Installing a 24 volt dc wind generator to 24 volt batteries
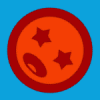
bergy
Registered Users Posts: 1 ✭
Hi, i have bitten off more than i can chew,and are seeking some guidance
I have recently installed a offgrid solar systen to my home, i installed 3 * 250 watt panels connected to a 2.4 kw off grid inverter.It worked so well i thought i would add a wind turbine to increase the system size (why didn't i just add more solar panes )
I purchased a 2.0 kw Eolo vertical axis wind tower rated at 24 volt dc output current max 60 watt max voltage 36v.
I also purchased a 24 volt controller and a 700watt heater to use as a heat sink.
Now my issue is how to connect all of this and get it to work.
Do i need a rectifier ? Do i connect the wind generator to the 24 volt batteries direct.before the controller.
I am confused .
The wires out of the wind generator seem very small considering the output of 1500 watts at 36 volt and 60 amp.
Any advise would be appreciated.
Thanks
I have recently installed a offgrid solar systen to my home, i installed 3 * 250 watt panels connected to a 2.4 kw off grid inverter.It worked so well i thought i would add a wind turbine to increase the system size (why didn't i just add more solar panes )
I purchased a 2.0 kw Eolo vertical axis wind tower rated at 24 volt dc output current max 60 watt max voltage 36v.
I also purchased a 24 volt controller and a 700watt heater to use as a heat sink.
Now my issue is how to connect all of this and get it to work.
Do i need a rectifier ? Do i connect the wind generator to the 24 volt batteries direct.before the controller.
I am confused .
The wires out of the wind generator seem very small considering the output of 1500 watts at 36 volt and 60 amp.
Any advise would be appreciated.
Thanks
Comments
-
Wind generation (and hydro ) has its own set of complications, unlike solar which a regular charge controller can simply disconnect when batteries are fully charged, a wind turbine still needs to have a load to prevent over speeding. The method used is to divert the energy to a suitable load bank using a charge controller with diversion control. The load must be carefully sized, neither too small or too large to prevent damage to the controller or the generation source.
Although I've no practical experience with wind generation, during my considerations I researched all avenues and decided solar alone would be the least complicated. My controller a Morningstar TS 60 is capable of diversion and the manual goes into detail of how to size the diversion load, the manual can be downloaded from their Web site should you need to educate yourself and there are numerous Web sites dealing with this subject which can be resourceful.
Read all you can as a forum such as this cannot, in my opinion, cover all the details but is an excellent place to get pointed in the right direction and get information from others experiences.
1500W, 6× Schutten 250W Poly panels , Schneider MPPT 60 150 CC, Schneider SW 2524 inverter, 400Ah LFP 24V nominal battery with Battery Bodyguard BMS
Second system 1890W 3 × 300W No name brand poly, 3×330 Sunsolar Poly panels, Morningstar TS 60 PWM controller, no name 2000W inverter 400Ah LFP 24V nominal battery with Daly BMS, used for water pumping and day time air conditioning.
5Kw Yanmar clone single cylinder air cooled diesel generator for rare emergency charging and welding. -
Ok... Welcome to the forum Bergy.
And details matter here... Is this the turbine setup you have?:
http://www.lmagency.biz/contents/en-uk/p76.html
In general, Vertical Axis Wind Turbines (VAWT) do not need a diversion controller to maintain maximum blade RPM (they tend to be self limiting). I did not find a manual for this unit--So if you have a link, it would be helpful.
Assuming they system is rated for use with a diversion controller, generally, they are rated for the maximum output of the wind turbine--So a 700 Watt load bank seems to be a little small... Unless you have brakes or other speed ;limiting/shutdown mechanism (I did not see any in the specs I found).
To be honest, most VAWT do not output very much power--They are on very short towers and tend not to be too efficient--Especially when mounted low to the ground/near obstructions (such as buildings/trees up wind). It may be worth it to try the turbine and see what kind of output you can get from it--A typical wind turbine just shorts the alternator outputs to shut down the unit when needed (did not see a turbine controller).
Here is a short manual for a similar setup to yours (different turbine design)--But it gives you the basics:
http://www.desertpowerinc.com/pdf/SeaHawkManualNew.pdf
But the short answer is:
Alternator -> 3 phase rectifier -> circuit breaker/fuse -> battery bank +/- bus -> Diversion controller -> heater
Basically the battery is the "heart" of your system. All charging sources and loads connect to the +/- Battery Bus Bars (including the rectifier, you diversion controller, the solar panel charge controller, your AC inverter, etc.).
