Battery temperature sensor location
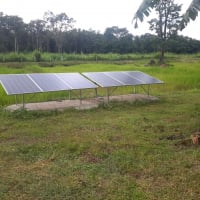
I'm taking a pole of opinions, thought it would be interesting what the outcome would be.
REMEMBER ONE WORD
(1) Install the BTS sensor on the battery.
Second system 1890W 3 × 300W No name brand poly, 3×330 Sunsolar Poly panels, Morningstar TS 60 PWM controller, no name 2000W inverter 400Ah LFP 24V nominal battery with Daly BMS, used for water pumping and day time air conditioning.
5Kw Yanmar clone single cylinder air cooled diesel generator for rare emergency charging and welding.
Comments
-
side
-
Terminal
-
SideOff-grid.
Main system ~4kw panels into 2xMNClassic150 370ah 48v bank 2xOutback 3548 inverter 120v + 240v autotransformer
Night system ~1kw panels into 1xMNClassic150 700ah 12v bank morningstar 300w inverter -
Terminal
I know you are not looking for a reason but... The terminal has a direct, very heat-conductive connection to the battery itself, and so will accurately reflect the temperature of the battery. The plastic outside of a battery is not very heat-conductive, so whatever temperature it reads will not reflect as much the temperature of the battery, and will be more influenced by the ambient air.Off-grid cabin: 6 x Canadian Solar CSK-280M PV panels, Schneider XW-MPPT60-150 Charge Controller, Schneider CSW4024 Inverter/Charger, Schneider SCP, 8S (25.6V), 230Ah Eve LiFePO4 battery in a custom insulated and heated case. -
For side of battery RBTS, take a piece of Styrofoam and hollow out a place for the sensor, then place over sensor/side of battery. Will read case temperature more accurately.
-Bill
Near San Francisco California: 3.5kWatt Grid Tied Solar power system+small backup genset -
Your question is incomplete, so I cannot answer
How many batteries in what configuration and application and location?
I always have more questions than answers. That's the nature of life. -
Terminal for best heat transmission without a lot of mickey mousing stuff stuck on the side of a battery.
If you are forced to use it on a side, add a layer of thermal insulation like fiberglass or foam to keep the ambient temps from interfering. -
Side. nestled between 2 2v cells in the approx middle of bank
KID #51B 4s 140W to 24V 900Ah C&D AGM
CL#29032 FW 2126/ 2073/ 2133 175A E-Panel WBjr, 3 x 4s 140W to 24V 900Ah C&D AGM
Cotek ST1500W 24V Inverter,OmniCharge 3024,
2 x Cisco WRT54GL i/c DD-WRT Rtr & Bridge,
Eu3/2/1000i Gens, 1680W & E-Panel/WBjr to come, CL #647 asleep
West Chilcotin, BC, Canada -
ONLY on the side of one battery in the center of the bank, and only under a rigid foam sheet one, or more inches thick. With multiple strings of batteries it becomes a bit problematic, so would get rid of multi strings, and then place BTS under one battery center of the bank, half way down the side, under rigid foam on the single string of batteries.
Also, would place ALL BTS/RTSes on the same battery, under the same foam sheet -- very easy.
Heat rises, and resistance in battery interconnect crimps and between interconnect lugs and battery terminals will cause heating. Both of these can cause errors in the "battery" temperature that the RTS mounted on a battery lug/terminal, reports to chargers.
IMO, Vic
Off Grid - Two systems -- 4 SW+ 5548 Inverters, Surrette 4KS25 1280 AH X2@48V, 11.1 KW STC PV, 4X MidNite Classic 150 w/ WBjrs, Beta KID on S-530s, MX-60s, MN Bkrs/Boxes. 25 KVA Polyphase Kubota diesel, Honda Eu6500isa, Eu3000is-es, Eu2000, Eu1000 gensets. Thanks Wind-Sun for this great Forum. -
Vic said:
ONLY on the side of one battery in the center of the bank, and only under a rigid foam sheet one, or more inches thick. With multiple strings of batteries it becomes a bit problematic, so would get rid of multi strings, and then place BTS under one battery center of the bank, half way down the side, under rigid foam on the single string of batteries.
Also, would place ALL BTS/RTSes on the same battery, under the same foam sheet -- very easy.
Heat rises, and resistance in battery interconnect crimps and between interconnect lugs and battery terminals will cause heating. Both of these can cause errors in the "battery" temperature that the RTS mounted on a battery lug/terminal, reports to chargers.
IMO, Vic
How would that benefit them? -
Lumisol said:Vic said:
ONLY on the side of one battery in the center of the bank, and only under a rigid foam sheet one, or more inches thick. With multiple strings of batteries it becomes a bit problematic, so would get rid of multi strings, and then place BTS under one battery center of the bank, half way down the side, under rigid foam on the single string of batteries.
Also, would place ALL BTS/RTSes on the same battery, under the same foam sheet -- very easy.
Heat rises, and resistance in battery interconnect crimps and between interconnect lugs and battery terminals will cause heating. Both of these can cause errors in the "battery" temperature that the RTS mounted on a battery lug/terminal, reports to chargers.
IMO, Vic
How would that benefit them?
You will need to ask those manufacturers. VicOff Grid - Two systems -- 4 SW+ 5548 Inverters, Surrette 4KS25 1280 AH X2@48V, 11.1 KW STC PV, 4X MidNite Classic 150 w/ WBjrs, Beta KID on S-530s, MX-60s, MN Bkrs/Boxes. 25 KVA Polyphase Kubota diesel, Honda Eu6500isa, Eu3000is-es, Eu2000, Eu1000 gensets. Thanks Wind-Sun for this great Forum. -
As I said earlier, the "best" choice is strictly dependent on the actual application details and specifics.
