Intoduction and queries
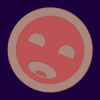
newl
Solar Expert Posts: 53 ✭✭✭✭
G'day all,
I've been following the forum on and off for the past few months and I'd like say hello and what an awesome bunch you lot appear to be with support and knowledge. I've been off grid now for a few months and am absolutely loving it. Means a lot to me to be able to get out of the suburbs and back to the land on my 500 acre property. Currently living in a good quality and respectable sized canvas tent with plans to have a studio/guest accommodation built within 6-12 months, large shed (that I can switch to living in if the studio/guest accommodation isn't suitable) 6 months after that and finally the house within 1-2 years after that. I'll try and get some photos up in the pinned Show Me Yours thread in the next week or so.
My current primary setup is a 12V system (I also have other smaller solar configurations around the property for dog collar radio fencing, electric horse fencing, lighting):
* 2 x 200W panels
* 1 x 30A 12V/24V PWM charge controller
* 4 x (PDF spec sheet) PDC-121000 100AH batteries currently wired in parallel. Charge controller and inverter are connected at opposite polls.
* 1 x 12V 300W pure sine wave inverter that will surge to 450W
My usage currently is (sans refrigerators):
* 12V LED strip lighting - 5 hours 60W = 300WH/25AH (I am aiming high on W and time with these as I honestly have no idea what their current draw is)
* 240V Laptop - 5 hours 25W = 125WH/.52AH (again, aiming a bit high time wise, real usage is typically 3-4 hours, W is pretty accurate even with elcheap-o plug in power measurement device)
Eventually, I'll want to add a 12V extractor fan once my gear goes into a small 3m x 3m garden shed and more than likely a pedestal for my usage being as I am currently coming into the summer months. These are the only immediate additions that I can think of apart from 12V LED lighting in the loo/shower block that I have not yet build.
Everything else that I use runs LPG (stove, hot water system) or is rechargeable (flashlights, hot water system). Water is collected by a car port, 16M^2 which gives me 1L per 1mm of rain fall, and stored in two 5000L water tanks. This too is an area in which I need to improve, not enough surface area for catchment; working on that.
Sitting by idle at the moment are an additional two panels and a Morningstar Tristar-45 MPPT. I have a spare charge controller (identical to the above) so I could toss that on with the other two panels but I'm at a point growth wise that I feel that I would be better off making the switch to 24V. I have what I feel is ample storage with 400AH at 12V and the panels do not have any problems keeping the batteries topped up. I also realize that 800W of panels will be overkill for the current battery configuration. Being as the system is only a couple months old, could I get away with getting four more without too much disruption between what has been used for two months and what has been sitting on a shelf (I know that mixing batteries in terms of their life isn't a good idea yet these would be fairly close)?
My reason for wanting to make the switch to 24V is two fold. First, I can switch the Tristar in and run all 800W (all four panels in series, single string) in an optimum configuration and gain the added obvious benefits of an MPPT controller that I can grow with as my needs grow. Secondly, I have two refrigerators at the moment, neither of them is in use, that I would now like to start using at least one of them. I have a Waeco (Dometic) RC1180 50L and an NEC 80L bar fridge. Of the two, the Waeco draws the most power at 119W +/-10% (cheap $20 plug in digital power meter) while the NEC draws ~560W start up surge and settles to 75-80W. Consumption and space consideration wise, the NEC wins the draw. Flexibility wise, the Waeco wins because it is 240V/12V/LPG so I'll probably keep it for a backup.
Ideally, I would prefer to go 48V and then get a 48V inverter and 48VDC->12VDC converter to be able to run all of my existing 12V gear. A bit out of my price range at the moment so I am making the (albeit costly for when I do go 48V) decision to use 24V as the stepping stone and continue to learn about the system, the technology, my usage and habits, all of which come into play.
Now, the part that I am not specifically clear on is the difference is between 12V@400AH and 24V@200AH (two parallel strings of two in series). I know that the power capability remains the same (Ohms Law) but does the drop in AH have an impact as such? Related to this, in reference to 48V system, would running the four batteries in a single string 48V series configuration at 100Ah also have an impact? I realize that using larger voltages means my cabling (naturally depending on distances and losses) doesn't need to be as beefy and that is an advantage in terms of cost.
I'm open to support, ideas feedback and wisdom. Hit me!
I've been following the forum on and off for the past few months and I'd like say hello and what an awesome bunch you lot appear to be with support and knowledge. I've been off grid now for a few months and am absolutely loving it. Means a lot to me to be able to get out of the suburbs and back to the land on my 500 acre property. Currently living in a good quality and respectable sized canvas tent with plans to have a studio/guest accommodation built within 6-12 months, large shed (that I can switch to living in if the studio/guest accommodation isn't suitable) 6 months after that and finally the house within 1-2 years after that. I'll try and get some photos up in the pinned Show Me Yours thread in the next week or so.
My current primary setup is a 12V system (I also have other smaller solar configurations around the property for dog collar radio fencing, electric horse fencing, lighting):
* 2 x 200W panels
* 1 x 30A 12V/24V PWM charge controller
* 4 x (PDF spec sheet) PDC-121000 100AH batteries currently wired in parallel. Charge controller and inverter are connected at opposite polls.
* 1 x 12V 300W pure sine wave inverter that will surge to 450W
My usage currently is (sans refrigerators):
* 12V LED strip lighting - 5 hours 60W = 300WH/25AH (I am aiming high on W and time with these as I honestly have no idea what their current draw is)
* 240V Laptop - 5 hours 25W = 125WH/.52AH (again, aiming a bit high time wise, real usage is typically 3-4 hours, W is pretty accurate even with elcheap-o plug in power measurement device)
Eventually, I'll want to add a 12V extractor fan once my gear goes into a small 3m x 3m garden shed and more than likely a pedestal for my usage being as I am currently coming into the summer months. These are the only immediate additions that I can think of apart from 12V LED lighting in the loo/shower block that I have not yet build.
