System design help needed
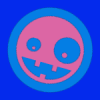
Slipstevens
Registered Users Posts: 4
hello everyone,
I'm needing some help putting together a power system for a small, full time off grid home, any input would be greatly appreciated. The location is Houston, BC, Canada, my daily power needs will be roughly 7500wh. The best location for the array is 700 feet from the house on a open side hill. I have a Magnum Ms4448pae (48 volt) inverter with remote generator start, battery monitoring kit, and 16 220ah 6volt batteries. What I am wondering is how many 240w solar panels should I get,what voltage should they be, how should they be wired for such a long run (also guage of wire I should use), and what charge controller to use with room for possible expantion?
thanks for your time
I'm needing some help putting together a power system for a small, full time off grid home, any input would be greatly appreciated. The location is Houston, BC, Canada, my daily power needs will be roughly 7500wh. The best location for the array is 700 feet from the house on a open side hill. I have a Magnum Ms4448pae (48 volt) inverter with remote generator start, battery monitoring kit, and 16 220ah 6volt batteries. What I am wondering is how many 240w solar panels should I get,what voltage should they be, how should they be wired for such a long run (also guage of wire I should use), and what charge controller to use with room for possible expantion?
thanks for your time
Comments
-
Re: System design help needed
Take a look at the 200 or 250 Classics here http://www.midnitesolar.com/
they also have a good string sizing tool http://www.midnitesolar.com/sizingTool/displaySizing.php which iwll help you with distance and array strings.
there is a thread almost the same as your but I can not remember where right now...
hth
KID #51B 4s 140W to 24V 900Ah C&D AGM
CL#29032 FW 2126/ 2073/ 2133 175A E-Panel WBjr, 3 x 4s 140W to 24V 900Ah C&D AGM
Cotek ST1500W 24V Inverter,OmniCharge 3024,
2 x Cisco WRT54GL i/c DD-WRT Rtr & Bridge,
Eu3/2/1000i Gens, 1680W & E-Panel/WBjr to come, CL #647 asleep
West Chilcotin, BC, Canada -
Re: System design help needed
Welcome to the forum.
Say, why are so many of my fellow BCers getting into solar of late? Did I miss a memo or something?
You're doing pretty good so far.
What you've got with your sixteen 220 Amp hour batteries is 440 Amp hours @ 48 Volts. Lots of power: roughly 10kW hours worth DC.
What we'd normally expect for an array to recharge that:
44 Amps peak current * 48 Volts minimum = 2112 Watts less derating (you're probably above 3,000 feet) of 80% would be a 2640 Watt array. Using 240 Watt panels that would be 11 of them. Pretty hard to set up an array of 11, so you could make it 12 no problem.
Now for the problems.
You're even further North than I am, so how's your back-up power system? Trying to squeeze 7500 Watt hours out of our Winter days is practically a miracle. Sure, you get the cold but you don't get the sun. You practically need a one-on-one array Watt to AC Watt hour ratio.
Other problem is that 700 foot run from array to charge controller. This is MidNite Classic territory as you aren't going to be able to get a high enough array Voltage to make that run otherwise, and be able to handle the inevitable high Voc of -40C temps.
The panels probably have a Vmp around 30, right? With the 2880 array using four panels in series by three strings the Imp would be bout 24 you'd need to use 1/0 to make that run. Who wants to do that? Lots of money. If you put eight panels in series and push the Vmp to 240 and drop the Imp to 12 you can do it on ... looks like 6 AWG. But then the Voc is going to be outrageous (over 300 even without cold weather) and you'd have to use a Xantrex 600V MPPT 80, which costs $1,200.
Definitely a dilemma.
So here's another possibility: could you put the whole power plant where the array will be and run the stable 240 VAC from there to the house? -
Re: System design help needed
I will comment on wire runs. I'm thinking about adding one more solar array about 300 ft from batteries. That's not as long a run as yours, but a similar problem. Here's how I approach it (assuming you have a 3kW array located 700ft away):
1. Cheap solution. #6 wire and a regular MPPT controller Vmp=100V Imp=35A. At full production, you will lose 680W in your wires. You'll need 420m of wire ($2/m at Home Depot) = $840 + Controller $600 = $1440
2. Thick wire solution. #3 wire. Everything else the same. At full production, this wire will lose 340W. At $4/m at Home Depot, it'll cost you $1680 + Controller $600 = $2280
3. High voltage solution. Higher voltage, which allows for thinner #10 wire. Vmp = 400V Imp = 8A. At full production, you will lose only 90W in your wires, but controller (XWCC80-600) will cost $1200. The wire costs $1.20/m in HD Total will be $500 + $1200 = $1700.
