Setting correct custom charge control parameters for mppt with Lithium
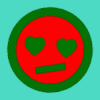
snareman1
Registered Users Posts: 1 ✭
I have a van setup with the following:
Canadian Solar CS3K-305MS Monocrystalline 305 Watt Solar Panel @ 30V Renogy 100ah Lithium 12V battery Tracer -BN 4215 40A MPPT Charge Controller with MT-50 remote meter I've got a MT50 controller hooked up to a Solar Epic Tracer 4215BN charge controller that is putting power into a 12V Renogy Lithium 100ah battery. I'm currently using the suggested settings for a Sealed battery and making the assumption that these settings will work for my LITHIUM BUT I KNOW THAT CANT BE RIGHT. Below is a chart that I retyped from the users manual, please forgive any typos. I can't say I fully understand which each of these rows means and the manual doesn't define them well. If someone out there has a resource on this please pass it along. Any other considerations when configuring this charge controller and battery?
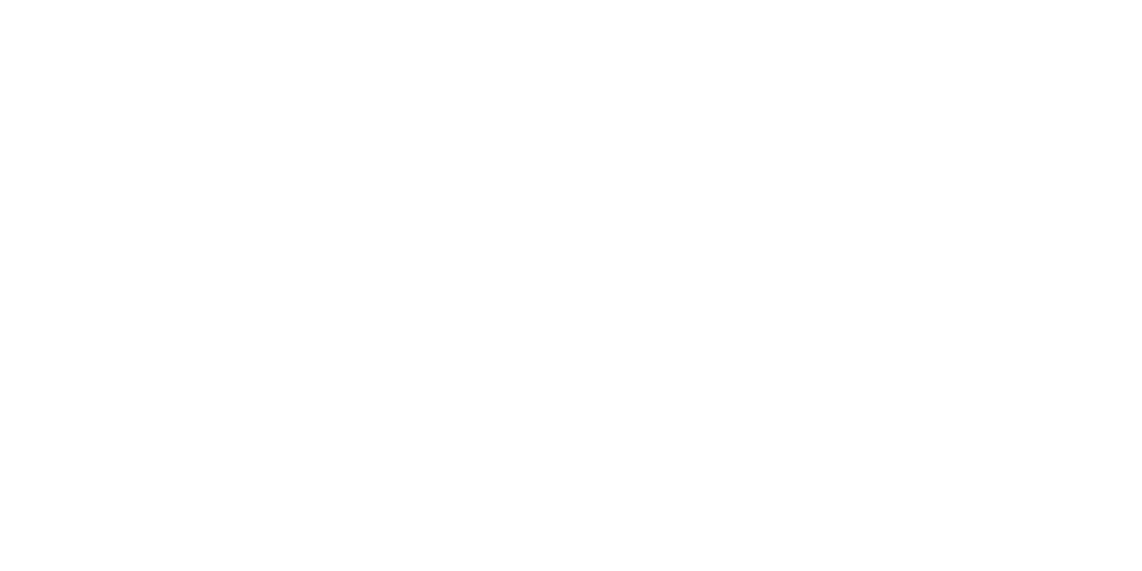
I want to make sure I have the correct parameters set on the charge controller.
Battery specs here: https://www.renogy.com/template/files/Manuals/RNG-LFP_Manual_V1.0.pdf
Panel Specs here: https://www.solar-electric.com/lib/wind-sun/CSI_datasheet_CS3K-MS.pdf
thank you
Canadian Solar CS3K-305MS Monocrystalline 305 Watt Solar Panel @ 30V Renogy 100ah Lithium 12V battery Tracer -BN 4215 40A MPPT Charge Controller with MT-50 remote meter I've got a MT50 controller hooked up to a Solar Epic Tracer 4215BN charge controller that is putting power into a 12V Renogy Lithium 100ah battery. I'm currently using the suggested settings for a Sealed battery and making the assumption that these settings will work for my LITHIUM BUT I KNOW THAT CANT BE RIGHT. Below is a chart that I retyped from the users manual, please forgive any typos. I can't say I fully understand which each of these rows means and the manual doesn't define them well. If someone out there has a resource on this please pass it along. Any other considerations when configuring this charge controller and battery?