Everything else that I use runs LPG (stove, hot water system) or is rechargeable (flashlights, hot water system). Water is collected by a car port, 16M^2 which gives me 1L per 1mm of rain fall, and stored in two 5000L water tanks. This too is an area in which I need to improve, not enough surface area for catchment; working on that.

Sitting by idle at the moment are an additional two panels and a Morningstar Tristar-45 MPPT. I have a spare charge controller (identical to the above) so I could toss that on with the other two panels but I'm at a point growth wise that I feel that I would be better off making the switch to 24V. I have what I feel is ample storage with 400AH at 12V and the panels do not have any problems keeping the batteries topped up. I also realize that 800W of panels will be overkill for the current battery configuration. Being as the system is only a couple months old, could I get away with getting four more without too much disruption between what has been used for two months and what has been sitting on a shelf (I know that mixing batteries in terms of their life isn't a good idea yet these would be fairly close)?
My reason for wanting to make the switch to 24V is two fold. First, I can switch the Tristar in and run all 800W (all four panels in series, single string) in an optimum configuration and gain the added obvious benefits of an MPPT controller that I can grow with as my needs grow. Secondly, I have two refrigerators at the moment, neither of them is in use, that I would now like to start using at least one of them. I have a Waeco (Dometic) RC1180 50L and an NEC 80L bar fridge. Of the two, the Waeco draws the most power at 119W +/-10% (cheap $20 plug in digital power meter) while the NEC draws ~560W start up surge and settles to 75-80W. Consumption and space consideration wise, the NEC wins the draw. Flexibility wise, the Waeco wins because it is 240V/12V/LPG so I'll probably keep it for a backup.
Ideally, I would prefer to go 48V and then get a 48V inverter and 48VDC->12VDC converter to be able to run all of my existing 12V gear. A bit out of my price range at the moment so I am making the (albeit costly for when I do go 48V) decision to use 24V as the stepping stone and continue to learn about the system, the technology, my usage and habits, all of which come into play.
Now, the part that I am not specifically clear on is the difference is between 12V@400AH and 24V@200AH (two parallel strings of two in series). I know that the power capability remains the same (Ohms Law) but does the drop in AH have an impact as such? Related to this, in reference to 48V system, would running the four batteries in a single string 48V series configuration at 100Ah also have an impact? I realize that using larger voltages means my cabling (naturally depending on distances and losses) doesn't need to be as beefy and that is an advantage in terms of cost.
I'm open to support, ideas feedback and wisdom. Hit me!

Comments
-
Re: Intoduction and queries
Welcome to the forum.
This may help you understand the reasons for choosing one system Voltage over another: http://forum.solar-electric.com/showthread.php?15989-Battery-System-Voltages-and-equivalent-power -
Re: Intoduction and queries
Welcome to the forum Newl.
A few comments:My current primary setup is a 12V system (I also have other smaller solar configurations around the property for dog collar radio fencing, electric horse fencing, lighting):
* 2 x 200W panels
Interesting, you have found one of the few large (high wattage) solar panels that outputs Vmp~18 volts--Which is good for 12 volt battery bank with PWM controller. Will help to keep your system costs lower.
If you need to add panels (now or later), this controller is only good for ~2x of your 200 watt panels. So, no room to expand without paralleling charge controllers (not usually a problem) or installing your larger controller.* 4 x (PDF spec sheet) PDC-121000 100AH batteries currently wired in parallel. Charge controller and inverter are connected at opposite polls.
You have AGM (Sealed) batteries, and this might be a better idea for a remote installation. Having to buy/make distilled (or de-ionized) water for filling batteries in remote/dry region may have its own difficulties (capturing and storing clean/filtered rainwater is an option too).
A rule of thumb I like to use for sizing the batter bank to solar array size i the 5% to 13% rule of thumb:- 14.2 volts charging * 400 AH capacity * 1/0.77 panel+controller derating * 0.05 rate of charge = 369 watt array minimum
- 14.2 volts charging * 400 AH capacity * 1/0.77 panel+controller derating * 0.10 rate of charge = 738 watt array nominal
- 14.2 volts charging * 400 AH capacity * 1/0.77 panel+controller derating * 0.13 rate of charge = 959 watt array "cost effective maximum"
AGM batteries are a better choice for a smaller array (lower self discharge rate, no equalization/mixing of electrolyte required by higher current). But that 400 watt array is still a bit on the small size for that size battery bank. It would be nice to get closer to the 10% rate of charge if this is your only power and you need the electricity.
I would suggest Battery Monitor (Victron is another very good brand) for your system. While you can use a volt meter to get a good idea of how your system is running--You cannot measure specific gravity of your bank, so you have to be very diligent/careful and understand what your volt meter is telling you. A battery monitor (while not perfect) will help you both measure/monitor your loads and help you keep the batteries happy.
Almost everyone "murders" their first set or two of batteries--Usually from under charging/over discharging/too large of loads (another reason to suggest "cheaper" flooded cell "golf cart" batteries for your first try vs the more expensive AGM). A battery monitor will help you understand your loads/battery state of charge better.* 1 x 12V 300W pure sine wave inverter that will surge to 450W
GREAT! Somebody with a reasonable size of inverter on their battery bank. Do you have a switch to turn it off when not in use (may still use ~6-10 watts just being "on"--a significant power hit for a small power system).
My usage currently is (sans refrigerators):* 12V LED strip lighting - 5 hours 60W = 300WH/25AH ...)