The lowest loss solution is (3). Solution (2) is not viable for you because it's both more expensive and more lossy. With solution (1), compared to (3), you save $260, but get extra 600W of losses - you'll need 3 more solar panels to compensate for this.
The problem with solution (3) is that 400VDC is capable of killing you if you touch it, and also that you're stuck with XWCC80-600, which, some people would say, is not as reliable as regularly sized controllers. -
Re: System design help needed
Or you can split the distance by putting the batt bank and electronics in between the array and house, part Hi V DC, rest 110V AC, depends on what your wallet will stand.
KID #51B 4s 140W to 24V 900Ah C&D AGM
CL#29032 FW 2126/ 2073/ 2133 175A E-Panel WBjr, 3 x 4s 140W to 24V 900Ah C&D AGM
Cotek ST1500W 24V Inverter,OmniCharge 3024,
2 x Cisco WRT54GL i/c DD-WRT Rtr & Bridge,
Eu3/2/1000i Gens, 1680W & E-Panel/WBjr to come, CL #647 asleep
West Chilcotin, BC, Canada -
Re: System design help needed
Thanks guys for the fast responses. I was trying to avoid taking down some nice trees but that can be changed in order to shorten the distance to around 120-150 feet or so, hopefully this difference will make things work? For a back-up system all it is right now is a 3500w generator. I'm not living here yet but hoping to be in it for this up-coming winter. -
Re: System design help needed
Shortening the distance from 700 feet to 150 feet will make a huge difference.
For example:
120 Volts @ 24 Amps over 700 feet using 6 AWG results in an 11 percent Voltage drop.
120 Volts @ 24 Amps over 150 feet using 6 AWG results in a 2.5 percent Voltage drop.
There is still the issue of actually deciding on an array size and configuration as that will have a significant difference on the wiring as well as on the charging. -
Re: System design help needed
what would you do in this situation for the array size cariboocoot? -
Re: System design help needed
Are you trying for year-round power? If so, how much do you want to rely on a generator?
I can tell you that in the 100 Mile area where I am maintaining power in the fall when it starts to get cloudy is a real challenge. And my kW hours are about 1/3 yours.
That 7500 Watt hours AC on 48 Volts would be about 174 Amp hours DC, or roughly 40% of your proposed battery bank size. That doesn't give you much leeway for bad weather days without running a generator.
First thing I'd do would be look in to reducing the power needs. Follow that with increasing the battery bank size if needed so that they can be accommodated at 25% DOD. Then be generous with the array size, perhaps even 2X the normal capacity for handling those less-than-perfect days. And still have a generator in reserve. -
Re: System design help needed
Is there any possibility of decreasing your loads? say to 5000wh or so?
KID #51B 4s 140W to 24V 900Ah C&D AGM
CL#29032 FW 2126/ 2073/ 2133 175A E-Panel WBjr, 3 x 4s 140W to 24V 900Ah C&D AGM
Cotek ST1500W 24V Inverter,OmniCharge 3024,
2 x Cisco WRT54GL i/c DD-WRT Rtr & Bridge,
Eu3/2/1000i Gens, 1680W & E-Panel/WBjr to come, CL #647 asleep
West Chilcotin, BC, Canada -
Re: System design help needed
Eventually I will want year round power but for now I will have to use the generator until my wallet allows me otherwise. thanks for the advice and input from others. Once I make some decisions I will be back to pester you some more -
Re: System design help needed
Pay as much attention to generator system design too... A good start (for you) may be to have a nominal sized battery bank to support loads over night and random (smaller loads) during the day with the battery bank. And heavier loads (washing, cooking, pumping water to a cistern, etc.) with a genset.
And add a nominal solar array.
The problem with gensets is they are (typically) fuel efficient at 50% loading or more. Lightly loaded gensets are very common when people by an 8+kW genset (not that expensive, reliable with auto start capabilities, etc.) and you find they are drinking a 1/2 gallon to one gallon of fuel per hour, or more. And you only have 400-1,000 watt of loads (on average, plus a 1.5 HP well pump).
