Setting for Schneider Conext with Lithium-ion batteries
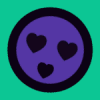
With the help of this forum and the forum host company I have put together a system that I believe will serve our purpose at our off-grid cabin. I have searched all over and have a limited idea of what the settings should be for the CC and Inv/Char but in reality I have yet to fire up the equipment so truly don't know what all the parameters are that can be set and certainly not what each of these should be set at. Your help (Mcgivor may have a very similar system) would be greatly appreciated.
For context:
Total Usage Average Watt-Hours/Day: 1910 - Total Max Watt-Hours/Day: 2529
Insolation charts show around 5 hours/day -- pnls face south/fixed @ 45*
1470 watts solar - 6x245W/voc 37.5/ISC 8.68 - 2 strings of 3 panels
Schneider 60/150 CC
Schneider 4048 inv/charger
Schneider System Control Panel
4 x 2kw 48v Chevy Volt modules = 8kw storage
I have read through the manuals for the Schneider equipment and watched their videos (and others) but I can't find anything for this equipment that specifically addresses Lithium-ion batteries. So all this really doesn't resonate as yet because I haven't had hands on to push buttons. Presently we cannot access the cabin except by snow machine or snowshoes, so the system will be installed in late May when the road opens up. I feel confident with the mechanics of the installation it's just the programming of the equipment that has me stressed!
I guess I'm really looking for someone with a similar system that can give me a list of what setting I need to adjust, and what those setting should be.
Thank you! Don
Comments
-
I'm not a lithium battery guy, but I think your battery may not be LiFePo, and the different chemistry may require a different charging voltage profile. I'm not even sure the profile is the same for all Chevy Volt packs (may have changed over the years?).
Off-grid.
Main system ~4kw panels into 2xMNClassic150 370ah 48v bank 2xOutback 3548 inverter 120v + 240v autotransformer
Night system ~1kw panels into 1xMNClassic150 700ah 12v bank morningstar 300w inverter -
You are correct.... my mistake. They are Lithium-ion batteries.
Thank you for correcting me! I will try to edit the post.
Don
-
To the best of my knowledge they are Nickel Manganese Cobalt, MNC cells, there may be differences depending on year of manufacturer, research would be a prerequisite to determine exactly what chemistry you have. Despite falling under the lithium ion umbrella, their charging requirements and setpoint may differ dramatically. Since I've no experience with the particular, unknown to me, chemistry, there is very little useful information I could offer, other than to say it's probably best to stay well within the extremes of both maximum charging and discharge values.
1500W, 6× Schutten 250W Poly panels , Schneider MPPT 60 150 CC, Schneider SW 2524 inverter, 400Ah LFP 24V nominal battery with Battery Bodyguard BMS
Second system 1890W 3 × 300W No name brand poly, 3×330 Sunsolar Poly panels, Morningstar TS 60 PWM controller, no name 2000W inverter 400Ah LFP 24V nominal battery with Daly BMS, used for water pumping and day time air conditioning.
5Kw Yanmar clone single cylinder air cooled diesel generator for rare emergency charging and welding. -
The Chevy volt uses LG NMC cells. They are high voltage unless someone has rewired them or taken apart the blocks of cells. They are meant to be liquid cooled. They are also excellent and I have a friend using them who really likes them.
The CEO of GM recently said they have never had a warranty failure of them.
"we go where power lines don't" Sierra Nevada mountain area
htps://offgridsolar1.com/
E-mail offgridsolar@sti.net -
@Mcgivor - @DAngelini
I did some research and yes Lithium NMC for the specific type of Lithium-ion. The modules I have are made up of 12 individual cells equaling ~42-45ah or 2kw of storage. I have 4 of these so 8kw or about 180ah.
My problem is I have never programmed a CC or Inv/Chrger before and I don't want to screw it up. That said I'm pretty confident I can do it but am looking here for maybe some insight as to what the process entails to set up the Schneider Conext.... and what parameters need to be adjusted besides upper limit and lower limit cut-offs. The guy whom I got the modules from has a very large system of these modules with something like 32kw of storage. He uses Schneider equipment and gave me some pointers and some numbers that are relevant:
49.5v = 90% SOC (recommended)
50.4v = 100% and is ABSOLUTE MAX
45.5v = DOD (This he said was a starting point but probably can adjust this down to 44.0v with no ill effects)
42.0v = Absolute low, this is the "knee" and below this will likely cause damage to the modules.
