Boost charge question
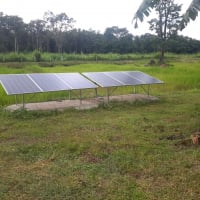
mcgivor
Solar Expert Posts: 3,854 ✭✭✭✭✭✭
Regarding setting a CC to have a higher bulk voltage than absorbtion, the manual for the Schneider 60 -150 MPPT states that it is advantageous to do so in an off grid cyclical application, the raised voltage is held for one hour before dropping back down. This makes sense in that it will stir the electrolyte and prevent sulfation, albeit at the cost of water loss. The battery manufacturer gives no mention of charging voltages other than to state the equalized voltage for 24V nominal is 28.8V, which where I currently have the bulk/absorbtion set. So the question is what would a reasonable setting be for the boost charge? Battery is FLA.
1500W, 6× Schutten 250W Poly panels , Schneider MPPT 60 150 CC, Schneider SW 2524 inverter, 400Ah LFP 24V nominal battery with Battery Bodyguard BMS
Second system 1890W 3 × 300W No name brand poly, 3×330 Sunsolar Poly panels, Morningstar TS 60 PWM controller, no name 2000W inverter 400Ah LFP 24V nominal battery with Daly BMS, used for water pumping and day time air conditioning.
5Kw Yanmar clone single cylinder air cooled diesel generator for rare emergency charging and welding.
Second system 1890W 3 × 300W No name brand poly, 3×330 Sunsolar Poly panels, Morningstar TS 60 PWM controller, no name 2000W inverter 400Ah LFP 24V nominal battery with Daly BMS, used for water pumping and day time air conditioning.
5Kw Yanmar clone single cylinder air cooled diesel generator for rare emergency charging and welding.
Comments
-
Generally, the Bulk phase of the charge cycle is called the "constant current" phase because the charging source is running at maximum current and/or the battery bank is sucking up everything being fed to it - at that voltage. Raising the voltage will simply drive the battery to pull more current, assuming that it is available from the source.
In a classic "low battery" scenario, the starting voltage is lower than set point at the beginning of the charge cycle because the batteries are demanding more current than the system can supply. The charging system modulates the voltage to maintain the current. The charging voltage gradually climbs to reach the desired set point as the battery accepts the charge. The transition from Bulk to Absorb isn't a "switch", it is simply the point where the output voltage reached design output and the current draw of the batteries begins to drop.
Of course if the charging capacity of the system is large compared to the battery bank, or the batteries are only mildly discharged - the Bulk and Absorb phases operate the same way.
So, assuming you have the charging capacity available, raising the Bulk voltage will increase the charging current and reduce the charging time. Then dropping back to the 28.8v will allow the batteries to slowly absorb the final charge. The actual voltage setting for the boost will depend upon how hard you are intending to push the batteries.
Some people use a "finishing charge" at 29.6v when the batteries approach full charge instead of boost at the beginning. I suggest working with your battery manufacturer to determine what is optimum for their product.
I always have more questions than answers. That's the nature of life. -
The boost charging I'm used to is on forklift traction batteries.
No voltage specs just keep it under 20% to 25% of the name plate amp hours and stop charging if the battery gets near 110°F or starts off gassing.
I think you generally want to keep the volts under equalizationSolar hybrid gasoline generator, 7kw gas, 180 watts of solar, Morningstar 15 amp MPPT, group 31 AGM, 900 watt kisae inverter.
Solar roof top GMC suburban, a normal 3/4 ton suburban with 180 watts of panels on the roof and 10 amp genasun MPPT, 2000w samlex pure sine wave inverter, 12v gast and ARB air compressors.
-
Marc Kurth said:Generally, the Bulk phase of the charge cycle is called the "constant current" phase because the charging source is running at maximum current and/or the battery bank is sucking up everything being fed to it - at that voltage. Raising the voltage will simply drive the battery to pull more current, assuming that it is available from the source.
In a classic "low battery" scenario, the starting voltage is lower than set point at the beginning of the charge cycle because the batteries are demanding more current than the system can supply. The charging system modulates the voltage to maintain the current. The charging voltage gradually climbs to reach the desired set point as the battery accepts the charge. The transition from Bulk to Absorb isn't a "switch", it is simply the point where the output voltage reached design output and the current draw of the batteries begins to drop.
Of course if the charging capacity of the system is large compared to the battery bank, or the batteries are only mildly discharged - the Bulk and Absorb phases operate the same way.
So, assuming you have the charging capacity available, raising the Bulk voltage will increase the charging current and reduce the charging time. Then dropping back to the 28.8v will allow the batteries to slowly absorb the final charge. The actual voltage setting for the boost will depend upon how hard you are intending to push the batteries.