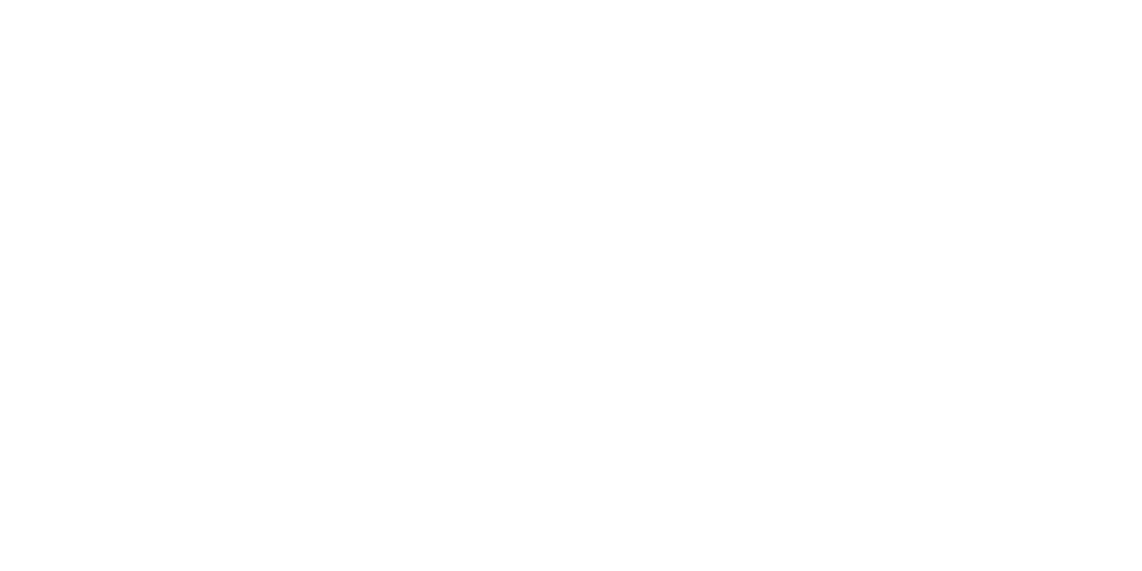
I want to make sure I have the correct parameters set on the charge controller.
Battery specs here: https://www.renogy.com/template/files/Manuals/RNG-LFP_Manual_V1.0.pdf
Panel Specs here: https://www.solar-electric.com/lib/wind-sun/CSI_datasheet_CS3K-MS.pdf
thank you
Comments
-
The image is not showing up for me... (was the image "made pubic"?)
-BillNear San Francisco California: 3.5kWatt Grid Tied Solar power system+small backup genset -
What is the make and model number of the 100AH lithium battery. The battery manufacturer should provide the charge settings. Most lithium batteries of this type are drop-in compatible with AGM batteries, bulk charging to absorb at 14.2 to 14.6 volts and float at about 13.4V. They also have a built in BMS to protect the battery from over charging or discharging.
Edit: Just saw your battery spec sheet. It does indicate 14.4V absorb setting. Didn't see a float setting, but 13.4 should be fine.
Rick4480W PV, MNE175DR-TR, MN Classic 150, Outback Radian GS4048A, Mate3, 51.2V 360AH nominal LiFePO4, Kohler Pro 5.2E genset. -
Ask Renolgy what settings they would use with their controllers, the 7 hours for charging is extremely long, i would assume this is for cell ballancing. Most information I've read states it's not good to hold the cell voltages at 3.65V (14.6V) for extended periods, to do this daily is questionable. Many LFP users charge to a cell voltage of around 3.45 - 3.50V (13.80 - 14.00V ), just before the knee in the charging curve because there is little capacity above this voltage. Some battery system manufacturers recomend these lower charge voltage settings, as well as higher low battery cut out, as part of the warranty, lower charge voltage plus less depth-of-discharge equals longer warranty, obviously they would keep records as part of the BMS. Before randomly charging with an algorithm for AGM, it would be prudent to do some research and get some answers.
My my bulk/absorb equates to14.00V, absorb 6 minutes, float 13.50V, no temperature compensation, seems to work well with prysmatic cells, for what that's worth.1500W, 6× Schutten 250W Poly panels , Schneider MPPT 60 150 CC, Schneider SW 2524 inverter, 400Ah LFP 24V nominal battery with Battery Bodyguard BMS
Second system 1890W 3 × 300W No name brand poly, 3×330 Sunsolar Poly panels, Morningstar TS 60 PWM controller, no name 2000W inverter 400Ah LFP 24V nominal battery with Daly BMS, used for water pumping and day time air conditioning.
5Kw Yanmar clone single cylinder air cooled diesel generator for rare emergency charging and welding. -
........Just saw your battery spec sheet. It does indicate 14.4V absorb setting. Didn't see a float setting, but 13.4 should be fine.
Rick
This prevents harmful cycling at the top. That assumes that the pack is not loaded. I realize most users here are off grid and in that case the pack would be discharging as soon as the charge current stops.8 kW Enphase micros AC coupled to a SolArk 12K -
Without delving into details, the float setting should be set at a voltage where the battery is neither charging nor dischargeing, this voltage is important, , float should be in the neighborhood of 3.375V per cell.