In many cases, it may make sense to have two gensets, one smaller for day to day use (quiet/fuel efficient Honda eu2000i or so family, or Yamaha/similar inverter genset) and reserve the larger genset for backup/larger loads (running the shop, weekly cistern filling, etc.). And then you have the whole fuel selection issue. Diesel, propane, gasoline all have their pluses and minuses.
If you can size the battery bank to genset correctly, use the generator at 50+ loading to recharge the battery bank from 50% to ~85% State of Charge (i.e., relatively heavy/stable genset loading), then the last 15% SOC can be managed with a smaller solar array/or smaller genset a couple times a week to finish the charging.
At this point, it appears that a good genset with full auto start support (rugged, reliable, fuel efficient) is around a 4kW Honda EM4000SX (if I got the number correct for the "deluxe" engine+digital controller). Anything smaller is going to be manual start (push button with manual choke, etc. or pull start) unless you start doing your own modifications and controller design/configuration.
-BillNear San Francisco California: 3.5kWatt Grid Tied Solar power system+small backup genset -
Re: System design help needed
CariboocootSo here's another possibility: could you put the whole power plant where the array will be and run the stable 240 VAC from there to the house?
Time for me to hijack this thread and ask for a clarification for my own needs. If I put my outback system at the aray, 200' from my house, to get a 240 volt run, I would basically be running two 120 volt wire runs from the house to the inverter (AC in) and two 120 volt wire runs from the inverters to the house (AC out).
The alternative is two arrays of 2820 watts at 88 volts dc to the inverter at the house 200' away.
Do I understand a 240 volt wire run and are there any glaring efficiency items between these two runs?
My current plan is to run 4ea of 4/0 aluminum from the two arrays. As a side note; I kinda want to be able to increase the 2820 to around 4000 watts some day as one of my controllers is a fm80.
I figure on 4000 watts at 88 volts is 46 amps and at 120 volts is 33 amps. Is this where the savings in wire might come from?
I hope this is a similar subject that brings understanding for the original poster as well as me.
Thanks
gww -
Re: System design help needed
Remembering that Power = Voltage * Current = V2/R = I2*R
So, if you can increase the voltage by 240 volts / 88 volts = 2.72 : 1 ratio...
So, you can use 2.722 or ~1/7.5 times less copper for the same power. And you have much more "headroom" for voltage drop.
Note that with split phase 120/240 VAC lines, you do have to carry a "neutral" to0--So that does add to your wiring costs.
The downside is the 240 VAC is a "regulated" voltage (needs to be correct voltage for devices to work correctly) where the Vmp-array just has to be > Vbatt-charging plus a couple of volts (for controller losses). So, with very long 120/240 VAC runs, you can have issues with flickering lights when motors start, etc.
Remember that solar arrays do not have "surge current"--Whereas 120/240 VAC do (upwards of 2-5x rated current)--So you still have to ensure your wiring (and transformers, if used) will support the surge current from pumps, etc.
With a typical ~150 VDC maximum input MPPT charge controller, you are looking at Vmp-array of around a 100 volts (unless you are in a climate that does not get cold--then you may be able to go a bit higher in voltage).
.
And you have the Midnite Classic and a Xantrex high voltage MPPT controllers that can support >> 100 VDC arrays (the Xantrex can go probably to around 400 VDC Vmp).
So, my first choice would be to go with a "high array input voltage" charge controller with the battery bank+electronics close to the home (easier to monitor/service battery bank, possibly more stable battery temperature if hot/cold climate if "next/in" home).
If you have no other choice, a remote battery bank+electronics is certainly a possibility and better than trying to send low voltage / high current all that distance.
-Bill "some random thoughts" B. :roll:Near San Francisco California: 3.5kWatt Grid Tied Solar power system+small backup genset -
Re: System design help needed
I guess I should add, there is the option of using Grid Tied inverter(s) at the array, and a GT compatible AC Inverter/Charger at the home... I normally do not like to suggest this option, but it is becoming more common and there are more pieces of equipment that support the GT Off Grid concept (AC off grid inverters that can "control" GT inverters by adjusting 60/50 Hz base frequency to knock the GT inverters off line when the battery bank is full).
Could be very interesting with Micro Inverters (such as Enphase) to build out a scalable systems.
This gets rid of the "240 VAC surge" issue on the long distance wire run... The GT side will not see any surges (and you have 120/240 VAC available for a water pump if can be co-located with the array--use a surge "friendly" pump/vfd/etc.).
