the sun is most of the time too hot to hang out on the roof where the panels will be with no shade.
Thank You for your kind consideration.
Comments
-
Do you have a generator or grid connection?
To get your total loads, multiply the watts to run each of your loads times hours in use per day. This gives you watt-hours/day, a number needed to get design battery and pv size.
With 2 x 12v 120ah batteries in series, you would have 120 x 24 = 2880 watt-hours of total storage. Lithium typically allows for nearly all storage to be used so say 2800 WH available. With 3 x 8v 165ah in series, you would have 165 x 24 = 3960 WH total. A lead acid battery shouldn't go below ~50% regularly, so ~ 1900 available. At the same price, the lithium appear to offer a better deal in terms of watt-hour cost, though there could be other factors (eg cycle life, lithium bms, etc).
Looking at your list of loads though, you'll likely need another source of power, or more pv and storage. Just the air con at 1000w x 3 hours overnight is 3000 wh/day alone, which would be more than either banks storage.Off-grid.
Main system ~4kw panels into 2xMNClassic150 370ah 48v bank 2xOutback 3548 inverter 120v + 240v autotransformer
Night system ~1kw panels into 1xMNClassic150 700ah 12v bank morningstar 300w inverter -
Hi David, welcome to the battery forum.
Before jumping into the deep end without knowing how to swim, I would highly recommend doing an energy audit. To begin with, is this an off grid application, or a backup system? Off grid is particularly demanding requiring significantly more than the outlined loads versus battery capacity.you are speaking of.
To get an idea of requirements add all the loads in watts and multiply by the time in hours, this will provide a figure to calculate the battery capacity needed. For example a 1000W load for 3 hours will need 3Kw of energy, the battery would need to be sized to provide this. A 100Ah battery at 24V nominal has a theroritic capacity of 2.4Kwh, but this figure is misleading because in the case of lead acid the usable capacity is only 50% of actual, so ~1.2Kwh, lithium is better offering, ~ 80% or 2KW usable due to not suffering from depth of discharge issues. Not only dose the PV array need to recharge the battery, it needs to support applicable loads during the day.
The complexity of your question is dependent on actual intended useage, from initial view it would appear to be a medium to large system, but it's best to start with intended use.
Building larger than required is often the path to less dissapointment, it took some time to reach this in my case, with many errors and regrets, if you wish, you could always visit, I'm near Udon Thani Thailand, 100% off grid and willing to share any information.1500W, 6× Schutten 250W Poly panels , Schneider MPPT 60 150 CC, Schneider SW 2524 inverter, 400Ah LFP 24V nominal battery with Battery Bodyguard BMS
Second system 1890W 3 × 300W No name brand poly, 3×330 Sunsolar Poly panels, Morningstar TS 60 PWM controller, no name 2000W inverter 400Ah LFP 24V nominal battery with Daly BMS, used for water pumping and day time air conditioning.
5Kw Yanmar clone single cylinder air cooled diesel generator for rare emergency charging and welding. -
Thank You for your responses I had a feeling. The lithium would actually in practice provide more oomph, I am on grid and my inverter will start charging the batteries and go to grid ac when battery level falls to 10.5 volts. Another available possibility for batteries is 8 x 75 amp 12 volt valve regulated in series parallel how many watt hours would this provide , these are 2nd hand though, about the same price. Thank You Mcgivor for your invitation .
Is the answer for now to buy a big lithium battery ? It seems to me lithium is the only way to go. -
That would give you more watt-hours, but 4 strings isn't ideal, and valve regulated can be hard to spot the likely charging issues. I'd avoid used, but would at minimum want to do a proper load test as they can potentially lose much of their capacity pretty quickly if abused.
As McGivor and I have suggested, it would be better to nail down the daily watt-hours expected from battery for loads, then design battery and charging system. Also, it would help if you could help us better understand your expectations. Is it to save money on grid power? Time shift for time-of-day grid rates? Backup for frequent grid power outages?
Knowing how much power is needed, and for how long is key in designing a system that meets your expectations.Off-grid.
