Charge rate on a hot day
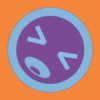
(2x) 100w panels, total 200w. I am getting 50w to 67w Watts or so on full sun, but very hot and humid out. 81F to 87F. Is this the watts I should be getting with that heat? In Ottertail city Minnesota, from about mid June untill today(july22 2024). In may I rebuilt/updated my system and I was getting 187w on full sun displayed On my old eppever mppt. I now have a new Litime MPPT. And a new LItime bat. Was it perhaps the changing of my system? Like an error or issue? Or is the the weather? Slightly Stressed and confused. I kinda want all those 200 watts right now. Running my generator alot now.. So I tested each panel, giving 16.5v to 19.5 volt full hot humid sun, w/ slight haze out. The back of the panel says 21.5v (max?).- "Open Circut Voltage) it was pluged in, but I removed the plastic back and tested. Additionaly, the panel notes: "Optimum Opperating Voltage - 17.5v" Renogy panels. Thanks.
Comments
-
Yes, No sort-of...
SO solar panels produce less in heat. Normally about 75% of their rated value. This is called Normal operating Cell Temperature value or NOCT. Some panels publish these values on their info sheets. Here are 2;
If you are only getting 50-65 watts combined out of the 2 panels. You might first look at the state of charge on your battery, Lead acid batteries charge in bulk to about 80% of full then they accept less current.
Next would be to question if your MPPT charge controller is real or PWM. Then look at how you are wired into the MPPT controller. MPPT controllers NEED to have about a 30% head room about the charging voltage to work properly. So likely need them in series if the controller is designed to handle their output.
Also check voltage drop in the wire distance run from panels to charge controller/battery bank and you connections, all tight and well made? NO alligator clips on the batteries but real hardwire connections?Home system 4000 watt (Evergreen) array standing, with 2 Midnite Classic Lites, Midnite E-panel, Magnum MS4024, Prosine 1800(now backup) and Exeltech 1100(former backup...lol), 660 ah 24v Forklift battery(now 10 years old). Off grid for 20 years (if I include 8 months on a bicycle).
- Assorted other systems, pieces and to many panels in the closet to not do more projects. -
OP. Keep in mind that your system will only produce what your loads demand. If your batteries are at 100%, your system will only produce enough to supply your loads.As an experiment, try putting a large load on your system during full sun. You’ll likely see higher production from your array then.Best of luck.Off-Grid in Terlingua, TX
5,000 watt array - 14 CS 370 watt modules. HZLA horizontal tracker. Schneider: XW6048NA+, Mini PDP, MPPT 80-600, SCP. 390ah LiFeP04 battery bank - 3 Discover AES 42-48-6650 48 volt 130ah LiFePO4 batteries -
What the folks said above... Plus a little more detail...
Guessing this is your MPPT solar charge controller?
https://www.litime.com/products/litime-30a-mppt-12v-24v-auto-dc-input-solar-charge-controller-with-bluetooth-adapter
It can take up to 100 VDC as Vpanel-max input voltage... Are your two solar panels wired in series or parallel? These panels should be wired in series to get your Vmp-array into the 29+ VDC range (hot day).
Also, check the wiring from the MPPT controller to your battery bank. Ideally you want 0.05 to 0.10 VDC Max voltage drop from controller to battery bank at full current. Too much voltage drop, your battery bank will charge slower (MPPT controller will output the correct charging voltage, but the battery bank sees lower charging voltage because of the wiring drop--And reducing battery charging current).
-BillNear San Francisco California: 3.5kWatt Grid Tied Solar power system+small backup genset -
I have a lifepo4 200ah. It charges at 50w to 60w even when it is at 13.0v which is about 30 percent. It seems to always charge at this PV wattage no matter the voltage of the battery, even when its very low. Great point though, thank you. I also tried putting some heavy loads on the battery bank and checking the 50w to 60w and it unfortunate stayed the same. Smart experiment though, Thank you. Good to know.
I have now redone alot of wiring with extra heavy gauge high quality cable, where it was slightly reduced at one point going into the MPPT. Very Solid soldering, and very nice crimped tight and soldered pure copper bolt on connectors etc. Bolted it all very tight. And marine grade 3/1 shrinking over the solderings. I put alot into it to make it 100 percent. I have one solder joint left, that I have to dig up, it is buried underground. I have the feeling that it's good, but I am going to solder and connect it properly anyway, ofcourse.
My voltage at my panels individually appears to be the same voltage at my MPPT
Right now with in-direct sun, and clouds. 5:25pm Ottertail, Minnesota, August 3rd. 16.35v on each panel individualy, and aswell at the MPPT 16.35v.
I currently have it wired with the negative from each panel to a main negative lead going to NEG terminal on MPPT. And same for positive. Does that say which way I wired it? Is it correct? This must be parralell concidering it did not double the voltage.