60 watts is a lot of LED... Are you planning on us 12 volt LED or 120/230 VAC lighting?* 240V Laptop - 5 hours 25W = 125WH/.52AH (again, aiming a bit high time wise, real usage is typically 3-4 hours, W is pretty accurate even with elcheap-o plug in power measurement device)
Probably a typo/calculation error here--The way I do the sizing including inverter losses:- 25 watts * 5 hours * 1/0.85 inverter losses * 1/12 volt battery bank = 12.3 AH @ 12 volt bank
- 25 watts * 5 hours * 1/0.85 inverter losses = 147 Watt*Hours
Your total load is ~447 WH per day or 37 AH @ 12 volts per day... The battery sizing of 1-3 days "no sun" and 50% maximum discharge (longer battery life), picking 2 days and 50% max discharge"- 37 AH per day * 2 days * 1/0.50 max discharge = 148 AH @ 12 volt battery bank "nominal"
Your bank is a bit on the "large size" for such a system (pushes up the solar array sizing to keep "battery bank happy"). Does give you some room to grow/miss your numbers.
I assume you are in a sunny/dry area of Australia--so lets assume that you get a good 4 hours of sun for 9+ months of the year (you might do better):- 400 watt solar array * 0.52 system derating * 4 hours of sun per day = 832 WH per day
You currently have only 447 WH of usage planned per day--So your array seems to output plenty of power for your needs (solar and loads do vary--You should never plan on using 100% of your predicted capacity every day--Monitor your battery bank and ensure that you do not "stress" your battery--cut power usage/fire up backup generator when needed).Eventually, I'll want to add a 12V extractor fan once my gear goes into a small 3m x 3m garden shed and more than likely a pedestal for my usage being as I am currently coming into the summer months. These are the only immediate additions that I can think of apart from 12V LED lighting in the loo/shower block that I have not yet build.
If you can--use a chimney/optimize for natural circulation (inlet low, large outlet high). Fans (and any mechanical devices) tend to use a relatively large amount of energy per day to operate. If you can avoid using the power in the first place--You are better off (smaller solar powered fans do not move that much air--You can use a fan+direct connect solar panel instead--Saves the whole battery issue as you only need the fan to run when the sun is up--I would guess).Everything else that I use runs LPG (stove, hot water system) or is rechargeable (flashlights, hot water system). Water is collected by a car port, 16M^2 which gives me 1L per 1mm of rain fall, and stored in two 5000L water tanks. This too is an area in which I need to improve, not enough surface area for catchment; working on that.
Use a 12 volt water pump to pressurize some indoor plumbing?... I also realize that 800W of panels will be overkill for the current battery configuration. Being as the system is only a couple months old, could I get away with getting four more without too much disruption between what has been used for two months and what has been sitting on a shelf (I know that mixing batteries in terms of their life isn't a good idea yet these would be fairly close)?
For the size battery bank you have--800 Watts would not be a waste--I would hook them up (all things being equal). Good charge controllers will keep the battery voltage appropriate for the batteries. And AGMs, while they do not like high charging voltages, can take pretty much any current you throw at them. Put two controllers in parallel (run wire from each controller back to the battery bank--short/heavy wire to keep voltage drops low--should have a fuse/breaker per controller/load branch circuit for safety).My reason for wanting to make the switch to 24V is two fold. First, I can switch the Tristar in and run all 800W (all four panels in series, single string) in an optimum configuration and gain the added obvious benefits of an MPPT controller that I can grow with as my needs grow.
Keeping the DC current down (I suggest switching to the next higher battery bank voltage if your DC current goes over ~100 amps--i.e., ~1,2 watts for 12 volt max; 2,400 watt for 24 volt bank, etc.). However, trying to find power appropriate 24 and 48 volt inverters for smaller systems can be difficult--and larger inverters use more power when idling).Secondly, I have two refrigerators at the moment, neither of them is in use, that I would now like to start using at least one of them. I have a Waeco (Dometic) RC1180 50L and an NEC 80L bar fridge. Of the two, the Waeco draws the most power at 119W +/-10% (cheap $20 plug in digital power meter) while the NEC draws ~560W start up surge and settles to 75-80W. Consumption and space consideration wise, the NEC wins the draw. Flexibility wise, the Waeco wins because it is 240V/12V/LPG so I'll probably keep it for a backup.
If you can, get a Kill-a-Watt type meter (link to 120 VAC version) and measure their daily load (over 1-7 days or so). Small bar fridges tend to use almost as much power as a full size/very efficient home refrigerators these days (~300 WH per day for a bar fridge; around 370-400 WH per day for a full size fridge). One option would be to convert a chest freezer for fridge use (may use as little as 250 WH per day at 77F/25C).
Either way, you will proably need a minimun of 1,200 to 1,500 inverter to start a full sized fridge.Ideally, I would prefer to go 48V and then get a 48V inverter and 48VDC->12VDC converter to be able to run all of my existing 12V gear. A bit out of my price range at the moment so I am making the (albeit costly for when I do go 48V) decision to use 24V as the stepping stone and continue to learn about the system, the technology, my usage and habits, all of which come into play.
As you have seen--It is difficult to "cost effectively" grow a solar power system... New inverters for each voltage change, perhaps a new charge controller to 48 volts, solar panels change (you may not find Vmp matching panels 2-4 years down the road) and such... If you will be going to a larger system eventually, you may just want to save some money and "skip" the 24 volt verson unless you can use it elsewhere (guest cabin, remote camp site, etc.).Now, the part that I am not specifically clear on is the difference is between 12V@400AH and 24V@200AH (two parallel strings of two in series). I know that the power capability remains the same (Ohms Law) but does the drop in AH have an impact as such? Related to this, in reference to 48V system, would running the four batteries in a single string 48V series configuration at 100Ah also have an impact? I realize that using larger voltages means my cabling (naturally depending on distances and losses) doesn't need to be as beefy and that is an advantage in terms of cost.
