Need help setting up solar electric system on our converted bus/motor home
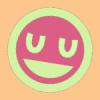
I really would appreciate your detailed installation technical advice.
I'm using "cable distance" as the measurement of one positive or negative cable.
The bus/motor home is presently being supported by a 120 volt 20 amp electric line. We have to be careful not to overload the line.
We have purchased three 175 Watt Monocrystalline solar panels, one 60 amp MPPT controller, and a 3000watt pure sine wave inverter
We also have a transfer switch to disconnect the 120 volt line power from the system when transferring to the solar/battery energy.
1. We have (5) 12 volt batteries mounted in the bus/motor home: (2) 135 AH deep cycle lead acid, (3) group 31 100 AH lead acid
2. The cable distance from the (3) group 31 batteries to the controller location is presently 20', with 20' of 1awg gauge copper cable. ( This once was used to start a air conditioning compressor motor )
All batteries are using bus frame for negative "ground" and 1awg copper cable for positive charge.
All batteries are connected in parallel
3. The cable distance from the (2) 135AH deep cycle batteries to the controller will be 3'.
4. The cable distance from the inverter to the controller will be 3'
5. The cable distance from (3) 175watt ( wired in series) solar panels to the converter will be 100'
The controller, inverter, and connect-disconnect switch will all be mounted in a separate well vented compartment under the present location of the 12volt fuse panel and 120 volt circuit breaker panel.
The bus is located in a shady spot and the panels will be mounted 10' above the ground in a sunny spot..
I have been researching a lot and am frustrated and somewhat confused.
Comments
-
Welcome to the forum TellGRBill,
Regarding cable length for voltage drop calculations... It depends on which website/chart you use. For example, this one uses "one way distance" assuming that this is a round trip with two equal AWG/Size cables:
https://www.calculator.net/voltage-drop-calculator.html
You have not talked about your loads. A 20 Amp @ 120 VAC line can supply, at best, (20a*120v=power) 2,600 Watts. And for utility supplied power, that is not a huge amount of power (Watts or rate of energy usage).
What we do not know, is are you using 500 Watts a few hours a day (500 Watts * 2 hours per day = 1,000 Watt*Hours per day--Not a lot), or 500 Watts * 24 hours per day = 12,000 WH per day (or *30 days = ) 360,000 WH per month = 360 kWH per month--An "smaller than average" North American home load (typically around 500-1,000 kWH per month).
The idea is to measure/estimate your daily energy usage... Use that to size your battery bank (say 2 days of storage, and 50% maximum planned discharge for longer battery life)... Then size the solar array / backup genset / etc. to keep the battery bank charged (happy).
At present, you have a mixed battery bank of 570 AH @ 12 volt of various lead acid batteries in parallel--Which would typically be used with a maximum AC inverter of (very roughly) 1,500 Watt AC inverter... A 3,000 Watt inverter (loaded to 3,000 Watts continuous and 6,000 Watt surge) would quickly drain, if not collapse, the battery bank:- 3,000 Watts * 1/0.85 AC inverter eff * 1/10.5 VDC inverter cutoff voltage = 336 Amps @ 3,000 Watt load @ 1/2 discharged 12 volt battery bank
http://www.smartgauge.co.uk/batt_con.html
As well as, ideally, matching battery type/capacity/age is also helpful to keep battery maintenance/debugging to a minimum (you don't want one or two batteries failing every 1 year--As an example).
Also, roughly, where are you located? Solar panels only work in full sun (no shade). Depending on your location (weather, seasons, etc.), the harvest from a solar array is highly variable/location specific.
There are lots of calculations I can do here... But at this point, you really do not have a well balanced system (battery bank too small for inverter, solar panels are on the small size for the battery bank, and the existing array would have problems trying to keep the battery bank charged with large AC inverter--And large AC loads?).
Is this solar system for emergency backup power (utility service fails) or just to save money, or what? If you already have utility power to the RV... A backup genset + stored fuel (propane, gasoline, etc.) would usually be a less expensive solution for a few days of backup power for a couple times a year.
-BillNear San Francisco California: 3.5kWatt Grid Tied Solar power system+small backup genset -
Your detailed comments are appreciated and the time you spent very generous. I'll try to answer as clearly as I can.1. Since I wrote the details, I have found that I have more carefully measured a direct route from the controller to the solar panels+ 70'2. I have also obtained some 1/0 AWG copper welding cable from storage that will connect from the controller to the solar panels.3. I now have enough 1/0 AWG copper welding cable to connect both battery banks,.4. I plan to run the 1 AWG power cable presently connecting the two battery banks to connect to a negative bus, from the 3 batteries, and connect all negatives to that negative bus.5. I just ordered #4 AWG welding cable to connect between all components: controller, inverter, transfer switch and + & - bus6. The maximum power usage is estimated (roughly) at 2400 Watt hours, but normal usage is much less, I think.7. I purchased the 60 amp controller and 3000 Watt inverter not because we are ready to maximize use, but to prepare for possible future expansion and because I thought that heavier, stronger is better.8. We have been using the bus/motor home with the battery banks in their present locations and it's not practical to move them.9. When we replace the batteries, we will try to standardize them all.10. We have purchased the three solar panels because that is all the room that we have on the present mounting spot.11. Our location is in Michigan 49349 zip code.12. This used to be a US National Guard troop carrier bus that we converted into a youth group motor home and used tor 20 years to take youth groups on educational and service projects, until we were advised to retire it because replacement mechanical parts were no more available. The same condition has also happened to us at 80yrs.Thank youI await your reply
-
STOP BUYING STUFF!!!
You simply can't build a realistic solar electric system without knowing your loads.
Talk about your loads, what will be and what has been running in your bus?
If you have a 20 amp 120 service line, you might run the service through a Kil-A-Watt meter or a similar product to see what your load is currently.
Right now, we don't know if you have just lights to run, or air conditioning and a fridge...
Here's a site that might help you calculate your loads;
Off Grid Solar Load Calculator | Northern Arizona Wind & Sun (solar-electric.com)
Home system 4000 watt (Evergreen) array standing, with 2 Midnite Classic Lites, Midnite E-panel, Magnum MS4024, Prosine 1800(now backup) and Exeltech 1100(former backup...lol), 660 ah 24v Forklift battery(now 10 years old). Off grid for 20 years (if I include 8 months on a bicycle).
- Assorted other systems, pieces and to many panels in the closet to not do more projects. -
1 gauge wire from your solar panels is overkillIsland cottage solar system with appriximately 2500 watts of panels, 1kw facing southeast 1.3kw facing southwest 170watt ancient Arco's facing due south. All panels in parallel for a 24 volt system. Trace DR1524 MSW inverter which has performed flawlessly since 1994. Outback Flexmax 80 MPPT charge controller four 467A-h AGM batteries. Insignia 11.5 cubic foot electric fridge 1/4hp GSW piston pump. My 31st year.
-
706jim said:1 gauge wire from your solar panels is overkill
2.1 Kw Suntech 175 mono, Classic 200, Trace SW 4024 ( 15 years old but brand new out of sealed factory box Jan. 2015), Bogart Tri-metric, 460 Ah. 24 volt LiFePo4 battery bank. Plenty of Baja Sea of Cortez sunshine.
-
1. Since I wrote the details, I have found that I have more carefully measured a direct route from the controller to the solar panels+ 70'
Keeping distances short is helpful. Just to give you and idea, for every drop of 2 AWG (i.e., from 10 to 8 AWG), the cut area of the copper wire doubles, the resistance per foot goes down by 1/2, and the current capacity goes up by ~2x.2. I have also obtained some 1/0 AWG copper welding cable from storage that will connect from the controller to the solar panels.
Several issues with 1/0 welding cable to watch out for. First, welding cable is very fine wire and if you use crimp connections, fine stranded wire needs slightly larger crimp connectors to fit all the strands in. Second many (most all) charge controllers are designed to accept solid or coarse stranded cable--Fine strands tend to squirm out of typical set screw wire termination. Most controllers and other electrical items (combiners, breaker panels, etc.) have limited cable acceptance capacity--For example a charge controller may only accept 6 or 4 AWG coarse stranded cable--You would have to splice a transition from welding to smaller AWG cable to fit devices. Welding cable is not usually UV rated--When using for outside solar wiring, the cable should be inside conduit/boxes to protect from sun and weather. Lastly make sure the cable insulation is rated for your use (insulation temperature, etc.).3. I now have enough 1/0 AWG copper welding cable to connect both battery banks,.
Wire the batteries so that they have balanced cable lengths (wire resistance) between each battery, such as:
http://www.smartgauge.co.uk/batt_con.html
And don't forget fuses/breakers to protect your wiring. Fuses/Breakers protect the wiring against over current/short circuits which causes cables to overheat and possibly start a fire.4. I plan to run the 1 AWG power cable presently connecting the two battery banks to connect to a negative bus, from the 3 batteries, and connect all negatives to that negative bus.
For each + wire leaving the bus, each should have its own fuse/breaker to protect the smaller cable/branch circuit wiring (i.e., 14 AWG going to LED lighting should have a 15 amp over current protective device. Simplified NEC ampacity chart:
https://lugsdirect.com/WireCurrentAmpacitiesNEC-Table-301-16.htm5. I just ordered #4 AWG welding cable to connect between all components: controller, inverter, transfer switch and + & - bus
Make sure that each wire run is rated to carry the current (and fused/breaker). Note that DC rated/fuses need to be used on DC circuits. Also watch voltage drop... For example, suggest a maximum voltage drop of 0.5 volts from the battery bus to 12 VDC loads. And from charge controller to DC Bus, around 0.1 volt maximum drop for faster/accurate battery charging.
