Newbie.. Parallel Renogy Rover controllers?
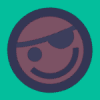
wayoffgrid
Registered Users Posts: 1 ✭
My name is Bryan and I am new to this forum. I live off grid in Southeastern Kentucky on the Big South fork of the Cumberland River.
I came here with a single 500 watt 12 v system consisting of 5 100 watt renogy solar panels run in series, a Renogy Rover 40 amp mppt controller, a single Renogy 1000w inverter (my lighting and refrigeration are 12 volt) and three 200 ah Renorgy AGM batteries. I augmented it with a small generator when needed. On the advice of someone I trusted I doubled the system with two separate arrays into two controllers run in parallel charging the same battery bank (same components). I'm not impressed with the result. I am hearing that the Renogy Rover 40 amp controllers cannot be run in parallel, only the 60 amp and 100 amp but I don't know if it's true Renogy doesn't seem to be able to supply me an answer.. I'm also hearing that they can be run in parallel with certain hacks to the programming. If there's anyone out there with experience who can enlighten me I would greatly appreciate it. I'm not getting a full charge, it seems to be going into a float charge before it should. I'm dropping down to 78 to to 80% at night and only charging up to about 90%. It also seems that the controllers are reading 12.9 volts when my multimeter is telling me I'm at 13.1 volts.
Be forewarned, I have my areas of expertise and this is definitely not one of them. It appears I was dropped on my head the day they were handing out the capacity to understand anything electrical.
Thank you in advance.
I came here with a single 500 watt 12 v system consisting of 5 100 watt renogy solar panels run in series, a Renogy Rover 40 amp mppt controller, a single Renogy 1000w inverter (my lighting and refrigeration are 12 volt) and three 200 ah Renorgy AGM batteries. I augmented it with a small generator when needed. On the advice of someone I trusted I doubled the system with two separate arrays into two controllers run in parallel charging the same battery bank (same components). I'm not impressed with the result. I am hearing that the Renogy Rover 40 amp controllers cannot be run in parallel, only the 60 amp and 100 amp but I don't know if it's true Renogy doesn't seem to be able to supply me an answer.. I'm also hearing that they can be run in parallel with certain hacks to the programming. If there's anyone out there with experience who can enlighten me I would greatly appreciate it. I'm not getting a full charge, it seems to be going into a float charge before it should. I'm dropping down to 78 to to 80% at night and only charging up to about 90%. It also seems that the controllers are reading 12.9 volts when my multimeter is telling me I'm at 13.1 volts.
Be forewarned, I have my areas of expertise and this is definitely not one of them. It appears I was dropped on my head the day they were handing out the capacity to understand anything electrical.
Thank you in advance.
Comments
-
If each controller has it's own solar array, I see no reason you could not have 3 arrays and 3 controllers.
However, MPPT controllers make some electrical noise, and maybe small, cheap ones don't have enough filtering to ignore the noise.
The trick is to get the meters on all the controllers adjusted so they come out of absorb at pretty much the same time
Powerfab top of pole PV mount | Listeroid 6/1 w/st5 gen head | XW6048 inverter/chgr | Iota 48V/15A charger | Morningstar 60A MPPT | 48V, 800A NiFe Battery (in series)| 15, Evergreen 205w "12V" PV array on pole | Midnight ePanel | Grundfos 10 SO5-9 with 3 wire Franklin Electric motor (1/2hp 240V 1ph ) on a timer for 3 hr noontime run - Runs off PV ||
|| Midnight Classic 200 | 10, Evergreen 200w in a 160VOC array ||
|| VEC1093 12V Charger | Maha C401 aa/aaa Charger | SureSine | Sunsaver MPPT 15A
solar: http://tinyurl.com/LMR-Solar
gen: http://tinyurl.com/LMR-Lister , -
Welcome to the forum WayOffGrid,
You can put several charging sources on one battery bank... I suggest that each controller has its own wiring back to the common Battery Connection (or "bus"). Usually you will have one fuse or circuit breaker on each + wire leaving the bus to each controller, and a - wire coming back to the negative battery bus/common connection. This helps minimize the "cross talk" between controllers.
I suggest we start at the beginning first... Can you give us a link to the present Renogy controller? Need to know the input and output ratings for it.
Next, what solar panels do you have... What is their Vmp (voltage maximum power) and Imp (current maximum power) ratings? And Voc (voltage open circuit (rating)?
Typically, the smaller Renogy controllers (I am no expert) have an maximum rated input voltage of 100 VDC on the solar input. Placing more than 3 or 4 panels in series (like your 5x right now?) can over voltage the input to the controller.