Every wire that leaves the battery + bus connection, should have a fuse or circuit breaker rated to protect the wires from over current.
One of our posters here has done a very good photographic history of his solar power system (much of it was pure DIY). About 1/2 way down the page on the left are his solar projects.
http://www.2manytoyz.com/
I guess you are in New South Wales Australia?
Personally, I am not a big fan of wind power--You need to live in a pretty windy area (if it is miserably windy, then you can have good wind). And you really need (typically) a tower that is 10-20 meters minimum high to get into non-turbulent air (VAWT do not any better in turbulent air vs horizontal axis wind turbines HAWT).
How tall is your tower, are the prevailing winds side of the installation clear of tall trees and structures?
Personally, I would like to see you get the solar portion of your system up and running first. What size/type battery bank do you have (flooded cell/AGM, how many AH, etc.). What kind of loads do you want to run? How many Watt*Hours per day, etc.
A 2.4 kWatt off grid inverter, to use its full capabilities would need a minimum of ~480 AH @ 24 volt battery bank.
For example using a 480 AH @ 24 volt flooded cell lead acid battery bank, I would suggest a 5% to 13% rate of charge with solar--5% for a weekend/seasonal system. 10%+ rate of charge for a full time off grid system:- 480 AH * 29 volts charging * 1/0.77 panel+controller derating * 0.05 rate of charge = 904 Watt array minimum
- 480 AH * 29 volts charging * 1/0.77 panel+controller derating * 0.10 rate of charge = 1,808 Watt array nominal
- 480 AH * 29 volts charging * 1/0.77 panel+controller derating * 0.13 rate of charge = 2,350 Watt array "cost effective" maximum
http://www.boatus.com/boattech/articles/choosing-cables-and-terminals.asp
http://www.engineeringtoolbox.com/awg-wire-gauge-d_731.html
10 AWG is ~2.59 mm in diameter (I am in the US, I do not work with metric wire sizes). There is also a conversion of 3 phase to 1 phase wiring (three phase wiring would be less than 60 Amps per wire before the rectifier).
In general, for a reliable system, I would be suggesting a much more conservative wiring for your connection back to the battery bank. The US National Electric Code would suggest (60 amps * 1.25 NEC derating = 75 amps continuous load rating wire wiring/breakers/etc.):
https://lugsdirect.com/WireCurrentAmpacitiesNEC-Table-301-16.htm
Would be around 4-2 AWG wiring depending on insulation type (4 AWG ~ 5.19 mm dia of copper wire).
Anyway--None of the above is a suggestion for you to go off and starting wiring up the system--There are a lot of basic design questions and detail that need to be worked out first. If done wrong, it can waste a bunch of your time and money, and can injure somebody, start a fire, or worse.
Assuming you are in Australia.. You need to work with materials/equipment available to your and compliant with your safety codes.
-Bill
Near San Francisco California: 3.5kWatt Grid Tied Solar power system+small backup genset - 480 AH * 29 volts charging * 1/0.77 panel+controller derating * 0.05 rate of charge = 904 Watt array minimum
Categories
- All Categories
- 229 Forum & Website
- 137 Solar Forum News and Announcements
- 1.4K Solar News, Reviews, & Product Announcements
- 199 Solar Information links & sources, event announcements
- 898 Solar Product Reviews & Opinions
- 256 Solar Skeptics, Hype, & Scams Corner
- 22.5K Solar Electric Power, Wind Power & Balance of System
- 3.5K General Solar Power Topics
- 6.7K Solar Beginners Corner
- 1K PV Installers Forum - NEC, Wiring, Installation
- 2.1K Advanced Solar Electric Technical Forum
- 5.6K Off Grid Solar & Battery Systems
- 428 Caravan, Recreational Vehicle, and Marine Power Systems
- 1.1K Grid Tie and Grid Interactive Systems
- 654 Solar Water Pumping
- 816 Wind Power Generation
- 624 Energy Use & Conservation
- 619 Discussion Forums/Café
- 312 In the Weeds--Member's Choice
- 75 Construction
- 124 New Battery Technologies
- 108 Old Battery Tech Discussions
- 3.8K Solar News - Automatic Feed
- 3.8K Solar Energy News RSS Feed