MC connector crimping
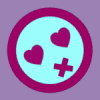
fiddlehead
Solar Expert Posts: 29 ✭
Does anyone know where the best place to purchase a crimping tool for MC 4 connectors and also where to get the connectors?
Any other useful hints about crimping your own cables would be helpfull as well.
Any other useful hints about crimping your own cables would be helpfull as well.
Comments
-
Re: MC connector crimping
From what (little) I understand about the MC 3/4 connectors--you have to "take a class" with the mfg. to be "approved" to purchase the tooling and parts.
For one-time type installations (i.e., you are not an installer)--typically you just purchase some already made-up male/female jumper cables--cut the cables in half and wire them as transition splices to the balance of your system. From NAWS:
http://store.solar-electric.com/incaforsoelp.html
-BillNear San Francisco California: 3.5kWatt Grid Tied Solar power system+small backup genset -
Re: MC connector crimping
You get them from Multicontact USA. Probably run you around $600 for the set with MC4 dies. -
Re: MC connector crimping
The other way besides cutting the cables is just ordering from one of the BIG supply houses like Solar Depot (west coast) or on the east coast Sun I would assume. If you add the item with a big order they are pretty inexpensive."we go where power lines don't" Sierra Nevada mountain area
htps://offgridsolar1.com/
E-mail offgridsolar@sti.net -
Re: MC connector crimping
Thanks, I do installs, so I was looking for something long term that gives me options other than pre-cut lengths -
Re: MC connector crimping
Check Maverick Solar:
http://stores.mavericksolar.com/StoreFront.bok
He supplies a lot of misc. stuff to installers around here. -
Re: MC connector crimping
My solution to MC4 connectors cut them off twist and solder the wires together then slide over glue lined heatshrink.. .. Guaranteed to never be a problem .. all connectors eventually get some corosion on them and the efeciency reduced.
Cheap and very reliable.. recommended by 4 out of 5 Eskimo housewives . and also by me.. -
Re: MC connector crimping
Make sure you check your warranty documents... I have seen some that say this will violate the terms to cut the connectors off.
-BillNear San Francisco California: 3.5kWatt Grid Tied Solar power system+small backup genset -
Re: MC connector crimping
HMM mabe but if they are good panels from reputable company and the panel failed they would have to prove the fault was caused by cutting off the connector,, dam hard to do in my opinion.. But its by far the best way to get a connection that is never going to cause a problem for the 20 + year life of the panel something I doubt could not be said for a plug in connector..:cool: -
Re: MC connector crimping
Their rules, their paper work...
My guess is that they like the ease of testing (one connection type) and probably want the option to resell used (no trouble found & repaired) panels with the original connectors (helps keep warranty costs down).
Whether or not they would reject your claims because of the cut end--I really don't know the answer--perhaps others can elaborate.
-BillNear San Francisco California: 3.5kWatt Grid Tied Solar power system+small backup genset -
Re: MC connector crimping
Well I dont know warranty rules in USA but here in Australia they would have to prove that the cutting the plugs off had something to do with the fault..
And as I see it if it was well made panel it shouldnt be/get faulty anyway. tough luck about them having to repair it then replace the plugs if they want to resell it. -
Re: MC connector crimping
Hehehhe,..As an installer, that would take forever!, cost a fortune in labor.. -
Re: MC connector crimpingYou get them from Multicontact USA. Probably run you around $600 for the set with MC4 dies.
:DThats the ticket! Just break down and buy the kit, I sell the Rennsteig Kits from Germany. it contains Cutter, strippers and die sets for all crimps. SL-1 SL-2 MC-3 MC-4 and Tyco...great item all approved by all panel manufacturers. -
Re: MC connector crimpingMy solution to MC4 connectors cut them off twist and solder the wires together then slide over glue lined heatshrink.. .. Guaranteed to never be a problem .. all connectors eventually get some corosion on them and the efeciency reduced.
