Newbie looking for a simple solution
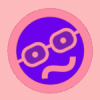
photoman
Registered Users Posts: 9 ✭✭
My wife brought home a 24volt lithium battery that she wants to use for lights in our shed and greenhouse. What would be the cheapest solar panel and controller I could use, and what would be the best way to convert down to 12 volts for the lights. Thank you!
Comments
-
Can you tell us a bit more about your specific lithium battery (AH capacity, any battery management system) and where (nearest major city) the system will be used?
How much energy per day you would like to use per day (Amp*Hour # xx volts, Watt*Hours, etc. per day)?
There are a fair number of 24 VDC work lamps/RV bulbs/etc. out there... If you are just looking for lighting--I would try a few 24 volt lamps and see how they work for you... Saves the costs and energy loses for a DC to DC down converter:
https://www.amazon.com/s?k=24+vdc+led+work+lights&ref=nb_sb_noss
https://www.amazon.com/s?k=dc+to+dc+buck+converter
The big issue with Li Ion batteries is their cells are very sensitive to over/under voltage conditions. If you run the cells out of spec, you can ruin them pretty quickly. A battery management system can help turn off the battery if the operating conditions are violated.
Also, Li Ion rechargable batteries typically should not be recharged below ~40F (or below freezing)--If you are in a cold weather area, keeping the battery "warm" (or having a BMS turn the battery off when temperatures fall) is necessary.
-BillNear San Francisco California: 3.5kWatt Grid Tied Solar power system+small backup genset -
My wife got the 24v battery from a hospital cart. It already has a bms, but i need to dig into it further. The battery is 10 AH, and that's all we have, so I assume I'll need a 24v solar panel and can get by with a cheapy charge controller. Your idea about 24 volt lights sounds great (I didn't know they existed). I am in Ohio, and could bring the battery in during the winter if needed.
-
OK, the min/max daily (or over night) discharge I would suggest:
- 10 AH * 1/2 days storage * 0.50 max discharge = 2.5 AH @ 12 volts (2 days of storage, and less than "full discharge" of battery)
- 10 AH * 1/1 days storage * 0.70 max discharge (90% to 20% typical) = 7.0 AH @ 12 volts max possible daily (1 day) discharge
http://www.solarelectricityhandbook.com/solar-irradiance.htmlColumbus
Measured in kWh/m2/day onto a solar panel set at a 50° angle from vertical:
Average Solar Insolation figures
(For best year-round performance)
Using October average sun of 4.16 hours per day (long term average) based on min/max battery usage:Jan Feb Mar Apr May Jun 2.81
3.43
3.86
4.54
4.77
4.98
Jul Aug Sep Oct Nov Dec 5.18
4.99
4.84
4.16
2.78
2.38
- 2.5 AH per day * 35 volts Vmp array * 1/4.16 hours of sun per day = 21 Watt panel/array "October Break even" minimum discharge
- 7.0 AH per day * 35 volts Vmp array * 1/4.16 hours of sun per day = 59 Watt panel/array "October Break even" max discharge
- 21 Watt array * 2 = 42 Watt array minimum battery discharge every day
- 59 Watt array * 2 = 118 Watt array maximum battery discharge every day
- 42 Watt array / 2 panels = 2x 21 Watt @ 17.5 volt Vmp panels in series
- 118 Watt array / 2 panels = 2x 59 Watt @ 17.5 volt Vmp panels in series
- 42 Watts / 35 volts Vmp * 1.25 NEC deratring = 1.5 Amp PWM controller minimum
- 118 Watts * 1/35 volts Vmp * 1.25 NEC deratring = 4.2 Amp PWM controller minimum
Note: LiFePO4 batteries require ZERO temperature compensation (Lead Acid batteries require slightly higher voltages when charging in cold conditions, and lower voltages when hot).
Looking at the above supported discharge--You need to find LED bulbs that will not draw more power than you want. For example, say 5 hours of light per night:- 2.5 AH of stored current * 1/5 hours of use = 0.5 amp "average" current
- 0.5 Amp average current * 24 volts = 12 Watts of average power (12 Watts for one bulb or 1 Watt for 12 bulbs, etc.)
- 7.0 AH of stored current * 1/5 hours of use = 1.4 amps "average" current
- 1.4 amps * 24 volts = 34 Watts of average power (for 5 hours).
