LiFePo4 battery pack questions
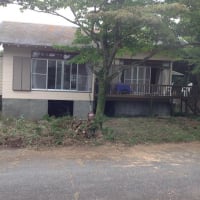
KenMorgan
Registered Users Posts: 92 ✭✭
Thanks to forum member Mcgivor I have managed to select and purchase some Calb 200 a/h lithium cells. importing them into Japan was easier than expected the Seller was very helpful with some of the additional paperwork that was required here.
The plan after top balancing them is to build a 2p16s pack to feed my inverters with. some of the questions I have are as follows:
Compression: after top balancing the cells I need to rearrange them into the 2p16s configuration is releasing the cells form compression after the top balance charge is complete advisable? will the cells swell as I release the compression? is this safe for the batteries?
if so then I need to stop the top balance and finish my battery box first so that I can put them in in under compression and then top balance.
BMS: the wires on the BMS appear to be too short for the battery packs shape, can I lengthen them (solder/heatshrink) with the same or thicker gauge wire? will this cause the BMS to not read correctly?
With the info that Mcivor gave me he suggested a 54.4 charge voltage which puts the individual cell at 3.4vdc and then use the LVD function of my inverters to set a shutdown thresh hold high enough to prevent the BMS from activating for instance in the 44 volt range which effectively leaves the individual cell at 2.75. the end result seems that it would comfortably put me in the 20-85% range for the batteries ensuring a longer life.
So the last question I guess is the various settings with in my solar controller Morningstar TSMPPT-60. I have downloaded MSView and played with the available settings just to help familiarize myself with the system.
anybody familiar with the setting could help walk me through it? so the bulk or absorb setting would be the above mentioned 54.4, but what about float? set it the same?
One thought I had was that as there is no need to equalize why not use the equalize function (in manual mode only) to occasionally let the cells be top balanced say 3.65 volts per cell vice 3.4 (58.4 vs 54.4) this would still be just below the BMS cutoff but might it help to top off or balance occasionally without the need to disassemble the pack. Thoughts?
with my current system the heat from the batteries, inverter, and solar controllers was enough to keep the battery shed at 5° or 6° Celsius on average with a couple of dips down to 1 degree during the coldest hours. I do not think I will get the same amount of heat with the lithium's so I have decided to make a battery warmer to keep the batteries warm enough 4 x 12 volt 25 watt heating pads wired in series will be Kapton taped to an aluminum plate along with 4 temp sensors taped to the lower portions of the cells insulated with foam and a temp controller set to turn on at 6° and turn off at 8° or 9° C this might be also on a timer to keep the heaters turned off from1800 to 0400 to save power. I will have to play with that portion to figure out what's best and too be honest as I have no desire to pull the pack apart after the build, I will probably tape several other size heating pads under there in case these are not enough
The plan after top balancing them is to build a 2p16s pack to feed my inverters with. some of the questions I have are as follows:
Compression: after top balancing the cells I need to rearrange them into the 2p16s configuration is releasing the cells form compression after the top balance charge is complete advisable? will the cells swell as I release the compression? is this safe for the batteries?
if so then I need to stop the top balance and finish my battery box first so that I can put them in in under compression and then top balance.
BMS: the wires on the BMS appear to be too short for the battery packs shape, can I lengthen them (solder/heatshrink) with the same or thicker gauge wire? will this cause the BMS to not read correctly?
With the info that Mcivor gave me he suggested a 54.4 charge voltage which puts the individual cell at 3.4vdc and then use the LVD function of my inverters to set a shutdown thresh hold high enough to prevent the BMS from activating for instance in the 44 volt range which effectively leaves the individual cell at 2.75. the end result seems that it would comfortably put me in the 20-85% range for the batteries ensuring a longer life.
So the last question I guess is the various settings with in my solar controller Morningstar TSMPPT-60. I have downloaded MSView and played with the available settings just to help familiarize myself with the system.
anybody familiar with the setting could help walk me through it? so the bulk or absorb setting would be the above mentioned 54.4, but what about float? set it the same?
