Piggott PMA coil- what size wire to use?
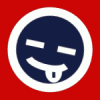
HE411
Registered Users Posts: 8 ✭✭
Greetings one and all! I found this board while doing some research on building an axial flux PMA. Looks like there are some very smart people here. Hopefully I can lean on your knowledge and experience to solve some of the (self-made?) PMA riddles that have stalled my development progress.
We live in a class 2 wind zone (5.4 m/sec annual avg) but in our specific location the wind is somewhat less than the class 2 rating being 4.5 m/sec on average. Still plenty of power to harvest but a modified Piggott PMA is needed to harvest the available power at speeds lower than that stated in his writings imho. Mr. Piggott's 2003 document How to Build a Wind Turbine specifies 320 turns of #21 wire per coil for a 48 volt PMA machine having 10 coils total for a machine that begins to produce power at a wind speed of 3 m/sec with an 8' rotor. I want to increase the rotor size to 12' and build the PMA with 20 coils to produce 60 volts. 60 volts is specified to allow for PMA inefficiency and line loss as the tower has to be set almost 400' from the actual point of use. This adds a comfortable margin to what is essentially a 48 volt machine. Using the equation from www.6pie.com/faradayslaw.php each coil requires 1764 turns at a rotor speed of 250 RPM to produce 60 volts. Herein lies one of the riddles. How can this be? 1764 turns of what size wire? The formula used for calculating the total number of turns is N=V/(( Te*A)/ S)) where V= desired output voltage, Te= (magnet gauss*.5)/10000, A= magnet area in square meters and S= 60/rotor RPM. Lastly, N is divided by the number of coils to determine the number of turns per coil.
So for this example the equation becomes N=60/(((6325*.5/10000)*(2*1/1550.0031))/(60/250))=35289 total turns. Finally 35289/20=1764 turns per coil at 250 RPM. At 500 RPM 882 turns is needed to produce 60 volts and at 1000 RPM 441 turns per coil is needed. This, to me, seems ridiculous and as you can see there is no provision for wire gauge in this equation. What am I missing here? Is this the correct equation? Is there a better equation that includes the wire size or is it even needed in the calculation? If it is not needed then how is the wire size determined?
We live in a class 2 wind zone (5.4 m/sec annual avg) but in our specific location the wind is somewhat less than the class 2 rating being 4.5 m/sec on average. Still plenty of power to harvest but a modified Piggott PMA is needed to harvest the available power at speeds lower than that stated in his writings imho. Mr. Piggott's 2003 document How to Build a Wind Turbine specifies 320 turns of #21 wire per coil for a 48 volt PMA machine having 10 coils total for a machine that begins to produce power at a wind speed of 3 m/sec with an 8' rotor. I want to increase the rotor size to 12' and build the PMA with 20 coils to produce 60 volts. 60 volts is specified to allow for PMA inefficiency and line loss as the tower has to be set almost 400' from the actual point of use. This adds a comfortable margin to what is essentially a 48 volt machine. Using the equation from www.6pie.com/faradayslaw.php each coil requires 1764 turns at a rotor speed of 250 RPM to produce 60 volts. Herein lies one of the riddles. How can this be? 1764 turns of what size wire? The formula used for calculating the total number of turns is N=V/(( Te*A)/ S)) where V= desired output voltage, Te= (magnet gauss*.5)/10000, A= magnet area in square meters and S= 60/rotor RPM. Lastly, N is divided by the number of coils to determine the number of turns per coil.
So for this example the equation becomes N=60/(((6325*.5/10000)*(2*1/1550.0031))/(60/250))=35289 total turns. Finally 35289/20=1764 turns per coil at 250 RPM. At 500 RPM 882 turns is needed to produce 60 volts and at 1000 RPM 441 turns per coil is needed. This, to me, seems ridiculous and as you can see there is no provision for wire gauge in this equation. What am I missing here? Is this the correct equation? Is there a better equation that includes the wire size or is it even needed in the calculation? If it is not needed then how is the wire size determined?