-BillNear San Francisco California: 3.5kWatt Grid Tied Solar power system+small backup genset -
I think so. You suggest mounting two 17.5 panels in series to feed the charge controller 35 volts. The PWM charge controller will then convert that to the proper voltage to charge the battery, which should be listed somewhere on the battery itself? I assume around 26 volts?Being a used battery, I will be looking for videos that describe whatever balancing is necessary.Then out from the battery to a fuse block for the light circuits I assume.Thank you for the temperature compensation tip about LiFePO4, and your detailed response. Your math on sizing the charge controller and the lighting load is very valuable to me. This is our first try (my wife is as excited as I am) at anything solar, and we are very interested. We plan on adding solar power to a van, so this is a good way to get some experience.
-
Many smaller Li Ion battery batteries are pretty much "sealed" and you really do not have access to each cell. You rely on the BMS to take care of everything inside the battery. Generally, you run LiFePO4 batteries from 20% to 90% state of charge for best life. And store around 50% full (for longest life when stored). So having the correct voltages (charging, low voltage cutoff) is critical with Lithium batteries. They are not very forgiving of being taken over or under rated operational voltage (generally ruins the batterieds pretty quickly--And with other Lithium chemistries, can cause smoke or fire).
For cabling--Using 14 AWG ROMEX or other house wiring with 10 amp fuse/breaker to/from battery should be fine for your installation (all your currents are under the 15 amps * 0.80 NEC derating = ) 12 amp suggested max current for 14 AWG copper wiring.
And just a semantic note... Technically, the battery in a solar power system regulates the battery bus voltage. The typical PCM (and MPPT) solar charge controller does not "regulate" battery bus voltage. It just measures the battery bus voltage, estimates the state of charge, and regulates the solar array current (power) to the battery bus.
When the battery needs charging (well discharged), the PWM controller (pulse width modulation) is 100% "ON"... Max current from array to battery bus. As the battery bus approaches the charging set point voltage, the PWM controller switch on/off quickly... From 100% to 50% on to near 0% on when the battery is full. Once the battery is full, the PWM controller will fall back to "float voltage" setting (a few volts below absorb set point) to support loads on the battery bank while the sun is still up.
Also, Lead Acid and other battery types typically want the "absorb voltage" held for something like 2-6 hours of so, until the battery bank is "fully charged".e
Lithium Ion batteries, typically the charge controller stops charging when the set point voltage is reached--And falls back to float (if charger has a "float stage") and will not start charging again until the battery has been discharged some amount.
Lead Acid batteries are "equalized" by EQ charging--Basically controlled over charging. The "full cells" are over charged so that the weak cells can be brought to full charge by the "leakage current" through the "full" cells.
Lithium Ion batteries cells cannot be over charged and pass the leakage current to the weak/lower charged cells. They will fail if over voltage charged--
"Balancing" Li Ion cells is using a BMS which will pass (typically around 2 amp max for a mid-size BMS) current "round" the full cells, to bring up the lower State of Charge (SoC) cells. You supply the "correct" charging voltage, and the BMS takes care of the rest.
Manual balancing is you placing a 3.7 volt (or whatever voltage you need to use) charger on each cell (or paralleled groups of cells) for hours (or longer) to get exactly 3.700 volts on each cell (parallel group of cells)---Or you can use a load (resistor/light bulb/etc.) to discharge the "high cells" to the same voltage as the rest of the bank.
Lead Acid batteries--There is a normal drift/self discharge/etc. of cells to out of balance conditions. AGM cells tend not to drift near as much (and "over voltage" EQ generally not done on AGM because it can damage the cells). Li Ion cells generally stay in balance very well (when everything is "good"). You want all Li Ion cells to be at/near identical state of charge so that they all are full/empty at the same time. You don't want one low cell to fall to zero SoC while the others atre at 20% SoC.. Or one high cell to go over 100% SoC while the rest are at 90% SoC...
If your bank needs manual intervention--You need to read about Li Ion cell care of feeding. There are lots of details to take into account.
Others here (like McGivor and others) know much more about Li Ion (and have more experience) than I.
Lithium batteries--LiFePO4 (lithium iron phosphate) and similar chemistries are relatively safe. Other "higher performance" types can easily be set on fire with poor charging/discharging control. And you do not want an Lithium battery fire. They can vent hydrofluoric acid--This stuff is horrendously poisonous. Breathing it or getting it on your skin will cause serious health effects and/or death. And it cannot be neutralized/cleaned up--Cleanup is gutting the building/contaminated materials and taking to a hazardous waste dump.