Be very careful with regards to voltage, with LFP, you wil not be dealing with tenths of a volt like LA, but rather with thousands of a volt, the reason voltage is stated as 3.375V per cell for example, not 3.4V, milivolts count and are very important. If a meter is not available to read this resolution, I highly suggest getting one and an accurate one for that matter..
1500W, 6× Schutten 250W Poly panels , Schneider MPPT 60 150 CC, Schneider SW 2524 inverter, 400Ah LFP 24V nominal battery with Battery Bodyguard BMS
Second system 1890W 3 × 300W No name brand poly, 3×330 Sunsolar Poly panels, Morningstar TS 60 PWM controller, no name 2000W inverter 400Ah LFP 24V nominal battery with Daly BMS, used for water pumping and day time air conditioning.
5Kw Yanmar clone single cylinder air cooled diesel generator for rare emergency charging and welding. -
Big system, name brand BMS battery banks do not have this critical voltage requirement by the way.
Just putting it out there for casual observers.
The Op here definitely needs to be accurate measuring voltage."we go where power lines don't" Sierra Nevada mountain area
htps://offgridsolar1.com/
E-mail offgridsolar@sti.net -
Dave Angelini said:Big system, name brand BMS battery banks do not have this critical voltage requirement by the way.
Just putting it out there for casual observers.
The Op here definitely needs to be accurate measuring voltage.
The words chosen were some and recomend, not critical, then again Simpliphi may not be considered a big1500W, 6× Schutten 250W Poly panels , Schneider MPPT 60 150 CC, Schneider SW 2524 inverter, 400Ah LFP 24V nominal battery with Battery Bodyguard BMS
Second system 1890W 3 × 300W No name brand poly, 3×330 Sunsolar Poly panels, Morningstar TS 60 PWM controller, no name 2000W inverter 400Ah LFP 24V nominal battery with Daly BMS, used for water pumping and day time air conditioning.
5Kw Yanmar clone single cylinder air cooled diesel generator for rare emergency charging and welding. -
mcgivor said:Without delving into details, the float setting should be set at a voltage where the battery is neither charging nor dischargeing, this voltage is important, , float should be in the neighborhood of 3.375V per cell...Dave Angelini said:Big system, name brand BMS battery banks do not have this critical voltage requirement by the way.
Just putting it out there for casual observers.
The Op here definitely needs to be accurate measuring voltage.I only think millivolt precision is important if you are near the top of the charging curve. That is where it is steep and a few millivolt difference could over charge the cells. If you are charging a LiFePO with a curve as shown above then cutting off at 3.4 or 3.5 you are still safely below the knee of the curve (3.6v). You may be only charging to 80% of the capacity but so much more of the capacity is usable with Lithium being conservative means more cycles and longer life.
With regard what @mcgivor is saying about float voltage, if I understand him correctly, the float voltage is set below the bulk voltage so the charger never goes into float after bulk/absorb. I am assuming that he is using the example given earlier where bulk/absorb is at 3.5v so a float voltage of 3.4v would not go into float during a normal charge cycle.As @Dave Angelini said all of that is moot if a BMS controls the charging. The BMS will charge to a set voltage, in this case 3.5v. When that voltage is reached the battery goes into current taper, until some minimum current at which time the BMS either signals the charger to stop charging or the BMS cuts off the charging by opening a relay. The later is what typically happens with the Big system or name brand BMS battery banks that he is talking about. The manufacturer sets those parameters. My experience with a customizable BMS is that a simple fixed voltage power supply can be used as a charger because the BMS controls everything. That is the case with motive power packs and grid connected charging of which I am more familiar.
In an off grid situation there may be variations in charging current depending on the output of the solar array so there may not always be constant current. I think the concept is the same and in either case the charging curve looks the same.8 kW Enphase micros AC coupled to a SolArk 12K -
The charging cycle used is bulk, absorption for 6 minutes after which it transitions to float. The bulk absorb voltage is intentionally kept below what the BMS would needs to reach 3.650V per cell, rationale being it's stressful to operate at that voltage for very little gain in capacity. The float voltage is set at 3.375V per cell, unable to rise above that due to limited input voltage. Obviously a low cell count prysmatic bank it's easy to monitor the voltage at the cellular level, unlike drop in replacements where there could be hundreds if not thousands of cells sealed in a container.1500W, 6× Schutten 250W Poly panels , Schneider MPPT 60 150 CC, Schneider SW 2524 inverter, 400Ah LFP 24V nominal battery with Battery Bodyguard BMS
Second system 1890W 3 × 300W No name brand poly, 3×330 Sunsolar Poly panels, Morningstar TS 60 PWM controller, no name 2000W inverter 400Ah LFP 24V nominal battery with Daly BMS, used for water pumping and day time air conditioning.
