Low current levels from solar panels under clear skies?!?
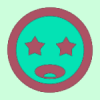
cottersay
Registered Users Posts: 6 ✭
We just set up your Renogy solar system for our RV. It consists of four Renogy 100W 12V Monocrystalline Solar Panels, wired (10AWG) in parallel to a Renogy Wanderer Li 30A 12V PWM NG Charge Controller, then on to our twin 100Ah BB 12V Lithium batteries (in parallel).
We are in Arizona (White Mountains) at almost 10,000 feet with measurements taken under clear skies*, and all of the solar panels are facing due South, angled upward toward the noon-day sun. Here are the pitiful current (Ampere) levels we are obtaining from each of these panels:
Panel #1: 0.49A
Panel #2: 1.38A
Panel #3: 0.39A
Panel #4: 0.46A
The total output current from the charge controller to the RV is only 2.70A.
For the conditions as described above, this is abysmally low, even panel #2.
Oddly, when a cloud moderately covers the Sun, the current level dips very little.
The Renogy controller has been set to Lithium.
Any suggestions, because the solar system as-is is pretty useless...?
Thank you,
-Cotter
*Clear skies for a few minutes in between a month of thunder, lightning, rain, hail, etc.
*Clear skies for a few minutes in between a month of thunder, lightning, rain, hail, etc.
Comments
-
Welcome to the forum Cotter.
I am sorry to read about the charging issues you are having with the Renogy system... Just an FYI, I am just a volunteer on this forum, and I do not work for NAWS. And NAWS does not monitor this forum regarding customer questions/issues--I have forwarded your post to NAWS.
But we can certainly see if we can help you now.
First thing--Solar panels when connected in parallel (4x panels with Vmp~17.5 volts connected in parallel to a single PWM charge controller?)--They generally share current very closely unless there are other issues.- No shading on any of the panels (even just some shade on one cell in a panel can but current by 1/2 or more). No vent pipes, Cell phone antenna, AC unit, vent fan, etc. casting shadows on the panels?
- How did you measure the current for each panel? One easy method is--If you have a 4 position circuit breaker combiner box--Just turn on one string at a time and read the PWM controller display (if you did this way, did you log the voltage per string too?). Another method is to use an AC+DC Current Clamp DMM--Just clamp one wire at a time (zero meter) and measure the current (hopefully, you measured all panels within a minute or so--Same sun/weather/etc...).
The amount of current (Imp--maximum power current, and Isc--maximum short circuit current) a solar panel will supply is based on the amount of sunlight hitting the cells/panels:- 100 Watts * 1/17.5 Volts Vmp = 5.71 Amps Imp (estimated)
Unfortunately, our eyes are not very good at estimating solar energy on panels.... More or less, "full sun/clear day" seems to be around 50% to 100% of Imp/Isc (using our eyes for "good sun")...
If it not too difficult, disconnecting the 4 panels (or open fuses/breakers in combiner box)--Two quick measurements. One is Voc (voltage open circuit) typically 20-22 Volts (hot day, voltage a bit less). Not really sunlight sensitive (full or 1/2 sun, same voltage).
And the second test is to short circuit each panel and measure the current (your DMM set to 10 amp max scale, or using a DC current clamp DMM). The short circuit current is a pretty accurate measurement of solar energy (within 5% or better). If you have 4 panels, and quickly measure Isc--They should all read within 5% of each other (6 amps, 5.7, 5.9, 5.8 etc.)... Since you have 4 panels, hopefully all are good and read almost identical Isc (some clouds, you may see 3.1, 2.9, etc.. Amps). The big thing is all should be nearly the same current in this test.
At this point, hopefully your panels will output similar current (under full sun/no shade). Bad wiring, or other issues (solar panels do have "by-pass" diodes in the J-Box. And sometimes those diodes "go bad". Miswired panels (+/- reversed) can surge current through cells or diodes and fry them (possibly nearby lightning strikes damage panels, etc.).
Once all panels have the same/similar operating current--Then we can look at the rest of the system.
-BillNear San Francisco California: 3.5kWatt Grid Tied Solar power system+small backup genset -
Also, can you confirm your dealer/supplier for your solar equipment?