Comments
-
Re: Piggott PMA coil- what size wire to use?
Wow. This can make ones head hurt. I DONT have the answers, but instead, can pose a few more questions about it.
As voltage goes higher (more turns) you would need to have smaller gauge wire to fit the coils into the same space.
Smaller gauge has higher internal resistance, and more heating losses.
You can eventually reach a point, where you are heating the coils, and not producing usable power.
Maybe you can create a nomograph (nongram), chart, and plot the 12V, 24 & 48 points, and see where the 60V would lay.
I think you can increase the voltage also, by increasing the speed, and maybe creating a larger diameter rotor with more sets of coils and magnets, the 48V specs will achieve 60V outputs, due to the higher "relative" speeds of a larger rotor with the same actual RPM's (which is what you are doing with larger rotor)
YVMV
(Your voltage may vary)Powerfab top of pole PV mount | Listeroid 6/1 w/st5 gen head | XW6048 inverter/chgr | Iota 48V/15A charger | Morningstar 60A MPPT | 48V, 800A NiFe Battery (in series)| 15, Evergreen 205w "12V" PV array on pole | Midnight ePanel | Grundfos 10 SO5-9 with 3 wire Franklin Electric motor (1/2hp 240V 1ph ) on a timer for 3 hr noontime run - Runs off PV ||
|| Midnight Classic 200 | 10, Evergreen 200w in a 160VOC array ||
|| VEC1093 12V Charger | Maha C401 aa/aaa Charger | SureSine | Sunsaver MPPT 15A
solar: http://tinyurl.com/LMR-Solar
gen: http://tinyurl.com/LMR-Lister , -
Re: Piggott PMA coil- what size wire to use?
Another thing to keep in mind by winding the coils for 60 vdc the alternator will be in a stall all the time. i highly suggest you visit over to www.otherpower.com. -
Re: Piggott PMA coil- what size wire to use?
I popped over to otherpower.com and was able to find some useful information but no direct answers. Spent the afternoon checking out Dan-n-Dan's 20 foot monster. It seems that they rely on trial and error mostly to figure out the coil details which is fine if you have the resources to do that. I'll keep digging.
You bring up some good points Mike. There is only so much power available in the wind and the amount you can harvest depends mainly on the size of the rotor to which the alternator must be matched. If the alternator is too big then a stall condition is created when loaded in lower winds. Too small then you run the risk of burnout in higher winds which circles back to the original riddle. I'm going to fall back, rethink the scenario, draw some graphs and crunch a few more numbers. I may already have the answer and just don't know it.
Hank -
Re: Piggott PMA coil- what size wire to use?
I believe we have this riddle solved and it's not as complicated as originally thought. That equation on 6pie.com? Forget about it. It's obviously good for something but is not well suited for the need at hand. Going back to Mr. Faraday's original equation and with a little help from Mr. Maxwell an equation was derived that does suit the need at hand. Wire gauge doesn't even enter the equation at this stage.
The system voltage, number of coils and magnets, magnet surface strength and cut in speed must be selected first before anything else can happen. Plugging these values into equation 3a provides a handy little quotient by which the system voltage is divided to arrive at the number of turns per coil. What's the coil airspace? It's the area of a single magnet (L x W) in square meters. While we're here, tesla is gauss/10000. Use the gauss surface field strength rating from the magnet makers spec sheet in the conversion to tesla.
The number of turns per coil:
So, the number of turns per coil depends entirely on the system voltage and the values that determine the quotient N' regardless of the wire size.
Wire size comes into play when figuring the ampacity (current carrying capacity) and physical size of the coil. A heavy wire, relatively speaking, has more ampacity than a thin wire. A heavy wire obviously makes a bigger coil than one made with thin wire given the same number of turns. It's a simple matter of choosing the right wire size for the application and let the coil be as big or as small as it needs to be. An easy formula for determining wire size is:
Divide the required coil current by 4869.48 and take the square root to find ρ. Look up the value for ρ on an AWG wire size chart and select the nearest bare wire gauge from the chart. It won't hurt to round up to the next larger gauge. Magnet wire is available in various "builds". The build represents the type of coating and the coating thickness which adds to the wire diameter. Select the build and the wire choice is made.
