Help with Low Power Mountain Top Solar Radio Repeater
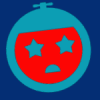
Hello,
For the past two years I have been experimenting with making a small GMRS radio repeater. The radio, a Retevis RT97, does not use much power. It uses about 2 amps at 12 volts when transmitting and 75 milliamps in standby. It is in standby most of the time. The charge controller is a simple PWM. It charges it charges at 14.6/14.4/ and floats at 14.0 volts. It has a low voltage load cut out circuit that will turn off the load at 11.2 volts. It will reconnect the load when it sees voltages over 12.6. More information on the controller is at the bottom.
Field Trials:
My first attempt was using a 9 amp hour battery and a 30 watt panel with a 10 amp PWM controller. This worked well enough during the late spring, summer early fall when we have an enormous amount of sunlight. During the winter it would start to shut down and take nearly a week or so to come back online for a few days before going down again. Around February of 2021 I went up to check on it. I found the solar controller off and the battery was showing 2.5 volts. Brought the battery home and when warm it moved up to around 5 volts. I was able to "recover" this battery but I haven't done any load tests on it to see how it fared. I assumed the battery and panel were too small to make it through cloudy days, the voltage dropped, cut off, and then the battery froze. Once the battery froze the controller shut down and never came back online.
For my next attempt I figured I would increase the solar generation capacity, increase battery storage capacity and put the battery underground to protect it from the cold snaps. I added a 50 watt panel, changed to a 35 SLA amp hour battery and put it just over a foot under ground. That setup was installed in May of 2021. It worked without going down all spring, summer, fall and into the winter. I subjected the radio to some "strenuous" use during December and it saw several days where it had about 4 hours of transmitting time.
On December 20th I was using it for several minutes and it shut down mid transmission. This lead to me believe that it hit the low voltage cut off. Being in Alaska, and the day before winter solstice, I wasn't all that surprised. At this time of year the panels only get 3 hours of sunlight directly hitting them. December was also a very cloudy month. It was about 20 degrees F that week. The following week we had nearly 7 days of clear skies and full sun. The air temperature dropped to around -15 degree F at night that week. Near the end of the week the system had not come back online and I grew suspicious. I figured maybe the battery froze or maybe the panels can't make enough power to get the voltage up above 12.6. The outdoor air temperatures have been in the upper teens to 30s for the past few days. The ground temperatures are showing around 20 degrees F based on research I did online but I suspect them to be closer to 0 or 10 degrees as that is more in line with a average daily temperature.
Experiments:
I took a 14 amp hour SLA battery, ran it under a 2 amp load at 66 degrees F until the cut off circuit of a spare charge controller turned off the load at 11.2 volts. I placed the battery outside in the negative temperatures for 24 hours. When I checked the battery it had a voltage of 11.8 and could still run the light bulb for a short time before hitting the low voltage cut off again. It didn't appear to freeze in the negative 10 to 15 degree evening.
I then took that cold battery, the charge controller, and a spare 30 watt panel out to sunlight around noon. I hooked up the charge controller and it was still indicated a low battery and kept the load circuit shut off. Once hooked up to solar, the 30 watt panel took only a minute or two to get the voltage above 12.6 volts. This turned the load circuit back on. Several minutes later the voltage of the battery was up at 14.4 volts while connected to the panel. I measured to amps between the controller and the battery. In full sun the 30 watt panel and PWM was creating one amp of power to the battery. Clearly, in full sun, the panel can create enough power to reach standard charging voltages. So that doesn't appear to be the issue....and neither does a frozen battery based on my next tests. The attached images are from this test.
I did a second test. One where I tried to freeze a SLA battery. I have an older 3.3 amp hour battery. I attached the charge controller to it and discharged it with a .5 amp load for several hours before the controller shut off the load. The voltage stabilized at 12 without the load after about 30 minutes. I connected the load right to the battery and drew it down to sub 9 volts. The battery stabilized to 11.3 volts after a few hours. When I connected the charge controller, the small, ~20 milliamp load, brought the voltage down to 10.5 volts. I chucked this whole contraption in the freezer for 12 hours. Checked it again and the controller is still on, still indicating low voltage and the load circuit is off. The voltage still reads 10.5 volts. It weakly illumining my .5 amp load (a light bulb) and the voltage dropped to around 4 volts before recovering back to 10.5 upon removal. I assume this means the battery, even in such a low state isn't frozen?