So, I think I'm not asking the right questions here and reading back through my post it sounds like I hadn't a clue! I have a little bit of knowledge but we all know what they say about having "a little bit of knowledge!"
I'll try again. I believe I must enter "user defined" or "custom" when setting up for the type of battery...My modules will have a BMS but it will be independent to the charge controller, to my knowledge it cannot "talk" to the CC. So, is it here that I will be able to program in the SOC and DOD (not sure I'm asking this right) OR... do I separately enter the DOD under the Inv/Chrgr settings?
I believe there are options for single stage, dual stage and three stage charging.... with Lithium what do I choose?
Can/should I enable a low temp cut-off so no current goes to the batteries when/if the modules fall below - say 34F?
I assume if when programming the CC and you choose FLA the CC would then adjust itself to that kind of battery. Are there other parameters I am not even aware of that need to be set for using Lithium modules?
The more I write the more ignorant I feel... but it is ignorance not stupidity, I can and will learn!
Thank you, Don
-
Those settings seem off. How are the packs setup, 12s? If so then they would be 44.4v nominal, 12x3.7.
I run two Gen1 packs in that setup past 4 months, 32kwh, and use the following settings via a Victron MPPT controller:
Absorbtion - 48.9 (4.075 per cell)
Float - 48.8 (4.06)
Equalization - NO
Inverter is set to cut out at 42v, 3.5v is the knee.
BMS - none at this time. Own one but have not installed yet. Packs and cells are staying within a hundredth of each other. Was checking every other day and now weekly. Waiting to see if they drift but so far rock solid. I think the big reason is that they were produced for a hard life but my C rate is under .5 vs 7 or 8 when used in a car. They are living an easy life.
Here is a guy that has done some testing on a larger system for 2+ years no issues, mix of Volt and Leaf packs. Interesting video - https://youtu.be/LwY9mIChTn4
-
@solsolardad Yes mine are gen 1 and are in groups of 12. And yes they are 3.7v each so 44.4v
So it appears that the guy I got my batteries from uses a higher Absorption of 49.5 (4.12) compared to your 48.9 (4.075). He didn't give me a float voltage so by your example probably 49.4v. He apparently pushes the top end of the curve and is more conservative on the bottom end with a cut out at 44.0v.
I have seen one of these YouTube videos..... thanks for directing me back to look at others he has done. From what I get from his videos is that my battery guy is bumping the absorption up to 90% whereas you and the video guy are only charging to 85%. It's getting g clearer! The video guy makes a good case for steering clear of absolute top and bottom.
Maybe these numbers make sense:
Absorption - 49.0
Float - 48.9
Equalization - off
I'm wondering though on the inverter cut out if this should be at 42.5 or even 43.0 to stay away from that absolute low?
Thank you for this information!
-
Agree that his settings are a little aggressive but he may have his reasons. Given my overall storage I am fine being a little more conservative not pushing my top end. If I didn’t have as much storage I would try and eek out a little more but no need, less cycles = longevity.
The absolute low is 3.0v per cell I believe. I would never go that low, 36v, but would not hesitate to go down to 42v, 3.5v per cell. DOE did a study on our Gen1 battery, interesting read that highlights cycle impacts and voltage ranges. It was the additional info that I used in setting my ranges for use. Good luck.
-
Other things to consider are, temperature compensation, should be set to 0V to maintain a constant value . Absorption time, is a tricky one, finding a means to terminate at < 3% of rated current, but this is for saturation which is something probably best avoided to increase life expectancy. Personally I use a 6 minute absorption for lifepo4, bulk and absorbtion set at the same value, looking at the graph below and using information in this link https://batteryuniversity.com/learn/article/charging_lithium_ion_batteries a termation value of 4.2V per cell or 50.4V would be ~85% charged, perhaps a good setting. Without a BMS however, it's probably best to aim a little lower like 4.0V. It's important to remember that there will be a voltage drop between the controllerand the battery, since the Schneider controller has no voltage sense input, the battery voltage will be slightly lower.
The settings used are to fool the controller into doing what it wasn't primarily designed to do, which is charge LA batteries. During my searching I found settings recommended for lifepo4, using Schneider equipment which saved much time in experimenting. This is a link which has valuable information regarding lithium battery charging and BMS manufacturers http://liionbms.com/php/index.php it has an interactive explanation regarding cell ballancing.
So it's really important to start off very conservatively as you appear to be doing, having a display of each cells behavior would be an asset worth having and a BMS selection tool.