For solar panel to charge controller and for 120/240 VAC wiring, use typically use 1% to 3% max voltage drop (i.e., 120 VAC line * 0.03 max drop = 3.6 volt max drop).
You can use a simple voltage drop calculator to confirm (this uses "one way" cable length).6. The maximum power usage is estimated (roughly) at 2400 Watt hours, but normal usage is much less, I think.
Typically, suggest 500 to 1,000 WH per day for "cabin" lighting, DC water pump, cell phone charging, etc. And around 3,300 WH per day if you have a full size refrigerator, solar friendly well pump, and use a laptop computer for work/number of hours per day.7. I purchased the 60 amp controller and 3000 Watt inverter not because we are ready to maximize use, but to prepare for possible future expansion and because I thought that heavier, stronger is better.
Oversizing is not always your friend... For example larger controllers and AC inverters use more power "just turned on". For example a small 300 Watt inverter may use 6-8 Watts. A 3,000 Watt inverter can use 10-40 Watts... If left on 24x7 that (for example) 40 Watt tare load * 24 hours = 960 Watt*Hours per 24 hours or ~40% of your total power budget (40 Watts is probably an over estimate of a typical 3,000 Watt inverter tare losses--But you need to find out your tare losses to be sure).8. We have been using the bus/motor home with the battery banks in their present locations and it's not practical to move them.
If the bus no longer needs to be mobile, you might think about a power shed outside the vehicle. Batteries can vent (especially flooded cell lead acid batteries) and some charge controllers and many A/C inverters use cooling fans which can be irritatingly noisy. As well as a single place larger area for your battery bank and better access for installation & maintenance.9. When we replace the batteries, we will try to standardize them all.
Always a good thing to have "matched" sets of batteries--Better capacity sharing and when one or two start to go bad, usually time to change out the entire bank--Instead of having to debug/replace single random battery failures every few years.10. We have purchased the three solar panels because that is all the room that we have on the present mounting spot.
For off grid solar--Generally you want as much solar panel as you can afford/fit. Today panels are cheap and battery banks/genset fuel is expensive. Over paneling is a good option when you can do it.11. Our location is in Michigan 49349 zip code.
For now, using a simple solar calculator for Lansing Mi, fixed array facing south:
http://www.solarelectricityhandbook.com/solar-irradiance.htmlLansing
Measured in kWh/m2/day onto a solar panel set at a 47° angle from vertical:
Average Solar Insolation figures
(For best year-round performance)
The average harvest for February (assume the other three winter months use backup power/genset for bad weather):Jan Feb Mar Apr May Jun 3.20
3.71
4.20
4.59
4.86
5.29
Jul Aug Sep Oct Nov Dec 5.36
4.97
4.81
3.86
2.67
2.56
3 * 175 Watt solar panels * 0.52 off grid AC system efficiency * 3.71 of average February sun = 1,013 WH per day "break even" February
Not even 1/2 of your planned 2,400 Watt*Hour per day usage with this array... For example, at the very least you would need:
2,400 WH * 1/0.52 off grid system eff * 1/3.71 Hours of Sun Feb = 1,244 Watt array "break even" minimum for February
And you should only plan on using 50% to 65% of your predicted solar harvest for "base loads" (i.e., loads that must run every day vs optional loads like vacuum cleaner, TV, etc. that can be turned off during bad weather or are "worth" firing up a backup genset to run).12. This used to be a US National Guard troop carrier bus that we converted into a youth group motor home and used tor 20 years to take youth groups on educational and service projects, until we were advised to retire it because replacement mechanical parts were no more available. The same condition has also happened to us at 80yrs.
Yea, getting closer to my "use by" by date too.
Still not completely clear on the usage. Will the bus be fixed location or are you planning on some adventuring in the RV? In White Cloud MI 12 months a year, or do you "go south" for the winter?
Choosing battery types can be important too. Flooded Cell lead acid function pretty well for below freezing temperatures (the higher the state of charge, the lower the freeze point is for electrolyte). With AGM batteries (a form of lead acid), even if less that full charge and the battery freezes, they should not crack the cases.
Lithium Ion (such as LeFePO4 or litium Iron Phospate) batteries cannot cycle below ~50F. For cold climates, they need to be insulated and/or heating to keep warm (can be stored below freezing, just not cycled). Usually use a BMS battery management system to protect against temperature, over/under charge/etc. issues too.Your thoughts?
-BillNear San Francisco California: 3.5kWatt Grid Tied Solar power system+small backup genset -
WOW...what a dedicated advisor you are !! Thank you.This bus is now "permanently" located on our farm that we do some crop harvesting. We have a farm house but our daughter lives in it full time now. We use only the bus/motor home like you would a cottage, but want it as an "escape" location for natural or social/political disasters.1. I know that 1/0 AWG welding cable is "overkill" but it's free and not otherwise used.2. I plan to transition from 1/0 AWG cable to 4 AWG welding cable, or connecting 1/0 cable directly to + bus strip, and then #4 AGW cable from the bus strip. Is #4 AWG cable heavy enough for present and possible future upgrade?3. I plan to run the 1/0 welding cable through two PVC conduit pipes, under ground from the solar panels to the + bus strip.4. I plan to install recommended DC circuit breakers on each line coming from the + bus strip. There is a circuit breaker panel for each 120 volt circuit in the bus and the solar system will be connected to the 120 volt panel through a transfer switch, connecting solar and disconnecting the Grid and the onboard generator. There are two 12 volt fuse panels, and fuses for each 12 volt circuit.5. I don't know how to determine voltage drop other than using a meter or on a wire gauge chart. I would like to do "over kill" when I can afford to do it. The distance from + bus to controller and inverter should be 3' - 4' Will #4 AWG welding cable be adequate ?6. We are using a windmill to pump water to our 140 gallon water tanks and "on demand" 12 volt pumps to deliver water to sinks as needed. We have an electric water heater but use it sparingly or heat water on our LP gas stove.7. We're using all Renogy 175 watt solar panels, 60 Amp controller and 3000 watt inverter.8. It sounds like we will need to be very miserly using electricity, (we think we have been), and get more solar panels.9. I was planning to wire the solar panels in series but now with the 1/0 AWG welding cable from solar panels, thinking parallel.Bill
-
You are very welcome Bill. As you build out your system and learn the pluses and miniuses--Coming back and posting about your experiences will help others too down the road.
2. I plan to transition from 1/0 AWG cable to 4 AWG welding cable, or connecting 1/0 cable directly to + bus strip, and then #4 AGW cable from the bus strip. Is #4 AWG cable heavy enough for present and possible future upgrade?
3. I plan to run the 1/0 welding cable through two PVC conduit pipes, under ground from the solar panels to the + bus strip.
I really don't suggest people design/purchase for future upgrades. Yes, you can maybe get 2x larger system with an "existing" installation. However, to a degree, it is like trying to upgrade a VW bug to a 1 ton pickup... Can you do it? Yes. Should you--Not always clear.
Solar, and electronics in general, are constantly evolving. The "great deal" on 175 Watt panels you bought 5 years ago may cost 2x more ($$$ per Watt) than a 300 Watt panel now. It can become difficult (as an example) to mix and match different Vmp/Imp panels in one array with a single charge controller. There are rules/guidelines for placing panels in series (match Imp within 10% or better) and in parallel (Vmp within 10% or better).
Also, as you go with larger system(s), there becomes a point where you will want to migrate from 12 volt to 24 volt and/or 48 volt battery bus. Higher voltage battery bus means lower current in wiring. Less issues with voltage drop and having to manage large AWG cables.
I am not quite sure... But if you are using a 3,000 Watt AC inverter on a 12 VDC battery bus--Vs 3,000 Watt on a 48 volt bus:- 3,000 Watt inverter * 1/0.85 typical inverter eff * 1/10.5 volt battery cutoff voltage = 336 Amps worst case continuous current @ 12 volts
- 3,000 Watt inverter * 1/0.85 typical inverter eff * 1/42.0 volt battery cutoff voltage = 84 Amps worst case continuous current @ 48 volts
For example, say 4 feet of 4 AWG wire *(one way run with this calculator) with 60 amps on a 12 volt bus. Want maximum of 0.05 to 0.10 volt drop from charger to batteries (24 volt = 0.1-0.2 V drop; 48 volt = 0.2 to 0.4 V drop). Using a relatively simple voltage drop calculator:
https://www.calculator.net/voltage-drop-calculator.html?necmaterial=copper&necwiresize=5&necconduit=pvc&necpf=0.99&material=copper&wiresize=0.4066&resistance=1.2&resistanceunit=okm&voltage=12&phase=dc&noofconductor=1&distance=4&distanceunit=feet&eres=60&x=63&y=18&ctype=necResult
Voltage drop: 0.15
A bit over the suggested 0.10 drop for a 12 volt battery bank--But not the worst case. Shortening to 3 feet gets you to 0.11 volt drop--Better. If you have a 24 or 48 volt battery bus, then the 0.15 volt drop is trivial.