The final test I did was taking the charge controller (I have a few of these lol), and seeing how it reacts to low voltages. I used a buck converter to raise and lower the input voltages. I found that it can run with voltages as low as 2.5 to 3 volts. Below those it will shut down. Once the voltage creeps above 2.5 to 3 it turns back on. As the voltages increase it will turn the load back on as normal. This seems to indicate that if a battery froze and stopped producing power, once the battery thawed the controller would come back to life. With the controller coming back to life I would assume it would start adding power from the panels. The only thing I didn’t test to far it to see how the controller reacts when solar is connected under such extreme low voltage situations.
Thoughts/Problems:
I almost am starting to feel like maybe the solar controller has failed somehow and the battery is “okay”. The battery is surly in a very low state of charge but I don't think it is frozen and incapable of taking a charge at the moment. I tried to confirm this by visiting the site but due to weather and terrain it is inaccessible.
The current charge controller is a Hunie 10 amp PWM I got on Amazon.
https://www.amazon.com/HUINE-Waterproof-Controller-Intelligent-Regulator/dp/B07Q79TC2L/ref=sr_1_1?crid=TAYDHBWGBXOW&keywords=huine+10&qid=1641936630&sprefix=huine+10%2Caps%2C186&sr=8-1
I decided to try an EPEVER MPPT controller for next year…mostly b/c I can program a higher cut off voltage to protect the batteries better when I fail to get them charged. I chose the 10 amp Traver2606BP.
https://www.epever.com/product/tracerbp-10-30a-mppt-charge-controller/
Again this is a remote mountain top setup. The only way to get to it is backpacking so size and weight constraints are a major contributing factor. My questions are, where are the flaws in my system, am I using flawed logic, does anyone have any similar situations and what suggestions do you have to overcome these issues.
Comments
-
see the battery freeze/charge chart below. It's rare to be cold enough to freeze a charged battery. Discharged, the battery will freeze and must be thawed before recharging - can't charge a frozen battery safely. Boom !!
I'd say get a standard "marine" AGM battery about 80ah. They are common enough to be cheap, maybe cheaper than the 35ah battery.
More panels. if batteries are going flat, you need less use, or more charging. If you select 21-18V panels, you can keep the PWM controller if within it's amp limits. Otherwise get a +160w grid tie panel @ 40V and use a MPPT controller. Cost money, but would stay on the air.
AGM can survive freezing, flooded cannot. AGM & Flooded share the same temperatures.
Make sure your charge controller is rated for the temperatures it will see, Morningstar makes some wide rated ones.
Powerfab top of pole PV mount | Listeroid 6/1 w/st5 gen head | XW6048 inverter/chgr | Iota 48V/15A charger | Morningstar 60A MPPT | 48V, 800A NiFe Battery (in series)| 15, Evergreen 205w "12V" PV array on pole | Midnight ePanel | Grundfos 10 SO5-9 with 3 wire Franklin Electric motor (1/2hp 240V 1ph ) on a timer for 3 hr noontime run - Runs off PV ||
|| Midnight Classic 200 | 10, Evergreen 200w in a 160VOC array ||
|| VEC1093 12V Charger | Maha C401 aa/aaa Charger | SureSine | Sunsaver MPPT 15A
solar: http://tinyurl.com/LMR-Solar
gen: http://tinyurl.com/LMR-Lister , -
After 36 hours in a freezer at 0 degrees the small SLA test battery was reading 8.5 volts while running the test charge controller. When disconnected and let to settle for about 10 minutes it read 10.2 volts. We have overcast skies with some back light lighter clouds from the sun in one part. I took the 30 watt panel pointed it towards the brightest part of the sky and connected it to the cold battery and cold charge controller. It started adding back in power.
I don't know what to make of this beside that clear when the controller is working that even a beyond dead battery will power up the charge controller enough to keep it running. In this extreme low voltage state the charge controller will still add power back in when presented with PV power. It has been maybe 20 minutes and the voltage was raised to 12.5. I removed the power from the panel, put it back in the freezer, and let it sit for 10 minutes. The voltage was showing 9.42 while running the charge controller. I removed the controller and it back in the freeze for 10 minutes and the voltage showed 11.62. It clearly gained some power in just that short time.
So worst case scenario: The load is pulling power right at the end of the day. The low voltage cut out removes the load right as the sun sets. The solar controller, not seeing power being generated by the panels now, changes from generating power to stand-by. The charge controller is puling 15 ish milliamps while just running. Over night it snows...and by some unrealistic chance the snow sticks to the panel (which is nearly vertical). The sun returns 18 hours later but the panel is covered in snow and takes a few days to clear off. When the snow clears the sky is overcast. The panels start to add power back in. This would make slow progress towards a recharge but more significantly would at least prevent a total discharge to a flat battery until clear skies return to fully charge the battery. Correct?
