Automotive alternator as a maintenance charger for my battery bank?
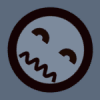
My solar equipment:
(2) 100w 12v solar panels
A basic PWM charge controller
(2) Deka 8C6V batteries configured for 12v (330@20AH)
This little system supplies all my daily living electrical needs. Mostly for my LED lights and RV style forced air furnace.
Until now I've used an old Honda EM500 generator as stand alone power for my daily hours of wireless internet surfing and satellite TV. On average 5 hours a day and a half gallon of gas.
My current problem:
Recently the genset on the generator has started failing and I no longer can trust it to put out a steady 120VAC @ 60Hz.
This Honda generator is old enough that replacement parts are pretty much unavailable. However, the little engine is still in great shape and I've grown very fond of it only using a half gallon of gas a day. Using some basic formulas I calculate it's probably between 1.6 & 1.75 horsepower. I know this engine has been used in up to 800w generators.
The solution I'm considering:
I know the practical/efficiency reasons why using an automotive alternator to charge discharged batteries isn't the best solution.
... But what about using one to maintain the charge on charged batteries while they are being lightly used?
I have a Delco Remy 105 amp alternator that's been gathering dust. I also have a 1000w pure sine wave inverter.
Originally I was thinking about hooking the alternator up to the engine to power the inverter. (A DIY inverter generator) As before it would be stand alone. This setup should easily supply the less than 500 watts I need to surf the 'net or watch sat. TV.
Then I got to thinking about taking advantage of the extra charging time I could be putting into my batteries.
Currently my batteries get charged all day long from my panels. Then from sundown until sunup they start getting used to run my lights and furnace.
Why not hook the engine/alternator up to my batteries and the inverter off of my batteries? That way the batteries can maintain their charge in the evenings while I watch TV and run my lights and furnace, until I go to bed.
This seems like a simple elegant solution. OR AM I MISSING SOMETHING???
Any constructive feedback would be welcome. Resbum
Comments
-
Should not hurt anything... Just monitor the charging voltage for the battery bank. Automotive alternators generally charge around 13.8 to 14.2 volts or so. Pretty 'soft' charging.
For flooded cell deep cycle batteries, you are correct--It would take many extra hours to get the battery bank charged, and would not be very good for "equalization" charging. But, it won't hurt anything as long as your solar array is charging well.
-Bill
Near San Francisco California: 3.5kWatt Grid Tied Solar power system+small backup genset -
Thanks, Bill. I was pretty sure that was the answer, but wanted to bounce it off of others.
My electrical needs are pretty light, so the panels do a good job of keeping my batteries charged.
The sole goal of doing this isn't even for a net gain, but just to offset any energy used in the early morning or evenings.
Resbum -
Since you are likely using a 3 wire delco SI12 alternator.
There are 2 things you could do to up the volts.
1, hook the alt voltage sense wire up to the battery like its supposed to be. Most people just hook the voltage sense wire up to the alternator, which defeats the purpose of having a voltage sense wire.
2, put a resistor in line with the voltage sense wire.
Solar hybrid gasoline generator, 7kw gas, 180 watts of solar, Morningstar 15 amp MPPT, group 31 AGM, 900 watt kisae inverter.
Solar roof top GMC suburban, a normal 3/4 ton suburban with 180 watts of panels on the roof and 10 amp genasun MPPT, 2000w samlex pure sine wave inverter, 12v gast and ARB air compressors.
-
Hi oil pan, thanks.
The alternator I have is off a 98 Chevy Lumina. A friend gave it to me when he sold the car. I know it's a CS130D. I believe they were a one wire hookup in the Lumina. Not positive. This alternator does have all four pins inside the connector sleeve.
I've seen info about the resistor online, but do you have a recommendation? -
The other thing to keep in mind is the wire length from the alternator to the battery/batteries. You could get a voltage drop there which would slow the charge rate as well, just something else to keep in mind.