Voltage drop percentage: 1.24%
Voltage at the end: 11.85
You said you put several conduit runs from array to your bus... Note on wiring. For AC wiring, the Hot and Return cables need to all be in the same conduit. If you run "Hot" in one conduit and "Return/Neutral" in another conduit into a metal box (like AC breaker box), the two wires entering in two different holes creates a "transformer" effect in the box sheet metal creating circulating currents--And can overheat the sheet metal with heavier currents.
For pure DC power (such as solar arrays) there is no "circulating current issues" (requires a "changing magnetic field" such as AC current).
Gets a bit more complex with DC power to AC inverter input. For single phase AC inverters, the DC input is a "pulse train" of 120 Hz Sine Squared waveform... I.e., peak current when 120/240 VAC is at its peak, and near zero current when AC wave is at zero crossing (p=v*I; when voltage is zero, there is zero power transfer).
So, you need to run AC wiring and DC input to things like AC inverters in the same conduit and "through" the same hole in metal boxes. Also there is "coupling" between the wires which lowers the impedance (complex resistance) too (i.e., lower voltage drop in AC wiring).
For Solar Array wiring, the "coupling" of current is not an issue--But things like lightning survivability and electrical (radio frequency) interference. Wires next to each other (in higher frequency power, we even "twist" pairs/groups of wires) to minimize the "antenna" effect. Basically if you run wires (and twist), they make very "bad" antennas. Don't broadcast RF noise. And don't "receive" nearby lightning strike energy.
So use a larger conduit and run (for example) all Array wiring in the same conduit if at all possible. I like to oversize conduit so I can pull new/larger cable for upgrades. In theory, if you are going to run DC from the array and 120 VAC back to the (AC outlet for power tools, shed, garden area), a separate conduit should be used for "not same" wiring (i.e., "high voltage" DC from array in one conduit, AC in another conduit run).
3. I plan to run the 1/0 welding cable through two PVC conduit pipes, under ground from the solar panels to the + bus strip.
I am not sure what your plan is here... Run cable from "each panel" to the bus and combine on a common solar bus, then to the MPPT charge controller solar input?
Just to be clear, there are "design rules" for solar array configurations. Basically when you have (typically) three or more solar panels in parallel, then each "panel string" needs its own series protection fuse/breaker. For example, you may need a 15 Amp fuse. This prevents the other "good parallel connected panels" from feeding a "bad/shorted" panel and starting a fire.
You can bring the X number of separate cables back to the bus and install a "combiner box" there. Or you can can have the combiner box at the solar array (protected from weather) and run just a pair of cables out of the combiner box (plus safety/lightning ground) back to the bus. This is your choice. (Vmp-array, Vpanel max input voltage, etc.).
Too not get too messy in this reply--Need to look at Vpanel max input for the MPPT controller you picked (typically around 100 or 150 VDC). In cold climates, the Vmp-array-std is around 2/3rd of Voc-array-std). I.e., a 100 VDC controller should have Vmp-array-std around 66.6 VDC max (depends on local minimum temperatures).
Also, when configuring a MPPT controller and array... The Vmp-array should be (ideally) about 2x battery bank voltage. For a 12 volt bank charging at ~15 Volts, Vmp-array-std should be around 30 VDC minmum. For a 24 VDC battery bank/30 VDC charging, around 60 VDC minimum Vmp-array-std (std standard test conditions/temperature--aka "marketing numbers" on panel label).
As Photowhit said--There are lots of design issues that should be addressed on a paper design before buying hardware. It is "easy" to buy the pieces for a good price then spend lots of time and energy to try and get everything configured to work together (or it may not).
4. I plan to install recommended DC circuit breakers on each line coming from the + bus strip. There is a circuit breaker panel for each 120 volt circuit in the bus and the solar system will be connected to the 120 volt panel through a transfer switch, connecting solar and disconnecting the Grid and the onboard generator. There are two 12 volt fuse panels, and fuses for each 12 volt circuit.
There is a "confusing" grounding issue with RV's and multiple power sources.
In North America, we "assume/design" AC (and DC) power systems with a "bonded" Neutral (return, negative DC) to earth/chassis ground.
This allows us to use circuit breakers on the "hot" leads, and not need them on the grounded neutral/return leads (i.e., a Hot to plumbing/chassis will pop a breaker in the "hot lead". However since the return (negative DC) is ground referenced/bonded, a neutral to chassis/plumbing short will not draw current (both neutral and ground have a "zero volt" differential and no current flow when shorted).
In North American wiring, usually the Neutral and Ground conductors are connected together in the main AC panel (and connected to cold water pipe, 8-10 foot ground rod, etc.).
With RVs, the "shore power" in N+G bonded in the home/business supplying AC power. And larger gensets and AC inverters (typically 3,500 watts or larger?) default to having N+G AC bond inside the Genset/Inverter.
So, you have to address the system so that you don't have N+G bond inside the RV when shore powered. And a transfer switch that connects N+G bond when on internal AC inverter power or Genset power.
You don't want (for example) N+G bonds in two locations. First the N and G conductors are in parallel and "share" load currents. Code does not want load currents in safety ground (see circulating currents in above answer).
Second, if you have a GFI outlet from house to RV, or GFI breaker (ground fault interrupter) in the House Branch Circuit panel, having two N+G connections (one in home, second in RV), it will trip the GFI protection device (shared current in N and G wiring is fault. All current flowing in H+N is good).
With many higher end AC inverters, they have transfer switches and can also have N+G bonding switching too that address this issue.
Next page....Near San Francisco California: 3.5kWatt Grid Tied Solar power system+small backup genset -
You ended with: Next page..... How do find "next page"
-
5. I don't know how to determine voltage drop other than using a meter or on a wire gauge chart. I would like to do "over kill" when I can afford to do it. The distance from + bus to controller and inverter should be 3' - 4' Will #4 AWG welding cable be adequate ?
- 3,000 Watt inverter * 1/0.85 inverter eff * 1/10.5 battery cutoff voltage = 336 Amps @ 12 volt battery bus
- 3,000 Watt inverter * 1/0.85 inverter eff * 1/21.0 battery cutoff voltage = 168 Amps @ 24 volt battery bus
https://lugsdirect.com/WireCurrentAmpacitiesNEC-Table-301-16.htm
4 AWG is only "good" for 70-95 Amps... So "no" for a fully loaded 3,000 Watt inverter.
Voltage drop calculator, use the previous Voltage Drop Calculator link (and heavier AWG cable).
Note NEC is relatively conservative... There are higher amperage rating if you use marine ampacity tables and wiring outside of conduit. Choices (avoiding fire, lower voltage drop, I like to use NEC tables.
6. We are using a windmill to pump water to our 140 gallon water tanks and "on demand" 12 volt pumps to deliver water to sinks as needed. We have an electric water heater but use it sparingly or heat water on our LP gas stove.
That is a good plan. RV water pumps use very little energy overall. 12/24 VDC native pumps, no AC inverter needed to power.
Using wind/alternative power to pump to cistern saves on using "expensive" battery backed solar+inverter to power pump. There are solar powered "slow pumps" that can also work well (pump during the sun, cistern stores water overnight/for "dark" weather conditions).
LP Gas--Gets into the whole "SHTF" question. Are you planning for a few days/weeks of weather/ice storms. Or are you looking for sustainable off grid of months+ off grid. LP for emergencies is fine.
RVers are now using solar+Lithium Ion batteries+inverter for induction cook-tops. Works well. Need lots of solar or alternative power for full time off grid (genset, driving vehicle, shore power, etc.).
7. We're using all Renogy 175 watt solar panels, 60 Amp controller and 3000 watt inverter.- 3 * 175 Watt panels = 525 Watt array
- 525 Watt array * 0.77 panel+controller eff * 1/14.5 volts charging * 1/0.10 rate of charge = 278 AH @ 12 volt battery suggested max battery bank for full time off grid.
If full time off grid--RVers are using induction cook-tops+Lithium Ion batteries (don't work in sub 50F temperatures) and 2-3kWatt AC inverters. Catch is they have larger arrays and a lot more sun than use. And are using the vehicle alternator to charge while driving (not use) or backup genset or shore power--Maybe not you in SHTF conditions. It is a solution for going LP/fossil fuel free (even electric hot water heater when needed).
With smaller systems, really need to conserve energy. With larger systems and $$$, more can be done.
A 1,000 Watt*Hour solar harvest in winter (with small array)... Assume 5 hours per night, 2x nights storage:- 1,000 WH harvest / 10 hours = 100 Watt load per day/night for 5 hours (2x nights for bad weather).
- 1,000 WH harvest / 5 hours (daily sunny wather) = 200 Watt AC load during good weather.for 5 hours per day/night
- 20 Watt Tare loses (guess at 3kWatt inverter) * 5 hours per day = 100 WH or 10% of your daily harvest
8. It sounds like we will need to be very miserly using electricity, (we think we have been), and get more solar panels.
Yep... And Yep.
I am not trying to ruin your day... I want to give you the "tools" so you can work out your needs and design a system to support those needs. And not be that person a week or two into using "the system" and finding out you have dead batteries, no power, and no idea where to go next (it happens).
I really suggest backing up and doing the paper designs first to size a system that will support your needs. Energy usage is a highly personal set of choices. I am not trying to design a system that works for me, or a "mythical" you.