For example, Voc for your panel may be around 22 VDC. And 5x in series is around 110 VDC--And it only gets higher as panels get colder (sub freezing and really cold climates can raise voltage 10-20% pretty easily).
Next--Did you follow the wiring instructions for the solar charge controller? The controller's Vbatt terminals to Battery "Bus" should be relatively heavy and short. I.e., a few feet of 8 AWG cable would be a suggestion. You want very low voltage drop (around 0.05 to 0.10 volts @ 12 volt bus) at full rated current for optimum charging.
Regarding reading 12.9 vs 13.1 volts... That is probably within the margin of error of the meter and controller. I would not worry. You can always crank up the charging voltage by a few 0.1's of a volt if needed.
For the AC inverter... A 1,000 Watts is pretty heavy current draw from the battery bank. For example, roughly:- 1,000 Watts AC load * 1/0.85 inverter efficiency * 1/10.5 battery cutoff voltage = 112 Amps max continuous (2x for surge current rating)
The battery is the "heart" of your system. Your AGM batteries (as always, check the mfg. specifications/manual for proper settings). More or less, you want to see ~14.2 to 14.4 volts at the battery terminals. And held there for at least 2 hours (upwards of 6 hours for 50% or deeper discharge). Making sure your batteries reach these values is where you (and your batteries) need to be--Ideally at least once or twice a week when cycling. You only want to be >90% SoC daily. 100% is not really "needed" or ideal.
Next... What is your system producing and how much energy are you using. An example of harvest calculations. Picking Lexington, KY (this simple calculator does not have much for Kentucky--There are others better and more complex to use--But close enough to start).
Fhttp://www.solarelectricityhandbook.com/solar-irradiance.htmlor example:Lexington
Measured in kWh/m2/day onto a solar panel set at a 52° angle from vertical:
Average Solar Insolation figures
(For best year-round performance)
In May the average harvest for your system would be (in Watt*Hours and Amp*Hours--Whichever you understand better):Jan Feb Mar Apr May Jun 2.75
3.30
4.12
4.74
4.67
5.10
Jul Aug Sep Oct Nov Dec 5.11
5.02
5.10
4.48
3.17
2.51
- 500 Watts * 0.52 off grid system AC eff * 4.67 hours of sun per day = 1,214 WH per day
- 1,214 WH per day / 14.4 volts charging = 84 AH @ 12 volts
You can get lots of AC and DC meters out there to help you measure/monitor your loads and better understand what is happening:
AC Watt*Hour meter: https://duckduckgo.com/?q=amazon.com+kill-a-Watt+meter
DC Watt*Hour meter: https://www.amazon.com/dc-power-meter/s?k=dc+power+meter
And there are some pretty inexpensive Battery Monitors too (there are many nicer ones for $2xx or more too):
https://www.amazon.com/s?k=battery+monitor+system
You need to make sure your system is properly design, installed, and operating correctly. And you need to understand your loads.... Overall, the average off grid system should always generate more energy (to recharge battery bank and run the loads) than the loads themselves consume.
You can see that you are now in pretty much the peak sunshine season... And it will only get worse as you head into winter. That is why off grid solar systems are usually over designed (over paneled) to minimize generator runtime in winter and/or damage to the battery bank (over discharged, under charged).
I know that the above is probably not "your system"... But you can see how the math works and the questions we need to answer to get closer to understanding your system.
-Bill
Near San Francisco California: 3.5kWatt Grid Tied Solar power system+small backup genset
Categories
- All Categories
- 229 Forum & Website
- 137 Solar Forum News and Announcements
- 1.4K Solar News, Reviews, & Product Announcements
- 199 Solar Information links & sources, event announcements
- 898 Solar Product Reviews & Opinions
- 256 Solar Skeptics, Hype, & Scams Corner
- 22.5K Solar Electric Power, Wind Power & Balance of System
- 3.5K General Solar Power Topics
- 6.7K Solar Beginners Corner
- 1K PV Installers Forum - NEC, Wiring, Installation
- 2.1K Advanced Solar Electric Technical Forum
- 5.6K Off Grid Solar & Battery Systems
- 428 Caravan, Recreational Vehicle, and Marine Power Systems
- 1.1K Grid Tie and Grid Interactive Systems
- 654 Solar Water Pumping
- 816 Wind Power Generation
- 624 Energy Use & Conservation
- 619 Discussion Forums/Café
- 312 In the Weeds--Member's Choice
- 75 Construction
- 124 New Battery Technologies
- 108 Old Battery Tech Discussions
- 3.8K Solar News - Automatic Feed
- 3.8K Solar Energy News RSS Feed