You touched on this but you could use the same setup with a regular "car" battery connected to alternator and the inverter to a good charger to push power back in that way, probably less run time if you have a good sized 12v charger (50 amps or so), but more load while it is running. I used to do both these when I had a 12v setup, my problem was the car idling and going the 12v straight route the 25 feet of #2 I lost .4 volts and with a load I could charge about 30 amps while idling and using an inverter jumping it up to 120vac and DLS-55 charger back to 12v I could easily put 55 amps in the batteries the whole time with a LOT smaller wire3kw solar PV, 4 LiFePO4 100a, xw 6048, Honda eu2000i, iota DLS-54-13, Tesla 3, Leaf, Volt, 4 ton horizontal geothermal, grid tied - Green Bay, WI -
Thanks, Brock.
Luckily, I only need about four feet of cable from the engine/alternator to the battery bank.
If the Honda engine was larger I would consider hooking the system up as you describe. Because the engine is less than 2hp my only goal is to replace the energy I'm using at the time. Not get a net gain charge out of it.
Resbum
-
Although I have a back up generator, I built this for fun thinking that it would be quiet. With a 60 amp alternator the engine actually labors pretty hard. Someday I will get a backwards fan from a Corvair so the airflow is correct.
-
1.6HP gives you about 800 watts on electricity, but remember that the alternator is using power for itself when generating power.
What is the max RPM of the old engine?
Many alternators generate closer to their rated power when the car engine runs about 1,200 car engine RPM or higher, which translates to about 3,600 alternator rpm.
Of course every alternator is different and the newer alternators may be better yet.
-
Hi Johann, thanks for the numbers. I was happy to see that your math and specs mirror what I believed them to be.
Anyone please feel free to correct any of assumptions I'm about to make. I know I'm oversimplifying things, but the generalities should be correct.
The Engine:
The manual for the Honda EM500 generator said the operating RPM off the engine is 3600RPM. Most of the small engines that perform in this range have a torque curve that tops out somewhere around 3000RPM.
Very very simplified--- Horsepower is a byproduct of Torque & RPM (ability & time). Torque is the actual measure of an engine's ability to force the connecting rod down after combustion, turning the crankshaft. So, whether it's 3000RPM or 3600RPM, if an engine has the same torque it has the same ability to do work. The reason horsepower goes up after torque levels off is because at 3600RPM the engine can do the same amount of work faster, meaning more work gets done in the same period of time. It has nothing to do with the ability of the engine to do the work at 3000 or 3600RPM. That's why an engine's peak fuel efficiency tends to be around peak torque, not peak horsepower. The reason generators aren't set to operate there is because under a sudden load the engine gets pulled down before the governor can recover. If the engine is pulled down off the torque curve it stalls instead of recovering.
The Alternator:
Here's a performance chart for the 105 amp CS130D alternator.
http://oljeep.com/gw/alt/Alternator_Theory_15a_files/image032.jpg
Here's the page this chart comes from. It's an excellent tutorial on alternator theory. I won't go into another long winded explanation like I did with the engine.
http://oljeep.com/gw/alt/Alternator_Theory.html
Alternators start to lose efficiency where the performance curve starts to level out. Usually around 70% of their rated capacity is when it starts happening faster. That translates into the point where the alternator starts getting harder to turn. In this case that's around 70 amps. By 90 amps it really starts tanking on its efficiency.
That translates to 70 amps = 2000rpm and 90 amps 3000rpm.
My Goals:
I would be happy setting things up so the alternator was only putting out 50 amps. 50a X 14v = 700w. Remember, I'm not looking for a net gain. I just want to offset electrical usage out of my batteries while watching satellite TV or surfing wireless internet. I already know that requires less than 500w.
My plans call for running the engine and alternator 1 to 1. By directly coupling them together, shaft to shaft, I'm also not losing the 5% of power that belts and pulleys suck up.
I can't set the engine RPM too low or it falls off its torque curve. Initially, I'm thinking of starting at 3000RPM. From there I can tweak things.
Since the batteries should be charged up from my solar panels that shouldn't cause a high current draw.