-Bill "more than one way to .... " B.Near San Francisco California: 3.5kWatt Grid Tied Solar power system+small backup genset -
Re: System design help needed
gww;
The problem the OP runs into with his extremely long wire run is that if he ups the array Vmp to a point high enough to make wire sizing practical with minimal losses over the distance, the array Voc hits an unmanageable level (especially in Winter).
When dealing with the AC side of things the source Voltage is fixed and the only variation is caused by the affect of loads and wiring resistance.
In your case you want to use 120 VAC, which would have greater V-drop over a given distance for a given wire size than 240 VAC. You are also switching the example from the expected V*A of the array power to the expected V*A of the inverter output (and generator output?).
In the case of a 3648, the output current (continuous) would be a maximum 30 Amps @ 120 VAC. Across 200 feet you would need 4 AWG copper to keep the V-drop below 3%. If you increase the Voltage to 240, the current drops to 15 Amps (for the same power) and the wire gauge goes down to 10 AWG for the same% Voltage drop.
Does this help? -
Re: System design help needed
You can always use a sub-station transformer, to boost the 240VAC to 480VAC, go the long run at HV, and then a step down transformer at the loads. Most wire and conduit is spec'd for 600V
I'm running 240VAC all over, and bought a couple 240 - 24VAC transformers to power gear at the ends of runs, and use a autotransformer to boost 120V genset to 240V for GEN/AC2 input for battery charging.Powerfab top of pole PV mount | Listeroid 6/1 w/st5 gen head | XW6048 inverter/chgr | Iota 48V/15A charger | Morningstar 60A MPPT | 48V, 800A NiFe Battery (in series)| 15, Evergreen 205w "12V" PV array on pole | Midnight ePanel | Grundfos 10 SO5-9 with 3 wire Franklin Electric motor (1/2hp 240V 1ph ) on a timer for 3 hr noontime run - Runs off PV ||
|| Midnight Classic 200 | 10, Evergreen 200w in a 160VOC array ||
|| VEC1093 12V Charger | Maha C401 aa/aaa Charger | SureSine | Sunsaver MPPT 15A
solar: http://tinyurl.com/LMR-Solar
gen: http://tinyurl.com/LMR-Lister , -
Re: System design help needed
CariboohootIn the case of a 3648, the output current (continuous) would be a maximum 30 Amps @ 120 VAC. Across 200 feet you would need 4 AWG copper to keep the V-drop below 3%. If you increase the Voltage to 240, the current drops to 15 Amps (for the same power) and the wire gauge goes down to 10 AWG for the same% Voltage drop
I see you are using an outback inverter. Doesn't the inverter put out higher then thirty amps with grid or generator support? In the manual I see a 60 amp maximun fuse from the house ac. I am learning.
I am getting ready to install soon and want to try and get it right and as cheeply as I can.
I guess my question was; with my inverters the best I can do is 120 volt runs and not 240 volt runs? I wrote an voltage caculator question trying to figure this out. I guess I need to check the cost of 8ea 4gage compared to 4ea 4/0 alum.
If I go with the inverter at the aray would this add up to a total of 4 ground wires with this run or two?
Is there a 240 volt ac run that does not consist of two leggs of 120 volt?
Thanks for your answer
gww -
Re: System design help neededCariboocoot
I see you are using an outback inverter. Doesn't the inverter put out higher then thirty amps with grid or generator support? In the manual I see a 60 amp maximun fuse from the house ac. I am learning.
Mine is a VFX3524 in the middle of nowhere; there is no grid and when the gen is connected it's running loads and charging batteries (no gen support on the strictly off-grid version).
The total input rating is for loads and battery charging at the same time, with a surge factor included. The fuse/breaker rating will be based on this maximum current plus NEC rating, which means it will be higher than the actual expected current. If you apply the NEC "* 1.25 *1.25, then round up" formula to 30 Amps you get 50 Amps.I guess my question was; with my inverters the best I can do is 120 volt runs and not 240 volt runs? I wrote an voltage caculator question trying to figure this out. I guess I need to check the cost of 8ea 4gage compared to 4ea 4/0 alum.
Two things:
You can use transformers to raise/lower the Voltage to and from the inverter. Outback has a 4kW autotransformer available for this purpose. If you use two inverters they can be stacked for 240 Volts. There are a lot of ways of putting Outback equipment together, which is both a blessing and a curse.
Second, aluminium wire is not 100% interchangeable with copper for current handling.
