Wind Project inquiries. (Vibration analysis on a turbine and blades.)
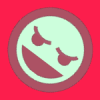
SH Yang
Registered Users Posts: 9 ✭
Good Day.
My project is the vibration analysis on a turbine and blades with FFT and CWT after attaching 3 axis acclerometers on a turbine and blades and voltages and currents (both voltages and currents are provided from the wind turbine channels).
Currently, I knew that the ouputs from the accelerometers needs to be transformed FFT for vibration analysis, however,
I am not sure that how the voltages and currents will be used for vibration interpreting.
According to my research, so far, I guess, the voltages and currents need to be calculated into powers, and then analyze how the vibration (frequency) affects the powers on the turbine. Am I right??
And
Thanks,
SH
My project is the vibration analysis on a turbine and blades with FFT and CWT after attaching 3 axis acclerometers on a turbine and blades and voltages and currents (both voltages and currents are provided from the wind turbine channels).
Currently, I knew that the ouputs from the accelerometers needs to be transformed FFT for vibration analysis, however,
I am not sure that how the voltages and currents will be used for vibration interpreting.
According to my research, so far, I guess, the voltages and currents need to be calculated into powers, and then analyze how the vibration (frequency) affects the powers on the turbine. Am I right??
And
Thanks,
SH
Comments
-
Re: Wind Project inquiries. (Vibration analysis on a turbine and blades.)
What do you mean by "powers?"...
Conversion into dBmW (decibel referenced to a Milli Watt)?
Or 10xLog10 (xxmW/1mW)
You will see 20xLog10 (xxmW/1mW) but this is because, for the most part, the sensors are measuring Amps or Voltage rather than power:- Power = I2R = V2/R = V*I
Bringing the "2" down from the square in the power equation to a multiplication in the Log function (10x for power; 20x for V or I measurements).
You will be looking for strong energy peaks in your spectrum...
More or less 2-3 db differences are within the margin of error... 10+ db differences are significant differences.
In general, you will want to plot the power vs frequency in mWatts Log/Log or linear DB voltage or current /Log frequency scale (note that DB is already a logarithmic conversion so plotting a linear db/Log scale is the same as Watt Log/Log plot).
When looking at your results--Look for Bode Plots--The standard (at least a couple decades ago) used to understand the "stability" of any damped response system.
The response of the system at resonant frequency(ies) and the phase between the measurement parameters will tell you if the system will be stable or build up vibrational energy--possibly to destruction (for example, alternator "cogging" at a frequency that causes blades or gear train to oscillate). Understanding dampening of the energy at various "resonant" frequencies is going to be critical--You don't want straight cut gear frequency causing excessive resonant oscillations of the blades which could cause their base or hub to fracture from long term stresses (my guess--this was not really my field).
Is this what you were asking?
-Bill "it has been a long time" B.Near San Francisco California: 3.5kWatt Grid Tied Solar power system+small backup genset -
Re: Wind Project inquiries. (Vibration analysis on a turbine and blades.)
If you search the internet for "wind turbine blade vibration analysis" there are a lot of articles available on that subject. -
Re: Wind Project inquiries. (Vibration analysis on a turbine and blades.)
That's what I questioned.
Thanks you very much! -
Re: Wind Project inquiries. (Vibration analysis on a turbine and blades.)
We have found that the practical key to consistent production on-board is to start with a moderate-sized swept area, and then to apply leading-edge technology to the blade set to extract the maximum amount of energy. By first focusing on the airfoils, we get a super-efficient, super-quiet Aero'coustic blade that gives exceptional power while maintaining low-speed start-up capability. This way the turbine can take advantage of all-day energy production, but also can generate more serious power when the winds pick up. It doesn't do much good to have great potential generating capacity if the blades never turn in the real world. Compare our start-up and output to the competition, and you will see the distinct advantage.
Details of the Design:
The blade and tail design focuses on several key strategies:
•Low Start-up Speeds
•Low Rotational Inertia
•Low Noise at Optimum Tip Speeds (15- 20 knots)
•Low Yaw Error
While our carbon-fiber Reinforced blade set has an extremely low rotational inertia, a strong and lightweight blade is only part of the story. The starting torque on a wind turbine is generated in the blade area closest to the hub, while the power producing torque is produced in the blade area closer to the tips. By use of computer modeling and simulation, a variable blade profile was produced that can react quickly in low wind speeds, yet produce high torque and optimal tip speed ratios at high speeds. The blades are produced in a solid-model patterned injection-molding tool, so that each blade is identical in weight and profile. Using a 20% carbon-fiber filled polymer make the blade very light, durable, and repeatable.
Lightweight blades have a low rotational inertia, which is critical in wind-energy production. Low rotational inertia allows the blades to accelerate more quickly, which means they can spin faster in lower wind speeds, therefore keeping the tip-speed-ratio (the speed of the tips vs. the speed of the wind) more constant. Operating closer to the optimum tip-speed-ratio during gusts also allows the turbine to improve energy capture from these sudden gusts.
Another way to increase aerodynamic efficiency --and to reduce noise on an airfoil blade-- is to manipulate and control the lateral airflow over the foil. Of course, some of the best engineering solutions often come from mimicing what is already found in nature. Whales and certain fish have amazing hydrodynamic efficiency and stealth through the use of tubercles, or raised and slotted sections on the leading edges of their fins. Our blades likewise use biomimicry-inspired riblets along the leading edge of the blades, which help the airfoil to create more power at lower speeds, and to operate more efficiency in turbulent air streams. These Aero'coustic riblets, also prevent the air from traveling down the blade edge and "vortexing" off the blade tip contributing to tip noise.
Yaw error is the difference between the direction the wind turbine is facing and the actual direction of the wind itself. As this yaw error increases, power decreases geometrically. Tail design, and the reduction or elimination of yaw error, is another very important element in the WhisperTorq's design. Our upward facing fin (not blocked by mounting pole) and vented self-tracking tail is wind-tunnel designed for minimal yaw error and maximum tracking efficiency. Compare our wind-tracking to the tracking of the mass-produced units sold by the "big box" marine stores and you can see the difference. -
Re: Wind Project inquiries. (Vibration analysis on a turbine and blades.)If you search the internet for "wind turbine blade vibration analysis" there are a lot of articles available on that subject.
However not all of them are reliable. Maybe post some links to some of the resources you've found useful...
_________________________________
Steve Works
vibration testing
Categories
- All Categories
- 229 Forum & Website
- 137 Solar Forum News and Announcements
- 1.4K Solar News, Reviews, & Product Announcements
- 199 Solar Information links & sources, event announcements
- 898 Solar Product Reviews & Opinions
- 256 Solar Skeptics, Hype, & Scams Corner
- 22.5K Solar Electric Power, Wind Power & Balance of System
- 3.5K General Solar Power Topics
- 6.7K Solar Beginners Corner
- 1K PV Installers Forum - NEC, Wiring, Installation
- 2.1K Advanced Solar Electric Technical Forum
- 5.6K Off Grid Solar & Battery Systems
- 428 Caravan, Recreational Vehicle, and Marine Power Systems
- 1.1K Grid Tie and Grid Interactive Systems
- 654 Solar Water Pumping
- 816 Wind Power Generation
- 624 Energy Use & Conservation
- 620 Discussion Forums/Café
- 313 In the Weeds--Member's Choice
- 75 Construction
- 124 New Battery Technologies
- 108 Old Battery Tech Discussions
- 3.8K Solar News - Automatic Feed
- 3.8K Solar Energy News RSS Feed