Also the same voltage at the MPPT may indicate this last connection under ground is okay... and the cable distance/gauge provides no voltage drop. but I am going to check and solder it very solid anyways.
I am pretty sure it is 8g cable at 80feet. It's 80 feet I just measured it but I put the cable in 6 years ago and there is no markings on it. I think some of it was from a Plasma cutter, I'm 95.6 percent sure it's 8 gauge.
But it should be good because my last MPPT for my Lead acid setup showd I was getting 180 PV watts..righr before i changed it. very interestine I had it wired parralell for that...
I may have to try a new MPPT and see what happens.
Bill my MPPT is a 60amp NON Bluetooth MPPT from Litime. Yes I keep spending extra on large components because i want to expand it to a larger system. I also have a 2000w samlex puresine inverter. At this point My plan is to keep adding panels and batteries when I can.
I'm no solar Profesional but I think it's coming together somewhat OK. Haha
Bill im not sure how measure the voltage drop from MPPT to Battery. The voltage drop from my MPPT to Battery should be very minimal, i hope and presume, because I used a 6AWG at 2 feet and 8 inches. But I'm not sure does that sound right? It's 12v lifep04 200ah if that matters. -
I think my 60A Litime MPPT has a max voltage of 150v. Is there minimum voltage for these? Or is it just recomended to go closer to the maximum...?🤔
I have the panels in series now. That was wayyyyyyy easier than I expected. I was ready to snip and solder, and cover with water proof shrink and or research adapters and order adapters. Haha.
I had all of the click on adapters as I'm sure you know. It took about 2 easy. Minutes.
Ofcourse I am at 30volts. With heavy clouds. And ofcourse my PV charging watts appear to be much the same, concidering I increased my voltage but sacrificed my amperage.
PV watts are 20w right now with clouds and 30v
I just don't understand why I was at 180 plus watts with my old cheap epever and AGM battery.
I still have to check the underground solder joint. And then my last effort is to pop a new MPPT in. -
If your batteries are full your controller won't pass any power unless you put a good load on your system. Minimum voltage would need to be say 8 volts higher than your battery but as you found out, wiring in series is the best, easiest method. You are not Sacrificing any amps, your MPPT controller will get maximum current to your batteries when you need it. Current will multiply substantially when the controller does it's voltage conversion.
2.1 Kw Suntech 175 mono, Classic 200, Trace SW 4024 ( 15 years old but brand new out of sealed factory box Jan. 2015), Bogart Tri-metric, 460 Ah. 24 volt LiFePo4 battery bank. Plenty of Baja Sea of Cortez sunshine.
-
Max voltage of 150 VDC means do not exceed. Basically, cold/sub freezing days, Voc, etc. means array voltage is higher than Voc-std (standard temperature/test conditions)...
If you are in the northern mountain during winter--A 150 VDC Max input voltage works out to around 100-110 Vmp-array-std max "safe working voltage".
And, the typical "optimum" Vmp-array would be around 2x battery bank voltage... A near 15 VDC battery would work "optimally" with a Vmp-array-std of 30-40 volts (assuming hot weather and almost 20% drop of Vmp-array-hot conditions).
Generic MPPT controller example for a 24 VDC battery bank:
https://www.manualslib.com/manual/1185794/Outback-Power-Systems-Mx60.html?page=13#manual
Note that it is almost always "better" to go with the higher voltage array because the slightly less efficient controller makes up for the lower losses due to wire heating (P=I^2 * R). I.e., 2x higher voltage means 1/2 the current, and either 1/4 the wire heating losses, or you can use much smaller diameter cable for the "same" losses (typically we aim for 1-3% wiring losses).
Also, if you have to install the array farther from the solar controller--You can save a bunch of money on array wiring cost (array to controller) when working at higher array voltages.
You can go from 36-110 VDC (hot summer to well below zero winter) and the controller will be "slightly" less efficient as the Vmp-array approaches the "higher limits".
-BillNear San Francisco California: 3.5kWatt Grid Tied Solar power system+small backup genset -
After I switched the panel wiring to Series the watts do seem to be increased. But I keep having to leave the house in the mornings for the entire day. And the one day I was home, It was cloudy all day. But I was hitting over 100 watts already this late morning! So I think we fixed it! Wow lots to learn. Lots of info. But I like it all. My dad was an electrician!
So with a larger charge controller more voltage is required. Okay.
Now I need to pop another 100 watt panel in, I have to to work out concerns with my 8g cable running 80feet to MPPT. I wonder If that can handle 300w. Also I wonder about panel compatability. I have two renogy 100w panels now, each are a few years apart and I noticed on the back voltage was slightly different. And now when I shop it appears these renogy panels are even more different.