4 AWG copper 120 VAC @ 30 Amps over 200 feet; 2.55% V-drop
4 AWG aluminium on the same power; 4.97% V-drop
To get the same performance on aluminium you need 1 AWG (2.48% V-drop)If I go with the inverter at the aray would this add up to a total of 4 ground wires with this run or two?
The ESG for such a system with that kind of distance would only need one ground wire between the two, as it wouldn't be carrying current. You should drive a ground rod at both locations.Is there a 240 volt ac run that does not consist of two legs of 120 volt?
Yep. Lots of 240 Volt uses don't actually use neutral at all. For the most part the neutral line wouldn't be carrying much current either as one hot leg balances against the other.
Again, there are many different ways to set this up. As such I'm leaving out a lot of info and probably making things more confusing rather than clearer. -
Re: System design help needed
Cariboohoot
I am going to leave this thread back to the original posters questions.
Thank you for your response
gww -
Re: System design help needed
I lied, I guess I still want to hyjack this thread a little longer.
bill
Could you expand on your ideal below a little more?I guess I should add, there is the option of using Grid Tied inverter(s) at the array, and a GT compatible AC Inverter/Charger at the home... I normally do not like to suggest this option, but it is becoming more common and there are more pieces of equipment that support the GT Off Grid concept (AC off grid inverters that can "control" GT inverters by adjusting 60/50 Hz base frequency to knock the GT inverters off line when the battery bank is full).
Could be very interesting with Micro Inverters (such as Enphase) to build out a scalable systems.
This gets rid of the "240 VAC surge" issue on the long distance wire run... The GT side will not see any surges (and you have 120/240 VAC available for a water pump if can be co-located with the array--use a surge "friendly" pump/vfd/etc.).
-Bill "more than one way to .... " B.
Do I understand correctly that this option with my equiptment would basically replace my charge controllers with a batteryless grid tye inverter?
Sorry if this is a sidetrack.
thanks
gww -
Re: System design help neededDo I understand correctly that this option with my equiptment would basically replace my charge controllers with a batteryless grid tye inverter?
No, not replace anything. Just a different configuration of hardware.
You still need an off grid AC inverter (that is capable of being back fed by a GT Inverter) to setup a local 120/240 VAC grid.
The GT Inverter is now plugged into that "local grid" (the off grid inverter output), and "sees" "utility" power. And the GT inverter syncs up and will feed into the local grid.
The Off Grid inverter will simply adjust its output current to support the load + GT inverter. If the load is greater than the GT inverter output, the off grid inverter supplies extra power. If the load is less than the GT output, the off grid inverter starts running "backwards" and absorbs the extra power and sends it to the battery bank (on those inverters capable of this function).
When the battery bank is full, the Off Grid Inverter then takes the AC frequency to +/- 1 Hz off of 60 Hz, which the GT inverter recognizes as a "failed" grid--And the GT inverter shuts down for 5 minutes. The Off Grid inverter goes back to 60 Hz and waits for the cycle to repeat.
You have several off grid inverter and gt inverter options.- The standard off grid MSW inverter--Should not work with GT inverter (GT should require true sine wave input)
- A standard OG TSW inverter that does not accept back feed power (don't know brands/models)
- A standard OG TSW inverter that does accept back feed power, but is not designed/rated/tested for function and does not include battery charger control (battery can over charge, owner must make own method for battery charge control).
- A "new" OG TSW off grid inverter with GT inverter support. Includes logic and hardware to control battery charging and offset line frequency to knock GT inverter off line when needed.
- A Sunny "Island" System (SMA) which varies the frequency off of 50/60 Hz and a GT inverter that accepts variable input frequency to "throttle" back energy output (not On/Off but 0-100% variable output). Very nice, not cheap. The frequency is varied +/- with respect to base frequency so clocks/timers remain accurate "on average".
Clear as mud?
-BillNear San Francisco California: 3.5kWatt Grid Tied Solar power system+small backup genset -
Re: System design help needed
I don't understand. I may after I think on your comments for awhile.
I have been reading and have seen several referances to taking a grid tie inverter that accepts 600 volts dc and coupling it with a battery charging inverter like my outback and this was the system.
I have never got the info for the exact inverters involved and some seemed to think it would work except when it lost sequence at which time it would over charge the battery.
I would think 600 volts would be a pretty small gage wire run.
I don't need a responce as I will probly just run the 88 volts dc from the pv to the house and go with 4/0 gage alum wire. Then my wire should handle any configuration I decide on. I just want to understand as much as I can and if I learn it fast enough I may change if not I am sure what I plan to do will work.