I, personally, do not like to parallel batteries--So I would be better with 2 parrallel strings at 24 volts or one series string at 48 volts. The big issue is finding an AC inverter that matches your power needs/bank balance. The 48 volt inverters are going to be in the 2-4kW+ range--Great if you need that level of power and have teh battery bank+solar array to support it... But can be "over kill" for people with smaller power needs.
And, I would suggest avoiding oversizing the battery bank if you don't need the power. Batteries age faster (sulfate) if they are not quickly and fully recharged a cuople times a week (recharged to over 90% state of charge). A large bank takes a good sized array to quickly recharge--and when the batteries fail, you have to spend more money to replace the bank.
Your comments?
-BillNear San Francisco California: 3.5kWatt Grid Tied Solar power system+small backup genset -
Re: Intoduction and queriesInteresting, you have found one of the few large (high wattage) solar panels that outputs Vmp~18 volts--. Will help to keep your system costs lower.
This path was intentional so that I was able to keep the costs down.If you need to add panels (now or later), this controller is only good for ~2x of your 200 watt panels..
Starting out with the two panels with this particular controller was also intentional for the same reason. It was cheap enough that I bought a second one as a backup. Now that I'm getting into the better gear, backups aren't an option at this moment in time so I'll keep these two controller just in case or re-task them on other uses around the property.Personally, I am not a fan of lots of batteries in parallel. I like to see larger AH batteries/Cells to give you one too a maximum of two to three strings in parallel.
You have AGM (Sealed) batteries, and this might be a better idea for a remote installation..
I knew of the problems that running in parallel may bring and with the two that I started out with, I didn't feel that it would be a big issue. When I tossed the other two on the bank a week after the system was commissioned, a flag went up in my head telling me to rethink the design. So, all the information that you guys have given over the years and the tons of reading that I did, something stuck somewhere for that flag to go up.A rule of thumb I like to use for sizing the batter bank to solar array size i the 5% to 13% rule of thumb:- 14.2 volts charging * 400 AH capacity * 1/0.77 panel+controller derating * 0.05 rate of charge = 369 watt array minimum
- 14.2 volts charging * 400 AH capacity * 1/0.77 panel+controller derating * 0.10 rate of charge = 738 watt array nominal
- 14.2 volts charging * 400 AH capacity * 1/0.77 panel+controller derating * 0.13 rate of charge = 959 watt array "cost effective maximum"
- Thank you... Fixed in original post too--Bill B.
RoC is all the same?But that 400 watt array is still a bit on the small size for that size battery bank. It would be nice to get closer to the 10% rate of charge
I wasn't 100% certain that it was sufficient, thanks for clarifying that. With this redesign, I can hopefully resolve that. I also have a Honda eu20i with a Ctek 25A charger.I would suggest Battery Monitor (Victron is another very good brand) for your system..
I do not have one yet and it has been on the shopping list yet just not a higher priority as of late. The Victron monitor, I believe I can get in a brick and mortar shop locally as I have seen the inverters pictured on the right in one of my local electronics shops.Almost everyone "murders" their first set or two of batteries--Usually from under charging/over discharging/too large of loads.
I'm hoping that I don't kill mine. lol If I do, I'll be running off of the generator for a bit. Reduced maintenance was a factor in me choosing sealed AGM batteries. Another was that bush fires are quite common and having a properly configured system can help prevent them.GREAT! Somebody with a reasonable size of inverter on their battery bank. Do you have a switch to turn it off when not in use
The unit is a Sinergex. Draws 2.76W with no load. Does have a power switch on the unit as well as remote switching capability (not currently in use) and is ran through a DC circuit breaker for added protection and isolation. When I leave in the mornings to head to work, I will (usually but not always) flip the breaker.60 watts is a lot of LED... Are you planning on us 12 volt LED or 120/230 VAC lighting?
It was/is a high guess. I'm running 12V strip lighting that comes on a roll, nabbed them on fleabay for $15 each (grabbed two, one is a 3528, the other is a 5050). I'm planning on running 12V lighting to avoid the inverter losses.- 37 AH per day * 2 days * 1/0.50 max discharge = 148 AH @ 12 volt battery bank "nominal"
That is fairly close to my calculations as well. I was slightly under that AH usage value.Your bank is a bit on the "large size" for such a system..Does give you some room to grow/miss your numbers.
As with most others that live off grid, it is better to have too much than not enough.I assume you are in a sunny/dry area of Australia--so lets assume that you get a good 4 hours of sun for 9+ months of the year:- 400 watt solar array * 0.52 system derating * 4 hours of sun per day = 832 WH per day
You currently have only 447 WH of usage planned per day--So your array seems to output plenty of power for your needs (solar and loads do vary--You should never plan on using 100% of your predicted capacity every day--Monitor your battery bank and ensure that you do not "stress" your battery--cut power usage/fire up backup generator when needed).
You're pretty spot on with the minimum hours. From pvwatts:1, 7.75, 82, 0.07 2, 7.27, 70, 0.06 3, 6.50, 71, 0.06 4, 5.43, 57, 0.05 5, 4.39, 50, 0.05 6, 3.77, 42, 0.04 7, 4.01, 47, 0.04 8, 4.72, 54, 0.05 9, 5.99, 66, 0.06 10, 6.42, 70, 0.06 11, 6.91, 73, 0.07 12, 7.17, 77, 0.07 "Year", 5.85, 759, 0.68
I suppose that one of my fears is not using the bank to its potential. As examples of patterns, I don't always run lighting at night and I'll only leave the power point for the laptop switched on long enough to charge it and repeat again in a few hours when it needs it. What I do not want to do as expressed before isIf you can--use a chimney/optimize for natural circulation (inlet low, large outlet high). Fans....
