Offgrid DC overvoltage fault
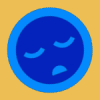
oalloyd
Registered Users Posts: 1 ✭
I have a HP6KW48V inverter, flexmax 80 CC,3 strings of 3 250W panels. Inverter displays battery voltage 2V above actual voltage.
I got no faults using 6V lead acid Battery banks but when i switched to 1 bank of 4 12V 100ah LifePo4 battery packs all hell broke loose.
I replaced one battery with faulty BMS but one faults persists:
Inverter trips on over voltage fault. Conditions consistent with fault include; Inverter may display 68 VDC, PV volts on CC may be 105VDC, May occur as CC switches from bulk to absorb or float
CC settings: bulk 58, float 58, absorb 58V @ 0.0A @ 30min., rebulk 53
Switching off the PV array when the VmP is 101 seems to eliminate the fault. I would like suggestions on a device that can achieve this automatically (overvoltage protection of some sort). Also i welcome any thoughts on possible causes and solutions. I am wondering if the one bank is too small for the solar array i have using LifePo4 batteries.
Ps. reducing the strings from 3 to 2 panels is not a viable option.
I got no faults using 6V lead acid Battery banks but when i switched to 1 bank of 4 12V 100ah LifePo4 battery packs all hell broke loose.
I replaced one battery with faulty BMS but one faults persists:
Inverter trips on over voltage fault. Conditions consistent with fault include; Inverter may display 68 VDC, PV volts on CC may be 105VDC, May occur as CC switches from bulk to absorb or float
CC settings: bulk 58, float 58, absorb 58V @ 0.0A @ 30min., rebulk 53
Switching off the PV array when the VmP is 101 seems to eliminate the fault. I would like suggestions on a device that can achieve this automatically (overvoltage protection of some sort). Also i welcome any thoughts on possible causes and solutions. I am wondering if the one bank is too small for the solar array i have using LifePo4 batteries.
Ps. reducing the strings from 3 to 2 panels is not a viable option.
Tagged:
Comments
-
Have you watched the Vbatt voltage with a known good voltmeter?
It sort of sounds like the BMS is tripping ("turning off the battery") from over voltage--Possibly too much current from charge controller going into a "full" battery bank...
FLA batteries are pretty good at short term absorption of high voltage/high current from a solar charge controller. If nothing else, FLA take the "extra current" and turn it into Hydrogen and Oxygen gasses. Short term no problem... Longer term excessive charging uses water, overheats batteries, erodes plates, and causes positive grid/plate corrosion.
Li Ion batteries do not have this capability--When "excessive" charging current they over voltage and early life failure--And/or the BMS shutdown the battery bank (open switch and disconnect the battery bank from the charging source).
I have never used an MPPT solar charge controller (I am grid tied)--But there seemed to be an issue when doing MPPT "scans" of the array (Vmp vs Imp every 5-15 minutes) for some (especially older) charge controllers. And from what a few folks have seen, during the "scans", the MPPT controller(s) send "unregulated" current to the battery bank while doing "their MPPT thing".
I don't know enough about the FM 80/etc. controllers--But I wonder if you are getting excessive current from the charge controller at times--Bringing the battery voltage up/possibly tripping the BMS battery disconnect (if your BMS has that capability). When that happens, Vbatt will certainly peak well above normal--And cause your inverter to read high voltage/trip High voltage shutdown. (????).
Some controller brands/models have different MPPT settings/options--Does yours and can you change it to another MPPT method?
Your system is capable of outputting >~30 Amps into your 100 AH--Which is a lot (but a good Li Battery should be able to take upwards of 100 Amps charging--At least when the bank is less than 100% SoC).- 3 * 3 * 250 Watt panels * 0.77 panel+controller derating * 1/58 volts = 29.9 Amps
Also check (for example) the Vbatt bus voltage, and measure Vbatt terminals on the FM 80, AC inverter, etc... Make sure you do not have too much voltage drop in your wiring (short, heavy cables for DC current) and you don't have dirty/loose electrical connections anywhere.
It really sounds like the FM 80 is dumping "excess current" into your full battery bank during MPPT "search". It was something that I was concerned about years ago--And with Li Ion+BMS setups, this could be a bigger issue now.
One possible fix... Look at your 58 volt set point choices... For a typical LiFePO4 type battery bank, suggest running 20% to 90% state of charge (do not charge to 100%)... That leaves you a 10% "headroom" for the Li Ion battery bank to safely/reliably absorb the "excess" current spikes during otherwise (possibly) normal FM 80 operations... Also, typically Li Ion batteries last longer when operated in the 20% to 90% range. Charging to 100% typically shortens their operational life.