Cheap and very reliable.. recommended by 4 out of 5 Eskimo housewives . and also by me.. -
Re: MC connector crimping
Go to www.multicontactusa.com Take the training and learn about correct contact crimping and the reason for it!...FREE...Then qualify to purchase connectors and crimps to make your own line sets....PS (I am NOT A NEW GUY!) at Solar.....and member of several Orgs. NYSEIA>IBEW>NESEA>GreenEnergyCouncil>Member owner usasolarstores.com,NorthEastAlternativeEnergySystemsllc.. NABCEP trained on thermal and PV. 15 installs half thermal. assisted dozens of others. -
Re: MC connector crimping
Probably run you around $600 for the set with MC4 dies. If you are an installer you could justify that $600 but for others thats a lot of money to spend on an item that has no other use ..
And I cant believe the installer that said it would take forever.. I would say less than one minute to strip twist solder and heatshrink.. I use one of those small butane gas torches.. they have very high heat and its pinpoint so only the joint gets hot and it takes about 20secs to heat and apply solder..
And despite any replacement problems(none really you just get a pair of wire cutters to cut the soldered joint off 20 secs) most likely no longer than its going to take to pull a coroded connector apart in 15 years time..
This to me is still the cheapest ,most reliable way to join 2 wires.. I notice none of the installers have been able to say otherwise.. why ? they know its true.. but want you to use thier services so thay can get a ROI on that expensive crimper.. -
Re: MC connector crimping
Actually-- I don't think that twist and solder connections of power wiring is considered legal under the NEC. So, I would believe that soldering is not an an allowed option for licensed electricians.
Soldered connections are known to "blow apart" under high current loads and can leave exposed wiring (high current shorts, lightning strikes).
Generally, most NEC acceptable connections (I am not an expert on the NEC) require physical connections (crimps, mechanical clamping, etc.) for "legal" connections.
-BillNear San Francisco California: 3.5kWatt Grid Tied Solar power system+small backup genset -
Re: MC connector crimping
Its true I also have no idea of what the rules are there..
BUT have terrible trouble believing 2 wires twisted together in line over about a 2in length then soldered and with heat shrink over them would ever blow apart no matter what.. And if it is true then I dont see how a plug and socket would be able to stand greater currents.. if for no other reason the very small contact area of the connectors..
You really never convince me that 2 lengths of #8 wire with a 2in long twist and soldered would fail before a MC socket and plug would if both had to carry a load of say 48v and 100 amps.. :roll: -
Re: MC connector crimping
Soldering is allowed by the NEC - IF the connection is *mechanically* and electrically secure *before* the solder is applied (Section 110.14(B).)
I.e., twist them together properly to get a good connection, then apply the solder.
And, the covering of the solder joint must be => the insulation and protection value of the wire's insulation. So while the solder joint might be perfectly legal - the shrink wrap might not.
For big wire, like battery cables - if you just gotta solder the lugs, crimp them FIRST. Otherwise the connection, while electrically secure, is not considered "mechanically" secure.
But if you have a good crimp...why bother with solder?
Here's a good guide to soldering electrical wiring, with a bunch of excellent illustrations of *mechanically secure* connection methods. Start at the bottom of the linked page, and hit the "Next" link (top left - hard to find) a half a dozen times to see it all:
(EDIT: Just noticed that there are several pages and I was not at the start. Link replaced.)
http://www.tpub.com/content/construction/14027/css/14027_120.htm
[NOTE: Figure 5-28 (Pigtail Splice) is INCORRECT! That illustration shows the wire being twisted *counter-clockwise*, which is wrong. When twisted in that direction, the screwing-on of the wire nut will tend to *loosen* the twisted connection.
The correct way is to twist the wire *clockwise* so that when the wire nut is applied, it will tend to *tighten* the connection.
This is of course not relevant when wire nuts are not used. And probably not relevant on a solidly soldered connection. Nevertheless, it's a good practice.]