Main system ~4kw panels into 2xMNClassic150 370ah 48v bank 2xOutback 3548 inverter 120v + 240v autotransformer
Night system ~1kw panels into 1xMNClassic150 700ah 12v bank morningstar 300w inverter -
My aim is not to pay for electricity from the grid , for now I will exclude the air con and probably build a similar system for that after learning from this one and seeing exactly what it consumes, it was a lavish afterthought. My consumption is about 8.2kw per. day I suspect 50% of that is inverter fridge freezers spread over 24 hours, all the other high power use is during the day. Some short 1kw cooking and washing machine twice a week , can use on sunny day as bread maker 30 kw a month.
Note : I am going to use 3 x 340 watt 24 volt panels in parallel as 4 put out too many watts for Tracer mppt 40 amp controller.
I don't understand why volts and amps can be in spec but watts are too high.
Thank You.
Just found this lithium battery can I use it ?
Samsung SDI lithium battery, size 29.6v 120Ah, CCA measurement can be more than 2000, pay current.
-
Hi David,
this is is david from California,
Do use all 4 of your panels in series/parallel arraignment. The panels can generate 1360 watts at maximum and the controller can operate at 1130 watts, so not a serious overpowering of the controller and the controller's current limiting will protect itself and limit current to 40 amps, and with an MPPT controller you need some voltage headroom over the battery voltage. For 24 volt system this would be 40 volts or so. Your panels in series parallel should be about 60 volts or so and will work well with that controller2 Classic 150, 2 Kid, 5 arrays 7.5 kw total 2ea. 2S6P Sharp NE-170/NE-165, 1ea. 12P Sanyo HIT 200, 2ea. 4/6P Sanyo HIT 200, MagnaSine MS4024AE, Exeltech XP-1100, 2 Banks L-16 battery, Rolls-Surette S-530 and Interstate Traction, Shunts with whizbangJr and Bogart Tri-Metric, iCharger i208B dc-dc buck/boost converter with BMS for small form lithium 8S 16650 or LiFePO4, -
Tecnodave said:Hi David,
this is is david from California,
Do use all 4 of your panels in series/parallel arraignment. The panels can generate 1360 watts at maximum and the controller can operate at 1130 watts, so not a serious overpowering of the controller and the controller's current limiting will protect itself and limit current to 40 amps, and with an MPPT controller you need some voltage headroom over the battery voltage. For 24 volt system this would be 40 volts or so. Your panels in series parallel should be about 60 volts or so and will work well with that controller
Thank You David for your comment and confirming to me a bit of overload is OK. I cancelled one panel to be on the safe side so will have to reorder it.
-
David,
In solar use of lithium batteries we do not use the full capacity to get longer life. Maximum charge is to about 95% of amp hour rating and maximum discharge is about 20% of capacity. So total usable capacities are more like 3,000 watt/hours
Do consider a BMS (Battery management system) to manage charging and discharging those lithium cells. They need more than just a charge controller to get long life. Hopefully someone with a bit more experience in LiFePO4 cells in solar use will add to what I have said.
My expertise is large format Flooded Lead Acid and that is what I use in my solar systems. I have a small set of 8 40 amp/hr LiFePO4 Prisimatic cells like what you have as well as other lithium types., 18650's and other small LiLo and LiPo for use in portable use.
I use a Chinese model airplane charger for my lithium, the Junsi iCharger i208B which has a BMS balancing system built in.2 Classic 150, 2 Kid, 5 arrays 7.5 kw total 2ea. 2S6P Sharp NE-170/NE-165, 1ea. 12P Sanyo HIT 200, 2ea. 4/6P Sanyo HIT 200, MagnaSine MS4024AE, Exeltech XP-1100, 2 Banks L-16 battery, Rolls-Surette S-530 and Interstate Traction, Shunts with whizbangJr and Bogart Tri-Metric, iCharger i208B dc-dc buck/boost converter with BMS for small form lithium 8S 16650 or LiFePO4, -
Can I use this battery : Samsung SDI lithium battery, size 29.6v 120Ah, (yes it's big!)