I highlight the fire hazards of Li Ion cells--The chances of fire is low for a well designed and operated system... But placing the battery/bank in a place other than your bedroom is a good idea. The details really matter here. Am I overstating the risks--I really cannot say (I don't have the detailed knowledge/experience). But don't treat any large battery bank or Li Ion bank with a cavalier attitude... It can bite you.
-Bill
PS: Look up anything you can find on the outside of the battery (brand/model number/ratings/part number) and try to find a manual for that battery. With Lithium Ion, you have to be pretty exact with charging voltages/current/temperatures/etc. or you will have a relatively short battery life.Near San Francisco California: 3.5kWatt Grid Tied Solar power system+small backup genset -
Here is a random example of an integrated LiFePO4 battery and BMS (specs, manuals, etc.):
https://lithiumhub.com/product/24-volt-10ah-battery/
Their maximum charging voltage of 29.2±0.1V is a very tight spec. But their recommended voltage range is 24.4 to 25.2 volts--Not as tight. And under the 80% charged voltage of 26.56 volts
And watch the manuals... Many are translated from Chinese/Japanese/Korean (or other languages) and can contain errors such as recommended charge current of 5:00AM (yes, 5:00 in the morning, not 5 amps):
https://lithiumhub.com/wp-content/uploads/2019/06/24V-10Ah-specs-front.pdf
And a nice manual/marketing doc:
https://lithiumhub.com/wp-content/uploads/2019/02/ownersmanual.lowrez.updated.pdf
-BillNear San Francisco California: 3.5kWatt Grid Tied Solar power system+small backup genset -
photoman said:My wife got the 24v battery from a hospital cart. It already has a bms, but i need to dig into it further. The battery is 10 AH, and that's all we have, so I assume I'll need a 24v solar panel and can get by with a cheapy charge controller. Your idea about 24 volt lights sounds great (I didn't know they existed). I am in Ohio, and could bring the battery in during the winter if needed.
Many of the cheap controllers will in the absence of a float cycle maintain a voltage, 28.8V in the case of 24V nominal, with reduced current controlled by pulse width modulation PWM, small rapid pulses at varying frequency. To extend the life of LiFePo4 it's better to have a maximum bulk voltage of around 27.6V, or about 90% SOC.
Spend a little more to get a quality product, particularly if the plan is to build another larger system at a later date, Morningstar Sunsaver, Prostar, TS and TS MPPT are MSVIEW compatible, the latter being larger capacity. There are other manufacturers Victron, Midnight Outback which may be excellent choices though I've no first hand experience with them, Morningstar by the way has excellent support, which is second to none.
1500W, 6× Schutten 250W Poly panels , Schneider MPPT 60 150 CC, Schneider SW 2524 inverter, 400Ah LFP 24V nominal battery with Battery Bodyguard BMS
Second system 1890W 3 × 300W No name brand poly, 3×330 Sunsolar Poly panels, Morningstar TS 60 PWM controller, no name 2000W inverter 400Ah LFP 24V nominal battery with Daly BMS, used for water pumping and day time air conditioning.
5Kw Yanmar clone single cylinder air cooled diesel generator for rare emergency charging and welding. -
Ok. I'll get a programmable PWM. I can see other uses for a smaller system in the future, so having the flexibility to use this one if necessary is a good idea. I will start looking for some 24v lighting as well, to avoid the loss between a 24v to 12v converter. Thanks everyone for your experience and advice!
-
I found a 60 watt 24v mono panel on amazon for 78 dollars. Morningstar Sunsaver 10A controller for 65 dollars. The battery says its 25.6Volts, 9.6Ah, 245.8Whr. I'm still currently looking for 24v bulbs, but does this sound like a good match?
-
You need to find a Vmp ~= 35-49 VDC.Many "24 volt" panels have Vmp~30 VDC. That is too low of voltage. Vmp falls by almost 20% on hot days under full sun. Need the higher voltage to quickly and fully charge your 24 volt battery.BillNear San Francisco California: 3.5kWatt Grid Tied Solar power system+small backup genset
-
I have one more stupid question. My battery says the max charge is less that 4.8 amps. I assume a non-programmable 10A charge controller always puts out 10A in ideal conditions, so I couldn't use one, but a 10amp programmable controller could be set to 4.8 amps exactly. My choices are either a non-programmable 4A 24V PWM controller (if there is such a thing) or a programmable controller of higher amperage. Is this correct?