One thought I had was that as there is no need to equalize why not use the equalize function (in manual mode only) to occasionally let the cells be top balanced say 3.65 volts per cell vice 3.4 (58.4 vs 54.4) this would still be just below the BMS cutoff but might it help to top off or balance occasionally without the need to disassemble the pack. Thoughts?
with my current system the heat from the batteries, inverter, and solar controllers was enough to keep the battery shed at 5° or 6° Celsius on average with a couple of dips down to 1 degree during the coldest hours. I do not think I will get the same amount of heat with the lithium's so I have decided to make a battery warmer to keep the batteries warm enough 4 x 12 volt 25 watt heating pads wired in series will be Kapton taped to an aluminum plate along with 4 temp sensors taped to the lower portions of the cells insulated with foam and a temp controller set to turn on at 6° and turn off at 8° or 9° C this might be also on a timer to keep the heaters turned off from1800 to 0400 to save power. I will have to play with that portion to figure out what's best and too be honest as I have no desire to pull the pack apart after the build, I will probably tape several other size heating pads under there in case these are not enough
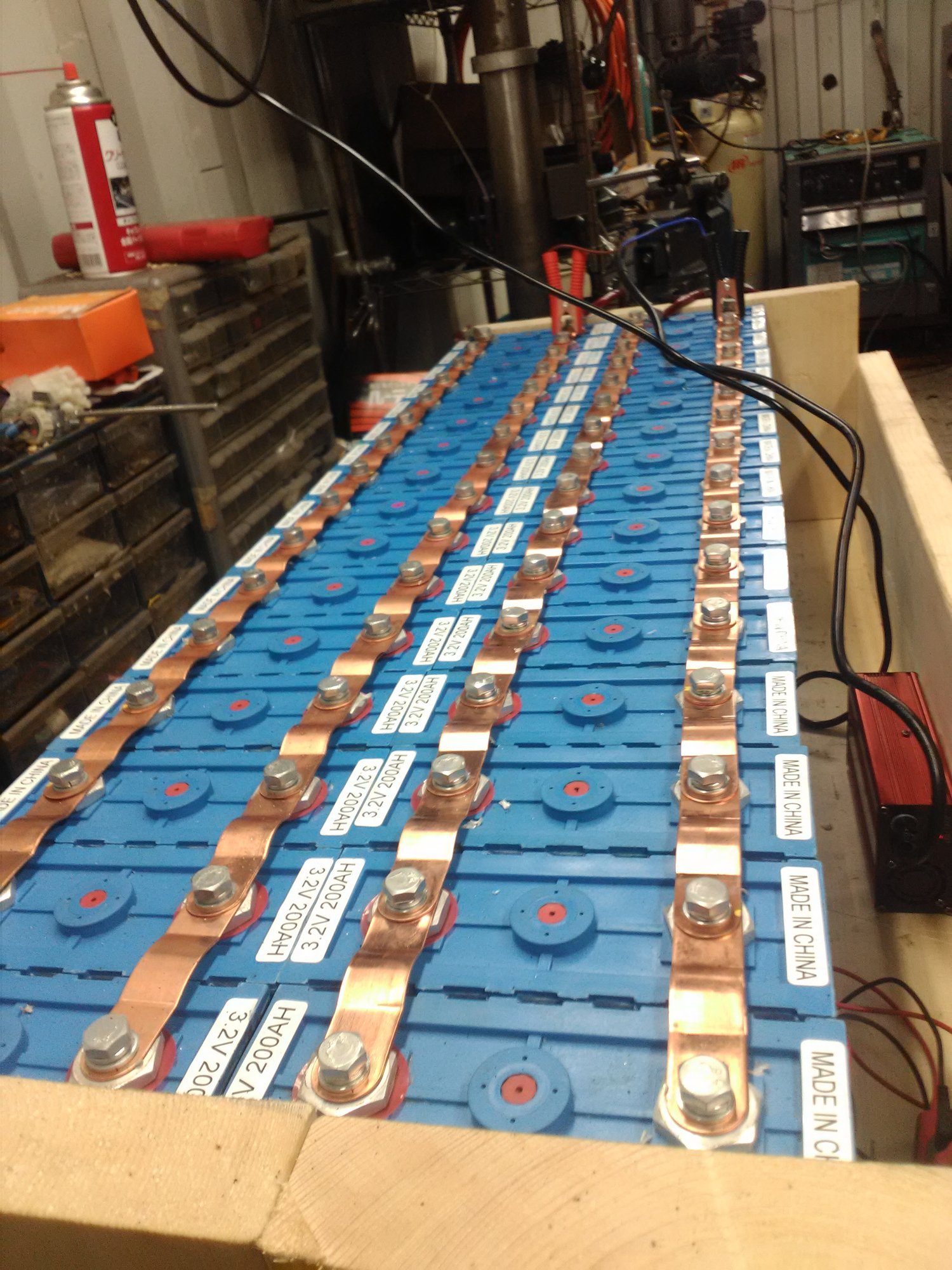
70kw LiFePo4 battery bank, 18 JA solar 200 watt panels, 20 sharp 200 watt panels, morningstar controller(s) and a
magnum 4448 inverter with all the usual junk that goes with it.
Tagged:
Comments
-
Hi Ken, good to hear all went well with the purchase, Jimmy is very helpful and professional, which is why I recommend him to you
Q. Compression: after top balancing the cells I need to rearrange them into the 2p16s configuration is releasing the cells form compression after the top balance charge is complete advisable? will the cells swell as I release the compression? is this safe for the batteries?
Normally clamping the cells together is used in mobile applications to prevent movement between them from causing damage to the terminals and bus bars, in a static situation it's not really required but dosent hurt. The cells retain their shape in normal conditions, there shouldn't be any problem encountered when compression is released.
Q. With the info that Mcivor gave me he suggested a 54.4 charge voltage which puts the individual cell at 3.4vdc and then use the LVD function of my inverters to set a shutdown thresh hold high enough to prevent the BMS from activating for instance in the 44 volt range which effectively leaves the individual cell at 2.75. the end result seems that it would comfortably put me in the 20-85% range for the batteries ensuring a longer life.
