Battery low voltage with load
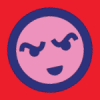
mikereilly
Registered Users Posts: 7 ✭
Hi:
I"m totally new to all of this. I picked up a complete kit on Amazon (2x flexible 100w poly panels, 20a charge controller, 10ft wires mc4 connectors. 120ah deep cycle marine battery. This is for a small camper trailer.
Anyway, after hooking 1) charge controller to battery 2) panels to charge controller and letting it charge for an afternoon (to 12.7V as per charge controller reading), I wanted to do an overnight test to see how well it held up to our Nova-Cool 2-way fridge (12/120) and then see if the panels could recharge the battery fully. After a few hours, the low voltage cut off kicked in (set at 12V). Now I also had the re-connect voltage set for 12.0v and it kept bouncing back and forth. Confused by this, I thought I'd just disconnect the load and see what was up, I mean, a 2 amp draw for a couple of hours should barely register on the battery, shouldn't it? After disconnecting, I noticed that the charge controller read 12.5V. A bit better, but still not quite as high as I'd expect.
I figure part of the problem is that the battery probably wasn't fully charged but was reading 12.7 initially due to (is it called a surface charge?) I'm still unclear on why the charge controller would read so low only under load. Could it be just from the small resistance from the battery leads? What is my remedy here? I'd like to be able to run the load through the charge controller in order to prevent discharging the battery too significantly and thus reducing it's life span. If this low reading is caused by wire resistance, should I just set my cut off voltage lower since it's an artificially low reading? Thanks in advance for any advice you may be able to give on this. I just want to be able to keep the beer cold in the camper when we're off in Baja this Winter.
I"m totally new to all of this. I picked up a complete kit on Amazon (2x flexible 100w poly panels, 20a charge controller, 10ft wires mc4 connectors. 120ah deep cycle marine battery. This is for a small camper trailer.
Anyway, after hooking 1) charge controller to battery 2) panels to charge controller and letting it charge for an afternoon (to 12.7V as per charge controller reading), I wanted to do an overnight test to see how well it held up to our Nova-Cool 2-way fridge (12/120) and then see if the panels could recharge the battery fully. After a few hours, the low voltage cut off kicked in (set at 12V). Now I also had the re-connect voltage set for 12.0v and it kept bouncing back and forth. Confused by this, I thought I'd just disconnect the load and see what was up, I mean, a 2 amp draw for a couple of hours should barely register on the battery, shouldn't it? After disconnecting, I noticed that the charge controller read 12.5V. A bit better, but still not quite as high as I'd expect.
I figure part of the problem is that the battery probably wasn't fully charged but was reading 12.7 initially due to (is it called a surface charge?) I'm still unclear on why the charge controller would read so low only under load. Could it be just from the small resistance from the battery leads? What is my remedy here? I'd like to be able to run the load through the charge controller in order to prevent discharging the battery too significantly and thus reducing it's life span. If this low reading is caused by wire resistance, should I just set my cut off voltage lower since it's an artificially low reading? Thanks in advance for any advice you may be able to give on this. I just want to be able to keep the beer cold in the camper when we're off in Baja this Winter.
Comments
-
Welcome to the forum Mike,
Lead Acid battery voltage is a relatively complex issue... A "resting" fully charged FLA (flooded cell lead acid deep cycle) battery is around 12.7-12.8 volts.
To charge a FLA battery, you want the controller to have the "absorb" voltage setpoint to ~14.75 volts. And to hold that voltage for 2-6 hours or so (longer if deeper discharge).
If you are seeing 12.7 volts while charging--Then the battery is significantly discharged and/or you have very little charging current.
For a 120 AH @ 12 volt "marine battery" -- Say you discharge it at a 10% discharge rate to 75% state of charge--That would be 12 amp for ~2.5 hours.
200 Watts of solar panels would take:- 200 Watts * 0.77 panel+controller deraring * 1/14.5 volts charging = 10.6 amps charging current (full sun, near noon)
I don't know what Nova Cool fridge you have, but assume it draw 4.4 amps when first plugged in and draws and average of ~2.2 amps when cold and cycling (50% duty cycle at 12 volts).
So, you are still looking at ~2 hours * 4.4 amps = 8.8 AH out of a 12 volt battery (120AH capacity)... Still not near enough to trigger a low voltage alarm (typically 11.5 to 10.5 volts--depending on settings/loads/etc.).
Anyway--First things first. Lead Acid batteries do not like to sit at less than 75% state of charge for very long (more than a few hours) or they start sulfating... So you should get that battery properly on charge (AC battery charger, your trailer in full sun, etc.).
10 amps of charging current * 5 hours of sun per day (relatively sunny area) = 50 AH per day
So, it will take 2-3 days in your RV (assuming everything working OK) to recharge the battery back to full (via solar).
Do you have a hydrometer?
https://www.solar-electric.com/search/?q=hydrometer
Do you have a DC Current Clamp capable DMM?
https://www.amazon.com/gp/product/B019CY4FB4 (mid-range priced meter)
There are less expensive DC current clamp DMM meters available too (less than $50 or so). Note that you want a DC current clamp meter (usually AC/DC current clamp) and not an AC only Current Clamp DMM (you have to read the descriptions closely).