Under to start : mppt 40 amp 24 volt and 1300 watt of panels then add another 1100 watts of panels and another tracer mppt 40 amp to supplement charging. -
Tecnodave said:David,
In solar use of lithium batteries we do not use the full capacity to get longer life. Maximum charge is to about 95% of amp hour rating and maximum discharge is about 20% of capacity. So total usable capacities are more like 3,000 watt/hours
Do consider a BMS (Battery management system) to manage charging and discharging those lithium cells. They need more than just a charge controller to get long life. Hopefully someone with a bit more experience in LiFePO4 cells in solar use will add to what I have said.
My expertise is large format Flooded Lead Acid and that is what I use in my solar systems. I have a small set of 8 40 amp/hr LiFePO4 Prisimatic cells like what you have as well as other lithium types., 18650's and other small LiLo and LiPo for use in portable use.
I use a Chinese model airplane charger for my lithium, the Junsi iCharger i208B which has a BMS balancing system built in.
$1100 , 34000thb . -
Despite the cost of grid power ~ 5 Bhat per Kwh ( US $0.15) using batteries will still exceed that by quiet a margin. Even if had grid I would still have solar due to frequent outages particularly during the rainy season, the use would be a blend of both, probably solar during the day and grid overnight.
Batteries are available in Thailand but not as common as in the west, my 24V 400Ah of LFP cells were ordered directly from China, 68 000 Bhat, no import duties or tax on batteries , but they involved building into a system which dose require some experience. This company
https://shop.solaris.co.th/catalogsearch/result/?q=Home has entire lithium based systems, totally integrated with MPPT charger and inverter , the owner is German and very helpful, well worth a look if you have not made any purchases. The prices are not bad considering they are an engineered system, but naturally price is subjective to what is affordable.
Should you go the DIY route don't rush into anything without a plan, carefully calculate loads with a power logging device for each applience. The electrical bill is useful in providing a global view, but a logger can be used for overnight demand, where batteries are needed the most.
As far as air conditioning is concerned, I use two inverter type, a Samsung 18 SEER, and Diakin 26 SEER both 9000 BTU, the Diakin uses half the energy so it is my bedroom unit, once setpoint is reached, I use 27°C as my sleep setting, it only uses 156W cyclical throughout the night to maintain that temperature.1500W, 6× Schutten 250W Poly panels , Schneider MPPT 60 150 CC, Schneider SW 2524 inverter, 400Ah LFP 24V nominal battery with Battery Bodyguard BMS
Second system 1890W 3 × 300W No name brand poly, 3×330 Sunsolar Poly panels, Morningstar TS 60 PWM controller, no name 2000W inverter 400Ah LFP 24V nominal battery with Daly BMS, used for water pumping and day time air conditioning.
5Kw Yanmar clone single cylinder air cooled diesel generator for rare emergency charging and welding. -
mcgivor said:Despite the cost of grid power ~ 5 Bhat per Kwh ( US $0.15) using batteries will still exceed that by quiet a margin. Even if had grid I would still have solar due to frequent outages particularly during the rainy season, the use would be a blend of both, probably solar during the day and grid overnight.
Batteries are available in Thailand but not as common as in the west, my 24V 400Ah of LFP cells were ordered directly from China, 68 000 Bhat, no import duties or tax on batteries , but they involved building into a system which dose require some experience. This company
https://shop.solaris.co.th/catalogsearch/result/?q=Home has entire lithium based systems, totally integrated with MPPT charger and inverter , the owner is German and very helpful, well worth a look if you have not made any purchases. The prices are not bad considering they are an engineered system, but naturally price is subjective to what is affordable.
Should you go the DIY route don't rush into anything without a plan, carefully calculate loads with a power logging device for each applience. The electrical bill is useful in providing a global view, but a logger can be used for overnight demand, where batteries are needed the most.