In a rose colored universe I'd be firing this up to a charged battery bank to offset TV and internet power usage, nothing more.
Holy Buckets. I'm sorry to anyone who managed to read to this point. I didn't intend such a long winded post. This kind of turned into me talking my way through what I'm thinking.
Any comments and input is appreciated.
Resbum
-
Resbum said:
Alternators start to lose efficiency where the performance curve starts to level out. Usually around 70% of their rated capacity is when it starts happening faster.
<snip>
My plans call for running the engine and alternator 1 to 1. By directly coupling them together, shaft to shaft, I'm also not losing the 5% of power that belts and pulleys suck up.
--vtMaps
4 X 235watt Samsung, Midnite ePanel, Outback VFX3524 FM60 & mate, 4 Interstate L16, trimetric, Honda eu2000i -
At best, you are probably 50% efficient (engine fuel in to Watts out). If it is easier to belt drive (mounting, issues with flex coupling/momentum impulses, etc.).--Then do the belt thing.
Direct attach between a piston engine and a large rotating mass (alternator)--You can have issues with the coupling tearing itself apart). Of course, the problem is 10x worse with diesel engines (higher compression).
-Bill
Near San Francisco California: 3.5kWatt Grid Tied Solar power system+small backup genset -
Newer gear uses flat serpentine belts, very little power loss in them compared to V belts. And you can play with different size pulleys to get the RPM's set for your application, Automotive alternators generally are pretty high RPM units, Compare pulley sizes next time you are under the hood. Belts are very forgiving compared to direct coupled
Powerfab top of pole PV mount | Listeroid 6/1 w/st5 gen head | XW6048 inverter/chgr | Iota 48V/15A charger | Morningstar 60A MPPT | 48V, 800A NiFe Battery (in series)| 15, Evergreen 205w "12V" PV array on pole | Midnight ePanel | Grundfos 10 SO5-9 with 3 wire Franklin Electric motor (1/2hp 240V 1ph ) on a timer for 3 hr noontime run - Runs off PV ||
|| Midnight Classic 200 | 10, Evergreen 200w in a 160VOC array ||
|| VEC1093 12V Charger | Maha C401 aa/aaa Charger | SureSine | Sunsaver MPPT 15A
solar: http://tinyurl.com/LMR-Solar
gen: http://tinyurl.com/LMR-Lister , -
I think it's a good idea to run with a reduced output like you want to because in real life it will suck up more power from the engine than you think.
The alternator fan will spin backwards pulling hot air from the front toward the electronics in the back. I don't know if anybody makes a reverse fan for a CS alternator. This may not be a problem at reduced outputs.
If the alternator presently uses a V belt, the belt will not match the industrial dimensions that are used for an engine pulley that you would buy. Automotive belts are slightly different than industrial belts.
Since this engine was made to be direct drive, you must find out that shaft dimensions and whether they are tapered or straight to see if a pulley is available. Also, were the engine bearings designed for the side load that the belt tension with place on them. -
Serpentine belts do not appear offer any efficiency improvement over a V-belt in a simple 2 pulley system.
Both serpentine and V-belt share about a 98% efficiency figure.
V-belts pulleys can easily be found in all different sizes and they are cheap.
The myth that serpentine belts are so much efficient seems comes from when you use 1 serpentine belt to replace 3 or 4 V-belts under the hood of a vehicle. Of course the serpentine is going to be more efficient in that situation.
Problem with direct driving the alternator is you will have to run the engine near max RPM to get good power from it. If you over drive the alternator you could run the engine at say 1500 rpm and get good power from the alternator and good fuel economy from the engine. 1500 RPM on the alt you are likely only going to get less than 20 amps out of is.
Another thing to remember is these passenger car alternators were not designed to put out full rated amps continuously. As little as a 50 amp load can cause scorched windings or at the very least heat soak, which will reduce alternator output.