Some people use a "finishing charge" at 29.6v when the batteries approach full charge instead of boost at the beginning. I suggest working with your battery manufacturer to determine what is optimum for their product.
The maximum recommended charge current is 25A per battery , there are 2 strings parallel, the maximum charge current is set at 30A, 15A per string, given that this current is not exceed, raising the voltage would be a sort of be a mild equalization without dumping the maximum current the array can supply into the battery. This setting is about 12% of the capacity of the battery, so limiting the current and raising the voltage should be benificial in that it stirs the electrolyte without overcharging, being that this "boost" is limited to one hour, my assumption is that the voltage would be slightly higher, not at equalization voltage, say in the mid 29v range. The manufacturer offers no information regarding such settings, the only voltage stated is the equalized voltage, float and equalization are dependent on the charger. See attached Pdf, Battery is EB 1301500W, 6× Schutten 250W Poly panels , Schneider MPPT 60 150 CC, Schneider SW 2524 inverter, 400Ah LFP 24V nominal battery with Battery Bodyguard BMS
Second system 1890W 3 × 300W No name brand poly, 3×330 Sunsolar Poly panels, Morningstar TS 60 PWM controller, no name 2000W inverter 400Ah LFP 24V nominal battery with Daly BMS, used for water pumping and day time air conditioning.
5Kw Yanmar clone single cylinder air cooled diesel generator for rare emergency charging and welding. -
So with the "boost" charge, it would go something like:
Bulk- 3 hours at max 30a until voltage gets to eg. 30v.
Boost- 1 hour held at 30v with tapering current
Rest- however long it takes with no current for voltage to drop to 28.8v
Absorb- tapering current to set EndAmps or TimeOut.
IMHO it would be better to get batteries charged then do EQ if needed. They would be only part charged after boost phase and might take a while to drop to Vabsorb and start charging again, and may not finish before dark. I'm not sure what the advantage is of doing the sort-of-EQ before absorb is, or of doing it daily.Off-grid.
Main system ~4kw panels into 2xMNClassic150 370ah 48v bank 2xOutback 3548 inverter 120v + 240v autotransformer
Night system ~1kw panels into 1xMNClassic150 700ah 12v bank morningstar 300w inverter -
Estragon said:So with the "boost" charge, it would go something like:
Bulk- 3 hours at max 30a until voltage gets to eg. 30v.
Boost- 1 hour held at 30v with tapering current
Rest- however long it takes with no current for voltage to drop to 28.8v
Absorb- tapering current to set EndAmps or TimeOut.
IMHO it would be better to get batteries charged then do EQ if needed. They would be only part charged after boost phase and might take a while to drop to Vabsorb and start charging again, and may not finish before dark. I'm not sure what the advantage is of doing the sort-of-EQ before absorb is, or of doing it daily.1500W, 6× Schutten 250W Poly panels , Schneider MPPT 60 150 CC, Schneider SW 2524 inverter, 400Ah LFP 24V nominal battery with Battery Bodyguard BMS
Second system 1890W 3 × 300W No name brand poly, 3×330 Sunsolar Poly panels, Morningstar TS 60 PWM controller, no name 2000W inverter 400Ah LFP 24V nominal battery with Daly BMS, used for water pumping and day time air conditioning.
5Kw Yanmar clone single cylinder air cooled diesel generator for rare emergency charging and welding. -
At my latitude I get to float at about the same time in summer, but not in fall/winter so that would be an issue for me, but not you. My batteries seem to bubble pretty well at Vabsorb and EQing as needed (roughly every 3mos) seems to be working.
Assuming the boost stage is temp compensated and voltage not too high, I guess it wouldn't hurt to enable boost. Might mean fewer EQs?Off-grid.
Main system ~4kw panels into 2xMNClassic150 370ah 48v bank 2xOutback 3548 inverter 120v + 240v autotransformer
Night system ~1kw panels into 1xMNClassic150 700ah 12v bank morningstar 300w inverter -
Estragon said:At my latitude I get to float at about the same time in summer, but not in fall/winter so that would be an issue for me, but not you. My batteries seem to bubble pretty well at Vabsorb and EQing as needed (roughly every 3mos) seems to be working.
Assuming the boost stage is temp compensated and voltage not too high, I guess it wouldn't hurt to enable boost. Might mean fewer EQs?1500W, 6× Schutten 250W Poly panels , Schneider MPPT 60 150 CC, Schneider SW 2524 inverter, 400Ah LFP 24V nominal battery with Battery Bodyguard BMS
Second system 1890W 3 × 300W No name brand poly, 3×330 Sunsolar Poly panels, Morningstar TS 60 PWM controller, no name 2000W inverter 400Ah LFP 24V nominal battery with Daly BMS, used for water pumping and day time air conditioning.