The "tools" give you the ability to do "what if" comparisons and not get blind sided later.
Doing a solar shed for your AC and DC bus power--Gives you more options (not constrained by existing vehicle size and electrical system).
And you can always pull out the bus and pull in a (for example) simple (well insulated) camper trailer--And not have 1/2 your solar system go with the bus.
Again, your needs, your choices. Just some suggestions thousands of miles away from a guy that has never lived winter in snow.
9. I was planning to wire the solar panels in series but now with the 1/0 AWG welding cable from solar panels, thinking parallel.
Your panels:<div><div>SPECIFICATIONS</div></div><div class="Quote">Max Power at STC: 175W<br>Open Circuit Voltage: 21.6V<br>Short Circuit Current: 10.62A<br>Opitmum Operating Voltage: 18V<br>Optimum Operating Current: 9.73A<br>Operating Temperature: -40°F to 176°F (-40°C to 80°C)<br>Maximum System Voltage: 600VDC UL<br>Maximum Series Fuse Rating: 15A<br>Cables: 12 AWG 2.3ft long<br>Dimensions: 52.3x26.4x1.38 in (1328*670*35mm)<br>Weight: 20.9 lbs (9.5Kg)<br>Solar Cells: 32 Monocrystalline Cells<br>Junction Box: IP65<br>Connectors: Solar Connectors<br>Module Efficiency: 19.80%<br>Material and workmanship warranty: 5 years<br>Performance Warranty: 5 year 95% output warranty 10 year 90% output warranty 25 year 80% output warranty</div>
I am looking for Vmp and Imp... Vmp=18 volts.
Highly suggest that you pick 2-3 panels in series. Ideally for MPPT, the Vmp-array-std should be 2x 14.5 volts (battery charging) or 29 Volts Vmp minimum for optimal MPPT controller operation.
Depending on the MPPT charge controller you picked (say 100 VDC Vpanel-max) you could put all panels in series for a good solution too (3 panels per string).
Just for practice, assuming 3% maximum wiring drop, 70 feet, 9.73 Amps Imp, 3x panels in series for 54 Vmp-array:
Result for 10 AWG cable and 9.73 amps of solar array current
Voltage drop: 1.62
Or for 100 amps of solar array (10x larger array) on 1/0 cable:
Voltage drop percentage: 3.00%
Voltage at the end: 52.38
https://www.calculator.net/voltage-drop-calculator.html?necmaterial=copper&necwiresize=9&necconduit=pvc&necpf=0.99&material=copper&wiresize=0.4066&resistance=1.2&resistanceunit=okm&voltage=54&phase=dc&noofconductor=1&distance=70&distanceunit=feet&eres=100&x=81&y=22&ctype=necResult for 1/0 AWG cable and 100 amps of solar array current
Voltage drop: 1.66
If you run 54 volt Vmp-array (3 of your panels in series), you can install a much larger array (larger controller, higher voltage battery bank, etc.)
Voltage drop percentage: 3.08%
Voltage at the end: 52.34
This is what "future room for expansion" looks like... Lots of "what ifs". Note there are limitations too... One array maps to one MPPT controller. You can not have one "massive array" and 2 or more MPPT controllers connected to that one array--So you would need multple independent arrays each feeding a dedicated MPPT controller--And "all" MPPT controller charging your battery bank.
Usually it is better to start from scratch if you ever build a larger solar power system. Like trying to turn a VW bug into a 1 ton piclup-Can be done, but probably should not be done.
Details matter here... The first pass paper design is just Watts and Watt*Hours of rate of energy use (Watts) and amount of energy used per day (Watt*Hours).
Start converting into volts, amps, and amp*hours once you have the first "soft paper numbers". You can do the modeling/math with just Watts and Watt*Hours first and see if it meets your energy needs (or not).
Then start picking hardware and figure out how to optimally wire together and see if it meets you needs and budget.
This is an interpretive process. And with all of the hardware choices out there, there are many different solutions out there. Many will give you similar results, and some may not be practicable (engineering wise) or cost effective for you... Then back to the drawing board.
Sorry the answers are so long and complex. When you have "what if" and an "unbalanced" design (large inverter, smaller battery bank, and very small solar array)--Can end up answering the "same question" two or three different times with different starting assumptions.
-BillNear San Francisco California: 3.5kWatt Grid Tied Solar power system+small backup genset -
You're a great mentor/teacher !I'll try to draw conclusions.All my material is still in its packaging or on the shelf waiting assembly.1. I bought some things with a larger capacity because I wanted to be ready for where I now find myself, on the way but not there yet.2. I have needed to find meanings for some of the terms you used, and I appreciate what you have helped me with.3. I can see that I need a system that will provide at least 2400 - 3000 KW power.My solar panels and battery bank will not provide that for us.4. I am thinking of how to locate the panels in a different location where I can add at least three more 175 watt solar panels together.I think the overkill 1/0 AWG welding cable should allow us to add panels at this distance away from the battery bank, 60 amp controller and 3000watt inverter should help to get us near where we want to be with this system with the extra panels and more batteries.5. No one has been able to provide me with the depth of information that you have given. I spoke to a technician from Renogy who called me this afternoon following many emails exchanges from customer service people in the past couple weeks. Sometimes I was given information that was not accurate. Today the technicial said that I needed a 4/0 AWG cable from the battery bank to the inverter. I don't think I can be confident in that advice requiring a 4/0 battery supply cable to the inverter..
-
TellGRBill said:Today the technicial said that I needed a 4/0 AWG cable from the battery bank to the inverter. I don't think I can be confident in that advice requiring a 4/0 battery supply cable to the inverter.
Pretty straight forward an equation that is used in DIY solar electric all the time, Amps x volts = watts
So a 3000 watt output inverter would require 3000/12volts = 250amps (actually a bit more, due to efficiency and possible voltage sag to 11.xx volts)
NEC Ampacity chart;
One of the reasons it's better to plan ahead before purchasing. A higher voltage DC system Allows for smaller cabling, more capacity per charge controller, and less losses in general.Home system 4000 watt (Evergreen) array standing, with 2 Midnite Classic Lites, Midnite E-panel, Magnum MS4024, Prosine 1800(now backup) and Exeltech 1100(former backup...lol), 660 ah 24v Forklift battery(now 10 years old). Off grid for 20 years (if I include 8 months on a bicycle).
- Assorted other systems, pieces and to many panels in the closet to not do more projects. -
Thanks for the conformation.
-
I went inline to see if I can buy the short pieces of 4/0 cable with lugs attached and was happy with what I found.Any additional suggestions for using the three 175 watt solar panels, 60amp controller, and 3000 watt inverter that I purchased, and/or if I add three 175 watt solar panels ?
-
As Photowhit said--Planning first, buy later.
1. I bought some things with a larger capacity because I wanted to be ready for where I now find myself, on the way but not there yet.
Solar is not cheap. An 1,800 Watt AC inverter on a 24 volt 650 AH battery bank and 1,500-3,000 Watt array can support upwards of 3.3 kWH per day assuming you have enough sun...
To support a full size fridge, is already a medium sized solar power system.
We have lots of rules of thumbs around here to save on "deriving the fundamentals" with each new member.
For example, I like to use:- 12 volt battery bus: 1,200 to 1,800 Watt AC inverter suggested maximum
- 24 volt battery bus: 2,400 to 3,600 Watt AC inverter suggested maximum
- 48 volt battery ban: Over 2,400/3,600 Watt inverters
Another is I suggest a maximum of 800-1,000 AH maximum on battery bank AH capacity... Over that, jump up from 12 to 24, 24 to 48, etc.
Mostly, you will see that home power systems are limited to 48 VDC battery bus... Mostly I believe because >60 Volts, Code requires the stuff to be behind locked doors/access (considered hazardous voltage). And a 10% rate of charge is already 80=100 Amps--Enough to push Cable AWG sizes up (to keep voltage drops low).
Can you get a 5,000 Watt @ 12 VDC input inverter (even up to 8 kWatt?)... Aims sells a lot of them:
https://www.aimscorp.net/5000-Watt-Pure-Sine-Inverter.html
With NEC, generally paralleling of cables is not allowed... Unless the cable is 4/0 AWG or heavier.
Using our rules of thumb, at the very least a 5 kWH inverter should have >2,000 AH of 12 volt Flooded Cell battery bank.
Don't suggest jumping into this without planning.
2. I have needed to find meanings for some of the terms you used, and I appreciate what you have helped me with.
Please feel free to ask. We all had friends/teachers that helped us learn the terms and about solar too.
3. I can see that I need a system that will provide at least 2400 - 3000 KW power.
That is not a small system. And power (Watts or even Amps) is just a rate (like miles per hour). The other is time--How many Watts (or Amps) for how many hours...
Large capacity inverters are relatively cheap. Batteries, solar panels, cabling, etc. not so much... And batteries have to be replaced every 3-5-7-10+ years (again choices in battery construction, chemistry, and quality).
Can setup a 12 volt system that will supply 3,000 Watts for ~1 hour on a 300 AH @ 12 volt lithium battery bank. If that meets your needs--Great.
If you have a 3/4 HP well pump, a fulls size refrigerator, LED Lighting, computer, etc.... Then a 3 kWatt inverter makes sense (for starting a non-solar friendly well pump).