Being as the load is so small it would take a significant amount of time to run down that 35 amp hour battery to the point of below 3 volts where it can no longer even power up the charge controller. Besides a failure of the charge controller itself, the battery being run to below 3 volts is the only way I can see this system not self-recovering from a low voltage state. Correct?
I fully understand how horrid this is for the battery and this is far far from ideal but it leaves me to believe that the $20 charge controller failed some how and not the battery.
Does anyone have any experience with those small waterproof EPEVER charge controllers?
In a more ideal situation the controller won't fail on me in the middle of winter and I would like to have the low voltage cutout 11.6 volts. I even thought of pushing it "way up" to 12.0 volts. This higher voltage pushes the battery that much further from freezing temps and should help lengthen the life. It would also "shorten" the recovery time until the load is turned back on. While a drain down 11.6 volts is still too low for repeated cycling and long life it really should only see that point once or twice a year. It is more of a fail-safe.
Is my logic in all this just wrong? -
mike95490 said:see the battery freeze/charge chart below. It's rare to be cold enough to freeze a charged battery. Discharged, the battery will freeze and must be thawed before recharging - can't charge a frozen battery safely. Boom !!
I'd say get a standard "marine" AGM battery about 80ah. They are common enough to be cheap, maybe cheaper than the 35ah battery.
More panels. if batteries are going flat, you need less use, or more charging. If you select 21-18V panels, you can keep the PWM controller if within it's amp limits. Otherwise get a +160w grid tie panel @ 40V and use a MPPT controller. Cost money, but would stay on the air.
AGM can survive freezing, flooded cannot. AGM & Flooded share the same temperatures.
Make sure your charge controller is rated for the temperatures it will see, Morningstar makes some wide rated ones.
https://www.batteriesplus.com/productdetails/slaa12=35c
The charge controller states its rated for -20 C to +60 C. I guess from a technical standpoint that is only -4 degrees F. So I am outside it's bounds. I guess this is another obvious strike towards the controller being the issue. -
I always like to try a little "modeling" of systems with some pretty simple math... Jumping right in:
- 24 hours per day * 0.075 Amps (standby) * 12 volts = 21.6 Watt*Hours per day (standby)
- 2 hours per day * 2.0 Amps (transmitting) * 12 volts = 48 Watt*Hours per day (transmiting)
- 21.6 + 48 = 70 WH per day
- 70 WH * 3 days * 1/0.50 max discharge * 1/12 volt battery bank = 35 Amp*Hour @ 12 volt battery bank.
- 35 AH * 14.4 volts charging * 1/0.77 pane+controller deratings * 0.05 rate of charge = 33 Watt array minimum
- 35 AH * 14.4 volts charging * 1/0.77 pane+controller deratings * 0.10 rate of charge = 65 Watt array nominal
- 35 AH * 14.4 volts charging * 1/0.77 pane+controller deratings * 0.13 rate of charge = 85 Watt array "typical" cost effective maximum
Also note that the "recommended" charging current is a good match for loading in sunny climates... In poor sun areas (Alaska in winter), you need a lot more solar panels to get any useful amount of solar harvest (typically, 3 hours or more sun per day is "OK").
And sizing the array based on your daily loads and location... Picking Anchorage Alaska for your location (purely a guess), fixed array facing south and nearly vertical panel.
http://www.solarelectricityhandbook.com/solar-irradiance.htmlAnchorage
Measured in kWh/m2/day onto a solar panel set at a 14° angle from vertical:
Average Solar Insolation figures
(Optimal winter settings)
Looking at December:Jan Feb Mar Apr May Jun 0.91
1.93
3.23
4.07
4.30
4.24
Jul Aug Sep Oct Nov Dec 3.82
3.48
3.09
2.39
1.34
0.54
- 70 Watt*Hours * 1/0.61 off grid DC solar system efficiency * 1/0.54 hours of sun per day December = 213 Watt array December "break even" [fixed typo. -Bill]
- 213 Watt array (for December) * 1/0.50 base load "fudge factor" = 426 Watt array for base loads (little or no genset backup)
Obviously... If you only "expected" 0.5 hours of activity per day from the repeater, you could cut the December array by 1/2--And you could use a 1/2 (or even smaller) solar panel/array.