-
Li Ion rechargeable batteries have very low internal resistance (both physical resistance and "chemical" limits to current). So, unless you have other proof--Assume that a Li Ion battery will take 100% of the available charging current from the charger (in practice, you are not going to push 1,000 amps into a 10 AH battery).
When you talk about "programmable" charging current... There are some very nice AC chargers that have programmable output--But you do have to look for them.
For solar chargers... There are the MPPT type which can have programmable output current limits (and they "natively" should limit charging current to "specified" output current (i.e., 40 Amps max, no matter the state of the battery the size of the solar array/amount of sun). In fact, with MPPT type solar charge controllers, it pretty common practice to "over panel" a controller to allow for low sun days, etc...
PWM solar charge controllers are "different". They are (for the most part) simply On/Off switches (transistors). They do not have a programmable ability to limit their output current. Full sun/large solar array/etc. and the controller may output more current than you want into the battery bank...
Now--For PWM controllers. Say you have a Vmp!35 volt panel and want 4.8 amps max into the battery pack... The math on that is:- 35 Volts Vmp * 4.8 amps (Imp) = 168 Watt panel/array maximum
- Assuming a 1.25 Safety Factor: 168 Watts (Pmp) / 1.25 = 134 Watt array max suggested
Midnite (for example) has an option that measures the current directly into the battery bank... And if you limit the battery current to 30 Amps--The controller will limit to 30 Amps into the battery (and any extra current can go to the loads).
For your small/charge by day/use by night system... The Midnite controller is way overkill for your needs.
And no "stupid questions" here... Details matter with solar (and engineering design specifically)--Needs, specific hardware, programming, location, etc. all can affect your design and choices. Batteries store a lot of energy and can output a lot of current (Li Ion batteries, even more so)--And making some bad assumptions/ignoring the details--Can let out the "magic smoke" or even start a fire.
-BillNear San Francisco California: 3.5kWatt Grid Tied Solar power system+small backup genset -
It's starting to click. As long as my panels can't produce more than 4.8 Amps, I could use a 10 Amp controller as long as the voltage output from the controller matches the battery. I assume it's the BMS that will "shut off" the current from the controller when the battery is fully charged?
-
Be careful with the BMS assumption... Some will shut the battery off (over voltage, under voltage, over current, etc.)... Some will communicate with your controller(s)/inverters/etc. and send them the data to gracefully react to the issue(s). Some may not... Yours probably does shut down the battery if something goes off the rails.
You really don't want the BMS to "throw the kill switch" as a daily/weekly event if you can avoid it... You/your equipment should run in the lane, and the BMS be the curb/guard rails (keeps things safe, may need manual intervention to get back on the road). As long as the charging set point is below the BMS max--Everything should run well.
If you are going to use LED 24 Volt lights... Quite a few solar charge controllers come with a Low Voltage Disconnect (LVD). For smaller (current) loads (not for running big AC inverters), they can be set for 10.5 volts or adjustable to what you need... Turns off the "lights", but leaves everything "live" for recharging when the sun comes up.
-BillNear San Francisco California: 3.5kWatt Grid Tied Solar power system+small backup genset -
Can I connect a fuse block to the "Load" terminals of the charge controller to run 3 circuits of lights, or would you suggest connecting the fuse block directly to the battery? Is there an advantage using one or the other?
-
Connect "heavy loads" to the battery bus directly (generally, the LVDs are rated something like 8 amps up to the "controller's" max charging rating--It depends)...
You are looking at 0.5 to 1.4 amps or so (based on my calculations above for "average" optimum discharge current)... That is very low and can easily be done with an LVD on "many" controllers (again, details matter).
You have a choice of running a single fuse between the LVD and the loads, or running a fuse/breaker to each "load branch circuit" (i.e., you have several strings of lights in different locations).
Fuses/breakers are there to protect the wiring... If you use "relatively heavy" wiring (like 14 AWG house wiring), a single 12-15 amp fuse and running all the lights from that one fuse would be fine.
If you had (for example) three strings running 0.1 amps each and used 18 AWG wire--Then you would want to choose a fuse to protect the smaller wires.