Because of pump--3 kWatt inverter makes sense (starting surge). Example of math for loads/WH capacity.
1,200 Watt water pump * 0;5 hours per day = 600 Watt hours per day
800 Watt induction hotplate @ medium * 1 hour per day usage = 800 WH per day
1,000 WH per day efficient full size fridge = 1,000 WH per day
5 LED lamps * 13 Watts * 5 hours an evening = 250 WH pd
30 Watt laptop * 5 hours = 150 WH pd
12 volt * 8 amps * 1/2 hour per day = 38 WH per day (yes, I know that this is DC, just lump into AC power to keep simple)
========================================================================================
2,838 WH per day (example of math).
I am just going to round up to 3,300 WH per day for very efficient small home/cabin (support vacuum cleaner, washing machine, etc. on sunny days).
3,300 WH per day * 1/0.85 AC inverter eff * 2 days storage * 1/0.50 max planned discharge for FLA battery) * 1/24 volt battery bank = 647 AH @ 24 volt battery bank
Next sizing the solar array. Two calculations. One based on rate of charge (5% for "backup/emergency power; 10-13%+ full time off grid minimum rate of charge). Second based on actual daily loads and hours of sun per day.
Battery charging:- 647 AH * 29.0 Volt charging * 1/0.77 panel+controller deratings * 0.05 rate of charge = 1,218 Watt array minimum
- 647 AH * 29.0 Volt charging * 1/0.77 panel+controller deratings * 0.10 rate of charge = 2,437 Watt array nominal
- 647 AH * 29.0 Volt charging * 1/0.77 panel+controller deratings * 0.13 rate of charge = 3,168 Watt array "cost effective maximum"
Lansing
Measured in kWh/m2/day onto a solar panel set at a 47° angle from vertical:
Average Solar Insolation figures
(For best year-round performance)
Say "break even" into December at 2.56 hours of sun per dayJan Feb Mar Apr May Jun 3.20
3.71
4.20
4.59
4.86
5.29
Jul Aug Sep Oct Nov Dec 5.36
4.97
4.81
3.86
2.67
2.56
- 3,300 WH per day * 1/0.52 off grid AC system eff * 1/2.56 hours of sun per day December = 2,479 Watt array "break even"
Now we look at base loads (loads that mush run every day) and optional loads (only need to run during sunny weather or starting genset.
Say lights, refrigerator, RV pump are "base loads" or
1,000 WH per day fridge
250 WH per day lights
150 WH pd laptop
38 WH per day RV pump
=========================================
1,438 WH per day "base loads"
Suggest that only use 50-65% of predicted power for base load. In this case:- 1,438 WH base loads / 0.50 predicted usage = 2,876 WH per day "base load"
Looking above, we have 2,437 to 3,168 Watt array (10% to 13% rate of charge) and 2,479 Watt Array "break even" December--Suggest 2,479-3,168 Watt array is a good start (again, over paneling is, in general, good for battery banks).
And to confirm battery bank AH capacity. For flooded cell lead acid batteries, suggest a minimum of 200 AH per 1,000 Watt of inverter output (24 volt bank). In this case:- 3,000 Watt inverter * 200 AH per 1,000 Watt of inverter = 600 AH minimum FLA battery bank for 3,000 Watt inverter... So the 647 WH battery bank "works" with 3 kWatt inverter.
The above is a system that should meet the needs listed. Doing things like "over solar paneling" helps reduce genset runtime and fuel usage. Looking at the "solar unfrinedly" water pump and spending $2,000 to $3,000 more for a "solar friendly well/water pump" (the solar friendly pumps have no surge current and you can use an inverter that is about 1/2 the size (i.e., for example, the next highest surge is the full size energy star refrigerator which needs around a 1,200 to 1,500 Watt minimum inverter to start reliably).
Once the first pass paper design is done, we can start looking at hardware and configurations that are sized to the above numbers. In solar numbers within 10% of each other are "the same". Rounding up to next size array, battery bank, and such is not bad. Using inexpensive batteries for the first bank (cheap FLA golf cart batteries for example) to get the system up and running and see how it works for you. If you need more battery bank, easy to add more. If you "murder the first bank" (family comes by to borrow bus for a week and leaves everything turned on when they go out and about)--You don't feel so bad replacing a "cheap bank" (many of use "murder our first bank").
If you choose to use heavier cables because they are here and free. Not an issue--Just make sure that you can terminate them and the insulation is rated for your use (older "welding cables" were not generally UL/NRTL/NEC rated cables).
-BillNear San Francisco California: 3.5kWatt Grid Tied Solar power system+small backup genset -
Here are the specifications for the equipment we're using.Seven 175 watt panels, 60 amp MPPT controller, 3000 watt inverter.How do I get the best result from them ?I'm sorry. I said that we need 2400 - 3000kw watts and I meant 3000 WH watt hours for our bus.
-
They won't play well together...
Not sure if your charge controller can be 'over paneled', It's an MPPT type, so would like to see an input of 1.5X the output voltage to work properly. 1.3X minimum.
If your needs are 2.5 kWhs a day as an estimate, I'd guess around 8 kWhs of storage for lead acid batteries as a minimum or 665 amp hours at 12 volts or 335 at 24 volts. minimum array wattage to service is about 10% of capacity (to about 15% for flooded batteries). Solar panels typically produce about 75-80% of their name plate (STC vs NOCT) so 800 watts x 1.3= 1040 - 1600 watts.
So likely scrap the inverter, go to a higher voltage inverter, buy another 175 watt solar panel so you can run them in pairs for 12 volt or strings of 4 for 24 volt. Add 2 more and use strings of 5, if you want to run 48 volts system as suggested below. Check VOC to see if it is safe.
This would allow you to use the existing charge controller but leave no room for 'growing loads' a somewhat natural problem. You might consider going to a 48 volt inverter now. This would allow for a single string of 8 - 6 volt 215amp golf cart batteries, reducing issues with higher cost batteries or multiple strings of batteries. 48volts x 215 amps = a little over 10 kWhs of storage.Home system 4000 watt (Evergreen) array standing, with 2 Midnite Classic Lites, Midnite E-panel, Magnum MS4024, Prosine 1800(now backup) and Exeltech 1100(former backup...lol), 660 ah 24v Forklift battery(now 10 years old). Off grid for 20 years (if I include 8 months on a bicycle).
- Assorted other systems, pieces and to many panels in the closet to not do more projects. -
I just paid too much to scrap the new inverter.Can I rewire the battery banks to get 24 volt battery banks and still have a 12 volt direct connection to those banks?Looks like the inverter can only take 12volts input, so 24volt bank will not help.Our present battery banks are three group 12volt 31 100 AH and two 12 volt 135 AH batteries wired parallelThis is pretty frustrating. I've spent many, many hours reading information on the internet about solar systems, emailed the people at Renogy with questions and data and thought I was ready to purchase the main components and assemble them.I've already spent what I consider a lot of money, am willing to spend some more, and would like to see a positive result.
-
TellGRBill said:I just paid too much to scrap the new inverter.Can I rewire the battery banks to get 24 volt battery banks and still have a 12 volt direct connection to those banks?
Home system 4000 watt (Evergreen) array standing, with 2 Midnite Classic Lites, Midnite E-panel, Magnum MS4024, Prosine 1800(now backup) and Exeltech 1100(former backup...lol), 660 ah 24v Forklift battery(now 10 years old). Off grid for 20 years (if I include 8 months on a bicycle).
- Assorted other systems, pieces and to many panels in the closet to not do more projects. -
"Your charge controller can only handle 800 watts, so you'll need another charge controller."Does this mean that the controller can not handle the 1275 watt solar panels?My life has always been to make the best with what I have available.I just want to be able to function at a minimum level if we have to depend on solar.We presently have a 5000watt generator and 120 volt 20amp power line.We heat with wood, can cook with LP gas or wood, and can depend on the hand water pump or have the wind mill run the hand pump.How many 175 watt panels total are you recommending, using our present controller ?Note: distance between battery banks is 20' not 30 '
-
TellGRBill said:"Your charge controller can only handle 800 watts, so you'll need another charge controller."Does this mean that the controller can not handle the 1275 watt solar panels?My life has always been to make the best with what I have available.I just want to be able to function at a minimum level if we have to depend on solar.We presently have a 5000watt generator and 120 volt 20amp power line.We heat with wood, can cook with LP gas or wood, and can depend on the hand water pump or have the wind mill run the hand pump.How many 175 watt panels total are you recommending, using our present controller ?Note: distance between battery banks is 20' not 30 '
I don't know if 'over paneling is okay with this controller, I'd hunt down the instruction sheet and check, but what you posted says only 800 watts input at 12 volts. I suspect you can safely go with 5 but in parallel they wouldn't work in MPPT mode, or not much (instructions may not say this, but some do let you know that MPPT needs some 'head room' above the output voltage.
Midnite adds this at the bottom of their string sizing tool. boB and Robin Gudgel designed and introduced one of the first practical MPPT charge controllers.
Highest battery voltage for a 12 volt system would be around 15.5 volts equalizing so around 20 volts input.
So the max would be 4 panels 2 in series (string) and 2 strings in parallel. Looks like you have reasonable sun even in winter, this is likely to support the fridge and some lighting, phone charging and some laptop use...
