Solar + Hydropower + Inductive diversion load
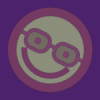
Hi all,
I've been asked by a neighbour to help with designing/setting up his new off-grid setup. The main power source will be solar through an MPPT controller into a decent sized battery bank. In addition he has a small wind turbine which has it's own controller and he has also been given a "Stream Engine" micro-hydro turbine.
He has an intermittently refilled large water storage reservoir up the hill (topped up once a week in the summer) from which he can bring down water for hydro + then irrigation. Since there's a finite supply of water at some times of year, the idea occurred to us that the ideal diversion load would be a pump to send water back up the hill during the later part of summer days so that the turbine could run at night to generate power once the sun went in. There are some large scale hydro plants that act as giant batteries on this basis, so it would be cool to do something similar.
The issue I've hit is that almost everything I've read suggests that the only really effective way to co-ordinate such a diversion load with an MPPT solar controller is to use a 100% resistive load that is progressively phased in with PWM via an SSR in order to maintain desired voltages. My Outback FM80 could do this, for example. That's obviously not going to work for a pump, however.
Is there a better way of approaching this that won't fall foul of the problems involved with suddenly cutting in a large load and pulling the rest of the system out of the desired charge stage?
Thanks in advance for any suggestions!
Comments
-
Using PWM on an induction motor is probably not a great idea. At best, as you do PWM, it creates more "frequencies" (not pure 60 Hz sine wave anymore). Generally, these higher frequencies cause circulating current in the field pieces in the induction motor (and in the rotor) and the only place for this energy to go is I^2*R heating (motor runs hot, additional frequencies can cause early motor failure through heat and possible vibrations).
Better just to turn motor on for X minutes and off for Y minutes--I would suggest.
-Bill
If you want to see how your pump would behave with PWM, just get a standard PWM dimmer and wire it to your motor, and see how it behaves.
-BB
Near San Francisco California: 3.5kWatt Grid Tied Solar power system+small backup genset -
Yes, I am aware of how undesirable PWM on an induction motor is - that was my reason for posting! My concern is that just "turning the motor on for a few minutes" is not going to play nicely with the solar charge controller. I've seen lots of others here and on other forums talking about problems with dump loads where they either don't kick in soon enough to be useful, or they repeatedly drop the rest of the system out of absorb/float when the dump load pulls the battery voltage down too suddenly.
Outback VFX3048E, Outback FM80, Outback FNDC, Outback Mate3, Outback Hub4, 15x Munchen 250W panels (5x3), 8 x Rolls S605 (48V system) -
I'd say run the pump whenever the battery is in FLOAT. If the controller cannot produce enough power (say at 4pm) and it drops out of float , cut the pump
You need to run the pump from a Pure sine inverter, or a VFD that can be controlled by the controller.
But the real flaw in the plan, is the amount of water, head and flow rate. To get usable power, you will empty the tank in about an hour, and take 9 hrs to pump it back up. Do those calculations FIRST before going further. Utility scale hydro plants don'scale down well to homeowner size
Powerfab top of pole PV mount | Listeroid 6/1 w/st5 gen head | XW6048 inverter/chgr | Iota 48V/15A charger | Morningstar 60A MPPT | 48V, 800A NiFe Battery (in series)| 15, Evergreen 205w "12V" PV array on pole | Midnight ePanel | Grundfos 10 SO5-9 with 3 wire Franklin Electric motor (1/2hp 240V 1ph ) on a timer for 3 hr noontime run - Runs off PV ||
|| Midnight Classic 200 | 10, Evergreen 200w in a 160VOC array ||
|| VEC1093 12V Charger | Maha C401 aa/aaa Charger | SureSine | Sunsaver MPPT 15A
solar: http://tinyurl.com/LMR-Solar
gen: http://tinyurl.com/LMR-Lister , -
My concern here is that by the latter part of the absorb charge, the turbine is going to be generating more power than the batteries need - and my understanding was that without a properly "graduated" dump load this has the potential to shorten the life of the turbine. I guess the other option is to look at an electrically actuated valve to cut off the water to the turbine - perhaps only running it at night to avoid this problem - but then we'll probably have fun with water hammer!
As concerns the efficiency question, there is no requirement to pump back the same amount of water back up as came down. The reservoir is several hundred thousand litres and is refilled once a week. Pumping *some* water back up the hill - however little that is - is just a more useful application of the excess power than putting into a resistive load - particularly since this is most likely to be an issue in the summer, where there is no requirement for any more heat in these parts! But if it turns out to be massively more complex and expensive than just dumping the extra power as heat, we may not bother - that's what I'm trying to explore now.
Are there PWM controlled VFDs that could credibly run a high head, low flow pump? I'm wondering if it's possible to use a standard SSR diversion load signal from the solar CC to control a pump with such a device - I guess the power draw wouldn't be directly proportional to the pump speed, but hopefully better than just "on" or "off"!
Outback VFX3048E, Outback FM80, Outback FNDC, Outback Mate3, Outback Hub4, 15x Munchen 250W panels (5x3), 8 x Rolls S605 (48V system)
Categories
- All Categories
- 228 Forum & Website
- 136 Solar Forum News and Announcements
- 1.4K Solar News, Reviews, & Product Announcements
- 199 Solar Information links & sources, event announcements
- 898 Solar Product Reviews & Opinions
- 256 Solar Skeptics, Hype, & Scams Corner
- 22.5K Solar Electric Power, Wind Power & Balance of System
- 3.5K General Solar Power Topics
- 6.7K Solar Beginners Corner
- 1K PV Installers Forum - NEC, Wiring, Installation
- 2.1K Advanced Solar Electric Technical Forum
- 5.6K Off Grid Solar & Battery Systems
- 428 Caravan, Recreational Vehicle, and Marine Power Systems
- 1.1K Grid Tie and Grid Interactive Systems
- 654 Solar Water Pumping
- 816 Wind Power Generation
- 624 Energy Use & Conservation
- 619 Discussion Forums/Café
- 312 In the Weeds--Member's Choice
- 75 Construction
- 124 New Battery Technologies
- 108 Old Battery Tech Discussions
- 3.8K Solar News - Automatic Feed
- 3.8K Solar Energy News RSS Feed