1500W, 6× Schutten 250W Poly panels , Schneider MPPT 60 150 CC, Schneider SW 2524 inverter, 400Ah LFP 24V nominal battery with Battery Bodyguard BMS
Second system 1890W 3 × 300W No name brand poly, 3×330 Sunsolar Poly panels, Morningstar TS 60 PWM controller, no name 2000W inverter 400Ah LFP 24V nominal battery with Daly BMS, used for water pumping and day time air conditioning.
5Kw Yanmar clone single cylinder air cooled diesel generator for rare emergency charging and welding. -
Thank you so much! Looks like i have some reading to do today. I have searched this forum (got some good info from a post exchange - mcgivor/karrak), found battery university and tried to glean what I could from that, and some YouTube videos, esp the ones from Schneider. Now to follow the links you have provided for some more education!
The provider of my BMS is Bobolink Solar - https://bobolinksolar.com/ Kelvin has been working with these batteries for several years and is a huge proponent of them. He just shipped a second generation BMS out to me Friday. As i said earlier, I don't think it communicates with the CC but rather just manages charge level of all 48 cells. I'm sure I will be talking with him on this as well.
What you both have provided is extremely useful! I'm just really new to this size of system (only experience with solar is a cheap Chinese CC and a 75 watt panel to keep my campervan batteries charged) and I want to get it up and running without destroying $1,500 worth of Lithium modules! My budget is pretty well depleted so hiring a solar installer is out of the question... that said I wouldn't anyway as we will be living with this system and I believe it is important to completely understand it myself.
OK.... off to do some reading!
Thank you!
-
One of the biggest stumbling blocks, it would appear is the communication between the BMS and the charge controller. On other forums this is the most prominent point, often voiced by those in the EV sphere, which is is vastly different from off grid applications. The presumption is how to stop the charging source from charging. When operating within the safe zone, well below the upper limits, in itself avoids many potential problems. Programming the controller to avoid this area, for the most part, eliminates the risk to some degree, but not totally.
The choice of BMS is an important one, many have a direct physical connection from the controller to the battery, if something were to go wrong with the controller, where it cannot regulate voltage, for example, there needs to be something in place to interrupt the controller. This is where a seperate charge and discharge ports are so useful, the two are divorced from one another, allowing the BMS to terminate either the load, or charging independently.
However I went a step further with a second BMS to physically disconnect should the primary BMS fail to perform it's tasks, it is a passive monitor, a second layer of protection. We are all aware of the reliance of a single input source with the Boeing Max 8 incidents, albeit not as important.
There is so much to learn and absorb, but with a prehensile mind, it's easier to grasp the fundementals and translate them to a particular application. By no means do I claim to be an expert, but problem solving has always been of interest to me.
1500W, 6× Schutten 250W Poly panels , Schneider MPPT 60 150 CC, Schneider SW 2524 inverter, 400Ah LFP 24V nominal battery with Battery Bodyguard BMS
Second system 1890W 3 × 300W No name brand poly, 3×330 Sunsolar Poly panels, Morningstar TS 60 PWM controller, no name 2000W inverter 400Ah LFP 24V nominal battery with Daly BMS, used for water pumping and day time air conditioning.
5Kw Yanmar clone single cylinder air cooled diesel generator for rare emergency charging and welding. -
@solardad Just read through the battery testing report you linked. I won't pretend I understand it all but one thing seemed pretty clear, these batteries used in household solar applications are "on vacation" compared to the discharge rates - and if I read it correctly - the charge rates associated with their intended application. In our particular application - 120v ac /no 240v circuits - we will probably use only about 2.5kw in a 24hr period and I expect that much of our day time usage will actually be much less than what our 1,470 watt array will produce. I wouldn't be surprised if the batteries are topped up by 11 - 12 am.
A question for you.... mcgivor is set for 6 minutes absorption before dropping to float. Is this similar to your settings for the Li- NMC modules?
@solardad @mcgivor Another concern I have is with temperature. We may not be at the cabin much of the winter and temps inside the house will drop well below freezing. My "battery guy" who lives in Phoenix so has no worry about this feels that if I have some constant usage going on this will heat the modules sufficiently to bring them above freezing and allow charging. Do you have any experience with cold temps? My satellite internet/router will likely be on as well as a couple of cameras. Probably a total of maybe 45 watts of usage...not much but constant. I have toyed with the idea of a seedbed heating mat under the modules if needed. Your thoughts?
Thank you!
-
Generally, with lithium batteries, from what little I know, you "stop charging" when the setpoint is reached, and you do not float charge them as they do not self discharge (for months or a year).