BTW - if you still have the RV 'dual fuel' fridge, it will be an energy hog on electric.Home system 4000 watt (Evergreen) array standing, with 2 Midnite Classic Lites, Midnite E-panel, Magnum MS4024, Prosine 1800(now backup) and Exeltech 1100(former backup...lol), 660 ah 24v Forklift battery(now 10 years old). Off grid for 20 years (if I include 8 months on a bicycle).
- Assorted other systems, pieces and to many panels in the closet to not do more projects. -
Bill, I think we need to nail down your energy requirements first.
What are your loads? I gave a quick example of how to summarize and identify high power loads (like a 120 VAC well pump) and how to take average/running power (Watts) and use hours per day usage (hours) to figure out Watt*Hours per day per load. Then add all the WH per day per load together and get WH per day.
3,000 WH per day is a "reasonable number" for a home/cabin that is very efficient, using a modern energy star refrigerator (not a 2 or 3 way Ammonia RV fridge--Which can be OK on propane, but is a real electrical hog on 12 VDC / 120 VAC).
In post #16 I went through a full (one pass) paper design for a 3,300 WH per day off grid power system. Again, what I don't know is your electrical loads (small things like lights, laptop computer, RV Water pump, LED TV, maybe a clothes washer, what kind/size/rating refrigerator, etc.).
A 3.3 kWH per day system is already a "medium sized" solar power system. And it would be best to run on a 24 VDC (or even 48 VDC) battery bank if you are looking for some "future proofing".
Can you make all this run on a 1,500 to 1,800 Watt AC inverter + 1,294 AH @ 12 VDC @ FLA battery bank--Yes, you could. Adding a 3,000 Watt AC inverter @ 12 volts is a lot to ask for (you can run parallel heavy copper cables such as 2+ and 2- cables from battery bus to Inverter input--But you are add another band aid for a "maxed out" 12 VDC system.
And to charge @ 13% rate of power for a 12 volt @ 1,292 AH Battery bank:- 1,294 AH * 0.13 rate of charge = 168 Amps charging
- 168 Amps charging / 60 amps per charger = 2.8 charger => 3 Renogy 60 Amp chargers
- P=I*V
- 1,294 AH * 12 volts * 1/48 volts (i.e, 4x voltage, 1/4 current/AH capacity) = 324 AH @ 48 VDC bank (same amount of energy stored)
- 324 AH * 0.13 rate of charge = 42 amps
You would be "saving money" with a 12 volt 3 kWatt inverter but spending 3x the money on three 60 Amp charge controllers to "stay" at 12 volt battery bank. Plus now you need to have "3 separately wired solar arrays", each wired to a separate MPPT charge controller (3 pairs of cables from array to MPPT chargers, which then all are connected to one battery bank).
Also, look at the tare losses of your 3 kWatt inverter... Just powered "on", it draws 2.5 amps or (2.5a*12v= ) 30 Watts just to power that larger inverter. 30 Watts * 24 hours per day = 360 WH per day (or 10% of your daily winter harvest/energy usage).
Many folks here that started with a smaller 12 VDC system and tried to get >3 kWH per day harvest--They said if they had to do it over again, they would start with a 24 or even 48 VDC system).
You may choose a 24 VDC bank because you can use a 24 VDC RV type water pump (and you can get 24 VDC LED lights, water pump, fans, and even some 24 VDC appliances from Heavy Truck/Marine stores.
Having a 24 bank and some DC loads (plus 120 VAC inverter)---Or just go 120 VDC loads only (120 VDC RV water pump, LED lights, etc.) and forget DC devices. You just need to make the DC loads 1/0.85 (1.18x) larger (larger battery bank, larger solar array) because of the bit of AC inverter losses.
And there are things you should not do. Having a 24 volt battery bank and "tapping" 12 volts off of the lower batteries. It "works" in that you can draw power this way--But fails because the "high and low" 12 volt "banks" are no longer balanced. You will slowly under charge the low 12 volt batteries and over charge the high 12 volt batteries.
in engineering terms (where money is no object), yes you can do the 24/12 volt split by buying a battery Balancer that equalizes the low and high banks--But costs money. Or you can get a DC to DC converter for a few smaller loads that converts 24 VDC to 12 VDC (a DC to DC buck converter/power supply) for a few 12 VDC loads. Does work (and a few conversion losses). Or just get 120 VAC appliances.
With modern Energy Star designed appliances, the 120 VAC appliances are almost as efficient as their 12 VDC counter parts, and the 120 VAC versions can be cheaper (look at 12/24 VDC fridge vs 120 VAC fridge pricing).
I understand you want to make do with what you have--But with solar and the relatively complex requirements and interactions makes taking "random" components and putting together to make a working system can be a real nightmare.
The MPPT Charge controller you have is a reasonable device. It is 140/150 VDC max solar panel input voltage (very good mid-range specs). It can work on 12/24/48 volt banks.
The Solar panels are fine.
The 3kW @ 12 VDC AC inverter--Not a good choice--Very limiting to stay with 12 VDC battery bus. And AC inverter are 12 or 24 or 48 volts. There are (generally) no AC inverters that work on a 12-48 volt battery bank. Could it be done? Yes. But it is one of those things that becomes expensive to manufacture--An AC inverter with a wide range 10.5 to 65 VDC input range at full rated power is cost prohibitive for commercial market.
Solar Panels--People like to think of them as "solar batteries" (i.e, solar panel outputs 18 VDC). However, they are not really "batteries" or voltage sources--Solar panels are actually "current mode" sources. Basically under full sun, the solar panel will out put 10 amps from 18 volts to 0 volts. Above 18 volts, the output current falls. Cold panels Vmp=18 volts actually rises. And in hot conditions/full sun, the Vmp=18 volt falls..
Very roughly the output voltage range goes from (roughly 18 volts * 0.81 hot derate = ) 14.58 volts Vmp-hot. And, roughly in sub freezing temperatures, Voc-below-freezing is around 29 volts (skip math for now--Just believe me for the moment). You live in a Hot Summer/sub freezing winter climate. So the Voc-array-cold and Vmp-array-hot needs to "match" the requirements of the MPPT charge controller.
And we get into Vmp-array-std (standard test conditions or "marketing numbers") we end up with the rules, again roughly for your climate. The Vmp-array ranges below are converted to Vmp-array-std (standard test/temperature or Name Plate) conditions- 12 volt bank => Vmp array ~24 VDC minimum (Vmp-array-hot) to ~100 Vmp-array-max (Voc-array-freezing)
- 24 volt bank => Vmp array ~48 VDC minimum (Vmp-array-hot) to ~100 Vmp-array-max (Voc-array-freezing)
- 48 volt bank => Vmp array ~96 VDC minimum (Vmp-array-hot) to ~100 Vmp-array-max (Voc-array-freezing)
The above are "rules of thumbs" so we can get "close" to the answers. Then do the detailed calculations (your exact temperature range. exact hardware, etc.). If you (or me) had to do the detailed calculations for "every possible" configuration--There are not enough hours in a day (and I am a volunteer here--Only so much I can do away from the family/other responsibilities).
So, go through my questions (Watts usage, :Peak Watts, what are your major loads lights, type of fridge, computer, TV, washer, etc.), full time off grid or backup power, etc.
I don't think we can come up with a "dirt cheap" system using what you have on-hand already. The big stumbling point is the 3 kWatt @ 12 volt inverter--I would suggest it has to go. I would suggest at least a 24 (or possibly 48) VDC battery bank. That makes the 12 volt pump "redundant" for this system. Either pick 24 VDC or 120 VAC RV style pump for another ~$150.
Review power/energy budget, define battery bank. What is your minimum "winter power need". Define the solar array size in Watts.
And if you like the 175 Watt Panels (they are perfectly fine here). Knowing the battery bank voltage and capacity, you then figure out the X series * Y parallel strings.
Note that picking 12/24/48 VDC battery bus, affects if you want 3/2/1 60 amp MPPT charge controllers (lower voltage bank, more charge controllers in "parallel").
All choices have consequences/interactions with other upstream/down stream hardware and may force "recalculations" between choices.
-BillNear San Francisco California: 3.5kWatt Grid Tied Solar power system+small backup genset -
Bill,You have convinced me that I am out of my league.You have done a fine job trying to educate me about the complex electrical solar systems.You have done your best to help me design and assemble a first class, efficient solar system.I studied all the material that I could find before I bought the solar equipment that I bought.You have helped me change some of my plans for our solar system. But our solar system is only an emergency backup system.What I am looking for now is direction guiding me to assemble what I have collected, with a few more 175watt solar panels that you have convinced me are needed, that will help us get through emergency situations. I want to use the present controller, inverter, and battery banks in the most productive and efficient way possible, and I ask for your advice to do that.I know that this will violate your high quality standard, but I am used to living second class, enjoying the struggle, and enjoying the financial freedom it brings.Please help me.BillTo see some of our life adventures and struggles, check out our website: www.whereverGodwills.org There are photos of our converted bus there, and some photos of its past and present use.If you have lost patience with me, I understand, and want you to know that I recognize and appreciate your effort !!
-
My wife keeps giving me a hard time for these long and complex answers... Like should I paint this red? Well, red does reflect heat better than black but it absorbs blue and UV light so it tends to fade quicker and does a less good job of protecting the material under that paint. Whereas blue tends to reflect the higher energy photons (blue, UV) and protect.... (kick to my leg under the table)...
