RENOGY Rover 60A voltage display is to high
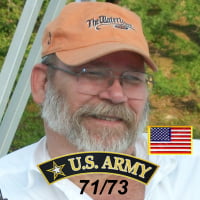
MEK1954
Registered Users Posts: 23 ✭✭
I have a RENOGY Rover 60A and the voltage on the front panel display is to high by about 0.7 to 0.8 volts and I beleave it is putting the charge controller into float mode before the battery's are fully charged. On a good day my system will normally charge at about 34 to 38 amps for about 3 to 4 hrs. but yesterday at about 12.30 the current started dropping and by 1PM it was down to 21 amps and would only go higher if I increased the load on the inverter. Later in the afternoon when the sun was lower the charge level dropped below my demand level and the renogy display quickly drops from 100% charge level to 80% charge level. I did try to set the float level from 13.8 to 14.0 v but that did not make any difference. Is there anyway to set the voltage on the renogy
display to the correct level?
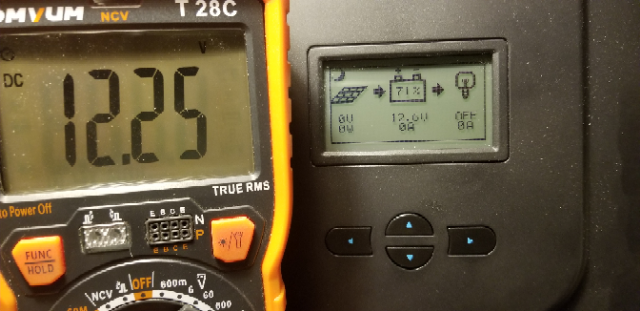
Comments
-
What is the awg and length of the wiring from the battery bank to the controller.You want about 0.1 to 0.2 volt maximum voltage drop in the wiring.You DMM, was that measured at the battery bus or on the controller Vbatt terminals?BillNear San Francisco California: 3.5kWatt Grid Tied Solar power system+small backup genset
-
What is the awg and length of the wiring from the battery bank to the controller. -------> 4ga from controller +bat to junction block and 1/0ga from block to +bat 4ga from - controller to junction block and 1/0ga from block to -batYou want about 0.1 to 0.2 volt maximum voltage drop in the wiring. ------> from + controller to +bat there is a 0.008 vYou DMM, was that measured at the battery bus or on the controller Vbatt terminals? --------> measured at controller + to batt+ to get a 0.008v and the measurement on the DVM was on the battery terminals
-
If the controller is running hot, it will reduce the output voltage about 0.030 volts per degree C over 25C (and increase charging voltage by the same account for every 1C from below 25C).If the controller is not running hot (and reducing charging voltage), that is about all I know.Perhaps somebody else here knows if you can calibrate the unit.You might check their website and see if they have a computer or other interface to program the controller.BillNear San Francisco California: 3.5kWatt Grid Tied Solar power system+small backup genset
-
The controller display is an indication of state of charge during charging only, it is based on voltage alone, when there is no PV input the battery % value will correspond whth the battery voltage. With a typical lead acid battery the standing (without PV or load) voltage of a fully charged battery would be in the neighborhood of 12.6V, so the indicated 71% SOC is misleading.
The voltage displayed on the controller has a resolution of 100mA, the DMM is 10mA so in theroy the DMM should be more accurate however depending on its quality it may be as much as +/- 5% of what it's actually reading, 5% of 12.25 = 0.61 so the actual value being measured could be 12.86V or 11.64V, hopefully the accuracy is better than 5% but even 1% would be +/- 0.125 of actual. This is true for the controller accuracy it may be inaccurate which is more likely as it is merely an indication.
Having the meter tested against a known calibrated one will help confirm if what's being seen is to be believed, the DC voltage accuracy for the meters I have, the $100 Fluke 12 is 0.9%, the $300 Fluke 179 is 0.09%, testing between the two 179's I have is usually within 2mV (0.002V) but >5mV when tested against the 12.
1500W, 6× Schutten 250W Poly panels , Schneider MPPT 60 150 CC, Schneider SW 2524 inverter, 400Ah LFP 24V nominal battery with Battery Bodyguard BMS
Second system 1890W 3 × 300W No name brand poly, 3×330 Sunsolar Poly panels, Morningstar TS 60 PWM controller, no name 2000W inverter 400Ah LFP 24V nominal battery with Daly BMS, used for water pumping and day time air conditioning.
