Battery Capacity
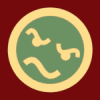
My name is Steve, I'm from Montreal, Quebec and new to the forum.
Here is my setup:
CS60-260P 260 watt solar panel
EPSOLAR Tracer-4210RN 40A MPPT Solar charge controller
Remote meter MT-5
4x 12 volts sealed battery SBS190F
I have a solar fridge Solstice 308 which draw 30 to 42 watt an hour. When I check with my amp meter it draw 3.5 amp (42 watt).
My 4 12 volts 190 amp hour battery connected in parallel give me a battery bank of 760 amp in 12 volts.
When I turn on the fridge say at noon, when the battery is at 100% (14.0 volts). When I wake up at 7:00 am the day after, the remote meter MT-5 indicate 47% SoC.
Battery at 12.4 volts.
So I am wondering why it is saying 47% when my battery bank is 760 amps. And my fridge draw 3.5 amp for 17 hours (59.5 amp total out of my 760).
Sorry if my english is not very good, I try my best!
Thank you
Steve
Comments
-
Welcome to the forum Steve...
You will have to pardon my English (it is the only language I know.).
Anyway... What kind of batteries do you have (12 volt bank?)? Flooded Cell, AGM, or other?
14.0 volts as a charging set point is a bit on the low side for many Lead Acid Batteries. Flooded Cell Lead Acid batteries generally have a set point of 14.75 volts or so for charging (and the charger should hold that voltage for ~2-6 hours... The deeper the discharge, the longer the Absorb time). Bulk is charging the battery from below 14.x volts to 14.75 volts. Absorb is holding at 14.75 volts for X hours. And Float is holding at ~13.3-13.6 volts (keep battery charged, support other DC loads, not over charge the battery).
For AGM batteries, typically the charging set point is round 14.4 volts.
Lead Acid batteries are difficult to measure state of charge with just battery voltage... The battery should "rest" (no charge/discharge) for around 3 hours, and (depending on brand/model), the resting voltage at ~75F/25C will give you the state of charge:
https://www.solar-electric.com/learning-center/deep-cycle-battery-faq.html/#Gelled%20ElectrolyteHere is a nice article with charts for battery voltage vs state of charge under different conditions:State of Charge
Here are no-load typical voltages vs state of charge
(figured at 10.5 volts = fully discharged, and 77 degrees F). Voltages are for a 12 volt battery system. For 24 volt systems multiply by 2, for 48 volt system, multiply by 4. VPC is the volts per individual cell - if you measure more than a .2 volt difference between each cell, you need to equalize, or your batteries are going bad, or they may be sulfated. These voltages are for batteries that have been at rest for 3 hours or more. Batteries that are being charged will be higher - the voltages while under charge will not tell you anything, you have to let the battery sit for a while. For longest life, batteries should stay in the green zone. Occasional dips into the yellow are not harmful, but continual discharges to those levels will shorten battery life considerably. It is important to realize that voltage measurements are only approximate. The best determination is to measure the specific gravity, but in many batteries this is difficult or impossible. Note the large voltage drop in the last 10%.
State of Charge 12 Volt battery Volts per Cell 100% 12.7 2.12 90% 12.5 2.08 80% 12.42 2.07 70% 12.32 2.05 60% 12.20 2.03 50% 12.06 2.01 40% 11.9 1.98 30% 11.75 1.96 20% 11.58 1.93 10% 11.31 1.89 0 10.5 1.75 Why 10.5 Volts?
Throughout this FAQ, we have stated that a battery is considered dead at 10.5 volts. The answer is related to the internal chemistry of batteries - at around 10.5 volts, the specific gravity of the acid in the battery gets so low that there is very little left that can do. In a dead battery, the specific gravity can fall below 1.1. Some actual testing was done recently on a battery by one of our solar forum posters, and these are his results:
I just tested a 225 ahr deep cycle battery that is in good working order..