Pretty simple but it took a week to figure it out. One of my instructors in college once asked "Why do you constantly reinvent the wheel?" My reply? "I don't reinvent it. I just need to understand what makes it go around". BTW all of my notes so far are compiled in a short paper. I'm more than willing to share it with everyone but a formula needs checked for notation before it's published. Any math people here who can check summation notation for accuracy? The math is correct. I'm just not sure of the notation. -
Re: Piggott PMA coil- what size wire to use?
Wow ! Very Nice !Powerfab top of pole PV mount | Listeroid 6/1 w/st5 gen head | XW6048 inverter/chgr | Iota 48V/15A charger | Morningstar 60A MPPT | 48V, 800A NiFe Battery (in series)| 15, Evergreen 205w "12V" PV array on pole | Midnight ePanel | Grundfos 10 SO5-9 with 3 wire Franklin Electric motor (1/2hp 240V 1ph ) on a timer for 3 hr noontime run - Runs off PV ||
|| Midnight Classic 200 | 10, Evergreen 200w in a 160VOC array ||
|| VEC1093 12V Charger | Maha C401 aa/aaa Charger | SureSine | Sunsaver MPPT 15A
solar: http://tinyurl.com/LMR-Solar
gen: http://tinyurl.com/LMR-Lister , -
Re: Piggott PMA coil- what size wire to use?
Bare wire diameter is in what units ? Inches, mm, thousandths of an inch, ?
And Rotor Velocity in Seconds... Is that Seconds as in time or
Seconds as in arc-seconds ?
boB -
Re: Piggott PMA coil- what size wire to use?
Thanks Mike! Bob, it's seconds as in time. Now that I look at it, a more accurate description of T is revolutions per second (RPM/60). My apologies for the confusion. Bare wire diameter is thousandths of an inch.
Hank -
Re: Piggott PMA coil- what size wire to use?
>>T is revolutions per second (RPM/60)
Ahhh yes. Duh ! T= Time... Of course. RPS I guess.
Thanks.
boB -
Re: Piggott PMA coil- what size wire to use?
Here is where the millions of dollars spent on r&d come in. The thicker or heavier gaged the wire the further away from the magnet each winding will be and less magnetic flux will be cut and the less output per winding because the magnetic flux is greatest at the surface of the magnet and drops off dramatically even at a quarter of an inch. The thinner the wire the closer each winding will be to the magnet and the greater the magnetic flux and less windings are needed to give you what you want but less current can be drawn with out burning the coil up.
This is where you get to try different ways to draw the magnetic flux out and through the coil.
Each winding will have to be calculated using Faraday's formula because for each winding the flux is different. That might seem a bit much to ask but remember Millions of dollars in r&d that's not because it's an easy thing to calculate and they just want to get a tax right off. -
Re: Piggott PMA coil- what size wire to use?
wouldn't they just get a stronger magnet or more of them to make up for the thicker wires? -
Hello, I am having trouble using the equation that was posted to calculate the number of turns of wire per coil. I have made this spreadsheet for the equation and I keep getting confusing results. I would like to make my own small alternator with 6 coils and 16 magnets (eight for each rotor), I would like a cut in rpm of around 70 at about 15 volts. The magnets I'm intending on using are grade N50 with flux density of 1.41 Tesla (14100 Gauss) with dimensions of 1" x .5" x .25". After solving the equation I get 5,260 turns per coil. This seems extremely high for a 15V alternator at 70 rpm.
I believe I have done the math right, I have converted the rpm to rps as described above. I converted the magnet surface area in square inches to square meters (.5 in^2 to 0.00032258 m^2).