I contacted NAWS and they do not sell Renogy equipment. And he did not find your forum email address/name in their customer/web order systems.
https://www.solar-electric.com/info.htmlNorthern Arizona Wind & SunNorthern Arizona Wind & Sun - Electricity from the sun since 1979
3695 E Industrial Drive
Flagstaff, AZ 86004
Office: (800) 383-0195 or (928) 526-8017
Fax: (928) 527-0729Telephone hours: 7:00 AM to 5:00 PM AZ Time, Mon-Fri.
Warehouse hours (for order pickups): 8:00 AM to 4:00 PM AZ Time, Mon-Fri.
Office hours: 8:00 AM to 4:00 PM Arizona Time, Mon-Fri. Closed on most major (federal) holidays.
Sincerely,
-BillNear San Francisco California: 3.5kWatt Grid Tied Solar power system+small backup genset -
You don't mention what the battery state of charge is. The controller is only going to pass as much current as needed to maintain the charging voltage. Li batteries typically have their own controllers, too. You'll need to do some research to see what voltages are needed/expected for charging, and what the solar controller is putting out.
-
Thanks BB and Mike. As soon as the sun comes out again, I will perform those tests. But to answer your questions, there is no shade at all on any of the panels, I used a DC current clamp for current measurements, the SOC of the Lithiums when the panels were tested was 50%, the solar setup is new, all connections and cables are WindyNation pre-made MC4's, and no nearby lightning strikes or mis-wirings occurred.
Sorry, but I didn't know that this forum was for a solar store -- I assumed it was for general solar questions! -
The forum is for anyone and everyone.
It just happened to be founded by one of the (now retired) owners of NAWS (family business) as an open forum. And NAWS pays for hosting fees and software maintenance.
Other than wanting a forum for all (whomever is interested, wherever purchased, etc.)--We pretty much run ourselves based on the conversations and needs of the members.
It was my misunderstanding of your first post... I thought you were (possibly) a customer of NAWS (...your Renogy solar system...)--And I was trying to get you help from the store.
I am very sorry. Anyway--Let's continue on.
-BillNear San Francisco California: 3.5kWatt Grid Tied Solar power system+small backup genset -
What are voltage and amps into the charge controller and voltage out of the charge controller? You said 2.7 a out of the CC, but at what voltage? I think I would test each panel by disconnecting them all and using just one at a time and see what the measurements are. Any chance you have the pos and neg switched at the combiner on one or more panels?
-
This is a PWM controller--So all the string currents "in" from array should equal current "out" to the battery bank/DC loads.
I wanted to focus on the current from each of the 4x parallel solar panels first... With identical panels under identical sun, then the current from each panel should be pretty much the same. Something does not sound right on the "upstream" side of the system.
Once that has been addressed, then we can look at the charge controller (voltage set point, actual measured voltage and current on the battery bus, etc.)... It is true, that you will only get current out of the array if the charge controller determines the battery bank & DC loads need current. If the bank is full and there are no loads (as determined by the charge controller), then there would be near zero current flow from the solar array.
-BillNear San Francisco California: 3.5kWatt Grid Tied Solar power system+small backup genset -
Thanks for all the help, guys! I followed the testing procedures as laid out by BB, JTDiesel, and Mike_S, and discovered that the solar output current didn't change whether there was a single panel connected or all four connected to the solar controller (about 3A, with all panels and controller output averaging about 22V open circuit). This led me to believe that the RV's solar wiring may be -- for some unknown reason (but knowing RV manufacturer's sloppiness) -- being sent into some input in the RV's 120V-12V converter; so I attached the solar controller's output directly into the Li battery bank and voila; I was now able to get 17A on this hazy day.
Anyone ever heard of this problem before?
-
A while ago, as I remember, somebody had a pre-wired RV solar trailer setup (or something). Turned out that the wiring was kind of non-standard and he had to trace wiring/replace wiring/connectors to get system installed and working correctly.