So panel adding and learning compatability is my next feat. I also have a new, 30w panel laying around from a solar home lighting kit, and two 100 watt panels that will be used for a solar well pump kit too, that I could use for now. I suppose it would be silly to just assume those could link into my panels in series? What key numbers should I look for?
-
For connecting panels in series, you want to "match" the Imp (current maximum power) to within 5% or better (best) or at least within 10% for optimum power from the array (I.e., a 10 amp and 9 amp panel would be withing ~10%).
For connecting in parallel, you want to "match" Vmp (voltage maximum power) with in 5% to 10% or better (I.e., closer to exact match is best).
If you have several strings, the Imp of the series panels need to "match", and the parallel strings Vmp-string should "match".
If you have a "mix" of panels, matching series current and/or voltage of the panels can be difficult. And building an array from wildly different panels can be difficult to justify (more wiring connections, adding a "little panel with a large panel, etc.).
I.e., you could have 3x 100 Watt panels in series and 3* 30 Watt panels in series, then parallel connect them (say Vmp-panel = 18 volts, 3*18 volts = 54 Volts Vmp-array) and 3*18 volt 30 Watt panels in series for 54 Volt Vmp-array).
Also when you have (typically) 3 or more parallel strings, you need to put series fuse/breaker for each string to reduce the chances of fire from short circuits... If you have 100 and 30 Watt panels, the 30 Watt panels will need smaller rated fuses/breakers if "mixed" with 100 Watt panels on the same array.
You can get into some other issues... Many smaller/older panels are not really rated for 600 or 1,000 VDC vs the new large format panels. So you are getting "out of the box" for higher voltage array for smaller panels.
Regarding 3x 100 Watt panels with (guess) Vmp-panel = 18 volts (+/-)
Imp = Pmp/Vmp = 100 Watts / 18 volts = 5.56 Amps Imp
Looking at a typical AWG wiring chart, 8 AWG wiring can be rated for:
https://usawire-cable.com/wp-content/uploads/nec-ampacities.pdf
40 to 55 Amps (copper) depending on insulation grade...
Using a voltage drop calculator for 3*18=54 volts Vmp-array, Imp=5.56, one way wire run 80 feet of 8 AWG cable.
Check a voltage drop calculator, some use round trip length):
https://www.calculator.net/voltage-drop-calculator.html
So, 80 feet of 8 AWG is 1.3% voltage drop--That is a small amount of energy loss... And 8 AWG is way over the 5.56 amps you will be sending through the wiring.
(NOTE: There are lots of details and deratings for NEC wiring charts--The above is a first level simplification of what is fully documented in the NEC code books).
Adding a single 30 Watt panel--Don't even bother. Adding two more 100 Watt panels (if they are the same Vmp/Imp rating as your other three panels and your controller max Vpanel rating accepts the higher voltage), just make a 5x panel series array....
-BillNear San Francisco California: 3.5kWatt Grid Tied Solar power system+small backup genset -
Okay good info thanks.
I used my 2, 100 panels that are for the solar well pump kit for now. The IMP for all panels are around 5.5amps.
So now I have 4, 100 watt panels in series. it appears my 8g copper cable at 80 feet should be enough considering amperage stays the same at around 5a when wired in series? My mppt states watts at around 220w and voltage around 68v, coming from the panels. Still a bit low for full sun, but if i recall correctly, max wattage is at about 3pm and 4pm for my situation and it is 1230noon.
Readings appear to change somewhat drastically based on the angle of the panels, 45 degree angle seems to be good right now. but my two previously installed panels are most likely far too vertical. I probably have to change them. I installed them long ago, in a hurry. I didn't think that angle was so important and I also didn't want to snow to stick on the panel, here in Minnesota.
And I do think that 80ft cable I used should be fairly quality, because it came from a nicer Plasma cutter. I would assume they would use pretty good wires and Sheild. But not sure. It is pure copper. -
The watts remained the same 220w even when I put a very heavy draw on the battery bank. To eliminate the possibility of a full battery charge rate.
-
What is the maximum Array Input voltage for your controller?
Where are you at? Minisota?
If your controller's Max array input voltage is 100 VDC, 4x panels in series may be too high of Voc-array-cold--And could exceed 100 VDC during the winter. If this is the case, you would keep your 2x panels in series * 2 strings (your 4 panels) and put them in parallel.... Yes the current will couple, but you are still looking at 2.6% voltage drop--Still not bad (typically aim for 1% to 3% voltage drop for wiring). With MPPT controllers and higher voltage arrays, even if you have higher voltage drop--The controller will work fine--You just lose that "extra power" as voltage drop/wiring heating (small amount typically).