Am I doing something wrong or does the alternator I have described actually require over 5,000 windings.
Here is a screenshot of the spreadsheet.
Thanks for your help. -
Welcome to the forum WindnStuff,
I get the same answer as you doing the spread sheet math...
However, do you have a link to the original equation? The x/y/z can be evaluated several ways... Nominally, my math from decades (as I recall) past would have evaluated that as x/(y*z) ... If you do that with /J9, I get 438.6 turns.
-BillNear San Francisco California: 3.5kWatt Grid Tied Solar power system+small backup genset -
Hello, Thank you for the speedy reply.
The equation I used was posted in the form of a photo in a previous response. I will post it again below.
https://us.v-cdn.net/6024911/uploads/attachments/2846/433.jpg
I have been unable to get the same answer as you which is probably because I am inexperienced with using the spreadsheet. A simple explanation of the exact equation you used would be greatly appreciated.
-
Looks like your spread sheet equation (simplified) should be:
= E9*J9*60/(2*F9*G9*H9*I9)
= 15 Volts * 60 * 6 / (2 * 16 * 1.42 * 0.00032258 * 70)
= 5263 turns (corrected--Looks like a missed a decimal point--Bill)
That is the math (unless I made a mistake). I have nothing to say about the equations themselves (no experience).
-BillNear San Francisco California: 3.5kWatt Grid Tied Solar power system+small backup genset -
The equation you posted for the spreadsheet is correct from what I can tell, but I think you made a mistake in the math. When I did the same equation I got an answer of 5262.83 which is exactly 10 times your answer so I'm guessing you missed a decimal place somewhere.
Thank you. -
You are correct.... It all looked OK at 11pm last night.
Sorry.
-BillNear San Francisco California: 3.5kWatt Grid Tied Solar power system+small backup genset -
I have plugged in the results from an alternator design I found online and the difference between the estimation and the actual was large. The alternator used 6 coils each with 120 turns of wire connected in series, 8 magnets (20 mm diameter, 5 mm height, area of 0.00031415 m^2) on each rotor. At 600 rpm the alternator produced about 16 volts. When I put in the voltage and the rpm, the equation gives 672 turns of wire per coil which is more than 5 times the actual value.
In my experience this equation has given me useless results, however it is likely I have done something wrong.
Thanks again for the help.
Here are the sites I got the alternator design from.
http://www.windandwet.com/windturbine/turbine1/alternator.php
http://www.windandwet.com/windturbine/turbine1/alternator_test.php
-
I'm surprised to see this post is still here. Much has transpired in the past 12 years, most important being answers to the original questions posted. Looks like others have tried to use an equation i posted for calculating the number of wire turns per coil to build a Piggot style PMA. Well, the equation as originally posted is flawed. My apology to windnstuff and others who may have tried to use that equation. The correct equation is:
Categories
- All Categories
- 228 Forum & Website
- 136 Solar Forum News and Announcements
- 1.4K Solar News, Reviews, & Product Announcements
- 199 Solar Information links & sources, event announcements
- 898 Solar Product Reviews & Opinions
- 256 Solar Skeptics, Hype, & Scams Corner
- 22.5K Solar Electric Power, Wind Power & Balance of System
- 3.5K General Solar Power Topics
- 6.7K Solar Beginners Corner
- 1K PV Installers Forum - NEC, Wiring, Installation
- 2.1K Advanced Solar Electric Technical Forum
- 5.6K Off Grid Solar & Battery Systems
- 428 Caravan, Recreational Vehicle, and Marine Power Systems
- 1.1K Grid Tie and Grid Interactive Systems
- 654 Solar Water Pumping
- 816 Wind Power Generation
- 624 Energy Use & Conservation
- 619 Discussion Forums/Café
- 312 In the Weeds--Member's Choice
- 75 Construction
- 124 New Battery Technologies
- 108 Old Battery Tech Discussions
- 3.8K Solar News - Automatic Feed
- 3.8K Solar Energy News RSS Feed