Can the LBCO be set any higher than 44V, that's actually quite low, I would suggest a minimum of 48V or preferably higher at 50V if possible.
Q. BMS: the wires on the BMS appear to be too short for the battery packs shape, can I lengthen them (solder/heatshrink) with the same or thicker gauge wire? will this cause the BMS to not read correctly?
Assuming the sense wires are being referred to, I too had to lengthen them, I used solder heat shrink, they don't carry current, should a joint fail, the BMS will disconnect the battery, a rat has conducted this test for me by gnawing on one.
Q. the last question I guess is the various settings with in my solar controller Morningstar TSMPPT-60. I have downloaded MSView and played with the available settings just to help familiarize myself with the system.
The settings are actually very simple, basically a process of eliminating many of the requirements of a LA bank, I have been using a profile that seems to work well for the past nine months which I will share with you, as soon as I hook up the PC, perhaps tomorrow.
Q.One thought I had was that as there is no need to equalize why not use the equalize function (in manual mode only) to occasionally let the cells be top balanced say 3.65 volts per cell vice 3.4 (58.4 vs 54.4) this would still be just below the BMS cutoff but might it help to top off or balance occasionally without the need to disassemble the pack. Thoughts?
Once the cells are ballanced they tend to remain ballanced, even after two years on my original bank of no name cells I increased the charging voltage to 3.650 VPC to allow the BMS to conduct it's ballancing process, there was some differential but nothing significant. The CALB cells are far superior in that they came with a capacity test report, so based on my personal experience I would recommend manually increasing the voltage annually whilst observing the trends, in other words don't program things to happen automatically.1500W, 6× Schutten 250W Poly panels , Schneider MPPT 60 150 CC, Schneider SW 2524 inverter, 400Ah LFP 24V nominal battery with Battery Bodyguard BMS
Second system 1890W 3 × 300W No name brand poly, 3×330 Sunsolar Poly panels, Morningstar TS 60 PWM controller, no name 2000W inverter 400Ah LFP 24V nominal battery with Daly BMS, used for water pumping and day time air conditioning.