I put a load on it 30a for 4 hrs it dropped its voltage to 11.2
I then let it cool down for 2 hrs
then put the load back on again in 1hr 42 mins it dropped to 10.3v
35 mins under 30a load 9.1v (273w)
10 mins later max output current 11.6a 8.5v (98.6w)
5 mins later max output current 5.2 amps 7.9v (41w)
3 mins later 7.6v and 2.3a (17.5w)
This shows after it gets below 10.3 v you only have 35 mins of anything useful available from the battery.
battery is now dead and most likely will not fully recoverBattery Charging
Battery charging takes place in 3 basic stages: Bulk, Absorption, and Float.
Bulk Charge - The first stage of 3-stage battery charging. Current is sent to batteries at the maximum safe rate they will accept until voltage rises to near (80-90%) full charge level. Voltages at this stage typically range from 10.5 volts to 15 volts. There is no "correct" voltage for bulk charging, but there may be limits on the maximum current that the battery and/or wiring can take.
Absorption Charge: The 2nd stage of 3-stage battery charging. Voltage remains constant and current gradually tapers off as internal resistance increases during charging. It is during this stage that the charger puts out maximum voltage. Voltages at this stage are typically around 14.2 to 15.5 volts. (The internal resistance gradually goes up because there is less and less to be converted back to normal full charge).
Float Charge: The 3rd stage of 3-stage battery charging. After batteries reach full charge, charging voltage is reduced to a lower level (typically 12.8 to 13.2) to reduce gassing and prolong battery life. This is often referred to as a maintenance or trickle charge, since it's main purpose is to keep an already charged battery from discharging. PWM, or "pulse width modulation" accomplishes the same thing. In PWM, the controller or charger senses tiny voltage drops in the battery and sends very short charging cycles (pulses) to the battery. This may occur several hundred times per minute. It is called "pulse width" because the width of the pulses may vary from a few microseconds to several seconds. Note that for long term float service, such as backup power systems that are seldom discharged, the float voltage should be around 13.02 to 13.20 volts.
Chargers: Most garage and consumer (automotive) type battery chargers are bulk charge only, and have little (if any) voltage regulation. They are fine for a quick boost to low batteries, but not to leave on for long periods. Among the regulated chargers, there are the voltage regulated ones, such as Iota Engineering, PowerMax, and others, which keep a constant regulated voltage on the batteries. If these are set to the correct voltages for your batteries, they will keep the batteries charged without damage. These are sometimes called "taper charge" - as if that is a selling point. What taper charge really means is that as the battery gets charged up, the voltage goes up, so the amps out of the charger goes down. They charge OK, but a charger rated at 20 amps may only be supplying 5 amps when the batteries are 80% charged. To get around this, Xantrex (and maybe others?) have come out with "smart", or multi-stage chargers. These use a variable voltage to keep the charging amps much more constant for faster charging.
http://www.rencobattery.com/resources/SOC_vs-Voltage.pdf
If you have a flooded cell battery, you can use a Hydrometer to better estimate state of charge:
https://batteryuniversity.com/learn/article/how_to_measure_state_of_chargeApproximate
state-of-chargeAverage
specific gravityOpen circuit voltage 2V 6V 8V 12V 100% 1.265 2.10 6.32 8.43 12.65 75% 1.225 2.08 6.22 8.30 12.45 50% 1.190 2.04 6.12 8.16 12.24 25% 1.155 2.01 6.03 8.04 12.06 0% 1.120 1.98 5.95 7.72 11.89 Table 2: BCI standard for SoC estimation of a starter battery with antimony.
Readings are taken at 26°C (78°F) after a 24h rest.And then there are other issues... For lead acid batteries that have been sitting around partially charged (typically less than 75% State of Charge) for days/weeks/months, the batteries will "sulfate" and permanently lose capacity.
Another thing that can affect operation is the size of the battery cables and how they batteries are wired in parallel. This site does a nice job on battery cabling:
http://www.smartgauge.co.uk/batt_con.html
If not wired correctly, the batteries will not properly share charging and discharging currents.
I am not a fan of placing lots of batteries in parallel. And instead, suggest that you look at (in this case) putting the 4 batteries into 2 series by 2 parallel battery strings. For 24 volts at 380 AH.
But that can have issues with your solar array (may need higher Vmp-array voltage for charging 24 volt bank). Many DC refrigerators will run on both 12 and 24 volts (but not all). And if you have other devices--That can be an issue too (12 volt loads, 12 volt AC inverter, etc.).