I will keep going here--But I don't want to frustrate you either.
For me, I look at "emergency" more as camping conditions vs long term off grid living at being a bit more "comfortable" and sustainable (more solar energy, less fossil fuel usage, etc.).
I live in a very moderate climate and a 500-1,000 WH per day, 300 Watt inverter, few hundred AH of 12 volt battery bank. Can charge cellphones, run some LED lightning, charge batteries (AA, AAA, for lights/radio, some cordless power tools, etc.). Have a genset and some fuel to take me through a week or two of no-power. Instead of AC battery chargers, maybe a simple 12 VDC charger or even a USB to Battery Charger setup (multiple cell types such AA, AAA, 18650 Lithium cells and a USB battery pack).
For full time on a rural property. A fridge, LED lights, water pump, possibly a clothes washer, cell phone, laptop, RV water pump or "solar friendly" water pump, etc... That can easily be that 3,300 WH per day.
My stored fuel is not a great choice--Mostly gasoline with preservative that is recycled back into the car once a year (and some 20 lb propane tanks). A small/efficient inverter generator (I like 2000-3000 watt AC inverter-generators--The will run most plug-in appliances, and refrigerator on 2 gallons of fuel per day--Vs a "cheap and noisy" 3-10 kWatt genset that can run >6 gallons of fuel per day even with small loads).
If you don't need to power a refrigerator long term, then a small system (500-1,000 WH per day with a 300 Watt or so AC inverter on 2x 5 volt @ 200 AH battery banks) will do nicely. Just to give you an idea:- 2 * 6 volt * 200 AH (2x golf cart batteries in series) = 2,400 WH storage (or 12 volts @ 200 AH)
- 2,400 WH DC Storage * 1/2 days usage * 0.50 planned discharge = 600 WH per day
- 600 WH per day / 5 hours of use at night (water pumping, LED lighting, cell phone, tablet computer) = ~120 Watt average load
- AC or DC loads (LED lights DC, cell phone & tablet DC USB, 12 volt RV pump)--Can be mostly DC (no inverter losses).
Recharge with genset (bad weather) or by sun (good weather). The solar array:- 14.5 volts charging * 200 AH * 1/0.77 panel+controller losses * 0.05 rate of charge = 162 Watt minimum (emergency) array
- 14.5 volts charging * 200 AH * 1/0.77 panel+controller losses * 0.10 rate of charge = 325 Watt nominal (full time off grid) array
- 14.5 volts charging * 200 AH * 1/0.77 panel+controller losses * 0.13 rate of charge = 422 Watt max "cost effective" array
- 600 WH per day * 1/0.61 DC off grid FLA system eff * 1/2.56 Hours of sun (December) = 384 Watt Dec "break even" array
A simple 300 Watt AC inverter (handy to have). I like this one because it has a nice on/off remote switch, no fans, rugged:
https://www.solar-electric.com/morningstar-si-300-115v-ul-inverter.html
I am sure you can find many others for less price and with "different' options.
Your "upgrade" is a parallel second string of golf cart batteries for a 12 volt @ 400 AH battery bank. And, for sure, the 5x 175 Watt panels in series. for 2x more stored power.
Possibly some sort of battery charger from AC genset to battery bank (if needed). 20-40-80 Amp range.
For some folks. Use "battery/solar" for evening/overnight loads (lights, radio, etc.) and use a solar+genset (as needed) to recharge during the day.
Shopping list:- 2 or 4 "golf cart batteries (6 volt @ 200 or so AH) in series/parallel for 12 volt battery bank (replace every 3-5 years
- 3x 175 watt panels minimum to 5x 175 Watt panels max
- 1x Renogy 60 Amp MPPT charge controller
- 1x 300 Watt or so 12 volt AC inverter
- Circuit breakers to protect wiring (to charge controller, to AC inverter). Easy on when needed, easy off (inverter/DC loads) in "storage".
- 3 * 175 Watt array * 0.61 dc system eff * 2.56 December = 820 WH per average December day
- 5 * 175 Watt array * 0.61 dc system eff * 2.56 December = 2,050 WH per average December day
- 3 * 175 Watt array * 0.61 dc system eff * 4.59 April = 1,470 WH per average April (summer) day
- 5 * 175 Watt array * 0.61 dc system eff * 4.59 April = 3,675 WH per average April (summer) day
Maximum suggested in inverter (i.e., 400 Watt maximum and 1/2 size at 200 Watts is nice too).- 200 AH @ 12 volt FLA battery bank => 400 Watt "maximum suggested" AC inverter
- 400 AH @ 12 volt FLA battery bank => 800 Watt "maximum suggested" AC inverter
Some additional tools:- Some sort of battery hydrometer (needed for FLA batteries).
- Some sort af AC/DC Current Clamp DMM.
https://www.solar-electric.com/midnite-solar-battery-hydrometer.html (nice one)
https://www.amazon.com/UNI-T-Digital-Handheld-Resistance-Capacitance/dp/B0188WD1NE (AC+DC clamp meter, inexpensive and good enough for our needs).
The hydrometer--There are glass float types--But they roll off tables and break easily. Also rinse out hydrometers after use with distilled water (electrolyte dries inside and gets sticky).
And a simple $10 AC+DC DMM (digital multi-meter) is fine too. The current clamp is really handy to have if you want to better understand how your system works (just "clamp" on a cable to measure in Amps (AC or DC, you select).
There are also energy meters out there... The Kill-a-Watt type is great for 120 VAC plug in loads. The DC monitors are nice for DC loads. And there are DC Battery Monitors of many types that make battery monitoring much easier:
https://www.amazon.com/killawatt-meter/s?k=killawatt+meter
https://www.amazon.com/s?k=dc+power+monitor
https://www.amazon.com/Battery-Capacity-Indicator-Monitors-Lead-Acid/dp/B08L8RDW17
Your thoughts?
-Bill
Near San Francisco California: 3.5kWatt Grid Tied Solar power system+small backup genset -
Nice website and community service Bill.
We are still doing a bit of volunteer work with a Boy Scouts/Ventures crew in our area, but have dialed back after our kids grew up.
-BillNear San Francisco California: 3.5kWatt Grid Tied Solar power system+small backup genset -
Solar is one of the things that it is difficult to make cheap, especially if you don't have a good plan/design in the first place.
What I don't want is you to have the system work for a few days or during the summer, and go dead after a few days of use in winter conditions.
The "heart" of your system is the battery bank. The bank needs to support your loads (without killing the bank) and the charging sources (solar, genset, AC power) needs to recharge the bank in the next day or too--Keep the battery bank "Happy".
People generally underestimate their energy usage, and overestimate how much energy a solar power system can supply. And they end up with an over-sized inverter and undersized battery bank and solar array. Under charge / over discharging will kill a battery bank in months, weeks, or even days.
You are not the first, and you will not be the last that went down that road. (not pointing fingers, just a fact which we often see here).
Pushing energy conservation and usage/setting expectations is what I/we do first.
Also remember battery banks age (battery end of life at 80% to even 50% of capacity, depending on vendor and your needs). 20 years and solar panels are dusty/dirty and degraded to 80% of capacity. And most electronics have an approximately 10+ year life. And usually are not repairable after 5-10+ years (vendors no longer support, electronic parts are no longer available, no schematics/bills of material, etc.).
Keeping your energy needs low, and the solar system "small" helps keep maintenance costs low too.
-BillNear San Francisco California: 3.5kWatt Grid Tied Solar power system+small backup genset -
If you go to our web site, check the adventure travel button for some adventure world wide camping stories and photos.I just purchased the AC+DC clamp meter, that you recommended.I already have batteries that I want to use and replace with similar deep charging 110ah 12volt semi truck batteries when these batteries need replacing.I am going to follow your suggestion of using a battery charger with the generator during power out situations to charge batteries when the solar can not keep up. I just bought a 40 amp battery charger at Walmart.https://www.walmart.com/ip/Onemayship-400W-12V-24V-Heavy-Duty-Smart-Car-Battery-Charger-Automatic-Pulse-Repair-Trickle/1052854801?athbdg=L1700You keep recommending that I buy a lower capacity inverter, but I have already purchased the 3000 watt inverter and paid for it.I was going to bury the 1/0 welding in two 3/4" PVC conduit pipes because I thought it safer. But now I'll follow your suggestion to put them in together in a 1" conduit pipe. I'll probably have to use liquid dish soap on the cables to help them slide throughWhen I bought the controller, it came with a electronic system monitor.I have decided to hook up the solar panels in parallel the way I'm set up with a controller that I understand requires the same voltage on both sides of the controller..I have purchased reducer connectors and screw tightening end lugs for the 1/0 cablesI have purchased both a + bus strip and a - bus strip .I have purchased #4 welding cable to connect between components and the power busesI still have to purchase the cable to connect the inverter to the + & - power bus.I was planning to mount the three solar panels on roof of an army trailer we are using for tool and supply storage but increasing the number of panels requires more space so I'll make a ground mount for them.You mentioned RV and generator/shore power problem. We had that problem of causing the GFI to trigger in a camping area and have remedied it with a switch recommended by an electrician by the circuit breaker panel and generator.