My thought when saying that is that I could easily run the 12V off of the load connection of the charge controller. Fan and a direct connect panel is another option and probably cheaper. Another option is one of the spinning vents (we normally have a steady breeze/wind at this location).Use a 12 volt water pump to pressurize some indoor plumbing?
Nope, water is gravity fed from the tanks at the moment. A 12V pump is also on the shopping list. They're a very common thing here in Australia and they're not overly expensive. I'll have to work that in at some point and have more knowledge of the requirements of whatever pump I purchase and whether the system can support it (both in normal operation and start up surge). Solar powered pumps are also quite common and that too is an option. It would be a matter of changing behaviors and patterns in relation to usage which is easy enough to achieve.For the size battery bank you have--800 Watts would not be a waste--I would hook them up (all things being equal). Good charge controllers will keep the battery voltage appropriate for the batteries...
The Tristar can handle three panels for a 12V system though two panels is optimum per their string calculator. 600W and 800W is optimum for a 24V system. Going 48V, I can run heaps more but that is down the track system size wise.Keeping the DC current down (I suggest switching to the next higher battery bank voltage if your DC current goes over ~100 amps--i.e., ~1,2 watts for 12 volt max; 2,400 watt for 24 volt bank, etc.). However, trying to find power appropriate 24 and 48 volt inverters for smaller systems can be difficult--and larger inverters use more power when idling).
Having a battery monitor will certainly help me keep informed so I'll try and pick one up in the next month or two. Ideally I would like to have the system redesigned before winter sets in to ensure a proper supply of electricity.If you can, get a Kill-a-Watt type meter (link to 120 VAC version) and measure their daily load (over 1-7 days or so). Small bar fridges tend to use almost as much power as a full size/very efficient home refrigerators these days (~300 WH per day for a bar fridge; around 370-400 WH per day for a full size fridge). One option would be to convert a chest freezer for fridge use (may use as little as 250 WH per day at 77F/25C).
I have a very similar device that provides the same/similar functionality. In order to achieve the measuring period, I'd have to drag them down to the suburbs which is achievable (or alternatively, run it on the generator for a day which isn't as good an idea but is less work). Switching to a larger fridge is currently not financially feasible (have my fingers in many pies at the moment). Interesting read on the chest freezer thread.
Either way, you will proably need a minimun of 1,200 to 1,500 inverter to start a full sized fridge.
That was the impression I got from another thread that I got distracted on after reading the chest freezer thread.As you have seen--It is difficult to "cost effectively" grow a solar power system... New inverters for each voltage change, perhaps a new charge controller to 48 volts, solar panels change (you may not find Vmp matching panels 2-4 years down the road) and such... If you will be going to a larger system eventually, you may just want to save some money and "skip" the 24 volt verson unless you can use it elsewhere (guest cabin, remote camp site, etc.).
Skipping at this point is the most cost effective as I will only need to get a larger inverter. If I aim for a 2kW inverter, I feel that it would cope with what I need to run now with a little bit of wiggle room for the near future. Plus, as you say, the existing gear can be migrated and used elsewhere.I, personally, do not like to parallel batteries--So I would be better with 2 parrallel strings at 24 volts or one series string at 48 volts. The big issue is finding an AC inverter that matches your power needs/bank balance...
So you're suggesting the following for 24V. If so, this was my intended configuration. Yes, the 48V inverters aren't cheap either.12V Parallel 12V = 12V@200AH + 12V Parallel 12V = 12V@200AH = series for 24V@200AH
And, I would suggest avoiding oversizing the battery bank if you don't need the power. Batteries age faster (sulfate) if they are not quickly and fully recharged...
Solid advice. At the moment, sun isn't a problem and the batteries seem to be getting their fill though perhaps not as quickly with only the two panels.
So, for now, I feel that the best path of action is for me to get a larger 12V inverter in the range of 2kW to handle the bar fridge (again, being the lesser evil of the two power hogs) and its start up surge requirements. If I'm hearing you correctly, I should be okay to run the fridge and my existing gear that I've disclosed, right? Last thought that just popped into my head, I should stop babying the batteries with an expected 25%-30% and aim for 50% usage because I'm truly not intending on keeping them long term and if they last me for the time frames that I have intended to try my best to keep to they will have served their purpose.
Thanks heaps for the response Bill.
Cariboocoot, helpful and informational link. Cheers. -
Re: Intoduction and queries
Thank you Newl for finding the typos around Rate of Charge equations... I have fixed them.So you're suggesting the following for 24V. If so, this was my intended configuration. Yes, the 48V inverters aren't cheap either.12V Parallel 12V = 12V@200AH + 12V Parallel 12V = 12V@200AH = series for 24V@200AH
Not quite sure what you are asking... If you have 4x 12 volt @ 100 AH batteries, your options would be:- 4x in series... You would get a 12 volt @ 400 AH battery bank
- 2x in series, then those two in parallel... gives you 24 volts @ 200 AH battery bank
- 4x in series... gives you a 48 volt @ 100 AH battery bank
All would store the same amount of energy (voltage*AH=storage energy in Watt*Hours):- 4x 12 volts * 100 AH = 4,800 Watt*Hours = 4.8 kWH
If you have the 4x 12 volt @ 100 AH batteries, and a 12 volt inverter that currently meets your needs--Use them all. Wire them up per this website to help ensure the batteries share the load properly.