Charging an AGM (Lead Acid) battery at 0F (-18C)... The typical charging voltage increase is -0.005 volts per cell per degree C:- 14.4 volts charging + -0.005 volts per Cell per C * 6 cells (for 12 volt battery) * (-18C actual - +25C standard temp) = 14.4 volts std + 1.29 volts cold offset = 15.69 volts charging (@0C)
From what little I have read--12 volt solar chargers need ~9 volts minimum to restart (assuming you are charging a 12 volt battery bank--Many charge controllers will use the "initial" battery voltage (i.e., under 17 volts = 12 volt battery bank; over 17 volts = 24 volt battery bank)--Unless they have a switch/software setting for bank voltage.
There is a good solar harvest estimator here--You can put in latitude and longitude and, if you want, a downloadable .cvs (spreadsheet) so you can see "hour by hour" energy harvest:
https://pvwatts.nrel.gov/pvwatts.php
It is not quite as easy to use--But can give you better results for "out in the middle of nowhere" results.
The above is not intended to be "the answer"--But more of an example of the math and decisions (and fudge factors) that go into sizing the system. The numbers are fairly conservative.
Your thoughts, corrections, and questions?
-BillNear San Francisco California: 3.5kWatt Grid Tied Solar power system+small backup genset -
Thank you so much for taking the time to reply. I am grateful for the shared knowledge. The actual use of the repeater can be pretty low. It's primary purpose was for friends and family back up communication when the cell networks go down. In the 2018 Earthquake we were without comms for nearly the whole day. It's use has expanded slightly and I opened it up for general use by other GMRS users including in the 'back country' areas it reaches.
30 min of transmission time a day is pretty heavy. At best it sits idle for the week and sees a 2 hour net when linked into the myGMRS.com network on a Sunday. I was getting a bit greedy and pushed the limits with the weekly nets for 4 weeks straight during the darkest time of the year.
Size and weight constraints at the moment preclude going with a larger array at this point. The thing working to my favor is the rapidly increasing amount of sun outside of December. We darn near have 24 hours of light here at Summer solstice. It appears that if I can get a reliable solar controller for the cold and one that can temperature compensate that might solve my issue with the failure I am having. If I limit the use of the repeater during the dark month of December I should be sitting in a good spot.
-
BB. said:I always like to try a little "modeling" of systems with some pretty simple math... Jumping right in:
- 24 hours per day * 0.075 Amps (standby) * 12 volts = 21.6 Watt*Hours per day (standby)
- 2 hours per day * 2.0 Amps (transmitting) * 12 volts = 48 Watt*Hours per day (transmiting)
- 21.6 + 48 = 70 WH per day
- 70 WH * 3 days * 1/0.50 max discharge * 1/12 volt battery bank = 35 Amp*Hour @ 12 volt battery bank.
- 35 AH * 14.4 volts charging * 1/0.77 pane+controller deratings * 0.05 rate of charge = 33 Watt array minimum
- 35 AH * 14.4 volts charging * 1/0.77 pane+controller deratings * 0.10 rate of charge = 65 Watt array nominal
- 35 AH * 14.4 volts charging * 1/0.77 pane+controller deratings * 0.13 rate of charge = 85 Watt array "typical" cost effective maximum
- 70 Watt*Hours * 1/0.61 off grid DC solar system efficiency * 1/0.54 hours of sun per day December = 213 Watt array December "break even" [fixed typo. -Bill]
And typically, if you "needed" the system to run every day (at 2 hour xmit and 22 hours receive)--Would suggest that you only use 0.65 to 0.50 of "predicted" solar harvest:- 213 Watt array (for December) * 1/0.50 base load "fudge factor" = 426 Watt array for base loads (little or no genset backup)
That is based on a half hour average of solar correct?
There is no way I can create that large of an array for this particular project. This means I need to cut my power consumption and/or increase the battery reserve to push past the darkest parts of the winter.
I can easily cut the myGMRS nets from the system in the winter. This would drastically reduce the power consumption to 25 watts a day.
Based on my test above at winter solstice I am getting 50% efficiency from the panels in direct sunlight. The 30 watt panel was making 14.4 watts.
That means that I need a hour of sunlight a day on a 50 watt panel to replace what is used.
We don't get sun everyday due to clouds. Oftentimes we get two or three weeks of overcast and then a week of perfectly clear skies. So a 35 amp hour battery is 420 watts give or take. 210 watts for a 50 percent discharge gives me about 8.4 days of stand-by time with zero input from the panels. At that point the controller should shut off the load and it would need 2.8 days of sun at three hours of sun a day to fully charge.