-
Sorry if you didn't understand what I was saying about your charge controller info that you posted. I can help you understand perhaps in stating that a charge controller is usually rated at output current (amps) so it will handle more wattage at higher voltage as it shows in your info sheet. 800watts/12volts, 1600watts/24 volts, or 3200watts at 48 volts.
If you ask;TellGRBill said:"Your charge controller can only handle 800 watts, so you'll need another charge controller."Does this mean that the controller can not handle the 1275 watt solar panels?
I've built and helped many build off grid systems, I'm glad to explain further, but it appears you would prefer Bill's help. I can add info to my replies if you ask but can't read minds or answer questions put to you.
We understand you have purchased a 3000 watt inverter and desire to use what you have.
I've lived off grid on solar for 20+ years. Helping people (and getting help) here for 10+ years.Home system 4000 watt (Evergreen) array standing, with 2 Midnite Classic Lites, Midnite E-panel, Magnum MS4024, Prosine 1800(now backup) and Exeltech 1100(former backup...lol), 660 ah 24v Forklift battery(now 10 years old). Off grid for 20 years (if I include 8 months on a bicycle).
- Assorted other systems, pieces and to many panels in the closet to not do more projects. -
Thank you for your advice Photowhit. I was on a roll with Bill and felt I needed to continue that roll.
-
As Photowit says--You have to review the documentation with each of your major devices and respect their limits.
In general a good quality MPPT controller can be "over paneled" to a degree--And it will safely limit/clip its DC output to rated current (60 Amps).
A common reason to over panel is that solar panes output less power than their marketing number seem to claim. In "real life" for example:- 5 * 175 Watt panels = 875 Watts Standard Test Conditions
- 875 Watts * 0.77 panel+controller deratings = 674 Watts realistically observed maximum under operating conditions
- 674 Watts * 1/14.5 Volts nominal charging voltage = 46.5 Amps typical max output (solar noon, cool day, battery less than 80% full, etc.)
Normally, following the Mfg's specs--Yes, you would need two 60 Amp Renogy controllers with 1/2 the panels (~640 Watts) to one MPPT controller, and ~640 Watts to the other (or any other "in spec" variation--The two arrays do not have to be "electrically" the same. Each controller will take what it is given Vmp & Imp wise). Each controller would be "maxed out" at ~800 Watts Per specs.
If you want to try a 300 Watt AC inverter and not spend much money, you can get them from Amazon for $20-$50...
https://www.amazon.com/300-watt-inverter/s?k=300+watt+inverter
For your present ~570 AH @ 12 volt bus battery bank, in good shape, the maximum suggested inverter would be:- 570 AH * 250 Watts * 1/100 AH (per amphour) = 1,425 Watt maximum suggested AC inverter for this bank
The "problem/issue" with these very inexpensive AC inverters is that they are probably MSW (modified square/sine wave) 120 VAC. MSW wave forms can be "hard" on induction motors and many small AC power bricks, wall transformers and such can overheat.- The above models don't state if MSW or PSW/TSW (pure/true sine wave) or not. The link below brings up PSW inverters that are around $50+. Certainly worth a try--If "most" of your AC loads are 300 Watts or less:
https://www.amazon.com/s?k=300+watt+inverter+psw
I do recommend PSW/TSW type inverters. It is the old 80/20 rule. 80% of the 120 VAC loads work fine, and 20% have "issues". And it is not simple to figure out which loads will overheat on MSW inverters.
Regarding conduit--I just buy over-sized conduit to give me room for more cables later and easier pull now (i.e., one 875 watt pair of cables vs two pair of 640 Watt array cables later). Buy once, bury once (I am cheap, I like ABS as it is more rugged than PVC--it seems to me--But it is not "to code").
Regarding batteries... A 12 volt @ 100 AH battery stores the same amount of energy as a 6 volt @ 200 AH battery (12v*100ah=6v*200ah) or 1,200 WH.
Personally I like to put two 6 volt batteries @ 200 AH in series vs 2 x 12 volt @ 100 AH in parallel. Fewer cells to check and water(6 vs 12 cells). Easier to do a quick voltage/health check (i.e,. measure each 6 volt series connected battery for voltage; vs 2x 12 volt batteries in parallel--The voltage measurement is the average to the two batteries). There are also wiring issues to balance current flow (more difficult with a bunch of parallel batteries) and I like larger plate deep cycle batteries (i.e., 200 AH cell vs 2x 100 AH cells).
And you have to verify the "Truck Batteries" are really deep cycle batteries and not SLI (starting/lighting/ignition) or Marine (compromise between SLI and True Deep Cycle). And golf cart batteries are usually cheap and plentiful.
For solar panel connections--Ideally at least 2 panels in series and a maximum of 5 panels in series. Your good choice options for driving a 12 volt batter bank:
1 panel total: 1 series panel = 1 series * 1 to 5 panels in parallel (not a good use of MPPT capabilities)
2 or 4 panels: 2 series panels = 2 series * 1 to 2 panels in series (good use of MPPT) and 2 or 4 panels
3 panels: 3 series panels = 3 series * 1 string (3 panels max) (good use of MPPT). 6+ panels is over controller rating @ 12 volt bank
4 panels: 4 series panels = 4 series * 1 string (good use of MPPT)
5 Panels: 5 series panels = 5 series * 1 strong (good use of MPPT, maximum Power rating for controller)
There are 2 other options using a total of 6 panels:- 2 series * 3 parallel strings = 1,050 Watt STD array rating and 809 Watts derated array.
- 3 series * 2 parallel strings = 1,050 Watt STD array rating and 809 Watts derated array.
Regarding the choice of (for example) 2s * 2p or 4s * 1p... There are some technical issues why 2s * 2p is slightly more efficient (by something like 1%). But I would not lose any sleep over it. As long as your panels are "shade free" from 9am-3pm (at least) no difference.
What you cannot do is connect 2 series for one string an 1 series for a second string and parallel them together. Each string needs to have "matched' Vmp voltage. 2s+1s in parallel--The 1s string will not supply any significant amount of to the array (it will be equivalent to 2s two panel array).
Shading "kills" solar PV panel output--So just keep them free of shade as much as you can.
Regarding GFI issues. A common GFI trip is (below "looks like" short between Neutral and Ground to GFI--Which it is):
Shore power => GFI outlet => RV AC panel
N+G bond sound like N+G bonded
The "fix"
Shore power => GFI outlet => RV AC panel
N+G bond Switch "off" N+G
Same with Genset (for many gensets) as "larger" genset types (typically 3.5 kWH or larger?) have N+G bond and GFI outlets (looks like shore power N+G bonding).
If you have a smaller genset, they usually "float" the Neutral (no ground bond) and don't have a GFI outlet to trip.
Don't know if your solution--But it sounds similar.
4 AWG cable (using NEC) is good for 70-95 amps depending on insulation temperature rating.
https://lugsdirect.com/WireCurrentAmpacitiesNEC-Table-301-16.htm
Roughly:- 12 VDC * 70 amps * 0.85 inverter eff = 647 Watts max 120 VAC inverter output @ single run of 4 AWG cable
- 12 VDC * 95 amps * 0.85 inverter eff = 969 Watts max 120 VAC inverter output @ single run of 4 AWG cable
- 1,475 Watts (max inverter output per bus bank) * 1/0.85 AC inverter eff * 1/10.5 volts batt cutoff = 165 Amps max @ 12 volt bus
Which from NEC table would be 1/0 to 3/0 cable (depending on insulation rating). Or, you could parallel 2x 4 AWG cables rated for at least 83 amps.
NEC "frowns" on paralleling smaller cables... But it is done (keep each pair of cables "identical length" so they ave equal resistance and equal current flow.
Not an ideal solution--But makes best use of what you have.
Of course, this depends on your 'required' AC output from your 3 kWatt inverter (1,425 suggested max, or more).
And please read/follow Photowhit... He has a whole bunch of real life experience trying to build/run low cost / high cost efficiency solar power systems. And buying hardware on sale/etc. to save costs too.
I am giving you the "engineer's" answers. Which are a bit more on the conservative side. I am not a solar power engineer--So talking with Photowhit and others with the experience on their own systems is a great source of information too.
-BillNear San Francisco California: 3.5kWatt Grid Tied Solar power system+small backup genset
Categories
- All Categories
- 224 Forum & Website
- 132 Solar Forum News and Announcements
- 1.3K Solar News, Reviews, & Product Announcements
- 196 Solar Information links & sources, event announcements
- 893 Solar Product Reviews & Opinions
- 255 Solar Skeptics, Hype, & Scams Corner
- 22.4K Solar Electric Power, Wind Power & Balance of System
- 3.5K General Solar Power Topics
- 6.7K Solar Beginners Corner
- 1K PV Installers Forum - NEC, Wiring, Installation
- 2.1K Advanced Solar Electric Technical Forum
- 5.5K Off Grid Solar & Battery Systems
- 427 Caravan, Recreational Vehicle, and Marine Power Systems
- 1.1K Grid Tie and Grid Interactive Systems
- 652 Solar Water Pumping
- 815 Wind Power Generation
- 624 Energy Use & Conservation
- 616 Discussion Forums/Café
- 309 In the Weeds--Member's Choice
- 75 Construction
- 124 New Battery Technologies
- 108 Old Battery Tech Discussions
- 3.8K Solar News - Automatic Feed
- 3.8K Solar Energy News RSS Feed