5Kw Yanmar clone single cylinder air cooled diesel generator for rare emergency charging and welding. -
Ivor, thanks for chiming in, you have been a great help and resource in regards to this, i hope that I can sometime in the future repay you for the help you have given.
R/
Ken70kw LiFePo4 battery bank, 18 JA solar 200 watt panels, 20 sharp 200 watt panels, morningstar controller(s) and a magnum 4448 inverter with all the usual junk that goes with it. -
These are the settings that I came up with, value input is at 12V nominal multiply for voltage used.
First image. Bulk value is set for cell voltage of 3.425V, temperature compensation set to zero, which is actually redundant without a RTS as default no compensation, battery service is a personal choice.
Second image. Float enabled, set to 3.375 VPC, transition to float is based on duty cycle, after much experimenting this 89%for 1 second provides a quick transition. Higher percentages didn't work due to the duty cycle fluctuations in bulk sometimes dipping below 100% prompting premature transfer, lower could work though I am happy with this value so far.
Third image. Basically all zero, although there is a 13V there it's not required as the BMS would provide battery protection.
There may be different opinions with the MPPT, which I don't have to verify, but would expect them to be essentially the same, for the most part it a dummy down of a LA profile. This has been working for 9 months, perhaps there could be enhancements made but I'm reluctant to change what seems to work.
As the controller is designed primarily for LA, many options are fundementally redundant, this battery is a midnight to 9am (changes made depending on season) with occasional pumping during the day, the vast majority of which is powered directly by the array during float. A second system provides day time loads, the transfers are automatically controlled via inverter programming.
Hope this is helpful to anyone who is considering using LiFePo4, these values would NOT be valid for other lithium chemistries, they are my personal results derived through experimenting, using information gathered along with assistance from CALB battery and Morningstar support.
Always open to feedback or critique.1500W, 6× Schutten 250W Poly panels , Schneider MPPT 60 150 CC, Schneider SW 2524 inverter, 400Ah LFP 24V nominal battery with Battery Bodyguard BMS
Second system 1890W 3 × 300W No name brand poly, 3×330 Sunsolar Poly panels, Morningstar TS 60 PWM controller, no name 2000W inverter 400Ah LFP 24V nominal battery with Daly BMS, used for water pumping and day time air conditioning.
5Kw Yanmar clone single cylinder air cooled diesel generator for rare emergency charging and welding. -
mcgivor said:These are the settings that I came up with, value input is at 12V nominal multiply for voltage used.
First image. Bulk value is set for cell voltage of 3.425V, temperature compensation set to zero, which is actually redundant without a RTS as default no compensation, battery service is a personal choice.
Second image. Float enabled, set to 3.375 VPC, transition to float is based on duty cycle, after much experimenting this 89%for 1 second provides a quick transition. Higher percentages didn't work due to the duty cycle fluctuations in bulk sometimes dipping below 100% prompting premature transfer, lower could work though I am happy with this value so far.70kw LiFePo4 battery bank, 18 JA solar 200 watt panels, 20 sharp 200 watt panels, morningstar controller(s) and a magnum 4448 inverter with all the usual junk that goes with it. -
mcgivor said:
Can the LBCO be set any higher than 44V, that's actually quite low, I would suggest a minimum of 48V or preferably higher at 50V if possible.
Yes I can easily set it higher so you think that 50 would be better? thats 3.125 per cell.70kw LiFePo4 battery bank, 18 JA solar 200 watt panels, 20 sharp 200 watt panels, morningstar controller(s) and a magnum 4448 inverter with all the usual junk that goes with it. -
My assumption was correct that there would be different settings for the MPPT controller, the PWM duty cycle is typically set at 30% for LA batteries, the MPPT appears to use a time based absorption algorithm. Morningstar TS controllers have a battery voltage sense input which corrects the differential between the voltage measured at the controller versus that at the battery terminals caused by voltage drop.