5Kw Yanmar clone single cylinder air cooled diesel generator for rare emergency charging and welding. -
I have 3 mounted digital volt, currant, watt meters staggered along my system - Pre batt, post bat and at a remote location and they all read the same ( within 0.001v) except the remote meter it reads 0.01v less and that is because it is on longer wire. so 4 meters show basically about the same and I am trying to learn how to adjust the renogy to display the actual voltage so it does not go into premature float charge before my battery's are charged.
-
I bought another controller and it reads the same voltage as the meter.
-
MEK1954 said:I bought another controller and it reads the same voltage as the meter.1500W, 6× Schutten 250W Poly panels , Schneider MPPT 60 150 CC, Schneider SW 2524 inverter, 400Ah LFP 24V nominal battery with Battery Bodyguard BMS
Second system 1890W 3 × 300W No name brand poly, 3×330 Sunsolar Poly panels, Morningstar TS 60 PWM controller, no name 2000W inverter 400Ah LFP 24V nominal battery with Daly BMS, used for water pumping and day time air conditioning.
5Kw Yanmar clone single cylinder air cooled diesel generator for rare emergency charging and welding. -
It is still a RENOGY 60A but this one has blue buttons and I bought a second one and all voltage's are the same
-
At this point, assuming that you are committed to this controller(s), you should only need to "worry" about the Absorb and Float Set Point(s).
Use your voltmeter to confirm the voltage at the battery bus (or controller Vbatt terminals). Assuming the controller is otherwise repeatable, then setting the voltage(s) to what you want at the battery--That should be good enough. (ideally, the controller and batteries would be around room temprature of ~75F/25C so you do not have the -0.003 or -0.005 volts per cell per degree C offsets (as controller temperature sensor cools, it will raise the battery charging voltage/setpoints).
The "battery state of charge" indicators on most controllers is very iffy at best. Just monitor the voltage(s) of battery bus and go with that...
Unless you want to install some other type of battery monitoring meter(s).
-Bill
Near San Francisco California: 3.5kWatt Grid Tied Solar power system+small backup genset -
Thank you all for sharing your knowledge, you have been a lot of help.Mark
-
Why can't people on these discussion boards ever just give a simple straight answer to questions?
Can the Rover charge controller be calibrated, yes or no?... If yes, how? -
The current manual does not seem to have a "calibration entry" and could not find any software/interfaces that could access the controller through the RS-232 interface and adjust any configuration settings. The most interesting is here using a Raspberry Pi:
https://www.renogy.com/content/RNG-CTRL-RVR60/RVR60-Manual.pdf
https://www.reddit.com/r/SolarDIY/comments/frafmv/any_alternatives_to_the_renogy_bt_app_for/
And there is always contacting Renogy directly and asking them:
https://www.renogy.com/contact-us
-BillNear San Francisco California: 3.5kWatt Grid Tied Solar power system+small backup genset -
OffGridHermit said:Why can't people on these discussion boards ever just give a simple straight answer to questions?
Categories
- All Categories
- 228 Forum & Website
- 136 Solar Forum News and Announcements
- 1.4K Solar News, Reviews, & Product Announcements
- 199 Solar Information links & sources, event announcements
- 898 Solar Product Reviews & Opinions
- 256 Solar Skeptics, Hype, & Scams Corner
- 22.5K Solar Electric Power, Wind Power & Balance of System
- 3.5K General Solar Power Topics
- 6.7K Solar Beginners Corner
- 1K PV Installers Forum - NEC, Wiring, Installation
- 2.1K Advanced Solar Electric Technical Forum
- 5.6K Off Grid Solar & Battery Systems
- 428 Caravan, Recreational Vehicle, and Marine Power Systems
- 1.1K Grid Tie and Grid Interactive Systems
- 654 Solar Water Pumping
- 816 Wind Power Generation
- 624 Energy Use & Conservation
- 619 Discussion Forums/Café
- 312 In the Weeds--Member's Choice
- 75 Construction
- 124 New Battery Technologies
- 108 Old Battery Tech Discussions
- 3.8K Solar News - Automatic Feed
- 3.8K Solar Energy News RSS Feed