As far as air conditioning is concerned, I use two inverter type, a Samsung 18 SEER, and Diakin 26 SEER both 9000 BTU, the Diakin uses half the energy so it is my bedroom unit, once setpoint is reached, I use 27°C as my sleep setting, it only uses 156W cyclical throughout the night to maintain that temperature.
My battery price seems in the ball park , it seems to me most of the equipment selection is predefined by the parameters of the units, e,g. Tracer mppt controller 40 amp highly rated takes a 1000watts of panels 4 panels, to use more presumably have to move to s different class if controller which probably costs x 5..
I would not go there. I did with the inverter because of the hopeless reviews of the cheapos. Thanks again mcgivor.
-
I have decided and have bought two Bellco 210 ah lead acid deep cycle batteries at 67 kg each . Half price of double useable output lithium ? 18400 thb v 33,000 thb.
Now for Panel angle I thought latitude no. for angle I am 12.5 ' but today I find a formula that makes it 35' I also read angle is more important further away from the equator and 10' to 15' does not make a lot of difference. I prefer 12.5 ' and I see a picture of a massive solar installation in Rayong where I am and panels do not look like at 35'.
Any opinions ?
Thank You in advance. -
Here is a simple website that lets you try different angles (tilt) and compass angles:
http://www.solarelectricityhandbook.com/solar-irradiance.htmlRayong
Measured in kWh/m2/day onto a solar panel set at a 77° angle from vertical (~13 degrees from flat):
Average Solar Insolation figures
(For best year-round performance)
Large installations may not be optimized for collection of as much energy as possible (for example summer solar noon)... Perhaps they want Afternoon Sun (many place have peak power into afternoon and evening time)... So they may face the array more towards the west.Jan Feb Mar Apr May Jun 6.34
6.35
5.93
5.62
4.94
4.69
Jul Aug Sep Oct Nov Dec 4.64
4.45
4.42
4.91
6.02
6.43
Other places have pretty common afternoon clouds and thunderstorms, so facing more easterly for AM sun gives them more energy.
In general, suggest a minimum of 5 degree tilt (not flat) to allow rain and wind to clear panels of dust and leaves (more or less self cleaning).
-Bill
Near San Francisco California: 3.5kWatt Grid Tied Solar power system+small backup genset -
I'm located 17°N, my two arrays are both south facing one at ~17° the other at~30° fom horizontal, this time of year the smaller 17° array 1500W outperformes the larger 1890W, December January it's the other way around, the difference is minor but the best all year position is probably best,~ 13° for Rayong.1500W, 6× Schutten 250W Poly panels , Schneider MPPT 60 150 CC, Schneider SW 2524 inverter, 400Ah LFP 24V nominal battery with Battery Bodyguard BMS
Second system 1890W 3 × 300W No name brand poly, 3×330 Sunsolar Poly panels, Morningstar TS 60 PWM controller, no name 2000W inverter 400Ah LFP 24V nominal battery with Daly BMS, used for water pumping and day time air conditioning.
5Kw Yanmar clone single cylinder air cooled diesel generator for rare emergency charging and welding. -
Thank You Bill and mcgivor for your advice showing the written word is not sacrosanct I have settled on about 15' mainly because the wife wants 20' ! I am making angle support with blocks and securing the panels with some metallic posts yet to be sourced (wife /Thai people!!!) and others for previous input.
-
I have turned the system on for a couple of days now with mixed success I am getting 70to 80 volts from the panels (4 x 330watts series parrallel) and the tracer 40 amp is delivering sometimes 35 amps to the batteries , but quite a lot less coming out of the panels. I have lowered the low voltage disconnect to match the charge start voltage of the inverter/ charger. Maybe wrong thing to do.
Now the big problem is everything going OK until I plug in the bread making machine, 920 watts, on inverter AC full batteries after a few minutee the 60 amp breaker I have between the tracer and the batteries pops outb(Ithink mixing stage) 'Over Voltage disconnect' wait til the break clicks reset it and after a few minutes the controller seems to be back to normal then ( having removed the bread maker to house AC) click the breaker goes again . This has happened on each of the three occasions I have plugged in the bread maker , three different days, of course after the breaker has popped the bread maker is still working on inverter battery AC ! Until removed. Hard to see the connection ?