If I moved to a 55 amp hour battery we get 13.2 days of standby and 4.4 days to recharge after a cutout.
This obviously discounts the solar panels production of power on overcast days which would help stretch the time to cutoff by some. I have not verified the panels efficiency here during winter on overcast days. -
The "50% fudge factor" (or 1/0.50 = 2x larger array) is just a suggestion for supporting "base loads" (those loads that need to run 24x7--Such as running a refrigerator vs a TV set which can be left off during bad weather).
Solar power is highly variable--Clouds, low hours of sun in winter, etc.--Solar panel just produce very little power.
It is just a "safety factor". If you do not need 2 hours per day of transmit during winter, can "live" with the system being down during a week of bad weather, etc, then you can adjust the system's size accordingly.
Based on the average hours of sun per day for December of 0.54... A 213 Watt panel would supply ~70 WH per day @ 2 hours of transmitter use per day.
The "efficiency" of solar panel harvest does depend on the type of solar charge controller you are using...
A PWM (pulse width modulation) solar charge controller--Temperature does not affect solar harvest very much. As lot-ng as Vmp is over Vbatt charging (i.e., 15 volt Vmp-array > 14.4 volts Vbatt charging) is all we are worried about.
Solar panel Vmp (voltage maximum power) varies with temperature. Warm to hot panels (warm summer day in full sun), Vmp can fall to almost 80% of rated output voltage. Sub freezing panels, Vmp can be 100% to maybe 110% of rated Vmp-standard-temperature.
Solar panel Imp (current maximum power) does fall with lower temperatures--But the reduction in Imp is 1/5 to 1/10 that of Vmp temperature deratings (hot temperature). In general, we ignore Imp vs temperature.
A MPPT (maximum power point) solar charge controller will efficiently take higher Vmp-array voltage and down convert to lower Vbatt voltage (and provide higher Ibatt current). Hot summer day of 80% * Vmp-array vs a sub freezing array of 100-110% * Vmp output power (power=voltage*current).
For larger solar arrays, the higher price of an MPPT type charge controller can be a better choice vs a cheaper PWM controller. Generally a MPPT controller is used for "higher Vmp-array voltage" arrays (such as a pair of 200 Watt Vmp=30 volt solar panels in parallel or even series connection charging a 12 volt battery bank).
A downside to MPPT charge controllers is that they take more energy to run the internal computer and buck mode down converter/switching power supply. If your panels are "in the dark" for a period of time (poor sun, snow on panels, etc.), the MPPT controller can add its own load to the battery bank and reduce harvest/discharge battery bank some too.
I also used an "over conservative" system derating of 0.61 (basically used Flooded Cell battery "efficiency"). A better estimate would be (for a PWM charge controller) would be:- 0.77 panel+controller derating (warm to hot weather) * 0.90 AGM battery efficiency = 0.69 overall DC solar system efficiency
- 1.0 "sub freezing Vmp voltage" * 0.95 MPPT controller eff * 0.95 AGM eff (deeper cycling AGM battery has better efficiency) = 0.90 overall DC system eff.
- 70 Watt*Hours * 1/0.61 off grid DC solar system efficiency * 1/0.54 hours of sun per day December = 213 Watt array December "break even" for FLA and PWM controller
- 70 Watt*Hours * 1/0.69 off grid DC solar system efficiency * 1/0.54 hours of sun per day December = 188 Watt array December "break even" for AGM battery + PWM
- 70 Watt*Hours * 1/0.90 off grid DC solar system efficiency * 1/0.54 hours of sun per day December = 144 Watt array December "break even" with AGM deeper cycling + MPPT controller in winter
- Wrong: * 0.61 *
- Correct * 1/0.61 *
The "deratings" and "fudge factors" are there to make calculations quick and easy... And to allow for the unknowns and variation in weather patterns (over the years--The "hours of sun" per day are typically based on 20+ year average measurements. +/- 10% year to year variations are "normal"--And a week or two of "bad weather" do happen on occasion. Solar harvest during heavy clouds can fall to 10% or 5% of the "sunny weather" harvest).
-BillNear San Francisco California: 3.5kWatt Grid Tied Solar power system+small backup genset -
I can tolerate the system going down in the winter a few times. I saw that as the nature of the beast being I wanted to limit its size and I am in Anchorage, Alaska. What really triggered this post was trying to do was cross check my theory. Again thank you for walking through what is probably super basic knowledge with me.