For example, here is a chart with smaller AWG wiring and fuses suggested... Note that the NEC rates 14 AWG as 15 Amps max for most types of installations... But can go up to 25 amps with high temp insulation... The chart below starts with 14 AWG = 25 amps--I would take the chart and use max fuse/rating to be 1/2 of what the chart suggests (to be very conservative):
https://www.engineeringtoolbox.com/wire-gauges-d_419.html
For large loads or loads and/or high starting surge (such as AC inverters, electric motors, etc.)--These currents usually exceed the LVD circuit's max current--And can smoke the LVD/Charger's circuits.
For your system--I would use a controller with LVD... That way the controller shuts down lightning at the voltage limit you set--And do not trigger the BMS LVD.
You can even (if needed) have two circuits... "Bulk lighting" on the LVD, and a couple "emergency/night lights" on the battery bus--So an LVD cutoff does not leave you in complete darkness. (I carry a flashlight or two with me pretty much all the time as my "spare" lighting).
Lithium Ion (and even Lead Acid) batteries an supply a surprising amount of current into a dead short... Every "wire" that leaves the + bus should have a fuse to protect it...
For example, say you are charging (and loads) are 5 amps or less. And you use 14 AWG wire... I would use 10-12-15 amps for a single fuse from the battery bank (one fuse to + Bus). And if you use 14 AWG wiring "everywhere", that one fuse should be fine.
Or, you can run a 10 amp fuse from the bus to the charge controller. And three 1/2 amp (or whatever) fuses, one to each lighting circuit.
The idea is to protect all downstream wiring the the appropriate fuses/breakers. I am making this sound a bit paranoid--And engineers do "overkill" a lot--Because we cannot predict every installer's setup/failure that happens in the field.
And--There is another calculation that you should do to figure out wire AWG... Basically the length of run, the current, and aceptable voltage drop... A greenhouse can be pretty large. Sending low voltage current at 12 or 24 VDC--Voltage drop can be a pretty significant issue.
Just to give you an idea. Say 1.4 amps, 50 feet one way wire run (for this website), and 1.0 volt maximum drop on a 24 VDC bus:
https://www.calculator.net/voltage-drop-calculator.html?material=copper&wiresize=8.286&voltage=24&phase=dc&noofconductor=1&distance=50&distanceunit=feet&eres=1.4&x=0&y=0Result
Voltage drop: 0.35
The neat thing about using LEDs (and any other "low power/low current" efficient loads), you can send the low voltage DC longer voltages without too much voltage drop. Here, even at 50 feet, 14 AWG wire only gives 0.35 volt drop @ 24 VDC.
Voltage drop percentage: 1.47%
Voltage at the end: 23.65
Now--You can continue to use 14 AWG as a base for your design, or go with smaller wire (or longer wire runs)--Whatever works best for you... If you choose smaller AWG wiring, then reviewing fuse/breaker choices for the thinner wire needs addressing.
And another issue... The charge controller to battery bank wiring needs to be short and heavy (relatively speaking). Keep controller "near" the battery bank, and run the longer leads from solar array to charger panel input. Ideally, I would suggest the voltage drop from the charge controller to the battery bank be a maximum of 0.1 to 0.2 volts (24 volt bus). For accurate battery sensing voltage and optimum charging control.
-BillNear San Francisco California: 3.5kWatt Grid Tied Solar power system+small backup genset -
So much great advice!! I'm going to shop for panels, a controller, lighting, and wiring today, and can't wait to get started. Thank you!
Categories
- All Categories
- 229 Forum & Website
- 137 Solar Forum News and Announcements
- 1.4K Solar News, Reviews, & Product Announcements
- 199 Solar Information links & sources, event announcements
- 898 Solar Product Reviews & Opinions
- 256 Solar Skeptics, Hype, & Scams Corner
- 22.5K Solar Electric Power, Wind Power & Balance of System
- 3.5K General Solar Power Topics
- 6.7K Solar Beginners Corner
- 1K PV Installers Forum - NEC, Wiring, Installation
- 2.1K Advanced Solar Electric Technical Forum
- 5.6K Off Grid Solar & Battery Systems
- 428 Caravan, Recreational Vehicle, and Marine Power Systems
- 1.1K Grid Tie and Grid Interactive Systems
- 654 Solar Water Pumping
- 816 Wind Power Generation
- 624 Energy Use & Conservation
- 619 Discussion Forums/Café
- 312 In the Weeds--Member's Choice
- 75 Construction
- 124 New Battery Technologies
- 108 Old Battery Tech Discussions
- 3.8K Solar News - Automatic Feed
- 3.8K Solar Energy News RSS Feed