And the 20amp breaker in the house breaker box 20 metres away supplying the inverter charger pops too but the 20 amp Panasonic wall breaker I installed near the inverter charger does not . -
I am not quite sure I understand the comment about lower Array current vs Battery bank current of 35 Amps... Just to be clear, MPPT charge controllers are constant power devices... Power in = Power out (excluding 5% or losses)... So, as an example, say your getting 35 amps into your battery bank at 27 volts (made up numbers to show the math):
- Remembering that Power = Voltage * Current
- Power to Battery bank = 35 amps * 27 volts (all battery facing values) = 945 Watts to battery
- On the solar panel side P=V*I; I=P/V
- Array Current Iarray = Parray/Varray = 945 Watts / 70 volts (all array facing values) = 13.5 Amps from the array
Also, if you have 35 amps on a 24 volt battery bank and are seeing ~945 Watts... A typical solar array will output around 75-77% of nameplate rating on a cool day near noon (panels facing sun):- 4*330 Watt panels = 1,320 Watt Std rating
- 1,320 Watts Std * 0.75 panel+controller derating = 990 Watts (typically "best case" power on cool/clear days)
Now, if you are seeing 35 Amps on a 12 volt battery bank--That does not sound right... Either the battery bank is mostly full, or there could be some issues with the charge controller/controller setpoints/system wiring or other issues. You should see >50% of Pmp-std on sunny days and with a battery bank needing charging.
Can you confirm the battery bank voltage (12 or 24 volts)? And what the battery bus voltage is when the bread maker is running.
Where is the 60 amp Circuit Breaker installed? Between battery bank and AC inverter? 2x 60 amp breakers (one from battery bank to AC inverter, a second to the MPPT charge controller?). Or what...
And, there is always the possibility that the 60 Amp breaker pops at way less than 60 Amps (inexpensive breakers, breakers that are not calibrated correctly, etc.). Getting a DC Current Clamp DMM (digital multimeter) can confirm what the "real current" is:
https://www.amazon.com/gp/product/B019CY4FB4 (medium priced meter)
Note there are AC only Current Clamp DMM and AC/DC Current Clamp DMMs... You want to AC/DC (both) Current Clamp DMM.
Read descriptions carefully. Virtually all of the Current Clamp meters can measure AC/DC voltages. But may only measure AC current--The descriptions can be a bit confusing at times.
-Bill
Near San Francisco California: 3.5kWatt Grid Tied Solar power system+small backup genset -
BB. said:I am not quite sure I understand the comment about lower Array current vs Battery bank current of 35 Amps... Just to be clear, MPPT charge controllers are constant power devices... Power in = Power out (excluding 5% or losses)... So, as an example, say your getting 35 amps into your battery bank at 27 volts (made up numbers to show the math):
- Remembering that Power = Voltage * Current
- Power to Battery bank = 35 amps * 27 volts (all battery facing values) = 945 Watts to battery
- On the solar panel side P=V*I; I=P/V
- Array Current Iarray = Parray/Varray = 945 Watts / 70 volts (all array facing values) = 13.5 Amps from the array
Also, if you have 35 amps on a 24 volt battery bank and are seeing ~945 Watts... A typical solar array will output around 75-77% of nameplate rating on a cool day near noon (panels facing sun):- 4*330 Watt panels = 1,320 Watt Std rating
- 1,320 Watts Std * 0.75 panel+controller derating = 990 Watts (typically "best case" power on cool/clear days)
Now, if you are seeing 35 Amps on a 12 volt battery bank--That does not sound right... Either the battery bank is mostly full, or there could be some issues with the charge controller/controller setpoints/system wiring or other issues. You should see >50% of Pmp-std on sunny days and with a battery bank needing charging.
Can you confirm the battery bank voltage (12 or 24 volts)? And what the battery bus voltage is when the bread maker is running.