I don't know of an RV unit... But there are some "all in one" boxes that do solar-inverter-charger systems (connect solar panels + 120 VAC + genset + Batteries + 120 VAC output all in one box). Would need to know what brand/model to understand what the RV mfg. may have been thinking.
If you now have a direct panels to battery wiring/current path... You should be ready to install the solar charge controller. Ideally relatively close to the battery bank (to keep voltage drop down) and a fuse/breaker on/near the battery for the wiring that goes back to Vbatt charge controller input (if there is a short circuit, the Li Battery can output a crazy amount of current into a dead short--Need fuse/breaker to stop the excessive current flow from melting your wiring and starting a fire).
Secondarly, Li Ion batteries need a charge controller (and usually a battery management system) to prevent over and under voltage at the Lithium bank (Li batteries do not like too high or too low of voltage, and many have a BMS with over current limit/shutdown too).
-BillNear San Francisco California: 3.5kWatt Grid Tied Solar power system+small backup genset -
Oops... I missed that was solar charge controller connected to battery back, not the solar panels themselves.-BillNear San Francisco California: 3.5kWatt Grid Tied Solar power system+small backup genset
-
Very good points, Bill! As soon as I can I will install the solar controller directly inside the battery box, with access to the outside world with a bulkhead SAE receptacle. This should be very helpful in lowering I2R losses.
(Also, I have an MC4 30A fuse before the controller, and a 30A fuse block after the controller.) -
Some of the Renogy '12v' mono panels only have 30 or 32 series connected cells. Should avoid panels less then 36 series connected cells.
They are okay for PWM controllers but don't have enough overhead voltage for MPPT controllers on 12v battery.
Check what you have in number of series cells per panel. With 30 series cells (Vmp about 14.5v to 15v with sun heating) and some cabling voltage drop you may be getting too close to Voc on panels causing their current to drop off.
Also check panels individually. If Voc do not match you will get loss when paralleled. You can short out panel and measure Isc, for given illumination level, with clip on amp meter. A 10A port on DVM can also measure Isc.
If voltage is different but Isc is similar you can series connect panels and use MPPT controller although for RV mounted panels you may have issue with getting equal illumination on all panels. Series connected panels only produce current of weakest current panel. -
Excellent points, RCinFLA. I have heard of the "dead short the panel's output leads" to test Isc, but is that safe for the panels during a clear high noon? If so, for how long is it safe?
Earlier I tested the open circuit voltage of each panel, and they were a little over 20V. Is that abnormally high?
Each 50W panel of the 100W suitcase has 36 German made solar cells. -
Dead short of a single panel (or series string of panels) is fine. They are rated for full time Imp (current maximum power rating)--And Isc is roughly 1.25x Imp.
I would not short them for days/weeks at a time... They should be fine--But it does generate extra heat in the panel/cells--Which ages the cells/panels a bit faster. Overall, solar panels are in full sun and run hot anyway--Especially if there is no wind on a hot day.
Your 20 volts for a 36 cell panel is fine. Here are some typical specifications for a 100 Watt panel:
https://www.solar-electric.com/solarland-slp100-12m-100-watt-12-volt-solar-panel.html- Maximum power (Pmax): 100 Watts
- Nominal voltage: 12 Volts DC
- Voltage at Pmax (Vmp): 18.5 Volts DC (range from 17.5 to 18.5 volts is typical)
- Current at Pmax (Imp): 5.4 Amps DC
- Open-circuit voltage (Voc): 22.4 Volts DC
- Short-circuit current (Isc): 5.94 Amps DC
- Power tolerance: +/- 5%
- Dimensions: 51.18" x 20.79" x 1.97"
- Weight: 19.62 pounds
What can kill panels immediately--Instead of connecting + of panel to + of battery bank (and - to -) to charge the battery--Connecting the panels backwards (+ panel to - battery, - panel to + battery)--The panels are basically giant diodes (each cell is a diode)--And connecting backwards will dump a bunch of current through the reverse connected cells and fry them. Any fuses/circuit breakers will (usually) not be fast enough to save a reverse connected panel.