This whole project started out as just an experiment to see if I could get something to even function at all. Now that I have gotten so close to getting reliable 24/7 function I want to see it through.
It has been just over a month and it still has not come back online. That is the problem. Going down is fine but I need it to come back up. We just went through a week with the temperatures over 32 degrees, somedays reaching in the 40s and who knows what it felt like in the direct sun. If that battery froze up in the -10/-15 degree temps it should have thawed for sure. One thing I was trying to test before is what voltage and currant can a frozen battery put out? I was unable to get a battery to freeze but I would assume near zero? I am ruling out a frozen battery at this point. That leaves an electrical/mechanical failure of the repeater itself or the charge controller. I am leaning towards the charge controller based on last years experience. Without the site visit I guess I can't really prove anything.
I happen to have an MPPT Charge Controller due to arrive today. I bought one a few weeks ago due to the ability to "program" it. I wanted to be able to to set a higher cut out voltage. The main factor in my charge controller selection is it's IP rating. Needs to be very weather resistant.
I ordered an Epever Tracer 2606BP and the needed cable to connect to a computer. IF the specs are to be trusted it is rated for a much lower temperature than the Huine PWM I bought on Amazon and it uses a similar amount of power at 13mA. It also has some interesting timer modes that I want to see if I can set it to shut the load off during the midnight/early morning hours of the winter solstice. I see Epever also have a PWM, LS1024EPD, which is non-programmable but uses next to nothing at 5mA. If it does arrive today I will post some pictures and real work specs on its consumption.
Anyone have experience with this brand?
-
No problems with questions... Never hurts to get the details that underlie the various rules of thumbs we use around here--There are assumptions piled on assumptions many times.Lead Acid batteries are not very easy to quantify state of charge based on just voltage measurements. It is the nature of the beast.More or less--It looks like if you want to go down to -15F, you need to assume ~62% State of Charge to keep the battery electrolyte from freezing.Also, need to remember that at -15F, your Lead Acid/AGM only has about 50% of its "rated" capacity:-BillNear San Francisco California: 3.5kWatt Grid Tied Solar power system+small backup genset
-
If I had been paying closer attention I would have just ordered this instead of another China controller. Oh well.
https://www.solar-electric.com/ss-6l.html
-
Welp. The Epever seems to work alot better. It's uses 22-25 mA when running. Hooked to my 30 watt test panel sitting on my deck it is showing that about 50 mA are being made from the overcast and snowing skies.
This is it running with no load and no solar.
-
This is it running with no load and solar input.
-
With MPPT charge controllers, the Vmp-array should be a couple volts higher than the Vbatt--Charging...With your solar charger:It looks like it would be best to put two "Vmp~18 volt" "matched" panels in series... You get over Vbatt+2 volts, and stay under the Voc=46 volts (at 25C) and under Voc-cold=60 Volts (towards -40C?)....When you run Vmp~Vbatt (near Vbatt) on a MPPT controller solar input--The MPPT controller, more or less, behaves like a PWM controller... You need Vmp>>Vbatt (+2 volts or more) to get the Power=Volts*Current "help" of MPPT controllers.-BillNear San Francisco California: 3.5kWatt Grid Tied Solar power system+small backup genset
-
Mppt was a side effect of getting a programmable controller but running the panels in series is definitely something to consider now.
Also it looks like it does only consume 13 mA when the load is turned off. Even with no real load attached having the load "on" pulls about 10 mA.
Here is a screen shot of the setting I uploaded but I don't know what a few settings should be. The ones I changed came from the Technical Manual for the battery.
I couldn't find an Equalization Current Figure and I can't even tell if one is needed on AGM. I also don't know what Boost Recon Charging should be, nor do I even know what it is. Right now I am gonna guess that is the voltage the controller needs to see to switch from boost charging to Float? I have run of out time to "play" with this today but I will read into the help files some more later.
-
AGM (and most sealed lead acid batteries) do not need "EQ" charging (raising charging voltage to 15.0+ volts, and somewhere around 2.5% to 5% rate of charge (100 AH * 5% eq = 5 amps--Hold EQ and check Specific gravity every 30-60 minutes, and when cells stop rising in SG, or battery is overheating, then stop EQ).
For AGM, the EQ I have read about and seems to make sense... Once every 6 months make "EQ" voltage the standard charging voltage such as 14.4 volts for typical AGM and hold the voltage for ~8 hours. For AGM you do not want "controlled" overcharging as gassing occurs and will pop the cell pressure relief and vent gasses/electrolyte (and can overheat the AGM catalysts used to recombine the gasses back to water).