If I were going to build a single cylinder engine alternator generator I would likely use a Honda 5.5 or 6.5 horse engine, over drive the alt by around 1:3 for the alt I would use a SI12 type alternator, remote rectifier assembly (most of the real heavy duty alternators use remote rectifiers) and do a 3 to 4 wire windings conversion. Pretty much like I am doing here to this vehicle application alternator:
http://ecomodder.com/forum/showthread.php/schottky-diode-alternator-33199.html
Solar hybrid gasoline generator, 7kw gas, 180 watts of solar, Morningstar 15 amp MPPT, group 31 AGM, 900 watt kisae inverter.
Solar roof top GMC suburban, a normal 3/4 ton suburban with 180 watts of panels on the roof and 10 amp genasun MPPT, 2000w samlex pure sine wave inverter, 12v gast and ARB air compressors.
-
Small engines typically do well with axial loads, its the thrust loads that kill them.
Solar hybrid gasoline generator, 7kw gas, 180 watts of solar, Morningstar 15 amp MPPT, group 31 AGM, 900 watt kisae inverter.
Solar roof top GMC suburban, a normal 3/4 ton suburban with 180 watts of panels on the roof and 10 amp genasun MPPT, 2000w samlex pure sine wave inverter, 12v gast and ARB air compressors.
-
Thank you all for the valuable feedback. I have questioned doing a direct coupling and you've convinced me to go with belt drive.
I already have a source for 6-groove serpentine parts and the alternator has a 2 1/8" pulley. I need to see if it can be easily converted to fit on the engine shaft or just buy two new ones. I'll most likely start with a 3:2 ratio, running the engine at 3000rpm and the alt. at 2000rpm.
Resbum -
The best chance at getting a pulley or a lovejoy coupler to attack to a single cylinder engine is if the engine has a 5/8 inch or half inch keyed shaft.
If there was a generator attached to that motor then its a tapered shaft and you are pretty much out of luck.
At 2000rpm the alternator may produce enough power but may not be able to cool its self.
Solar hybrid gasoline generator, 7kw gas, 180 watts of solar, Morningstar 15 amp MPPT, group 31 AGM, 900 watt kisae inverter.
Solar roof top GMC suburban, a normal 3/4 ton suburban with 180 watts of panels on the roof and 10 amp genasun MPPT, 2000w samlex pure sine wave inverter, 12v gast and ARB air compressors.
-
Thanks for all the input oil pan. Also, that's an interesting thread you have over in ecomodder.
Resbum -
It sounds like you want to do what I am trying to do with my alt.
Basically running it full load but not at full speed. The high amp alts like the CS130 can scorch there windings producing as little as 50 amps at lower speeds.
Solar hybrid gasoline generator, 7kw gas, 180 watts of solar, Morningstar 15 amp MPPT, group 31 AGM, 900 watt kisae inverter.
Solar roof top GMC suburban, a normal 3/4 ton suburban with 180 watts of panels on the roof and 10 amp genasun MPPT, 2000w samlex pure sine wave inverter, 12v gast and ARB air compressors.
Categories
- All Categories
- 229 Forum & Website
- 137 Solar Forum News and Announcements
- 1.4K Solar News, Reviews, & Product Announcements
- 199 Solar Information links & sources, event announcements
- 898 Solar Product Reviews & Opinions
- 256 Solar Skeptics, Hype, & Scams Corner
- 22.5K Solar Electric Power, Wind Power & Balance of System
- 3.5K General Solar Power Topics
- 6.7K Solar Beginners Corner
- 1K PV Installers Forum - NEC, Wiring, Installation
- 2.1K Advanced Solar Electric Technical Forum
- 5.6K Off Grid Solar & Battery Systems
- 428 Caravan, Recreational Vehicle, and Marine Power Systems
- 1.1K Grid Tie and Grid Interactive Systems
- 654 Solar Water Pumping
- 816 Wind Power Generation
- 624 Energy Use & Conservation
- 619 Discussion Forums/Café
- 312 In the Weeds--Member's Choice
- 75 Construction
- 124 New Battery Technologies
- 108 Old Battery Tech Discussions
- 3.8K Solar News - Automatic Feed
- 3.8K Solar Energy News RSS Feed