-BillNear San Francisco California: 3.5kWatt Grid Tied Solar power system+small backup genset -
Bill, I did connect the output of the solar controller to the batteries with reverse polarity (the battery clamps of the SAE connector cable where reversed in color; black should have been red, and visa-versa) -- would that have damaged the panels?
Also, I noticed that the solar controller now shuts down for a few minutes (with zero output current) every hour, and then restarts. Is this normal? (Just in case, I have bought a much better solar controller than the $32 Renogy Wanderer; the $132 Valterra GP-PWM-30-UL Solar Controller.) -
Cotter,
It is hard to say... Some charge controllers are polarity protected and some are not. Hopefully the panels are fine and, at worst, it is the charge controller that could have been damaged.
No--A solar charge controller does not shutdown for a few minutes at at time under normal situations. Take a look at the Battery Bus voltage (and battery terminal voltage at the controller itself)... It is possible that with longer wire runs/bad connections/etc. that the controller ends up thinking the battery is full (because of high voltage drop from controller to battery bus), then after a bit decides the batteries need charging again.
But I really have no insight to what is happening. And reverse polarity sometimes causes hidden damage that shows up later as "early life failure".
-BillNear San Francisco California: 3.5kWatt Grid Tied Solar power system+small backup genset -
On a cheap PWM controller reversing battery connections might damage it. You can also get pass through to panels when polarity reversed because the series MOSFET switch body diode will conduct putting the reverse voltage on panels.
If you did damage on panels it would be with the bypass diodes in the junction box, not the PV cells. Usually you can open the junction box and check the bypass diodes with a DVM ohm/diode checker. There is one bypass diode for each up and back column pair, so for a six column by 6 row cell panel there would be three bypass diodes, or two bypass diodes for a 4 column by 9 row panel. These are fairly easy to replace.
PV cells are illumination based current source clamped by their inherent diode. If left open circuit all the illumination current just shunts down the inherent cell diode. This gives the Voc voltage of about 0.6 to 0.7 volt per cell, or 21.6 - 25v for 36 series connected cells.
Maximum power point is allowing maximum panel voltage rise to the point where just a slight amount of illumination current leaks back down the cells inherent diode. This yields the maximum V x I product. This is about 0.5v per cell or 18v for 36 series connected cells.
Isc is done at low clamped panel voltage so it represent the illumination current produced. In full sun 1000 w/m^2 a good cell produces about 45 mA per square cm. or 8.7 amps for a full 155 x 155 mm cell wafer.
Silicon diode has negative temp coefficient of -2.1 mV per degree C for each cells. so as temp of panel rises with sun heating, its output voltage is reduced. Since you have the multiply the -2.1 mV/ degC per cell times number of series cells, most panel specs % change per degC.
Poly cells are not perfect diode so their temp coefficient varys from near zero to idea diode of -2.1 mv/deg C. Generally, the more 'wood chippy' the surface looks the worse the cell quality. Newer poly panels have improved a lot and you almost cannot see the difference in panel surface from mono, maybe a little more blue-ish tint.
Categories
- All Categories
- 229 Forum & Website
- 137 Solar Forum News and Announcements
- 1.4K Solar News, Reviews, & Product Announcements
- 199 Solar Information links & sources, event announcements
- 898 Solar Product Reviews & Opinions
- 256 Solar Skeptics, Hype, & Scams Corner
- 22.5K Solar Electric Power, Wind Power & Balance of System
- 3.5K General Solar Power Topics
- 6.7K Solar Beginners Corner
- 1K PV Installers Forum - NEC, Wiring, Installation
- 2.1K Advanced Solar Electric Technical Forum
- 5.6K Off Grid Solar & Battery Systems
- 428 Caravan, Recreational Vehicle, and Marine Power Systems
- 1.1K Grid Tie and Grid Interactive Systems
- 654 Solar Water Pumping
- 816 Wind Power Generation
- 624 Energy Use & Conservation
- 619 Discussion Forums/Café
- 312 In the Weeds--Member's Choice
- 75 Construction
- 124 New Battery Technologies
- 108 Old Battery Tech Discussions
- 3.8K Solar News - Automatic Feed
- 3.8K Solar Energy News RSS Feed