If you will be paralleling battery banks for the long term... I would suggest getting a DC Current Clamp Meter. They will allow you to monitor the DC current in each string to ensure that all are (roughly) carrying the same loads (charging and discharging--no bad connections, no shorted/open cells that can damage the other batteries over time). This meter is only $60 USD in US (Sears.com) and it is "good enough" for our basic needs (you can spend $400 USD or more for a "good one" from Fluke/etc.). I don't have any suggestions for your region.My thought when saying that is that I could easily run the 12V off of the load connection of the charge controller. Fan and a direct connect panel is another option and probably cheaper. Another option is one of the spinning vents (we normally have a steady breeze/wind at this location).
Apparently the "wind turbine" type spinning vents are not really any better at enhancing air flow when the weather is windy. Just lots of area (sq. meters) for natural circulation (both inlets and outlets) is the best thing.
Reducing loads on the battery bank is always a good idea--especially automatic loads (i.e., fan runs during the week and you get bad weather---and can't get back in time to kill the loads--which kills the battery bank). Small loads (fans, computers, TV, etc.) that run for 8-24 hours per day can easily be more power hogs than a microwave that only runs 20 minutes a day.
Your thought appeared to get cut off?I suppose that one of my fears is not using the bank to its potential. As examples of patterns, I don't always run lighting at night and I'll only leave the power point for the laptop switched on long enough to charge it and repeat again in a few hours when it needs it. What I do not want to do as expressed before is
(???)
Basically, if you have a good ratio of Solar Array Wattage to Battery Bank Storage (i.e., the 5%-13% rate of charge)--and you have panels available for the 10+% rate of charge--Go for it.
The batteries will be happier with more charging current available. And if there is nothing you can do with 1 or 2 batteries pulled from the bank (i.e., take two extra panels+batteries for another guest tent/work area???)--Just add the panels and see how the system performs.
In any case, you will be learning from this bank/system--See how everything works. If you add/install a larger inverter (the AGM batteries are real good at surge current)--And keep the DC power leads short and heavy (between battery and inverter)--You might be quite happy with the existing bank and a 12 volt 1,200-2,000 watt inverter to run the bar fridge.
Note, while MSW inverters are much less expensive--MSW may be hard on the refrigerator (cause it to fail an early death--it very hard to predict if the fridge will last 10+ years or only 1-2 years on an MSW inverter--Just do not know). Induction motors generate more waste heat because of the non-sine wave form from MSW (modified square wave) and can age the pump faster.
-BillNear San Francisco California: 3.5kWatt Grid Tied Solar power system+small backup genset -
Re: Intoduction and queriesIf you have the 4x 12 volt @ 100 AH batteries, and a 12 volt inverter that currently meets your needs--Use them all. Wire them up per this website to help ensure the batteries share the load properly.
I am currently wired up with the second method; charging on opposite corners +/- and pulling from the opposite +/- corners to those two. The last method is simple enough to implement with a couple extra cables that I'd be prepared to shell out for to have them made up to length. Would I still need to charge and use from opposite ends though?
I've been having a circuit breaker trip intermittently the past week. I'm fairly certain it is because of the way I wired it and it is probably undersized.
I'm using a double pole 20A 500VDC breaker primarily for isolation. One one pole, I have the positive of the panels come in and then out to the PWM charge controller. The PWM charge controller output then goes through the other pole of the same breaker and then out to the positive side of the battery bank. I then have a second identical breaker fed off of the opposite positive lead of the battery bank into that breaker, bonded both poles and then out to the inverter.
Being as the two existing panels are wired in series, the Imp is 11A, Isc is 11.5A which is well below the rating of the breaker, though it probably isn't if both poles need to be utilized to get the 20A capacity.
I feel that I've probably confirmed the cause (someone is welcome to chime in with wisdom), not specifically 100% sure what sized breakers that I should be running. While on the topic, fuse size suggestions would be very helpful too. I'm about to build up a power board and redo things so they'll sit nicely on the shed wall. With this redo, I found a 600W/1000W TSW inverter for a decent price and that covers my existing requirements and meets surge requirements as well.
-
Re: Intoduction and queriesI am currently wired up with the second method; charging on opposite corners +/- and pulling from the opposite +/- corners to those two. The last method is simple enough to implement with a couple extra cables that I'd be prepared to shell out for to have them made up to length. Would I still need to charge and use from opposite ends though?
As long as you don't do #1 (feeding a "ladder network" from one end)--You are fine. The idea is that to any battery in the string, you have equal length (resistance) wire paths. + and - lengths do not need to be identical--just the total + and - path lengths.I've been having a circuit breaker trip intermittently the past week. I'm fairly certain it is because of the way I wired it and it is probably undersized.
I'm using a double pole 20A 500VDC breaker primarily for isolation. One one pole, I have the positive of the panels come in and then out to the PWM charge controller. The PWM charge controller output then goes through the other pole of the same breaker and then out to the positive side of the battery bank.
I then have a second identical breaker fed off of the opposite positive lead of the battery bank into that breaker, bonded both poles and then out to the inverter.
I guess this does not make sense too me... How large is your inverter? 20 Amps on the 24 VDC battery bus is only good for ~400 watt of continuous AC output (power=voltage*current*inverter-efficiency).Being as the two existing panels are wired in series, the Imp is 11A, Isc is 11.5A which is well below the rating of the breaker, though it probably isn't if both poles need to be utilized to get the 20A capacity.