You will likely discover that the more actual field experience a person has, the more they lean to toward side mount, sandwiched between batteries - when insulated properly. The reasons have already been described.
Post mounting is quick and easy to install. And in some cases, it can be better - but then.......
Marc
I always have more questions than answers. That's the nature of life. -
I don't want my batteries crowded together in the first place, so the side mount is a less viable choice if you want air flow between the cases as I do.
To each his own, that's why there are options. Some people don't have spaces between batteries and they tent to heat up each other faster so a side mount might work if you are short on space. -
Case in point: the mounting rack for my 2/v cells allows for at max a few mm distance between cells.. that is all.. and it is very hard to squeeze the BTS in between 2 cells.
KID #51B 4s 140W to 24V 900Ah C&D AGM
CL#29032 FW 2126/ 2073/ 2133 175A E-Panel WBjr, 3 x 4s 140W to 24V 900Ah C&D AGM
Cotek ST1500W 24V Inverter,OmniCharge 3024,
2 x Cisco WRT54GL i/c DD-WRT Rtr & Bridge,
Eu3/2/1000i Gens, 1680W & E-Panel/WBjr to come, CL #647 asleep
West Chilcotin, BC, Canada -
Since we've ignored the one word answer asked for, I'll add that my side choice considers that ambient can be really cold, and top mounting could be a problem. I'd rather a controller read a bit high on temp and compensate to a bit lower voltage most of the time, instead of boiling the things dry. It depends.Off-grid.
Main system ~4kw panels into 2xMNClassic150 370ah 48v bank 2xOutback 3548 inverter 120v + 240v autotransformer
Night system ~1kw panels into 1xMNClassic150 700ah 12v bank morningstar 300w inverter -
Yep. My projects drifting out on the arctic ocean are setup very differently than my projects on the equator - which are different than those sitting in metal box in Southern Desert areas vs. a climate controlled battery room, etc. etc.
There is not one correct answer if you want optimum results. So a one word answer is worthless. And yes, we have run tests on this in the field.
Marc
I always have more questions than answers. That's the nature of life. -
Estragon said:Since we've ignored the one word answer asked for, I'll add that my side choice considers that ambient can be really cold, and top mounting could be a problem. I'd rather a controller read a bit high on temp and compensate to a bit lower voltage most of the time, instead of boiling the things dry. It depends.
A lot depends on the space around the bank too, if it's just slightly larger than the bank itself and lined with wood and vinyl flooring over wood or if it's a large concrete room.
My bank is in the former. -
Marc (IMO) is spot on. I worked for years in an electronics reliability lab, and the conditions of operation are everything in temperature evaluation. Ambient air temperature, localized heat traps, room airflow, forced air / convection cooling, charge / operational voltage, current draw, and localized hot spots all affect temperature, and derating.
No one answer covers it but If I were to place a sensor, I'd use an LED thermometer at peak usage time around all of the cells and from there determine a location for a sensor. If the cells were enclosed with forced air circulation I'd use a thermal probe and DVM, slow but it may be the best way available without a lab.
Anyway, I would "think" that the terminal would be a less than wonderful sensor location because the cable itself is a heat sink while cell innards have less opportunity to vent heat.
Oh, P.S. without a corrective action plan after determining that there is excessive temperature, knowing the results of testing is useless.
-
terminal510 watt pv, TS-MPPT 60, Exeltech XP1100, XP600 & XP250 @ 24V, 4x Trojan 105RE, Trimetric 2030, Yamaha EF2400i gen.
-
Terminal to find the best,most direct thermal link to the plates inside.
When I set up in a colder environment I tend to use boxes to house banks for better monitoring with less heat loss, in warmer environments I use boxes, but to mitigate heat gain.
I always use enclosures though but for different reasons in different climates.
Batteries that are too hot or too cold are not happy.
Whether I am installing at the north pole or on the equator, I set it up to maintain the battery enclosure at 70 to 74 degrees. Sometimes it's by heating and sometimes by cooling but the battery ambient temperature is always a controlled variable since it is so critical to the system life.
Categories
- All Categories
- 229 Forum & Website
- 137 Solar Forum News and Announcements
- 1.4K Solar News, Reviews, & Product Announcements
- 199 Solar Information links & sources, event announcements
- 898 Solar Product Reviews & Opinions
- 256 Solar Skeptics, Hype, & Scams Corner
- 22.5K Solar Electric Power, Wind Power & Balance of System
- 3.5K General Solar Power Topics
- 6.7K Solar Beginners Corner
- 1K PV Installers Forum - NEC, Wiring, Installation
- 2.1K Advanced Solar Electric Technical Forum
- 5.6K Off Grid Solar & Battery Systems
- 428 Caravan, Recreational Vehicle, and Marine Power Systems
- 1.1K Grid Tie and Grid Interactive Systems
- 654 Solar Water Pumping
- 816 Wind Power Generation
- 624 Energy Use & Conservation
- 619 Discussion Forums/Café
- 312 In the Weeds--Member's Choice
- 75 Construction
- 124 New Battery Technologies
- 108 Old Battery Tech Discussions
- 3.8K Solar News - Automatic Feed
- 3.8K Solar Energy News RSS Feed