With Solar MPPT charge controllers, the Vmp-array should be relatively consistent (around 80% to 100% of Vmp-array-std typically). As the batteries reach over 90% State of charge, the charging current will fall, and the array voltage will approach Voc-arry (and in sub freezing weather, even higher). You do not ever want to exceed Vpanel-max input voltage for your MPPT controller--It is pretty easy to fry the transistors in the charge controller with too much voltage (and some controllers will log the over voltage and void the warranty).
-BillNear San Francisco California: 3.5kWatt Grid Tied Solar power system+small backup genset -
The max voltage for my MPPT is 150v. Its a Litime Non Bluetooth 60A MPPT. Okay good to know I need to be at a 120vmp to 150vmp array. (80%-100%) So 6, 100 watt panels would be pretty good?
I suppose I am not getting appropriate charge functions and efficiency with running this 150vmp with a 80 vmp array?
Can I still keep the same 8g cables ran at 80 feet? Because series wiring array holds that 5 to 6 amp current?
I am in ottertail City, Minnesota.
Thanks Bill.
You've clarified ALOT -
That is great... 150 VDC gives you lots of headroom.
Assuming a 12 volt battery bank, more or less, you can operate the array at Vmp-array at ~30 Volts to 100+ volts in almost any condition. "Optimum" harvest voltage for a typical MPPT controller is roughly 2x battery bank voltage--And you will lose a another percent or 2 if you go higher voltage (see previous post). Other than the controller needing good ventilation (to prevent running hot/over heating), don't worry about this "reason" for picking array voltage.
There are other "better" reasons regarding the array sizing (series/parallel questions). More or less, going with higher voltage array allows smaller AWG/longer cables from array to charge controller (always keep controller to battery cables short and relatively heavy AWG cables--Another post, if needed). You could have 4 panels in parallel and would need a a "combiner box" (with 4x fuses or breakers) to protect the array and panels. With 4 panels in series, you do not need the extra expense of the combiner box, heavier cables from 4x more current, etc...
Here is a nice program that lets you try different array sizes/configurations:
https://www.midnitesolar.com/sizingTool/index.php
For example (numbers are close but made up):
Depending on your panel's exact ratings, you can go 5 in series, and possibly 6 panels (winter cold causes Voc and Vmp to rise). You can plug in your panel ratings, local temperatures, and see what answers you get.
Regarding a 60 Amp controller, the maximum "cost effective" array would be (numbers are always approximate):
60 amps * 14.75 volt battery * 1/0.77 panel+MPPT controller deratings = 1,149 Watt array "max cost effective"
1,149 Watt "max" array / 100 Watt panels = 11.49 panels ~11-12 max 100 watt panels suggested.
I.e., 5 series * 2 parallel = 10 panel array
6 series * 2 parallel = 12 panel array
3 series * 4 parallel = 12 panel array (need combiner box, heavier cables from combiner to charge controller, $$$+)
More or less, the MPPT controller will "clip" output at high noon, on cool clear days to 60 amp output to battery.
As you can see, MPPT controller are related for max output current at 12/24/48 volt battery banks. At some point, you have the choice of a second controller or change to 24 or 48 VDC battery bank (new AC inverter, backup charge AC charge controller, etc.)... Choices...
-BillNear San Francisco California: 3.5kWatt Grid Tied Solar power system+small backup genset -
To test individual PV panels use the short ckt test. Printed on the panel spec sheet is the short ckt current in amps. make sure your ammeter is capable of twice printed current, plug the Pos and Neg panel leads into the meter or into each other if using a clamp on meter. Don't worry an isolated panel can't generate enough current to cause sparks or burn its own leads. Don't do this test on day with thunder heads in the sky as those big white reflector can momentarily almost double the 1000 watts per square meter hitting the earth. It's folly to try to test panels with any thing other than a known fixed load, short ckt being the most accurate.
Categories
- All Categories
- 229 Forum & Website
- 137 Solar Forum News and Announcements
- 1.4K Solar News, Reviews, & Product Announcements
- 199 Solar Information links & sources, event announcements
- 898 Solar Product Reviews & Opinions
- 256 Solar Skeptics, Hype, & Scams Corner
- 22.5K Solar Electric Power, Wind Power & Balance of System
- 3.5K General Solar Power Topics
- 6.7K Solar Beginners Corner
- 1K PV Installers Forum - NEC, Wiring, Installation
- 2.1K Advanced Solar Electric Technical Forum
- 5.6K Off Grid Solar & Battery Systems
- 428 Caravan, Recreational Vehicle, and Marine Power Systems
- 1.1K Grid Tie and Grid Interactive Systems
- 654 Solar Water Pumping
- 816 Wind Power Generation
- 624 Energy Use & Conservation
- 619 Discussion Forums/Café
- 312 In the Weeds--Member's Choice
- 75 Construction
- 124 New Battery Technologies
- 108 Old Battery Tech Discussions
- 3.8K Solar News - Automatic Feed
- 3.8K Solar Energy News RSS Feed