5Kw Yanmar clone single cylinder air cooled diesel generator for rare emergency charging and welding. -
At 40C plus, you would have to put ME in the water bath. At -40C like we occasionally get, we can dress for it.Off-grid.
Main system ~4kw panels into 2xMNClassic150 370ah 48v bank 2xOutback 3548 inverter 120v + 240v autotransformer
Night system ~1kw panels into 1xMNClassic150 700ah 12v bank morningstar 300w inverter -
Estragon said:At 40C plus, you would have to put ME in the water bath. At -40C like we occasionally get, we can dress for it.
You drink about 10 liters of water per day and don't visit the bathroom much, so you are in a constant water bath, so to speak, lived in Northern Canada, the cold is dry cold but I'm a tropical person and prefer the heat, you acclimatize, overall its cheaper in the tropics, less clothing, no heating and you can grow food all year, I'm not only off grid but 80% self sufficient and working towards 100%.1500W, 6× Schutten 250W Poly panels , Schneider MPPT 60 150 CC, Schneider SW 2524 inverter, 400Ah LFP 24V nominal battery with Battery Bodyguard BMS
Second system 1890W 3 × 300W No name brand poly, 3×330 Sunsolar Poly panels, Morningstar TS 60 PWM controller, no name 2000W inverter 400Ah LFP 24V nominal battery with Daly BMS, used for water pumping and day time air conditioning.
5Kw Yanmar clone single cylinder air cooled diesel generator for rare emergency charging and welding. -
mcgivor said:
You drink about 10 liters of water per day and don't visit the bathroom much, so you are in a constant water bath, so to speak, lived in Northern Canada, the cold is dry cold but I'm a tropical person and prefer the heat, you acclimatize, overall its cheaper in the tropics, less clothing, no heating and you can grow food all year, I'm not only off grid but 80% self sufficient and working towards 100%.
I always have more questions than answers. That's the nature of life. -
I have a Schneider controller with boost capability. Since I'm not looking to do a mini-EQ on a daily basis which the boost function is capable of yet still appreciate the benefits of a tiny electrolyte stir regularly I just set my boost voltage .1v higher than my absorb. I suspect going .2v higher wouldn't hurt a bit. I would not suggest getting anywhere close to EQ voltages if you use the boost feature.
The way I look at it since charging heats the batteries you get a little extra electrolyte stir before the batteries get warm as they do further into the absorb cycle.Conext XW6848 with PDP, SCP, 80/600 controller, 60/150 controller and Conext battery monitor
21 SW280 panels on Schletter ground mount
48v Rolls 6CS 27P
-
WaterWheel said:I have a Schneider controller with boost capability. Since I'm not looking to do a mini-EQ on a daily basis which the boost function is capable of yet still appreciate the benefits of a tiny electrolyte stir regularly I just set my boost voltage .1v higher than my absorb. I suspect going .2v higher wouldn't hurt a bit. I would not suggest getting anywhere close to EQ voltages if you use the boost feature.
The way I look at it since charging heats the batteries you get a little extra electrolyte stir before the batteries get warm as they do further into the absorb cycle.1500W, 6× Schutten 250W Poly panels , Schneider MPPT 60 150 CC, Schneider SW 2524 inverter, 400Ah LFP 24V nominal battery with Battery Bodyguard BMS
Second system 1890W 3 × 300W No name brand poly, 3×330 Sunsolar Poly panels, Morningstar TS 60 PWM controller, no name 2000W inverter 400Ah LFP 24V nominal battery with Daly BMS, used for water pumping and day time air conditioning.
5Kw Yanmar clone single cylinder air cooled diesel generator for rare emergency charging and welding.
Categories
- All Categories
- 229 Forum & Website
- 137 Solar Forum News and Announcements
- 1.4K Solar News, Reviews, & Product Announcements
- 199 Solar Information links & sources, event announcements
- 898 Solar Product Reviews & Opinions
- 256 Solar Skeptics, Hype, & Scams Corner
- 22.5K Solar Electric Power, Wind Power & Balance of System
- 3.5K General Solar Power Topics
- 6.7K Solar Beginners Corner
- 1K PV Installers Forum - NEC, Wiring, Installation
- 2.1K Advanced Solar Electric Technical Forum
- 5.6K Off Grid Solar & Battery Systems
- 428 Caravan, Recreational Vehicle, and Marine Power Systems
- 1.1K Grid Tie and Grid Interactive Systems
- 654 Solar Water Pumping
- 816 Wind Power Generation
- 624 Energy Use & Conservation
- 619 Discussion Forums/Café
- 312 In the Weeds--Member's Choice
- 75 Construction
- 124 New Battery Technologies
- 108 Old Battery Tech Discussions
- 3.8K Solar News - Automatic Feed
- 3.8K Solar Energy News RSS Feed