The only reason I could see for setting and holding a float charge (and this is a very good reason) is so the (for example) solar array can maintain the state of charge while your loads are running during the day--You do not want to cycle/discharge the bank) while the sun is up and "free power".
Also, the battery bank will sustain surge current/loads (usually short term loads) that temporarily exceed the actual array output.
Once the evening comes, the solar array cannot hold the float voltage, and the battery bank starts to take over the loads overnight--Until the next sunny day.
-Bill
Near San Francisco California: 3.5kWatt Grid Tied Solar power system+small backup genset -
@nobadays So my settings are based purely on what Victron suggested with the MPPT controller (250/100) for Lithium.
Absorption is set to a max of 1hr..
For illustration my time per phase on a typical weekday (assuming decent sun):
** I would expect yours and anyone else's times to be different based on your individual scenario, setup, demands **
3~5 hrs. of Bulk charging depending on battery state from overnight use. Charge rate depends on solar irradiance but maxes out at 95amps (set by me but the individual 48v packs only see 5-6 amps.). They will charge at this rate until they reach 80-85% of the set Absorption voltage, (me - 48.9v)
1hr of Absorption - Time is fixed and recommended by Victron. Charge rate set by controller but the charge is roughly 70-80% of Bulk charge.
Float, remainder of the day - Charge rate set by controller but is just enough to keep the battery at the established Float level, 48.8v. They only reach Float if they hit there established Absorption voltage (what BB high-lighted)
Temperature is one item that I have not considered since my battery location is in an old bulk head in our basement. So concrete walls and floor. Over the winter the lowest it got down to is high 30s.. I expect the summer to be in the 60s.
Do you know what the temp ranges are within the cabin? Earth is your friend and has a constant temp. throughout the year. So if your system location can leverage that, ex. installed in a basement / crawlspace I would imagine you could limit the exposure to extreme low temps.. I would tend to agree with your battery guy since these were designed to live in a car but I would personally do more research. I would try your BMS contact since I believe he is in Canada and may have personal insight (I think Bob also has a Volt setup).
BMS - As mentioned I purchased a BMS unit but have held off based on what I have encountered with other installs and my own setup. I have read some horror stories related to BMS fails, i.e. resisters failing and causing an over charge or the opposite and cells being drained. There are also the BMS successes, but ones that I come across seem to be related to other cell types (18650/tesla cells, chinese lipo packs, etc.) For now I am doing a "wait and see" and will probably hook up the BMS and use it as a battery monitoring system vs. battery management system.
Good luck
-
Being the Victron controller has a fixed one hour absorption or 2 amps before transition to float, dose the transition occur sooner than 1 hour, by becoming saturated at the voltage setpoint and the current drops below 2A?
@nobadays The attached pdf is where I discovered the settings, they appear to be working well, naturally if one was to use them as a starting point with NMC, the voltages would need to be adjusted.
1500W, 6× Schutten 250W Poly panels , Schneider MPPT 60 150 CC, Schneider SW 2524 inverter, 400Ah LFP 24V nominal battery with Battery Bodyguard BMS
Second system 1890W 3 × 300W No name brand poly, 3×330 Sunsolar Poly panels, Morningstar TS 60 PWM controller, no name 2000W inverter 400Ah LFP 24V nominal battery with Daly BMS, used for water pumping and day time air conditioning.
5Kw Yanmar clone single cylinder air cooled diesel generator for rare emergency charging and welding. -
@mcgivor Yes. The 1hr is not fixed but ranges between 60mins to as low as 37mins but on average it has been 45mins. or more for that stage.
-
@BB. I had read "somewhere" that with Lithium that you did exactly that.... "fill'um up shut it off". But it appears this is not the case for the newer Lithium chemistry....
@solardad Wow, one hour seems like a long time to hold at absorption.... do see in your answer to mcgivor that this time period varies, but this is quite a contrast to mcgivor's 6 minutes.... Yes, good idea to contact Kelvin at bobolink he should have experience with cold temps. He might also lend insight on settings though I think he uses Victron equipment as well.
@mcgivor Thank you for this piece of information.... I had downloaded that at one time but must have deleted it... now I can add this to the mix. Here is another interesting pdf from Morningstar: https://2n1s7w3qw84d2ysnx3ia2bct-wpengine.netdna-ssl.com/wp-content/uploads/2018/04/Lithium-Iron-Phosphate-LiFePO4-Generic-Charge-Settings.pdf not the same chemistry as mine but good info.