Your fridge?
https://rematek-energie.com/eng/Solar-refrigerator/12-24V/TSI-SOLSTICE-308/p/1695
- Low energy consumption. At 12 VDC: 2.5 to 3.5Ah, 30 to 50A a day. At 24 VDC: 1.25 to 1.75Ah, 15 to 25A a day.
- Danfoss DC compressor operates on 12 or 24 VDC
A 40 Amp 12 volt controller on a 760 AH battery bank, at best, can charge:
40 Amps max charge current / 760 AH battery bank = 0.053 = 5.3% rate of charge
A bit of quick math on how 42 Watts @ 24 hours per day vs the size of your solar array:
http://www.solarelectricityhandbook.com/solar-irradiance.htmlMontreal
Measured in kWh/m2/day onto a solar panel set at a 44° angle from vertical:
Average Solar Insolation figures
(For best year-round performance)
Let us call "summer season" at 4.0 hours of sun minimum:Jan Feb Mar Apr May Jun 2.59
3.60
4.37
4.65
4.68
4.89
Jul Aug Sep Oct Nov Dec 4.93
4.83
4.26
3.14
2.21
2.06
42 Watts * 24 hours per day = 1,008 WH per day
1,008 WH per day * 1/0.61 DC off grid System Eff * 1/4 hours per day "summer sun average" = 413 Watt array "break even"
Generally suggest that you have a larger solar array than "break even" (unless you use a genset during cloudy weather)... Almost 2x 413 Watt array would not be bad... And do you have other loads (lights, water pumping, laptop and cell phone charging, etc.)?
And how big of array can a 40 Amp MPPT type charge controller on a 12 volt battery bank manage:
40 amps * 14.5 volts charging * 1/0.77 panel+controller deratings = 753 Watt typical maximum array for 40 Amp @ 12 volt MPPT charge controller...
If you re-wired your battery bank for 24 volts, that same charge controller could manage a ~2x larger array very nicely (no need for new MPPT charge controller).
Anyway--I will stop here. Don't know for sure what the issue may be (if any) with your battery bank... A little reprogramming to a higher charging voltage, possibly add a couple panels to your existing array, possible rewiring the battery bank connections and that should help a lot. If the battery bank has been "used hard", a new battery bank may be needed (battery banks left "dead" can sulfate to unusable in a few weeks or a month).
-BillNear San Francisco California: 3.5kWatt Grid Tied Solar power system+small backup genset -
My battery are sealed lead acid.
They have been tested with a Megger for impedance and are in good quality.
Removing load and letting the battery rest for many hours for testing is not an option for me as it is on an island and we need power when we are there.
I'm just wondering if I can trust the remote meter MT-5 to know how much charge is left in my battery (like a fuel gauge). I don't think so and I'm wondering how could I get the info?
We already have a 12V to 120V inverter installed for a future tv in the cabin but we would like to know the health ("fuel left") in the battery with just the fridge after a night.
Without adding any battery and/or solar array, I guess switching from 12V to 24V wont help at all?
-
There are other options out there for metering your battery bank... But making sure the set points are programmed correctly is a start. Do you have a manual (or website) for the batteries you are using so you can start with the mfg's recommendations.
What size solar array do you have?
Is the array free of all shading (usually at least from 9am to 3pm or longer)? Any shading (one or two cells of partial shading) can cut the array output by 1/2 or even worse.
Do you know how long and what gauge the cable is from the charge controller to the battery bank? For a 12 volt battery bank, you want a maximum of 0.05 to 0.10 volts wiring drop at full charging current (so the charge controller gets accurate battery bank voltage).
Assuming the voltage reading for the remote meter is accurate--Following the voltage is a good place to start.
-Bill
Near San Francisco California: 3.5kWatt Grid Tied Solar power system+small backup genset -
Hi BB,
Thank you for you help and time.
The wire between CC and battery is #8 AWG.
Maybe 4-5 foot.
The wire between each battery for the connections in parallel is #4 AWG.
I think I made those 6 inch.
For the solar array, it probably get shade sometime during the day. But many hours full sun.
My CC is a EPSOLAR Tracer-4210RN.
Is it possible to change set points?