Wiles briefly covered the legality of soldering in one of his "Code Corner" articles:
http://photovoltaics.sandia.gov/docs/PDF/Code_Corner_96.pdf -
Re: MC connector crimping
"BUT have terrible trouble believing 2 wires twisted together in line over about a 2in length then soldered and with heat shrink over them would ever blow apart no matter what.."
i'll second what others have said. the wire doesn't blow apart, but if a bad mechanical connection exists this also creates a bad electrical connection. a bad electrical connection has higher resistance and thus creates a point of heat generation and causes the solder to melt fast and explode outwardly in some cases. you can't rely on the solder to make the connection either electrically or physically sound as this is a recipe for failure. in the cases of good connections that already exist it is possible to reinforce what is already good with solder. some locations may be extra wet and a solder coating may help in slowing down or preventing any oxidative damage from occuring in the connection. a lightning strike or even strong emp can still explode the solder no matter what. -
Re: MC connector crimping
from resistance tables:
Silver 1.59×10−8
Copper 1.72×10−8
Aluminum 2.82×10−8
Tin 1.09×10−7
Lead 2.2×10−7
So a solder joint with only the tin/lead solder making the connection, the higher resistance of the solder, will heat up and melt first. If the was a split bolt or something that crimped the copper to copper, that would be better, but after a couple years, would not oxide get working in there, and cause a higher resistance?
Maybe a vaporized solder joint is more spectacular than a vaporized copper
oxide joint ? Maybe a high silver content solder ? (most "silver solder" is only about 5% silver, rest is tin)
http://en.wikipedia.org/wiki/Resistivity#Table_of_resistivitiesPowerfab top of pole PV mount | Listeroid 6/1 w/st5 gen head | XW6048 inverter/chgr | Iota 48V/15A charger | Morningstar 60A MPPT | 48V, 800A NiFe Battery (in series)| 15, Evergreen 205w "12V" PV array on pole | Midnight ePanel | Grundfos 10 SO5-9 with 3 wire Franklin Electric motor (1/2hp 240V 1ph ) on a timer for 3 hr noontime run - Runs off PV ||
|| Midnight Classic 200 | 10, Evergreen 200w in a 160VOC array ||
|| VEC1093 12V Charger | Maha C401 aa/aaa Charger | SureSine | Sunsaver MPPT 15A
solar: http://tinyurl.com/LMR-Solar
gen: http://tinyurl.com/LMR-Lister , -
Re: MC connector crimping
IM not saying "just solder it." You bare about 2in of the wire you twist them together along the length so as to have strong joint (I use 2 pairs of vice grips to do it.. then heat the joint and add the solder then the heat shrink preferably the one with the glue inside.. this makes it very moisture proof. I have done joints like that for use on large luxury boats(above 100ft) and NEVER had a failure and thats in the worst possible enviroment.. marine.
attached twisted wire.. then add heat and solder.. -
Re: MC connector crimping
Please use the MC4 or whatever the LOCKING connector is on the module. I have already had inspectors give me a hard time about using up my remaining Sharp ND-U1F's, which have MC3's! I have done a few side jobs for DIY'ers just for this issue. Not a big deal. If you are an installer, pay for the kit that MC will start you out with. Yes, around $600. If you are installing multiple systems, it will pay for itself in time saved by the third job. Good luck and congrats... -
Re: MC connector crimping
to DWH.. But if you have a good crimp...why bother with solder?.. SIMPLE IT STOPS OR AT THE VERY LEAST DRAMATICLY SLOWS DOWN THE COROSION..ifyou only crimp no matter how good on a marine enviroment that great crimp will fail after a few months with corossion but NOTif soldered also and covered with 2 layers of heatshrink if std heat shrink or one layer if glue impregnated heat shrink.. I have done tiis on luxury boats above 100ft for many rears and no problems.. ..
to MIKE90045 So a solder joint with only the tin/lead solder making the connection, the higher resistance of the solder, will heat up and melt first. If the was a split bolt or something that crimped the copper to copper, that would be better, but after a couple years, would not oxide get working in there, and cause a higher resistance? NO THAT ANSWER IS COMPLETELY INCORRECT
NOTE THE TWIST IN MY POST #22 ITS GOOD MECHANICALLY -
Re: MC connector crimping
hey guys,
what about using anderson connectors(45A) and sealing with tape for those panels that come with junction boxes.