If you cannot do the 8 hour every 6 months--Just skip EQ. AGM cells tend to stay well balanced and EQ Charging is not manditory.
-BillNear San Francisco California: 3.5kWatt Grid Tied Solar power system+small backup genset -
Thank you. I set EQ at 0 which disables it. I contacted Epever to try and see what difference between discharge limit and low voltage cut off is. The low voltage cutoff removes the load but I don't know what happens before and after the discharge limit.
-
So I set up some parameters for daily consumption as follows:
10 min of transmission time a day, 17 hours and 50 min of standby and 6 hours off. This uses 29.64 watts/hours of power. The transmission times is very conservative to reflect the solar power issues in the dead of winter here. Outside of December transmission time can dramatically increase.
Running a 35 amp hour battery gives me some headroom. Remove 20% capacity for cold weather. Shutting off the load at 11.8 volts means I consumed about roughly 70% of the usable capacity. That is about 253 watt hours giving me a runtime 8.5 days of use with zero solar.
Once the load shuts down I need to have enough power in the battery to keep the charge controller going until it gets sun. We had three weeks of heavy clouds this winter in December. Each side was 'bookended' with several days of clear skies. With about 100 watt hours remaining in the battery that gives me about 24 days until it runs the battery to 10.5 volts. That should be plenty of time for a day or two of sun.
Based on my real world measurements, each sunny day at winter solstice makes about 135 watt hours with my panels, so about 3 sunny days are needed to push it back to "full charge" from full depletion.
Once we are away from December I have more than enough power. It's just that month of December.
___________________________________
Rates of Power Consumption:
Transmission = .17 hours x 2.15 amps x 12.9 volts = 4.72 watt hours
Standby = 17.83 hours x .104 amps x 12.9 volts = 23.92 watt hours
Off = 6 hours x .013 amps x 12.9 volts = 1.00 watt hours
Total Daily Watt Hours = 29.64
___________________________________Solar Panel/Charge Controller/Battery Efficiency = .72
___________________________________Avg Solar Insolence Per Day
November: 1.34
December: 0.54
January: 0.91
___________________________________Minimum Panel Sizes To Cover Power Consumptions:
November: 30.82 watts
December: 76.18 watts
January: 45.35 watts
June: 9.71 watts
___________________________________ -
Finally got to the repeater. Solar controller was off as I suspected. As soon as I hook up a fresh battery it comes alive.
With no load the battery shows 7.5 volts.
I attempted to jump it up to a higher voltage to see if she would at least take some kinda charge but it doesn't appear to want to take much, if any current from the battery I brought.
As soon as I disconnect the jump battery the voltage plummets back down. No spark or indicator or high current flow gives me the impression the battery is frozen. The ground is still frozen so can't get to that battery itself at the moment. -
A dead lead acid battery will freeze just below 32F. The electrolyte is close to water in specific gravity.The battery needs to be something like 50% or higher state of charge to not freeze in colder temperatures.BillNear San Francisco California: 3.5kWatt Grid Tied Solar power system+small backup genset
-
Yeah. She is froze. Voltage drops to .45 with the small 25 mA load. Battery is dead dead.
EDIT:
The only think I don't understand is how it froze....It was making power up until it shut down. When it shut down it was under a load. So if it had not been frozen when the load was shut down the voltage shouldn't really have dropped much more before seeing sun which would have added in power and thus increasing the batteries resistance to freezing. The only thing I keep coming back to is a faulty solar controller that wasn't turning off the load as it should.
For the trial next season I have the MPPT controller as you saw above and I got a "24 volt panel", (Vmp):33.54V. Hopefully the MPPT coupled with a much higher low voltage cut off will keep it alive next winter. -
I finally got the batter out of the ground. Still has some ice on it, which I expected, but the voltage was at 12.01 volts. It held that voltage under a small load. After a close inspection it appears the wire leading to the controller failed internally. Charged it up and it seems to be fine. Just a small additional voltage drop when under load vs a brand new one.
Oh well....reinforced the new power wire with a PET braided sleeve.
I am in the process of hiking version 3 up the mountain now. A 60 watt 24 volt (33 volts really) panel is the largest single panel I can handle.
-
Just figured I would swing in with an update. The repeater has been up and running with no down time all summer. Which is to be expected. I will say that we have had basically 2 months of clouds. July and Aug, while lots of daytime hours, were all cloud covered and/or raining.