Battery SBS190F
https://www.google.com/url?sa=t&source=web&rct=j&url=https://www.enersys.com/WorkArea/DownloadAsset.aspx?id=25769807513&ved=2ahUKEwjqrpS6mY_rAhWhlHIEHbcQBckQFjAAegQIAxAB&usg=AOvVaw38HNXCmuUKCQ2ptBVkjFIH
https://www.google.com/url?sa=t&source=web&rct=j&url=https://www.osibatteries.com/images/document/US-SBS-IS-009_0315.pdf&ved=2ahUKEwjqrpS6mY_rAhWhlHIEHbcQBckQFjABegQIAhAB&usg=AOvVaw3yPs1VglR4V1eGab27LvVV
Solar array 260 watts
CS6P-260P
https://www.google.com/url?sa=t&source=web&rct=j&url=https://s3.us-east-2.amazonaws.com/legacy.portalsolar.com.br/Content/EditorImages/files/Placa%20Solar%20Canadian%20Solar%20-%20Modelo%20CS6P-265P%20-%20265Watts.pdf&ved=2ahUKEwiuxdyGmo_rAhWVYDUKHXD4CyMQFjABegQIBxAB&usg=AOvVaw19nUPbQGuqBRZayYTVGH-D
-
a single 260 w panel is really small to attempt to run a fridge from. 3 of them in parallel would be a good starting point, and running a 24V system to avoid massive parallel battery wiring would help too.
In your case, obtaining a totalizing amp meter ( fridge consumed 55ah, solar replaced 43ah ) is the better way to measure, if you need a "fullness" meter. With experience, you will eventually learn to read voltage under load, as a state of charge, but each configuration is different.
42 watts x 24 hours = 1008watt hours. This agrees with conventional energy star fridges which consume roughly 1kwh daily
So for only the fridge running, you need to replace that with about 10% more, about 1108.8 watt hours returned to the battery bank.
a single 260 w panel would be expected, under ideal conditions, to harvest no more than 80% of it's nameplate.
Now your 208w panel, needs 5.3 hours of full blown noon sun, which requires a solar tracker to maintain alignment for 5.3 hours
Can you see where this is going ? you don't have 5.3 noon equivalent hours in most places on the planet. Any overcast sky, clouds, haze, smoke, reduces your harvest spectacularly. Additionally, outside of solar noon, atmosphere reduces the available light, so you are going to need more panel.
Powerfab top of pole PV mount | Listeroid 6/1 w/st5 gen head | XW6048 inverter/chgr | Iota 48V/15A charger | Morningstar 60A MPPT | 48V, 800A NiFe Battery (in series)| 15, Evergreen 205w "12V" PV array on pole | Midnight ePanel | Grundfos 10 SO5-9 with 3 wire Franklin Electric motor (1/2hp 240V 1ph ) on a timer for 3 hr noontime run - Runs off PV ||
|| Midnight Classic 200 | 10, Evergreen 200w in a 160VOC array ||
|| VEC1093 12V Charger | Maha C401 aa/aaa Charger | SureSine | Sunsaver MPPT 15A
solar: http://tinyurl.com/LMR-Solar
gen: http://tinyurl.com/LMR-Lister , -
The batteries appear to be a GEL type battery designed for long term (10 year life) Float/Backup service. They do not appear to be designed for daily cycling (solar).
https://www.enersys.com/sbsxl/
https://www.enersys.com/WorkArea/DownloadAsset.aspx?id=25769807496The next generation of front terminal batteries from EnerSys®. The SBS XL series comes from a respected lineage, the industry leading, EnerSys SBS Thin Plate Pure Lead (TPPL) battery. SBS XL takes the SBS to the next level. The SBS XL is designed to provide 10 years of life at 95°F (35°C) in back up applications at high operating temperatures.The recommend a 10% rate of charge... And the charging voltage recommended is pretty low--That is common for GEL batteries (to prevent gas bubbles from forming in the GEL/Plate boundaries which can permanently reduces capacity).
I did not see a voltage set point for cycling applications in the documents I looked at.
You should probably contact Enersys customer support and see what they say.