Cheers...
Damani -
Re: MC connector crimpingto DWH.. But if you have a good crimp...why bother with solder?.. SIMPLE IT STOPS OR AT THE VERY LEAST DRAMATICLY SLOWS DOWN THE COROSION..ifyou only crimp no matter how good on a marine enviroment that great crimp will fail after a few months with corossion but NOTif soldered also and covered with 2 layers of heatshrink if std heat shrink or one layer if glue impregnated heat shrink.. I have done tiis on luxury boats above 100ft for many rears and no problems.. ..
to MIKE90045 So a solder joint with only the tin/lead solder making the connection, the higher resistance of the solder, will heat up and melt first. If the was a split bolt or something that crimped the copper to copper, that would be better, but after a couple years, would not oxide get working in there, and cause a higher resistance? NO THAT ANSWER IS COMPLETELY INCORRECT
NOTE THE TWIST IN MY POST #22 ITS GOOD MECHANICALLY
Totally disagree with this post! This is not how modern boats are built and serviced. A crimped marine connection with heat sealant shink tubing sitting in bilge water lasts for decades. Weakening a wire by soldering and then subjecting it to vibration is where failures are born. If you use the best practices when soldering and have it inspected it is possible to do really good work. It just is too easy to have failures and that is why the industry has stopped soldering."we go where power lines don't" Sierra Nevada mountain area
htps://offgridsolar1.com/
E-mail offgridsolar@sti.net -
Re: MC connector crimping
This is not how modern boats are built and serviced
Its ok for us in Australia to be using old fashioned methods.. something about if its been good for the last 20 years mabe its still a good idea..
Its ok to me .you wire up all the boats you do anyway you are happy with.. im sure you have done many more big boats than me (the last one I worked on used over 5klm of power wiring.And the owners are happy it all works ok.. so dont you go telling them its not done to your standard or mabe they get angry with us poor workers. Me I just keep doing it the"wrong" way until someone stops paying me for my work.. or I give up work im already past retirement age.. -
Re: MC connector crimping
In the electronics and telecommunications industry, soldering wire connections has been abandoned decades ago.
Soldering creates a "fulcrum" point in the wire where bending forces are focused. Causes the copper to work harden and fail. Crimp connections do not concentrate bending forces near as much and the wire will last much longer when subjected to bending/vibration.
I have also had problems with corrosion as flux gets wick up the strands of the wire and attracts water/moisture. Rosin core (and the newer no-clean fluxes) reduce the problem--but I still try to avoid soldering because of the contamination issues.
A properly made crimp connection (high enough pressures and properly designed connector+crimping tool) will be gas tight anyway. Solder and flux should not be able to enter the crimp joint.
Also, I wonder if soldering tends to weaken the crimp by annealing the copper (relaxing the internal copper stresses). May be less of an issue if the solder joint is made with a temperature controlled iron. Using an uncontrolled temperature iron (or a propane torch) will run the risk of reaching annealing temperatures.
Not to mention the problems of cold solder joints (moving the joint/wire while the solder is still cooling).
Lastly, solder, very roughly, has about 10x more electrical resistance vs copper wire. In high current circuits (short circuits, lightning, etc.), this causes localized heating which can easily melt the copper and cause the joint to physically fail (especially if the joint is not crimped or mechanically secured). This is why soldering connections (without mechanical securing) is not allowed by US codes.