I think I will contact my "battery guy" to see how long he holds at absorption, maybe even get a list of his settings. His system has been running these modules for over two years.
Thank you!
-
The absorption time is probably irrelevant for the most part, after all the settings are just to fool a controller into doing what it was not primarily designed to do, which is to charge lead acid batteries. Using the Victron example the absorption is essentially just a holding voltage until the time expires or the current drops, the time taken would probably be dependent on loads, without which it would would be reduced.
It's important to remember the capacity difference is minor when charging to the safe zone, right before or at the knee, an interesting point with reference to the Simpliphi example regards the warranty, a 1.6V difference changes the warranty by 50%. 1.6V may seem trivial but when translated to the cellular level, it becomes more relevant.
The cellular voltage is really what should be discussed because it's all about milivolts with lithium, which are sensitive at such seemingly small values, which exemplifies the need for accurate instrumentation to measure such values reliability.
1500W, 6× Schutten 250W Poly panels , Schneider MPPT 60 150 CC, Schneider SW 2524 inverter, 400Ah LFP 24V nominal battery with Battery Bodyguard BMS
Second system 1890W 3 × 300W No name brand poly, 3×330 Sunsolar Poly panels, Morningstar TS 60 PWM controller, no name 2000W inverter 400Ah LFP 24V nominal battery with Daly BMS, used for water pumping and day time air conditioning.
5Kw Yanmar clone single cylinder air cooled diesel generator for rare emergency charging and welding. -
@mcgivor wrt absorption, agree. knowing that that these batteries can take a fast charge with little issues i don't think that phase matters much. the only time it may is given the relative C rate. I have read there is some benefit to have the last 10-15% of the charge to be at a lower rate. Also agree the focus should be at the cell level and not pack. Volt is rated down to 3v but the reported knee/drop off in performance is at 3.5v. Also Gen1 vs Gen 2 packs are slightly different at the top end I have read, Gen1 is 4.15v vs 4.2v for Gen2.
As an aside, a challenge that I have is related to the accuracy of meters / BMSs reading Volts. Interesting video of a Chevy Volt user testing 3 or 4 meters and the differences they exhibited in measuring a cell voltage. They differed enough that it makes me shudder at managing with an inaccurate value when the overall battery bank is already in balance. Have you come across this scenario?
PT1 - https://youtu.be/1Gy2QvFinKQ
PT2 - https://youtu.be/rSJX2ohggrg
@nobadays There maybe others out there with your scenario but I recall seeing an old thread with Kelvin did a Volt setup for his cabin that was used only part time. And being in Canada I assume it would be cold... ;-)
Here is another Volt user that maybe worth asking how they contended with the cold: https://www.youtube.com/watch?v=yCudeUYf52Q
-
@solardad The quality of the meter largely determines the accuracy, my two Fluke 179 meters measure very close to one another +/- 3mA, the Fluke 12, which is much less expensive is about 5mA off the 179 readings. Some cheap meters may have an accuracy of 2% or worse, the Fluke 179 is 0.09% +2, the Fluke 12 is 0.9%+1. Understandably not everyone can justify $350 for a meter but it's worth checking the specifications before purchasing. The BMS displayed voltage concur with my meters most of the time, but never > or <10mA.
@nobadays s The "filling them up then stop" is when the batteries are simply being charged for use at a later time, such as in EV applications. This was a subject that many had opinions on, some saying the controller needs to be shut down by some means of communication or physical disconnect. This is not the case as the controller can be programmed to reduce voltage to a value which is neither charging nor dischargeing (float) allowing loads to take advantage of surplus energy, as @BB. stated.
1500W, 6× Schutten 250W Poly panels , Schneider MPPT 60 150 CC, Schneider SW 2524 inverter, 400Ah LFP 24V nominal battery with Battery Bodyguard BMS
Second system 1890W 3 × 300W No name brand poly, 3×330 Sunsolar Poly panels, Morningstar TS 60 PWM controller, no name 2000W inverter 400Ah LFP 24V nominal battery with Daly BMS, used for water pumping and day time air conditioning.
5Kw Yanmar clone single cylinder air cooled diesel generator for rare emergency charging and welding. -
@solardad Thanks for the Youtube link... I have seen this and the system he has was purchased from Bobolink Solar/Kelvin. I think it might be wise to contact him and Kelvin for my concerns about freezing temps and charging.
I think between you, Micgivor and the reading you both have supplied I'v got a pretty good idea of how to set up the CC/Inv-chrgr. Thank you!