Most solar charge controllers are programmable for charging different battery types. In this case, the spec. sheet seems to be set really low for charging (2.27 volts per cell @ 25C or 13.62 volts for 12 volt bank) which may be for float charging (again, no cycling voltage charge points are in the spec sheet).
Until you get feedback from Enersys support, probably not a good idea to raise the charging voltage (GELs typically are charged at 14.2 volts for cycling applications--But not recommended for cycling apps).
260 Watt array is pretty small for this bank (if your array is 1x 260 Watt solar panel)... The charging current (best case, solar noon, cool/clear days):- 260 Watt array * 0.77 panel+controller deratings * 1/14.0 volts charging = 14.3 amps typical max charging current
And to run just the refrigerator, I would be suggesting a 413 Watt array would barely keep up "in summer" with just the refrigerator. A 1x 260 Watt panel--Your bank would slowly lose average state of charge without a backup gasoline generator (deficit charging).
For the connection of 8 AWG for 5 feet from charge controller to battery bank @ 40 amps (if you get a larger array), the voltage drop would be:
https://www.calculator.net/voltage-drop-calculator.html?material=copper&wiresize=2.061&voltage=14&phase=dc&noofconductor=1&distance=5&distanceunit=feet&eres=40&x=0&y=0
Voltage drop: 0.25
Voltage drop percentage: 1.79%
Voltage at the end: 13.75
That is really too much voltage drop where 0.05 to 0.10 volt drop recommended, not 0.25 volts (if you use 40 amps charging). At 14.3 amps the voltage drop would be:
Voltage drop: 0.090
Voltage drop percentage: 0.64%
Voltage at the end: 13.91
8 AWG cable is just heavy enough (bit less than 0.10 volt drop max suggested).
For a 40 amp rate of charge, the minimum AWG recommended is 4 AWG at 5 feet:
Voltage drop: 0.099
Voltage drop percentage: 0.71%
Voltage at the end: 13.901
4 AWG is pretty heavy cabling--If you can shorten the cable length to 2.5 feet or less (and you can use smaller AWG cable--1/2 the distance then ~ +3 AWG "lighter" wiring).
At this point--Not sure that your present (GEL?) battery is the right pick. The 260 Watt array (?) is too small for your loads, and your wiring from the charge controller to the battery bank is too long/too small for a 40 Amp charging current (too much voltage drop).
-Bill
PS: What is a GEL Lead Acid battery:
https://batteryuniversity.com/learn/article/bu_201b_gel_lead_acid_batteryThe early gelled lead acid battery developed in the 1950s by Sonnenschein (Germany) became popular in the 1970s. Mixing sulfuric acid with a silica-gelling agent converts liquid electrolyte into a semi-stiff paste to make the gel maintenance free. The AGM that arrived in the early 1980s offers similar performance to gel but each system offers slightly different characteristics to fill unique market needs. Gel batteries are commonly used in UPS, big and small, while AGM has carved out a market with starter and deep-cycle applications. Gel and AGM batteries are part of the valve-regulated lead acid (VRLA) family to make the traditional flooded lead acid maintenance free.Again--Contact EnerSys (or your local battery supplier) to figure out the charging voltage needed for your cycling battery bank (I am NOT a battery engineer).
-BBNear San Francisco California: 3.5kWatt Grid Tied Solar power system+small backup genset -
If I change the wire from the battery to the fridge. I think it might be 12 or 14AWG on maybe 20 feet... to 8AWG, the voltage drop will be less, so does it will take less battery for the same amount of time?
And with only one 12 volts panel, switching my system from 12 to 24 volts, will my battery charge faster?
Again, thank you very much for you time, patience and help.
I'm new to this world and learning a lot!
EDIT: I'm thinking now my battery bank (760 amps) might be too big for my solar array (260 watts). Maybe I should use only 2 in parallel (still 12 volts but 380 amps). What do you think? -
Generally, we aim for 1% to 3% maximum voltage drop... That is a 1% to 3% (or a bit more) loss of power...