Paralleling beakers/fuses is not usually a great idea (minor resistance variations can steer the shared current away from one breaker and into another).I feel that I've probably confirmed the cause (someone is welcome to chime in with wisdom), not specifically 100% sure what sized breakers that I should be running. While on the topic, fuse size suggestions would be very helpful too. I'm about to build up a power board and redo things so they'll sit nicely on the shed wall. With this redo, I found a 600W/1000W TSW inverter for a decent price and that covers my existing requirements and meets surge requirements as well.
For example, a 24 volt DC input to a 1,000 AC inverter should have a branch circuit/wiring rated to a minimum of:- 1,000 watts inverter output * 1/0.85 inverter eff * 1/21 volts batt cutoff * 1.25 NEC derating = 70 amp minimum wiring/fusing/breaker rating
So, round up to the next standard (like 80 amps). And ensure you don't have much more than 1 volt wiring drop (24 volt bus) from battery to inverter (short/heavy cabling).
-BillNear San Francisco California: 3.5kWatt Grid Tied Solar power system+small backup genset -
Re: Intoduction and queriesI guess this does not make sense too me... How large is your inverter? 20 Amps on the 24 VDC battery bus is only good for ~400 watt of continuous AC output (power=voltage*current*inverter-efficiency).
Still using the 300W inverter at the moment on a 12V system. My plan is to get a 12V 600W (with 1200W surge, made a typo in the surge value previously) TSW inverter in the next week or two.
So working on your formula:
* 1,200W inverter output * 1/0.85 inverter eff * 1/10.5 volts batt cutoff * 1.25 NEC derating = 168A.
Looks like I need to do some upgrading. -
Re: Intoduction and queries
Just a quick update on the system. I have not yet changed the battery bank configuration due to a choice of financial constraints. What I have done is to add the other two 200W panels on to the Tristar MPPT45 which has been working with my original PWM charge controller for the past three weeks now and they're both happy as Larry to co-exist with one another. What I miss with the Tristar is the digital read out so I still currently rely on the PWM data display for information. What I'll probably do in the new year, early on, is to get the remote display for the Tristar and perhaps a battery monitoring system if can stretch the budget so that I can track information relatively quickly without having to go outside to do so. Cabling has been upgraded per previous discussions in this thread as well as DC circuit breakers (these were difficult to source here in Western Australia due to local solar installers grabbing everything that wholesalers had for a government rebate run out so I had to source these elsewhere). I still have not yet purchased a larger inverter. This decision has not been due to financial constraints as I have a specific account set aside for property work. I've just been lazy and being as we're currently in full blown summer at the moment, the heat is very much a deterrent (it'll be 40C+/104F all week long) so I have instead chosen to purchase a portable air conditioning (refrigerated reverse cycle) unit for now as that serves me immediately by helping me keep cool while at home in the holidays and can also heat my living area in the winter. This is currently run off of my Honda EU20i. I ran it for 6 hours or so today and the genny wasn't in full eco mode (with regard to revs) so I doubt that I'll get the claimed 18 hours out of a full tank of fuel. That is okay though, even if it doesn't fully agree with my inner greenie..I need to be comfortable and not sweating my back side off.Once I know for certain what I want, feature wise, with an inverter, I'll grab one. There are many available on the market and what I'm interested in is cheap redundancy so the Chinese market is where I'm looking. Some are super simple with merely inputs, outputs and an on/off switch, others are more fancy with remote data displays. The ones with remote data displays and/or data logging would probably be most beneficial to what I want. This way, I could data log the MTTP, battery bank and the inverter and then merge the data for more meaningful information in determining various aspects.
-
Re: Intoduction and queries
Newl, when looking / comparing inverters look at the 'no load' and 'idle' draw as well as the efficiency % in addition to the afore mentioned capabilities. Also compare with the next largest model, there are a few surprises out there...
hth
KID #51B 4s 140W to 24V 900Ah C&D AGM
CL#29032 FW 2126/ 2073/ 2133 175A E-Panel WBjr, 3 x 4s 140W to 24V 900Ah C&D AGM
Cotek ST1500W 24V Inverter,OmniCharge 3024,
2 x Cisco WRT54GL i/c DD-WRT Rtr & Bridge,
Eu3/2/1000i Gens, 1680W & E-Panel/WBjr to come, CL #647 asleep
West Chilcotin, BC, Canada -
Re: Intoduction and queries
Yeah, most of what I have seen thus far seem to hit the .7 to .8 idle usage so 8.4W to 9.6W. I feel that it is rare to see functionality like the 300W MorningStar inverter where it almost drops dead if there is no load. I wish more manufacturers did similar. I do not recall efficiency ratings average off hand. I do know that I look at that as well. -
Re: Intoduction and queries
Finally got off my bum and ordered the TSW 600W/1200W inverter late last week.
No load current draw: .65A
Efficiency: 85-90%
Both of these values are better than most of the Chinese gear that I had been looking at, granted it costs three times as much and yet at the same time, it has also been certified for use in this country.
Was thinking about numbers today as I've been monitoring my usage for the past 14 days for a total of 8.2kW/h (A/C). So knowing this I can project out to a monthly value:
8200 / 14 days = 585Wh daily * 30 days = 17571Wh monthly usage
Knowing the size of my battery bank (four 12V 100Ah in parallel) with a maximum 50% DoD:
12v * 400Ah = 4800Wh * 0.87 = 5517Wh * .50(DoD) = 2088Wh daily * 30 days = 62640Wh monthly available
So with the two values, I'm set fairly close my original design target at the moment of 33% DoD averaged for a month. Once the inverter arrives, I'll be running the 240VAC bar fridge which hits roughly 580W start up surge and settles to approximately 78/80W.