Where is the 60 amp Circuit Breaker installed? Between battery bank and AC inverter? 2x 60 amp breakers (one from battery bank to AC inverter, a second to the MPPT charge controller?). Or what...
And, there is always the possibility that the 60 Amp breaker pops at way less than 60 Amps (inexpensive breakers, breakers that are not calibrated correctly, etc.). Getting a DC Current Clamp DMM (digital multimeter) can confirm what the "real current" is:
https://www.amazon.com/gp/product/B019CY4FB4 (medium priced meter)
Note there are AC only Current Clamp DMM and AC/DC Current Clamp DMMs... You want to AC/DC (both) Current Clamp DMM.
Read descriptions carefully. Virtually all of the Current Clamp meters can measure AC/DC voltages. But may only measure AC current--The descriptions can be a bit confusing at times.
-Bill
Thank you very much for your massive reply ! To answer some of your queries 1.battery bank 2 x 12 volt 210 ah deep cycle flooded in series 24 volt , the 60 amp breaker from China internet is installed between the tracer mppt controller and the battery bank on positive lead I did buy a 250 amp breaker to go between batteries and inverter but I couldn't get the nut off the pole because it just spun round (cheap!!) so I didn't install it. My DC clamp arrived today must work out how to use it !bYes I was careful to get the DC amps model x 2 £..
I am in the tropics it is 30' ambient temperature most of the time battery sensor plugged into mppt only no remote 37' put fan on it 35,'
I saw a You tube video where the guy said the amps at the bottom in the middle of the screen on the MT50 remote were the Amps that the controller were producing from the of array input I don't think this is correct in the light of your scepticism it is where the 35 Amps comes from, above the volts are in the mid 20s.Panel volts are in high 70s most of the time .
Now I can't get it to do anything the 60 amp fuse Ikeeps popping no bread maker in operation I am charging the battery with AC from the inverter charger to 100% before I start.
Cheers Bill
Now turn on and get message warning OVD on KT-50 remote meter screen
So now I am running the load on inverter hope it normalised itself.!
-
I would double check eh wiring for the 60 amp breaker... If it is in the positive lead between the + battey bus and the + Vbatt of the charge controller--First there should be no way the controller can output 60 amps in your present configuration... And second, it should be completely independent of the AC inverter/bread maker operation (no current from the AC inverter should go through the breaker).
The only way it could possibly be tripped would be a "bad breaker" and the charge controller outputting its maximum current into the battery bank (something like 35 amps) because of the heavy load of the AC inverter.
Assuming you have a car/truck/vehicle... Play with the DC current clamp meter on the vehicle battery. Turn on the head lights, start the vehicle and see the load current turn into a charging current as the engine starts. Also notice that this is a +/- sign on the DC Current meter--It can tell you which way the current is flowing (of course, you can flip the meter on the cable, so +/- is relative to which direction the cable goes through the meter).
-BillNear San Francisco California: 3.5kWatt Grid Tied Solar power system+small backup genset -
If you have ever switched off the battery breaker to the MPPT controller, and left the PV panels attached, you have a good chance of having fried the MPPT. Controllers are powered by the battery and the regulate the PV to the battery voltage. if the battery is disconnected, you get open circuit PV voltage delivered throughout the MPPT controller because it has no place to send the excess voltage to. Fried.
Powerfab top of pole PV mount | Listeroid 6/1 w/st5 gen head | XW6048 inverter/chgr | Iota 48V/15A charger | Morningstar 60A MPPT | 48V, 800A NiFe Battery (in series)| 15, Evergreen 205w "12V" PV array on pole | Midnight ePanel | Grundfos 10 SO5-9 with 3 wire Franklin Electric motor (1/2hp 240V 1ph ) on a timer for 3 hr noontime run - Runs off PV ||
|| Midnight Classic 200 | 10, Evergreen 200w in a 160VOC array ||
|| VEC1093 12V Charger | Maha C401 aa/aaa Charger | SureSine | Sunsaver MPPT 15A
solar: http://tinyurl.com/LMR-Solar
gen: http://tinyurl.com/LMR-Lister , -
BB. said:I would double check eh wiring for the 60 amp breaker... If it is in the positive lead between the + battey bus and the + Vbatt of the charge controller--First there should be no way the controller can output 60 amps in your present configuration... And second, it should be completely independent of the AC inverter/bread maker operation (no current from the AC inverter should go through the breaker).