@mcgivor As you mention... the cellular voltage appears to be the key factor in long life for these modules. The reason I sprung for the BMS. My battery guy said I should check each cell about once a week for a few weeks to make sure they are staying in balance but could go to every few weeks if they appear to be stable. Although I will likely check them often for awhile I really felt the BMS was my best option for an "install and relax" system. I didn't go with FLA because I didn't want to be fiddling with them all the time...plus I figured I would kill them because I would forget to fiddle with them.
That makes sense about the "filling them up then stop" and about the float charging. I'm not sure how much usage we will even have during the day. We have been discussing that...talking about using heavy usage appliances during the middle of the day after the batteries are full. I do worry a bit about where the excess power will/should go during the day if we are not using it. I have read of people diverting to loads like water heaters or electric heaters to burn off the excess power.... is this necessary??
-
Remember with many BMS systems, thet have a ballance feature, the ballancing is only done in the upper voltage regon, something the controller settings would avoid. Many EV operators bottom ballance rather than top ballance, because running out of energy, is more important than reaching maximum saturation, in reality there is little capacity above the knee in the charging curve.
Often I wonder if achieving perfect ballance in an offgrid application is actually that nessersary, primarily because operating within the "safe" zone there is no venturing into the upper or lower limits, understandably is better to choose one or the other because it's not possible to have both. Personally I top ballanced initially because my BMS has top ballancing with a voltage of 3.600 VPC , when the controller is set to this value, the BMS allows 75mA of current to perform the ballance. After 6 months without BMS ballance the cells were amazingly close when actually performed.
Knowing where the cells were balanced initially, top or bottom, may or may not be a factor as long as they are balanced somewhere, because in reality it doesn't matter, pragmatically speaking, we aren't going there, in the safe zone.
Please understand I do not claim to be an expert, just sharing information gathered, one thing I can share is that in higher temperatures, >35°C the batteries are far superior to LA, which inherently manifest temperature to the point of diminished return in their life expectancy. Lifepo4 do not exhibit such traits, maintaining a much more constant temperature, probably due to efficiency and I would assume it translates to other lithium chemistries. Cold it something I have never experienced, so no comment with that regard.
1500W, 6× Schutten 250W Poly panels , Schneider MPPT 60 150 CC, Schneider SW 2524 inverter, 400Ah LFP 24V nominal battery with Battery Bodyguard BMS
Second system 1890W 3 × 300W No name brand poly, 3×330 Sunsolar Poly panels, Morningstar TS 60 PWM controller, no name 2000W inverter 400Ah LFP 24V nominal battery with Daly BMS, used for water pumping and day time air conditioning.
5Kw Yanmar clone single cylinder air cooled diesel generator for rare emergency charging and welding. -
@mcgivor I really can't tell for sure from the description of the Red Wing BMS but from what I read there this BMS is designed to balance them once the cells by transfering energy between cells... if a cell is high it transfers energy to another cell that is low. So rather than just "burning off" excess voltage on the high end it actively monitors and transfers voltage back and forth between all of the cells in the pack. Here is a link to the description https://bobolinksolar.com/product/redwing-lithium-bms/ you likely will understand far better than I do.
It does seem like as long as we steer clear of the max/min per cell voltages it would be hard to stress these modules too badly. But everything I read says keeping them balanced is key for longevity.
Categories
- All Categories
- 229 Forum & Website
- 137 Solar Forum News and Announcements
- 1.4K Solar News, Reviews, & Product Announcements
- 199 Solar Information links & sources, event announcements
- 898 Solar Product Reviews & Opinions
- 256 Solar Skeptics, Hype, & Scams Corner
- 22.5K Solar Electric Power, Wind Power & Balance of System
- 3.5K General Solar Power Topics
- 6.7K Solar Beginners Corner
- 1K PV Installers Forum - NEC, Wiring, Installation
- 2.1K Advanced Solar Electric Technical Forum
- 5.6K Off Grid Solar & Battery Systems
- 428 Caravan, Recreational Vehicle, and Marine Power Systems
- 1.1K Grid Tie and Grid Interactive Systems
- 654 Solar Water Pumping
- 816 Wind Power Generation
- 624 Energy Use & Conservation
- 619 Discussion Forums/Café
- 312 In the Weeds--Member's Choice
- 75 Construction
- 124 New Battery Technologies
- 108 Old Battery Tech Discussions
- 3.8K Solar News - Automatic Feed
- 3.8K Solar Energy News RSS Feed