80W * 24 hours = 1920Wh increase per day + 585Wh existing daily usage = 2505Wh daily total * 30 days = 75150Wh monthly usage
Hrmm..so it would appear that I'm over the 50% DoD maximum set point. Unless there is something wrong with my calculations which I'm happy to hear thoughts about. I was originally pretty certain that my system was big enough for a couple of days sans sun (with generator support if really needed)..at least based upon my spreadsheet calculations.
Thoughts anyone? -
Re: Intoduction and queriesI'll be running the 240VAC bar fridge which hits roughly 580W start up surge and settles to approximately 78/80W.
80W * 24 hours = 1920Wh increase per day + 585Wh existing daily usage = 2505Wh daily total * 30 days = 75150Wh monthly usage...
You can't have a startup surge (or at least more than once) unless it shuts down, fridges work on a thermostat and cycle on and off. I n the U.S. we have a Kill-A-Watt meter to figure out how much energy/Kwhs something uses over time. I suspect there is something similar for your power specs...Home system 4000 watt (Evergreen) array standing, with 2 Midnite Classic Lites, Midnite E-panel, Magnum MS4024, Prosine 1800(now backup) and Exeltech 1100(former backup...lol), 660 ah 24v Forklift battery(now 10 years old). Off grid for 20 years (if I include 8 months on a bicycle).
- Assorted other systems, pieces and to many panels in the closet to not do more projects. -
Re: Intoduction and queriesfridges work on a thermostat and cycle on and off.
The percent of time that your fridge is running is called the duty cycle. Most fridges run a duty cycle of 30-50%, but it depends on ambient temperature and how much warm stuff you put in the fridge. So 80watts * 24 hrs * dutyCycle = ???
--vtMaps4 X 235watt Samsung, Midnite ePanel, Outback VFX3524 FM60 & mate, 4 Interstate L16, trimetric, Honda eu2000i -
Re: Intoduction and queries
Newl, it might be simpler to do your calcs for a single days use, then add in your autonomy, if any (doesn't look like it). As Vtmaps mentioned there is also the question of duty cycles, you need to determine how many occur per day... you may have to do a 24 hr vigil counting them...
hth
KID #51B 4s 140W to 24V 900Ah C&D AGM
CL#29032 FW 2126/ 2073/ 2133 175A E-Panel WBjr, 3 x 4s 140W to 24V 900Ah C&D AGM
Cotek ST1500W 24V Inverter,OmniCharge 3024,
2 x Cisco WRT54GL i/c DD-WRT Rtr & Bridge,
Eu3/2/1000i Gens, 1680W & E-Panel/WBjr to come, CL #647 asleep
West Chilcotin, BC, Canada -
Re: Intoduction and queries
Both surge and running wattage values were measured with a meter that provides pretty much identical functionality as the Kill-A-Watt. The running value was immediately observed after the initial expected surge in warm ambient (must've been around 34C the day I did this test) temperature and no previous cooling and the thermostat set at the lowest possible temperature (highest setting).
So, with my observed behavior, what you guys are suggesting is that it may ramp up even higher than what I observed? -
Re: Intoduction and queriesI am currently wired up with the second method; charging on opposite corners +/- and pulling from the opposite +/- corners to those two. The last method is simple enough to implement with a couple extra cables that I'd be prepared to shell out for to have them made up to length. Would I still need to charge and use from opposite ends though?
When wiring 2 batteries or strings of batteries using the "diagonal" method rather than a busbar, you should land the charger and the inverter on the same set of battery terminals rather than cross-wiring them. This insures that when the charger is delivering current at the same time that inverter is drawing current, the resistance in the circuit between them will be minimized and both the CC and the inverter will see the same battery voltage.SMA SB 3000, old BP panels. -
Re: Intoduction and queries
That sounds logical and fits in with the electrical knowledge that I can dig up out of my head.
The added point is that I'm running two charge controllers on opposite corners as well so my Tristar 45 MPPT and the inverter leads (through the fuse and the breaker) are connected at the same points with the PWM controller on the opposite two.
I'm running two charge controllers because of the costs of cutting over to a higher voltage bank and neither is capable of handling more than the two panels each that they currently have for a 12V system. -
Re: Intoduction and queries
I tossed the 600W inverter on late last week and have been running it in with almost no problems (my laptop PSU packed it in on Saturday..unsure it it is related to the new inverter or just coincidence).
I haven't watched the remote monitor on the inverter super intensely. I have observed during this time that the fridge kicks in at 80W usage (after surge) for approximately two minutes once every five minutes.
Been watching the bank like a hawk as well during this period. Normally at 12.8V when I head to bed and around 12.2 to 12.4V when I wake up so it isn't really getting hammered. The bank is typically in float by 8AM.
Categories
- All Categories
- 229 Forum & Website
- 137 Solar Forum News and Announcements
- 1.4K Solar News, Reviews, & Product Announcements
- 199 Solar Information links & sources, event announcements
- 898 Solar Product Reviews & Opinions
- 256 Solar Skeptics, Hype, & Scams Corner
- 22.5K Solar Electric Power, Wind Power & Balance of System
- 3.5K General Solar Power Topics
- 6.7K Solar Beginners Corner
- 1K PV Installers Forum - NEC, Wiring, Installation
- 2.1K Advanced Solar Electric Technical Forum
- 5.6K Off Grid Solar & Battery Systems
- 428 Caravan, Recreational Vehicle, and Marine Power Systems
- 1.1K Grid Tie and Grid Interactive Systems
- 654 Solar Water Pumping
- 816 Wind Power Generation
- 624 Energy Use & Conservation
- 619 Discussion Forums/Café
- 312 In the Weeds--Member's Choice
- 75 Construction
- 124 New Battery Technologies
- 108 Old Battery Tech Discussions
- 3.8K Solar News - Automatic Feed
- 3.8K Solar Energy News RSS Feed