Today we had about 4 hours of sunlight before the clouds rolled in again and it started to drizzle. I hiked up to the repeater and took some readings from the solar controller. In the 4 months it has been running it looks like the controller made nearly twice as much power as the unit consumed.
Winter will start setting in quickly here with sunlight dropping quickly. If it is possible I will hike up just prior to the first snow and grab one more reading before I can no longer access the site.
-
Welp. I didn't get back to it before we got snowed in but we made it past winter solstice and we have been up 100% of the time this year.
-
Just some more follow up. It is now Aug 8th 2023. It is still up and running. I took some readings from it a few days ago. I also added a LoRa radio with an INA260 current and voltage monitor so I can now see the real time (updates every 15 minutes) voltage and currant going to/from the battery at will while not having to be right at the site.
-
From the LoRa monitor what I can see is a fully charged battery during the day and held at a float voltage of 13.6, drops to about 12.95-12.9 volts over the course of the evening/morning with a draw of about 80mA. The sun comes up and the draw slowly tapers off and starts into a net positive. Such as today, I watched it climb to draw of about 0 by around 9AM. By 11AM it was showing about 500 mA at around 13.5 volts. It is starting to become overcast today. This reading was taken with obscured sun but still a fairly bright sky.
My question is this. If that reading, which is about 7 watts, stayed steady for an hour, does that mean 7 watt/hours would be put back in the battery or are there losses with the power absorption? -
More or less, you probably want to see around 14.0 to 14.7 volts charging (depending on exact lead acid battery type) to be charging....
At 13.6 to 13.8 volts you are probably (mostly) just floating the battery (making up for self discharge, and supplying current to your radio system loads).
For lead acid batteries, must of the energy goes into charging if the battery is 80% or less state of charge. For batteries at 90%+ SoC, most of the energy goes into "gassing" the batteries.
To a degree, your charging voltage depends on what the Solar Charge Controller thinks it needs to do... Simpler chargers will go into full charging voltage (14.4-14.8 volts or so) every morning when the sun rises. Hold that voltage for X hours, then drop back to float.
Newer, more sophisticated charge controllers will look at the SoC before sunrise. If the SoC falls below XX SoC (say 75% to 80% or less), then the charge controller will go into the full charging cycle. If the SoC (or battery "resting voltage" does not fall below XX SoC/YY Volts, then the controller will go to float. The theory being that Lead Acid batteries need to be cycled (for deep cycle type batteries) and do not do well if kept at float charge 100% of the time.
Do yo have a 60 Watt panel/array? More or less, would expect 50% to 77% of panel wattage (i.e., 30 Watts minimum) available on a random/typical day (some high clouds to bright/sunny day)... If it gets really cloudy, you would have less available harvest energy. On a very dark/gloomy day, 5% of array rating is certainly possible.
Here we are--You are getting 6/7 Watts of charging... Is that because the charge controller is limiting charging voltage to the battery to 13.5 volts (basically float charge), or is the solar array/wiring limiting current to the charge controller (or bad wiring connection from controller to battery bus)?
You are correct that 0.5 amps * 6 hours = 3.- AH or 6 Watts * 6 Hours = 36 WH into the battery... But to say that is charging or simply floating/gassing the battery--Really depends on the present SoC and charging voltage.
-BillNear San Francisco California: 3.5kWatt Grid Tied Solar power system+small backup genset
Categories
- All Categories
- 228 Forum & Website
- 136 Solar Forum News and Announcements
- 1.4K Solar News, Reviews, & Product Announcements
- 199 Solar Information links & sources, event announcements
- 898 Solar Product Reviews & Opinions
- 256 Solar Skeptics, Hype, & Scams Corner
- 22.5K Solar Electric Power, Wind Power & Balance of System
- 3.5K General Solar Power Topics
- 6.7K Solar Beginners Corner
- 1K PV Installers Forum - NEC, Wiring, Installation
- 2.1K Advanced Solar Electric Technical Forum
- 5.6K Off Grid Solar & Battery Systems
- 428 Caravan, Recreational Vehicle, and Marine Power Systems
- 1.1K Grid Tie and Grid Interactive Systems
- 654 Solar Water Pumping
- 816 Wind Power Generation
- 624 Energy Use & Conservation
- 619 Discussion Forums/Café
- 312 In the Weeds--Member's Choice
- 75 Construction
- 124 New Battery Technologies
- 108 Old Battery Tech Discussions
- 3.8K Solar News - Automatic Feed
- 3.8K Solar Energy News RSS Feed