Thanks
gww -
Re: System design help neededI don't need a responce as I will probly just run the 88 volts dc from the pv to the house and go with 4/0 gage alum wire. Then my wire should handle any configuration I decide on. I just want to understand as much as I can and if I learn it fast enough I may change if not I am sure what I plan to do will work.
Why would you need 4/0 AWG wire? 400 ft of it will probably cost a fortune.
That's not an AC run. You're feeding it to the MPPT controller, you do not really need to preserve precise voltage. If you drop a little bit more of voltage, this will not affect MPPT operations, MPPT controller converts it to the voltage needed to batteries and can take wide range of input voltages.
The concen with smaller cable is that there will be a power loss (through heat). Even with much smaller cables, the loss is relatively small. For example, for 400 ft of wire (200ft back and forth) and 40A (assuming 4kW array and approximately 100V) you get the following losses:
#6 wire: 253W
#4 wire: 159W
#2 wire: 100W
Note that these losses are for full blast operations. When array produces at 50%, you'll get only 1/4 of these losses.
Compared to the price of cable, even loss in #6 cable seems very small to me. Such loss may be compensated by installing one more solar panel, which costs $300 (compare to the price of 4/0 cable).
Oversizing the wires for the future makes little sense - it's hard to find a controller that would handle array much bigger than 4kW you already have. -
Re: System design help needed
I believe Bill is referring to AC coupling, wherein a standard GT inverter is fed by the panels at the array site and its 240 VAC output flows to the off-grid inverter, syncs to it, and provides the charging power for the batteries via back-feeding much as it would do a standard grid system.
There are a couple of problems inherent in such a set-up. First is that the long run wire resistance still matters as it can cause enough resistance for the OG inverter's output to look off spec to the GT inverter causing it to shut down. Second is that not all OG inverters are designed to be AC coupled. Xantrex's XW will, certainly SMA's Sunny Island will, and supposedly Magnum is coming out with one that will allow AC coupling. The basic difference is the ability of the OG inverter to skew frequency and shut down the GT inverter when power demands (charging and loads) are met so that the back-feeding does not continue to the point where the batteries are overcharged.
As far as I know Outback inverters are not designed to handle such AC coupling. -
Re: System design help needed
Northguy
When I used an on line caculator I could not put anything in it except 48 volts. To get my wire lose down to 3% I came up with 2/0 copper wire. I matched that with 4/0 alum. I think I was using about 40 amps for this caculation. I couldn't do it with 88 volts and 110 volts ac was about 1/0 on a one way run. I went with alum cause it was half the price of the smaller copper. I will have two arays so about $1000 for the alum. not counting fixtures and copper pig tails.
I would love to do it cheeper and still have a robust system. My solar rack is 12'x40' which will hold two arays of 2820 watts each. One of my charge controllers will do about 4000 watts so I may eventually add to that level. I want to do it right for this. I have worked quite hard trying to figure this out. My panels are 29+ volts each with a voc of around 37 volts. I am going to run them in series of threes. So that adds up to either 3500 watts or 4200 watt. I may push the cc's to these values at some point in the future knowing that they may clamp the amps a bit. I will start with the two 2820 watt arays first.
Are your wire sizes for sure proper for these amps? If so I love it. I have not bought the wire yet.
PS it will be 800' for two arays.
Cariboohoot
Your answer did clarify a bit.
Thanks
gww -
Re: System design help neededAre your wire sizes for sure proper for these amps?
Here's the calculation:
I looked at AWG wire table. In that table, I found for wire #6 its resistance for 1000ft in the column entitled Ohms/Kft. I found the number 0.3951.
You have distance of 400ft (back and forth), which is 0.4 of 1000ft. So I multiplied it by 0.4: 0.3951*0.4 = 0.158. This is a resistance of 400 ft of #6 copper wire. R = 0.158 Ohm.
Now, you can calculate voltage drop: U = IR = 40A*0.158Ohm = 6.32V.
If you were running 120V AC line, that would be too big of a voltage drop. Voltage would be 113. Appliences wouldn't work. So, just as Coot said, you can not use that for 120V AC line. Therefore, when you use calculators, they will tell you that the wire is too thin - voltage drop is way more than 3%! With 48V as you used, it's almost 15% - total disaster.