These couple of tools will help you with debugging and better understanding your system.
-BillNear San Francisco California: 3.5kWatt Grid Tied Solar power system+small backup genset -
I'm not sure, but I think Nova-cool is a Danfoss type compressor. It has a relatively small startup surge (as compared to a regular AC fridge), but a surge nevertheless. This surge might be what triggered the low voltage cutoff.Off-grid.
Main system ~4kw panels into 2xMNClassic150 370ah 48v bank 2xOutback 3548 inverter 120v + 240v autotransformer
Night system ~1kw panels into 1xMNClassic150 700ah 12v bank morningstar 300w inverter -
Thanks for the response, Bill:
The controller shows only specifications for equalization, float, discharge stop and discharge reconnect. I'm assuming it does absorb/equalization at the same voltage? It had identified the battery as b01 (sealed) and set equalization to 14.4. After reading your comment, I've changed the battery type to b03 (flooded) which gets 14.6v.
The good news is that the voltage when there's no draw, as read by the charge controller, was 12.4-12.5 after I disconnected the load - and I've left it that way.
This morning, if I disconnect the charge controller from the battery I am getting 13.06v with my multimeter (must be reading a bit higher than the true charge?). Hooking the controller back up with the battery reads 12.9v, and on a cloudy morning here on Vancouver Island, I'm not getting a ton of charging at 13v after I connect the panels. Should get up to the float charge levels (13,8v) later when the sun can peer at those panels more directly through the clouds.
Looks like it's time to get a hydrometer at least. Can I get away with a cheap inline power analyzer/watt meter (kill a watt style?):
https://www.amazon.ca/Maskdoo-G-T-Power-Precision-Analyzer-Backlit/dp/B07JWHB2VB/ref=sr_1_10?keywords=killawatt&qid=1562348272&s=gateway&sr=8-10
I think (with my complete lack of experience in such things) that my main concern is the low voltage reading at the charge controller when the fridge is plugged in to it's load circuit.
-
OK, I've just done a quick experiment. So I'm pretty sure part of the issue in the changes of voltage is related to surface charge. Plugging a load in to what I think is a charged battery with panels unplugged results in a pretty quick drop off in voltage. Over the course of a couple of minutes the voltage measured by the charge controller dropped to 12.4v while the voltage at the battery read by the multimeter dropped to 12.68v. Voltage read by multimeter at the fridge matched more or less voltage read by the controller.
This leads me to believe that I'm getting around ~0.2v drop from the battery to the controller (as well as misleading surface charge that I need to deal with to get a more true reading). Does this make sense or am I talking through my hat? -
I'd use a single meter to measure all the voltages to establish what the drop is, so the multimeter at the controller output terminals, battery terminals, and load terminals. Note that voltage drop will generally increase as more current flows through a circuit.
I'd also read the two meters (controller and multimeter) on the controller output at the same time to get a sense of how far apart they are.
I'm not sure why you would have the fridge wired to the controller load terminals. They're usually used for things like lights which can then be controlled by settings (eg on at dusk, off at dawn). A load like the fridge would be wired to the battery (or distibution busses), with the positive wire fused or breakered for wire size used. IIRC, the Danfoss controls have a low battery cutoff already, so the controller also doing it too is kind of redundant.Off-grid.
Main system ~4kw panels into 2xMNClassic150 370ah 48v bank 2xOutback 3548 inverter 120v + 240v autotransformer
Night system ~1kw panels into 1xMNClassic150 700ah 12v bank morningstar 300w inverter -
The low voltage cut off is set at 10.4v on the fridge, which is way too low (the cut in is 11.7v - also too low).
So, taking Estragon's advice, I've checked all of the readings with the multimeter, although it involved baring a bit more wire than I'll want long term (but ok for a quick test I suppose). Here are the readings after everything stabilized at 15:25 (around 5 minutes of fridge run time):
All readings taken with solar panels disconnected
Battery: 12.74v
At controller from battery: 12.54v
At controller output side: 12.48v
At fridge: 12.38v
The controller reads 12.3 and 12.4v for the battery, alternating between the two, so it's off by ~0.2v from the multimeter, and the reading it shows compared to the battery voltage is 0.3-0.4v off (assuming the multimeter is correct). It looks like a 0.2v drop from battery to controller and another 0.15 or so by the time it gets to the fridge.
It looks to me like I should set the low voltage cut off on the controller to 11.9 or so to keep battery charge above 50% (voltage 12.2v). The thing is, the charger reads higher when the load turns off, so I'll have to determine what to set the cut in voltage at to prevent it from turning the fridge off and on repeatedly. -
The low voltage cut-off on the fridge is to protect the fridge (lower voltage = higher current for a given watt load), not the batteries. Generally speaking, you want the fridge to run to protect the contents. If running the fridge causes the batteries to discharge too much, that's a problem with system design that isn't going to be solved with cut-out settings.