For example, if your fridge draws 4.3 amps @ 14 AWG wire @ 20 Feet, the voltage drop would be:
https://www.calculator.net/voltage-drop-calculator.html?material=copper&wiresize=8.286&voltage=12&phase=dc&noofconductor=1&distance=20&distanceunit=feet&eres=4.3&x=0&y=0
Voltage drop: 0.43
Voltage drop percentage: 3.62%
Voltage at the end: 11.57
It is a bit more drop than I would suggest--But it does work (and wastes somewhere around 3.62% to 7% of your solar energy with the 14 AWG cable... Not the worst thing in the world...
Regarding to switching to 24 volts... The basic power equation is Power=Voltage*Current
So, if you double the voltage, then the current will fall by 1/2... And be the same amount of power (but you need 2-6x heavier cable to carry that same amount of power at the lower voltage).
Sending a lot of power at 12 volts for longer than a few meters--Gets difficult--Expensive copper cable to keep voltage drop down.
Your fridge is not using that much power, but at 20 Feet, it would have been better to use heavier cable. And that is only 42 Watts... When you need to send 420 Watts (like a small well pump), 12 volts becomes pretty difficult to even try and send the power any distance.
You sort of did the cart before the horse here... You installed your load and solar system without really doing much in the way of detailed design (details matter a whole bunch in solar power).
For example, your 12/24 VDC refrigerator is a pretty rare load--Works at both 12 and 24 volts just fine... It will take:- 42 Watt compressor / 24 volts = 1.75 Amps nominal
- 42 Watt compressor / 12 volts = 4.3 Amps nominal
Voltage drop: 0.18
Voltage drop percentage: 0.74%
Voltage at the end: 23.82
And your voltage drop/losses using the same 14 AWG cable is much less at 24 VDC.
Regarding the battery bank... No, the batteries will not charge any faster. However, instead of a 760 AH battery bank with a 76 Amp rate of charge (10%) @ 12 volts, the same energy storage (2s x 2p) is now 380 AH and 38 Amp for 10% rate of charge...
Besides saving the cost of copper cabling (80 amp cable around 4 or 2 AWG cable (heavy, expensive, difficult to bend, may not fit terminals easily), whereas 40 amp cable would be around 10 or 8 AWG... Much easier to wire (and cheaper), easier to send same power longer distances, etc.
Also 80 amp solar charge controllers are not cheap (around $600 USD for higher end MPPT controllers). Instead, you can use your existing 40 Amp controller on the 380 AH @ 24 volt battery bank (charge controller are rated for maximum current at 12/24 and perhaps 48 VDC battery bank). So, for the same price charge controller, at 24 volts your controller can support a 2x larger solar array and get your 10% rate of charge (the 40 amp @ 12 volts, only ~5% rate of charge).
But, there are things you have to watch for. Most solar charge controllers are "Buck Type" digital switching power supplies... They can only take higher voltage (lower current) from the solar array and efficiently down converter to the lower battery bank voltage (and higher charging current--Remember Power=Voltage*Current -- Power stays the same, voltage from input to output for MPPT controller--And raises current to battery bank).
This means you have to look at the Vmp-array... For a 24 volt battery bank, that means you need a higher voltage array than a 12 volt batter bank would. For an MPPT type charge controller, the Vmp-array minimum name plate voltage would be:- 29 volts charging * 1.3 MPPT operating factor = 37.7 volt array Vmp minimum suggested (24 volt bank)
- 14.5 volts charging * 1.3 MPPT operating factor = 18.85 volts Array Vmp minimum suggested (12 volt bank)
Note that running your Array at higher voltage Vmp is usually a good thing too... Lets you use a larger array with smaller copper cabling (and you can send more power longer distances with higher voltage array).
There are other details to watch for... Your 260 Watt panel may no longer be available--When you add panels in series, you need to match Imp panel to within ~10% or better.
When you put panels (or strings) in parallel, you need to match Vmp (or Vmp-string) to 10% or better too...
You need to look at the Vmp/Imp specifications for your panel and if you get (for example) 3 more panels (2s x 2p), you need to check the specifications closely (i.e, there may be a 265 or 270 Watt panel with very similar Vmp/Imp specs... And that is fine). However, matching a 260 Watt panel with a 320 Watt panel may not be practical.
Anyway--At this point you need more solar power to run the fridge... Your battery bank is a bit on the large size, but your array is too small to run the fridge through the summer reliably without using a genset during bad weather/occasionaly to bring up the bank charge...