The only way it could possibly be tripped would be a "bad breaker" and the charge controller outputting its maximum current into the battery bank (something like 35 amps) because of the heavy load of the AC inverter.
Assuming you have a car/truck/vehicle... Play with the DC current clamp meter on the vehicle battery. Turn on the head lights, start the vehicle and see the load current turn into a charging current as the engine starts. Also notice that this is a +/- sign on the DC Current meter--It can tell you which way the current is flowing (of course, you can flip the meter on the cable, so +/- is relative to which direction the cable goes through the meter).
-Bill
So how am I getting the overvoltage ? The PV voltage is around 80 volts on the mt50 remote.
Thanks for the tip on the clamp meter. -
mike95490 said:If you have ever switched off the battery breaker to the MPPT controller, and left the PV panels attached, you have a good chance of having fried the MPPT. Controllers are powered by the battery and the regulate the PV to the battery voltage. if the battery is disconnected, you get open circuit PV voltage delivered throughout the MPPT controller because it has no place to send the excess voltage to. Fried.
-
You are not getting "over voltage" on the MPPT controller... Two panels in series "want" to run Imp-array around 70-80 volts nominal (when controller is drawing "maximum" power from array to charge the battery bank with full available Watts).An MPPT controller is sort of the DC version of a "Variac" (variable AC transformer)... It takes the high voltage/low current of the array and efficiently down converts to the low voltage/high current needed by the battery bank (internally, the MPPT controller is a buck mode/down converter switching power supply). It "matches" the optimum output of your solar array to the optimum output to your battery bank. Basically like a transformer takes 120 VAC at 1 amp and down converts to 12 VAC at 10 amps (120v*1a=12v*10a=120 Watts).Or, if you like analogies... The MPPT controller between your Array and Battery bank is sort of like an automatic transmission between your engine and the wheels.I am not sure you are guaranteed to ruin your MPPT controller when the circuit breaker opens--But it is a good idea to avoid this happening in anything but a really bad situation (like when the MPPT controller fails shorted and tries to draw "unlimited" current from your battery bank).At this point, assuming everything was working OK--I do not see how a "good" 60 Amp breaker popped.It is always possible that I do not understand how you wired your battery bank and I am missing something...-BillNear San Francisco California: 3.5kWatt Grid Tied Solar power system+small backup genset
-
I'd really think carefully about removing the breaker from CC to battery. A CC failed short on output could make for an even worse day than not having bread
Is the breaker polarized (one terminal marked +, or line)? Is it DC rated?
The breaker isn't really there to protect against too much current coming from the controller. It's to protect the wire etc in the event of a dead short across the battery +ive/-ive from a failed charge controller.
Purely guesswork, but maybe the OVD is the controller defaulting to 12v if it doesn't see battery voltage, then going OVD when it does?Off-grid.
Main system ~4kw panels into 2xMNClassic150 370ah 48v bank 2xOutback 3548 inverter 120v + 240v autotransformer
Night system ~1kw panels into 1xMNClassic150 700ah 12v bank morningstar 300w inverter -
OK here is the strangest bit , in the specs of the Tracer 4210AN it says maximum input 100 volts I have on the controller 80 volts showing with 4 panels in series parallel , now I read the instruction book it says for Tracer 4210AN 72 cell 24 volt (mine has 78 cells) VoC less than 46 v maximum 2 best 1 panel.
So I go and disconnect 1string leaving 2 panels in series and I am getting 68 volts on PV and 16-20 amps battery status .
No breaker pop yet. -
You should have not issue with the series/parallel array... Especially being in a warm climate (Voc and Vmp go up, especially in freezing and sub freezing climates).