5Kw Yanmar clone single cylinder air cooled diesel generator for rare emergency charging and welding. -
mcgivor said:Dave Angelini said:Big system, name brand BMS battery banks do not have this critical voltage requirement by the way.
Just putting it out there for casual observers.
The Op here definitely needs to be accurate measuring voltage.
The words chosen were some and recomend, not critical, then again Simpliphi may not be considered a big8 kW Enphase micros AC coupled to a SolArk 12K -
That pdf wasn't as detailed as this one which is the setup info for Schneider Conext gear, there are documents for Outback perhaps others, it gives a float value amongst other information.1500W, 6× Schutten 250W Poly panels , Schneider MPPT 60 150 CC, Schneider SW 2524 inverter, 400Ah LFP 24V nominal battery with Battery Bodyguard BMS
Second system 1890W 3 × 300W No name brand poly, 3×330 Sunsolar Poly panels, Morningstar TS 60 PWM controller, no name 2000W inverter 400Ah LFP 24V nominal battery with Daly BMS, used for water pumping and day time air conditioning.
5Kw Yanmar clone single cylinder air cooled diesel generator for rare emergency charging and welding. -
The BMS in this battery pretty much mitigates all of the voltage concerns in this thread. The manufacturer recommends setting the absorb voltage to 14.6, which is 3.65 volts per cell. This is necessary for this type battery with an internal BMS because it has bleeder boards that balance the cells at that voltage. Keep in mind that the cells do not go out of balance very quickly. So completing absorb often is not a big concern.
The absorb time setting is another setting that will have to be discovered. The recommendation is that absorb end when the battery is accepting 2 amps at 14.6 volts. So, if the charge controller does not have an END AMPS setting, then the absorb time setting will have to be long enough to allow the charging amps to drop to 2 amps. You'll probably have to test several different time periods to get it close.
A float setting is necessary to maintain the battery SOC under load while the sun is still shining. It doesn't have to be a high voltage, in fact it is better be conservative here. 3.35 volts per cell or 13.4 volts is about the max for a conservative setting IMO. Also float charging LFP will not cause any harm if the float voltage is low enough, because the battery will not accept enough amperage to raise the voltage above the float setting.
Rick4480W PV, MNE175DR-TR, MN Classic 150, Outback Radian GS4048A, Mate3, 51.2V 360AH nominal LiFePO4, Kohler Pro 5.2E genset. -
Thanks @Raj174 and @Dave Angelini , that is the clarification that I was looking for. Most of my experience is with Lithium in a motive or stationary application charging from the grid. In those situations charging started when you plugged in the car or when I set the timer to use the cheapest off peak rates. In my new arrangement I am on NEM 2.0 and the optimum strategy may more resemble the off grid strategy of storing as much solar in the batteries as possible.
I will be using Nissan Leaf modules with an Orion BMS and am hoping that the CAN communications saves me the trouble of worrying about any of the above, but if I can't get CAN communications to work I will have to use some relays for BMS triggered events and some of the settings suggested in this thread.
My old LiFePO pack would have a resting voltage of 3.32v regardless if I charged to 3.55v or 3.45v. For a pack like that I used to set the recharge or float setting at 3.25 just to avoid cycling too much near the top.8 kW Enphase micros AC coupled to a SolArk 12K
Categories
- All Categories
- 228 Forum & Website
- 136 Solar Forum News and Announcements
- 1.4K Solar News, Reviews, & Product Announcements
- 199 Solar Information links & sources, event announcements
- 898 Solar Product Reviews & Opinions
- 256 Solar Skeptics, Hype, & Scams Corner
- 22.5K Solar Electric Power, Wind Power & Balance of System
- 3.5K General Solar Power Topics
- 6.7K Solar Beginners Corner
- 1K PV Installers Forum - NEC, Wiring, Installation
- 2.1K Advanced Solar Electric Technical Forum
- 5.6K Off Grid Solar & Battery Systems
- 428 Caravan, Recreational Vehicle, and Marine Power Systems
- 1.1K Grid Tie and Grid Interactive Systems
- 654 Solar Water Pumping
- 816 Wind Power Generation
- 624 Energy Use & Conservation
- 619 Discussion Forums/Café
- 312 In the Weeds--Member's Choice
- 75 Construction
- 124 New Battery Technologies
- 108 Old Battery Tech Discussions
- 3.8K Solar News - Automatic Feed
- 3.8K Solar Energy News RSS Feed