To give you an idea how the battery math works. We normally suggest 2 days storage and 50% maximum discharge for a Lead Acid battery bank. Using 24 volt bank, a suggested "nominal" size battery bank for your fridge would be:- 1,008 WH per day * 2 days * 1/0.50 max discharge * 1/24 volt battery bank = 168 AH @ 24 volts
Using a smaller battery bank is not really helpful here--Unless you have need for those two batteries elsewhere. Based on the battery bank size, the "nice" 10% rate of charge array would be:- 380 AH * 28.0 volts charging * 1/0.77 panel+controller derating * 0.10 rate of charge = 1,382 Watt array nominal
- 190 AH * 28.0 volts charging * 1/0.77 panel+controller derating * 0.10 rate of charge = 691 Watt array nominal
- 1,008 WH per day * 1/0.61 DC off grid system eff * 1/4.0 hours of "summer sun" = 413 Watt array "break even"
- 413 Watt array * 1/0.65 base load fudge factor = 636 Watt "nominal" array for summer fridge operation
With the larger array and battery bank, you could easily run ~2x or larger loads (AC inverter, laptop computer, water pump, TV, cell charger, etc.)...
The largest (cost effective) array your 40 amp controller can run on a 24 volt battery bank would be:- 40 amps * 29.0 volts charging * 1/0.77 panel+controller deratings = ~1,506 Watt array "typical" cost effective maximum
- 1,382 Watt array * 0.61 DC off grid system eff * 4.0 hours of sun minimum (summer) = 3,372 WH per day
You have some choices to make... 12/24 volts, 2 or 4 batteries, how large of an array, add AC inverter (slightly less efficient--0.51 AC off grid system eff vs 0.61 for DC off grid system eff).
I am making lots of guesses here---And you need to decide what your loads will be. Having a refrigerator is a pretty good size load for an off grid solar power system. Most people do want more power for LED Lighting, cell/laptop charging, possible Water pump, perhaps even a clothes washer... You are right on the cusp of supporting those loads...
-BillNear San Francisco California: 3.5kWatt Grid Tied Solar power system+small backup genset -
Bill your a legend..
Thankyou to share your knowledge.. -
You are very welcome foilcap.
And feel free to start your own discussion/thread if you have further questions about your own system.
Sincerely,
-BillNear San Francisco California: 3.5kWatt Grid Tied Solar power system+small backup genset -
For a fridge of your size I would recommend a 1Kw array and suitable battery bank for storage. Anything much less and you will have problems. From somebody else on an island.Island cottage solar system with appriximately 2500 watts of panels, 1kw facing southeast 1.3kw facing southwest 170watt ancient Arco's facing due south. All panels in parallel for a 24 volt system. Trace DR1524 MSW inverter which has performed flawlessly since 1994. Outback Flexmax 80 MPPT charge controller four 467A-h AGM batteries. Insignia 11.5 cubic foot electric fridge 1/4hp GSW piston pump. My 31st year.
Categories
- All Categories
- 228 Forum & Website
- 136 Solar Forum News and Announcements
- 1.4K Solar News, Reviews, & Product Announcements
- 199 Solar Information links & sources, event announcements
- 898 Solar Product Reviews & Opinions
- 256 Solar Skeptics, Hype, & Scams Corner
- 22.5K Solar Electric Power, Wind Power & Balance of System
- 3.5K General Solar Power Topics
- 6.7K Solar Beginners Corner
- 1K PV Installers Forum - NEC, Wiring, Installation
- 2.1K Advanced Solar Electric Technical Forum
- 5.6K Off Grid Solar & Battery Systems
- 428 Caravan, Recreational Vehicle, and Marine Power Systems
- 1.1K Grid Tie and Grid Interactive Systems
- 654 Solar Water Pumping
- 816 Wind Power Generation
- 624 Energy Use & Conservation
- 619 Discussion Forums/Café
- 312 In the Weeds--Member's Choice
- 75 Construction
- 124 New Battery Technologies
- 108 Old Battery Tech Discussions
- 3.8K Solar News - Automatic Feed
- 3.8K Solar Energy News RSS Feed