Regarding marine requirements in the US ([FONT=Verdana, Arial]American Boat and Yacht Council; secondary source)[/FONT]:- [FONT=Verdana, Arial]11.16.3.7. Solder shall not be the sole means of
mechanical connection in any circuit. If soldered, the
connection shall be so located or supported as to
minimize flexing of the conductor where the solder
changes the flexible conductor into a solid conductor.[/FONT] - [FONT=Verdana, Arial]EXCEPTION: Battery lugs with a solder contact
length of not less than 1.5 times the diameter of the
conductor.[/FONT] - [FONT=Verdana, Arial]NOTE: When a stranded conductor is soldered, the
soldered portion of the conductor becomes a solid
strand conductor, and flexing can cause the
conductor to break at the end of the solder joint
unless adequate additional support is provided.[/FONT] - [FONT=Verdana, Arial]11.16.3.8. Solderless crimp on connectors shall
be attached with the type of crimping tools designed
for the connector used, and that will produce a
connection meeting the requirements of E-11.16.3.3.[/FONT]
If you have issues with moisture, then get a compound designed to place on the wire before crimping... Most people probably use a silicon grease (even used on plug connections to seal out moisture--also used for high voltage ignition systems). For tough conditions, use a conductive grease with anti-oxidants.
-BillNear San Francisco California: 3.5kWatt Grid Tied Solar power system+small backup genset - [FONT=Verdana, Arial]11.16.3.7. Solder shall not be the sole means of
-
Re: MC connector crimping
Working on boats some folks get excited about how big of a boat or ship they have worked on. The people who go out on the oceans of the world "know" that all boats are small on the ocean! Either way nothing personal"we go where power lines don't" Sierra Nevada mountain area
htps://offgridsolar1.com/
E-mail offgridsolar@sti.net -
Re: MC connector crimping
Believe it or not there is a lot more involved in wiring up a 100ft boat than for wiring up one or three items in a 20ft runabout
At no time did Iever suggest not crimping the wire to the lug first or with length ways twisting the joining of wires BEFORE SOLDERING .. A good mechanical joint is necessary BEFORE SOLDERING
As I said you do it your way Ill do it my way.. -
Re: MC connector crimping
Rennsteig - I bought that from a solar distributor - don't know if it's ok to mention who here. It was about $600 and works for MC3 and MC4.
In a marine environment I guess I might make the connection and heat shrink the whole thing. Does that sound good? Maybe I could start doing it as SOP. I tape the MC3s partially for mechanical reasons and partially to seal from moisture.
Sometimes we have to undo things and redo them - seems like that would be a big pain with heat shrink though.
I've thought about using the conductive grease in junction boxes, but it seems like you are introducing a possible short. I mean on one job, if you are really careful, it would probably be best. In the long run doing it over and over, you might end up with a problem.
Categories
- All Categories
- 229 Forum & Website
- 137 Solar Forum News and Announcements
- 1.4K Solar News, Reviews, & Product Announcements
- 199 Solar Information links & sources, event announcements
- 898 Solar Product Reviews & Opinions
- 256 Solar Skeptics, Hype, & Scams Corner
- 22.5K Solar Electric Power, Wind Power & Balance of System
- 3.5K General Solar Power Topics
- 6.7K Solar Beginners Corner
- 1K PV Installers Forum - NEC, Wiring, Installation
- 2.1K Advanced Solar Electric Technical Forum
- 5.6K Off Grid Solar & Battery Systems
- 428 Caravan, Recreational Vehicle, and Marine Power Systems
- 1.1K Grid Tie and Grid Interactive Systems
- 654 Solar Water Pumping
- 816 Wind Power Generation
- 624 Energy Use & Conservation
- 619 Discussion Forums/Café
- 312 In the Weeds--Member's Choice
- 75 Construction
- 124 New Battery Technologies
- 108 Old Battery Tech Discussions
- 3.8K Solar News - Automatic Feed
- 3.8K Solar Energy News RSS Feed