72 vs 78 cells should not make a big difference (Vmp and Voc roughly increase by 2 volts at room temperature (not in full sun)--~1/2 volt per series solar cell).
Running a single solar panel (1x series) is not ideal... Vmp-array ~ 37-38 volts is a bit on the low side for charging your "24 volt" battery bank (your bank around 29.6 volts charging setpoint?).
Trying to "match" series/parallel panels with battery bank and charge controller operating ranges is always a pain... In your case, 2 panels in series is close to the 100 VDC max (2x Voc-std/cool)... And 1x panel is an less than optimum Vmp-hot setup.
Higher end MPPT solar charge controllers have Vpanel-max at ~140-150 VDC (and even higher)... But these are not cheap. And we have run into "high voltage" solar panels were the are a "no match" for charging 48 volt battery banks (Vmp~50-70 volts) with Vpanel-max in the ~140-150 volt range.
-BillNear San Francisco California: 3.5kWatt Grid Tied Solar power system+small backup genset -
With regards to the circuit breaker, is it running hot ? With thermal type breakers in hot climates without ventilation they sometimes overheat and trip prematurely. To test have a fan create air movement across the breaker, I have one 10A that trips at 6A when ambient is >40°C, the other 5 in the same enclosure, 3 of which carry slightly higher current have never tripped, if I leave the door open there is no problem.1500W, 6× Schutten 250W Poly panels , Schneider MPPT 60 150 CC, Schneider SW 2524 inverter, 400Ah LFP 24V nominal battery with Battery Bodyguard BMS
Second system 1890W 3 × 300W No name brand poly, 3×330 Sunsolar Poly panels, Morningstar TS 60 PWM controller, no name 2000W inverter 400Ah LFP 24V nominal battery with Daly BMS, used for water pumping and day time air conditioning.
5Kw Yanmar clone single cylinder air cooled diesel generator for rare emergency charging and welding. -
Well thanks for the input everyone , since I removed one string I have had no trip or other problem so I am going to leave it at that after a couple of harrowing and illogical days, I have ordered a new 30 amp 1300 watt pwm controller with charging and switching built in has nice toroidal transformer , to plug the other two panels into to run one 1200 BTU inverter Aircon so any suggestions on battery to give s few hours at night only mcgivor ?
-
Estragon said:I'd really think carefully about removing the breaker from CC to battery. A CC failed short on output could make for an even worse day than not having bread
Is the breaker polarized (one terminal marked +, or line)? Is it DC rated?
The breaker isn't really there to protect against too much current coming from the controller. It's to protect the wire etc in the event of a dead short across the battery +ive/-ive from a failed charge controller.
Purely guesswork, but maybe the OVD is the controller defaulting to 12v if it doesn't see battery voltage, then going OVD when it does?
The breaker is marked one terminal battery the other accessory. I believe from car audio market .
Categories
- All Categories
- 229 Forum & Website
- 137 Solar Forum News and Announcements
- 1.4K Solar News, Reviews, & Product Announcements
- 199 Solar Information links & sources, event announcements
- 898 Solar Product Reviews & Opinions
- 256 Solar Skeptics, Hype, & Scams Corner
- 22.5K Solar Electric Power, Wind Power & Balance of System
- 3.5K General Solar Power Topics
- 6.7K Solar Beginners Corner
- 1K PV Installers Forum - NEC, Wiring, Installation
- 2.1K Advanced Solar Electric Technical Forum
- 5.6K Off Grid Solar & Battery Systems
- 428 Caravan, Recreational Vehicle, and Marine Power Systems
- 1.1K Grid Tie and Grid Interactive Systems
- 654 Solar Water Pumping
- 816 Wind Power Generation
- 624 Energy Use & Conservation
- 619 Discussion Forums/Café
- 312 In the Weeds--Member's Choice
- 75 Construction
- 124 New Battery Technologies
- 108 Old Battery Tech Discussions
- 3.8K Solar News - Automatic Feed
- 3.8K Solar Energy News RSS Feed