However, for MPPT controller 6.32V drop doesn't really matter. Instead of 95V, it'll be 88V. It's still way higher than is needed for the batteries.
Now, you can calculate how much power you lose W = UI = 6.32V*40A = 253W. This means that when your panels produce 4kW, the controller will only receive 3,747W. 253W will be used to heat your wire.
If you repeat the calculations with 20A (50% of production), the loss will be only 63W.
You can look at the AWG table and do calculations for other wire sizes, relate these data to wire prices, and decide what wire you like better. -
Re: System design help needed
Don't forget, that aluminum wirego with 4/0 gage alum wire.Powerfab top of pole PV mount | Listeroid 6/1 w/st5 gen head | XW6048 inverter/chgr | Iota 48V/15A charger | Morningstar 60A MPPT | 48V, 800A NiFe Battery (in series)| 15, Evergreen 205w "12V" PV array on pole | Midnight ePanel | Grundfos 10 SO5-9 with 3 wire Franklin Electric motor (1/2hp 240V 1ph ) on a timer for 3 hr noontime run - Runs off PV ||
|| Midnight Classic 200 | 10, Evergreen 200w in a 160VOC array ||
|| VEC1093 12V Charger | Maha C401 aa/aaa Charger | SureSine | Sunsaver MPPT 15A
solar: http://tinyurl.com/LMR-Solar
gen: http://tinyurl.com/LMR-Lister , -
Re: System design help needed
northguy
Thanks for the math. I have been using on line caculators. I had forgotten about the lower loss at lower power. I had actually read that in hugh piggotts windturbine recipe book but had forgotton.
Thanks
Mike95...
Thanks for responding
gww -
Re: System design help needed
Funny thing, I know ebay is not the only place to shop but I looked at wire today there. I can't believe that when I look at direct burial wire the 4/0 aluminum is as cheep or cheeper as all the wire going all the way down to 4 awg aluminum. 2 awg copper is still about double the price. Spent about two hours looking at wire. I don't really know what the connectors to switch from aluminum to copper is but I got tired and will have to look latter.
I am really finding no cheep way to do this.
I am also trying to decide whether to try and crimp and heat shrink my own cables or just buy the 13" battery interconects and inverter feeds already made up from maby naws.
I haven't figured what I am going to do about buss bars yet either. I don't know if I should just get some brass bolts or some flat copper bar.
I got till august to get my stuff squared away. Then I start my install.
So I still have time to get more advice and ask more questions.
I had made up my mind that I was going to have to spend quite a bit on wire. I will probly try to remember the advice I have gotten and then when I go to some box store I will compare what I can get and just by it.
Thanks
gww -
Re: System design help needed
gathering stuff up at a good price is always a challenge. metal prices have gone crazy for sure. sometimes doing it yourself is good if you insure that you do it right. the connections to the cables need to be good. if you live near a place that takes in metals for $ (salvage yards) then you may want to hang there to offer to buy from somebody who may come in with long lengths of copper wire in big gauges. maybe the place itself could offer you some, at a profit for them of course, before it is sent off to be melted down.
as to a bus you have options from diy to premade. premade does not always have the size or numbers of slots you may want/need, but it is good to buy as they are plated to stop corrosion if you find any to suit your requirements. here is an example of some to buy premade,
http://www.solar-electric.com/tbb.html
Categories
- All Categories
- 228 Forum & Website
- 136 Solar Forum News and Announcements
- 1.4K Solar News, Reviews, & Product Announcements
- 199 Solar Information links & sources, event announcements
- 898 Solar Product Reviews & Opinions
- 256 Solar Skeptics, Hype, & Scams Corner
- 22.5K Solar Electric Power, Wind Power & Balance of System
- 3.5K General Solar Power Topics
- 6.7K Solar Beginners Corner
- 1K PV Installers Forum - NEC, Wiring, Installation
- 2.1K Advanced Solar Electric Technical Forum
- 5.6K Off Grid Solar & Battery Systems
- 428 Caravan, Recreational Vehicle, and Marine Power Systems
- 1.1K Grid Tie and Grid Interactive Systems
- 654 Solar Water Pumping
- 816 Wind Power Generation
- 624 Energy Use & Conservation
- 619 Discussion Forums/Café
- 312 In the Weeds--Member's Choice
- 75 Construction
- 124 New Battery Technologies
- 108 Old Battery Tech Discussions
- 3.8K Solar News - Automatic Feed
- 3.8K Solar Energy News RSS Feed