Voltage drop seems a bit high to me with little current flow. What are the wire sizes and distances involved?
Off-grid.
Main system ~4kw panels into 2xMNClassic150 370ah 48v bank 2xOutback 3548 inverter 120v + 240v autotransformer
Night system ~1kw panels into 1xMNClassic150 700ah 12v bank morningstar 300w inverter -
I think (although I'm not sure) that the wires from the controller to the battery are 3m (10ft) 12 gauge stranded tinned copper (look silver except where cut). I know for sure that from the controller to the fridge are 1.6m (5ft) 12 gauge solid copper.
-
You want to have the charge controller relatively close to the battery bank to limit voltage drop to 0.05 to 0.10 volts at rated current (ideally). Short/heavy copper cabling--Then the controller is "accurately" charging the battery bank.
You can use a simple voltage drop calculator to estimate the voltage drop (this one uses "one way" wire run--assuming there is a round trip for current flow):
https://www.calculator./voltage-drop-calculator.html
-BillNear San Francisco California: 3.5kWatt Grid Tied Solar power system+small backup genset -
12awg might be a bit light. As Bill said, you want the controller to see a pretty accurate battery voltage so it charges properly. Personally, I'd use the biggest wire that fits on the controller battery output terminal to minimize voltage drop.
Also, retighten connections after a day or so. They can loosen a surprising amount.Off-grid.
Main system ~4kw panels into 2xMNClassic150 370ah 48v bank 2xOutback 3548 inverter 120v + 240v autotransformer
Night system ~1kw panels into 1xMNClassic150 700ah 12v bank morningstar 300w inverter -
All right. After playing with the calculator a bit and considering the options, it looks like it's going to be a Good Idea (TM) to use as short a run as possible of as high a gauge as possible from the battery to the charge controller. I can probably get the one way trip down to about 3-4 feet and either 8 or 10 gauge due to limitations on the controller. Or I can shorten the existing wires and take the fridge off the controller's output circuit to keep the current from creating too much voltage drop between the two points.
-
I am not quite sure I understand your wiring... Basically, you want the charge controller to connect to the battery/battery bus (through a fuse or breaker on the + lead).
And you want the refrigerator to connect directly to the battery bus (through a breaker or fuse).
This is called "home run" or "star" wired... The battery bank is your low resistance high current source.
If you (for example) ran cable from battery bus to charge controller to refrigerator--That would be called "daisy chain" cable run.
You don't want to do this because the "noise" and current surges from the refrigerator can cause confusion and voltage drop for the charge controller.
It is possible that you are connecting the refrigerator compressor to the LVD (low voltage disconnect) terminals on the solar charge controller. While this can be an "interesting idea" (set the low voltage cutoff and reconnect based on what is good for your batteries--Like 11.5 volt cutoff and 12.5 volts reconnect)--You will have to see how well that works for you (voltage drop and such).
DC Refrigerators are fairly low current (around 4-8 amps at 12 volts?)--Generally, like to connect most loads directly to the battery bank and you do the LVD management manually.
AC inverters and other heavy loads are generally too high of current for most LVD outputs/solar charge controllers--And will tend to fry the LVD components.
-BillNear San Francisco California: 3.5kWatt Grid Tied Solar power system+small backup genset -
To still have low voltage disconnect use the controller load terminals to power a relay, a normally open contact cuts power fron the battery to the refrigerator.1500W, 6× Schutten 250W Poly panels , Schneider MPPT 60 150 CC, Schneider SW 2524 inverter, 400Ah LFP 24V nominal battery with Battery Bodyguard BMS
Second system 1890W 3 × 300W No name brand poly, 3×330 Sunsolar Poly panels, Morningstar TS 60 PWM controller, no name 2000W inverter 400Ah LFP 24V nominal battery with Daly BMS, used for water pumping and day time air conditioning.
5Kw Yanmar clone single cylinder air cooled diesel generator for rare emergency charging and welding.
Categories
- All Categories
- 228 Forum & Website
- 136 Solar Forum News and Announcements
- 1.4K Solar News, Reviews, & Product Announcements
- 199 Solar Information links & sources, event announcements
- 898 Solar Product Reviews & Opinions
- 256 Solar Skeptics, Hype, & Scams Corner
- 22.5K Solar Electric Power, Wind Power & Balance of System
- 3.5K General Solar Power Topics
- 6.7K Solar Beginners Corner
- 1K PV Installers Forum - NEC, Wiring, Installation
- 2.1K Advanced Solar Electric Technical Forum
- 5.6K Off Grid Solar & Battery Systems
- 428 Caravan, Recreational Vehicle, and Marine Power Systems
- 1.1K Grid Tie and Grid Interactive Systems
- 654 Solar Water Pumping
- 816 Wind Power Generation
- 624 Energy Use & Conservation
- 619 Discussion Forums/Café
- 312 In the Weeds--Member's Choice
- 75 Construction
- 124 New Battery Technologies
- 108 Old Battery Tech Discussions
- 3.8K Solar News - Automatic Feed
- 3.8K Solar Energy News RSS Feed