My suggestion would be to reduce the time to a lower value, with my Schneider MPPT controller, which doesn't have battery sense input I use 1 hour to compensate for voltage drop, the starting point was 6 minutes which was insufficient. With the Morningstar I would program a low value of 10 minutes as a starting point, then observe the current during this period, if it remains high at the end of 10 minutes, increase the time incrementally until the current drops to a minimal value which would indicate the battery is saturated at the programed voltage. There will be some experimenting involved to reach the ideal values, as no two systems are the same in terms of array and battery capacity.
The LBCO set at a higher voltage will extend the life expectancy, much the same as not holding at fully charged state for extended periods, some manufacturers of battery systems will have different warranty periods foe different settings and may void the warranty if exceeded. Here's the recomendations for SimpliPhi's battery using Schneider inverter , there is a similar document for Outback.
1500W, 6× Schutten 250W Poly panels , Schneider MPPT 60 150 CC, Schneider SW 2524 inverter, 400Ah LFP 24V nominal battery with Battery Bodyguard BMS
Second system 1890W 3 × 300W No name brand poly, 3×330 Sunsolar Poly panels, Morningstar TS 60 PWM controller, no name 2000W inverter 400Ah LFP 24V nominal battery with Daly BMS, used for water pumping and day time air conditioning.
5Kw Yanmar clone single cylinder air cooled diesel generator for rare emergency charging and welding. -
mcgivor said:My assumption was correct that there would be different settings for the MPPT controller, the PWM duty cycle is typically set at 30% for LA batteries, the MPPT appears to use a time based absorption algorithm. Morningstar TS controllers have a battery voltage sense input which corrects the differential between the voltage measured at the controller versus that at the battery terminals caused by voltage drop.
My suggestion would be to reduce the time to a lower value, with my Schneider MPPT controller, which doesn't have battery sense input I use 1 hour to compensate for voltage drop, the starting point was 6 minutes which was insufficient. With the Morningstar I would program a low value of 10 minutes as a starting point, then observe the current during this period, if it remains high at the end of 10 minutes, increase the time incrementally until the current drops to a minimal value which would indicate the battery is saturated at the programed voltage. There will be some experimenting involved to reach the ideal values, as no two systems are the same in terms of array and battery capacity.
The LBCO set at a higher voltage will extend the life expectancy, much the same as not holding at fully charged state for extended periods, some manufacturers of battery systems will have different warranty periods foe different settings and may void the warranty if exceeded.
70kw LiFePo4 battery bank, 18 JA solar 200 watt panels, 20 sharp 200 watt panels, morningstar controller(s) and a magnum 4448 inverter with all the usual junk that goes with it.
Categories
- All Categories
- 228 Forum & Website
- 136 Solar Forum News and Announcements
- 1.4K Solar News, Reviews, & Product Announcements
- 199 Solar Information links & sources, event announcements
- 898 Solar Product Reviews & Opinions
- 256 Solar Skeptics, Hype, & Scams Corner
- 22.5K Solar Electric Power, Wind Power & Balance of System
- 3.5K General Solar Power Topics
- 6.7K Solar Beginners Corner
- 1K PV Installers Forum - NEC, Wiring, Installation
- 2.1K Advanced Solar Electric Technical Forum
- 5.6K Off Grid Solar & Battery Systems
- 428 Caravan, Recreational Vehicle, and Marine Power Systems
- 1.1K Grid Tie and Grid Interactive Systems
- 654 Solar Water Pumping
- 816 Wind Power Generation
- 624 Energy Use & Conservation
- 619 Discussion Forums/Café
- 312 In the Weeds--Member's Choice
- 75 Construction
- 124 New Battery Technologies
- 108 Old Battery Tech Discussions
- 3.8K Solar News - Automatic Feed
- 3.8K Solar Energy News RSS Feed