For example set float to 13.6v*4=54.4v volts... Again, a little more headroom.
I am certainly no expert on the Li Ion/BMS/FM 80 subjects--Just some things to check/think about from what I have seen/read over the years. Contacting Outback (or using their forum) may give you some more information on what the FM 80 does during MPPT Vmp/Imp searches and such (do they dump current into an otherwise full/near full battery bank)...
Also, can you give us a little more information about your Li Ion banks (number of cells, min/max voltage, BMS details--Links are OK)?
Hopefully, some folks with more Outback/Li Ion experience than I can chime in...
Your thoughts?
-BillNear San Francisco California: 3.5kWatt Grid Tied Solar power system+small backup genset -
The fault (loss of power) is from the inverter right? It also can be from a BMS. I do not know the inverter make. Who designed this system please? In addition to Bill's questions. Where did you get the set-points on the FM 80 from? What is the Inverter HVCO set at ?
The Outback FM series is alot faster that 5 minutes BTW. More like 5 + seconds. Schneider mppt speeds are faster than xanbus network can display. If a load comes on, the MPPV can change 2 seconds later on the network solar voltmeter."we go where power lines don't" Sierra Nevada mountain area
htps://offgridsolar1.com/
E-mail offgridsolar@sti.net -
I was saying the scans are once every 5-xx minutes--I know the scans are only seconds long--And it was during this 5 second or so "scan" that the controller(s) seem to dump 100% of array power into the battery bank to measure the Vmp vs Imp array characteristics (and uses the Pmp=Vmp*Imp to set the the Vmp-array for the next 5-xx minute period).
In anycase, Dave knows a lot more about these systems than I ever will...
-BillNear San Francisco California: 3.5kWatt Grid Tied Solar power system+small backup genset -
You're pushing the battery to it's linits with the settings being used, some serious study of the chemistry is a prerequisite because unlike lead acid LiFePo4 one needs to base everything on a cellular level, because this is how the BMS monitors it's particular group of cells within an individual battery. Having four 12V batteries in series would mean four BMS's monitoring four cells each, if any single cell exceeds the limitations the BMS will disconnect the individual battery within the string, thus rendering the whole string disconnected.
Having a setting of 58V for the entire string equates to a cell voltage setpoint of 3.625 V per cell, at such a high setpoint it is highly likely that at least one cell in sixteen has reached its maximum 3.600V threshold. My suggestion would be to program the controller to the following values, bulk/absorption 55.2V, absorption time 10 minutes, float 54V, recharge 50V.
The capacity of the battery is unlikely the cause as typically LiFePo4 batteries can accept up to 1C or 100A charging current, how the capacity relates to the entire system would depend upon loads, but judging by the 4 kW inverter the battery dose appear small in comparison to the inverters potential.
On the other end of the spectrum is the low voltage disconnect, many inverters that are not programmable and are biased towards LA batteries, these setpoints are typically too low and will result in total discharge which is harmful to LFP in the long term. Although not mentioned consider this a head's up.
1500W, 6× Schutten 250W Poly panels , Schneider MPPT 60 150 CC, Schneider SW 2524 inverter, 400Ah LFP 24V nominal battery with Battery Bodyguard BMS
Second system 1890W 3 × 300W No name brand poly, 3×330 Sunsolar Poly panels, Morningstar TS 60 PWM controller, no name 2000W inverter 400Ah LFP 24V nominal battery with Daly BMS, used for water pumping and day time air conditioning.
5Kw Yanmar clone single cylinder air cooled diesel generator for rare emergency charging and welding.
Categories
- All Categories
- 228 Forum & Website
- 136 Solar Forum News and Announcements
- 1.4K Solar News, Reviews, & Product Announcements
- 199 Solar Information links & sources, event announcements
- 898 Solar Product Reviews & Opinions
- 256 Solar Skeptics, Hype, & Scams Corner
- 22.5K Solar Electric Power, Wind Power & Balance of System
- 3.5K General Solar Power Topics
- 6.7K Solar Beginners Corner
- 1K PV Installers Forum - NEC, Wiring, Installation
- 2.1K Advanced Solar Electric Technical Forum
- 5.6K Off Grid Solar & Battery Systems
- 428 Caravan, Recreational Vehicle, and Marine Power Systems
- 1.1K Grid Tie and Grid Interactive Systems
- 654 Solar Water Pumping
- 816 Wind Power Generation
- 624 Energy Use & Conservation
- 619 Discussion Forums/Café
- 312 In the Weeds--Member's Choice
- 75 Construction
- 124 New Battery Technologies
- 108 Old Battery Tech Discussions
- 3.8K Solar News - Automatic Feed
- 3.8K Solar Energy News RSS Feed